Reusable Launch Vehicles: Evolution Redefined Bhavana Y*, Mani Shankar N and Prarthana BK Department of Mechanical Engineering, SNIST, India
Total Page:16
File Type:pdf, Size:1020Kb
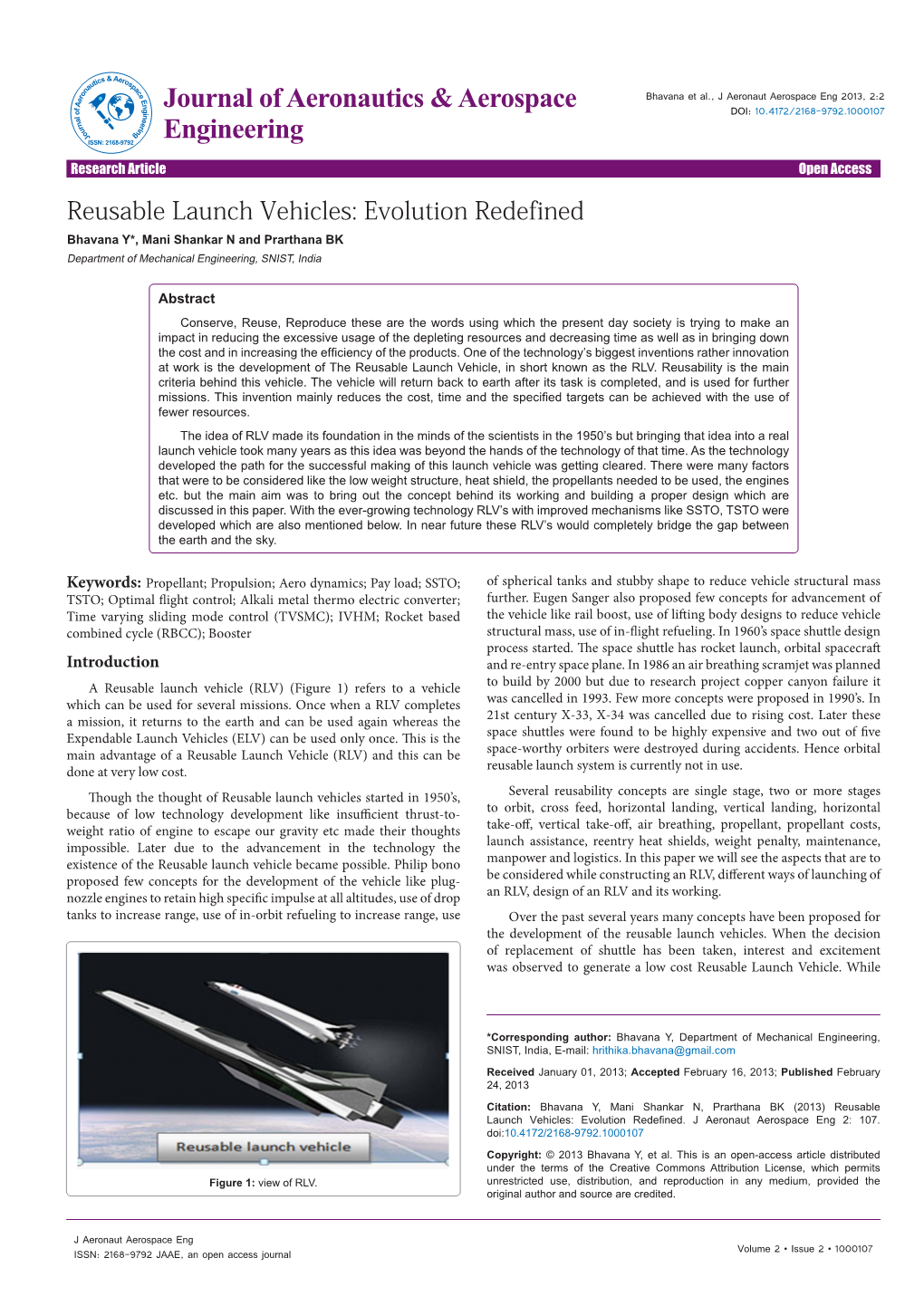
Load more
Recommended publications
-
NASA Lessons Learned on Reusable and Expendable Launch Vehicle Operations and Their Application Towards DARPA’S Experimental Spaceplane (XS-1) Program
NASA Lessons Learned on Reusable and Expendable Launch Vehicle Operations and Their Application Towards DARPA’s Experimental Spaceplane (XS-1) Program C. H. Williams NASA GRC R. G. Johnson NASA KSC 15 Jan 15 Outline • Selected Historic Shuttle Operations Data • Shuttle Lessons Learned Recommendations for Lower Cost, Operationally Efficient Launch Vehicle Systems • Selected Expendable launch vehicle experiences • Past NASA Launch Vehicle Development Programs, Studies (1985 to present) • Discussion: Suggested applications of NASA Lessons Learned to already-baselined contractor XS-1 Phase I concepts Selected Historic Shuttle Operations Data 3 Original Shuttle Ops Concept vs. Actual Concept Phase (c. 1974) Operational Phase 4 Overall Results of Cost Analysis • “Direct” (Most Visible) Work Drives Massive (and Least Visible) Technical & Administrative Support Infrastructure STS Budget "Pyramid" (FY 1994 Access to Space Study) • Example: Direct Unplanned Repair Activity Drives Ops Support Infra, Logistics, Sustaining Engineering, Total SR&QA and Flight Certification Generic $M Total Operations Function FY94 (%) Elem. Receipt & Accept. 1.4 0.04% Landing/Recovery 19.6 0.58% Direct (Visible) Work “Tip of the Iceberg” Veh Assy & Integ 27.1 0.81% <10% Launch 56.8 1.69% Offline Payload/Crew 75.9 2.26% + Turnaround 107.3 3.19% Vehicle Depot Maint. 139.0 4.14% Indirect (Hidden) Traffic/Flight Control 199.4 5.93% ~20% Operations Support Infra 360.5 10.73% + Concept-Uniq Logistics 886.4 Support (Hidden) 26.38% ~70% Trans Sys Ops Plan'g & Mgmnt 1487.0 44.25% -
L AUNCH SYSTEMS Databk7 Collected.Book Page 18 Monday, September 14, 2009 2:53 PM Databk7 Collected.Book Page 19 Monday, September 14, 2009 2:53 PM
databk7_collected.book Page 17 Monday, September 14, 2009 2:53 PM CHAPTER TWO L AUNCH SYSTEMS databk7_collected.book Page 18 Monday, September 14, 2009 2:53 PM databk7_collected.book Page 19 Monday, September 14, 2009 2:53 PM CHAPTER TWO L AUNCH SYSTEMS Introduction Launch systems provide access to space, necessary for the majority of NASA’s activities. During the decade from 1989–1998, NASA used two types of launch systems, one consisting of several families of expendable launch vehicles (ELV) and the second consisting of the world’s only partially reusable launch system—the Space Shuttle. A significant challenge NASA faced during the decade was the development of technologies needed to design and implement a new reusable launch system that would prove less expensive than the Shuttle. Although some attempts seemed promising, none succeeded. This chapter addresses most subjects relating to access to space and space transportation. It discusses and describes ELVs, the Space Shuttle in its launch vehicle function, and NASA’s attempts to develop new launch systems. Tables relating to each launch vehicle’s characteristics are included. The other functions of the Space Shuttle—as a scientific laboratory, staging area for repair missions, and a prime element of the Space Station program—are discussed in the next chapter, Human Spaceflight. This chapter also provides a brief review of launch systems in the past decade, an overview of policy relating to launch systems, a summary of the management of NASA’s launch systems programs, and tables of funding data. The Last Decade Reviewed (1979–1988) From 1979 through 1988, NASA used families of ELVs that had seen service during the previous decade. -
