Paper Technology Journal
Total Page:16
File Type:pdf, Size:1020Kb
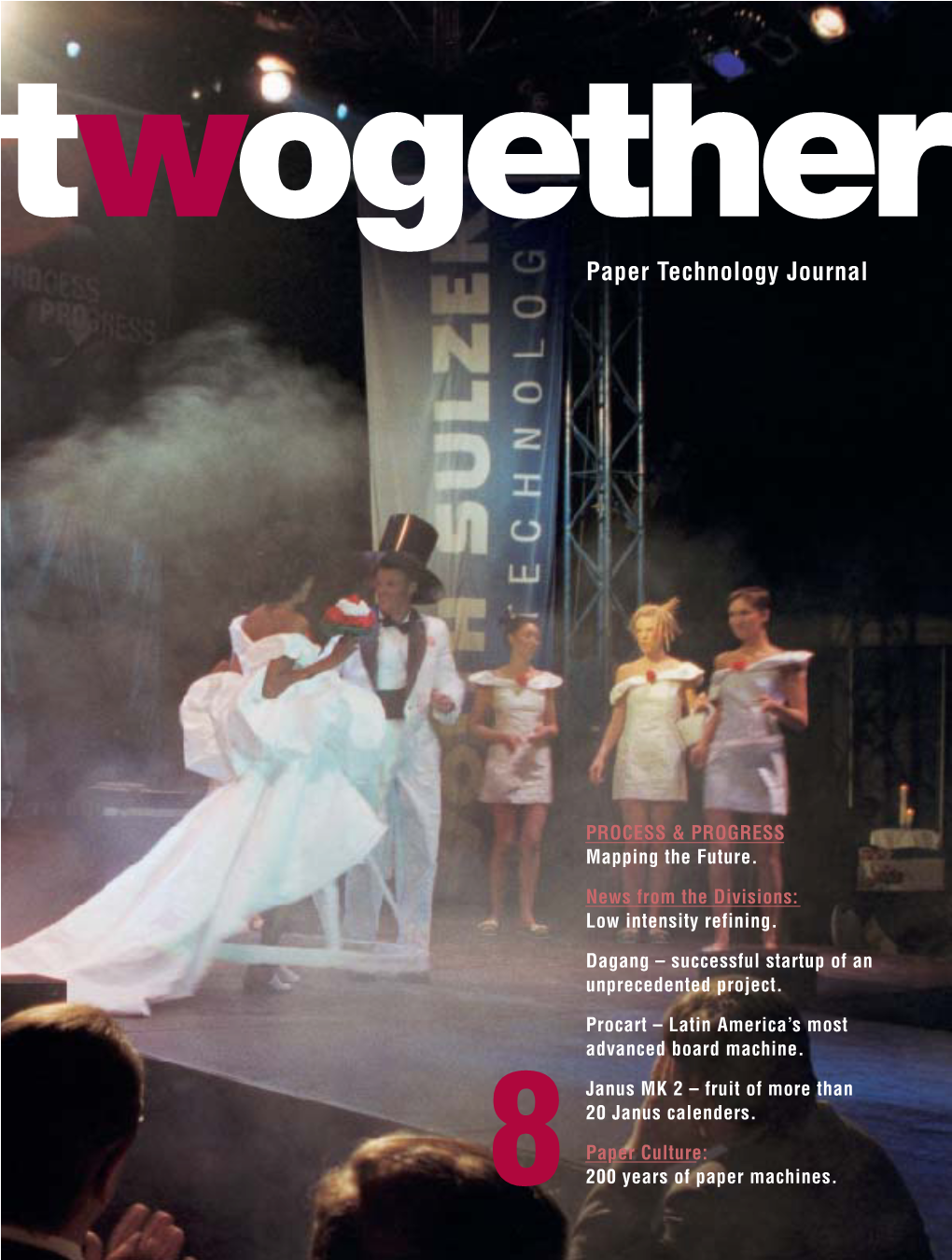
Load more
Recommended publications
-
Hazards in Paper and Pulp Industries – from an Engineering Insurance Perspective
Hazards in paper and pulp industries – from an engineering insurance perspective. IMIA WGP 49 (06) By Aki Ahonen Pohjola Ingvar Bodin Zurich Milan Dinets Ingosstrakh Mats Gådin If P&C Chairman Felix Staub Swiss Re Thomas Åström Pohjola Presented at the IMIA Conference in Boston, 12 September 2006. 1 Table of Contents 1 Introduction 4 1.1 General trends in the pulp and paper industry in the world. 4 1.2 Content of this paper 5 1.3 References 6 2 Technical descriptions and development 6 2.1 Pulp 6 2.1.1 Sulphate pulping (“Kraft” pulping) 6 2.1.1.1 Risks related to Kraft pulping 6 2.1.1.1.1 New chemicals for bleaching processes 6 2.1.1.1.2 Size increase of key machinery 7 2.1.2 Sulphite pulping 8 2.1.2.1 Special risk of sulphite pulping 8 2.1.3 Recycled pulping and deinked pulps 9 2.1.4 Mechanical pulp 9 2.2 Energy and chemical recovery 9 2.2.1 Kraft recovery boiler 10 2.2.1.1 General 10 2.2.1.2 Description 10 2.2.1.3 Special considerations 12 2.2.1.4 Trends in designing new recovery boilers 13 2.2.2 Black liquor gasification combined cycle 14 2.3 Paper Machine 14 2.3.1 Paper and board production in general 14 2.3.2 Contemporary technology and trends of paper and board machines 15 2.3.2.1 Dilution controlled head-box 15 2.3.2.2 Shoe press 16 2.3.2.3 Impingement drying 17 2.3.3 Tissue paper production 18 2.3.4 Technical trends and risks in general 19 2.4 Environmental aspects 20 2.4.1 Water treatment 20 2.4.2 Air purification 21 2.5 References 22 3 Loss prevention 23 3.1 General considerations 23 3.2 The most frequently used machine diagnostic methods 23 3.3 Critical components 24 3.3.1 Conveyors 24 3.3.2 Chippers 24 3.3.3 Digesters 25 3.3.4 Diffusers 25 3.3.5 Black liquor recovery boiler 26 3.3.6 Boiler fans 28 3.3.7 Lime kiln 29 3.3.8 Steam turbo sets 29 3.3.9 Main transformers 30 3.3.10 Paper machine 31 3.3.11 Yankee Dryers 31 2 3.4 References 32 4 EML / PML estimation. -
2019 Catalog 12-14.Pdf
www.legionpaper.com www.moabpaper.com www.risingmuseumboard.com www.solvart.com © Copyright 2019 Legion Paper Corporation All Rights Reserved. No portion of this publication may be reproduced without the permission of Legion Paper. OUR ROMANCE WITH PAPER Peace treaties are signed on it. Declarations of love are written on it. Artists’ works are portrayed on it. Of course, we mean paper; the medium that has evolved to reflect its own poetry, becoming an opportunity for pure innovation and unlimited creativity. Through the years, a melding of ancient craft and enlightened technology occurred, creating new practices and opening new horizons for expression in paper. When we trace its history, we find insight into man’s relentless imagination and creativity. Today, this convergence of ancient and modern continues and paper emerges with not only greater variety but a renewed appreciation of quality. To some, fine paper is the space that translates what is conceived in the mind to what is authentic. To others, having access to the right paper represents abundant possibility and profitability. The very selection of paper now becomes an adventure, realizing how the end result will vary based upon choice. Today, as in the years past, Legion Paper continues to source the finest papermakers around the globe, respecting the skill of the artisan and the unique attributes of the finished product. As we head into the future, Legion remains steadfast in its commitment to diversity, customer service and an unparalleled level of professionalism. We’re sure you will want to touch and feel some of the 3,500 papers described on the following pages. -
