Tool Temperature in Titanium Drilling
Total Page:16
File Type:pdf, Size:1020Kb
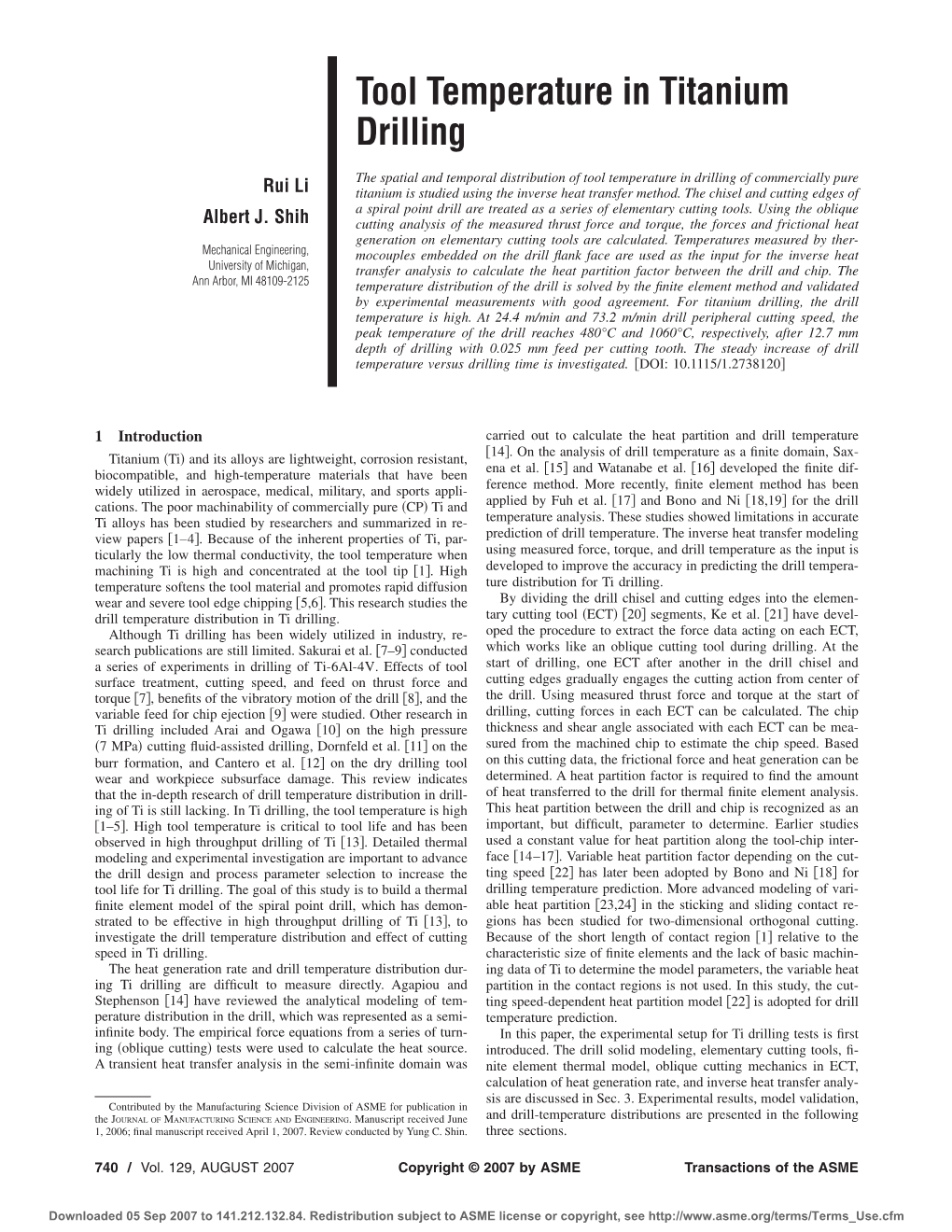
Load more
Recommended publications
-
Flexible Fluidic Actuators for Soft Robotic Applications
University of Wollongong Research Online University of Wollongong Thesis Collection 2017+ University of Wollongong Thesis Collections 2019 Flexible Fluidic Actuators for Soft Robotic Applications Weiping Hu Follow this and additional works at: https://ro.uow.edu.au/theses1 University of Wollongong Copyright Warning You may print or download ONE copy of this document for the purpose of your own research or study. The University does not authorise you to copy, communicate or otherwise make available electronically to any other person any copyright material contained on this site. You are reminded of the following: This work is copyright. Apart from any use permitted under the Copyright Act 1968, no part of this work may be reproduced by any process, nor may any other exclusive right be exercised, without the permission of the author. Copyright owners are entitled to take legal action against persons who infringe their copyright. A reproduction of material that is protected by copyright may be a copyright infringement. A court may impose penalties and award damages in relation to offences and infringements relating to copyright material. Higher penalties may apply, and higher damages may be awarded, for offences and infringements involving the conversion of material into digital or electronic form. Unless otherwise indicated, the views expressed in this thesis are those of the author and do not necessarily represent the views of the University of Wollongong. Research Online is the open access institutional repository for the University of -
The Close-Packed Triple Helix As a Possible New Structural Motif for Collagen
The close-packed triple helix as a possible new structural motif for collagen Jakob Bohr∗ and Kasper Olseny Department of Physics, Technical University of Denmark Building 307 Fysikvej, DK-2800 Lyngby, Denmark Abstract The one-dimensional problem of selecting the triple helix with the highest volume fraction is solved and hence the condition for a helix to be close-packed is obtained. The close-packed triple helix is ◦ shown to have a pitch angle of vCP = 43:3 . Contrary to the conventional notion, we suggest that close packing form the underlying principle behind the structure of collagen, and the implications of this suggestion are considered. Further, it is shown that the unique zero-twist structure with no strain- twist coupling is practically identical to the close-packed triple helix. Some of the difficulties for the current understanding of the structure of collagen are reviewed: The ambiguity in assigning crystal structures for collagen-like peptides, and the failure to satisfactorily calculate circular dichroism spectra. Further, the proposed new geometrical structure for collagen is better packed than both the 10=3 and the 7=2 structure. A feature of the suggested collagen structure is the existence of a central channel with negatively charged walls. We find support for this structural feature in some of the early x-ray diffraction data of collagen. The central channel of the structure suggests the possibility of a one-dimensional proton lattice. This geometry can explain the observed magic angle effect seen in NMR studies of collagen. The central channel also offers the possibility of ion transport and may cast new light on various biological and physical phenomena, including biomineralization. -
An Experimental Investigation of Helical Gear Efficiency
