Spin-Coating Waferbumping Fluxes for Semiconductor Assembly 98898
Total Page:16
File Type:pdf, Size:1020Kb
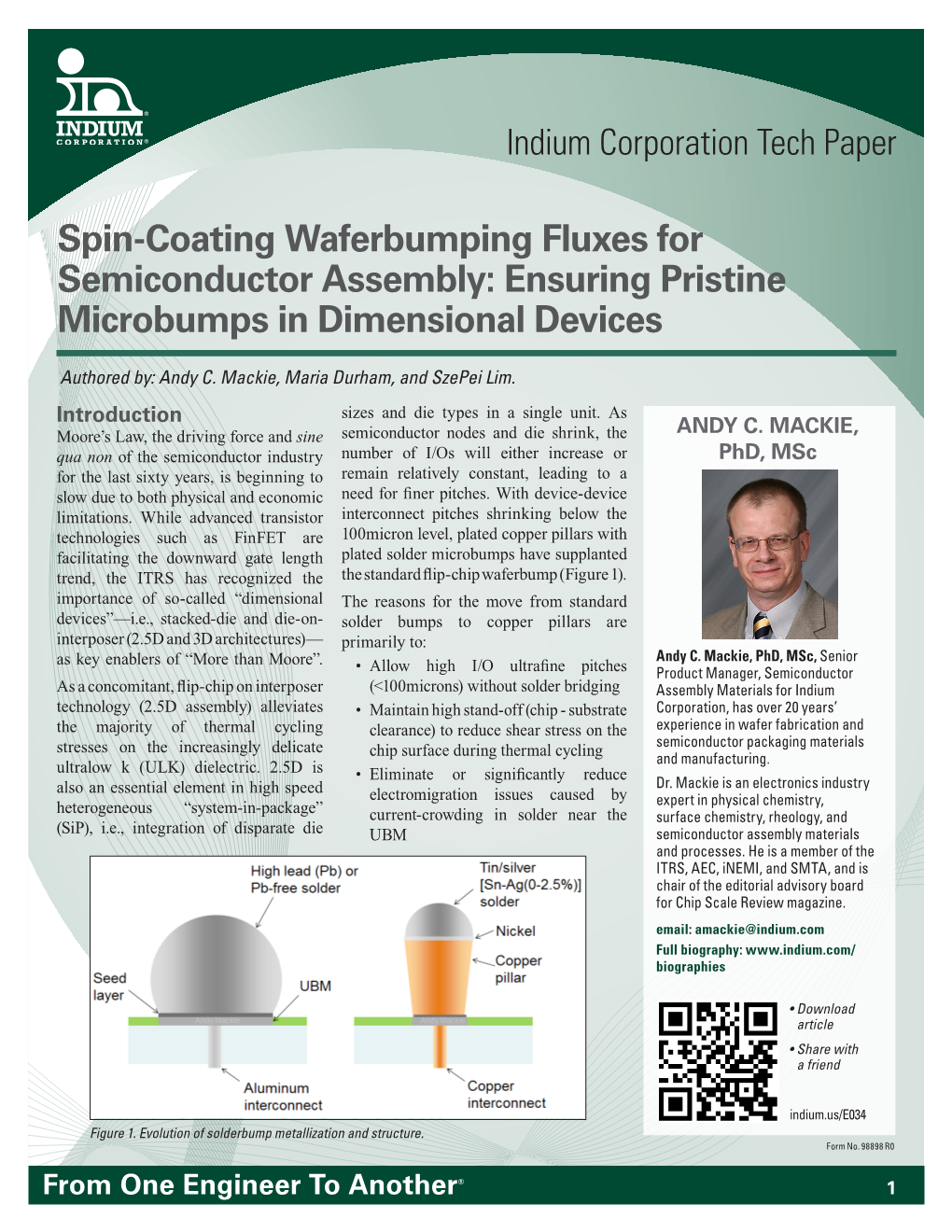
Load more
Recommended publications
-
H1 2015-2016 Results
H1 2015-2016 Results November 2015 Safe Harbour Statement This presentation contains forward-looking statements made pursuant to the safe harbour provisions of the Private Securities litigation reform Act of 1995. By nature, forward looking statement represent the judgment regarding future events and are based on currently available information. Although the Company cannot guarantee their accuracy, actual results may differ materially from those the company anticipated due to a number of uncertainties, many of which the Company is not aware. For additional information concerning these and other important factors that may cause the Company’s actual results to differ materially from expectations and underlying assumptions, please refer to the reports filed by the Company with the Autorité des Marchés Financiers (AMF). Soitec – H1 2015-2016 Results – November 2015 2 Agenda 1 Highlights 2 H1 2015-2016 Financial results 3 Outlook 4 Q&A Appendix: Electronics core business Soitec – H1 2015-2016 Results – November 2015 3 H1 2015-2016 - Core Business highlights Communication and Power – Demand remains robust for RF-SOI products in mobile applications; SOI content continues to grow within smartphones due to increased complexity (number of bands and performance) – Bernin 200mm-diameter wafer capacity is almost sold out for CY 2016 – Simgui (Chinese foundry) produced its first 200mm wafers in October 2015 and is now starting customers qualifications – Customers developing successfully 300mm wafers for RF - at least one major fabless and one foundry -
Multiprocessing Contents
Multiprocessing Contents 1 Multiprocessing 1 1.1 Pre-history .............................................. 1 1.2 Key topics ............................................... 1 1.2.1 Processor symmetry ...................................... 1 1.2.2 Instruction and data streams ................................. 1 1.2.3 Processor coupling ...................................... 2 1.2.4 Multiprocessor Communication Architecture ......................... 2 1.3 Flynn’s taxonomy ........................................... 2 1.3.1 SISD multiprocessing ..................................... 2 1.3.2 SIMD multiprocessing .................................... 2 1.3.3 MISD multiprocessing .................................... 3 1.3.4 MIMD multiprocessing .................................... 3 1.4 See also ................................................ 3 1.5 References ............................................... 3 2 Computer multitasking 5 2.1 Multiprogramming .......................................... 5 2.2 Cooperative multitasking ....................................... 6 2.3 Preemptive multitasking ....................................... 6 2.4 Real time ............................................... 7 2.5 Multithreading ............................................ 7 2.6 Memory protection .......................................... 7 2.7 Memory swapping .......................................... 7 2.8 Programming ............................................. 7 2.9 See also ................................................ 8 2.10 References ............................................. -
HEP Computing Trends
