Page 1 of 54
Total Page:16
File Type:pdf, Size:1020Kb
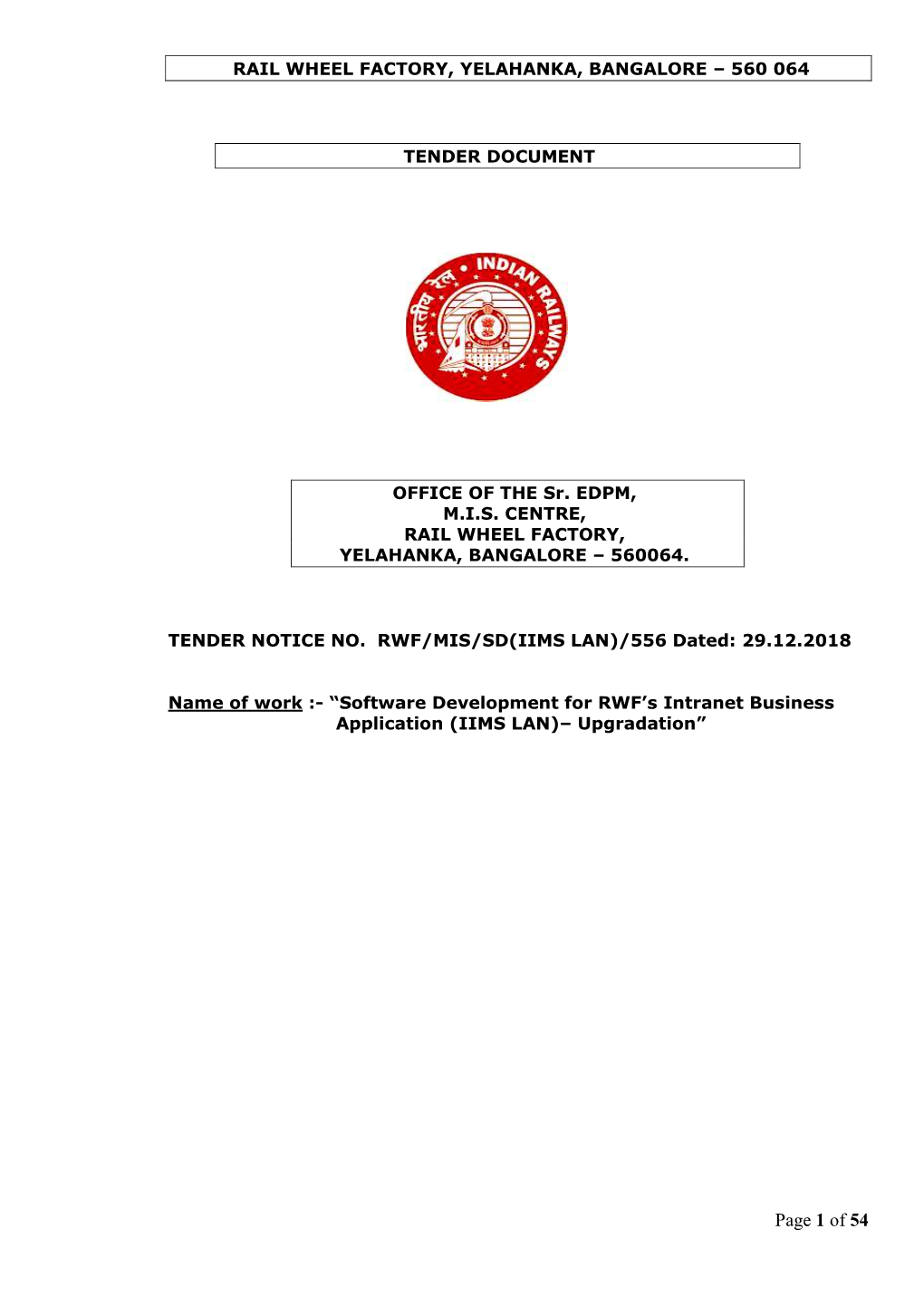
Load more
Recommended publications
-
November, 2015 Issue of Integral News
From: ICF Staff Club To frAG129/18, VII Main Rd AnnaNagar,Chennai-40 ---------------------------------------- ----------------------------------- -------------------------------------------------------------------------------------------------------------------------------------- Issue# 121 Free Monthly News Bulletin – for Internal Circulation November 2015 Email: [email protected] Contact: 900 314 1464, 9539, 9659, 9731, Rly 46490, 47661 Chief Editor: K.Ravi, SSE/Shop80 Associate Editors: M.A.Jaishankar, SSE/Proj A.R.S.Ravindra, SSE/Proj Treasurer:R.Mehalan, SE/IT Shell Offices: R.Thilak, Tech Trainee S.K.Satishkumar, SSE/Proj K.Sekar, Ch.OS/Engg N.Jeganivasan, Stores Inspector N.Ganesh,SSE/MPO/S S.Ghatikachalarao,SSE/WS th N.Devaraju, SSE/Plant Shri Ashok K Agarwal, GM, administering Vigilance Pledge on 26 Oct. V.Sasikala, OS/PB B.Jayalalitha, Accts Asst Shell Shops: P.Baskaran, SSE/40 A-shed: R.Nagarajan,, SSE/10 B-shed: A.V.Gopalakrishna, SSE/22 Shop 24,25,26: N.Ravikumar, SSE/26 D&L-shed:P.T.Sreevalsan, SSE/13 40,J,E: R.Lakshminarayanan, SSE/40 48,RPF: R.Senthilnathan,SSE48 11,23,41,TS:R.Jegathiswaran,SSE/41 Insp: J.Ananthakumar,SSE/42 Progress: P.K.Panda,SSE/PCO CMT: G.Sivakumar, CMS-1 Electrical:D.T.Vijayaraj,SSE/45 Stores : K.Sundar, OS/RB1/SD Fur Offices:Harikumar.NV,SSE/MPO Accts: Sudharsan.MN,SSO/Accts PlgF,TS: G.V.Ramesh,SSE/TS/F Stores:V.Annamalai,OS/P7 Fur Shops: R.Sundarrajan,SSE/30 30: Bipinkumar Karn, SSE/30 32,34: P.Sathyanarayanan, SSE/PC32 GM visiting ICF stall in International Railway Equipment Exhibition -
Government of India Ministry of Railways Lok Sabha
GOVERNMENT OF INDIA MINISTRY OF RAILWAYS LOK SABHA UNSTARRED QUESTION NO.5079 TO BE ANSWERED ON 24.07.2019 CORPORATIZATION OF PRODUCTION UNITS †5079. SHRI DEEPAK BAIJ: SHRI SU.THIRUNAVUKKARASAR: Will the Minister of RAILWAYS be pleased to state: (a) whether the Government is considering to corporatise some production units of Railways and if so, the details thereof; (b) whether these are currently unable to function according to their capacity; (c) if so, whether some changes would be made in the service conditions of those employees if the said units are converted into corporation; (d) the details of those production units which are under consideration for conversion into corporation along with the total number of workers/ labourers currently working in them; and (e) whether these units are in deficit or in profits and if so, the details thereof? ANSWER MINISTER OF RAILWAYS AND COMMERCE & INDUSTRY ( SHRI PIYUSH GOYAL ) (a) to (e) A statement is laid on the Table of the House. ****** STATEMENT REFERRED TO IN REPLY TO PARTS (a) TO (e) OF UNSTARRED QUESTION NO. 5079 BY SHRI DEEPAK BAIJ AND SHRI SU.THIRUNAVUKKARASAR TO BE ANSWERED IN LOK SABHA ON 24.07.2019 REGARDING CORPORATIZATION OF PRODUCTION UNITS. (a) Government has envisaged preparation of an action plan for corporatization of the Rolling Stock Production Units. Existing Production Units are expected to become part of this structure in a phased manner. This is expected to be attended with the following benefits: (i) State-of-the-art technology and modernization (ii) Managerial autonomy (iii) Superior operational efficiency due to better Management practices (iv) Export capability (v) Increase MSME business (vi) Employment generation (vii) Better benefits to employees (viii) Making India an international hub for rolling stock manufacturing. -
