Spacesuits Is Growing and Could Present an Attractive Opportunity for Investment
Total Page:16
File Type:pdf, Size:1020Kb
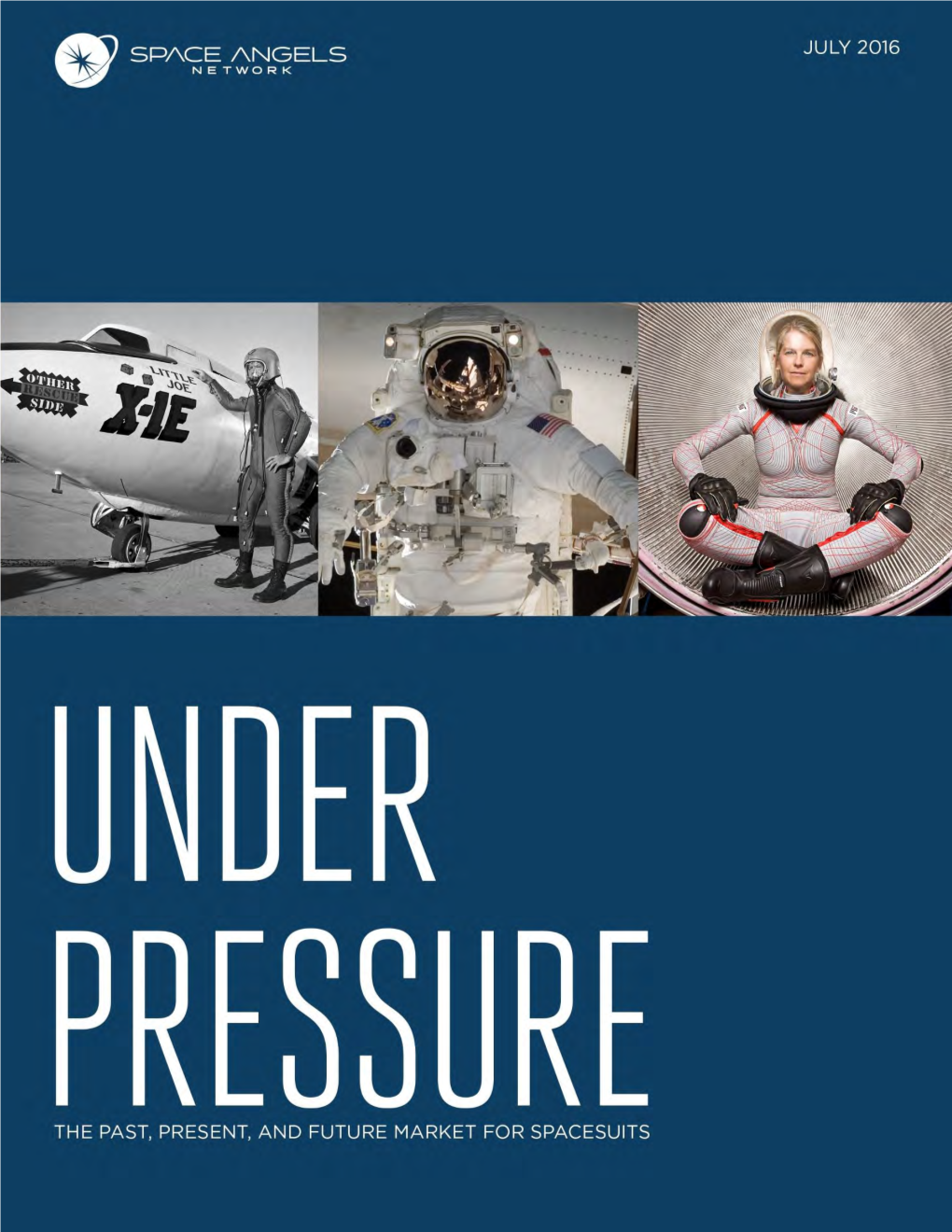
Load more
Recommended publications
-
Breaking the Pressure Barrier: a History of the Spacesuit Injection Patch
Breaking the Pressure Barrier: A History of the Spacesuit Injection Patch Shane M. McFarland1 Wyle/NASA-Johnson Space Center, Houston, TX Aaron S. Weaver2 NASA-Glenn Research Center, Columbus, OH The spacesuit assembly has a fascinating and complicated history dating back to the early 1930s. Much has been written on this history from an assembly perspective and, to a lesser extent, a component perspective. However, little has been written or preserved specifically on smaller, lesser-known aspects of pressure suit design. One example of this is the injection patch—a small 2–in.-diameter disk on the leg of the Apollo suit that facilitated a medical injection when pressurized, and the only known implementation of such a feature on a flight suit. Whereas many people are aware this feature existed, very little is known of its origin, design, and use, and the fact that the Apollo flight suit was not the only instance in which such a feature was implemented. This paper serves to tell the story of this seeming “afterthought” of a feature, as well as the design considerations heeded during the initial development of subsequent suits. Nomenclature EMU = Extravehicular Mobility Unit ETFE = ethylene tetrafluoroethylene EVA = extravehicular activity FEP = fluorinated ethylene propylene ILC = International Latex Corporation IM = intramuscular (injection) IO = intraosseal (injection) IV = intravascular (injection) LCG = liquid cooling garment NASA = National Aeronautics and Space Administration PGS = pressure garment subsystem TMG = thermal micromediorite garment UTC = urine transfer connector I. Introduction he earliest efforts in pressure suit design were driven by the need to survive high altitudes during attempts to T break speed or height flight records. -
EMC18 Abstracts
EUROPEAN MARS CONVENTION 2018 – 26-28 OCT. 2018, LA CHAUX-DE-FONDS, SWITZERLAND EMC18 Abstracts In alphabetical order Name title of presentation Page n° Théodore Besson: Scorpius Prototype 3 Tomaso Bontognali Morphological biosignatures on Mars: what to expect and how to prepare not to miss them 4 Pierre Brisson: Humans on Mars will have to live according to both Martian & Earth Time 5 Michel Cabane: Curiosity on Mars : What is new about organic molecules? 6 Antonio Del Mastro Industrie 4.0 technology for the building of a future Mars City: possibilities and limits of the application of a terrestrial technology for the human exploration of space 7 Angelo Genovese Advanced Electric Propulsion for Fast Manned Missions to Mars and Beyond 8 Olivia Haider: The AMADEE-18 Mars Simulation OMAN 9 Pierre-André Haldi: The Interplanetary Transport System of SpaceX revisited 10 Richard Heidman: Beyond human, technical and financial feasibility, “mass-production” constraints of a Colony project surge. 