The Intent of the CHP Is to Protect Employees from Health Hazards
Total Page:16
File Type:pdf, Size:1020Kb
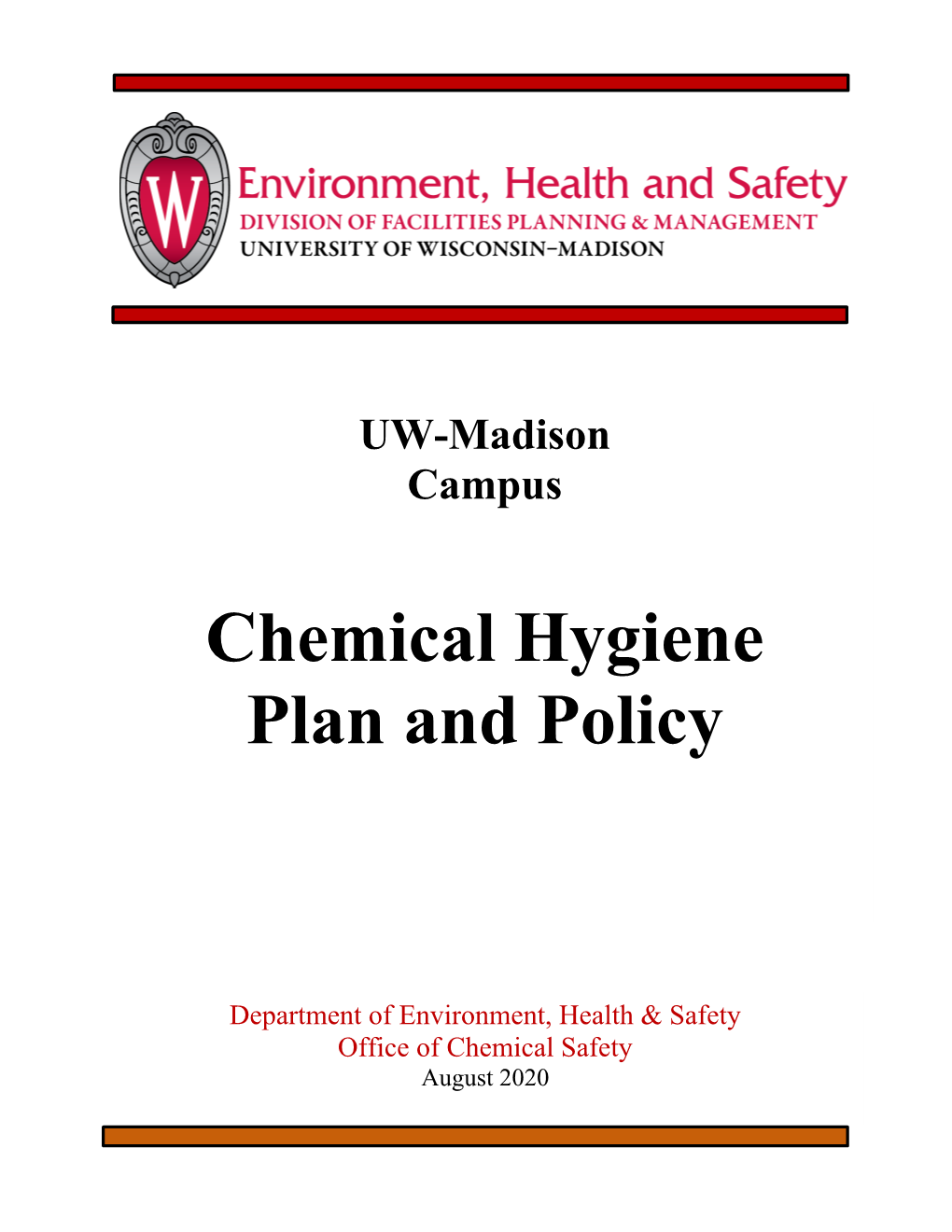
Load more
Recommended publications
-
General Listing Background Document for the Inorganic Chemical Listing Determination
GENERAL LISTING BACKGROUND DOCUMENT FOR THE INORGANIC CHEMICAL LISTING DETERMINATION August, 2000 U.S. ENVIRONMENTAL PROTECTION AGENCY ARIEL RIOS BUILDING 1200 PENNSYLVANIA AVENUE, N.W. WASHINGTON, D.C. 20460 TABLE OF CONTENTS Page LIST OF TABLES .............................................................ii LIST OF FIGURES ............................................................ii LIST OF APPENDICES .........................................................ii 1. INTRODUCTION .......................................................1 1.1 BACKGROUND ...................................................1 1.2 EXISTING INORGANIC CHEMICAL LISTINGS ........................2 1.3 OTHER EPA REGULATORY PROGRAMS AFFECTING THE INORGANIC CHEMICAL INDUSTRY ............................................3 2. INDUSTRY DESCRIPTION .........................................5 2.1 INDUSTRY PROFILE ..............................................5 2.2 INDUSTRY SECTORS .............................................5 2.2.1 Antimony Oxide ..............................................8 2.2.2 Barium Carbonate ............................................8 2.2.3 Boric Acid ..................................................8 2.2.4 Cadmium Pigments ............................................8 2.2.5 Inorganic Hydrogen Cyanide ....................................8 2.2.6 Phenyl Mercuric Acetate .......................................8 2.2.7 Dry Process Phosphoric Acid ....................................8 2.2.8 Phosphorous Pentasulfide .......................................8 -
"The Science for Diplomats" Annex on Chemicals
ORGANISATION FOR THE PROHIBITION OF CHEMICAL WEAPONS "THE SCIENCE FOR DIPLOMATS" ANNEX ON CHEMICALS A user friendly and scientifically annotated version of the Chemical Weapons Convention Annex on Chemicals OPCW THE “SCIENCE FOR DIPLOMATS” ANNEX ON CHEMICALS A user friendly and scientifically annotated version of the Chemical Weapons Convention Annex on Chemicals1 CONTENTS A. GUIDELINES FOR SCHEDULES OF CHEMICALS B. VISUALISING AND READING MOLECULAR STRUCTURES C. SCHEDULES OF CHEMICALS D. RIOT CONTROL AGENTS 1 An official version of the Annex on Chemicals can be obtained from the OPCW public website, www.opcw.org/chemical-weapons-convention/annexes/annex-chemicals/annex-chemicals. Version 3.0 – 10 March 2019 A. GUIDELINES FOR SCHEDULES OF CHEMICALS Guidelines for Schedule 1 1. The following criteria shall be taken into account in considering whether a toxic chemical or precursor should be included in Schedule 1: (a) It has been developed, produced, stockpiled or used as a chemical weapon as defined in Article II; (b) It poses otherwise a high risk to the object