Safety Consideration on Liquid Hydrogen
Safety Considerations on Liquid Hydrogen Karl Verfondern Helmholtz-Gemeinschaft der 5/JULICH Mitglied FORSCHUNGSZENTRUM TABLE OF CONTENTS 1. INTRODUCTION....................................................................................................................................1 2. PROPERTIES OF LIQUID HYDROGEN..........................................................................................3 2.1. Physical and Chemical Characteristics..............................................................................................3 2.1.1. Physical Properties ......................................................................................................................3 2.1.2. Chemical Properties ....................................................................................................................7 2.2. Influence of Cryogenic Hydrogen on Materials..............................................................................9 2.3. Physiological Problems in Connection with Liquid Hydrogen ....................................................10 3. PRODUCTION OF LIQUID HYDROGEN AND SLUSH HYDROGEN................................... 13 3.1. Liquid Hydrogen Production Methods ............................................................................................ 13 3.1.1. Energy Requirement .................................................................................................................. 13 3.1.2. Linde Hampson Process ............................................................................................................15 -
Commercial Orbital Transportation Services
National Aeronautics and Space Administration Commercial Orbital Transportation Services A New Era in Spaceflight NASA/SP-2014-617 Commercial Orbital Transportation Services A New Era in Spaceflight On the cover: Background photo: The terminator—the line separating the sunlit side of Earth from the side in darkness—marks the changeover between day and night on the ground. By establishing government-industry partnerships, the Commercial Orbital Transportation Services (COTS) program marked a change from the traditional way NASA had worked. Inset photos, right: The COTS program supported two U.S. companies in their efforts to design and build transportation systems to carry cargo to low-Earth orbit. (Top photo—Credit: SpaceX) SpaceX launched its Falcon 9 rocket on May 22, 2012, from Cape Canaveral, Florida. (Second photo) Three days later, the company successfully completed the mission that sent its Dragon spacecraft to the Station. (Third photo—Credit: NASA/Bill Ingalls) Orbital Sciences Corp. sent its Antares rocket on its test flight on April 21, 2013, from a new launchpad on Virginia’s eastern shore. Later that year, the second Antares lifted off with Orbital’s cargo capsule, (Fourth photo) the Cygnus, that berthed with the ISS on September 29, 2013. Both companies successfully proved the capability to deliver cargo to the International Space Station by U.S. commercial companies and began a new era of spaceflight. ISS photo, center left: Benefiting from the success of the partnerships is the International Space Station, pictured as seen by the last Space Shuttle crew that visited the orbiting laboratory (July 19, 2011). More photos of the ISS are featured on the first pages of each chapter. -
Twolstage REUSABLE LAUNCH SYSTEM UTILIZING a WINGED CORE VEHICLE and GLIDEBACK BOOSTERS