11 Jürgen Herholz: European Manned Space Projects 12 Jean-Luc Josset Search for life on Mars, the ExoMars rover mission and the CLUPI instrument 13 Philippe Lognonné and the InSight/SEIS Team: SEIS/INSIGHT: Towards the Seismic Discovering of Mars 14 Roland Loos: From the Earth’s stratosphere to flying on Mars 15 EUROPEAN MARS CONVENTION 2018 – 26-28 OCT. 2018, LA CHAUX-DE-FONDS, SWITZERLAND Gaetano Mileti Current research in Time & Frequency and next generation atomic clocks 16 Claude Nicollier Tethers and possible applications for artificial gravity -
Contingency Shuttle Crew Support (Cscs)/Rescue Flight Resource Book
CSCS/Rescue Flight Resource Book JSC-62900 CONTINGENCY SHUTTLE CREW SUPPORT (CSCS)/RESCUE FLIGHT RESOURCE BOOK OVERVIEW 1 Mission Operations CSCS 2 Directorate RESCUE 3 FLIGHT DA8/Flight Director Office Final July 12, 2005 National Aeronautics and Space Administration Lyndon B. Johnson Space Center Houston, Texas FINAL 07/12/05 2-i Verify this is the correct version before using. CSCS/Rescue Flight Resource Book JSC-62900 CONTINGENCY SHUTTLE CREW SUPPORT (CSCS)/RESCUE FLIGHT RESOURCE BOOK FINAL JULY 12, 2005 PREFACE This document, dated May 24, 2005, is the Basic version of the Contingency Shuttle Crew Support (CSCS)/Rescue Flight Resource Book. It is requested that any organization having comments, questions, or suggestions concerning this document should contact DA8/Book Manager, Flight Director Office, Building 4 North, Room 3039. This is a limited distribution and controlled document and is not to be reproduced without the written approval of the Chief, Flight Director Office, mail code DA8, Lyndon B. Johnson Space Center, Houston, TX 77058. FINAL 07/12/05 2-ii Verify this is the correct version before using. CSCS/Rescue Flight Resource Book JSC-62900 1.0 - OVERVIEW Section 1.0 is the overview of the entire Contingency Shuttle Crew Support (CSCS)/Rescue Flight Resource Book. FINAL 07/12/05 2-iii Verify this is the correct version before using. CSCS/Rescue Flight Resource Book JSC-62900 This page intentionally blank. FINAL 07/12/05 2-iv Verify this is the correct version before using. CSCS/Rescue Flight Resource Book JSC-62900 2.0 - CONTINGENCY SHUTTLE CREW SUPPORT (CSCS) 2.1 Procedures Overview.......................................................................................................2-1 2.1.1 ................................................................................ -
Project Selene: AIAA Lunar Base Camp
Project Selene: AIAA Lunar Base Camp AIAA Space Mission System 2019-2020 Virginia Tech Aerospace Engineering Faculty Advisor : Dr. Kevin Shinpaugh Team Members : Olivia Arthur, Bobby Aselford, Michel Becker, Patrick Crandall, Heidi Engebreth, Maedini Jayaprakash, Logan Lark, Nico Ortiz, Matthew Pieczynski, Brendan Ventura Member AIAA Number Member AIAA Number And Signature And Signature Faculty Advisor 25807 Dr. Kevin Shinpaugh Brendan Ventura 1109196 Matthew Pieczynski 936900 Team Lead/Operations Logan Lark 902106 Heidi Engebreth 1109232 Structures & Environment Patrick Crandall 1109193 Olivia Arthur 999589 Power & Thermal Maedini Jayaprakash 1085663 Robert Aselford 1109195 CCDH/Operations Michel Becker 1109194 Nico Ortiz 1109533 Attitude, Trajectory, Orbits and Launch Vehicles Contents 1 Symbols and Acronyms 8 2 Executive Summary 9 3 Preface and Introduction 13 3.1 Project Management . 