and purpose of this Convention by virtue of its high potential for use in activities prohibited under this Convention because one or more of the following conditions are met: (i) It possesses a chemical structure closely related to that of other toxic chemicals listed in Schedule 1, and has, or can be expected to have, comparable properties; (ii) It possesses such lethal or incapacitating toxicity as well as other properties that would enable it to be used as a chemical weapon; (iii) It may be used as a precursor in the final single technological stage of production of a toxic chemical listed in Schedule 1, regardless of whether this stage takes place in facilities, in munitions or elsewhere; (c) It has little or no use for purposes not prohibited under this Convention. -
Pacs by Chemical Name (Mg/M3) (Pdf)
Table 4: Protective Action Criteria (PAC) Rev 25 based on applicable 60-minute AEGLs, ERPGs, or TEELs. Values are presented in mg/m3. August 2009 Table 4 is an alphabetical listing of the chemicals in the PAC data set. It provides Chemical Abstract Service Registry Numbers (CASRNs)1, PAC values, and technical information on the source of the PAC values. Table 4 presents all values for TEEL-0, PAC-1, PAC-2, and PAC-3 in mg/m3. The conversion of ppm to mg/m3 is calculated assuming 25 ºC and 760 mm Hg. The columns presented in Table 4 provide the following information: Heading Definition No. The ordered numbering of the chemicals as they appear in this alphabetical listing. Chemical Name The chemical name given to the PAC Development Team. CASRN The Chemical Abstract Service Registry Number for this chemical. TEEL-0 This is the threshold concentration below which most people will experience no adverse health effects. This PAC is always based on TEEL-0 because AEGL-0 or ERPG-0 values do not exist. PAC-1 Based on the applicable AEGL-1, ERPG-1, or TEEL-1 value. PAC-2 Based on the applicable AEGL-2, ERPG-2, or TEEL-2 value. PAC-3 Based on the applicable AEGL-3, ERPG-3, or TEEL-3 value. Source of PACs: Technical comments provided by the PAC development team that TEEL-0, PAC-1, indicate the source of the data used to derive PAC values. Future efforts PAC-2, PAC-3 are directed at reviewing, revising, and enhancing this information. -
WO 2016/074683 Al 19 May 2016 (19.05.2016) W P O P C T
(12) INTERNATIONAL APPLICATION PUBLISHED UNDER THE PATENT COOPERATION TREATY (PCT) (19) World Intellectual Property Organization International Bureau (10) International Publication Number (43) International Publication Date WO 2016/074683 Al 19 May 2016 (19.05.2016) W P O P C T (51) International Patent Classification: (81) Designated States (unless otherwise indicated, for every C12N 15/10 (2006.01) kind of national protection available): AE, AG, AL, AM, AO, AT, AU, AZ, BA, BB, BG, BH, BN, BR, BW, BY, (21) International Application Number: BZ, CA, CH, CL, CN, CO, CR, CU, CZ, DE, DK, DM, PCT/DK20 15/050343 DO, DZ, EC, EE, EG, ES, FI, GB, GD, GE, GH, GM, GT, (22) International Filing Date: HN, HR, HU, ID, IL, IN, IR, IS, JP, KE, KG, KN, KP, KR, 11 November 2015 ( 11. 