ISSUES in FRONT-END ENGINEERING of CMOS NANOELECTRONICS by XIAOLONG YANG Presented to the Faculty of the Graduate School Of
Total Page:16
File Type:pdf, Size:1020Kb
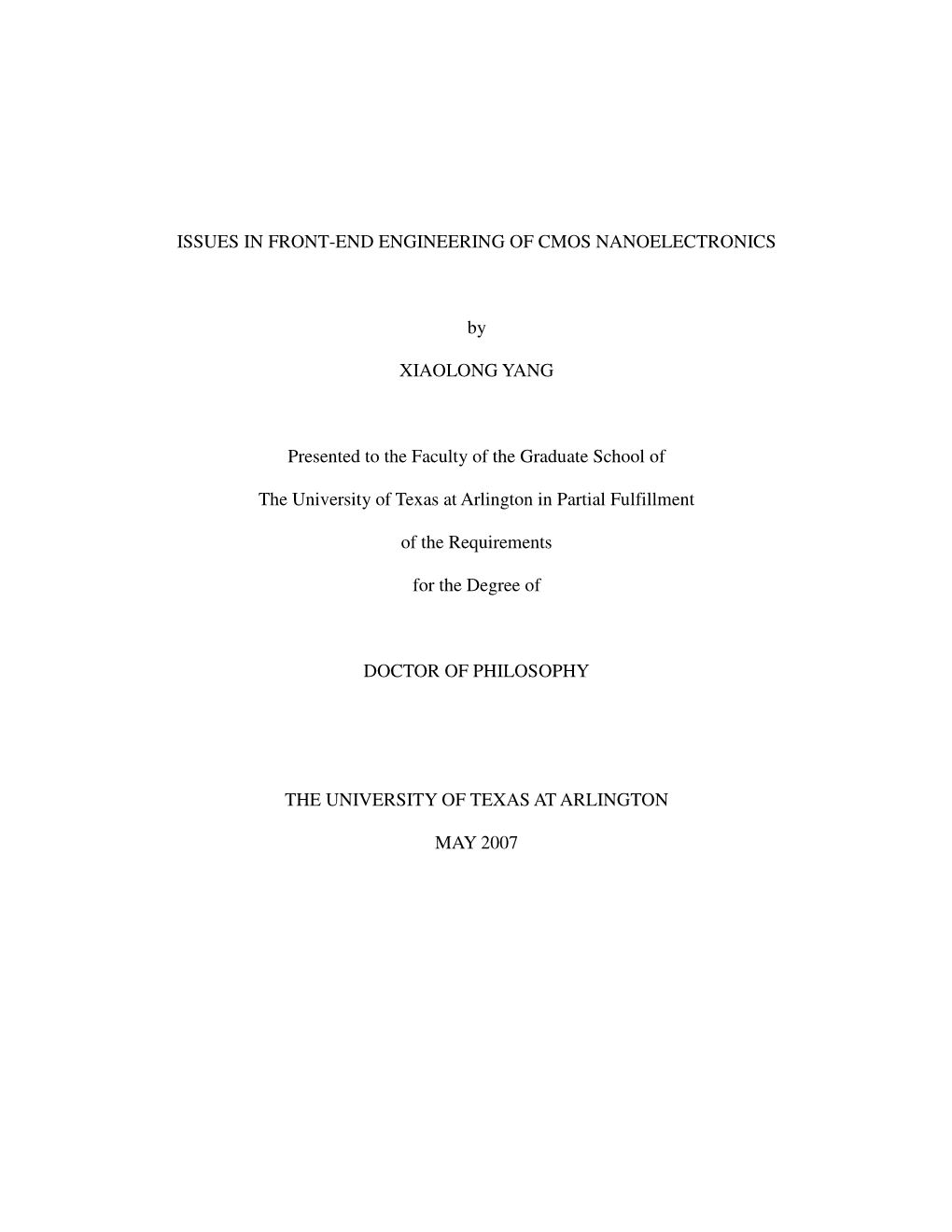
Load more
Recommended publications
-
Resonance-Enhanced Waveguide-Coupled Silicon-Germanium Detector L
Resonance-enhanced waveguide-coupled silicon-germanium detector L. Alloatti and R. J. Ram Citation: Applied Physics Letters 108, 071105 (2016); doi: 10.1063/1.4941995 View online: http://dx.doi.org/10.1063/1.4941995 View Table of Contents: http://scitation.aip.org/content/aip/journal/apl/108/7?ver=pdfcov Published by the AIP Publishing Articles you may be interested in Waveguide-coupled detector in zero-change complementary metal–oxide–semiconductor Appl. Phys. Lett. 107, 041104 (2015); 10.1063/1.4927393 Efficient evanescent wave coupling conditions for waveguide-integrated thin-film Si/Ge photodetectors on silicon- on-insulator/germanium-on-insulator substrates J. Appl. Phys. 110, 083115 (2011); 10.1063/1.3642943 Metal-semiconductor-metal Ge photodetectors integrated in silicon waveguides Appl. Phys. Lett. 92, 151114 (2008); 10.1063/1.2909590 Guided-wave near-infrared detector in polycrystalline germanium on silicon Appl. Phys. Lett. 87, 203507 (2005); 10.1063/1.2131175 Back-side-illuminated high-speed Ge photodetector fabricated on Si substrate using thin SiGe buffer layers Appl. Phys. Lett. 85, 3286 (2004); 10.1063/1.1805706 Reuse of AIP Publishing content is subject to the terms at: https://publishing.aip.org/authors/rights-and-permissions. IP: 18.62.22.131 On: Mon, 07 Mar 2016 17:12:57 APPLIED PHYSICS LETTERS 108, 071105 (2016) Resonance-enhanced waveguide-coupled silicon-germanium detector L. Alloattia),b) and R. J. Ram Massachusetts Institute of Technology, Cambridge, Massachusetts 02139, USA (Received 5 January 2016; accepted 3 February 2016; published online 16 February 2016) A photodiode with 0.55 6 0.1 A/W responsivity at a wavelength of 1176.9 nm has been fabricated in a 45 nm microelectronics silicon-on-insulator foundry process. -
Nanoelectronics the Original Positronic Brain?
Nanoelectronics the Original Positronic Brain? Dan Hammerstrom Department of Electrical and Computer Engineering Portland State University Maseeh College of Engineering 12/13/08 1 and Computer Science Wikipedia: “A positronic brain is a fictional technological device, originally conceived by science fiction writer Isaac Asimov “Its role is to serve as a central computer for a robot, and, in some unspecified way, to provide it with a form of consciousness recognizable to humans” How close are we? You can judge the algorithms, in this talk I will focus on hardware and what the future might hold Maseeh College of Engineering 12/13/08 Hammerstrom 2 and Computer Science Moore’s Law: The number of transistors doubles every 18-24 months No discussion of computing is complete without addressing Moore’s law The semiconductor industry has been following it for almost 30 years It is not really a physical law, but one of faith The fruits of a hyper-competitive $300 billion global industry Then there is Moore’s lesser known 2nd law st The 1 law requires exponentially increasing investment And what I call Moore’s 3rd law st The 1 law results in exponentially increasing design errata Maseeh College of Engineering 12/13/08 Hammerstrom 3 and Computer Science Intel is now manufacturing in their new, innovative 45 nm process Effective gate lengths of 37 nm (HkMG) And they recently announced a 32 nm scaling of the 45 nm process Transistors of this size are no longer acting like ideal switches And there are other problems … 45 nm Transistor -
