Cmos Vco & Lna Implemented by Air-Suspended
Total Page:16
File Type:pdf, Size:1020Kb
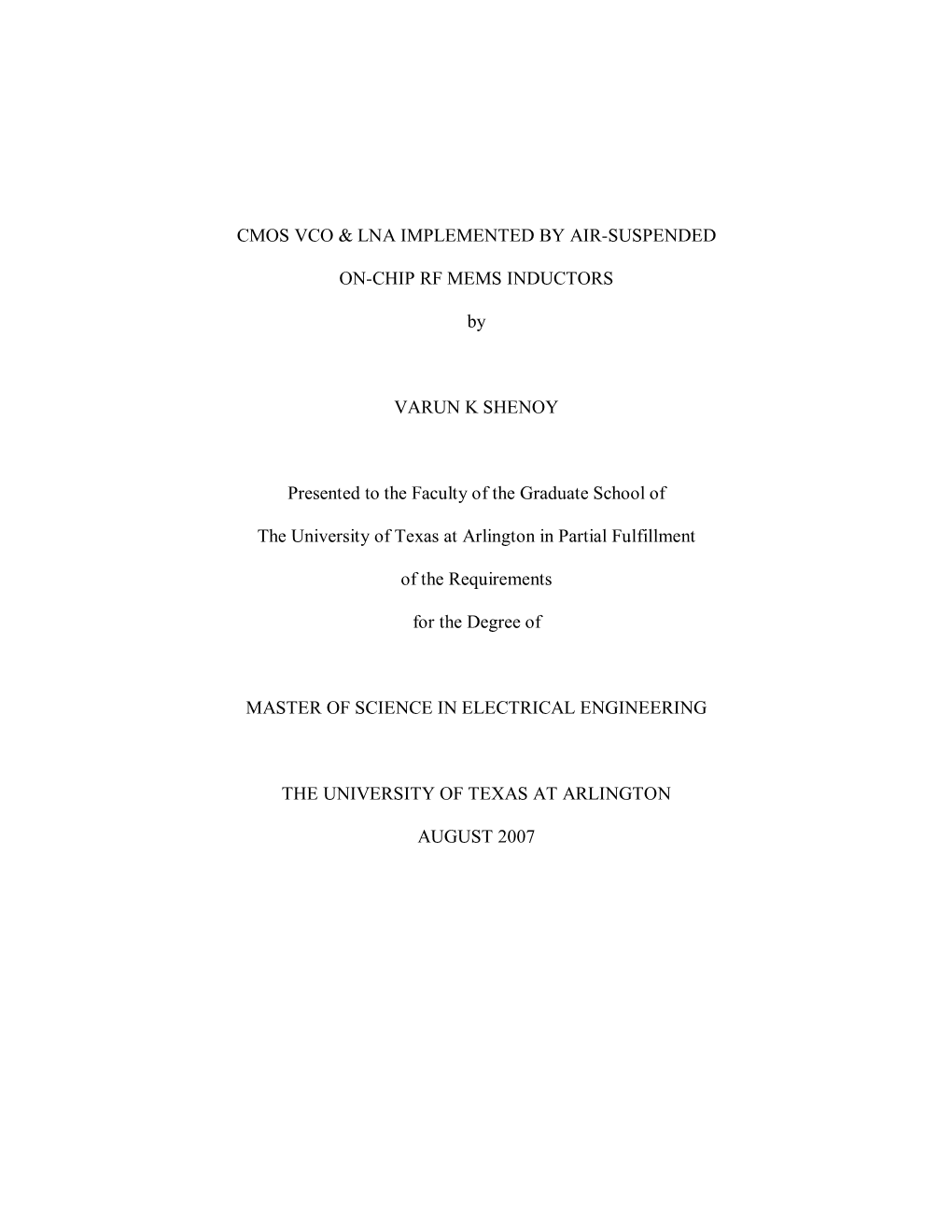
Load more
Recommended publications
-
Chapter 19 - the Oscillator
Chapter 19 - The Oscillator The Electronics Curse “Your amplifiers will oscillate, your oscillators won't!” Question, What is an Oscillator? A Pendulum is an Oscillator... “Oscillators are circuits that are used to generate A.C. signals. Although mechanical methods, like alternators, can be used to generate low frequency A.C. signals, such as the 50 Hz mains, electronic circuits are the most practical way of generating signals at radio frequencies.” Comment: Hmm, wasn't always. In the time of Marconi, generators were used to generate a frequency to transmit. We are talking about kiloWatts of power! e.g. Grimeton L.F. Transmitter. Oscillators are widely used in both transmitters and receivers. In transmitters they are used to generate the radio frequency signal that will ultimately be applied to the antenna, causing it to transmit. In receivers, oscillators are widely used in conjunction with mixers (a circuit that will be covered in a later module) to change the frequency of the received radio signal. Principal of Operation The diagram below is a ‘block diagram’ showing a typical oscillator. Block diagrams differ from the circuit diagrams that we have used so far in that they do not show every component in the circuit individually. Instead they show complete functional blocks – for example, amplifiers and filters – as just one symbol in the diagram. They are useful because they allow us to get a high level overview of how a circuit or system functions without having to show every individual component. The Barkhausen Criterion [That's NOT ‘dog box’ in German!] Comment: In electronics, the Barkhausen stability criterion is a mathematical condition to determine when a linear electronic circuit will oscillate. -
AM Transmitters
Chapter 4: AM Transmitters Chapter 4 Objectives At the conclusion of this chapter, the reader will be able to: • Draw a block diagram of a high or low-level AM transmitter, giving typical signals at each point in the circuit. • Discuss the relative advantages and disadvantages of high and low-level AM transmitters. • Identify an RF oscillator configuration, pointing out the components that control its frequency. • Describe the physical construction of a quartz crystal. • Calculate the series and parallel resonant frequencies of a quartz crystal, given manufacturer's data. • Identify the resonance modes of a quartz crystal in typical RF oscillator circuits. • Describe the operating characteristics of an RF amplifier circuit, given its schematic diagram. • Explain the operation of modulator circuits. • Identify the functional blocks (amplifiers, oscillators, etc) in a schematic diagram. • List measurement procedures used with AM transmitters. • Develop a plan for troubleshooting a transmitter. In Chapter 3 we studied the theory of amplitude modulation, but we never actually built an AM transmitter. To construct a working transmitter (or receiver), a knowledge of RF circuit principles is necessary. A complete transmitter consists of many different stages and hundreds of electronic components. When beginning technicians see the schematic diagram of a "real" electronic system for the first time, they're overwhelmed. A schematic contains much valuable information. But to the novice, it's a swirling mass of resistors, capacitors, coils, transistors, and IC chips, all connected in a massive web of wires! How can anyone understand this? All electronic systems, no matter how complex, are built from functional blocks or stages. -