HEP Computing Trends Andrew Washbrook University of Edinburgh ATLAS Software & Computing Tutorials 19th January 2015 UTFSM, Chile Introduction • I will cover future computing trends for High Energy Physics with a leaning towards the ATLAS experiment • Some examples of non-LHC experiments where appropriate • This is a broad subject area (distributed computing, storage, I/O) so here I will focus on the readiness of HEP experiments to changing trends in computing architectures • Also some shameless promotion of work I have been involved in.. Many thanks to all the people providing me with material for this talk! LHC Context Run 2 • Increase in centre of mass energy 13TeV • Increase in pile up from ~20 to ~50 • Increase in Trigger rate up to 1 KHz RAW to ESD • More computing resources required to Reconstruction reconstruct events Time High Luminosity LHC • HL-LHC starts after LS3 (~2022) • Aim to provide 300[-1 per year • Pileup of 150 expected • 200 PB/year of extra storage HL-LHC Timeline CPU Evolution • Die shrink getting smaller • Research down to 5nm depending on lithography and materials • Clock speed improvement has slowed • More cores per socket • Server at the Grid computing centre has at least 16 cores, typically more • Extrapolation from 2013 predicts 25% server performance improvement per year Processor scaling trends 1e+06 Transistors ● Clock Power ● Performance ● Performance/W ● ● ● ● ● ● ●●● ● ● ● ●●● ● ● ●●● ●● ●●●●● ● ● ●●●●● ●●●●●●●●● ●●●● ● ● ●●●● ●●●●●●●● ●●●●●● ● ●● ● ● ●● ● ●●●● ●●●●●●●●●●●● ● ● ● ●● ●●●● ●●●●●●●●●●●●●●●●● -
Drive for Better Vision
Drive for better vision 2011 Annual Report Dear Shareholders, 2011 was a year of transition for Himax as we made significant progress in expanding our sales and customer base for our small and medium-sized driver IC and non-driver businesses. The small-medium driver segment has become our single largest revenue contributor, overtaking the large panel driver business. Revenues from the non-driver businesses exceeded 10% of total revenues in 2011, also the first time in our history. Seeing strong fundamentals across many of our product lines, we are confident that we are in a position to deliver positive revenue and earnings growth in 2012. Our 2011 revenues totaled $633 million, representing a slight 1.5% decline from the previous year due to the drop-off in the large-panel driver category. This was mainly because of our loss of market share in one of our major customers who decided to diversify their driver IC supply base. However, we see significant growth opportunities in China, where panel manufacturers are aggressively expanding their large panel capacity. Small and medium-sized drivers grew strongly in 2011, thanks mainly to phenomenal demand in smartphones, which tend to require better displays and thus higher end driver ICs. We enjoy a strong position in the smartphone sector as a result of our leading technologies, competitive products and solid customer base. We expect the strong growth momentum for small and medium-sized drivers to continue into 2012, driven by growing markets such as smartphones, tablets and displays used in the automotive industry. Non-driver product sales increased even further in 2011 with several product segments experiencing significant shipment and revenue growth from last year. -
Since the Advent of Integrated Circuit Technology in 1958, the Integration Has Been Primarily Monolithic
