Kansanshi Operations Technical Report May 2015
Total Page:16
File Type:pdf, Size:1020Kb
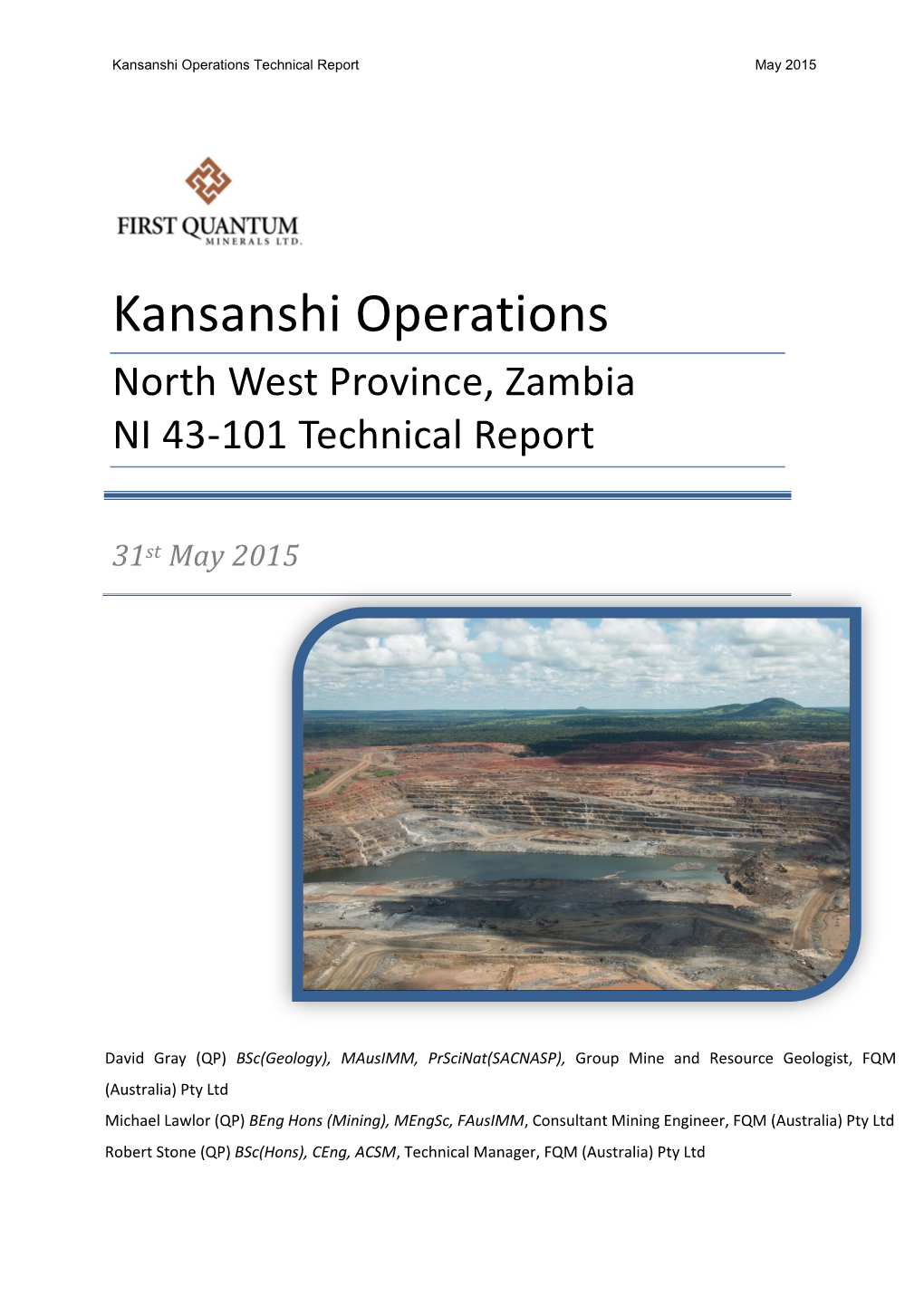
Load more
Recommended publications
-
Introduction - the Trident Project
Introduction - The Trident Project January 2014 www.first-quantum.com TSX: FM LSE: FQM LuSE: FQMZ TRIDENT PROJECT LOCATION January 2014 2 ABOUT THE TRIDENT PROJECT Trident Project: . Located in the Solwezi District of Northwestern Province, Zambia . Approximately 150km from Solwezi on the T5 main road to Mwinilunga . Comprises five prospecting large scale licences . A number of attractive base metal prospects including the Sentinel deposit and the Enterprise deposit . 5 x large-scale mining licences awarded 20 April 2011 for 25 years tenure . Land use agreement signed 14 July 2011 . EIA approved 8 July 2011 and Addendum 12 August 2013 . Resettlement Action Plan approved 15 October 2013 January 2014 3 TRIDENT PROJECT LAYOUT January 2014 4 SENTINEL MINE IN CONSTRUCTION – COMMISSIONING MID 2014 Updated resource published May 2012: . 514 boreholes for 172,692m defined an NI43-101 resource of: . Total measured & indicated : 1,027Mt @ 0.51% Cu . Inferred : 165Mt @ 0.42% Cu . Cut-off : 0.2% Cu . Mineral Reserve: 774 Mt @ 0.50% Cu . Proved : 476 Mt @ 0.52% Cu . Probable : 298 Mt @ 0.47%Cu. Strip ratio 2.2 : 1 Mine planning: . Grade of 0.5% Cu requires a high throughput of 55 Mtpa to achieve production target of 280 – 300,000t Cu per annum. Sentinel will put Zambia at the forefront of global mining technology January 2014 5 ENTERPRISE MINE IN APPROVAL – EARLY WORKS UNDERWAY Maiden resource published December 2012: . 359 boreholes for 116,000m defined an NI43-101 resource of: . Total measured indicated : 40.1Mt @ 1.07% Ni . Inferred : 7.1Mt @ 0.70% Ni . Cutoff : 0.15% Ni . -
EML Contracts Profile 2017.Cdr
50 ANNIVERSARY 1965 - 2015 www.eml-eis.com VALUE SERVICE QUALITY LOYALTY PRICE Contracting Reliable Quality Service since 1968 in the field of Electrical Contracting SUPPORT Zambia. COMPANY 2017-8 PROFILE 1 company details Name of the Company: Electrical Maintenance Lusaka Ltd. Address: Head Office Plot 195 Luanshya Road, East End Off Great North End Lusaka, 10101 Zambia Contact Details: +260 211 227824 +260 237014 - FAX [email protected] [email protected] [email protected] website: www.eml-eis.com 50 ANNIVERSARY 1965 - 2015 Contracts Department history 2 HISTORY: FOUNDER AND OWNER Mr George Narder achieved electrical and mechanical engineering qualifications in Italy following which he worked in Switzerland for 6 years. In 1963 he arrived in Zambia as part of a testing and commissioning team for the newly built Kariba Power Station and has lived in Zambia ever since. Mr Narder started an electrical engineering business in 1965, registered as Electrical Maintenance Lusaka LTD (EML). He has managed and run the company as its CEO for more than 50 years. Under his direct entrepreneurial management, EML has grown into one of the largest and most respected electrical and electronic engineering companies in Zambia. The company benefits from more than 60 years of his passion, knowledge and expertise. EML is proud to have participated in many facets of the social and Mr George Narder, Comm economic development of the country ELECTRICAL MAINTENANCE LUSAKA (EML) MOTO “Always with our customers” To continue improving on our 50 years of reliable quality service to the Zambian industry. our vision our mission e strive to remain one of Zambia’s ur added value is to provide quality leading and most diverse electrical products, service and training for all cWontracting, manufacturing, retail and electricalO requirements across the country, training companies. -
Corporate Affairs and Business Development
