4A-2 Strained Si Channel Mosfets with Embedded Silicon Carbon
Total Page:16
File Type:pdf, Size:1020Kb
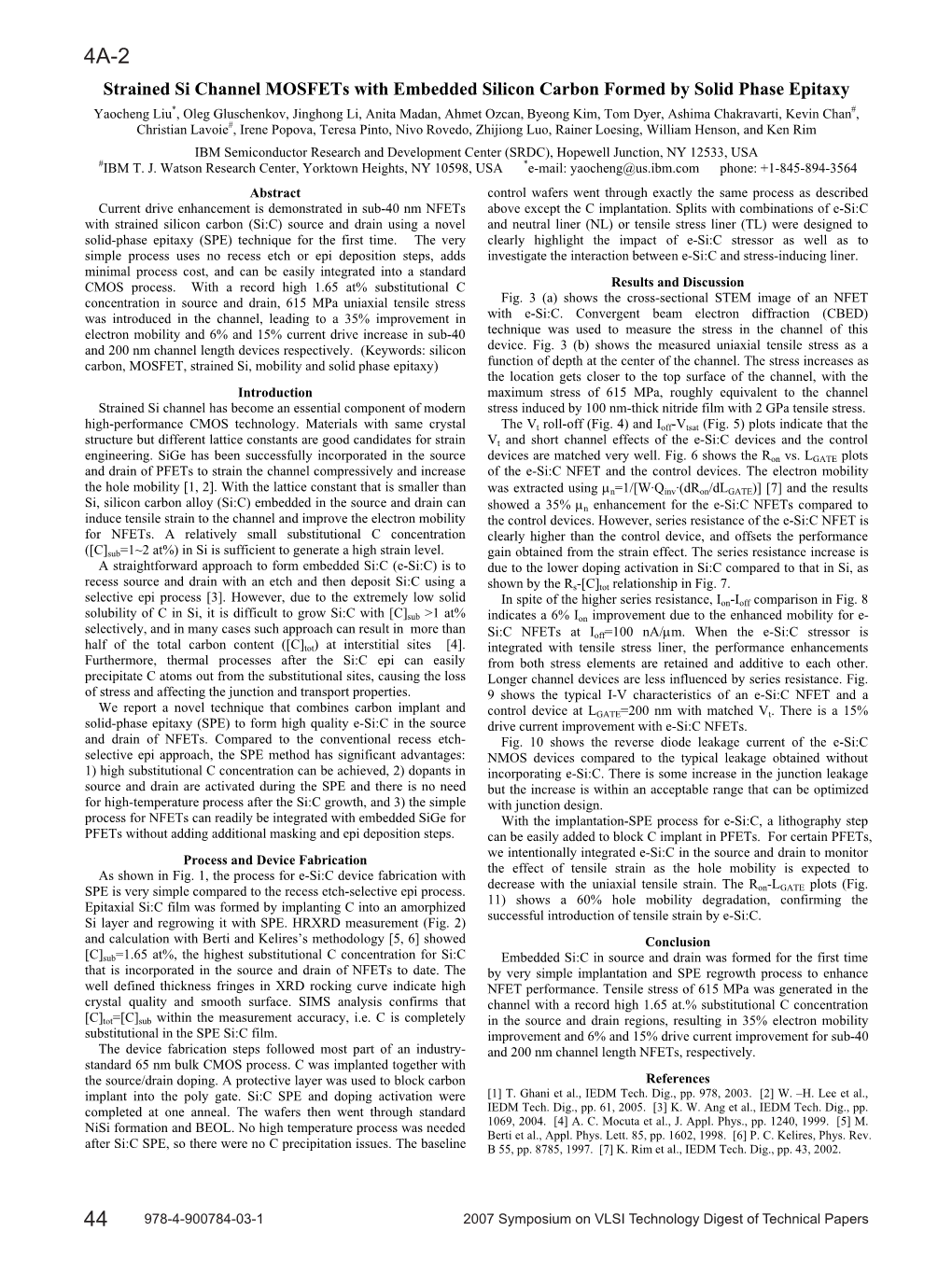
Load more
Recommended publications
-
Strained Silicon Devices M. Reiche , O. Moutanabbir , J. Hoentschel , U
Solid State Phenomena Vols. 156-158 (2010) pp 61-68 Online available since 2009/Oct/28 at www.scientific.net © (2010) Trans Tech Publications, Switzerland doi:10.4028/www.scientific.net/SSP.156-158.61 Strained Silicon Devices M. Reiche 1a , O. Moutanabbir 1b, J. Hoentschel 2c , U. Gösele 1d, S. Flachowsky 2e and M. Horstmann 2f 1 Max Planck Institute of Microstructure Physics, Weinberg 2, D – 06120 Halle, Germany 2 GLOBALFOUNDRIES Fab 1, Wilschdorfer Landstraße 101, D – 01109 Dresden, Germany a [email protected], b [email protected], c [email protected], d [email protected], e stefan.flachowsky@ globalfoundries.com, f [email protected] Keywords: strained silicon, mobility enhancement, process-induced strain, global strain, SSOI. Abstract. Strained silicon channels are one of the most important Technology Boosters for further Si CMOS developments. The mobility enhancement obtained by applying appropriate strain provides higher carrier velocity in MOS channels, resulting in higher current drive under a fixed supply voltage and gate oxide thickness. The physical mechanism of mobility enhancement, methods of strain generation and their application for advanced VLSI devices is reviewed. Introduction The ordinary device scaling was the most important principle of performance enhancement in Si CMOS for more than 30 years. However, starting with 90 nm technologies the performance enhancements of CMOS started to diminish through standard device scaling such as shrinking the gate length and thinning the gate oxide due to several physical limitations in miniaturization of MOSFETs. For example, thinning the gate oxide requires a reduction of the supply voltage and an increase of the gate tunneling current occurs. -
Strained Silicon Layer in CMOS Technology
ELECTRONICS, VOL. 18, NO. 2, DECEMBER 2014 63 Strained Silicon Layer in CMOS Technology Tatjana Pešić-Brđanin, Branko L. Dokić However, the other demands of designing integrated circuits Abstract— Semiconductor industry is currently facing with the with ultra large scale of integration, such as, for example, the fact that conventional submicron CMOS technology is increase in density on the chip and reducing the size of the approaching the end of their capabilities, at least when it comes to chip, have led to the scaling of other transistor dimensions. scaling the dimensions of the components. Therefore, much attention is paid to device technology that use new technological Fig. 1 shows the trend of reducing the gate length that has led structures and new channel materials. Modern technological to the emergence of new technologies [1]. Reducing the gate processes, which mainly include ultra high vacuum chemical length caused a simultaneous scaling of other technological vapor deposition, molecular beam epitaxy and metal-organic parameters, in order to meet the required performances of molecular vapor deposition, enable the obtaining of ultrathin, integrated circuits regarding high speed and low power crystallographically almost perfect, strained layers of high purity. consumption, or the desired degree of integration. However, In this review paper we analyze the role that such layers have in modern CMOS technologies. It’s given an overview of the with recent CMOS technologies, in which the gate length is characteristics of both strain techniques, global and local, with less than 90 nm, this performance improvement becomes more special emphasis on performance of NMOS biaxial strain and difficult due to physical limitations in miniaturization of MOS PMOS uniaxial strain. -