Opening Keynote #1 Extending Moore’s Law with Advanced Packages Abstract: Since the advent of integrated circuit technology in 1958, the integration has been primarily monolithic. Unfortunately, due to physical and economic reasons, the vast majority of analog chips, digital chips, and memory chips are each built on separate technologies. Therefore, in order to deliver optimum system performance, power, and cost, it is desirable to integrate multiple different die, each using its own optimized technology, in a single package. Advanced packaging technologies, e.g. 3DIC, SSIT(stacked silicon Interconnect technology) etc., have been developed to extend scaling beyond the Moore’s Law to achieve higher transistor count, increased functionality and superior performance. Xilinx is the leading provider of all programmable FPGA (Field Programmable Gate Array) products. To achieve high performance, but low power and cost, Xilinx has developed an innovative SSIT technology that employs microbumps and through-silicon vias (TSVs) to integrate multiple FPGA die slices placed side-by-side on a passive silicon interposer, and successfully delivered the industry’s first 28nm homogeneous SSIT device. This technology is further developed for advanced technical nodes (20nm, 16nm and beyond) to allow integrating heterogeneous components such as Processor, FPGA, GPU, Memory, Serdes, etc. on the same interposer die enabling faster computing through reduced latency. The advance of packaging and assembly technology will be introduced, and the benefits of advanced packaging to the various products will be highlighted. Successful qualification of these products is driving the high growth in the applications e.g. cloud computing, embedded vision, industrial IOT, and 5G wireless etc. -
Unstructured Computations on Emerging Architectures
Unstructured Computations on Emerging Architectures Dissertation by Mohammed A. Al Farhan In Partial Fulfillment of the Requirements For the Degree of Doctor of Philosophy King Abdullah University of Science and Technology Thuwal, Kingdom of Saudi Arabia May 2019 2 EXAMINATION COMMITTEE PAGE The dissertation of M. A. Al Farhan is approved by the examination committee Dissertation Committee: David E. Keyes, Chair Professor, King Abdullah University of Science and Technology Edmond Chow Associate Professor, Georgia Institute of Technology Mikhail Moshkov Professor, King Abdullah University of Science and Technology Markus Hadwiger Associate Professor, King Abdullah University of Science and Technology Hakan Bagci Associate Professor, King Abdullah University of Science and Technology 3 ©May 2019 Mohammed A. Al Farhan All Rights Reserved 4 ABSTRACT Unstructured Computations on Emerging Architectures Mohammed A. Al Farhan his dissertation describes detailed performance engineering and optimization Tof an unstructured computational aerodynamics software system with irregu- lar memory accesses on various multi- and many-core emerging high performance computing scalable architectures, which are expected to be the building blocks of energy-austere exascale systems, and on which algorithmic- and architecture-oriented optimizations are essential for achieving worthy performance. We investigate several state-of-the-practice shared-memory optimization techniques applied to key kernels for the important problem class of unstructured meshes. We illustrate -
High Density Packaging (HDP/MCM) Newsletter