1 1.2015) KZ, LA, LC, LK, LR, LS, LU, LY, MA, MD, ME, MG, MK, MN, MW, MX, MY, MZ, NA, NG, NI, NO, NZ, OM, (25) Filing Language: English PA, PE, PG, PH, PL, PT, QA, RO, RS, RU, RW, SA, SC, (26) Publication Language: English SD, SE, SG, SK, SL, SM, ST, SV, SY, TH, TJ, TM, TN, TR, TT, TZ, UA, UG, US, UZ, VC, VN, ZA, ZM, ZW. (30) Priority Data: PA 2014 00655 11 November 2014 ( 11. 1 1.2014) DK (84) Designated States (unless otherwise indicated, for every 62/077,933 11 November 2014 ( 11. 11.2014) US kind of regional protection available): ARIPO (BW, GH, 62/202,3 18 7 August 2015 (07.08.2015) US GM, KE, LR, LS, MW, MZ, NA, RW, SD, SL, ST, SZ, TZ, UG, ZM, ZW), Eurasian (AM, AZ, BY, KG, KZ, RU, (71) Applicant: LUNDORF PEDERSEN MATERIALS APS TJ, TM), European (AL, AT, BE, BG, CH, CY, CZ, DE, [DK/DK]; Nordvej 16 B, Himmelev, DK-4000 Roskilde DK, EE, ES, FI, FR, GB, GR, HR, HU, IE, IS, IT, LT, LU, (DK). -
The Migration of Arsenic and Lead in Surface Sediments at Three Kids Mine Henderson, Nevada
Publications (WR) Water Resources 12-1997 The Migration of arsenic and lead in surface sediments at Three Kids Mine Henderson, Nevada Douglas Brian Sims Follow this and additional works at: https://digitalscholarship.unlv.edu/water_pubs Part of the Biogeochemistry Commons, Environmental Health and Protection Commons, Environmental Indicators and Impact Assessment Commons, Environmental Monitoring Commons, Geology Commons, and the Soil Science Commons Repository Citation Sims, D. B. (1997). The Migration of arsenic and lead in surface sediments at Three Kids Mine Henderson, Nevada. Available at: https://digitalscholarship.unlv.edu/water_pubs/21 This Thesis is protected by copyright and/or related rights. It has been brought to you by Digital Scholarship@UNLV with permission from the rights-holder(s). You are free to use this Thesis in any way that is permitted by the copyright and related rights legislation that applies to your use. For other uses you need to obtain permission from the rights-holder(s) directly, unless additional rights are indicated by a Creative Commons license in the record and/ or on the work itself. This Thesis has been accepted for inclusion in Publications (WR) by an authorized administrator of Digital Scholarship@UNLV. For more information, please contact [email protected]. THE MIGRATION OF ARSENIC AND LEAD IN SURFACE SEDIMENTS AT THREE KIDS MINE HENDERSON, NEVADA by Douglas Brian Sims ^ Bachelor of Arts University of Nevada, Las Vegas 1995 A thesis submitted in partial fulfillment of the requirements for the degree of Master of Science in Water Resources Management r •:'•• 3 338 . Department of Geoscience University of Nevada, Las Vegas December 1997 The Thesis of Douglas B. -
459 Part 121—The United States Munitions List