Electron Effective Mobility in Strained Si/Si1-Xgex MOS Devices Using Monte Carlo Simulation
Electron effective mobility in strained Si/Si1-xGex MOS devices using Monte Carlo simulation V. Aubry-Fortuna, P. Dollfus, S. Galdin-Retailleau Institut d'Electronique Fondamentale, CNRS UMR 8622, Bât. 220, Université Paris-Sud, 91405 Orsay cedex, France. E-mail : [email protected] Abstract Based on Monte Carlo simulation, we report the study of the inversion layer mobility in n-channel strained Si/ Si1-xGex MOS structures. The influence of the strain in the Si layer and of the doping level is studied. Universal mobility curves µeff as a function of the effective vertical field Eeff are obtained for various state of strain, as well as a fall-off of the mobility in weak inversion regime, which reproduces correctly the experimental trends. We also observe a mobility enhancement up to 120 % for strained Si/ Si0.70Ge0.30, in accordance with best experimental data. The effect of the strained Si channel thickness is also investigated: when decreasing the thickness, a mobility degradation is observed under low effective field only. The role of the different scattering mechanisms involved in the strained Si/ Si1-xGex MOS structures is explained. In addition, comparison with experimental results is discussed in terms of SiO2/ Si interface roughness, as well as surface roughness of the SiGe substrate on which strained Si is grown. Keywords strained Si, effective mobility, Monte Carlo simulation, MOSFET PACS codes 72.20.Dp, 72.20.Fr, 85.30.Tv -1- 1. Introduction The use of strained-Si channel pseudomorphically grown on a SiGe virtual substrate is becoming a promising way to accelerate the improvement of CMOS performance. -
Sige CVD, Fundamentals and Device Applications
SiGeSiGe CVD,CVD, fundamentalsfundamentals andand devicedevice applicationsapplications DrDr DerekDerek HoughtonHoughton AixtronAixtron IncInc ICPS,ICPS, FlagstaffFlagstaff JulyJuly 20042004 . OVERVIEW 1.1. Introduction Introduction 2.2. SiGe SiGe Market Market SurveySurvey 3.3. Fundamentals Fundamentals ofof SiGeSiGe CVDCVD 4.4. CVD CVD EquipmentEquipment forfor SiGeSiGe 5.5. Device Device aplicationsaplications andand commercializationcommercialization 6.6. SiGe SiGe materialsmaterials engineering,engineering, metrologymetrology 7.7. Summary Summary and and DiscussionDiscussion SiGe’s Market Opportunity... Si CMOS/BJTs SiGe HBTs/CMOS? III-V FETs/HBTs Automotive Road Collision Pricing Avoidance Navigation/Areospace GPS x-band Radar Communications GSM DCS ISM DECT FRA WLAN DTH WLAN OC-48 DBS FRA G-Ethernet OC-192 LMDS 0.1 0.2 0.5 1 2 5 10 20 50 100 Frequency (GHz) SiGe HBT device structure and process description KeyKey figures figures of of SiGe SiGe HBT HBT process process •• SiGe SiGe BiCMOSBiCMOS uses uses SiGeSiGe HBT HBT ++ SiSi CMOSCMOS •• SiGe SiGe HBT HBT showsshows samesame processprocess asas SiSi BT BT withwith exceptionexception ofof 30-8030-80 nmnm thinthin SiGeSiGe base base layerlayer (Ge(Ge <25%) <25%) •• Growth Growth ratesrates usedused areare aboutabout 3030 nm/minnm/min (~(~ 22 minmin forfor basebase layer)layer) •• Typically, Typically, samesame LPCVDLPCVD growthgrowth chamberschambers cancan depositedeposite both both SiSi and and SiGeSiGe layers layers Only difference: Base SiGe replaces Silicon •• Depending Depending -