I. Common Base / Common Gate Amplifiers
I. Common Base / Common Gate Amplifiers - Current Buffer A. Introduction • A current buffer takes the input current which may have a relatively small Norton resistance and replicates it at the output port, which has a high output resistance • Input signal is applied to the emitter, output is taken from the collector • Current gain is about unity • Input resistance is low • Output resistance is high. V+ V+ i SUP ISUP iOUT IOUT RL R is S IBIAS IBIAS V− V− (a) (b) B. Biasing = /α ≈ • IBIAS ISUP ISUP EECS 6.012 Spring 1998 Lecture 19 II. Small Signal Two Port Parameters A. Common Base Current Gain Ai • Small-signal circuit; apply test current and measure the short circuit output current ib iout + = β v r gmv oib r − o ve roc it • Analysis -- see Chapter 8, pp. 507-509. • Result: –β ---------------o ≅ Ai = β – 1 1 + o • Intuition: iout = ic = (- ie- ib ) = -it - ib and ib is small EECS 6.012 Spring 1998 Lecture 19 B. Common Base Input Resistance Ri • Apply test current, with load resistor RL present at the output + v r gmv r − o roc RL + vt i − t • See pages 509-510 and note that the transconductance generator dominates which yields 1 Ri = ------ gm µ • A typical transconductance is around 4 mS, with IC = 100 A • Typical input resistance is 250 Ω -- very small, as desired for a current amplifier • Ri can be designed arbitrarily small, at the price of current (power dissipation) EECS 6.012 Spring 1998 Lecture 19 C. Common-Base Output Resistance Ro • Apply test current with source resistance of input current source in place • Note roc as is in parallel with rest of circuit g v m ro + vt it r − oc − v r RS + • Analysis is on pp. -
ECE 255, MOSFET Basic Configurations
ECE 255, MOSFET Basic Configurations 8 March 2018 In this lecture, we will go back to Section 7.3, and the basic configurations of MOSFET amplifiers will be studied similar to that of BJT. Previously, it has been shown that with the transistor DC biased at the appropriate point (Q point or operating point), linear relations can be derived between the small voltage signal and current signal. We will continue this analysis with MOSFETs, starting with the common-source amplifier. 1 Common-Source (CS) Amplifier The common-source (CS) amplifier for MOSFET is the analogue of the common- emitter amplifier for BJT. Its popularity arises from its high gain, and that by cascading a number of them, larger amplification of the signal can be achieved. 1.1 Chararacteristic Parameters of the CS Amplifier Figure 1(a) shows the small-signal model for the common-source amplifier. Here, RD is considered part of the amplifier and is the resistance that one measures between the drain and the ground. The small-signal model can be replaced by its hybrid-π model as shown in Figure 1(b). Then the current induced in the output port is i = −gmvgs as indicated by the current source. Thus vo = −gmvgsRD (1.1) By inspection, one sees that Rin = 1; vi = vsig; vgs = vi (1.2) Thus the open-circuit voltage gain is vo Avo = = −gmRD (1.3) vi Printed on March 14, 2018 at 10 : 48: W.C. Chew and S.K. Gupta. 1 One can replace a linear circuit driven by a source by its Th´evenin equivalence. -