Report No.CA 11 of 2009-10 (Railways)
PREFACE The Report for the year ended 31 March 2009 has been prepared in two volumes for submission to the President under Article 151 (1) of the Constitution of India. This volume covers comments arising from audit of the Accounts of Railways for the year 2008-2009 and Appropriation Accounts on Railway Grants for the same year. Other points arising from the test-audit of financial transactions of Railways are also included in Chapters on Earnings, Works and Contract Management, Stores and Assets Management and Other Topics. The audit observations contained in the Report are based on the results of audit conducted during the year 2007-2008 and early part of 2008-2009 as well as the findings of the test-audit conducted in earlier years, which could not be included in the previous Reports. Matters relating to the transactions subsequent to 2008-2009 have been mentioned, where relevant. vi Overview OVERVIEW Chapter 1 – Finances of the Railways - This chapter contains the financial results of revenue operations, plan expenditure, comments on Appropriation Accounts and other financial activities of the Railways. Salient points are: • The gross traffic receipts of Rs.79,861.85 crore registered a growth of 11.35 per cent and the working expenses of Rs.71,839.30 crore rose by 31.91 per cent over the year 2007-08. The net revenue surplus of Rs.4,456.78 crore after payment of dividend to General Revenues declined by 66.82 per cent over the previous year. (Para 1.2). • Net effective rate of dividend after setting off the subsidy from the dividend paid during last five years (2004-09) ranged between 4.18 per cent (2008-09) and 5.37 per cent (2007-08). -
Speech of Shri Lalu Prasad Introducing the Railway Budget 2006-07 on 24Th February 2006
Speech of Shri Lalu Prasad Introducing the Railway Budget 2006-07 On 24th February 2006 1. Mr. Speaker Sir, I rise to present the Budget Estimates 2006-07 for the Indian Railways at a point in time when, there has been a historical turn around in the financial situation of the Indian Railways. Our fund balances have grown to Rs. 11,000 cr and our internal generation, before dividend has also reached a historic level of Rs. 11,000 cr. With this unprecedented achievement, we are striding to realize the Hon’ble Prime Minister’s dream of making Indian Railways the premier railway of the world. Sir, this is the same Indian Railways which, in 2001 had deferred dividend payment, whose fund balances had reduced to just Rs. 350 cr and about which experts had started saying that it is enmeshed a terminal debt trap. You might term this a miracle, but I was confident that : “Mere zunu ka natija zaroor niklega, isee siaah samandar se noor niklega.” 2. Sir, the whole nation can see today that track is the same, railwaymen are the same but the image of Indian Railways is aglow. This has been the result of the acumen, devotion and determination of lakhs of railwaymen. Sir, the general perception so far has been that Railways’ finances cannot be improved without increasing second class passenger fares. But my approach is entirely different. In my view, improvements can only be brought about by raising the quality of services, reducing unit costs and sharing the resultant gain with customers. Therefore, instead of following the beaten path, we decided to tread a new one. -
Download Notice
