Ivan Kurunov Aitber Bizhanov Stiff Extrusion Briquetting in Metallurgy Topics in Mining, Metallurgy and Materials Engineering
Total Page:16
File Type:pdf, Size:1020Kb
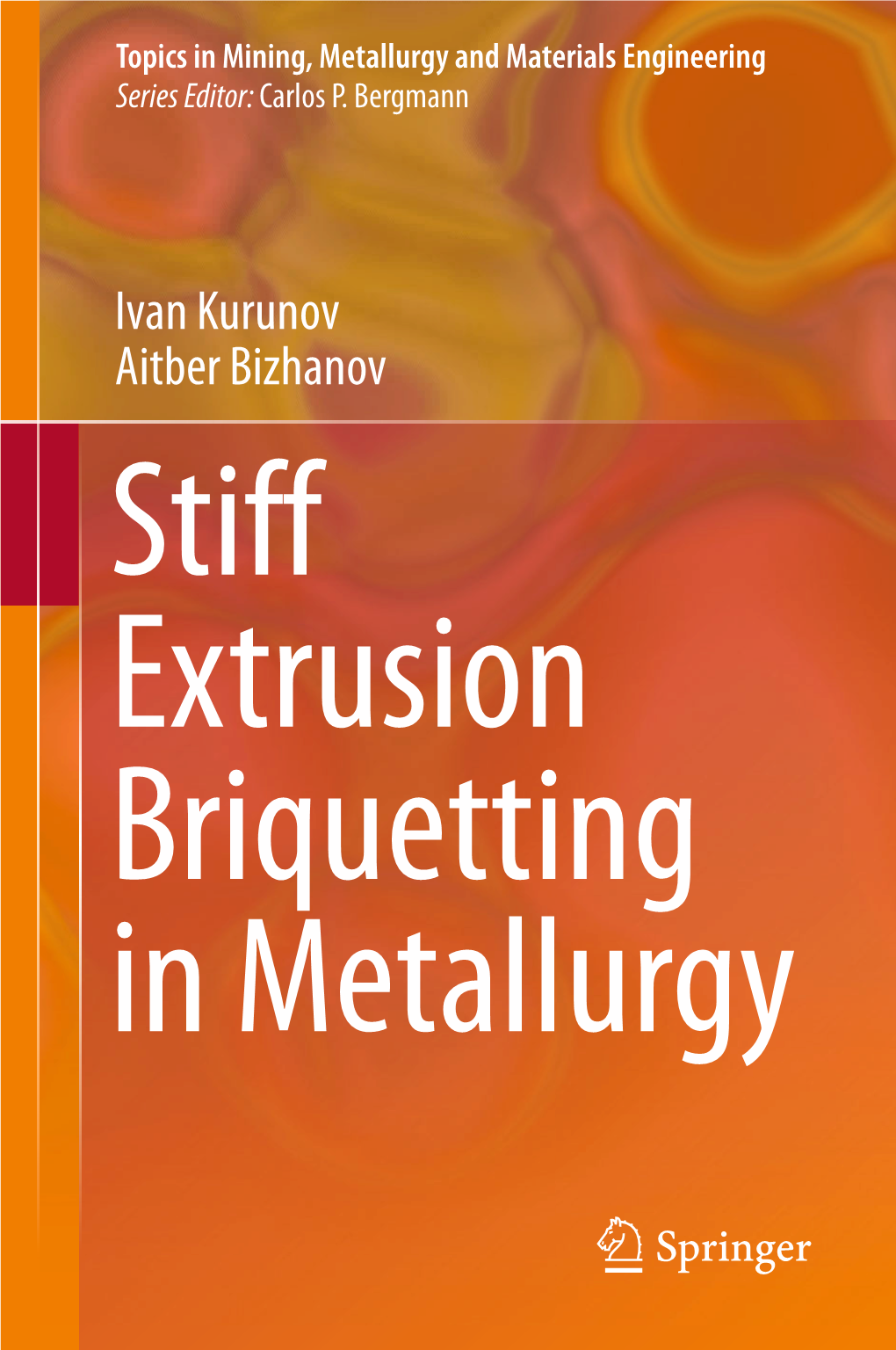
Load more
Recommended publications
-
Petrographic and Vitrinite Reflectance Analyses of a Suite of High Volatile Bituminous Coal Samples from the United States and Venezuela
Petrographic and vitrinite reflectance analyses of a suite of high volatile bituminous coal samples from the United States and Venezuela Open-File Report 2008-1230 U.S. Department of the Interior U.S. Geological Survey U.S. Department of the Interior Dirk A. Kempthorne, Secretary U.S. Geological Survey Mark D. Myers, Director U.S. Geological Survey, Reston, Virginia 2008 For product and ordering information: World Wide Web: http://www.usgs.gov/pubprod Telephone: 1-888-ASK-USGS For more information on the USGS—the Federal source for science about the Earth, its natural and living resources, natural hazards, and the environment: World Wide Web: http://www.usgs.gov Telephone: 1-888-ASK-USGS Suggested citation: Hackley, P.C., Kolak, J.J., 2008, Petrographic and vitrinite reflectance analyses of a suite of high volatile bituminous coal samples from the United States and Venezuela: U.S. Geological Survey Open-File Report 2008-1230, 36 p., http://pubs.usgs.gov/of/2008/1230. Any use of trade, product, or firm names is for descriptive purposes only and does not imply endorsement by the U.S. Government. Although this report is in the public domain, permission must be secured from the individual copyright owners to reproduce any copyrighted material contained within this report. ii Contents Introduction ........................................................................................................................................................................1 Methods ..............................................................................................................................................................................1 -
Update on Lignite Firing
Update on lignite firing Qian Zhu CCC/201 ISBN 978-92-9029-521-1 June 2012 copyright © IEA Clean Coal Centre Abstract Low rank coals have gained increasing importance in recent years and the long-term future of coal -derived energy supplies will have to include the greater use of low rank coal. However, the relatively low economic value due to the high moisture content and low calorific value, and other undesirable properties of lignite coals limited their use mainly to power generation at, or, close to, the mining site. Another important issue regarding the use of lignite is its environmental impact. A range of advanced combustion technologies has been developed to improve the efficiency of lignite-fired power generation. With modern technologies it is now possible to produce electricity economically from lignite while addressing environmental concerns. This report reviews the advanced technologies used in modern lignite-fired power plants with a focus on pulverised lignite combustion technologies. CFBC combustion processes are also reviewed in brief and they are compared with pulverised lignite combustion technologies. Acronyms and abbreviations CFB circulating fluidised bed CFBC circulating fluidised bed combustion CFD computational fluid dynamics CV calorific value EHE external heat exchanger GRE Great River Energy GWe gigawatts electric kJ/kg kilojoules per kilogram kWh kilowatts hour Gt billion tonnes FBC fluidised bed combustion FBHE fluidised bed heat exchanger FEGT furnace exit gas temperature FGD flue gas desulphurisation GJ -
Maceral Types and Quality of Coal in the Tuli Coalfield: a Case
