Downloaded and Was Then Combined with the Grid Resulting from the Previous Scanning Using the Meshmixer and Blender Software
Total Page:16
File Type:pdf, Size:1020Kb
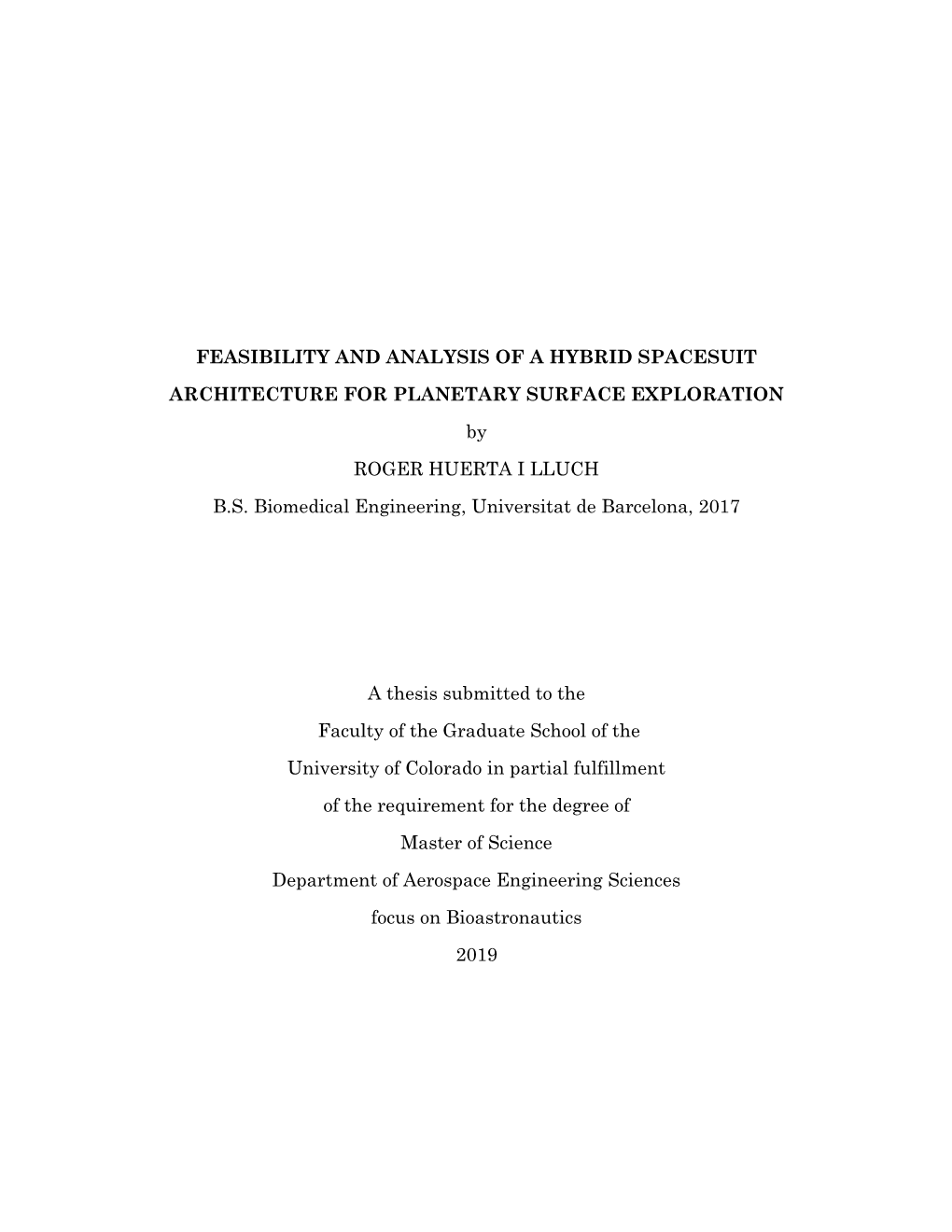
Load more
Recommended publications
-
Musculoskeletal Human-Spacesuit Interaction Model
Musculoskeletal Human-Spacesuit Interaction Model Ana Diaz Dava Newman Massachusetts Institute of Technology Massachusetts Institute of Technology 77 Massachusetts Avenue 77 Massachusetts Avenue Cambridge, MA 02139 Cambridge, MA 02139 617-909-0644 617-258-8799 [email protected] [email protected] Abstract—Extravehicular Activity (EVA) is a highly demanding episodes that could affect astronauts’ performance in a space activity during space missions. The current NASA spacesuit, the mission [1, 2]. Extravehicular Mobility Unit (EMU), might be thought of as the ‘world’s smallest spacecraft’ and is quite an engineering The EMU is pressurized to 29.6 KPa, using 100% oxygen for achievement. However, the EMU has also led to discomfort and spaceflight and a mixture of nitrogen and oxygen (nitrox) for musculoskeletal injuries, mainly due to the lack of mobility in training. It is made with 14 different layers, and it consists of the pressurized suit that makes moving and operating within the suit challenging. A new musculoskeletal modeling framework is three main components [3], as shown in Figure 1: developed in OpenSim to analyze human-spacesuit interaction and musculoskeletal performance during EVA. Two spacesuits - The Liquid Cooling and Ventilation Garment are considered: the current EMU and NASA’s Mark III (LCVG). This piece of garment made of nylon and spacesuit technology demonstrator. In the model, the effect of spandex covers the whole body and its main the spacesuits is represented as external torques applied to the objective is to eliminate the excess body heat by human body, based on experimental data. Muscle forces during water circulation through the garment. -
Extravehicular Activity ENAE 483/788D
Extravehicular Activity • Lecture #24 – November 19, 2020 • Full pressure suits and high-altitude aviation • Early human space program • Operational suits • Interfaces to habitats and rovers • Applications to ENAE 484 Spring 2021 © 2020 David L. Akin - All rights reserved http://spacecraft.ssl.umd.edu U N I V E R S I T Y O F Extravehicular Activity ENAE 483/788D - Principles of Space Systems Design MARYLAND 1 Spacesuit Functional Requirements A suit has to • Provide thermal control • Provide a breathable atmosphere • Hold its shape • Move with the wearer • Protect against external threats • Provide communications and data interactions U N I V E R S I T Y O F Extravehicular Activity ENAE 483/788D - Principles of Space Systems Design MARYLAND 2 Wiley Post - B. F. Goodrich, 1934 U N I V E R S I T Y O F Extravehicular Activity ENAE 483/788D - Principles of Space Systems Design MARYLAND 3 “Tomato Worm” Suits - c. 1940 U N I V E R S I T Y O F Extravehicular Activity ENAE 483/788D - Principles of Space Systems Design MARYLAND 4 XMC-2 Full Pressure Suit (ILC - 1955) U N I V E R S I T Y O F Extravehicular Activity ENAE 483/788D - Principles of Space Systems Design MARYLAND 5 Flat Panel Joint U N I V E R S I T Y O F Extravehicular Activity ENAE 483/788D - Principles of Space Systems Design MARYLAND 6 Rolling Convolute - Blade Joint U N I V E R S I T Y O F Extravehicular Activity ENAE 483/788D - Principles of Space Systems Design MARYLAND 7 Rolling Convolute Arm U N I V E R S I T Y O F Extravehicular Activity ENAE 483/788D - Principles of Space Systems -