Introduction to Process and Properties of Tissue Paper
Introduction to process and properties of tissue paper enrico galli, 2017 Enrico Galli self-presentation • I was born in Viareggio (Lucca county or “the so called tissue valley”) Tuscany - Italy • Graduated in Chemical Engineering at University of Pisa in 1979 • Process and project engineer and then technical manager in oil industry (oil refineries and spent lube oil re-refining) in GULF, API, AGIP in Italy • Technical manager in chemical and consumer products company (soap, detergents, derivate from fatty acids, sanitary gloves, tissue paper) in Italy. • Since 1984 in paper and tissue business: • Italy: Tissue (PM, PBD, CON), Newspaper (PM), Cardboard paper (PM, MM) • Estónia: Tissue (PM, CEO) • France: Tissue (PM) • Hungary: Tissue (CON) • Nigéria: Tissue (CON) • Romania: Tissue (PM, PBM, MM, CON), Writing paper (PBM) • Rússia: Tissue (PM) • Spain: Tissue (PBM) • UK: Tissue (PBM) • Cooperation with following main European Tissue Companies: Annunziata (now WEPA – Italy), GP (now Lucart – Italy), Horizon Tissue (Estonia), Imbalpaper (now Sofidel – Italy), Kartogroup (now WEPA – Italy, France, Spain), Montebianco (Romania), Pehartec (Romania), Perini (now Sofidel – Romania, UK), Siktyvkar Tissue Group (Russia), Vaida Papir (Hungary)… and now proudly NAVIGATOR in Portugal! • I have been supporting Sales and Marketing Teams for strategic planning as well as for products development in Baltic Countries, BENELUX, Denmark, Finland, France, Germany, Hungary, Ireland, Italy, Norway, Poland, Romania, Russia, Spain, Sweden, UK. • Since 1998 I have -
Mountain Pine Beetle-Attacked Lodgepole Pine for Pulp and Papermaking
Operational extractives management from- mountain pine beetle-attacked lodgepole pine for pulp and papermaking Larry Allen and Vic Uloth Mountain Pine Beetle Working Paper 2007-15 Natural Resources Canada, Canadian Forest Service, Pacific Forestry Centre, 506 West Burnside Road, Victoria, BC V8Z 1M5 (250) 363-0600 • cfs.nrcan.gc.ca/regions/pfc Natural Resources Ressources naturelles Canada Canada Canadian Forest Service canadien Service des forêts Operational extractives management from mountain pine beetle-attacked lodgepole pine for pulp and papermaking Larry Allen and Vic Uloth Mountain Pine Beetle Initiative W orking Paper 2007œ15 Paprican 3800 W esbrook Mall Vancouver, B.C. V6S 2L9 Mountain Pine Beetle Initiative PO # 8.43 Natural Resources Canada Canadian Forest Service Pacific Forestry Centre 506 W est Burnside Road Victoria, British Columbia V8Z 1M5 Canada 2007 ≤ Her Majesty the Queen in Right of Canada 2007 Printed in Canada Library and Archives Canada Cataloguing in Publication Allen, Larry Operational extractives m anagem ent from m ountain pine beetle-attached lodgepole pine from pulp and paperm aking / Larry Allen and Vic Uloth. (Mountain Pine Beetle Initiative working paper 2007-15) "Mountain Pine Beetle Initiative, Canadian Forest Service". "MPBI Project # 8.43". "Paprican". Includes bibliographical references: p. Includes abstract in French. ISBN 978-0-662-46480-8 Cat. no.: Fo143-3/2007-15E 1. Pulping--British Colum bia--Quality control. 2. Pulping--Alberta--Quality control. 3. Paper m ills-- Econom ic aspects--British Colum bia. 4. Pulp m ills--Econom ic aspects--Alberta. 5. Lodgepole pine--Diseases and pests–Econom ic aspects. 6. Mountain pine beetle--Econom ic aspects. -