applied sciences Article Maceral Types and Quality of Coal in the Tuli Coalfield: A Case Study of Coal in the Madzaringwe Formation in the Vele Colliery, Limpopo Province, South Africa Elelwani Denge * and Christopher Baiyegunhi Department of Geology and Mining, University of Limpopo, Private Bag X1106, Sovenga 0727, South Africa; [email protected] * Correspondence: [email protected] Featured Application: Authors are encouraged to provide a concise description of the specific application or a potential application of the work. This section is not mandatory. Abstract: The Madzaringwe Formation in the Vele colliery is one of the coal-bearing Late Palaeozoic units of the Karoo Supergroup, consisting of shale with thin coal seams and sandstones. Maceral group analysis was conducted on seven representative coal samples collected from three existing boreholes—OV125149, OV125156, and OV125160—in the Vele colliery to determine the coal rank and other intrinsic characteristics of the coal. The petrographic characterization revealed that vitrinite is the dominant maceral group in the coals, representing up to 81–92 vol.% (mmf) of the total sample. Collotellinite is the dominant vitrinite maceral, with a total count varying between 52.4 vol.% (mmf) and 74.9 vol.% (mmf), followed by corpogelinite, collodetrinite, tellinite, and pseudovitrinite with a Citation: Denge, E.; Baiyegunhi, C. count ranging between 0.8 and 19.4 vol.% (mmf), 1.5 and 17.5 vol.% (mmf), 0.8 and 6.5 vol.% (mmf) Maceral Types and Quality of Coal in the Tuli Coalfield: A Case Study of and 0.3 and 5.9 vol.% (mmf), respectively. The dominance of collotellinite gives a clear indication Coal in the Madzaringwe Formation that the coals are derived from the parenchymatous and woody tissues of roots, stems, and leaves. -
Lithofacies, Depositional Environments, and Regional Stratigraphy of the Lower Eocene Ghazij Formation, Balochistan, Pakistan
U.S. Department of the Interior U.S. Geological Survey Lithofacies, Depositional Environments, and Regional Stratigraphy of the Lower Eocene Ghazij Formation, Balochistan, Pakistan U.S. Geological Survey Professional Paper 1599 Prepared in cooperation with the Geological Survey of Pakistan A Cover. Exposures of the lower Eocene Ghazij Formation along the northeast flank of the Sor Range, Balochistan, Pakistan. Photograph by Stephen B. Roberts. Lithofacies, Depositional Environments, and Regional Stratigraphy of the Lower Eocene Ghazij Formation, Balochistan, Pakistan By Edward A. Johnson, Peter D. Warwick, Stephen B. Roberts, and Intizar H. Khan U.S. GEOLOGICAL SURVEY PROFESSIONAL PAPER 1599 Prepared in cooperation with the Geological Survey of Pakistan UNITED STATES GOVERNMENT PRINTING OFFICE, WASHINGTON : 1999 U.S. DEPARTMENT OF THE INTERIOR BRUCE BABBITT, Secretary U.S. GEOLOGICAL SURVEY Charles G. Groat, Director For sale by U.S. Geological Survey, Information Services Box 25286, Federal Center Denver, CO 80225 Any use of trade, product, or firm names in this publication is for descriptive purposes only and does not imply endorsement by the U.S. Government Library of Congress Cataloging-in-Publication Data Lithofacies, depositional environments, and regional stratigraphy of the lower Eocene Ghazij Formation, Balochistan, Pakistan / by Edward A. Johnson . .[et al.]. p. cm.—(U.S. Geological Survey professional paper ; 1599) "Prepared in cooperation with the Geological Survey of Pakistan." Includes bibliographical references. 1. Geology, Stratigraphic—Eocene. 2. Geology—Pakistan— Balochistan. 3. Coal—Geology—Pakistan—Balochistan. 4. Ghazij Formation (Pakistan). I. Johnson, Edward A. (Edward Allison), 1940- . II. Series. QE692.2.L58 1999 553.2'4'0954915—dc21 98-3305 ISBN=0-607-89365-6 CIP CONTENTS Abstract.......................................................................................................................... -