Challenges and Innovations in Nano‐CMOS Transistor Scaling
Challenges and Innovations in Nano‐CMOS Transistor Scaling Tahir Ghani Intel Fellow Logic Technology Development October, 2009 Nikkei Presentation 1 Outline • Traditional‐Scaling ‐ Traditional Scaling Limiters, Device Implications ‐ Intel’s Response • Post “Traditional‐Scaling” Innovations ‐ Mobility Booster: Uniaxial Strain - Poly Depletion Elimination: Metal Gate - Gate Leakage Reduction: HiK • Future Challenges and Options - Power Limitation - Potential New Transistor Structures and Materials 40+ Years of Moore’s Law at INTEL: From Few to Billions of Transistors 2X transistors every 2 years Transistor Count has Doubled Every Two Years 40+ Years of Moore’s Law at INTEL: From Few to Billions of Transistors 2X transistors every 2 years Traditional Scaling Era END OF TRADITIONAL SCALING ERA ~ 2003 Lasted ~40 YEARS Top “Traditional-Scaling” Enablers R. Dennard et.al. IEEE JSSC, 1974 • Gate Oxide Thickness Scaling - Key enabler for Lgate scaling • Junction Scaling - Another enabler for Lgate scaling - Improved abruptness (REXT reduction) • Vcc Scaling - Reduce XDEP (improve SCE) - However, did not follow const E field 1990’s: Golden Era of Scaling Vcc, Tox & Lg scaling & increasing Idsat Year 2000: INTEL 90nm CMOS Pathfinding End of “Traditional-Scaling” Era Gate oxide running Mobility degrades out of atoms with scaling 1.E+04 Jox limit VLSI Symp. 2000 300 Universal 1.E+03 NA= Mobility 3x1017 ] 1.E+02 SiO 250 2 2 /(V.s) [Lo et. al, EDL97] 2 1.E+01 18 200 1.3x10 [A/cm 130nm 1.E+00 1.8x1018 OX J 1.E-01 18 150 2.5x10 18 1.E-02 Nitrided SiO2 180nm 3.3x10 1.E-03 Mobility (cm 100 0.51.01.52.02.5 0 0.5 1 1.5 TOX Physical [nm] E EFF [MV/cm] • Gate Oxide Leakage • Universal Mobility Model direct tunneling limited • Ionized impurity scattering T. -
Elastic Strain Engineering in Silicon and Silicon-Germanium Nanomembranes
Elastic Strain Engineering in Silicon and Silicon-Germanium Nanomembranes By Deborah Marie Paskiewicz A dissertation submitted in partial fulfillment of the requirements for the degree of Doctor of Philosophy (Materials Science) at the UNIVERSITY OF WISCONSIN-MADISON 2012 Date of final oral examination: 11/14/12 The dissertation is approved by the following members of the Final Oral Committee: Max G. Lagally, Professor, Materials Science and Engineering Mark A. Eriksson, Professor, Physics Thomas F. Kuech, Professor, Chemical and Biological Engineering Paul G. Evans, Associate Professor, Materials Science and Engineering Irena Knezevic, Associate Professor, Electrical and Computer Engineering ©Copyright by Deborah Marie Paskiewicz 2012 All Rights Reserved i Abstract Elastic Strain Engineering in Silicon and Silicon-Germanium Nanomembranes Deborah M. Paskiewicz Under the supervision of Professor Max G. Lagally At the University of Wisconsin-Madison Strain in crystalline materials alters the atomic symmetry, thereby changing materials properties. Controlling the strain (its magnitude, direction, extent, periodicity, symmetry, and nature) allows tunability of these new properties. Elastic strain engineering in crystalline nanomembranes (NMs) provides ways to induce and relax strain in thin sheets of single- crystalline materials without exposing the material to the formation of extended defects. I use strain engineering in NMs in two ways: (1) elastic strain sharing between multiple layers using the crystalline symmetry of the layers to induce unique strain distributions, and (2) complete elastic relaxation of single-crystalline alloy NMs. In both cases, NM strain engineering methods enable the introduction of unique strain profiles or strain relaxation in ways not compatible with conventional bulk processing, where strain destroys the long-range crystallinity. -