13 3.2 Problem Definition . 14 3.2.1 Background and Motivation . 14 3.2.2 RFP and Description . 14 3.2.3 Project Scope . 15 3.2.4 Disciplines . 15 3.2.5 Societal Sectors . 15 3.2.6 Assumptions . 16 3.2.7 Relevant Capital and Resources . 16 4 Value System Design 17 4.1 Introduction . 17 4.2 Analytical Hierarchical Process . 17 4.2.1 Longevity . 18 4.2.2 Expandability . 19 4.2.3 Scientific Return . 19 4.2.4 Risk . 20 4.2.5 Cost . 21 5 Initial Concept of Operations 21 5.1 Orbital Analysis . 22 5.2 Launch Vehicles . 22 6 Habitat Location 25 6.1 Introduction . 25 6.2 Region Selection . 25 6.3 Locations of Interest . 26 6.4 Eliminated Locations . 26 6.5 Remaining Locations . 27 6.6 Chosen Location . -
Constellation Space Suit System Acquisition Schedule Plan
National Aeronautics and Space Administration ConstellationConstellation SpaceSpace Suit Suit SystemSystem ContractContract AwardAward AnnouncementAnnouncement DougDoug CookeCooke DeputyDeputy AssociateAssociate AdministratorAdministrator NASANASA ExplorationExploration SystemsSystems MissionMission DirectorateDirectorate JuneJune 12,12, 20082008 www.nasa.gov ConstellationConstellation SystemsSystems Division Extravehicular Activity – “EVA” • The space-suited astronaut is the ultimate symbol of human exploration • The spacesuit is essentially a self- contained, one-person spacecraft • It protects the crew from and enables them to work in the hostile environments of deep space and the lunar surface • It is the “last line of defense” for astronauts when they leave the relative safety of the crew exploration vehicle, lunar lander, or habitat 2 2 The Challenge for Exploration • Current spacesuits are not suitable for Exploration – Apollo Extravehicular Mobility Unit – Advanced Crew Escape Suit – Space Shuttle/International Space Station Extravehicular Mobility Unit • A new pressurized suit system will be required to support long-term Exploration requirements – Meets all capability requirements – Improves reliability – Improves logistics and maintenance – Reduces life cycle costs 3 3 The EVA System Design Approach Launch and Entry • A single spacesuit system with two configurations which share many components In-space Contingency • Common, evolvable infrastructure • Minimum set of hardware to meet all mission phase requirements • Modular, -
The EVA Spacesuit