Geochemistry, Petrology, and Palynology of the Princess No. 3 Coal, Greenup County, Kentucky
University of Kentucky UKnowledge Center for Applied Energy Research Faculty Publications Center for Applied Energy Research 12-2020 Geochemistry, Petrology, and Palynology of the Princess No. 3 Coal, Greenup County, Kentucky Madison M. Hood University of Kentucky, [email protected] Cortland F. Eble University of Kentucky, [email protected] James C. Hower University of Kentucky, [email protected] Shifeng Dai China University of Mining and Technology, China Follow this and additional works at: https://uknowledge.uky.edu/caer_facpub Part of the Geology Commons, and the Mining Engineering Commons Right click to open a feedback form in a new tab to let us know how this document benefits ou.y Repository Citation Hood, Madison M.; Eble, Cortland F.; Hower, James C.; and Dai, Shifeng, "Geochemistry, Petrology, and Palynology of the Princess No. 3 Coal, Greenup County, Kentucky" (2020). Center for Applied Energy Research Faculty Publications. 34. https://uknowledge.uky.edu/caer_facpub/34 This Article is brought to you for free and open access by the Center for Applied Energy Research at UKnowledge. It has been accepted for inclusion in Center for Applied Energy Research Faculty Publications by an authorized administrator of UKnowledge. For more information, please contact [email protected]. Geochemistry, Petrology, and Palynology of the Princess No. 3 Coal, Greenup County, Kentucky Digital Object Identifier (DOI) https://doi.org/10.1007/s40789-020-00298-0 Notes/Citation Information Published in International Journal of Coal Science & Technology, v. 7, issue 4. © The Author(s) 2020 This article is licensed under a Creative Commons Attribution 4.0 International License, which permits use, sharing, adaptation, distribution and reproduction in any medium or format, as long as you give appropriate credit to the original author(s) and the source, provide a link to the Creative Commons licence, and indicate if changes were made. -
Due Diligence and Valuation Report
Due Diligence and Valuation Report Arrowhead Code: 94-01-04 Coverage initiated: 26 11 2015 Company: Environmental Clean Technologies This document: 29 09 2016 Limited i Fair share value bracket: AUD0.033 to AUD0.042 Ticker: ASX:ESI Share price on date: AUD0.019ii Headquarters: Victoria, Australia Analyst Team Managing Director: Ashley Moore Shruti Gupta Website: http://www.ectltd.com.au/ [email protected] allows for flexibility in expansion as needed, thus Market Data eliminating the need to commit to bulk capacity 52-Week Range: AUD 0.011 – AUD 0.029iii while setting up a plant. Average Daily Volume: 3,962,478 iv Market Cap. on date: AUD 52.0 MMv Key Technologies – Matmor The Matmor process produces primary iron Financial Forecast Data (in AUD) through the reduction of iron oxides. Similar to ‘17E ‘18E ‘19E ‘20E ‘21E ‘22E Coldry, Matmor has a simple design, and is cost- High profit/ (1.6) 4.4 2.3 1.7 1.9 2.1 effective. The process uses Coldry’s output (loss) MM instead of the more-expensive coking coal as a High EPS (0.06) 0.17 0.09 0.06 0.07 0.08 (AUD cents) reducing agent. Low profit/ (2.1) 3.6 1.5 1.0 1.3 1.4 Compared to the traditional blast furnace route to (loss) MM produce iron, Matmor benefits from lower cost of Low EPS (0.08) 0.14 0.06 0.04 0.05 0.05 (AUD cents) feedstock owing to usage of low-grade coal in the process. Further, Matmor could also process iron Fiscal Year (FY) 1st July – 30th June ore fines and various iron oxide feed that is not suitable for production through the conventional Summary blast furnace process. -
Techno-Economic Feasibility Study – Public Release Document