MOSFET Channel Engineering Using Strained Si, Sige, and Ge Channels
MOSFET Channel Engineering using Strained Si, SiGe, and Ge Channels Eugene A. Fitzgerald, Minjoo L. Lee, Christopher W. Leitz, and Dimitri A. Antoniadis* Dept of Materials Science and Engineering, MIT, Cambridge, MA 02139, *Dept of Electrical Engineering and Computer Science, MIT, Cambridge, MA 02139 Ge, saturating at roughly 80% enhancement.[7] For strained Abstract—Biaxial tensile strained Si grown on SiGe virtual Si on virtual substrates with greater than 20% Ge content, the substrates will be incorporated into future generations of CMOS subband splitting in the conduction band is large enough to technology due to the lack of performance increase with scaling. completely suppress intervalley scattering (figure 1a). Holes Compressively strained Ge-rich alloys with high hole mobilities also have increased mobility in strained Si due to subband can also be grown on relaxed SiGe. We review progress in splitting (figure 1b); however, greater strain levels in the strained Si and dual channel heterostructures, and also introduce strained Si are required to achieve the same hole mobility high hole mobility digital alloy heterostructures. By optimizing growth conditions and understanding the physics of hole and enhancement as achieved for electrons. Unlike electrons, the electron transport in these devices, we have fabricated nearly in-plane and out-of-plane mobility of holes in strained Si also symmetric mobility p- and n-MOSFETs on a common Si0.5Ge0.5 increases, resulting in a more complicated picture of hole virtual substrate. transport. Fig. 2 shows the carrier mobility enhancement factors for electrons and holes as a function of Ge Index Terms—SiGe, strained silicon, germanium, MOSFETs, concentration in the relaxed Si1-xGex. -
Thin Film Deposition
Thin film deposition 1. Introduction to thin film deposition. 2. Introduction to chemical vapor deposition (CVD). 3. Atmospheric Pressure Chemical Vapor Deposition (APCVD). 4. Other types of CVD (LPCVD, PECVD, HDPCVD…). 5. Introduction to evaporation. 6. Evaporation tools and issues, shadow evaporation. 7. Introduction to sputtering and DC plasma. 8. Sputtering yield, step coverage, film morphology. 9. Sputter deposition: reactive, RF, bias, magnetron, collimated, and ion beam. 10. Deposition methods for thin films in IC fabrication. 11. Atomic layer deposition (ALD). 12. Pulsed laser deposition (PLD). 13. Epitaxy (CVD or vapor phase epitaxy , molecular beam epitaxy). 1 Common deposition methods for thin films in IC fabrication Epitaxial silicon deposition Advantages of epitaxial wafers over bulk wafers • Offers means of controlling the doping profile (e.g. lightly doped on heavily doped possible) • Epitaxial layers are generally oxygen and carbon free Gases used iin siilliicon epiittaxy Chemical reactions Concentration o of species at different positions along a horizontal reactor (carrier gas should be H2) SiCl4 + 2H2 Si + 4HCl SiCl4 concentration decreases while the other three constituents (SiHCl3, SiH2Cl2, HCl) increase. Equipment Three basic reactor configurations • Weight 2000 Kg • Occupy 2m2 or more of floor space. • Quartz reaction chamber with susceptors • Graphite susceptors for physical support. • A coating of silicon carbide (50 to 500 μm) applied by CVD process on susceptors. • RF heating coil or tungsten halogen lamps (cold wall), water cooling. Si APCVD epitaxy growth process • Hydrogen gas purges of air from the reactor. • Reactor is heated to a temperature. • After thermal equilibrium, an HCl etch takes place at 1150oC and 1200oC for 3 minutes. -