Which Is the Best Dual-Port SRAM in 45-Nm Process Technology? – 8T, 10T Single End, and 10T Differential –
Which is the Best Dual-Port SRAM in 45-nm Process Technology? – 8T, 10T Single End, and 10T Differential – Hiroki Noguchi†, Shunsuke Okumura†, Yusuke Iguchi†, Hidehiro Fujiwara†, Yasuhiro Morita†, Koji Nii†,††, Hiroshi Kawaguchi†, and Masahiko Yoshimoto† † Kobe University, Kobe, 657-8501 Japan. †† Renesas Technology Corporation, Itami, 664-0005 Japan. Phone: +81-78-803-6234, E-mail: [email protected] read ports. The next section describes their cell topologies. Abstract— This paper compares readout powers and operating frequencies among dual-port SRAMs: an 8T SRAM, 10T II. CELL TOPOLOGIES single-end SRAM, and 10T differential SRAM. The conventional 8T SRAM has the least transistor count, and is the most area A. 8T SRAM efficient. However, the readout power becomes large and the (a) cycle time increases due to peripheral circuits. The 10T Precharge Precharge circuit single-end SRAM is our proposed SRAM, in which a dedicated signal MC inverter and transmission gate are appended as a single-end read Bitline leakage port. The readout power of the 10T single-end SRAM is reduced by 75% and the operating frequency is increased by 95%, over the 8T SRAM. On the other hand the 10T differential SRAM can MC Memory cell (MC) operate fastest, because its small differential voltage of 50 mV RWL achieves the high-speed operation. In terms of the power WWL Readout current efficiency, however, the sense amplifier and precharge circuits lead to the power overhead. As a result, the 10T single-end P1 P2 Bitline keeper SRAM always consumes lowest readout power compared to the 8T and the 10T differential SRAM. -
Technology Roadmap for 22Nm CMOS and Beyond
Technology Roadmap for 22nm CMOS and beyond June 1, 2009 IEDST 2009@IIT-Bombay Hiroshi Iwai Tokyo Institute of Technology 1 Outline 1. Scaling 2. ITRS Roadmap 3. Voltage Scaling/ Low Power and Leakage 4. SRAM Cell Scaling 5.Roadmap for further future as a personal view 2 1. Scaling 3 Scaling Method: by R. Dennard in 1974 1 Wdep: Space Charge Region (or Depletion Region) Width 1 1 SDWdep has to be suppressed 1 Otherwise, large leakage Wdep between S and D I Leakage current Potential in space charge region is high, and thus, electrons in source are 0 attracted to the space charge region. 0 V 1 K=0.7 X , Y, Z :K, V :K, Na : 1/K for By the scaling, Wdep is suppressed in proportion, example and thus, leakage can be suppressed. K Good scaled I-V characteristics K K Wdep V/Na K Wdep I I : K : K 0 0K V 4 Downscaling merit: Beautiful! Geometry & L , W g g K Scaling K : K=0.7 for example Supply voltage Tox, Vdd Id = vsatWgCo (Vg‐Vth) Co: gate C per unit area Drive current I d K –1 ‐1 ‐1 in saturation Wg (tox )(Vg‐Vth)= Wgtox (Vg‐Vth)= KK K=K Id per unit Wg Id/µm 1 Id per unit Wg = Id / Wg= 1 Gate capacitance Cg K Cg = εoεoxLgWg/tox KK/K = K Switching speed τ K τ= CgVdd/Id KK/K= K Clock frequency f 1/K f = 1/τ = 1/K Chip area Achip α α: Scaling factor In the past, α>1 for most cases Integration (# of Tr) N α/K2 N α/K2 = 1/K2 , when α=1 Power per chip P α fNCV2/2 K‐1(αK‐2)K (K1 )2= α = 1, when α=1 5 k= 0.7 and α =1 k= 0.72 =0.5 and α =1 Single MOFET Vdd 0.7 Vdd 0.5 Lg 0.7 Lg 0.5 Id 0.7 Id 0.5 Cg 0.7 Cg 0.5 P (Power)/Clock P (Power)/Clock 0.73 = 0.34 0.53 = 0.125 τ (Switching time) 0.7 τ (Switching time) 0.5 Chip N (# of Tr) 1/0.72 = 2 N (# of Tr) 1/0.52 = 4 f (Clock) 1/0.7 = 1.4 f (Clock) 1/0.5 = 2 P (Power) 1 P (Power) 1 6 - The concerns for limits of down-scaling have been announced for every generation. -