Art of Technology: High Density Packaging (HDP/MCM) Newsletter http://www.art-of-technology.ch/newsletters/newsletter_en_200... Sept/Oct 2003 High Density Packaging (HDP/MCM) Newsletter The quick and affordable way to package your electronic systems, to ensure that they are small, lightweight and robust, with protection against environmental influences. Brought to you by Art of Technology, the leading European HDP/MCM miniaturization specialists. When HDP/MCM makes the most sense • with small to medium size volumes • when there are short development times (4 - 6 months to prototype) • with low development costs • modularity -when many different product variations can be built with just one module Expert Opinions Rao Tumalla, Chair Professor of the Georgia Institute of Technology in Microsystems Packaging, President of the IEEE-CPMT Society "Any way you look at it, HDP/MCM is required in the future because of IC integration issues and higher I/O chips. You are limited by smallest components with finest pitch - both are difficult to achieve,beyond where we are or will be shortly. So HDP/MCM is the only way to go for those products that require either high electrical performance or smaller form factor or both." Ken Gilleo, Editor of the "Area Array Packaging Handbook, Manufacturing and Assembly" "Packaging is the bridge between fast-moving semiconductors and slow moving PWBs and is becoming more important and complex as the gap increases." TABLE OF CONTENTS 1. HDP/MCM Technology Evolutions History of Substrates From wafer to system-in package 2. Application Notes High-Density packaging for wrist-wearable medical devices (PLUS article) High Density Packaging (HDP/MCM) for Mixed-Signal Electronic Systems 3. -
Intel's Atom Lines 1. Introduction to Intel's Atom Lines 3. Atom-Based Platforms Targeting Entry Level Desktops and Notebook
Intel’s Atom lines • 1. Introduction to Intel’s Atom lines • 2. Intel’s low-power oriented CPU micro-architectures • 3. Atom-based platforms targeting entry level desktops and notebooks • 4. Atom-based platforms targeting tablets • 5. Atom-based platforms targeting smartphones • 6. Intel’s withdrawal from the mobile market • 7. References 1. Introduction to Intel’s Atom lines • 1.1 The rapidly increasing importance of the mobile market space • 1.2 Related terminology • 1.3 Introduction to Intel’s low-power Atom series 1.1 The rapidly increasing importance of the mobile market space 1.1 The rapidly increasing importance of the mobile market space (1) 1.1 The rapidly increasing importance of the mobile market space Diversification of computer market segments in the 2000’s Main computer market segments around 2000 Servers Desktops Embedded computer devices E.g. Intel’s Xeon lines Intel’s Pentium 4 lines ARM’s lines AMD’s Opteron lines AMD’s Athlon lines Major trend in the first half of the 2000’s: spreading of mobile devices (laptops) Main computer market segments around 2005 Servers Desktops Mobiles Embedded computer devices E.g. Intel’s Xeon lines Intel’s Pentium 4 lines Intel’s Celeron lines ARM’s lines AMD’s Opteron lines AMD’s Athlon64 lines AMD’s Duron lines 1.1 The rapidly increasing importance of the mobile market space (2) Yearly worldwide sales and Compound Annual Growth Rates (CAGR) of desktops and mobiles (laptops) around 2005 [1] 350 300 Millions 250 CAGR 17% 200 Mobile 150 100 Desktop CAGR 5% 50 0 2003 2004 2005 2006 2007 2008 -
An Overview of Chip Level EMC Problems
