Cross-Linking Modification of Ammonium Polyphosphate Via Ionic
Total Page:16
File Type:pdf, Size:1020Kb
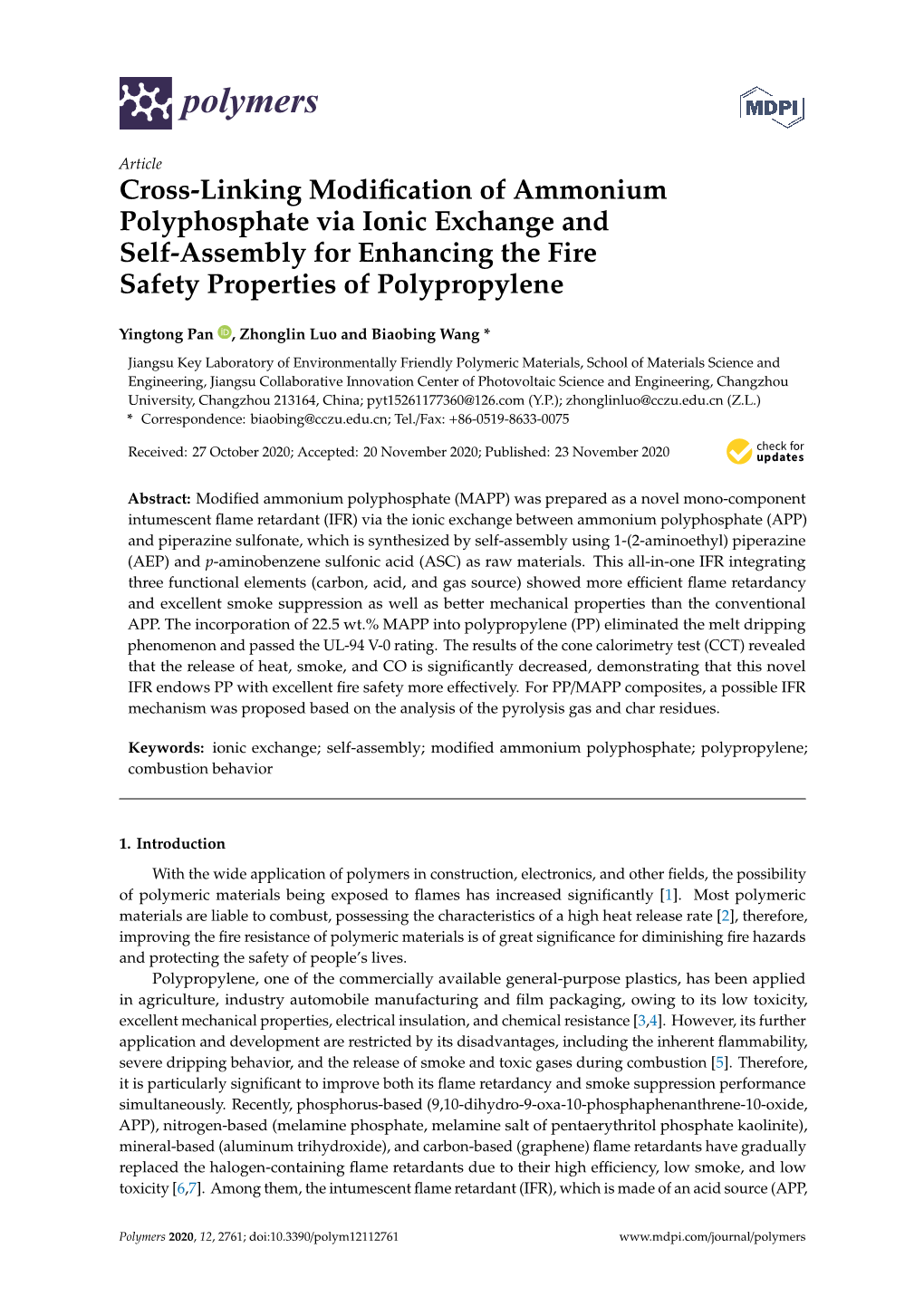
Load more
Recommended publications
-
Evaluation of Liquid Ammonium Polyphosphate As a Carrier of Iron and Zinc
EVALUATION OF LIQUID AMMONIUM POLYPHOSPHATE AS A CARRIER OF IRON AND ZINC by ; V<P RATMUNDO RALLAN GANIRON B. S. A., University of the Philippines, 1961 A MASTER'S THESIS submitted in partial fulfillment of the requirement for the degree MASTER OF SCIENCE Department of Agronomy KANSAS STATE UNIVERSITY Manhattan, Kansas 1966 Approved by: Jor Professor LP ZGGf it Tj( £/<?7 TABLE OF CONTENTS INTRODUCTION 1 REVIEW OF LITERATURE 3 Iron . 3 Zinc * MATERIALS AND METHODS 13 Fertiliser Materials 13 Field Experiments H Soil Sampling 20 Laaf Sampling 22 Chemical Analysis 22 (a) Zinc 22 (b) Iron 24 (c) Phosphorua 25 (d) Potassium •« 27 (a) Organic Matter 27 (f) pH 27 (g) Protain 27 RESULTS AND DISCUSSIONS 26 SUMMARY AND CONCLUSIONS 4$ ACKNOWLEDGMENT. 51 LITERATURE CITED 52 INTRODUCTION Increasing attention has baan focused to the need of fertilising with micronutrient elements to achieve maximum production and optimum quality of farm crops. The supply of these elements in the soil has become limited in some areas as a result of the introduction of high yielding varieties, better and more intensive cropping practices, and increased use of high analysis fertilisers. In some cases, the ob- served deficiencies of these micronutrients have been man- made due to addition of interfering elements for other pur- poses. For instance there is the copper induced iron chlorosis, copper being introduced as agricultural sprays and the phosphorus induced iron and zinc deficiencies, phos- phorus being introduced to meet the phosphorus requirement of farm crops. How to minimise such interactions and the problems of keeping these micronutrient elements available to the plants when applied to the soil have been the sub- ject of intensive researches. -
Effects of Different Sources of Fertilizer Nitrogen on Growth and Nutrition of Western Hemlock Seedlings
Effects of Different Sources U.S. Department of Agriculture Forest Service Pacific Northwest Forest of FertiIizer Nitrogen and Range Experiment Station Research Paper PNW-267 on Growth and Nutrition oJ February 1980 Western Hemlock Seedlings ---. --_. ------------------------ , I _J Authors M. A. RADWAN is Principal Plant Physiologist and DEAN S. DeBELL is Principal Silviculturist with the Forest Service, u.S. Department of Agriculture, Pacific Northwest Forest and Range Experiment Station, Forestry Sciences Laboratory, Olympia, Washington. En gl ish Equivalents 1 liter 0.2642 gallon 1 kilogram = 2.2046 pound 1 gram = 0.0353 ounce 1 centimeter = 0.3937 inch 1 kilogram per hectare 1.1206 pounds per acre (9/50C) + 32 = of EFFECTS OF DIFFERENT SOURCES OF FERTILIZER NITROGEN ON GROWTH AND NUTRITION OF WESTERN HEMLOCK Reference Abstract Radwan, M. A. , and Dean S. DeBell. 