Monday, 8 August 2016 Shareholder Update – India Activity Techno-Economic Feasibility Study – Public Release Document Dear Shareholders, We are pleased to provide to you the public release of the Techno-Economic Feasibility (TEF) study conducted on the proposed Coldry-Matmor Integrated Steel Plant. ECT would like to formally acknowledge and thank our project partners, NLC and NMDC, together with TEF Study Working Group members Dastur and Thermax. The TEF Study report contains detailed information regarding assessment of our technologies operating together, projected forwards to commercial scale. The intent of the report is to demonstrate not only the technical feasibility of our technologies, but also the comparative economic performance versus incumbent technology options. In demonstrating that strong relative performance, we underpin the business case to invest in the development stages ahead. The report in its original form contains significant volumes of information of a confidential nature, the release of which could contravene our confidentiality obligations with our partners and may impact on our ability to deliver value from the commercialisation of our technologies. The report was also a time based document, which contained information current as of the issue date. Our discussions have continued with our partners since that time, and this report does not capture changes in status associated with those discussions now underway. ECT is very encouraged by the results of the study, and by the response to the report received from our partners, NLC and NMDC and look forward to working though the development of project structuring and agreements and continuation of the detailed design program. Sincerely, Ashley Moore Managing Director For further information, contact: Ashley Moore – Managing Director [email protected] About ECT ECT is in the business of commercialising leading-edge coal and iron making technologies, which are capable of delivering financial and environmental benefits. -
YES BANK to Partner with ECT, Australia to Promote Clean Coal Technology in India
YES BANK to Partner with ECT, Australia to Promote Clean Coal Technology in India YES BANK to advise ECT in commercializing their patented– ‘Coldry’ technology in Indian markets Mumbai, January 8, 2014: YES BANK, India’s fourth largest private sector Bank, jointly with Greenard Willing, an Australian corporate advisory firm, has entered into an advisory agreement with Australia based Environmental Clean Technologies (ECT). The agreement aims to assist ECT in commercialization and technology transfer of Clean Coal technologies in India via a systematic knowledge-based approach. YES BANK's Sustainable Investment Banking Group along with Greenard Willing, will jointly set in place the structures and partners for implementation of ECT's manufacturing strategy in India, to deliver a lower capital cost structure for Coldry plant & equipment and also in the development of commercial scale Coldry processing plants for Indian and International projects. Speaking on the agreement, Aditya Sanghi, Senior MD, Investment Banking, YES BANK stated, “ECT’s Coldry technology offers sustainable and long term solution to meet the growing energy demands of India while mitigating the daunting issues of climate change. YES BANK has a strong commitment to mainstreaming sustainability within the industry and this partnership with ECT is a natural extension of our efforts to create sustainable development of India. YES BANK’s Sustainable Investment Banking team has in the past successfully delivered technology commercialization solutions to international clean technology ventures. It offers a unique knowledge-driven approach and has a strong understanding of the space with deep rooted relationships.” ECT's Managing Director Ashley Moore added, " We expect to conclude this initial stage of activities with YES BANK and Greenard Willing over the next quarter, and deliver qualified & capable selection of future Coldry plant and equipment suppliers, able to deliver, globally, at a highly competitive cost. -