RAIL WHEEL FACTORY (Ministry of Railways) YELAHANKA, BANGALORE- 560 106 Fax: 080-28460367, Phone: 080-28072924, 28072910, 28072904, 28460394. WEBSITE: www.rwf.indianrailways.gov.in E-Mail: [email protected] MATERIALS MANAGEMENT DIVISION TENDER NOTIFICATION NO.RWF/S/146/2011-12/03 DT. 21.09.2011. Rail Wheel Factory (RWF) is in the field of manufacture of Railway Wheels, Axles and Wheel sets. On behalf of the President of India, Controller of Stores/RWF invites sealed quotations for the following work in the prescribed form, which is obtainable in person on payment of the prescribed amount towards the cost of the tender form (non-refundable) from experienced/reputed contractors in the field: Sl No: 1 2 Tender Number RWF/S/TPT/RT/CONDMENED RWF/S/TPT/RT/SEABORNE/2011-12 AXLES/2011-12 Tender Opening on 24.10.2011 28.10.2011 Scope of Work Transportation of condemned railway Handling, loading and transportation of axles from various railway units within overseas consignments received at Chennai a distance of 501-1000 kms from RWF, Airport/Seaport to RWF, Yelahanka. to RWF, Bangalore. Quantity Upto 250 kgs 66 consignments Above 250 - 500 kgs 5 consignments 500 MT (Five hundred Metric Tonnes Above 500 – 1000 kg 4 consignments only). Above 1000 – 9000 kg 16 consignments Above 9000 kgs 180 MT Slab distance From Chennai Airport/Seaport to RWF. From railway units within a distance of Bangalore. 501-1000 kms from RWF. Estimated `5,02,200/- (Rupees Five lakhs two ` 8,26,250/- (Rupees Eight lakhs twenty tender value thousand two hundred only). six thousand two hundred fifty only). -
Country Or Region
INDIA: Opportunities in the Railway Sector INDIA: Opportunities in the railway sector Page 1 of 6 Shantanu Sarkar Date ( Dec /23 /20 13) ID:# Summary According to the official website of t he Indian Railways (IR) and other published sources, it is the world’s second largest passenger system and the fourth lar gest freight carrier. The IR also operates suburban trains and metro systems in some cities. According to the official India Railway (IR) website and other published sources , e ach day 19,000 trains carry an average of 2.8 million tons of freight and mor e than 23 million people between 7,500 stations in a network spanning 40,389 miles. Nearly two thirds, or 12,000 trains, are for passenger travel while 7,000 are dedicated freight trains . R olling stock totals include approximately 2 30 ,000 freight and 60,0 00 passenger cars. There are currently four thousand diesel and over five thousand electric locomotives in operation plying long haul routes, of which about 32% are electrified . The Indian Railways also operates nine factories which manufacture about 250 electric locomotives , 250 diesel -electric locomotives and 3 ,000 passenger coaches each year for domestic use as well as for export. In addition, it produces ‘ traction motors, switch gears and control gears, cast & fabricated bogies, cast steel railroad w heels and forged axles ’. The Indian R ailways use s several gauges including 1,676 mm (5 ft 6 in) broad gauge; 1,435 mm (4 ft 8 1 ⁄2 in) standard gauge; the 1,000 mm (3 ft 3 3⁄8 in) meter gauge; and two narrow gauges, 762 mm (2 ft 6 in) and 610 mm (2 ft). -
Yelahanka, Bengaluru–560 064, Karnataka, India