1980. Effects of different sources of fertilizer nitrogen on growth and nutrition of western hemlock seedlings. USDA For. Servo Res. Pap. PNW-267, 15 p. Pacific Northwest Forest and Range Experiment Station, Portland, Oregon. Twelve different nitrogen (N) fertilizer treatments were tested on potted western hemlock (Tsuga heterophylla (Raf. ) Sarg.) seedlings. Fertilizers affected soil N and pH, and growth and foliar chemical com position of seedlings. Ura plus N-Serve and sulfur-coated urea appear more promising for promoting growth than other fertilizers tested. Results, however, do not explain reported variability in response of hemlock stands to N fertilization. Keywords: Nitrogen fertilizer response, seedling growth, western hemlock, Tsuga heterophylla. RESEARCH SUMMARY Research Paper PNW-267 1980 The following fertilization treatments were applied in the spring to potted, 4-year-old western hemlock (Tsuga heterophylla (Raf. -
United States Patent (19) 11 Patent Number: 5,788,915 Blount (45) Date of Patent: Aug
IIIUSOO5788915A United States Patent (19) 11 Patent Number: 5,788,915 Blount (45) Date of Patent: Aug. 4, 1998 54 FLAME RETARDANT COMPOSITIONS 57 ABSTRACT UTILIZING PARTIALLY HYDROLYZED AMNO CONDENSATON COMPOUNDS Flame retardant compositions of this invention are produced by incorporating a partially index (LOI) hydrolyzed amino 76 Inventor: David H. Blount, 6728 Del Cerro condensation composition in a more flammable organic Blvd., San Diego, Calif. 92120 material. The partially hydrolyzed amino condensation com pounds are produced by heating urea or heating urea with (21) Appl. No.: 801,776 other nitrogen containing compounds that will condensate with or react with isocyanic acid and/or cyanic acid thereby 22 Filed: Feb. 14, 1997 producing an amino condensation compound which is then Related U.S. Application Data partially hydrolysis is done by reacting it with a limited amount of water. The partially hydrolyzed amino conden 62) Division of Ser. No. 723,779, Sep. 30, 1996. sation compounds may be used alone or may be mixed with or reacted with carbonization auxiliaries, aldehydes and (51) Int. Cl. ........................ C09K 21A00; C08G 12/12 fillers to produce a partially hydrolyzed amino condensation 52 U.S. Cl. ........................... 252/609; 528/259; 252/601 composition which is incorporated in more flammable 58) Field of Search ..................................... 252/609, 601: organic compositions such as polyurethanes, polyester 528/259 resins. epoxy resins, vinyl resins and other resins. The partially hydrolyzed amino condensation salts of 56 References Cited phosphorus, boron or sulfur containing compounds and the U.S. PATENT DOCUMENTS partially hydrolyzed amino condensation-aldehyde resins 3,900,665 8/1975 Weil ....................................... -
Basic Comparison Levels