Lec#12: Sine Wave Oscillators
Integrated Technical Education Cluster Banna - At AlAmeeria © Ahmad El J-601-1448 Electronic Principals Lecture #12 Sine wave oscillators Instructor: Dr. Ahmad El-Banna 2015 January Banna Agenda - © Ahmad El Introduction Feedback Oscillators Oscillators with RC Feedback Circuits 1448 Lec#12 , Jan, 2015 Oscillators with LC Feedback Circuits - 601 - J Crystal-Controlled Oscillators 2 INTRODUCTION 3 J-601-1448 , Lec#12 , Jan 2015 © Ahmad El-Banna Banna Introduction - • An oscillator is a circuit that produces a periodic waveform on its output with only the dc supply voltage as an input. © Ahmad El • The output voltage can be either sinusoidal or non sinusoidal, depending on the type of oscillator. • Two major classifications for oscillators are feedback oscillators and relaxation oscillators. o an oscillator converts electrical energy from the dc power supply to periodic waveforms. 1448 Lec#12 , Jan, 2015 - 601 - J 4 FEEDBACK OSCILLATORS FEEDBACK 5 J-601-1448 , Lec#12 , Jan 2015 © Ahmad El-Banna Banna Positive feedback - • Positive feedback is characterized by the condition wherein a portion of the output voltage of an amplifier is fed © Ahmad El back to the input with no net phase shift, resulting in a reinforcement of the output signal. Basic elements of a feedback oscillator. 1448 Lec#12 , Jan, 2015 - 601 - J 6 Banna Conditions for Oscillation - • Two conditions: © Ahmad El 1. The phase shift around the feedback loop must be effectively 0°. 2. The voltage gain, Acl around the closed feedback loop (loop gain) must equal 1 (unity). 1448 Lec#12 , Jan, 2015 - 601 - J 7 Banna Start-Up Conditions - • For oscillation to begin, the voltage gain around the positive feedback loop must be greater than 1 so that the amplitude of the output can build up to a desired level. -
Unit I - Feedback Amplifiers Part - a 1
EC6401 Electronic Circuits II Department of ECE 2014-2015 UNIT I - FEEDBACK AMPLIFIERS PART - A 1. Define positive and negative feedback? Ans: Positive feedback: If the feedback voltage (or current) is so applied as to increase the input voltage (i.e. it is in phase with it), then it is called positive feedback. Negative feedback: If the feedback voltage (or current) is so applied as to reduce the input voltage (i.e. it is 180out of phase with it), then it is called negative feedback. 2. What are the advantages of negative feedback? Ans: The advantages of negative feedback are higher fidelity and stabilized gain, increased bandwidth, less distortion and reduced noise and input & output impedances can be modified as desired. 3. List four basic types of feedback? Ans: (1) Voltage series feedback (2) Voltage shunt feedback (3) Current series feedback and (4) Current shunt feedback. 4. Negative feedback is preferred to other methods of modifying Amplifier characteristics. Why? Ans: Negative feedback is preferred to other methods of modifying Amplifier Characteristics because it has the following advantages of reduction in distortion, stability in gain, increased bandwidth etc. 5. State the condition in (1+A) which a feedback amplifier must satisfy in order to be stable. Ans: The two important and necessary conditions are (1) The feedback must be positive, (2) Feedback factor must be unity i.e. A = 1 6. What is meant by phase and gain margin? Ans: Phase Margin: It is defined as 1800 minus the magnitude of the Aat the frequency at which A is unity. If he phase margin is negative the system is stable otherwise unstable. -