Department of State § 121.1 (h) Equipment is a combination of 121.1 The United States Munitions List. parts, components, accessories, attach- 121.2–121.15 [Reserved] ments, firmware, or software that oper- 121.16 Missile Technology Control Regime ate together to perform a function of, Annex. as, or for an end-item or system. AUTHORITY: Secs. 2, 38, and 71, Pub. L. 90– Equipment may be a subset of an end- 629, 90 Stat. 744 (22 U.S.C. 2752, 2778, 2797); 22 item based on the characteristics of U.S.C. 2651a; Pub. L. 105–261, 112 Stat. 1920; Section 1261, Pub. L. 112–239; E.O. 13637, 78 FR the equipment. Equipment that meets 16129. the definition of an end-item is an end- item. Equipment that does not meet SOURCE: 58 FR 39287, July 22, 1993, unless the definition of an end-item is a com- otherwise noted. ponent, accessory, attachment, ENUMERATION OF ARTICLES firmware, or software. [79 FR 61228, Oct. 10, 2014] § 121.1 The United States Munitions List. § 120.46 Classified. (a) U.S. Munitions List. In this part, Classified means classified pursuant articles, services, and related technical to Executive Order 13526, and a secu- data are designated as defense articles rity classification guide developed pur- or defense services pursuant to sections suant thereto or equivalent, or to the 38 and 47(7) of the Arms Export Control corresponding classification rules of Act and constitute the U.S. Munitions another government or international List (USML). Changes in designations organization. are published in the FEDERAL REG- ISTER. -
ITAR Category
Category XIV—Toxicological Agents, Including Chemical Agents, Biological Agents, and Associated Equipment *(a) Chemical agents, to include: (1) Nerve agents: (i) O-Alkyl (equal to or less than C10, including cycloalkyl) alkyl (Methyl, Ethyl, n-Propyl or Isopropyl)phosphonofluoridates, such as: Sarin (GB): O-Isopropyl methylphosphonofluoridate (CAS 107–44–8) (CWC Schedule 1A); and Soman (GD): O-Pinacolyl methylphosphonofluoridate (CAS 96–64–0) (CWC Schedule 1A); (ii) O-Alkyl (equal to or less than C10, including cycloalkyl) N,N-dialkyl (Methyl, Ethyl, n- Propyl or Isopropyl)phosphoramidocyanidates, such as: Tabun (GA): O-Ethyl N, N- dimethylphosphoramidocyanidate (CAS 77–81–6) (CWC Schedule 1A); (iii) O-Alkyl (H or equal to or less than C10, including cycloalkyl) S–2-dialkyl (Methyl, Ethyl, n- Propyl or Isopropyl)aminoethyl alkyl (Methyl, Ethyl, n-Propyl or Isopropyl)phosphonothiolates and corresponding alkylated and protonated salts, such as: VX: O-Ethyl S-2- diisopropylaminoethyl methyl phosphonothiolate (CAS 50782–69–9) (CWC Schedule 1A); (2) Amiton: O,O-Diethyl S-[2(diethylamino)ethyl] phosphorothiolate and corresponding alkylated or protonated salts (CAS 78–53–5) (CWC Schedule 2A); (3) Vesicant agents: (i) Sulfur mustards, such as: 2-Chloroethylchloromethylsulfide (CAS 2625–76–5) (CWC Schedule 1A); Bis(2-chloroethyl)sulfide (CAS 505–60–2) (CWC Schedule 1A); Bis(2- chloroethylthio)methane (CAS 63839–13–6) (CWC Schedule 1A); 1,2-bis (2- chloroethylthio)ethane (CAS 3563–36–8) (CWC Schedule 1A); 1,3-bis (2-chloroethylthio)-n- propane (CAS -