Performance and Energy Efficient Network-On-Chip Architectures
Linköping Studies in Science and Technology Dissertation No. 1130 Performance and Energy Efficient Network-on-Chip Architectures Sriram R. Vangal Electronic Devices Department of Electrical Engineering Linköping University, SE-581 83 Linköping, Sweden Linköping 2007 ISBN 978-91-85895-91-5 ISSN 0345-7524 ii Performance and Energy Efficient Network-on-Chip Architectures Sriram R. Vangal ISBN 978-91-85895-91-5 Copyright Sriram. R. Vangal, 2007 Linköping Studies in Science and Technology Dissertation No. 1130 ISSN 0345-7524 Electronic Devices Department of Electrical Engineering Linköping University, SE-581 83 Linköping, Sweden Linköping 2007 Author email: [email protected] Cover Image A chip microphotograph of the industry’s first programmable 80-tile teraFLOPS processor, which is implemented in a 65-nm eight-metal CMOS technology. Printed by LiU-Tryck, Linköping University Linköping, Sweden, 2007 Abstract The scaling of MOS transistors into the nanometer regime opens the possibility for creating large Network-on-Chip (NoC) architectures containing hundreds of integrated processing elements with on-chip communication. NoC architectures, with structured on-chip networks are emerging as a scalable and modular solution to global communications within large systems-on-chip. NoCs mitigate the emerging wire-delay problem and addresses the need for substantial interconnect bandwidth by replacing today’s shared buses with packet-switched router networks. With on-chip communication consuming a significant portion of the chip power and area budgets, there is a compelling need for compact, low power routers. While applications dictate the choice of the compute core, the advent of multimedia applications, such as three-dimensional (3D) graphics and signal processing, places stronger demands for self-contained, low-latency floating-point processors with increased throughput. -
Lecture 5: Scaled MOSFETS for Ics
Lecture 5: Scaled MOSFETS for ICs MSE 6001, Semiconductor Materials Lectures Fall 2006 5 MOSFETS and scaling Silicon is a mediocre semiconductor, and several other semiconductors have better electrical and optical properties. However, the very high quality of the electrical properties of the silicon-silicon dioxide interface allows very good metal-oxide-semiconductor field-effect transistors (MOSFETs) to be fabricated. These devices have several properties, such as operation frequency and power con- sumption, that improve as their size is scaled down to smaller dimensions, which also allows more transistors to be packed onto a chip. The smaller sizes are achieved using higher-resolution pho- tolithography, which is improved by steadily improving the fabrication technologies. The trends of steadily improving performance and greater integration density with time are generically refered to A 70 Mbit SRAM test vehicle with >as0.5 “Moore’s billion trans Law”.istors Of course, scaling has to end eventually, somewhere before the scale of atoms and incorporating all of the features described in this paper has been fabricated on this technologyis. reached.The aggressive de- sign rules allow for a small 0.57Pm2 6-T SRAM cell that is also compatible with high performance logic processing. A top view of the cell after poly patterni5.1ng is show Basicn in Figur MOSFETe 12. In addition to small size, this cell has a robust static noise margin down to 0.7V VDD to alloMOSFETsw low voltage turnopera- on and off via the non-linear gate capacitor between the gate electrode and the tion (Fig. 13). Figure 14 is a Shmosubstrate.o plot for the The 70 M MOSFETb of Fig. -