Lecture 19 Common-Gate Stage
4/7/2008 Lecture 19 OUTLINE • Common‐gate stage • Source follower • Reading: Chap. 7.3‐7.4 EE105 Spring 2008 Lecture 19, Slide 1Prof. Wu, UC Berkeley Common‐Gate Stage AvmD= gR • Common‐gate stage is similar to common‐base stage: a rise in input causes a rise in output. So the gain is positive. EE105 Spring 2008 Lecture 19, Slide 2Prof. Wu, UC Berkeley EE105 Fall 2007 1 4/7/2008 Signal Levels in CG Stage • In order to maintain M1 in saturation, the signal swing at Vout cannot fall below Vb‐VTH EE105 Spring 2008 Lecture 19, Slide 3Prof. Wu, UC Berkeley I/O Impedances of CG Stage 1 R = in λ =0 RRout= D gm • The input and output impedances of CG stage are similar to those of CB stage. EE105 Spring 2008 Lecture 19, Slide 4Prof. Wu, UC Berkeley EE105 Fall 2007 2 4/7/2008 CG Stage with Source Resistance 1 g vv= m Xin1 + RS gm 1 vv g AgR==out x m vmD1 vvxin + RS gm R gR ==D mD 1 1+ gRmS + RS gm • When a source resistance is present, the voltage gain is equal to that of a CS stage with degeneration, only positive. EE105 Spring 2008 Lecture 19, Slide 5Prof. Wu, UC Berkeley Generalized CG Behavior Rgout= (1++g mrR O) S r O • When a gate resistance is present it does not affect the gain and I/O impedances since there is no potential drop across it (at low frequencies). • The output impedance of a CG stage with source resistance is identical to that of CS stage with degeneration. -
Fundamentals of MOSFET and IGBT Gate Driver Circuits
Application Report SLUA618A–March 2017–Revised October 2018 Fundamentals of MOSFET and IGBT Gate Driver Circuits Laszlo Balogh ABSTRACT The main purpose of this application report is to demonstrate a systematic approach to design high performance gate drive circuits for high speed switching applications. It is an informative collection of topics offering a “one-stop-shopping” to solve the most common design challenges. Therefore, it should be of interest to power electronics engineers at all levels of experience. The most popular circuit solutions and their performance are analyzed, including the effect of parasitic components, transient and extreme operating conditions. The discussion builds from simple to more complex problems starting with an overview of MOSFET technology and switching operation. Design procedure for ground referenced and high side gate drive circuits, AC coupled and transformer isolated solutions are described in great details. A special section deals with the gate drive requirements of the MOSFETs in synchronous rectifier applications. For more information, see the Overview for MOSFET and IGBT Gate Drivers product page. Several, step-by-step numerical design examples complement the application report. This document is also available in Chinese: MOSFET 和 IGBT 栅极驱动器电路的基本原理 Contents 1 Introduction ................................................................................................................... 2 2 MOSFET Technology ...................................................................................................... -
Tabulation of Published Data on Electron Devices of the U.S.S.R. Through December 1976