Paper Technology Journal
Paper Technology Journal World paper market: Quo vadis newsprint? News from the Divisions: Stock Preparation, Paper Machinery, Finishing and Service. A Scandinavian Success Story. Notable Startups. Orderbook Highlights. China, changing times in 3 the cradle of papermaking. Contents Foreword 1 Corporate News Highlights USA/Germany: Voith Appleton machine clothing. 55 Startups, orders on hand 2 Austria: World paper market The Andritz Group – partnering the Quo vadis newsprint? 5 pulp and paper industry 58 News from the Divisions Germany: Stock preparation: B+G Fördertechnik thirty years on 64 Membrane technology for the further close-up of paper mill water loops 14 Germany: Board and packaging Paper Machinery: pilot paper machine upgrade – Ortviken PM 4 – facing the future with tomorrow’s technology today 22 versatility 69 Paper Machinery: Latest generation of cylinder mould New names, new addresses formers – FloatLip former N, NO, S 28 Hunt & Moscrop: now Voith Sulzer Paper Machinery: Finishing Ltd., Manchester 72 Serang BM3/BM4 – the exemplary commissioning 30 Voith Sulzer Paper Technology: regional representation in Jakarta 72 Gap Former Technology: No. 26 DuoFormer CFD installation a success 37 Special awards for innovation and design Paper Machinery: New applications in multilayer Neusiedler Paper wins innovation technology 38 award with a revolutionary 3-layer headbox and NipcoFlex press 73 Paper Machinery: Brilliant Coating with JetFlow F – SPCI ’96 – impressive presence 73 data, facts, experience 44 Finishing: Advertisement of the year in Brazil 73 Econip – a new generation of deflection compensating rolls 48 China: Service: The changing origins of GR2 cover – next-generation paper – from hand-made performance leader 51 to machine-made 75 Cover picture: Ortviken – successfull start-up (see article on page 22). -
Corrugated Board Structure: a Review M.C
ISSN: 2395-3594 IJAET International Journal of Application of Engineering and Technology Vol-2 No.-3 Corrugated Board Structure: A Review M.C. Kaushal1, V.K.Sirohiya2 and R.K.Rathore3 1 2 Assistant Prof. Mechanical Engineering Department, Gwalior Institute of Information Technology,Gwalior, Assistant Prof. Mechanical Engineering 3 Departments, Gwalior Engineering College, Gwalior, M. Tech students Maharanapratap College of Technology, Gwalior, [email protected] [email protected] [email protected] ABSTRACT Corrugated board is widely used in the packing industry. The main advantages are lightness, recyclability and low cost. This makes the material the best choice to produce containers devoted to the shipping of goods. Furthermore examples of structure design based on corrugated boards can be found in different fields. Structural analysis of paperboard components is a crucial topic in the design of containers. It is required to investigate their strength properties because they have to protect the goods contained from lateral crushing and compression loads due to stacking. However in this paper complete and detailed information are presented. Keywords: - corrugated boards, recyclability, compression loads. Smaller flutes offer printability advantages as well as I. INTRODUCTION structural advantages for retail packaging. Corrugated board is essentially a paper sandwich consisting of corrugated medium layered between inside II. HISTORY and outside linerboard. On the production side, corrugated In 1856 the first known corrugated material was patented is a sub-category of the paperboard industry, which is a for sweatband lining in top hats. During the following four sub-category of the paper industry, which is a sub-category decades other forms of corrugated material were used as of the forest products industry. -