RWF_Global Tender Document_2016_Page 1 of 77 RAIL WHEEL FACTORY GOVERNMENT OF INDIA (BHARAT SARKAR) INDIAN RAILWAYS YELAHANKA, BENGALURU–560 064, KARNATAKA, INDIA. WEB ADDRESS:www.rwf.indianrailways.gov.in Fax: 91-080-28460367 Phone:91-080-28460394, 28566479, 28072741 WEB MAIL IDs: [email protected], [email protected], [email protected] BID DOCUMENT FOR GLOBAL TENDERS (WITH EFFECT FROM 31.08.2016) Global Tender No: __________________ Due Date:_______________ For the supply of: __________________________________________________________ _______________________________________________________ Time of Closing : 14.15 Hours (IST) Time of Opening: 14.30 Hours (IST) Bid Guarantee / Earnest Money Deposit amount in Rs.: (to be indicated in words and figures) _________________________________________________________________________________ Book No:_______________ Bid Document Price in Rs. (to be indicated in words and figures) ________________________________________________________ Issued to M/s ____________________________________________________ ____________________________________________________ ____________________________________________________ FOR CONTROLLER OF STORES RWF_Global Tender Document_2016_Page 2 of 77 1. QUALITY POLICY To achieve and maintain excellence in quality in the manufacture of wheels, axles and wheel-sets conforming to the requirement of our customers and to strive for continuous improvement. 2. ENVIRONMENTAL POLICY Rail Wheel Factory (RWF) has secured ISO: 14001 certification for its Environment Management System. We request our esteemed suppliers to kindly make all endeavors to adopt eco-friendly processes and packing material with regard to the products manufactured in general and in particular for the items manufactured for use by RWF. 3. SPECIAL NOTE Rail Wheel Factory is an ISO:9001, ISO:14001-2004 and OHSAS:18001-1999 certified organisation. RWF will appreciate if the tenderers also comply with the requirements of these standards while dealing with RWF. -
Indian Railways Annual Report & Accounts 2018-19
INDIAN RAILWAYS ANNUAL REPORT & ACCOUNTS 2018-19 (With highlights of the performance for 2019-20) Price : ` 225 Bharat Sarkar Published by Directorate of Statistics and Economics Government of India Ministry of Railways (Railway Board), Government of India, New Delhi Rail Mantralaya Ministry of Railways (Railway Board) INDIAN RAILWAYS ANNUAL REPORT & ACCOUNTS 2018-19 (With highlights of the performance for 2019-20) BHARAT SARKAR GOVERNMENT OF INDIA RAIL MANTRALAYA MINISTRY OF RAILWAYS (RAILWAY BOARD) Contents Organization Structure 2 Welfare, Development and 94 Empowerment of Women Apex Management 3 Review–Prospects 5 Facilities to Persons with 95 Disabilities Finance 8 Security 98 Freight Operation 14 Vigilance 102 Passenger Business 18 Promoting Hindi 104 Planning 35 North Eastern Region 106 Engineering 37 Public Relations 112 Railway Electrification 42 Railway Engineers Regiments 114 (Territorial Army) Signal and Telecom 51 Undertakings and other 117 Organizations Safety 56 Advisory Boards 143 Rolling Stock 62 Important Events 144 Material Management 70 Glossary 148 Research and Development 72 Summary of Audit Observations 150 provided by C & AG and ATNs Managing the Environment 77 Financial Statements and 153 Operating Statistics Personnel 85 ORGANIZATION STRUCTURE OF INDIAN RAILWAYS MINISTER OF RAILWAYS MINISTER OF STATE OF RAILWAYS RAILWAY BOARD CHAIRMAN RAILWAY BOARD MEMBER MEMBER FINANCIAL STAFF TRAFFIC COMMISSIONER MEMBER MEMBER MEMBER MEMBER MEMBER TRACTION S&T ROLLING ENGINEERING MATERIALS STOCK MANAGEMENT DIRECTOR GENERAL/RHS DIRECTOR GENERAL/ RPF SECRETARY, RAILWAY BOARD CPSE/CORP & ZONAL RAILWAYS PRODUCTION UNITS OTHER UNITS AUTONOMOUS BODIES/ (OPEN LINE) AUTHORITIES GENERAL MANAGERS GENERAL MANAGERS GENERAL MANAGERS BCL 1. CENTRAL BSCL CHITTARANJAN CENTRAL ORGANIZATION FOR 2. EASTERN LOCOMOTIVE WORKS RAILWAY ELECTRIFICATION BWEL 3. -