NAT'L INST. OF STAND ms & TECH R.I.C. Pubii - cations A111D4 4 Tfi 3 4 4 NBSIR 78-1564 Tabulation of Published Data on Electron Devices of the U.S.S.R. Through December 1976 Charles P. Marsden Electron Devices Division Center for Electronics and Electrical Engineering National Bureau of Standards Washington, DC 20234 December 1978 Final QC— U.S. DEPARTMENT OF COMMERCE 100 NATIONAL BUREAU OF STANDARDS U56 73-1564 Buraev of Standard! NBSIR 78-1564 1 4 ^79 fyr *'• 1 f TABULATION OF PUBLISHED DATA ON ELECTRON DEVICES OF THE U.S.S.R. THROUGH DECEMBER 1976 Charles P. Marsden Electron Devices Division Center for Electronics and Electrical Engineering National Bureau of Standards Washington, DC 20234 December 1978 Final U.S. DEPARTMENT OF COMMERCE, Juanita M. Kreps, Secretary / Dr. Sidney Harman, Under Secretary Jordan J. Baruch, Assistant Secretary for Science and Technology NATIONAL BUREAU OF STANDARDS, Ernest Ambler, Director - 1 TABLE OF CONTENTS Page Preface i v 1. Introduction 2. Description of the Tabulation ^ 1 3. Organization of the Tabulation ’ [[ ] in ’ 4. Terminology Used the Tabulation 3 5. Groups: I. Numerical 7 II. Receiving Tubes 42 III . Power Tubes 49 IV. Rectifier Tubes 53 IV-A. Mechanotrons , Two-Anode Diode 54 V. Voltage Regulator Tubes 55 VI. Current Regulator Tubes 55 VII. Thyratrons 56 VIII. Cathode Ray Tubes 58 VIII-A. Vidicons 61 IX. Microwave Tubes 62 X. Transistors 64 X-A-l . Integrated Circuits 75 X-A-2. Integrated Circuits (Computer) 80 X-A-3. Integrated Circuits (Driver) 39 X-A-4. Integrated Circuits (Linear) 89 X- B. -
Variable Capacitors in RF Circuits
Source: Secrets of RF Circuit Design 1 CHAPTER Introduction to RF electronics Radio-frequency (RF) electronics differ from other electronics because the higher frequencies make some circuit operation a little hard to understand. Stray capacitance and stray inductance afflict these circuits. Stray capacitance is the capacitance that exists between conductors of the circuit, between conductors or components and ground, or between components. Stray inductance is the normal in- ductance of the conductors that connect components, as well as internal component inductances. These stray parameters are not usually important at dc and low ac frequencies, but as the frequency increases, they become a much larger proportion of the total. In some older very high frequency (VHF) TV tuners and VHF communi- cations receiver front ends, the stray capacitances were sufficiently large to tune the circuits, so no actual discrete tuning capacitors were needed. Also, skin effect exists at RF. The term skin effect refers to the fact that ac flows only on the outside portion of the conductor, while dc flows through the entire con- ductor. As frequency increases, skin effect produces a smaller zone of conduction and a correspondingly higher value of ac resistance compared with dc resistance. Another problem with RF circuits is that the signals find it easier to radiate both from the circuit and within the circuit. Thus, coupling effects between elements of the circuit, between the circuit and its environment, and from the environment to the circuit become a lot more critical at RF. Interference and other strange effects are found at RF that are missing in dc circuits and are negligible in most low- frequency ac circuits. -
Oscilators Simplified