AN EXPERIMENTAL INVESTIGATION OF HELICAL GEAR EFFICIENCY A Thesis Presented in Partial Fulfillment of the Requirements for The Degree of Master of Science in the Graduate School of the Ohio State University By Aarthy Vaidyanathan, B. Tech. * * * * * The Ohio State University 2009 Masters Examination Committee: Dr. Ahmet Kahraman Approved by Dr. Donald R Houser Advisor Graduate Program in Mechanical Engineering ABSTRACT In this study, a test methodology for measuring load-dependent (mechanical) and load- independent power losses of helical gear pairs is developed. A high-speed four-square type test machine is adapted for this purpose. Several sets of helical gears having varying module, pressure angle and helix angle are procured, and their power losses under jet- lubricated conditions are measured at various speed and torque levels. The experimental results are compared to a helical gear mechanical power loss model from a companion study to assess the accuracy of the power loss predictions. The validated model is then used to perform parameter sensitivity studies to quantify the impact of various key gear design parameters on mechanical power losses and to demonstrate the trade off that must take place to arrive at a gear design that is balanced in all essential aspects including noise, durability (bending and contact) and power loss. ii Dedicated to all those before me who had far fewer opportunities, and yet accomplished so much more. iii ACKNOWLEDGMENTS I would like to thank my advisor, Dr. Ahmet Kahraman, who has been instrumental in fostering interest and enthusiasm in all my research endeavors. His encouragement throughout the course of my studies was invaluable, and I look to him for guidance in all my future undertakings. -
पेटेंट कार्ाालर् Official Journal of the Patent Office
पेटᴂट कार्ाालर् शासकीर् जर्ाल OFFICIAL JOURNAL OF THE PATENT OFFICE नर्र्ामर् सं. 20/2018 शुक्रवार दिर्ांक: 18/05/2018 ISSUE NO. 20/2018 FRIDAY DATE: 18/05/2018 पेटᴂट कार्ाालर् का एक प्रकाशर् PUBLICATION OF THE PATENT OFFICE The Patent Office Journal No. 20/2018 Dated 18/05/2018 18529 INTRODUCTION In view of the recent amendment made in the Patents Act, 1970 by the Patents (Amendment) Act, 2005 effective from 01st January 2005, the Official Journal of The Patent Office is required to be published under the Statute. This Journal is being published on weekly basis on every Friday covering the various proceedings on Patents as required according to the provision of Section 145 of the Patents Act 1970. All the enquiries on this Official Journal and other information as required by the public should be addressed to the Controller General of Patents, Designs & Trade Marks. Suggestions and comments are requested from all quarters so that the content can be enriched. ( Om Prakash Gupta ) CONTROLLER GENERAL OF PATENTS, DESIGNS & TRADE MARKS 18TH MAY, 2018 The Patent Office Journal No. 20/2018 Dated 18/05/2018 18530 CONTENTS SUBJECT PAGE NUMBER JURISDICTION : 18532 – 18533 SPECIAL NOTICE : 18534 – 18535 EARLY PUBLICATION (DELHI) : 18536 – 18540 EARLY PUBLICATION (MUMBAI) : 18541 – 18545 EARLY PUBLICATION (CHENNAI) : 18546 – 18564 EARLY PUBLICATION ( KOLKATA) : 18565 PUBLICATION AFTER 18 MONTHS (DELHI) : 18566 – 18732 PUBLICATION AFTER 18 MONTHS (MUMBAI) : 18733 – 18837 PUBLICATION AFTER 18 MONTHS (CHENNAI) : 18838 – 19020 PUBLICATION AFTER 18 MONTHS (KOLKATA) : 19021 – 19196 WEEKLY ISSUED FER (DELHI) : 19197 – 19235 WEEKLY ISSUED FER (MUMBAI) : 19236 – 19251 WEEKLY ISSUED FER (CHENNAI) : 19252 – 19295 WEEKLY ISSUED FER (KOLKATA) : 19296 – 19315 APPLICATION FOR RESTORATION OF PATENT : 19316 NO. -
Flexible Fluidic Actuators for Soft Robotic Applications
University of Wollongong Research Online University of Wollongong Thesis Collection 2017+ University of Wollongong Thesis Collections 2019 Flexible Fluidic Actuators for Soft Robotic Applications Weiping Hu University of Wollongong Follow this and additional works at: https://ro.uow.edu.au/theses1 University of Wollongong Copyright Warning You may print or download ONE copy of this document for the purpose of your own research or study. The University does not authorise you to copy, communicate or otherwise make available electronically to any other person any copyright material contained on this site. You are