CORPORATE AFFAIRS AND BUSINESS DEVELOPMENT ENVIRONMENTAL IMPACT ASSESSMENT THE PROPOSED CONNECTION OF NORTH WESTERN PROVINCE TO THE NATIONAL GRID AT 132kV PREPARED BY THE ENVIRONMENT AND SOCIAL AFFAIRS UNIT 2011 EXECUTIVE SUMMARY In the Northwestern Province (NWP) ZESCO Limited supplies electricity to five districts namely Mwinilunga, Mufumbwe, Kabompo, Zambezi and Chavuma from isolated Diesel Generation Stations located in each district. The older districts (Mwinilunga, Kabompo, and Zambezi) have been on diesel power supply for over forty years now. Solwezi and Kasempa are the only two districts in the province that are supplied from the national hydro power grid. Power supply from the diesel power stations is characterized by high operational costs, inadequate capacity, very low reliability and high emissions. ZESCO Limited has therefore long sought to replace diesel generated power supply with reliable and cost effective power from the national grid by connecting all the diesel power stations to the grid. By the year 2000, ZESCO Limited was operating ten diesel stations country wide, but by 2007, four such stations had been replaced by grid supply while two new stations were installed in two newly designated districts. Despite having great potential for mining and agricultural development, NWP generally remains underdeveloped due to insufficient and unreliable power supply. It is against this background that the Government of the Republic of Zambia through ZESCO Limited, intends to connect the 5 NWP Districts still on diesel, to the National Grid at 132 kilo Volts (kV) through a transmission line network from Kasempa T-Off (Nselauke) to Chavuma and linking Mwinilunga to Lumwana. The main objective of the project is to replace the diesel generated electricity with hydro electricity by constructing a 132kV transmission line network which would be linked to the main national power grid. -
National Investment Plan to Reduce Deforestation and Forest Degradation (2018-2022)
Republic of Zambia Ministry of Lands and Natural Resources National Investment Plan to Reduce Deforestation and Forest Degradation (2018-2022) November 2017 -i- Executive Summary Zambia has approximately 49.9 million hectares of forest, representing approximately 66 percent of its total land mass and is subsequently one of the most forested countries in southern Africa. However, deforestation is a major problem, with annual rates estimated at around 250,000 to 300,000 hectares. Such numbers amount to the potential loss of 10 million hectares of forest in the next 30 years (IDLO, 2014). The key drivers of deforestation and forest degradation in Zambia are agricultural expansion (commercial and subsistence), heavy reliance on wood fuel – energy demand (charcoal and firewood), unsustainable timber extraction (both legal and illegal) and infrastructure development (e.g., mining and other large infrastructural developments). A study by UN-REDD, (2015) on the economic value of Zambia’s forest ecosystems showed that the direct and indirect values of forests are estimated to make a direct contribution equivalent to about 4.7% of gross domestic product (GDP) or US$957.5 million (using 2010 figures). However, when the multiplier effects of forestry and tourism-related activities on other sectors are considered, the overall or economy-wide contribution of forests to GDP is estimated to be at least 6.3% or US$1,277 million (Table 1). Forests are estimated to provide at least 1.4 million jobs, supporting 60% of rural Zambian households, heavily dependent upon the use of natural resources to supplement or sustain their livelihoods (UN-REDD., 2015). -