An Overview of Chip Level EMC Problems Dr. Sergiu Radu Principal Engineer, EMC Design Sun Microsystems, Inc. Outline • Introduction. EMI mechanisms for VLSI chips • Heatsink effect for large VLSI chips • Back-bias impact on EMI • Integrated and separated power distribution • Noise injection into the PCB • Package level improvements for EMI • Die level improvements for EMI • Second harmonic emissions • Power distribution issues • Spread Spectrum Clock Generation • Die-shrink impact on EMI • Conclusions 2 CPU Radiated Emissions can be a very big problem Open Chassis Emissions for a [email protected]) (older system). Average: 18.6dB over Class A. 3 EMI mechanisms for VLSI chips • The Heatsink acting as a monopole antenna against the first solid plane of the PCB (tall Heatsink). • The Heatsink and the first solid plane of the PCB creating a patch antenna (wide Heatsink). • The low inductance power distribution of the VLSI chip allows noise injection into the PCB, which re-radiate (especially through closely placed DC-DC convertors). 4 The Heatsink as a monopole and cavity resonance 5 (PCI_E Switch - 5GHz) The Heatsink as a monopole and cavity resonance 6 (PCI_E Switch - 5GHz) The Heatsink as a patch antenna Example of heatsink cavity resonances -Compact PCI 7 Cavity Effect for Heatsink Grounding 2 2 2 = i j k f 150 i , j , k L H W 8 Outline • Introduction. EMI mechanisms for VLSI chips • Heatsink effect for large VLSI chips • Back-bias impact on EMI • Integrated and separated power distribution • Noise injection into the PCB • Package level improvements for EMI • Die level improvements for EMI • Second harmonic emissions • Power distribution issues • Spread Spectrum Clock Generation • Die-shrink impact on EMI • Conclusions 9 The typical heatsink grounding Grounding ring and EMI gasket on top layer PCB 10 Example: UltraSPARC IIIe in Sun Ultra 60 Heatsink Actually Grounded 11 Ultra Sparc T2+ CPU Provision for Grounding. -
Technology Roadmap Document for Ska Signal Processing
TECHNOLOGY ROADMAP DOCUMENT FOR SKA SIGNAL PROCESSING Document number .................................................................. WP2‐040.030.011‐TD‐001 Revision ........................................................................................................................... 1 Author ................................................................................................................ W.Turner Date ................................................................................................................ 2011‐02‐27 Status ....................................................................................................................... Issued Name Designation Affiliation Date Signature Additional Authors Submitted by: W. Turner Signal Processing SPDO 2011‐03‐26 Domain Specialist Approved by: P. Dewdney Project Engineer SPDO 2010‐03‐29 WP2‐040.030.011‐TD‐001 Revision : 1 DOCUMENT HISTORY Revision Date Of Issue Engineering Change Comments Number 1 ‐ ‐ First issue DOCUMENT SOFTWARE Package Version Filename Wordprocessor MsWord Word 2007 02‐WP2‐040.030.011.TD‐001‐1_SKATechnologyRoadmap Block diagrams Other ORGANISATION DETAILS Name SKA Program Development Office Physical/Postal Jodrell Bank Centre for Astrophysics Address Alan Turing Building The University of Manchester Oxford Road Manchester, UK M13 9PL Fax. +44 (0)161 275 4049 Website www.skatelescope.org 2011‐02‐27 Page 2 of 71 WP2‐040.030.011‐TD‐001 Revision : 1 TABLE OF CONTENTS 1 INTRODUCTION ............................................................................................ -