reminded of the following: This work is copyright. Apart from any use permitted under the Copyright Act 1968, no part of this work may be reproduced by any process, nor may any other exclusive right be exercised, without the permission of the author. Copyright owners are entitled to take legal action against persons who infringe their copyright. A reproduction of material that is protected by copyright may be a copyright infringement. A court may impose penalties and award damages in relation to offences and infringements relating to copyright material. Higher penalties may apply, and higher damages may be awarded, for offences and infringements involving the conversion of material into digital or electronic form. Unless otherwise indicated, the views expressed in this thesis are those of the author and do not necessarily represent the views of the University of Wollongong. Recommended Citation Hu, Weiping, Flexible Fluidic Actuators for Soft Robotic Applications, Doctor of Philosophy thesis, School of Mechanical, Materials, Mechatronic and Biomedical Engineering, University of Wollongong, 2019. https://ro.uow.edu.au/theses1/717 Research Online is the open access institutional repository for the University of Wollongong. -
Symbols for Rules & Formulas
Call us at (800) 491-1073 and ask for Design Support * commercialgear.com SYMBOLS FOR RULES & FORMULAS a Addendum tr Tooth Thickness Tolerance ac Chordal Addendum tt Transverse Circular Thickness anc Normal Chordal Addendum tx Axial Thickness B Backlash Vap Total Accumulated Pitch Variation b Dedendum Vapk Total Accumulated Pitch C Center Distance Variation within a sector of k Pitches c Clearance Vcq Total Composite Variation D Reference Standard Pitch (double flank) Diameter VcqT Total Composite Tolerance Db Base Diameter (double flank) Dc Datum Circle Vp Pitch Variation Di Internal Diameter VpA Allowable Pitch Variation DR Root Diameter Vpn Normal Pitch Variation Dt Throat Diameter Vq Tooth-to-Tooth Composite Variation (double flank) Do Out side diameter VqT Tooth-to-Tooth Composite dp Operating Pitch Diameter Tolerance (double flank) F Face Width Vr Radial Runout Fe Effective or Active Face VrT Radial Runout Tolerance Width Ft Total Face Width Vs Spacing Variation hk Working Depth Vx Index Variation ht Whole Depth(tooth depth) VΦ Profile Variation L Lead VΦT Profile Tolerance m Module Vψ Tooth Alignment Variation mc Contact Ratio VψT Tooth Alignment Tolerance mF Face Contact Ratio Z Length of Action mG Gear Ratio α Addendum Angle mn Normal Module Γ Pitch Angle mo Modified Contact Ratio ΓR Root Angle mp Transverse Contact Ratio Σ Shaft Angle mt Total Contact Ratio ε Involute Roll Angle N Number of teeth or threads θ Involute Polar Angle Ne Equivalent Number of teeth θN Angular Pitch Pd Diametral Pitch (transverse) λ Lead Angle Pnd -
Agma Information Sheet
AGMA 908---B89 (Revision of AGMA 226.01) April 1989 (Reaffirmed August 1999) AMERICAN GEAR MANUFACTURERS ASSOCIATION Geometry Factors for Determining the Pitting Resistance and Bending Strength of Spur, Helical and Herringbone Gear Teeth AGMA INFORMATION SHEET (This Information Sheet is not an AGMA Standard) INFORMATION SHEET Geometry Factors for Determining the Pitting Resistance and Bending Strength of Spur, Helical and Herringbone Gear Teeth AGMA 908---B89 (Revision of AGMA 226.01 1984) [Tables or other self---supporting sections may be quoted or extracted in their entirety. Credit line should read: Extracted from AGMA Standard 908---B89, INFORMATION SHEET, Geometry Factors for Determining the Pitting Resistance and Bending Strength of Spur, Helical and Herringbone Gear Teeth, with the permission of the publisher, American Gear Manufacturers Association, 1500 King Street, Suite 201, Alexandria, Virginia 22314.] AGMA standards are subject to constant improvement, revision or withdrawal as dictated by experience. Any person who refers to any AGMA Technical Publication should determine that it is the latest