High Hazard Chemical Policy
Environmental Health & Safety Policy Manual Issue Date: 2/23/2011 Policy # EHS-200.09 High Hazard Chemical Policy 1.0 PURPOSE: To minimize hazardous exposures to high hazard chemicals which include select carcinogens, reproductive/developmental toxins, chemicals that have a high degree of toxicity. 2.0 SCOPE: The procedures provide guidance to all LSUHSC personnel who work with high hazard chemicals. 3.0 REPONSIBILITIES: 3.1 Environmental Health and Safety (EH&S) shall: • Provide technical assistance with the proper handling and safe disposal of high hazard chemicals. • Maintain a list of high hazard chemicals used at LSUHSC, see Appendix A. • Conduct exposure assessments and evaluate exposure control measures as necessary. Maintain employee exposure records. • Provide emergency response for chemical spills. 3.2 Principle Investigator (PI) /Supervisor shall: • Develop and implement a laboratory specific standard operation plan for high hazard chemical use per OSHA 29CFR 1910.1450 (e)(3)(i); Occupational Exposure to Hazardous Chemicals in Laboratories. • Notify EH&S of the addition of a high hazard chemical not previously used in the laboratory. • Ensure personnel are trained on specific chemical hazards present in the lab. • Maintain Material Safety Data Sheets (MSDS) for all chemicals, either on the computer hard drive or in hard copy. • Coordinate the provision of medical examinations, exposure monitoring and recordkeeping as required. 3.3 Employees: • Complete all necessary training before performing any work. • Observe all safety -
Laboratory Safety and Chemical Hygiene Plan
Western Kentucky University Laboratory Safety and Chemical Hygiene Plan Rev. 12/10/2018 Laboratory Safety and Chemical Hygiene Plan Table of Contents 1 Introduction 7.3 Safely Handling Particularly Hazardous 1.1 Purpose Substances 1.2 Regulatory Basis 7.4 Nanomaterials and Nanoparticles 8 Emergency Planning 1.3 Scope 8.1 Emergency Procedures for Selected 2 Definitions Emergencies 3 Authority, Roles, and Responsibilities 9 Laboratory Security Measures 3.1 University Environmental Health and Safety 3.2 Chemical Hygiene Officer Appendix I – Laboratory Safety Training 3.3 Deans, Directors, and Department Heads or Documentation Chairs of Academic and Administrative Units Appendix II –Standard Operating Procedures 3.4 Laboratory Supervisors Template 3.5 Laboratory Workers & University Students Appendix III – Emergency Phone Number List Door 4 Standard Operating Procedures Posting 5 Laboratory Safety Guidelines Appendix IV – Chemical Container Compatibility 5.1 Controlling Chemical Exposure Appendix V – Hierarchy of Control Methods (visual) 5.2 Laboratory Safety Training 5.3 Personal Protective Equipment Appendix VI – Laboratory Safety Training Checklist 5.4 Medical Consultation Appendix VII – Laboratory