Nevada Division of Environmental Protection Basic Comparison Levels Key: I=IRIS; P= PPRTV; N=NCEA; H=HEAST; A=ATSDR; O=Other Documents; CA=CalEPA S=Surrogate X=Appendix PPRTV E=Based on TEF scheme r=Route Extra Key: C = Cancer endpoint; N = Noncancer endpoint; sat = Saturation Limit; max = Ceiling Limit NDEP Basic Comparison TOXICITY INFORMATION COMPARISON LEVELS LBCLs Indoor Outdoor Levels Skin Industrial/ Industrial/ Commercial Commercial Residential May-17 SFo RfDo IUR RfCi Abs. Residential Worker Worker Ambient Air Water DAF 1 DAF 20 CAS w/o Dermal Chemical Constituents Number 1/(mg/kg-d) (mg/kg-d) (ug/m3)-1 (mg/m3) VOCc Soils Soil (mg/kg) (mg/kg) Soil (mg/kg) (µg/m3) (µg/l) (mg/kg) (mg/kg) Key Key key Key Key Key Key Key Key Acephate 30560-19-1 8.70E-03 I 4.00E-03 I 0.10 5.59E+01 C 7.52E+02 C 2.95E+02 C 7.73E+00 C Acetaldehyde 75-07-0 2.20E-06 I 9.00E-03 I V 1.23E+01 C 5.35E+01 C 1.00E+05 max 1.28E+00 C 2.55E+00 C Acetochlor 34256-82-1 2.00E-02 I 0.10 1.23E+03 N 4.67E+04 N 1.83E+04 N 6.67E+02 N Acetone 67-64-1 9.00E-01 I 3.10E+01 A V 7.04E+04 N 1.00E+05 max 1.00E+05 max 3.23E+04 N 2.05E+04 N 8.00E-01 1.60E+01 Acetone Cyanohydrin 75-86-5 2.00E-03 X 0.10 1.00E+05 max 1.00E+05 max 1.00E+05 max 2.09E+00 N Acetonitrile 75-05-8 6.00E-02 I V 1.00E+05 max 3.75E+03 N 1.00E+05 max 6.26E+01 N 1.25E+02 N Acetophenone 98-86-2 1.00E-01 I V 2.52E+03 sat 2.52E+03 sat 2.52E+03 sat 3.34E+03 N Acetylaminofluorene, 2- 53-96-3 3.80E+00 CA 1.30E-03 CA 0.10 1.28E-01 C 1.72E+00 C 6.75E-01 C 2.16E-03 C 1.77E-02 C Acrolein 107-02-8 5.00E-04 I 2.00E-05 I V -
11-37-0 Liquid Ammonium Polyphosphate Guaranteed Analysis Total Nitrogen (N)
Product Data Sheet 11-37-0 LIQUID AMMONIUM POLYPHOSPHATE GUARANTEED ANALYSIS TOTAL NITROGEN (N) ................................................................................................................................ 11.00% 11.00% Ammoniacal Nitrogen AVAILABLE PHOSPHATE (P2O5) .................................................................................................................37.00% Molybdenum (Mo).........................................................................................................................................0.001% Derived from Ammonium Phosphate. KEEP OUT OF REACH OF CHILDREN tanks and certain fiberglass tanks. Aluminum tanks WARNING can also be used. However, aluminum tanks are not CAUSES SKIN IRRITATION. CAUSES EYE recommended for prolonged storage. IRRITATION. MAY CAUSE RESPIRATORY 2. Pumps: Any pump recommended for use with liquid IRRITATION. fertilizers. Remember the basic rule of "no brass." PRECAUTIONARY STATEMENTS: Avoid breathing fumes / gas / mist / vapors / spray. Wash thoroughly after handling. Use only USES outdoors or in a well-ventilated area. Call a poison center / doctor if 1. Is an excellent source of water soluble, fast acting you feel unwell. Specific treatment see First Aid section on this label. ammonium phosphate with the most desirable ratio of PERSONAL PROTECTIVE EQUIPMENT: Wear protective N:P2O5. gloves / protective clothing / eye protection / face protection. Take off 2. An ideal source of phosphate and nitrogen in complete contaminated clothing and wash before reuse. liquid mixes. FIRST AID: IF ON SKIN Wash with plenty of water. If skin irritation 3. For specific application rates follow the recommendation occurs, get medical advice / attention. IF INHALED Remove person of a qualified individual or institution, such as, but to fresh air and keep comfortable for breathing. IF IN EYES Rinse not limited to, a certified crop advisor, agronomist, cautiously with water for several minutes. Remove contact lenses, if university crop extension publication, or apply present and easy to do. -