POLITECNICO DI TORINO Repository ISTITUZIONALE Glove Exoskeleton for Extra-Vehicular Activities: Analysis of Requirements and Prototype Design Original Glove Exoskeleton for Extra-Vehicular Activities: Analysis of Requirements and Prototype Design / Favetto, Alain. - (2014). Availability: This version is available at: 11583/2546950 since: Publisher: Politecnico di Torino Published DOI:10.6092/polito/porto/2546950 Terms of use: openAccess This article is made available under terms and conditions as specified in the corresponding bibliographic description in the repository Publisher copyright (Article begins on next page) 04 August 2020 POLITECNICO DI TORINO DOCTORATE SCHOOL Ph. D. In Informatics and Systems – XXV cycle Doctor of Philosophy Thesis Glove Exoskeleton for Extra-Vehicular Activities Analysis of Requirements and Prototype Design (Part One) Favetto Alain Advisor: Coordinator: Prof. Giuseppe Carlo Calafiore Prof. Pietro Laface kp This page is intentionally left blank Dedicato a mio Padre... Al tuo modo ruvido di trasmettere le emozioni. Al tuo senso del dovere ed al tuo altruismo. Ai tuoi modi di fare che da piccolo non capivo e oggi sono parte del mio essere. A tutti i pensieri e le parole che vorrei averti detto e che sono rimasti solo nella mia testa. A te che mi hai sempre trattato come un adulto. A te che te ne sei andato prima che adulto lo potessi diventare davvero. opokp This page is intentionally left blank Index INDEX Index .................................................................................................................................................5 -
Dry Lubricant Coating Plays a Hand in Man Reaching for Mars
CASE STUDY Dry Lubricant Coating Plays A Hand In Man Reaching For Mars By Corey Wesnitzer, General Magnaplate Corp. Following the recent successful landings as the severe dust storms experienced on of the ‘Opportunity’ and ‘Spirit’ Rovers on MARS. In response to the growing likelihood Mars, NASA has become more open about its of manned planetary expeditions, ILC Dover investigations into a potential manned lunar of Dover, Delaware, has developed a new mission and a manned planetary expedition generation of spacesuit called the ‘I-Suit’. on Mars itself. In fact, NASA recently set up a new exploration office at its headquarters. Since project Apollo, ILC has been the designer and producer of the space suits Scientists and researchers involved in the for NASA (sub-contracted by Hamilton study, realizing that a hostile environment will Sundstrand), and the Company has leveraged confront long-distance space travelers, have its expertise in material fabrication to noted the requirement of highly specialized manufacture most of the blimps we see technologies and systems, e.g., durable type floating above sporting events, and even the suits for protection against events such inflatable ‘balloons’ that were responsible for the safe landing of both Mars Rovers. A total of 400 humans have been sent to explore space in ILC Dover suits since the mid-1960s and the next manned mission (slated for April 2005) is Expedition-9, a trip to the International Space Station. Space suits are largely modular in design and manufacturing them is a two-part process. ILC Dover is responsible for developing and manufacturing the arms, gloves, legs, torso, waist etc and the liquid cooling ventilation garment (LCVG) that removes most of the body heat from the suit. -
What Would Happen to Our Globes on the Globe of Mars?