Space Radiation Analysis for the Mark III Spacesuit
Space Radiation Analysis for the Mark III Spacesuit Bill Atwell1 and Paul Boeder2 Boeing Research & Development, Houston, TX, 77058USA Amy Ross3 NASA Johnson Space Center, Houston, TX, 77058USA The NASA has continued the development of space systems by applying and integrating improved technologies that include safety issues, lightweight materials, and electronics. One such area is extravehicular (EVA) spacesuit development with the most recent Mark III spacesuit. In this paper the Mark III spacesuit is discussed in detail that includes the various components that comprise the spacesuit, materials and their chemical composition that make up the spacesuit, and a discussion of the 3-D CAD model of the Mark III spacesuit. In addition, the male (CAM) and female (CAF) computerized anatomical models are also discussed in detail. We “combined” the spacesuit and the human models, that is, we developed a method of incorporating the human models in the Mark III spacesuit and performed a ray-tracing technique to determine the space radiation shielding distributions for all of the critical body organs. These body organ shielding distributions include the BFO (Blood-Forming Organs), skin, eye, lungs, stomach, and colon, to name a few, for both the male and female. Using models of the trapped (Van Allen) proton and electron environments, radiation exposures were computed for a typical low earth orbit (LEO) EVA mission scenario including the geostationary (GEO) high electron environment. A radiation exposure assessment of these mission scenarios is made to determine whether or not the crew radiation exposure limits are satisfied, and if not, the additional shielding material that would be required to satisfy the crew limits. -
Suited for Spacewalking
Education Product National Aeronautics and Space Administration Teachers Grades 5–12 Suited for S pac ewa l k i n g ATeacher’s Guide with Activities for Technology Education, Mathematics, and Science Suited for Spacewalking—A Teacher’s Guide with Activities for Technology Education, Mathematics, and Science is available in electronic format through NASA Spacelink—one of the Agency’s electronic resources specifically developed for use by the educational community. The system may be accessed at the following address: http://spacelink.nasa.gov Suited for Spacewalking A Teacher’s Guide with Activities for Technology Education, Mathematics, and Science National Aeronautics and Space Administration Office of Human Resources and Education Education Division Washington, DC Education Working Group NASA Johnson Space Center Houston, Texas This publication is in the Public Domain and is not protected by copyright. Permission is not required for duplication. EG-1998-03-112-HQ Deborah A. Shearer Acknowledgments Science Teacher Zue S. Baales Intermediate School This publication was developed for the National Friendswood, Texas Aeronautics and Space Administration by: Sandy Peck Writer/Illustrator: Clear Creek Independent School District Gregory L. Vogt, Ed.D. League City, Texas Crew Educational Affairs Liaison Teaching From Space Program Marilyn L. Fowler, Ph.D. NASA Johnson Space Center Science Project Specialist Houston, TX Charles A. Dana Center University of Texas at Austin Editor: Jane A. George Jeanne Gasiorowski Educational Materials Specialist Manager, NASA Educator Resource Center Teaching From Space Program Classroom of the Future NASA Headquarters Wheeling Jesuit University Washington, DC Wheeling, West Virginia Reviewers: Dr. Peggy House Linda Godwin Director, The Glenn T. -