(GWSL) Ug/L TCR=1.0E-05 THQ=0.2 Sub-Slab and Exterior
North Carolina Department of Environmental Quality Residential Vapor Intrusion Screening Levels October 2017 (based on June 2017 USEPA Regional Screening Tables) Ground Water Sub-slab and Exterior IASL (A) IASL (B) IASL (C)3 Screening Level Soil Gas Screening 3 3 3 Does Chemical 3 ug/m ug/m ug/m CAS # Chemical Name: (GWSL) ug/L Level (SGSL) ug/m Basis Basis Basis Basis Have a Non- TCR=1.0E-06 TCR=1.0E-05 TCR=1.0E-04 4 TCR=1.0E-05 TCR=1.0E-05 Cancer Effect? THQ=0.2 THQ=0.2 THQ=0.2 THQ=0.2 THQ=0.2 30560-19-1 Acephate 75-07-0 Acetaldehyde 6.9E+02 6.3E+01 N 1.3E+00 C 1.9E+00 N 1.9E+00 N Yes 34256-82-1 Acetochlor 67-64-1 Acetone 4.5E+06 2.2E+05 N 6.5E+03 N 6.5E+03 N 6.5E+03 N Yes 75-86-5 Acetone Cyanohydrin Not Volatile Not Volatile 4.2E-01 N 4.2E-01 N 4.2E-01 N Yes 75-05-8 Acetonitrile 8.9E+03 4.2E+02 N 1.3E+01 N 1.3E+01 N 1.3E+01 N Yes 98-86-2 Acetophenone 53-96-3 Acetylaminofluorene, 2- Not Volatile Not Volatile 2.2E-03 C 2.2E-02 C 2.2E-01 C 107-02-8 Acrolein 8.4E-01 1.4E-01 N 4.2E-03 N 4.2E-03 N 4.2E-03 N Yes 79-06-1 Acrylamide Not Volatile Not Volatile 1.0E-02 C 1.0E-01 C 1.0E+00 C Yes 79-10-7 Acrylic Acid 1.4E+04 7.0E+00 N 2.1E-01 N 2.1E-01 N 2.1E-01 N Yes 107-13-1 Acrylonitrile 7.3E+01 1.4E+01 C 4.1E-02 C 4.1E-01 C 4.2E-01 N Yes 111-69-3 Adiponitrile Not Volatile Not Volatile 1.3E+00 N 1.3E+00 N 1.3E+00 N Yes 15972-60-8 Alachlor 116-06-3 Aldicarb 1646-88-4 Aldicarb Sulfone 1646-87-3 Aldicarb sulfoxide 309-00-2 Aldrin 3.2E+00 1.9E-01 C 5.7E-04 C 5.7E-03 C 5.7E-02 C 107-18-6 Allyl Alcohol 1.0E+02 7.0E-01 N 2.1E-02 N 2.1E-02 N 2.1E-02 -
Contents / Iii
FCC 11 Contents / iii Contents 1 I; ~ith ~er PREFACE v i I PEOPLE xi NEW AND CHANGED..................................................................................................................................................... xiii GENERAL PROVISIONS AND REQUIREMENTS APPLYING TO SPECIFICATIONS, TESTS, AND ASSAYS OF THE FOOD CHEMICALS CODEX .. MONOGRAPHS.................................................................................................................................................................. 9 should IDENTITY STANDARDS.............................................................................................................................................. 1269 GENERAL TESTS AND ASSAyS................................................................................................................................... 1275 Appendix I: Apparatus for Tests and Assays.............................................................................................................. 