NASA Technical Memorandum 101513 I. TWOlSTAGE REUSABLE LAUNCH SYSTEM UTILIZING A WINGED CORE VEHICLE AND GLIDEBACK BOOSTERS Ian 0. MacConochie James A. Martin James S. Wood Miles 0. Duquette July 1989 - (flASA-TM-lo%!513) TUO-STaGE REUSABLE UUUCH B89-268 78 t SYSTEil UTILIBIFSG A UIBCBD COBE VlzEICLE BllD 6UDBBACX BOOSTERS (HAS., Langley Besearch Center) 21 p CSCL 22B Unclas # 63/16 0324583 National Aeronautics and Space Administration Langley Research Center Hampton, Virginia 23665 TWO-STAGE REUSABLE LAUNCH SYSTEM UTILIZING A WINGED CORE VEHICLE AND GLIDEBACK BOOSTERS BY Ian 0. MacConochie James A. Martin James S. Wood* Miles 0. Duquette* ABSTRACT A near-term technology launch system is descrlbed in which Space Shuttle main engines are used on a manned orbiter and also on twin strap-on unmanned boosters. The orbiter is configured with a circular body and clipped delta wings. The twin strap-on boosters have a circular body and deployable oblique wings for the glideback recovery. The dry and gross weights of the system, capable of delivering 70 klb of cargo to orbit, are compared with the values for the current Shuttle and a core vehicle with hydrocarbon-fuel ed boosters. INTRODUCTION In recent conceptual design studies of launch vehicles (Ref. l), emphasis has been placed on reducing operational complexity by employing comnonality in systems and propellants. In this regard, a launch vehicle has been configured in which liquid oxygen, liquid hydrogen, and current Space Shuttle main engines are used in both a manned core vehicle (orbiting stage) and its strap-on unmanned boosters. The principal objective of this study was to investigate the size and performance of an all-oxygen/hydrogen system using fixed numbers of Shuttle main engines. -
The New American Space Age: a Progress Report on Human Spaceflight the New American Space Age: a Progress Report on Human Spaceflight the International Space
The New American Space Age: A PROGRESS REPORT ON HUMAN SpaCEFLIGHT The New American Space Age: A Progress Report on Human Spaceflight The International Space Station: the largest international scientific and engineering achievement in human history. The New American Space Age: A Progress Report on Human Spaceflight Lately, it seems the public cannot get enough of space! The recent hit movie “Gravity” not only won 7 Academy Awards – it was a runaway box office success, no doubt inspiring young future scientists, engineers and mathematicians just as “2001: A Space Odyssey” did more than 40 years ago. “Cosmos,” a PBS series on the origins of the universe from the 1980s, has been updated to include the latest discoveries – and funded by a major television network in primetime. And let’s not forget the terrific online videos of science experiments from former International Space Station Commander Chris Hadfield that were viewed by millions of people online. Clearly, the American public is eager to carry the torch of space exploration again. Thankfully, NASA and the space industry are building a host of new vehicles that will do just that. American industry is hard at work developing new commercial transportation services to suborbital altitudes and even low Earth orbit. NASA and the space industry are also building vehicles to take astronauts beyond low Earth orbit for the first time since the Apollo program. Meanwhile, in the U.S. National Lab on the space station, unprecedented research in zero-g is paving the way for Earth breakthroughs in genetics, gerontology, new vaccines and much more. -
First Stage of a Highly Reliable Reusable Launch System