ILC Space Suits & Related Products
ILC Space Suits & Related Products 0000-712731 Rev. A REVISIONS LETTER DESCRIPTION DATE - Initial Release 10/26/07 A Update with review comments and inclusion of the Antarctic Habitat and 11/28/07 Shuttle Adjustable Protective Mitten Assembly (APMA). This report was written through the volunteer efforts of ILC employees, retirees and friends. Additionally, this report would not have been possible without the efforts of Ken Thomas at Hamilton Sundstrand who truly realizes the significance of preserving the history of US space suit development. The information has been compiled to the best of the participant’s abilities given the volunteer nature of this effort. Any errors are unintentional and will be corrected once identified and verified. If there are any questions regarding any detail of this report, please call (302) 335-3911 Ext. 248. The production of this report does not imply ILC Dover agrees with or is responsible for the contents therein. This report has been compiled from information in the public domain and poses no export licensing issues. William Ayrey Primary Author & Publisher 2 ILC Space Suits & Related Products 0000-712731 Rev. A Table Of Content Chapter 1 The Path Leading To Space -------------------------------------------------------------------------------- 6 The XMC-2-ILC X-15 Competition Prototype (1957) --------------------------------------------------------- 6 The SPD-117 Mercury Competition Prototype (1959) --------------------------------------------------------- 8 Chapter 2 The Journey To The Moon (1960-72) --------------------------------------------------------------- 9 ILC Developments & Prototype Suits Leading To The Apollo Contract (1960-62)----------------------- 10 SPD-143 Training Suits -------------------------------------------------------------------------------------------- 14 Glove Development For Apollo And The World (1962-Present) -------------------------------------------- 17 AX1H - The First New Design Of The Apollo Program ------------------------------------------------------ 19 AX2H Suits (Sept. -
NASA's Advanced Extra-Vehicular Activity Space Suit Pressure
48th International Conference on Environmental Systems ICES-2018-273 8-12 July 2018, Albuquerque, New Mexico NASA’s Advanced Extra-vehicular Activity Space Suit Pressure Garment 2018 Status and Development Plan Amy Ross,1 and Richard Rhodes 2 NASA Johnson Space Center, Houston, TX, 77058 Shane McFarland3 NASA Johnson Space Center/MEI, Houston, TX, 77058 This paper presents both near-term and long-term NASA Advanced Extra-vehicular Activity (EVA) Pressure Garment development efforts. The near-term plan discusses the development of pressure garment components for the first design iteration of the International Space Station exploration space suit demonstration configuration, termed the xEMU Demo. The xEMU Demo effort is targeting a 2023-2025 flight demonstration timeframe. The Fiscal Year 2018 (FY18) tasks focus on either the initiation or maturation of component design, depending on the state of development of the components, and the assembly of a suit configuration, termed Z-2.5, that will be used to evaluate changes to the upper torso geometry in a Neutral Buoyancy Laboratory (NBL) test series. The geometry changes, which are being driven by the need to reduce the front-to-back dimension of the advanced extravehicular mobility unit, diverge from a proven shape, such as that of the Mark III Space Suit Technology Demonstrator. The 2018 efforts culminate in the Z-2.5 NBL test. The lessons learned from the Z-2.5 NBL test will inform the xEMU Demo design as the effort moves toward design verification testing and preliminary and critical design reviews. The long-term development plan looks to surface exploration and operations. -