By Erika Azabache Villar a Thesis Submitted in Partial Fulfillment of The
SMALLER/FASTER DELTA-SIGMA DIGITAL PIXEL SENSORS by Erika Azabache Villar A thesis submitted in partial fulfillment of the requirements for the degree of Master of Science in Integrated Circuits and Systems Department of Electrical and Computer Engineering University of Alberta c Erika Azabache Villar, 2016 Abstract A digital pixel sensor (DPS) array is an image sensor where each pixel has an analog-to-digital converter (ADC). Recently, a logarithmic delta-sigma (ΔΣ) DPS array, using first-order ΔΣ ADCs, achieved wide dynamic range and high signal-to-noise-and-distortion ratios at video rates, requirements that are difficult to meet using conventional image sensors. However, this state-of-the-art ΔΣ DPS design is either too large for some applications, such as optical imag- ing, or too slow for others, such as gamma imaging. Consequently, this master’s thesis investi- gates smaller or faster ΔΣ DPS designs, relative to the state of the art. All designs are validated through simulations. Commercial image sensors, for optical and gamma imaging, are used as targeted baselines to establish competitive specifications. To achieve a smaller pixel, process scaling is exploited. Three logarithmic ΔΣ DPS designs are presented for 180, 130, and 65 nm fabrication processes, demonstrating a path to competitiveness for the optical imaging market. Decimator and readout circuits are improved, compared to previous work, while reducing area, and capacitors in the modulator prove to be the limiting factor in deep-submicron processes. Area trends are used to construct a roadmap to even smaller pixels. To achieve a faster pixel, a higher-order ΔΣ architecture is exploited. -
A Study of the Foundry Industry Dynamics
A Study of the Foundry Industry Dynamics by Sang Jin Oh B.S. Industrial Engineering Seoul National University, 2003 SUBMITTED TO THE MIT SLOAN SCHOOL OF MANAGEMENT IN PARTIAL FULFILLMENT OF THE REQUIREMENTS FOR THE DEGREE OF MASTER OF SCIENCE IN MANAGEMENT STUDIES AT THE MASSACHUSETTS INSTITUTE OF TECHNOLOGY ARCHVES JUNE 2010 MASSACHUSETTS INSTiUTE OF TECHNOLOGY © 2010 Sang Jin Oh. All Rights Reserved. The author hereby grants MIT permission to reproduce JUN 082010 and to distribute publicly paper and electronic LIBRARIES copies of this thesis document in whole or in part in any medium now known and hereafter created. Signature of Author Sang Jin Oh Master of Science in Management Studies May 7, 2010 Certified by (7 Michael A. Cusumano SMR Distinguished Professor of Management Thesis Supervisor Accepted by (I Michael A. Cusumano Faculty Director, M.S. in Management Studies Program MIT Sloan School of Management A Study of the Foundry Industry Dynamics By Sang Jin Oh Submitted to the MIT Sloan School of Management On May 7, 2010 In Partial Fulfillment of the Requirements for the Degree of Master of Science in Management Studies Abstract In the process of industrial evolution, it is a general tendency that companies which specialize in a specific value chain have emerged. These companies should construct a business eco-system based on their own platform to compete successfully with vertically integrated companies and other specialized companies. They continue to sustain their competitive advantage only when they share their ability to create value with other eco-system partners. The thesis analyzes the dynamics of the foundry industry. -