Chemical Pulping of Waste Pineapple Leaves Fiber for Kraft Paper Production
JMRTEC-135; No. of Pages 8 ARTICLE IN PRESS j m a t e r r e s t e c h n o l . 2 0 1 5;x x x(xx):xxx–xxx Available online at www.sciencedirect.com www.jmrt.com.br Original Article Chemical pulping of waste pineapple leaves fiber for kraft paper production a,∗ b Waham Ashaier Laftah , Wan Aizan Wan Abdul Rahaman a Department of Polymer Engineering, Faculty of Chemical Engineering, Universiti Teknologi Malaysia, Johor, Malaysia b Center for Composites, Universiti Teknologi Malaysia, Johor, Malaysia a r t i c l e i n f o a b s t r a c t Article history: The main objective of this study is to evaluate the implementation of acetone as a pulping Received 29 August 2014 agent for pineapple leaves. Mixtures of water and acetone with concentration of 1%, 3%, Accepted 15 December 2014 5%, 7%, and 10% were used. The effects of soaking and delignification time on the paper Available online xxx properties were investigated. Thermal and physical properties of paper sheet were studied using thermogravimetric analysis (TGA) and tearing resistance test respectively. The mor- × Keywords: phological properties were observed using microscope at 200 magnification. The paper sheet produced from pulping with 3% acetone concentration shows the highest mechan- Natural fiber Renewable resources ical properties. Papers strength was improved by increasing the delignification time. The ◦ Pineapple leaves delignification time was reduced by cooking the pineapple leaves at a temperature of 118 C Pineapple fiber under applied pressure of 80 kPa which has remarkable effect on paper strength. -
What Happens to Cellulosic Fibers During Papermaking and Recycling? a Review
PEER-REVIEWED REVIEW ARTICLE ncsu.edu/bioresources WHAT HAPPENS TO CELLULOSIC FIBERS DURING PAPERMAKING AND RECYCLING? A REVIEW Martin A. Hubbe,* Richard A. Venditti, and Orlando J. Rojas Both reversible and irreversible changes take place as cellulosic fibers are manufactured into paper products one or more times. This review considers both physical and chemical changes. It is proposed that by understanding these changes one can make better use of cellulosic fibers at various stages of their life cycles, achieving a broad range of paper performance characteristics. Some of the changes that occur as a result of recycling are inherent to the fibers themselves. Other changes may result from the presence of various contaminants associated with the fibers as a result of manufacturing processes and uses. The former category includes an expected loss of swelling ability and decreased wet-flexibility, especially after kraft fibers are dried. The latter category includes effects of inks, de-inking agents, stickies, and additives used during previous cycles of papermaking. Keywords: Paper recycling, Drying, Deinking, Hornification, Inter-fiber bonding, Refining, Fines, Fiber length, Conformability Contact information: Department of Forest Biomaterials Science and Engineering, Box 8005, North Carolina State University, Raleigh, NC 27695-8005, USA; *Corresponding author: [email protected] INTRODUCTION Cellulosic fibers can change significantly when formed into a wet web of paper and subsequently subjected to such processes as pressing, drying, printing, storage, repulping, and deinking. Some of the changes can be subtle. Often it is possible to substitute recovered fibers in place of virgin fibers used for the production of paper or paperboard. On the other hand, characteristic differences between recycled fibers and virgin fibers (fresh from pulping wood, not recycled) can be expected; many of these can be attributed to drying. -