First Stage of a Highly Reliable Reusable Launch System * $ Kurt J. Kloesel , Jonathan B. Pickrelf, and Emily L. Sayles NASA Dryden Flight Research Center, Edwards, California, 93523-0273 Michael Wright § NASA Goddard Space Flight Center, Greenbelt, Maryland, 20771-0001 Darin Marriott** Embry-Riddle University, Prescott, Arizona, 86301-3720 Dr. Leo Hollandtf General Atomics Electromagnetic Systems Division, San Diego, California, 92121-1194 Dr. Stephen Kuznetsov$$ Power Superconductor Applications Corporation, New Castle, Pennsylvania, 16101-5241 Electromagnetic launch assist has the potential to provide a highly reliable reusable first stage to a space access system infrastructure at a lower overall cost. This paper explores the benefits of a smaller system that adds the advantages of a high specific impulse air-breathing stage and supersonic launch speeds. The method of virtual specific impulse is introduced as a tool to emphasize the gains afforded by launch assist. Analysis shows launch assist can provide a 278-s virtual specific impulse for a first-stage solid rocket. Additional trajectory analysis demonstrates that a system composed of a launch-assisted first-stage ramjet plus a bipropellant second stage can provide a 48-percent gross lift-off weight reduction versus an all-rocket system. The combination of high-speed linear induction motors and ramjets is identified, as the enabling technologies and benchtop prototypes are investigated. The high-speed response of a standard 60 Hz linear induction motor was tested with a pulse width modulated variable frequency drive to 150 Hz using a 10-lb load, achieving 150 mph. A 300-Hz stator-compensated linear induction motor was constructed and static-tested to 1900 lbf average. -
Facing the Heat Barrier: a History of Hypersonics First Thoughts of Hypersonic Propulsion
Facing the Heat Barrier: A History of Hypersonics First Thoughts of Hypersonic Propulsion Republic’s Aerospaceplane concept showed extensive engine-airframe integration. (Republic Aviation) For takeoff, Lockheed expected to use Turbo-LACE. This was a LACE variant that sought again to reduce the inherently hydrogen-rich operation of the basic system. Rather than cool the air until it was liquid, Turbo-Lace chilled it deeply but allowed it to remain gaseous. Being very dense, it could pass through a turbocom- pressor and reach pressures in the hundreds of psi. This saved hydrogen because less was needed to accomplish this cooling. The Turbo-LACE engines were to operate at chamber pressures of 200 to 250 psi, well below the internal pressure of standard rockets but high enough to produce 300,000 pounds of thrust by using turbocom- pressed oxygen.67 Republic Aviation continued to emphasize the scramjet. A new configuration broke with the practice of mounting these engines within pods, as if they were turbojets. Instead, this design introduced the important topic of engine-airframe integration by setting forth a concept that amounted to a single enormous scramjet fitted with wings and a tail. A conical forward fuselage served as an inlet spike. The inlets themselves formed a ring encircling much of the vehicle. Fuel tankage filled most of its capacious internal volume. This design study took two views regarding the potential performance of its engines. One concept avoided the use of LACE or ACES, assuming again that this craft could scram all the way to orbit. Still, it needed engines for takeoff so turbo- ramjets were installed, with both Pratt & Whitney and General Electric providing Lockheed’s Aerospaceplane concept. -
PRE-X EXPERIMENTAL RE-ENTRY LIFTING BODY: DESIGN of FLIGHT TEST EXPERIMENTS for CRITICAL AEROTHERMAL PHENOMENA Paolo Baiocco