Indian Railways Annual Report & Accounts 2016-17
INDIAN RAILWAYS ANNUAL REPORT & ACCOUNTS 2016-17 (With highlights of the performance for 2017-18) Price : ` 150 Bharat Sarkar Government of India Rail Mantralaya Published by Directorate of Statistics and Economics Ministry of Railways Ministry of Railways (Railway Board), Government of India, New Delhi (Railway Board) INDIAN RAILWAYS ANNUAL REPORT & ACCOUNTS 2016-17 (With highlights of the performance for 2017-18) BHARAT SARKAR GOVERNMENT OF INDIA RAIL MANTRALAYA MINISTRY OF RAILWAYS (RAILWAY BOARD) Contents Organization Structure 2 Welfare, Development and 75 Empowerment of Women Apex Management 3 Review–Prospects 5 Facilities to Persons with 76 Disabilities Finance 8 Security 79 Freight Operation 13 Vigilance 82 Passenger Business 17 Promoting Hindi 84 Planning 27 North Eastern Region 87 Engineering 29 Public Relations 93 Railway Electrification 34 Railway Engineers Regiments 95 (Territorial Army) Signal and Telecom 37 Undertakings and other 97 Organizations Safety 42 Advisory Boards 125 Rolling Stock 50 Important Events 126 Material Management 56 Glossary 129 Research and Development 58 Summary of Audit Observations 131 provided by C & AG and ATNs Managing the Environment 63 Financial Statements and 141 Operating Statistics Personnel 68 ORGANIZation STRUCTURE MINISTER OF RAILWAYS MINISTER OF state OF railways (S) MINISTER OF state OF railways (G) railway BOARD CHAIRMAN railway BOARD MEMBER MEMBER MEMBER MEMBER MEMBER FINANCIAL TRAFFIC Staff ENGINEERING TRACTION ROLLING StoCK COMMISSIONER SECretary DIRECtor GENERAL/RHS DIRECtor GENERAL/S&T -
Download Notice
RAIL WHEEL FACTORY (Ministry of Railways) YELAHANKA, BANGALORE- 560 106 Fax: 080-28460367, Phone: 080-28072924, 28072910, 28072904, 28460394. WEBSITE: www.rwf.indianrailways.gov.in E-Mail: [email protected] MATERIALS MANAGEMENT DIVISION TENDER NOTIFICATION NO.RWF/S/146/2011-12/01 DT. 20.07.2011. Rail Wheel Factory (RWF) is in the field of manufacture of Railway Wheels, Axles and Wheel sets. On behalf of the President of India, Controller of Stores/RWF invites sealed quotations for the following work in the prescribed form, which is obtainable in person on payment of the prescribed amount towards the cost of the tender form (non-refundable) from experienced/reputed contractors in the field: Sl No: 1 2 3 Tender Number RWF/S/TPT/MSF-AXLES/ RWF/S/TPT/RT/WHEELSET/ RWF/S/TPT/RT/CONDEMNED 2011-12 2011-12 WHEEL DISC/ 2011-12 Tender Opening on 24.08.2011 29.08.2011 02.09.2011 Scope of Work Transportation of forged railway Transportation of finished railway Transportation of condemned axles from Metal & Steel Factory wheelsets from RWF, Yelahanka, railway wheel discs from various (MSF), Ishapore to RWF, Bangalore, to various consignees destinations in India to RWF, Yelahanka, Bangalore. in India. Yelahanka, Bangalore. Quantity 9100 MT (Nine thousand one 1500 MT (One thousand five 2700 MT (Two thousand seven hundred Metric Tonnes only). hundred Metric Tonnes only). hundred Metric Tonnes only). Slab distance From destinations within a From MSF, Ishapore to RWF, To consignees within a distance of distance of upto 500 kms from Bangalore. 501 to 1000 kms from RWF. RWF. -
Solar Assisted Power Supply for Rail Coaches M. Shravanth Vasisht