Paper Machine System Diagram
TMEIC Corporation Paper Machine System Diagram Paper Machine One-Line Press Section Head Box Forming Section Calender Dryer Size Reel Sections Press Driven roll Mechanical Components of Paper Associated Drive Control Concepts Regenerative Machine Drives Head Box / Fan Pump Fan pump drive control is typical for No The Paper stock at this point in the process is industrial pump loads. Variable 99% water and 1% fiber. The Fan Pump torque is required, increased speed forces the Paper stock through a set of means increased flow. nozzles in the head box onto the “wire” mesh. The fan pump speed is a major factor in the basis weight (caliper) and formation of the sheet of paper. Forming Section Forming section drives have a high No A typical flat former is a continuous rotating friction load due to the suction wire (today this is plastic) mesh that removes (normal forces) of the water through water from the paper by sucking it out of the wire mesh. This results in a high suspension. Multi-layer paper machines and normal running load, but a low paper board machines include additional acceleration load. forming sections (one forming section for each layer of paper). Press Section Press section drives also have a high No Rolls are nipped (pressed) together to load due to the strong forces in the nip squeeze the water out of the sheet of paper. between the rolls deforming the felts Multiple rolls are used with a felt (blanket) and roll. This results in a high normal supporting the sheet and accepting the water running load, but a low acceleration from the sheet. -
Fine Art Papers Guide
FINE ART PAPERS GUIDE 100 Series • 200 Series • Vision • 300 Series • 400 Series • 500 Series make something real For over 125 years Strathmore® has been providing artists with the finest papers on which to create their artwork. Our papers are manufactured to exacting specifications for every level of expertise. 100 100 Series | Youth SERIES Ignite a lifelong love of art. Designed for ages 5 and up, the paper types YOUTH and features have been selected to enhance the creative process. Choice of paper is one of the most important 200 Series | Good decisions an artist makes 200SERIES Value without compromise. Good quality paper at a great price that’s economical enough for daily use. The broad range of papers is a great in determining the GOOD starting point for the beginning and developing artist. outcome of their work. Color, absorbency, texture, weight, and ® Vision | Good STRATHMORE size are some of the more important Let the world see your vision. An affordable line of pads featuring extra variables that contribute to different high sheet counts and durable construction. Tear away fly sheets reveal a artistic effects. Whether your choice of vision heavyweight, customizable, blank cover made from high quality, steel blue medium is watercolor, charcoal, pastel, GOOD mixed media paper. Charcoal Paper in our 300, 400 and 500 Series is pencil, or pen and ink, you can be confident that manufactured with a traditional laid finish making we have a paper that will enhance your artistic them the ideal foundation for this medium. The efforts. Our papers are manufactured to exacting laid texture provides a great toothy surface for specifications for every level of expertise. -