1279 Appendix II: Physical Tests and Determinations........................................................................................................ 1282 A. Chromatography......................... 1282 B. Physicochemical Properties......................................................................................................................... 1290 C. Others............................. 1302 Appendix III: Chemical Tests and Determinations.................................................................................................... -
Bench Scale Production of Ammonium Potassium Polyphosphate Charles Arthur Hodge Iowa State University
Iowa State University Capstones, Theses and Retrospective Theses and Dissertations Dissertations 1969 Bench scale production of ammonium potassium polyphosphate Charles Arthur Hodge Iowa State University Follow this and additional works at: https://lib.dr.iastate.edu/rtd Part of the Chemical Engineering Commons Recommended Citation Hodge, Charles Arthur, "Bench scale production of ammonium potassium polyphosphate " (1969). Retrospective Theses and Dissertations. 4111. https://lib.dr.iastate.edu/rtd/4111 This Dissertation is brought to you for free and open access by the Iowa State University Capstones, Theses and Dissertations at Iowa State University Digital Repository. It has been accepted for inclusion in Retrospective Theses and Dissertations by an authorized administrator of Iowa State University Digital Repository. For more information, please contact [email protected]. 70-13,591 HODGE, Charles Arthur, 194-2- BENCH SCALE PRODUCTION OF AMMONIUÎ-l POTASSIUM POLYPHOSPHATE. Iowa State University, Ph.D., 1969 Engineering, chemical University Microfilms, Inc., Ann Arbor, Michigan THIS DISSERTATION HAS BEEN MICROFILMED EXACTLY AS RECEIVED BENCH SCALE PRODUCTION OF AMMONIUM POTASSIUM POLYPHOSPHATE by Charles Arthur Hodge A Dissertation Submitted to the Graduate Faculty in Partial Fulfillment of The Requirements for the Degree of DOCTOR OF PHILOSOPHY Major Subject; Chemical Engineering Approved: Signature was redacted for privacy. Signature was redacted for privacy. Head of Ma]or Department Signature was redacted for privacy. Iowa State -
Third Supplement, FCC 11 Index / All-Trans-Lycopene / I-1
Third Supplement, FCC 11 Index / All-trans-Lycopene / I-1 Index Titles of monographs are shown in the boldface type. A 2-Acetylpyridine, 20 Alcohol, 80%, 1524 3-Acetylpyridine, 21 Alcohol, 90%, 1524 Abbreviations, 6, 1726, 1776, 1826 2-Acetylpyrrole, 21 Alcohol, Absolute, 1524 Absolute Alcohol (Reagent), 5, 1725, 2-Acetyl Thiazole, 18 Alcohol, Aldehyde-Free, 1524 1775, 1825 Acetyl Valeryl, 562 Alcohol C-6, 579 Acacia, 556 Acetyl Value, 1400 Alcohol C-8, 863 ªAccuracyº, Defined, 1538 Achilleic Acid, 24 Alcohol C-9, 854 Acesulfame K, 9 Acid (Reagent), 5, 1725, 1775, 1825 Alcohol C-10, 362 Acesulfame Potassium, 9 Acid-Hydrolyzed Milk Protein, 22 Alcohol C-11, 1231 Acetal, 10 Acid-Hydrolyzed Proteins, 22 Alcohol C-12, 681 