Chasing Moore's Law with 90-Nm
Chasing Moore’s Law with 90-nm: More Than Just a Process Shrink By Ray Simar, Manager of Advanced DSP Architecture In the electronics industry, the term “process shrink” is often used to refer to when a semiconductor company migrates an existing design to a smaller process technology. In many cases, this is an upgrade path for reducing the cost, size, and power con- sumption of chips. An example of a “simple” process shrink is that of Texas Instruments’ 720-MHz TMS320C6416 DSP. Moving the C6416 DSP from a 130-nm CMOS process to 90-nm resulted in a price reduction of 50 percent. If this were the end of the story, it would still be impressive. However, this only describes a single facet of the changes that must come when a new process technolo- gy is introduced. A process shrink alone will not enable you to keep pace with Moore’s Law. To achieve the greatest gains, it is necessary to innovate in several dimensions simultaneously. To only claim the advantages of a smaller die is to ignore the new lev- els of SoC integration enabled by finer geometries. The real excitement starts when designers are able to integrate divergent technologies in ways never before possible. More than Just Faster and Cheaper As chips clock faster and faster internally, the process technology, which defines the distance between transistors, becomes a limiting factor. To achieve even greater speeds, either the distance between gates must be further reduced or new architec- tures developed. With the move to 90-nm, TI was able to manufacture a production-quality C6416 DSP running at 1 GHz. -
Characterization and Fabrication of 90Nm Strained Silicon PMOS Using TCAD
INTERNATIONAL JOURNAL OF ELECTRICAL AND ELECTRONIC SYSTEMS RESEARCH, VOL.5 UNE 2012 Characterization and Fabrication of 90nm Strained Silicon PMOS using TCAD M. A. Abd Hamid and F. Sulaiman, Member, IEEE Abstract —The paper focuses on the enhancement of growth of the information technology and semiconductor conventional 90nm PMOS using graded silicon germanium layer industry. Strained silicon is one of those rare new (SiGe) within the channel and bulk of semiconductor. The technologies that enables a fairly dramatic increase in performance of conventional 90nm PMOS and 90nm PMOS performance with a relatively simple change in starting with silicon germanium layer was compared. A process materials. Proof that transistors fabricate PMOS with simulation of Strained Silicon PMOS and its electrical characterization was done using Silvaco TCAD tool. The strained silicon were faster due to increased electron mobility analysis focused on Id-Vg and Id-Vd characteristic, and hole and velocity was first demonstrated in the mid-1980s. Then, mobility changes. With the Germanium concentration of 35%, in 1998, researchers showed it would work with leading-edge, the threshold voltage Vt for the strained Si and conventional sub-100 nm short-channel transistors. Today, companies such PMOS is -0.228035V and - 0.437378V respectively. This as Intel, IBM, Hitachi, AMD and UMC have reported success indicates that the strained silicon had lower power consumption. with strained silicon. In addition, the output characteristics obtained for Strain Strained silicon works by growing a thin layer of silicon on Silicon PMOS showed an improvement of the drain current as top of a layer of silicon germanium. -