TECHNICAL REPORT – PATENT ANALYSIS Enhancing Productivity in the Indian Paper and Pulp Sector
TECHNICAL REPORT – PATENT ANALYSIS Enhancing Productivity in the Indian Paper and Pulp Sector 2018 TABLE OF contEnts ACKNOWLEDGEMENTS 10 EXECUTIVE SUMMARY 11 1 INTRODUCTION 13 2 OVERVIEW OF THE PULP AND PAPER SECTOR 15 2.1. Status of the Indian Paper Industry 15 2.2. Overview of the Pulp and Papermaking Process 20 2.3. Patenting in the Paper and Pulp Industry: A Historical Perspective 22 2.4. Environmental Impact of the Pulp and Paper Industry 25 3 METHODOLOGY 27 3.1. Search Strategy 27 4 ANALYSIS OF PATENT DOCUMENTS USING GPI 31 4.1. Papermaking; Production of Cellulose (IPC or CPC class D21) 31 4.2. Analysis of Patenting Activity in Different Technology Areas using GPI 38 5 ANALYSIS OF THE INDIAN PATENT SCENARIO WITHIN THE CONTEXT OF THIS REPORT 81 5.1. Analysis of Patents Filed in India 81 6 CONCLUDING REMARKS 91 REFERENCES 93 ANNEXURE 94 Annexure 1. Technologies related to paper manufacturing 94 Annexure 2. Sustainable/green technologies related to pulp and paper sector 119 Annexure 3. Emerging Technology Areas 127 List OF FIGURES Figure 2.1: Geographical Spread of Figure 4.11: (d) Applicant vs. Date of Indian Paper Mills .................................16 Priority Graph: Paper-Making Machines Figure 2.2: Share of Different Segments and Methods ........................................42 in Total Paper Production .......................19 Figure 4.11: (e) Applicant vs. Date of Figure 2.3: Variety Wise Production of Priority Graph: Calendars and Accessories ..43 Paper from Different Raw Materials ........19 Figure 4.11: (f) Applicant vs. Date of Figure 2.4: Different Varieties of Paper Priority Graph: Pulp or Paper Comprising Made from Various Raw Materials ..........19 Synthetic Cellulose or Non-Cellulose Fibres ..43 Figure 2.5: Diagram of a Process Block Figure 4.11: (g) Applicant vs. -
Making Paper from Trees
Making Paper from Trees Forest Service U.S. Department of Agriculture FS-2 MAKING PAPER FROM TREES Paper has been a key factor in the progress of civilization, especially during the past 100 years. Paper is indispensable in our daily life for many purposes. It conveys a fantastic variety and volume of messages and information of all kinds via its use in printing and writing-personal and business letters, newspapers, pamphlets, posters, magazines, mail order catalogs, telephone directories, comic books, school books, novels, etc. It is difficult to imagine the modern world without paper. Paper is used to wrap packages. It is also used to make containers for shipping goods ranging from food and drugs to clothing and machinery. We use it as wrappers or containers for milk, ice cream, bread, butter, meat, fruits, cereals, vegetables, potato chips, and candy; to carry our food and department store purchases home in; for paper towels, cellophane, paper handkerchiefs and sanitary tissues; for our notebooks, coloring books, blotting paper, memo pads, holiday greeting and other “special occasion’’ cards, playing cards, library index cards; for the toy hats, crepe paper decorations, paper napkins, paper cups, plates, spoons, and forks for our parties. Paper is used in building our homes and schools-in the form of roofing paper, and as paperboard- heavy, compressed product made from wood pulp-which is used for walls and partitions, and in such products as furniture. Paper is also used in linerboard, “cardboard,” and similar containers. Wood pulp is the principal fibrous raw material from which paper is made, and over half of the wood cut in this country winds up in some form of paper products.