Acetaldehyde, 10 Acid Calcium Phosphate, 219, 1838 Alcohol C-16, 569 Acetaldehyde Diethyl Acetal, 10 Acid Hydrolysates of Proteins, 22 Alcohol Content of Ethyl Oxyhydrate Acetaldehyde Test Paper, 1535 Acidic Sodium Aluminum Phosphate, Flavor Chemicals (Other than Acetals (Essential Oils and Flavors), 1065 Essential Oils), 1437 1395 Acidified Sodium Chlorite Alcohol, Diluted, 1524 Acetanisole, 11 Solutions, 23 Alcoholic Potassium Hydroxide TS, Acetate C-10, 361 Acidity Determination by Iodometric 1524 Acetate Identification Test, 1321 Method, 1437 Alcoholometric Table, 1644 Aceteugenol, 464 Acid Magnesium Phosphate, 730 Aldehyde C-6, 571 Acetic Acid Furfurylester, 504 Acid Number (Rosins and Related Aldehyde C-7, 561 Acetic Acid, Glacial, 12 Substances), 1418 Aldehyde C-8, 857 Acetic Acid TS, Diluted, 1524 Acid Phosphatase -
Regional Screening Level (RSL) Industrial Air Supporting Table June 2011
Regional Screening Level (RSL) Industrial Air Supporting Table June 2011 Key: I = IRIS; P = PPRTV; A = ATSDR; C = Cal EPA; X = PPRTV Appendix; H = HEAST; J = New Jersey; Y = New York; O = EPA Office of Water; E = Environmental Criteria and Assessment Office; S = see user guide Section 5; L = see user guide on lead; M = mutagen; V = volatile; F = See FAQ; c = cancer; * = where: n SL < 100X c SL; ** = where n SL < 10X c SL; n = noncancer; m = Concentration may exceed ceiling limit (See User Guide); s = Concentration may exceed Csat (See User Guide); SSL values are based on DAF=1 Toxicity and Chemical‐specific Information Contaminant Carcinogenic Target Risk (TR) = 1E‐06 Noncancer Hazard Index (HI) = 1 k k v Carcinogenic SL Noncarcinogenic SL IUR e RfCi e o TR=1.0E‐6 HI=1 (ug/m3)‐1 y (mg/m3) y c mutagen Analyte CAS No. (ug/m3) (ug/m3) 5.1E‐06 C ALAR 1596‐84‐5 2.4E+00 Acephate 30560‐19‐1 2.2E‐06 I 9.0E‐03 I V Acetaldehyde 75‐07‐0 5.6E+00 3.9E+01 Acetochlor 34256‐82‐1 3.1E+01 A V Acetone 67‐64‐1 1.4E+05 6.0E‐02 P V Acetone Cyanohydrin 75‐86‐5 2.6E+02 6.0E‐02 I V Acetonitrile 75‐05‐8 2.6E+02 V Acetophenone 98‐86‐2 1.3E‐03 C Acetylaminofluorene, 2‐ 53‐96‐3 9.4E‐03 2.0E‐05 I V Acrolein 107‐02‐8 8.8E‐02 1.0E‐04 I 6.0E‐03 I Acrylamide 79‐06‐1 1.2E‐01 2.6E+01 1.0E‐03 I Acrylic Acid 79‐10‐7 4.4E+00 6.8E‐05 I 2.0E‐03 I V Acrylonitrile 107‐13‐1 1.8E‐01 8.8E+00 6.0E‐03 P Adiponitrile 111‐69‐3 2.6E+01 Alachlor 15972‐60‐8 Aldicarb 116‐06‐3 Aldicarb Sulfone 1646‐88‐4 4.9E‐03 I Aldrin 309‐00‐2 2.5E‐03 Ally 74223‐64‐6 1.0E‐04 X Allyl Alcohol 107‐18‐6 4.4E‐01 -
Jbottor of $I)Iiof(Opt)P in BOTANY
STUDIES ON THE EFFECT OF THERMAL POWER PLANT WASTEWATER AND COAL FLY ASH ON VIGNA RADIATA (L.) WILCZEK ABSTRACT THESIS SUBMITTED FOR THE DEGREE OF JBottor of $I)iIof(opt)P IN BOTANY BY 5HAHLA 5AEED DEPARTMENT OF BOTANY ALIGARH MUSLIM UNIVERSITY ALIGARH (INDIA) 2004 Abstract Abstract of the thesis- submitted to th^^Uigarh Muslim University, Aligarh, India for the Degree of Doctor of Philosophy in Botany. Experiments I to VI we^rjj cginied. out, based on factorial and simple randomized block designa*,during the years 2000-2002 with the