Multiprocessing Contents
Multiprocessing Contents 1 Multiprocessing 1 1.1 Pre-history .............................................. 1 1.2 Key topics ............................................... 1 1.2.1 Processor symmetry ...................................... 1 1.2.2 Instruction and data streams ................................. 1 1.2.3 Processor coupling ...................................... 2 1.2.4 Multiprocessor Communication Architecture ......................... 2 1.3 Flynn’s taxonomy ........................................... 2 1.3.1 SISD multiprocessing ..................................... 2 1.3.2 SIMD multiprocessing .................................... 2 1.3.3 MISD multiprocessing .................................... 3 1.3.4 MIMD multiprocessing .................................... 3 1.4 See also ................................................ 3 1.5 References ............................................... 3 2 Computer multitasking 5 2.1 Multiprogramming .......................................... 5 2.2 Cooperative multitasking ....................................... 6 2.3 Preemptive multitasking ....................................... 6 2.4 Real time ............................................... 7 2.5 Multithreading ............................................ 7 2.6 Memory protection .......................................... 7 2.7 Memory swapping .......................................... 7 2.8 Programming ............................................. 7 2.9 See also ................................................ 8 2.10 References ............................................. -
Stratix III Programmable Power
White Paper Stratix III Programmable Power Introduction Traditionally, digital logic has not consumed significant static power, but this has changed with very small process nodes. Leakage current in digital logic is now the primary challenge for FPGAs as process geometries decrease. While the move to the 65-nm process delivers the expected Moore's law benefits of increased density and performance, the performance increases can result in significant increases in power consumption, introducing the risk of consuming unacceptable amounts of power. If no power-reduction strategies are employed, power consumption becomes a critical issue because static power can increase dramatically with the 65-nm process. Static power consumption rises largely because of increases in various sources of leakage current. Figure 1 shows how these sources of leakage current (shown in blue) increase as the technology makes smaller gate lengths possible (shown in green). In addition, without any specific power optimization effort, dynamic power consumption can increase due to the increased logic capacity and higher switching frequencies that are attainable. Figure 1. Static Power Dissipation Increases Significantly at Smaller Process Geometries 300 100 250 Subthreshold 1 Leakage 200 150 10-2 Power Dissipation 100 Physical Gate Length [nm] Technology -4 Node 10 50 Gate-Oxide Leakage 0 10-6 Data from International Technology 1990 1995 2000 2005 2010 2015 2020 Roadmap for Semiconductors ITRS Roadmap Power consumption is composed of static and dynamic power. Static power is the power consumed by the FPGA when it is programmed with a Programmer Object File (.pof) but no clocks are operating. Both digital and analog logic consume static power. -
AN-Introducing 45Nm Technology in Microwind