Safety Inspection Checklist 5.5 Laboratory Safety Inspections Appendix VIII – Safe Work Practices for Laboratory 6 Laboratory Safety Systems & Equipment Fume Hoods 6.1 Fume Hoods Appendix IX – Sample Weekly Eye Wash Activation Record 6.2 Safety Interlocks and Alarms 6.3 Eye Wash and Safety Showers Appendix X – Chemical Compatibility Charts 6.4 Fire Extinguishers Appendix XI – GHS Label Elements and Pictograms 7 Chemical Hygiene Appendix XII – List of Highly Toxic Substances 7.1 General Principles Appendix XIII – Laboratory Safety Contacts 7.2 Carcinogens, Reproductive Toxins, and Acutely Toxic Chemicals Page 2 of 46 Laboratory Safety and Chemical Hygiene Plan 1. -
Acetylcholinesterase: the “Hub” for Neurodegenerative Diseases And
Review biomolecules Acetylcholinesterase: The “Hub” for NeurodegenerativeReview Diseases and Chemical Weapons Acetylcholinesterase: The “Hub” for Convention Neurodegenerative Diseases and Chemical WeaponsSamir F. de A. Cavalcante Convention 1,2,3,*, Alessandro B. C. Simas 2,*, Marcos C. Barcellos 1, Victor G. M. de Oliveira 1, Roberto B. Sousa 1, Paulo A. de M. Cabral 1 and Kamil Kuča 3,*and Tanos C. C. França 3,4,* Samir F. de A. Cavalcante 1,2,3,* , Alessandro B. C. Simas 2,*, Marcos C. Barcellos 1, Victor1 Institute G. M. ofde Chemical, Oliveira Biological,1, Roberto Radiological B. Sousa and1, Paulo Nuclear A. Defense de M. Cabral (IDQBRN),1, Kamil Brazilian Kuˇca Army3,* and TanosTechnological C. C. França Center3,4,* (CTEx), Avenida das Américas 28705, Rio de Janeiro 23020-470, Brazil; [email protected] (M.C.B.); [email protected] (V.G.M.d.O.); [email protected] 1 Institute of Chemical, Biological, Radiological and Nuclear Defense (IDQBRN), Brazilian Army (R.B.S.); [email protected] (P.A.d.M.C.) Technological Center (CTEx), Avenida das Américas 28705, Rio de Janeiro 23020-470, Brazil; 2 [email protected] Mors Institute of Research (M.C.B.); on Natural [email protected] Products (IPPN), Federal (V.G.M.d.O.); University of Rio de Janeiro (UFRJ), CCS,[email protected] Bloco H, Rio de Janeiro (R.B.S.); 21941-902, [email protected] Brazil (P.A.d.M.C.) 32 DepartmentWalter Mors of Institute Chemistry, of Research Faculty of on Science, Natural Un Productsiversity (IPPN), -
Chemical Weapons Convention Inventory Report - 2017
University of British Columbia Risk Management Services CHEMICAL WEAPONS CONVENTION INVENTORY REPORT - 2017 Department: Name of Building: Room No. Principal Investigator: SCHEDULE 1 CHEMICALS Location Quantity Obtained /Stored / Used A.Toxic Chemicals 1 O-Alkyl (<=C10, incl. cycloalkyl) alkyl (Me, Et, n-Pr or i-Pr) – phosphonofluoridates, Sarin: O-Isopropyl methylphosphonofluoridate (CAS 107-44-8) Soman: O-Pinacolyl methylphosphonofluoridate (CAS 96-64-0) 2 O-Alkyl (H or <=C10, incl. cycloalkyl) S-2-dialkyl (Me, Et, n- Pr or i-Pr) -aminoethyl alkyl (Me, Et, n-Pr or i-Pr) phosphonothiolates, and corresponding alkylated or protonated salts VX: O-Ethyl