aim to study the utility of the thermal fIcjWer plant wastewater (TPPW) and coal fly ash (FA) and the effect of NPK fertilizer doses on two varieties of green gram [Vigna radiata L. Wilczek), namely PDM-11 and PDM-54. The data were mostly significant and the present brief is based mainly on the basis of two important parameters, the seed yield and protein percentage for the purpose of grower and consumer respectively. Experiments I and II were performed on PDM-11 and PDM-54 respectively during spring season of 2000 to study the comparative effect of TPPW, GW, four levels of fly ash and four levels of nitrogen on the basis of growth, yield and quality. TPPW proved beneficial. Among fly ash levels, FA20 and of N doses, N15 proved optimum. The analysis of pooled data of the two experiments revealed that PDM-11 proved superior to PDM-54. Experiments III and IV were conducted simultaneously during spring season of the year 2001 on the same respective varieties under four levels of basal phosphorus doses supplemented with a uniform starter dose of 15 kg N ha-i and 20 kg K ha-i along with 20% fly ash. -
Preliminary Soil Remediation Goals (PSRG) Table
North Carolina Department of Environmental Quality Preliminary Soil Remediation Goals (PSRGs) June 2021 (based on May 2021 USEPA Regional Screening Tables) These notes must be used with the PSRG Table General Notes: 1. PSRGs are obtained using the USEPA Regional Screening Level (RSL) table. If a contaminant does not have a PSRG listed, then one or more of the contaminant-specific parameters are not available from the RSL table to calculate a soil PSRG (these contaminants are only included in the PSRG table to account for all entries on the RSL table). If a 02L Standard or IMAC is available for a contaminant with no PSRGs, protection of groundwater evaluation is still necessary. Leaching tests should be performed by an analytical laboratory to determine whether this contaminant it is leaching to groundwater above its NC 02L Standard or IMAC, or another method may be allowed by the state program providing oversight. 2. The health-based PSRGs (Residential and Industrial/Commercial) are based upon human health risk and do not address potential ecological risk. The PSRGs listed are the lower of: a. the carcinogenic target risk of 1.0E-06 (C), or b. the non-carcinogenic target hazard quotient of 0.2 (N). Residential health-based PSRGs should be used to identify site contaminants and delineate their extent. 3. The protection of groundwater PSRGs are provided as a conservative indicator of soil leachability and are developed using a USEPA soil leaching model with conservative assumptions and default values appropriate for North Carolina (see Equation 1 on page 4). Check remedial program guidance or the Technical Guidance for Risk-Based Environmental Remediation of Sites published on the NCDEQ Risk-Based Remediation website for alternative methods to further characterize site-specific soil leachability if soil concentrations exceed protection of groundwater PSRGs.