Wafer Level Packaging Interconnects: Russ Winslow Wafer Fabrication Vs
Volume 8, Number 2 QUARTER TWO 2004 A Publication of The MicroElectronics Packaging & Test Engineering Council INDUSTRY NEWS WaferWafer LevelLevel ENTEGRIS, INC. has announced that IC PackagingPackaging INTERCONNECT (ICI) has joined the Ente- gris Final Manufacturing Partner program. page 14 Interconnects: STATS CHIPPAC Interconnects: and have announced the signing of a definitive agreement for the companies to merge. page 17 WaferWafer FabricationFabrication vs.vs. PackagePackage AssemblyAssembly Industries Inc OneOne DayDay TechnicalTechnical SymposiumSymposium andand ExhibitsExhibits KULICKE & SOFFA and ASE GROUP an- nounce a strategic relationship between ComingComing toto SantaSanta ClaraClara AugustAugust 19th19th ...... pagepage 55 K&S’s Test Products Group and ASE Test Limited. page 18 MEMBER COMPANY PROFILE TECHNOLOGY ong considered one of the best kept secrets in the Dr. Young Gon Kim of Tessera reviews subcon world, NS Electron- five infrastructure barriers to SiP develop- ment for achieving time-to-market goals, ics Bangkok has developed La strong reputation for high and possible solutions to overcoming those barriers in “Solving SiP Time-to-Market quality, short cycle times, and Challenges”. page 24 excellent customer service. These attributes are the core of an Robert Rowland of RadiSys Corpora- overall strategy by NSEB manage- tion discusses components from a process ment to create a superior subcon engineer’s perspective. page 28 experience for major semiconduc- Kelly Linden and some of his colleagues tor manufacturers worldwide. from Microvision discuss “Wafer Scale Vacuum Packaging of a MEMS Optical Born from the decision of National Semi- Semiconductor equipment bookings increase Scanner”. page 30 conductor to reduce its offshore factory 70% over March 2003 level. -
FDSOI Technology Overview by Nguyen Nanjing Sept 22, 2017 Final
FD-SOI Technology Bich-Yen Nguyen Soitec Agenda 1 FD-SOI technology overview 2 Markets, foundries offers & ecosystems 3 FD-SOI material & roadmap 4 Summary 10/10/20172 SOITEC Confidential FD-SOI technology Challenge of Traditional Planar Bulk Transistor Scaling Source: IBM, T.C. Chen, ISSCC 2006 • Increased standby power dissipation • Amplified V variability th new transistor architectures and ⇒Impact Yield materials are needed ⇒Limit Vdd scaling 10/10/20173 SOITEC Confidential FD-SOI technology Continue Moore Law with New Materials & Device Architectures 2003 2005 2007 2009 2011 2012 Hartmann, GSA12 90nm 45 nm 22nm 65nm 32nm Strained Silicon Introduction of New High-K / Metal Gate Materials Introduction of New Fully Depleted Device Devices Architecture 10/10/20174 SOITEC Confidential FD-SOI technology Leakage Power is still a Major Issue Despite the Use of Hi-K Dielectric High-K/Metal Gate Stack Source: IBS SiON/Poly Gate Stack Technology node Leakage power is still tremendously growing after insertion of the High- K/MG gate stack at 28nm node as demands for more performance and functionality 10/10/20175 SOITEC Confidential FD-SOI technology New Device Architecture: Planar FDSOI or Multi-Gate Transistor Minimum Design Max Disruption scalability G G D SD S Buried OX S G D Bulk Si Bulk Si Buried oxide Conventional Planar Planar Single-or double Multiple-Gate, FinFET or Bulk Transistor Gate FDSOI Nanowire Transistor FDSOI : Fully Depleted Silicon-on Insulator Thin channel (Fully Depleted) with multi gates for better gate or short channel