Evaluation of the Bank's Country Strategy and Program 2002–2015 - Summary Report IDEV Country Strategy Evaluation, October 2016
Country Strategy Evaluation Zambia: An IDEV Evaluation of the Bank's Country Strategy and Program 2002–2015 Summary Report October 2016 Evaluation Syntheses IDEV conducts different types of evaluations to achieve its Impact Evaluations Sector Evaluations (Public Sector) strategic objectives Project Performance Evaluations Thematic Evaluations Project Cluster Evaluations Project Performance Evaluations (Private Sector) Corporate Evaluations Regional Integration Strategy Evaluations Country Strategy Evaluation Country Strategy Evaluations Country Strategy Evaluation Zambia: An IDEV Evaluation of the Bank's Country Strategy and Program 2002–2015 Summary Report October 2016 ACKNOWLEDGMENTS Task manager Madhusoodhanan Mampuzhasseril, Principal Evaluation Officer Team members Erika Maclaughlin, Long Term Consultant, Foday Turay, Chief Evaluation Officer, Latefa Camara, Long Term Consultant, James Sackey, Consultant Consultant Agrer S.a. - N.v., Belgium. Paolo Liebl Von Schirach, Team Leader. Members: Baptiste Forquy, Habtom Asmelash, Bernd Drechsler, John Murphy, Charles Haanyika, Vikramdityasing Bissoonauthsing External peer reviewer Bruce Murray, former Director General, Operations Evaluation Department, Asian Development Bank Knowledge management officers Jayne Musumba, Principal Knowledge Management Officer Jerry Lemogo, Junior Consultant, Communications and Knowledge Management Special thanks to Norad – The Norwegian Agency for Development Cooperation Division manager Samer Hachem Evaluator-General Rakesh Nangia © 2016 African Development -
Building a Copper Development Company LUMWANA WEST: Advanced Copper-Cobalt Deposit MURDIE and TORRENS: Massive Copper Targets
OPERATIONAL UPDATE Building a Copper Development Company LUMWANA WEST: Advanced Copper-Cobalt Deposit MURDIE and TORRENS: Massive Copper Targets LINDSAY OWLER, Director/CEO – November 2019 Argonaut Resources NL • ASX:ARE • Level 5, 126 Phillip St, Sydney, 2000 • phone (02) 9299 9690 CORPORATE OVERVIEW ASX Code ARE Capital structure Shares on issue: 1.544 billion Unlisted options: 65 million Market capitalisation: A$8 million Cash A$1.4 million Directors Pat Elliott Non-Executive Chairman Lindsay Owler Director and CEO Andrew Bursill Director and Company Secretary Malcolm Richmond Non-Executive Director OPERATIONAL UPDATE • NOVEMBER 2019 2 COPPER FOCUS South Australian Copper y Murdie Project IOCG y Torrens Project IOCG Massive systems, pedigree geology Zambia Copper Cobalt Lumwana West y Copper Cobalt scoping study New exploration projects y Heart of Zambian gold rush Zambia Copper Cobalt WA Gold Lumwana West Higginsville Higginsville – Gold, WA y Multiple gold and nickel targets Torrens Copper Murdie Copper South Australia OPERATIONAL UPDATE • NOVEMBER 2019 3 LUMWANA WEST, ZAMBIA Large tonnage copper-cobalt sulphide y Low stripping ratio y Saleable concentrate produced y Scoping study progressing y Argonaut 90% OPERATIONAL UPDATE • NOVEMBER 2019 4 LUMWANA WEST, ZAMBIA Project elements Jurisdiction Zambia has a long history of large-scale copper The Nyungu deposit mining. Social and governmental pressures continues to impress favour the development of new mines. with excellent technical Infrastructure Lumwana West is located at major electricity characteristics. and transport corridors. Resource The Nyungu copper-cobalt deposit has predictable geometry and scope for significant growth with continued drilling. Mining Very low stripping ratio of 1.5 tonnes of waste rock from every 1 tonne of ore. -
Necessity Driving Change and Improvement to the Cleaner Circuit at Lumwana Copper Concentrator