SIMPLIFIED WITH 61 PROJECTS DELTON T. HORN SIMPLIFIED WITH 61 PROJECTS DELTON T. HORN TAB BOOKS Inc. Blue Ridge Summit. PA 172 14 FIRST EDITION FIRST PRINTING Copyright O 1987 by TAB BOOKS Inc. Printed in the United States of America Reproduction or publication of the content in any manner, without express permission of the publisher, is prohibited. No liability is assumed with respect to the use of the information herein. Library of Cangress Cataloging in Publication Data Horn, Delton T. Oscillators simplified, wtth 61 projects. Includes index. 1. Oscillators, Electric. 2, Electronic circuits. I. Title. TK7872.07H67 1987 621.381 5'33 87-13882 ISBN 0-8306-03751 ISBN 0-830628754 (pbk.) Questions regarding the content of this book should be addressed to: Reader Inquiry Branch Editorial Department TAB BOOKS Inc. P.O. Box 40 Blue Ridge Summit, PA 17214 Contents Introduction vii List of Projects viii 1 Oscillators and Signal Generators 1 What Is an Oscillator? - Waveforms - Signal Generators - Relaxatton Oscillators-Feedback Oscillators-Resonance- Applications--Test Equipment 2 Sine Wave Oscillators 32 LC Parallel Resonant Tanks-The Hartfey Oscillator-The Coipltts Oscillator-The Armstrong Oscillator-The TITO Oscillator-The Crystal Oscillator 3 Other Transistor-Based Signal Generators 62 Triangle Wave Generators-Rectangle Wave Generators- Sawtooth Wave Generators-Unusual Waveform Generators 4 UJTS 81 How a UJT Works-The Basic UJT Relaxation Oscillator-Typical Design Exampl&wtooth Wave Generators-Unusual Wave- form Generator 5 Op Amp Circuits -
Common Gate Amplifier
© 2017 solidThinking, Inc. Proprietary and Confidential. All rights reserved. An Altair Company COMMON GATE AMPLIFIER • ACTIVATE solidThinking © 2017 solidThinking, Inc. Proprietary and Confidential. All rights reserved. An Altair Company Common Gate Amplifier A common-gate amplifier is one of three basic single-stage field-effect transistor (FET) amplifier topologies, typically used as a current buffer or voltage amplifier. In the circuit the source terminal of the transistor serves as the input, the drain is the output and the gate is connected to ground, or common, hence its name. The analogous bipolar junction transistor circuit is the common-base amplifier. Input signal is applied to the source, output is taken from the drain. current gain is about unity, input resistance is low, output resistance is high a CG stage is a current buffer. It takes a current at the input that may have a relatively small Norton equivalent resistance and replicates it at the output port, which is a good current source due to the high output resistance. • ACTIVATE solidThinking © 2017 solidThinking, Inc. Proprietary and Confidential. All rights reserved. An Altair Company Circuit Topology • ACTIVATE solidThinking © 2017 solidThinking, Inc. Proprietary and Confidential. All rights reserved. An Altair Company Waveforms Input Voltage Output Voltage • ACTIVATE solidThinking © 2017 solidThinking, Inc. Proprietary and Confidential. All rights reserved. An Altair Company The common-source and common-drain configurations have extremely high input resistances because the gate is the input terminal. In contrast, the common-gate configuration where the source is the input terminal has a low input resistance. Common gate FET configuration provides a low input impedance while offering a high output impedance.