S-2-diisopropylaminoethyl methyl phosphonothiolate (CAS 50782-69-9) 3 O-Alkyl (H or <=C10, incl. cycloalkyl) S-2-dialkyl (Me, Et, n- Pr or i-Pr) -aminoethyl alkyl (Me, Et, n-Pr or i-Pr) phosphonothiolates, and corresponding alkylated or protonated salts VX: O-Ethyl S-2-diisopropylaminoethyl methyl phosphonothiolate (CAS 50782-69-9) 4 Sulphur Mustards: 2-Chloroethylchloromethylsulfide (CAS 2625-76-5) Mustard gas: Bis (2-chloroethyl) sulfide (CAS 505-60-2) Bis (2-chloroethylthio)methane (CAS 63869-13-6) Sesquimustard: 1, 2-Bis (2-chloroethylthio) ethane (CAS 3563-36-8) 1, 3-Bis (2-chloroethylthio) -n-propane (CAS 63905-10-2) 1, 4-Bis (2-chloroethylthio) -n-butane (CAS 142868-93-7) 1, 5-Bis (2-chloroethylthio) -n-pentane (CAS 142868-94-8) Bis (2-chloroethylthiomethyl) ether (CAS 63918-90-1) O-Mustard: Bis (2-chloroethylthioethyl) ether (CAS 63918-89-8) 5 Lewisites: Lewisite 1: 2-Chlorovinyldichloroarsine (CAS 541-25-3) Lewisite 2: Bis (2-chlorovinyl) chloroarsine (CAS 40334-69-8) Lewisite 3: Tris (2-chlorovinyl) arsine (CAS 40334-70-1) 6 Nitrogen Mustards: HN1: Bis (2-chloroethyl) ethylamine (CAS 538-07-08) HN2: Bis (2-chloroethyl) methylamine (CAS 51-75-2) HN3: Tris (2-chloroethyl) amine (CAS 555-77-1) University of British Columbia Risk Management Services CHEMICAL WEAPONS CONVENTION INVENTORY REPORT - 2017 Department: Name of Building: Room No. -
Chemical Names and CAS Numbers Final
Chemical Abstract Chemical Formula Chemical Name Service (CAS) Number C3H8O 1‐propanol C4H7BrO2 2‐bromobutyric acid 80‐58‐0 GeH3COOH 2‐germaacetic acid C4H10 2‐methylpropane 75‐28‐5 C3H8O 2‐propanol 67‐63‐0 C6H10O3 4‐acetylbutyric acid 448671 C4H7BrO2 4‐bromobutyric acid 2623‐87‐2 CH3CHO acetaldehyde CH3CONH2 acetamide C8H9NO2 acetaminophen 103‐90‐2 − C2H3O2 acetate ion − CH3COO acetate ion C2H4O2 acetic acid 64‐19‐7 CH3COOH acetic acid (CH3)2CO acetone CH3COCl acetyl chloride C2H2 acetylene 74‐86‐2 HCCH acetylene C9H8O4 acetylsalicylic acid 50‐78‐2 H2C(CH)CN acrylonitrile C3H7NO2 Ala C3H7NO2 alanine 56‐41‐7 NaAlSi3O3 albite AlSb aluminium antimonide 25152‐52‐7 AlAs aluminium arsenide 22831‐42‐1 AlBO2 aluminium borate 61279‐70‐7 AlBO aluminium boron oxide 12041‐48‐4 AlBr3 aluminium bromide 7727‐15‐3 AlBr3•6H2O aluminium bromide hexahydrate 2149397 AlCl4Cs aluminium caesium tetrachloride 17992‐03‐9 AlCl3 aluminium chloride (anhydrous) 7446‐70‐0 AlCl3•6H2O aluminium chloride hexahydrate 7784‐13‐6 AlClO aluminium chloride oxide 13596‐11‐7 AlB2 aluminium diboride 12041‐50‐8 AlF2 aluminium difluoride 13569‐23‐8 AlF2O aluminium difluoride oxide 38344‐66‐0 AlB12 aluminium dodecaboride 12041‐54‐2 Al2F6 aluminium fluoride 17949‐86‐9 AlF3 aluminium fluoride 7784‐18‐1 Al(CHO2)3 aluminium formate 7360‐53‐4 1 of 75 Chemical Abstract Chemical Formula Chemical Name Service (CAS) Number Al(OH)3 aluminium hydroxide 21645‐51‐2 Al2I6 aluminium iodide 18898‐35‐6 AlI3 aluminium iodide 7784‐23‐8 AlBr aluminium monobromide 22359‐97‐3 AlCl aluminium monochloride