NECESSITY DRIVING CHANGE AND IMPROVEMENT TO THE CLEANER CIRCUIT AT LUMWANA COPPER CONCENTRATOR *R. Araya1, G. Cordingley2, A. Mwanza2 and L. Huynh3 1Xstrata Technology Canada Level 10- 700 West Pender Street Vancouver, Canada V6C 1G8 (*Corresponding author:[email protected]) 2Barrick Copper Business Unit P.O. Box 110199, Mwinilunga Road Lumwana East, Solwezi, Zambia 3Xstrata Technology Australia Level 10 – 160 Ann Street Brisbane, Australia QLD 4000 ABSTRACT Lumwana is an open pit Copper mine located in the Northwestern Province of Zambia approximately 80 km west from the provincial capital of Solwezi, approximately 300 km northwest from the Copperbelt and 700 km northwest from the national capital of Lusaka. The mine has two major Copper deposits: Malundwe and Chimiwungo. Copper mineralization includes Chalcopyrite, Bornite and Chalcocite. In addition to Copper, these deposits also contain the undesirable element Uranium contained in vein hosted and disseminated Uranite. The processing plant was designed using conventional technologies: semi-autogenous grinding (SAG) and ball mill for grinding, and mechanical cells for rougher and cleaner flotation. Soon after commissioning in early 2009, it was recognised that two stages of conventional cleaning were unable to produce plant final Copper concentrates with the desired Uranium grades. Studies have shown that a significant quantity of liberated and fine Uranium particles (up to 80-90%) is recovered with the concentrate by entrainment. Lumwana Operations sought the use of the Jameson Cell technology after observing successful implementation at other sites in rectifying similar issues. In late 2009, Jameson Cell pilot-plant test work was conducted at the site and this quickly led to the installation of a full-scale B5400/18 model into the existing cleaner circuit. -
Banks in Zambia
INFRASTRUCTURE Among the non-traditional crops with potential and are prioritized for investments include cotton, coffee, tobacco, sugarcane, pineapples, cashew nuts, cassava and horticultural/floricultural crops. Foreign investments have already been approved in principle for new crops such as jatropha, moringa and stevia and land approximating 100,000 hectares have been approved for each. b) Industrial Land: Industrial land in the capital city Lusaka is located on the western part of the city. Every city in Zambia is zoned an industrial area where all manufacturing activities can take place. It is also where an investor wishing to set up an industry can do so. In order to expand the country’s manufacturing base and enhance national competitiveness, the Government is establishing industrial parks and will extend tax incentives under the ZDA Act to developers of, and investors in Multi- Facility Economic Zones. Two types of MFEZ are being promoted: Production MFEZs for manufacturing related businesses and Export Trade MFEZ for commercial trading, warehousing etc. to exploit export markets. In addition, developers of industrial parks will qualify for the above incentives if: i. The layout of the development plan is approved by the relevant planning authority; ii. The park to be developed is at least 15 acres in size; iii. The park will have paved roads; and iv. Water and electricity supply within the park is provided. These measures are aimed at attracting both local and foreign investors to open up and invest in the MFEZ and industrial parks across the country. ZDA will assist all investors to identify suitable land for economic activities and ensure its proper allocation according to existing laws and regulations. -
4 Development Directions for Regional Infrastructure