Introducing 45 nm technology in Microwind3 MICROWIND APPLICATION NOTE Introducing 45 nm technology in Microwind3 Etienne SICARD Syed Mahfuzul Aziz Professor School of Electrical & Information Engineering INSA-Dgei, 135 Av de Rangueil University of South Australia 31077 Toulouse – France Mawson Lakes, SA 5095, Australia www.microwind.org www.unisa.edu.au email: [email protected] email: [email protected] This paper describes the improvements related to the CMOS 45 nm technology and the implementation of this technology in Microwind3. The main novelties related to the 45 nm technology such as the high-k gate oxide, metal- gate and very low-K interconnect dielectric is described. The performances of a ring oscillator layout and a 6- transistor RAM memory layout are also analyzed. 1. Recent trends in CMOS technology Firstly, we give an overview of the evolution of important parameters such as the integrated circuit (IC) complexity, gate length, switching delay and supply voltage with a prospective vision down to the 22 nm CMOS technology. The trend of CMOS technology improvement continues to be driven by the need to integrate more functions within a given silicon area. Table 1 gives an overview of the key parameters for technological nodes from 180 nm, introduced in 1999, down to 22 nm, which is supposed to be in production around 2011. Demonstration chips using 45-nm technology have been reported starting in 2004. Mass market manufacturing with this technology is scheduled for late 2007. Technology node 130 nm 90 nm 65 nm 45 nm 32 nm 22 nm First production 2001 2003 2005 2007 2009 2011 Effective gate 70 nm 50 nm 35 nm 25 nm 17 nm 12 nm length Gate material Poly Poly Poly Metal Metal Metal Gate dielectric SiO2 SiO2 SiON High K High K High K Kgates/mm2 240 480 900 1500 2800 4500 Memory point (2) 2.4 1.3 0.6 0.3 0.15 0.08 Table 1: Technological evolution and forecast up to 2011 The gate material has long been polysilicon, with silicon dioxide (SiO2) as the insulator between the gate and the channel (Fig. -
The New Era of Scaling in an Soc World
2009 ISSCC The New Era of Scaling in an SoC World Mark Bohr Intel Senior Fellow Logic Technology Development 1 The End of Scaling is Near? “Optical lithography will reach its limits in the range of 0.75-0.50 microns” “Minimum geometries will saturate in the range of 0.3 to 0.5 microns” “X-ray lithography will be needed below 1 micron” “Minimum gate oxide thickness is limited to ~2 nm” “Copper interconnects will never work” “Scaling will end in ~10 years” Perceived barriers are meant to be surmounted, circumvented or tunneled through 2 Outline • Transistor Scaling • Microprocessor Evolution • Vision of the Future 3 Scaling Trends 10 CPU Transistor Count 10 9 2x every 2 years 1 10 7 Microns 0.1 10 5 3 0.01 10 1970 1980 1990 2000 2010 2020 Transistor dimensions scale to improve performance, reduce power and reduce cost per transistor 4 Scaling Trends 10 CPU Transistor Count 10 9 2x every 2 years 1 10 7 Microns 0.1 65nm 10 5 45nm Feature Size 32nm 0.7x every 2 years 3 0.01 10 1970 1980 1990 2000 2010 2020 Transistor dimensions scale to improve performance, reduce power and reduce cost per transistor 5 MOSFET Scaling Device or Circuit Parameter Scaling Factor Device dimension tox, L, W 1/ κ Doping concentration Na κ Voltage V 1/ κ Current I 1/ κ Capacitance εA/t 1/ κ Delay time/circuit VC/I 1/ κ Power dissipation/circuit VI 1/ κ2 Power density VI/A 1 R. Dennard, IEEE JSSC, 1974 Classical MOSFET scaling was first described in 1974 6 30 Years of MOSFET Scaling Dennard 1974 Intel 2005 1 µm Gate Length: 1.0 µm 35 nm Gate Oxide Thickness: 35 nm