Data Collection Survey on Thar Coal Field in Pakistan FINAL REPORT
Islamic Republic of Pakistan Data Collection Survey on Thar Coal Field In Pakistan FINAL REPORT FEBRUARY 2013 JAPAN INTERNATIONAL COOPERATION AGENCY (JICA) Nippon Koei Co., Ltd. Coal Resources & Mining Engineering Co., Ltd. 4R JR 13-014 FINAL REPORT for The Data Collection Survey on Thar Coal Field in Pakistan CONTENTS Executive Summary Location Map Chapter 1 Introduction 1.1 Background of the Survey ......................................................................................................... 1 - 1 1.1.1 Present Situation of Power Supply and Demand ................................................................. 1 - 1 1.1.2 Political Measures on Energy Sector and Development Plan .............................................. 1 - 2 1.1.3 Latest Government Decision ................................................................................................ 1 - 3 1.2 Objective of Survey .................................................................................................................... 1 - 3 1.2.1 Objective of the Survey ........................................................................................................ 1 - 3 1.2.2 Survey Area ........................................................................................................................ 1 - 3 1.3 Scope of the Survey .................................................................................................................. 1 - 3 1.4 Survey Schedule ...................................................................................................................... -
Proximate Analysis, Calorific Value and Trace Metal Analysis of Coal
SHORTMuhammad COMMUNICATION Akbar et al., J.Chem.Soc.Pak., Vol. 41, No. 03, 2019 555 Proximate and Trace Metal Analysis of Pakistani Coal 1Muhammad Akbar, 1Muhammad Abdul Qadir, 2Ayoub Rashid, 3Abrar Hussain, 4Khalid Bhatti and 2Ahmad Adnan* 1Institute of Chemistry, University of the Punjab, Lahore, Pakistan. 2Department of Chemistry, Government College University, Lahore, Pakistan, 3University of Education, Lahore, Pakistan. 4Government P/G College Fatepur, Layyah, Pakistan. [email protected]* (Received on 9th May 2018, accepted in revised form 7th March 2019) Summary: Pakistan is facing severe energy crisis with depleting water and gas reservoirs. Pakistan has large reserves of coal found exclusively in Sindh, Baluchistan and Punjab, but this coal is regarded as low rank (Lignite grade). Present work aimed at the determination of the quality of coal by Proximate and trace metal analysis. Three coalfields including Dukki (Baluchistan), Chamalang (Baluchistan) and Salt range (Punjab) were selected for study. Proximate analysis and calorific values of coal samples were carried out using reported protocols and trace metal analysis including Co, Cr, Ni, Pb, Zn, Cd and Cu was done by ICP employing standard procedures. Results suggested that the coal belonging to these areas is of sub-bituminous type. Chamalang coal of Baluchistan was found to be of better quality than Dukki and Salt Range coal. Keywords: Coal, Proximate analysis, Calorific value, Ultimate analysis, Trace metals. Introduction For the last couple of decades, power when fired in power generation, incineration plants, shortage has become an enduring problem around the smelting, or combustion engines produces a variety plant, particularly in developing countries like of products responsible for environmental and health Pakistan. -