Performance Evaluation of Strained Si/Sige N-Channel Mosfet
International Journal of Engineering Research & Technology (IJERT) ISSN: 2278-0181 Vol. 1 Issue 9, November- 2012 Performance Evaluation Of Strained Si/Sige N-Channel Mosfet 1 Rakhi Sharma, 2 Ajay Kumar Yadav, 3 Dr.D.B.Ojha, 4Vishal Upmanu Mewar University, Chittorgarh (Raj.) functional form and lends itself to efficient computation. Concept of strained silicon and ABSTRACT effects due to germanium concentration in device parameters are also studied in this work Strained Si/SiGe n-channel MOSFET has tremendous Electronics, and in particular the applications in biomedical field. The modern integrated circuit has made possible the design of communication world is also taking interest to use powerful and flexible processors which provide strained Si/SiGe n-channel MOSFET in its highly intelligent and adaptable devices for the applications because of high speed of operation user. Integrated circuit memories fabricated by using MOS (Metal-Oxide-Semiconductor) INTRODUCTION technology have provided the essential elements to complement these processors and, together Electronics is characterized by with a wide range of logic and analog integrated reliability, low power dissipation, circuitry. N MOS technology has an important role extremely low weight and volume, and in IC fabrication. Works are going on to improve low cost, coupled with an ability to the performance of n MOSFETs. Device scaling cope easily with a high degree of which was a major driving force in the sophistication and complexity. development of high density ICs is facing a numberIJERT Electronics, and in particular the of obstacles, making it very difficult to sustain the IJERT integrated circuit has made possible the trend of device performance improvements. -
Stress Modeling of Nanoscale Mosfet
STRESS MODELING OF NANOSCALE MOSFET By NIRAV SHAH A THESIS PRESENTED TO THE GRADUATE SCHOOL OF THE UNIVERSITY OF FLORIDA IN PARTIAL FULFILLMENT OF THE REQUIREMENTS FOR THE DEGREE OF MASTER OF SCIENCE UNIVERSITY OF FLORIDA 2005 Copyright 2005 by Nirav Shah This work is dedicated to my parents for their unconditional love and support, and without whom, I could not have achieved what I have. ACKNOWLEDGMENTS First and foremost, I would like to thank my advisor, Dr. Scott E. Thompson, for all the support, encouragement and assistance he has given me throughout my graduate studies, and for the opportunity to work with him in the SWAMP group. Despite being really busy, he always found time for his students to discuss research and other technical deliberations. I will always adore his innovative thinking and diligent commitment to research, which I tried to imbibe during my work tenure. I am also very grateful to Dr. Mark E. Law and Dr. William R. Eisenstadt for supporting my research activities and for their guidance and support as my supervisory committee. This research could not have been completed without the financial support of the Semiconductor Research Corporation and Applied Materials Inc. I would like to thank the University of Florida and Department of Electrical and Computer Engineering for giving me an opportunity to explore the wide horizons of the technical arena. I would like to thank the SWAMP group and all its members for their warm support during my research. I appreciate the efforts of Teresa Stevens for being an excellent program assistant. I am grateful to Russ Robison for his assistance to get me acquainted with FLOOPS and his continuous support thereafter.