Preparatory Survey for Southern Africa Integrated Transport Program Chapter 4 4 Development Directions for Regional Infrastructure 4.1 Infrastructure Bottlenecks under Growth Scenarios 4.1.1 Current Industrial Situation of the Corridors In parallel with the macro analysis undertaken in Chapter 2, summary information on development potential in the region (especially of mineral resources development accompanied by cross-border transport improvements and an overview of a Mega Project) are presented in this section. More details may be found in Appendix B. The results serve as input to Section 4.1.3 on Infrastructure Bottlenecks under the Growth Scenarios. The figure below visually summarizes the mineral and agricultural potential in the Southern African region. (The number of corridor in Figure 4.1.1 corresponds to this section’s paragraph number.) Figure 4.1.1 Mineral and Agricultural Resources and Corridors (1) Nacala Corridor Nacala is regarded as the best location for a deepwater port on the East African coast. The Nacala Corridor has consequently been at the forefront of ongoing initiatives to rehabilitate the rail link to Malawi, thereby creating a number of “anchor” tenants and promoting development 4-1 Preparatory Survey for Southern Africa Integrated Transport Program Chapter 4 along the corridor. Together with Beira and other corridors (Sena and Tete), these developments have been linked to the possible export of coal from the Moatize and Benga coal fields as well as from the Muchana Vuzi coal fields north of the Cahorra Bassa Dam in Tete Province, Mozambique. The corridor is ultimately seen as linking Lusaka in Zambia with the Port of Nacala. -
Copper Capitalism Today: Space, State and Development in North Western Zambia
Copper Capitalism Today: Space, State and Development in North Western Zambia Dissertation Presented in Partial Fulfillment of the Requirements for the Degree Doctor of Philosophy in the Graduate School of The Ohio State University By Rohit Negi Graduate Program in Geography The Ohio State University 2009 Dissertation Committee: Kevin R. Cox, Advisor Mathew Coleman Kwaku L. Korang Copyright by Rohit Negi 2009 Abstract The days of doom and gloom in descriptions of African social and economic realities seem increasingly passé. After two decades of economic decline, externally imposed austerity, and deprivation, Africa is being widely seen as having turned the corner. Recent investment has produced a boom in extractive industries and relatively high rates of economic growth in the countries where these industries dominate the economy. These changes have fuelled fresh visions of an African ‘renaissance’. Others see these developments as a new page of an older history of booms and busts in Africa’s extractive industries, and with them, the respective national economies. These patterns coincide to a large degree with the vicissitudes of world commodity markets, and are therefore highly inconstant and unpredictable. Past busts have forced ordinary Africans and social scientists alike to continually reevaluate the continent’s place in the globalized world. A simple question, therefore, underlies this research: Is the new mining boom an African economic revival or a rerun of the previous cycle of growth and eventual decline? Using Zambia as a window, this dissertation examines the geographies of mining, state, and development in Africa. It draws upon ethnographic fieldwork in Zambia’s North Western Province to illuminate the reconfigurations of people, places, and power set in ii motion by a copper mining boom. -
Mapping the Geographical Distribution of Lymphatic Filariasis in Zambia