Solar Assisted Power Supply for Rail Coaches M. Shravanth Vasisht, Indian Institute of Science, India Vishal C, Indian Institute of Science, India J. Srinivasan, Indian Institute of Science, India Sheela K. Ramasesha, Indian Institute of Science, India The North American Conference on Sustainability, Energy & the Environment 2014 Official Conference Proceedings Abstract We have examined the feasibility of installing solar photovoltaic modules atop train coaches in India. Most long distance trains of Indian Railways consist of Alstom-LHB (Linke Hofmann Busch) coaches that do not have self-generating systems, making diesel generator cars mandatory to supply the required power for the electrical loads of the coaches. The feasibility of supplementing the diesel generator sets with power from solar photovoltaic modules installed on the coach rooftops has been studied. The area available on the roof of the coach was found to be more than sufficient to meet the electrical lighting load through photovoltaic modules. For the case study, a typical railway route that covers a distance of 1,800 km has been considered. The saving of diesel was around 90,000 litre per year per train-set. The analysis indicates that the return on investment is around 4 years. In addition, this scheme will reduce the CO2 emission by 239 tons per year per train. Indian Railways being the largest railway network of the world, operates 160 LHB trains in a day. Hence a significant savings in Diesel and reduction in CO2 emissions can be achieved. Keywords: Railway, Solar, Renewable, Energy, Transportation, Sustainable iafor The International Academic Forum www.iafor.org Introduction The transportation sector is a major contributor to the global CO2 emission and global warming. -
'The Management Accountant' August 2021
August 2021 VOL 56 NO. 08 Pages - 124 100 INDIAN RAILWAINNOVYSATIVE MEASURES FOR A BETTER TOMORROW Journal of THE INSTITUTE OF COST ACCOUNTANTS OF INDIA (Statutory Body under an Act of Parliament) www.icmai.in 1 PRESIDENT CMA Biswarup Basu [email protected] VICE PRESIDENT CMA P. Raju Iyer [email protected] COUNCIL MEMBERS CMA (Dr.) Ashish Prakash Thae, CMA Ashwinkumar Gordhanbhai Dalwadi, CMA Balwinder Singh, CMA Chiaranjan Chaopadhyay, CMA Debasish Mitra, CMA H. Padmanabhan, CMA (Dr.) K Ch A V S N Murthy, CMA Neeraj Dhananjay Joshi, CMA Papa Rao Sunkara, CMA Rakesh Bhalla, CMA (Dr.) V. Murali, CMA Vijender Sharma, Shri Manmohan Juneja, Shri Vivek Kulkarni, Shri Sushil Behl, CA Mukesh Singh Kushwah, CS Makarand Lele Secretary CMA Kaushik Banerjee [email protected] Senior Director (Studies, Training & Educaon Facilies and Placement & Career Counselling, Advanced Studies) CMA (Dr.) Debaprosanna Nandy SHARE YOUR STORIES WITH THE WORLD [email protected], [email protected], [email protected] Senior Director (Membership) & Banking, Financial Services and Insurance CMA Arup Sankar Bagchi With over 100 titles in print, including Indian and international language [email protected], [email protected] Director (Examinaon) translations, Spenta Multimedia’s expertise to create bespoke coffee Dr. Sushil Kumar Pareek table books is unparalleled. [email protected] Director (Finance) CMA Arnab Chakraborty We pride ourselves on our ability to turn your vision, thoughts and ideas fi[email protected] into luxury coffee table books, both in print and digital formats that Addional Director (Public Relaon, Delhi Office) Dr. Giri Ketharaj preserve the story and artistry of your brand, your work, and your passion.