FEATURE Globes in space: What would happen to our globes on the globe of Mars? BY KATHERINE MCVEIGH AND TOMAS BURKE Many films have been made regarding life on alternative planets. With the Mars One mission approaching in 2023, there are high expectations regarding future interplanetary travel. The authors provide an ophthalmology perspective on what could happen to our eyes if exposed to the atmosphere of Mars. n 1990, Arnold Schwarzenegger starred in Total Recall [1], a film where he finds himself on Mars. Damage to his Ispacesuit and subsequent exposure to the environment on Mars results in excessive bodily swelling, along with extensive proptosis whereby the globes extend anteriorly beyond the eyelids as his optic nerves are undoubtedly stretched to their maximal capacity. From an ophthalmological perspective, the interpretation of the impact of atmospheric exposure is intriguing. With the anticipated Mars One mission launch in 2023 aiming to establish a habitable settlement in a hostile environment, we ask if what happened is an accurate depiction of what could be expected to happen to us and our ophthalmic globes on that other globe? The atmosphere on Mars has an O2 level of 0.13% and CO2 level of 95%, and is very Armstrong limit, meaning that exposure to thin, approximately 1% of that on Earth at Tense oedematous soft tissue swelling of sea level [2]. This is believed to be a result the environment would result in a prompt the lids will then make it challenging to of the loss of the magnetosphere four and severe dehydration from the mucosal open the lids. -
Master Thesis
Master’s Thesis 2018 30 ECTS Department of International Environment and Development Studies Katharina Glaab Dividing Heaven: Investigating the Influence of the U.S. Ban on Cooperation with China on the Development of Global Outer Space Governance Robert Ronci International Relations LANDSAM The Department of International Environment and Development Studies, Noragric, is the international gateway for the Norwegian University of Life Sciences (NMBU). Established in 1986, Noragric’s contribution to international development lies in the interface between research, education (Bachelor, Master and PhD programmes) and assignments. The Noragric Master’s theses are the final theses submitted by students in order to fulfil the requirements under the Noragric Master’s programmes ‘International Environmental Studies’, ‘International Development Studies’ and ‘International Relations’. The findings in this thesis do not necessarily reflect the views of Noragric. Extracts from this publication may only be reproduced after prior consultation with the author and on condition that the source is indicated. For rights of reproduction or translation contact Noragric. © Robert Ronci, May 2018 [email protected] Noragric Department of International Environment and Development Studies The Faculty of Landscape and Society P.O. Box 5003 N-1432 Ås Norway Tel.: +47 67 23 00 00 Internet: https://www.nmbu.no/fakultet/landsam/institutt/noragric i ii Declaration I, Robert Jay Ronci, declare that this thesis is a result of my research investigations and findings. Sources of information other than my own have been acknowledged and a reference list has been appended. This work has not been previously submitted to any other university for award of any type of academic degree. -
Annual Report 2015
UNITED NATIONS OFFICE FOR OUTER SPACE AFFAIRS 2015 Annual Report UNITED NATIONS UNITED NATIONS OFFICE FOR OUTER SPACE AFFAIRS Annual Report 2015 Foreword . iii Introduction . 1 I .Highlights . 6 II . Space and development . 14 III . Partnerships and cooperation . 24 IV . Awareness-raising and capacity-building . 30 Administrative information . 36 Abbreviations . 40 UNITED NATIONS New York, 2016 © United Nations, May 2016. All rights reserved, worldwide. The designations employed and the presentation of material in this publication do not imply the expression of any opinion whatsoever on the part of the Secretariat of the United Nations concerning the legal status of any country, territory, city or area, or of its authorities, or concerning the delimitation of its frontiers or boundaries. Photographs ©: DigitalGlobe, ESA, NASA, UNOOSA, UN Photo. Publishing production: English, Publishing and Library Section, United Nations Office at Vienna. Foreword Space unifies, and a united international commu- nity will be essential if those targets are to be achieved. Lastly, Space provides us with unique tools, new cutting-edge technology and innovative solutions. All of this puts the United Nations Office for Outer Space Affairs (UNOOSA), with its unique mandate, at the centre of our joint problem-solving efforts, and 2015 can be seen as the first step in this direction. With the adoption of the Committee on the Peaceful Uses of Outer Space (COPUOS) to celebrate the fiftieth anniversary of the first United Nations Conference on the Exploration and Peaceful Uses of Outer Space, UNISPACE+50 The year 2015 was an eventful and crucial year for in Vienna in 2018, the spotlight is on UNOOSA the United Nations. -