Mapping the Geographical Distribution of Lymphatic Filariasis in Zambia Enala T. Mwase1, Anna-Sofie Stensgaard2,3*, Mutale Nsakashalo-Senkwe4, Likezo Mubila5, James Mwansa6, Peter Songolo7, Sheila T. Shawa1, Paul E. Simonsen2 1 School of Veterinary Medicine, University of Zambia, Lusaka, Zambia, 2 Department of Veterinary Disease Biology, Faculty of Health and Medical Sciences, University of Copenhagen, Copenhagen, Denmark, 3 Center for Macroecology, Evolution and Climate, Natural History Museum of Denmark, University of Copenhagen, Copenhagen, Denmark, 4 Ministry of Health, Lusaka, Zambia, 5 World Health Organization, Regional Office for Africa, Harare, Zimbabwe, 6 University Teaching Hospital, University of Zambia, Lusaka, Zambia, 7 World Health Organization, Lusaka, Zambia Abstract Background: Past case reports have indicated that lymphatic filariasis (LF) occurs in Zambia, but knowledge about its geographical distribution and prevalence pattern, and the underlying potential environmental drivers, has been limited. As a background for planning and implementation of control, a country-wide mapping survey was undertaken between 2003 and 2011. Here the mapping activities are outlined, the findings across the numerous survey sites are presented, and the ecological requirements of the LF distribution are explored. Methodology/Principal findings: Approximately 10,000 adult volunteers from 108 geo-referenced survey sites across Zambia were examined for circulating filarial antigens (CFA) with rapid format ICT cards, and a map indicating the distribution of CFA prevalences in Zambia was prepared. 78% of survey sites had CFA positive cases, with prevalences ranging between 1% and 54%. Most positive survey sites had low prevalence, but six foci with more than 15% prevalence were identified. The observed geographical variation in prevalence pattern was examined in more detail using a species distribution modeling approach to explore environmental requirements for parasite presence, and to predict potential suitable habitats over unsurveyed areas. -
EML Company Profile 2017.Cdr
50 ANNIVERSARY 1965 - 2015 www.eml-eis.com VALUE SERVICE QUALITY LOYALTY PRICE EML at a Glance Electrical Maintenance Lusaka Ltd has had a 50 year presence in Zambia and is currently SUPPORT the most diverse electrical and electronic engineering company in Zambia. EML has a strong focus on continuous improvement which is reflected in our sustained customer support, growth, referrals and stability COMPANY 2017 PROFILE 1 company details Name of the Company: Electrical Maintenance Lusaka Ltd. about Address: Head Office Plot 195 Luanshya Road, East End Off Great North End Lusaka, 10101 Zambia 50 Contact Details: +260 211 227824 ANNIVERSARY +260 237014 - FAX 1965 - 2015 [email protected] [email protected] [email protected] website: www.eml-eis.com SS Factory Contracts Department Sales and Admin goals & objectives 2 about products To continue delivering high quality, state of the art products through our well established, loyal international partnerships. manufacturing To continue to deliver superior products through our modern production facility and ensure that quality is maintained at an uncompromised high standard. construction To continue to deliver quality electrical infrastructure on time and within budget. Our priority is to maintain the highest level of safety throughout all our company’s operations. human resources To continue to attract, support and reward our staff while providing an environment of development and growth. customers To ensure our customers always receive the most professional and friendly service paired with the highest quality products in a fast evolving market. 3 history HISTORY: FOUNDER AND OWNER Mr George Narder achieved electrical and mechanical engineering qualifications in Italy following which he worked in about Switzerland for 6 years.