PRE-X EXPERIMENTAL RE-ENTRY LIFTING BODY: DESIGN OF FLIGHT TEST EXPERIMENTS FOR CRITICAL AEROTHERMAL PHENOMENA Paolo Baiocco * * CNES Direction des Lanceurs Rond Point de l’Espace – 91023 Evry Cedex, France Phone : +33 (0)1.60.87.72.14 Fax : +33 (0)1.60.87.72.66 E-mail : [email protected] ABSTRACT Atmospheric glided re-entry is one of the main key technologies for future space vehicle applications. In this frame Pre-X is the CNES proposal to perform in-flight experimentation mainly on reusable thermal protections, aero-thermo-dynamics and guidance to secure the second generation of re-entry X vehicles. This paper describes the system principles and main aerothermodynamic experiences currently foreseen on board the vehicle. A preliminary in-flight experimentation and measurement plan has been assessed defining the main objectives in terms of reusable Thermal Protection System (TPS) and Aero Thermo Dynamics (ATD) data on the most critical phenomena. This flight aims also to take the opportunity to fly some innovative measurements. A complete system loop has been performed including the operations, ground system assessment, and visibility analysis. The vehicle re-entry point is at 120 km and the mission objectives are fulfilled between Mach 25 and 5. Then the vehicle has to pass to subsonic speeds, the parachute opens and it is finally recovered in the sea. The VEGA and DNEPR launch vehicles are compatible of the Pre-X experimental vehicle. ACRONYMS ACS Attitude Control System AEDB Aero Dynamic Data Base AoA Angle of Attack ARD Atmospheric Re-entry Demonstrator ATD Aero Termo Dynamics ATDB Aero Termodynamic Data Base CDG Centre of Gravity CFA Continuum Flow Aerodynamics CFD Computational Fluid Dynamics CMC Ceramic Matrix Composite C/SiC Carbon / Silicon Carbide FCS Flight Control System FEI Flexible External Insulation GNC Guidance Navigation and Control LTT Laminar to Turbulent Transition LV Launch Vehicle RCS Reaction Control System SEL Electrical System Baiocco, P. -
Lift and Drag Characteristics of the HL-10 Lifting Body During Subsonic
NASA TECHNICAL NOTE NASA TN D-6263 - _- e,.i KIRTLAkD AFB,N.M, LIFT AND DRAG CHARACTERISTICS . OF THE HL-IO LIFTING BODY DURING SUBSONIC GLIDING FLIGHT b . .. by Jon S. Pyle h Flight Research Center Edwards, Cali$ 93523 NATIONAL AERONAUTICS AND SPACE ADMINISTRATION WASHINGTON, 0. C. MARCH 1971 TECH LIBRARY KAFB, NM I111111 11111 11111 11111 /Ill/lllll1111111111111 0333074 1. Report No. 2. Government Accession No. 3. Recipient's Catalog No. NASA TN D-6263 I 4. Title and Subtitle 5. Report Date LIFT AND DRAG CHARACTERISTICS OF THE HL-10 LIFTING BODY March 1973 DURING SUBSONIC GLIDING FLIGHT 6. Performing Organization Code 7. Author(s) 8. Performing Organization Report No. Jon S. Pyle H-608 10. Work Unit No. 727-00-00-01-24 ?- 9. Performing Organization Name and Address NASA Flight Research Center 11. Contract or Grant No. P. 0. Box 273 Edwards, California 93523 d 13. Type of Report and Period Covered 112. Sponsoring Agency Name and Address Technical Note National Aeronautics and Space Administration 14. Sponsoring Agency Code Washington, D. C. 20546 15. Supplementary Notes 16. Abstract Subsonic lift and drag data obtained during the HL-10 lifting body glide flight program are presented for four configurations for angles of attack from 5" to 26" and Mach numbers from 0.35 to 0. 62. These flight data, where applicable, are compared with results from small-scale wind-tunnel tests of an HL-10 model, full-scale wind-tunnel results obtained with the flight vehicle, and flight results for the M2-F2 lifting body. The lift and drag characteristics obtained from the HL-10 flight results showed that a severe flow problem existed on the upper surface of the vehicle during the first flight test. -