Session: CES401: ASME/AIAA LS&S Extravehicular Activity: Systems
https://ntrs.nasa.gov/search.jsp?R=20150021775 2019-08-31T05:23:29+00:00Z View metadata, citation and similar papers at core.ac.uk brought to you by CORE provided by NASA Technical Reports Server AN INTEGRATED EXTRAVEHICULAR ACTIVITY RESEARCH PLAN Andrew F. J. Abercromby, Amy J. Ross, J. Scott Cupples Multiple organizations within NASA and outside of NASA fund and participate in research related to extravehicular activity (EVA). In October 2015, representatives of the EVA Office, the Crew and Thermal Systems Division (CTSD), and the Human Research Program (HRP) at NASA Johnson Space Center agreed on a formal framework to improve multi-year coordination and collaboration in EVA research. At the core of the framework is an Integrated EVA Research Plan and a process by which it will be annually reviewed and updated. The over-arching objective of the collaborative framework is to conduct multi-disciplinary cost-effective research that will enable humans to perform EVAs safely, effectively, comfortably, and efficiently, as needed to enable and enhance human space exploration missions. Research activities must be defined, prioritized, planned and executed to comprehensively address the right questions, avoid duplication, leverage other complementary activities where possible, and ultimately provide actionable evidence- based results in time to inform subsequent tests, developments and/or research activities. Representation of all appropriate stakeholders in the definition, prioritization, planning and execution of research activities is essential to accomplishing the over-arching objective. A formal review of the Integrated EVA Research Plan will be conducted annually. External peer review of all HRP EVA research activities including compilation and review of published literature in the EVA Evidence Book is already performed annually. -
Life Support Baseline Values and Assumptions Document
NASA/TP-2015–218570 Life Support Baseline Values and Assumptions Document Editors: Molly S. Anderson Michael K. Ewert John F. Keener Sandra A. Wagner Responsible National Aeronautics and Space Administration Official: Molly S. Anderson CTSD, Lyndon B. Johnson Space Center National Aeronautics and Space Administration Mail Code EC2 2101 NASA Road One Houston, Texas 77058 March 2015 THE NASA STI PROGRAM OFFICE . IN PROFILE Since its founding, NASA has been dedicated to the • CONFERENCE PUBLICATION. Collected advancement of aeronautics and space science. The papers from scientific and technical conferences, NASA Scientific and Technical Information (STI) symposia, seminars, or other meetings sponsored Program Office plays a key part in helping NASA or cosponsored by NASA. maintain this important role. • SPECIAL PUBLICATION. Scientific, technical, The NASA STI Program Office is operated by or historical information from NASA programs, Langley Research Center, the lead center for NASA’s projects, and mission, often concerned with scientific and technical information. The NASA STI subjects having substantial public interest. Program Office provides access to the NASA STI Database, the largest collection of aeronautical and • TECHNICAL TRANSLATION. English- space science STI in the world. The Program Office language translations of foreign scientific and is also NASA’s institutional mechanism for technical material pertinent to NASA’s mission. disseminating the results of its research and development activities. These results are published Specialized services that complement the STI by NASA in the NASA STI Report Series, which Program Office’s diverse offerings include creating includes the following report types: custom thesauri, building customized databases, organizing and publishing research results .