Understanding Astronaut Shoulder Injury
Human-Spacesuit Interaction: Understanding Astronaut Shoulder Injury by ALEXANDRA MARIE HILBERT B.S. Mechanical Engineering Cornell University, 2013 Submitted to the Department of Aeronautics and Astronautics in partial fulfillment of the requirements for the degree of MASTER OF SCIENCE IN AERONAUTICS AND ASTRONAUTICS at the MASSACHUSETTS INSTITUTE OF TECHNOLOGY June 2015 © 2015 Massachusetts Institute of Technology. All rights reserved. Signature of Author Department of Aeronautics and Astronautics May 21, 2015 Certified by Dava J. Newman, Ph.D. Apollo Professor of Astronautics and Engineering Systems Director of Technology and Policy Program Thesis Supervisor Accepted by Paulo C. Lozano, Ph.D. Associate Professor of Aeronautics and Astronautics Chair, Graduate Program Committee 1 2 Human-Spacesuit Interaction: Understanding Astronaut Shoulder Injury by ALEXANDRA MARIE HILBERT Submitted to the Department of Aeronautics and Astronautics on May 21, 2015 in Partial Fulfillment of the Requirements for the Degree of Master of Science in Aeronautics and Astronautics ABSTRACT Extravehicular activities (EVA), or space walks, are a critical and complex aspect of human spaceflight missions. To prepare for safe and successful execution of the required tasks, astronauts undergo extensive training in the Neutral Buoyancy Lab (NBL), which involves many hours of performing repetitive motions at various orientations, all while wearing a pressurized spacesuit. The current U.S. spacesuit—the Extravehicular Mobility Unit (EMU)—is pressurized to 29.6 kPa (4.3 psi) and requires astronauts to exert a substantial amount of energy in order to move the suit into a desired position. The pressurization of the suit therefore limits human mobility, causes discomfort, and leads to a variety of contact and strain injuries. -
Find Ebook » Spacesuits
N7WVTXYEZ2NE \\ Kindle \\ Spacesuits Spacesuits Filesize: 3.98 MB Reviews This book might be well worth a study, and much better than other. Indeed, it can be perform, continue to an amazing and interesting literature. I realized this publication from my i and dad suggested this book to find out. (Dejuan Rippin) DISCLAIMER | DMCA JTDJHKOVURP7 > Book Spacesuits SPACESUITS Reference Series Books LLC Jan 2012, 2012. Taschenbuch. Book Condition: Neu. 248x189x10 mm. This item is printed on demand - Print on Demand Neuware - Source: Wikipedia. Pages: 37. Chapters: American spacesuits, Soviet and Russian spacesuits, Space suit components, Apollo/Skylab A7L, Sokol space suit, Space activity suit, Extravehicular Mobility Unit, Gemini space suit, Orlan space suit, Navy Mark IV, Advanced Crew Escape Suit, Constellation Space Suit, Suitport, Liquid Cooling and Ventilation Garment, Launch Entry Suit, Primary Life Support System, Carbon dioxide scrubber, Krechet-94, I-Suit, Feitian space suit, Mark III, Strizh, Thermal Micrometeoroid Garment, SK-1 spacesuit, Yastreb, Hard Upper Torso, Berkut spacesuit, Maximum Absorbency Garment, Shuttle Ejection Escape Suit. Excerpt: The A7L Apollo & Skylab spacesuit is the primary pressure suit worn by NASA astronauts for Project Apollo, the three manned Skylab flights, and the Apollo-Soyuz Test Project between 1968 and the termination of the Apollo program in 1975. The 'A7L' designation is used by NASA as the seventh Apollo spacesuit designed and built by ILC Dover. The A7L is a design evolution of ILC's A5L and A6L. The A5L was the initial design. The A6L introduced the integrated thermal and micrometeroid cover layer. Aer the AS-204 spacecra fire, the suit was upgraded to be fire-resistant and given the designation A7L. -