Increasing Launch Rate and Payload Capabilities
Aerial Launch Vehicles: Increasing Launch Rate and Payload Capabilities Yves Tscheuschner1 and Alec B. Devereaux2 University of Colorado, Boulder, Colorado Two of man's greatest achievements have been the first flight at Kitty Hawk and pushing into the final frontier that is space. Air launch systems aim to combine these great achievements into a revolutionary way to deliver satellites, cargo and eventually people into space. Launching from an aircraft has many advantages, including the ability to launch at any inclination and from above bad weather, which could delay ground launches. While many concepts for launching rockets from an airplane have been developed, very few have made it past the drawing board. Only the Pegasus and, to a lesser extent, SpaceShipOne have truly shown the feasibility of such a system. However, a recent push for rapid, small payload to orbit launches by the military and a general need for cheaper, heavy lift options are leading to an increasing interest in air launch methods. In order for the efficiency and flexibility of the system to be realized, however, additional funding and research are necessary. Nomenclature ALASA = airborne launch assist space access ALS = air launch system DARPA = defense advanced research project agency LEO = low Earth orbit LOX = liquid oxygen RP-1 = rocket propellant 1 MAKS = Russian air launch system MECO = main engine cutoff SS1 = space ship one SS2 = space ship two I. Introduction W hat typically comes to mind when considering launching people or satellites to space are the towering rocket poised on the launch pad. These images are engraved in the minds of both the public and scientists alike. -
Round Trip to Orbit: Human Spaceflight Alternatives
Round Trip to Orbit: Human Spaceflight Alternatives August 1989 NTIS order #PB89-224661 Recommended Citation: U.S. Congress, Office of Technology Assessment, Round Trip to Orbit: Human Spaceflight Alternatives Special Report, OTA-ISC-419 (Washington, DC: U.S. Government Printing Office, August 1989). Library of Congress Catalog Card Number 89-600744 For sale by the Superintendent of Documents U.S. Government Printing Office, Washington, DC 20402-9325 (order form can be found in the back of this special report) Foreword In the 20 years since the first Apollo moon landing, the Nation has moved well beyond the Saturn 5 expendable launch vehicle that put men on the moon. First launched in 1981, the Space Shuttle, the world’s first partially reusable launch system, has made possible an array of space achievements, including the recovery and repair of ailing satellites, and shirtsleeve research in Spacelab. However, the tragic loss of the orbiter Challenger and its crew three and a half years ago reminded us that space travel also carries with it a high element of risk-both to spacecraft and to people. Continued human exploration and exploitation of space will depend on a fleet of versatile and reliable launch vehicles. As this special report points out, the United States can look forward to continued improvements in safety, reliability, and performance of the Shuttle system. Yet, early in the next century, the Nation will need a replacement for the Shuttle. To prepare for that eventuality, NASA and the Air Force have begun to explore the potential for advanced launch systems, such as the Advanced Manned Launch System and the National Aerospace Plane, which could revolutionize human access to space.