Mineralogy and Geochemistry of Permian Coal Seams of the Sydney Basin, Australia, and the Songzao Coalfield, Sw China
MINERALOGY AND GEOCHEMISTRY OF PERMIAN COAL SEAMS OF THE SYDNEY BASIN, AUSTRALIA, AND THE SONGZAO COALFIELD, SW CHINA BY Lei Zhao B.E. (Environmental Engineering) M.Sc. (Environmental Science) Supervisors: Professor Colin Ward Dr Ian Graham Dr David French A dissertation submitted in fulfillment of the requirement for the degree of Doctor of Philosophy In Applied Geology School of Biological, Earth and Environmental Sciences University of New South Wales, Sydney, Australia 2012 ACKNOWLEDGEMENTS I would like to thank the following people and organisations for their assistance during my study and in completing this thesis. I sincerely appreciate my supervisor, Prof. Colin Ward, and co-supervisors, Dr. Ian Graham and Dr. David French, for providing training opportunities, consistent professional advice, and the immeasurable time they committed towards this work. Thank you for your assistance and encouragement throughout this study and the writing-up of the thesis. I would like to gratefully acknowledge the China Scholarship Council for financial support during this study. I am indebted to Dr. Chen-Lin Chou of Illinois State Geological Survey, and Prof. Kuilli Jin, Prof. Shifeng Dai and Prof. Longyi Shao of China University of Mining and Technology (Beijing), for their support and advice on my PhD study. I also would like to thank Dr. Zhongsheng Li of CSIRO for his professional support and technical assistance during the duration of my study. Thanks are expressed to CSIRO Energy Technology, Prof. Shifeng Dai of China University of Mining and Technology (Beijing), and Peter Krempin of the Austar coal mine, for providing samples and other relevant data for conducting the investigation. -
Charcoal, Forests, and Earth's Palaeozoic Geochemical Oxygen Cycle
i UNIVERSITY OF SOUTHAMPTON FACULTY OF NATURAL AND ENVIRONMENTAL SCIENCES Ocean and Earth Science CHARCOAL, FORESTS, AND EARTH’S PALAEOZOIC GEOCHEMICAL OXYGEN CYCLE by David Kevin Carpenter Thesis submitted in partial fulfilment of the requirements for the degree of Doctor of Philosophy September 2016 ii iii UNIVERSITY OF SOUTHAMPTON ABSTRACT FACULTY OF NATURAL AND ENVIRONMENTAL SCIENCES Ocean and Earth Sciences Thesis submitted in partial fulfilment of the requirements for the degree of Doctor of Philosophy CHARCOAL, FORESTS AND EARTH’S PALAEOZOIC GEOCHEMICAL OXYGEN CYCLE By David Kevin Carpenter It is widely assumed that the Devonian transition to a forested planet, and subsequent massive expansion of coal-swamp environments during the Carboniferous, significantly increased the production and retention of atmospheric oxygen by fuelling increased organic carbon burial, fundamentally altering the biotic regulation of Earth's long-term oxygen cycle. Modelling approaches to the reconstruction of Phanerozoic pO2 are hampered by the unavoidable complexity of the models, and the difficulty in testing their inherent assumptions. This has led to a wide variety of predictions for atmospheric O2 during this critical 120 million-year interval. The abundance of microscopic charcoal (‘inertinite’) in coals has previously been used as the basis for a direct pO2 reconstruction, on the assumption that fire activity correlates with oxygen supply; however, coals are scarce prior to the Viséan. A high-resolution Devonian–Carboniferous dataset charting inertinite abundance in dispersed organic matter indicates that O2 could not have fallen below c. 16.5% vol. at any stage, and that a previously identified Mid-Devonian ‘charcoal gap’ is most likely an artefact of low sampling density.