Sudhakar Rajulu, Phd NASA Johnson Space Center EXPLORATION CAMPAIGN
Ergonomic Assessment of a Space Suit: From the Perspective of Population Analysis, Fit, Accommodation, Comfort, and Performance Sudhakar Rajulu, PhD NASA Johnson Space Center EXPLORATION CAMPAIGN 2 Space Suits and Exoskeletons • Protection • Safety • Population variation Fit, Mobility, Reach, Exertion Performance • Potential Injury and Discomfort Restrictions Movement Excursion Incompatibility Compensatory adjustment issues Safe Limits Population based Assessment is Critical History of NASA Space Suits Apollo A7LB, Shuttle EMU, MK III Space Suit Design for Diverse Body Sizes • Body sizes used be “homogeneous” in early space program • Today, crews are in a wide variety of body size, shape, and physical skill • Smaller population needs to be included from early design stage Crewmembers in 1960’s Crewmembers in 2000’s Smaller Population Accommodation Apollo Sizing EV TLSA (Torso Limb Suit Assembly): The torso portion of the TLSA is custom sized and the limb portions are graduated in size and adjustable to accommodate individual crewman limb lengths Shuttle EMU (Extravehicular Mobility Unit) MK III Sizing Kosmo et al., 1988. Development of the NASA ZPS Mark III 57.2-kN/m2 (8.3 psi) Space Suit Anthropometric Measurements for Suit Design Early Technique based on Linear Measurements: • Take critical body measurements (stature, shoulder breadth, etc.) • Compare linear dimensions between suit and crewmembers • However, linear measurements do not represent 3-D body and suit geometry Special Consideration for Suit Fit and Accommodation Shoulder-to-Suit Clearance and Interactions: • Space suits have a very restrictive space and if not properly sized can result in discomfort, pain or injury • Suboptimal suit fit, in particular at the shoulders, has been identified as one of the predominant risk factors for shoulder injury while wearing a space suit. -
Download Doc « Spacesuits
AWM3MUDZKZ37 ~ Kindle « Spacesuits Spacesuits Filesize: 7.88 MB Reviews This book may be worth purchasing. I am quite late in start reading this one, but better then never. Once you begin to read the book, it is extremely difficult to leave it before concluding. (Esta Price) DISCLAIMER | DMCA BW8JUFQQI1ZE / eBook \\ Spacesuits SPACESUITS Reference Series Books LLC Jan 2012, 2012. Taschenbuch. Book Condition: Neu. 248x189x10 mm. This item is printed on demand - Print on Demand Neuware - Source: Wikipedia. Pages: 37. Chapters: American spacesuits, Soviet and Russian spacesuits, Space suit components, Apollo/Skylab A7L, Sokol space suit, Space activity suit, Extravehicular Mobility Unit, Gemini space suit, Orlan space suit, Navy Mark IV, Advanced Crew Escape Suit, Constellation Space Suit, Suitport, Liquid Cooling and Ventilation Garment, Launch Entry Suit, Primary Life Support System, Carbon dioxide scrubber, Krechet-94, I-Suit, Feitian space suit, Mark III, Strizh, Thermal Micrometeoroid Garment, SK-1 spacesuit, Yastreb, Hard Upper Torso, Berkut spacesuit, Maximum Absorbency Garment, Shuttle Ejection Escape Suit. Excerpt: The A7L Apollo & Skylab spacesuit is the primary pressure suit worn by NASA astronauts for Project Apollo, the three manned Skylab flights, and the Apollo-Soyuz Test Project between 1968 and the termination of the Apollo program in 1975. The 'A7L' designation is used by NASA as the seventh Apollo spacesuit designed and built by ILC Dover. The A7L is a design evolution of ILC's A5L and A6L. The A5L was the initial design. The A6L introduced the integrated thermal and micrometeroid cover layer. Aer the AS-204 spacecra fire, the suit was upgraded to be fire-resistant and given the designation A7L. -
Extravehicular Activity
Extravehicular Activity • Full pressure suits and high-altitude aviation • Early human space program • Operational suits • Interfaces to habitats and rovers • Spacesuit alternatives © 2019 David L. Akin - All rights reserved http://spacecraft.ssl.umd.edu U N I V E R S I T Y O F Extravehicular Activity MARYLAND 1 ENAE 697 - Space Human Factors and Life Support Spacesuit Functional Requirements A suit has to • Provide thermal control • Provide a breathable atmosphere • Hold its shape • Move with the wearer • Protect against external threats • Provide communications and data interactions U N I V E R S I T Y O F Extravehicular Activity MARYLAND 2 ENAE 697 - Space Human Factors and Life Support Wiley Post - B. F. Goodrich, 1934 U N I V E R S I T Y O F Extravehicular Activity MARYLAND 3 ENAE 697 - Space Human Factors and Life Support “Tomato Worm” Suits - c. 1940 U N I V E R S I T Y O F Extravehicular Activity MARYLAND 4 ENAE 697 - Space Human Factors and Life Support XMC-2 Full Pressure Suit (ILC - 1955) U N I V E R S I T Y O F Extravehicular Activity MARYLAND 5 ENAE 697 - Space Human Factors and Life Support Flat Panel Joint U N I V E R S I T Y O F Extravehicular Activity MARYLAND 6 ENAE 697 - Space Human Factors and Life Support Rolling Convolute - Blade Joint U N I V E R S I T Y O F Extravehicular Activity MARYLAND 7 ENAE 697 - Space Human Factors and Life Support Rolling Convolute Arm U N I V E R S I T Y O F Extravehicular Activity MARYLAND 8 ENAE 697 - Space Human Factors and Life Support Toroidal Joint Construction U N I V E R S I T Y -
Revisiting the Mark III/AX-5 Suit “Fly-Off”: Lessons Learned Applicable to Modern-Day Suits
49th International Conference on Environmental Systems ICES-2019-119 Boston, Massachusetts – 7-11 July 2019 Revisiting the Mark III/AX-5 Suit “Fly-Off”: Lessons Learned Applicable to Modern-Day Suits David L. Akin∗ University Of Maryland, College Park, MD, 20742, USA At the start of the 1990’s, the upcoming Space Station appeared to be an opportunity to create the next- generation spacesuit, following ten years of flight experience with the shuttle Extravehicular Mobility Unit (EMU). Two suits were candidates for the “Space Station Suit”: the Mark III from NASA Johnson Space Center, and the AX-5 from NASA Ames. The Mark III continued the EMU’s hybrid approach of hard upper torso and soft goods for the arms and lower torso assembly, while the AX-5 was an all-metal “hard” suit design with sealed rotary bearings for mobility. The evaluation process of the two suits lasted almost two years, and is likely the most detailed head-to-head comparison of two spacesuits ever undertaken. Tests were performed joint-by-joint for each suit, and suited runs by four EVA-trained astronauts were conducted in neutral buoyancy and parabolic flight. Wherever possible, each result was quantified to create a running “score” for the two suits, compared to an EMU as the control case. Crew subjective evaluations were presented and considered. In the end, no final conclusion was drawn nor formal report published. It was realized that no funding would be forthcoming for new suit development, and that the EMU would be the baseline U.S. suit for International Space Station and beyond.