information available from the Association on the subject. Suggestions for the improvement of this Standard will be welcome. They should be sent to the American Gear Manufacturers Association, 1500 King Street, Suite 201, Alexandria, Virginia 22314. ABSTRACT: This Information Sheet gives the equations for calculating the pitting resistance geometry factor, I,for external and internal spur and helical gears, and the bending strength geometry factor, J, for external spur and helical gears that are generated by rack---type tools (hobs, rack cutters or generating grinding wheels) or pinion---type tools (shaper cutters). The Information Sheet also includes charts which provide geometry factors, I and J, for a range of typical gear sets and tooth forms. -
TERMS of USE This Is a Copyrighted Work and the Mcgraw-Hill Companies, Inc
ebook_copyright 8 x 10.qxd 7/7/03 5:10 PM Page 1 Copyright © 2003 by The McGraw-Hill Companies, Inc. All rights reserved. Manufactured in the United States of America. Except as permitted under the United States Copyright Act of 1976, no part of this publication may be reproduced or distributed in any form or by any means, or stored in a data- base or retrieval system, without the prior written permission of the publisher. 0-07-142093-2 The material in this eBook also appears in the print version of this title: 0-07-141049-X All trademarks are trademarks of their respective owners. Rather than put a trademark symbol after every occurrence of a trademarked name, we use names in an editorial fashion only, and to the benefit of the trademark owner, with no intention of infringement of the trademark. Where such designations appear in this book, they have been printed with initial caps. McGraw-Hill eBooks are available at special quantity discounts to use as premiums and sales pro- motions, or for use in corporate training programs. For more information, please contact George Hoare, Special Sales, at [email protected] or (212) 904-4069. TERMS OF USE This is a copyrighted work and The McGraw-Hill Companies, Inc. (“McGraw-Hill”) and its licensors reserve all rights in and to the work. Use of this work is subject to these terms. Except as permitted under the Copyright Act of 1976 and the right to store and retrieve one copy of the work, you may not decompile, disassemble, reverse engineer, reproduce, modify, create derivative works based upon, transmit, distribute, disseminate, sell, publish or sublicense the work or any part of it without McGraw-Hill’s prior consent. -
Computer Aided Optimal Design of Helical Gears
Portland State University PDXScholar Dissertations and Theses Dissertations and Theses 1980 Computer aided optimal design of helical gears S. N. Muthukrishnan Portland State University Follow this and additional works at: https://pdxscholar.library.pdx.edu/open_access_etds Part of the Mechanical Engineering Commons Let us know how access to this document benefits ou.y Recommended Citation Muthukrishnan, S. N., "Computer aided optimal design of helical gears" (1980). Dissertations and Theses. Paper 4192. https://doi.org/10.15760/etd.6075 This Thesis is brought to you for free and open access. It has been accepted for inclusion in Dissertations and Theses by an authorized administrator of PDXScholar. Please contact us if we can make this document more accessible: [email protected]. AN ABSTRACT OF THE THESIS OF S. N. Muthukrishnan for the Master of Science in Mechanical Engineering presented December 21, 1990. Title: Computer Aided Optimal Design of Helical Gears. APPROVED BY THE MEMBERS OF THE THESIS COMMITTEE: \...:.ll<;i.l. / A random search method for optimum design of a pair of helical gears has been developed. The sequence of optimization consists of two principal components. The first is the selection phase, where the output is the starting solution for the design variables - module, facewidth, helix angle and number of teeth on the pinion. The input for the selection phase includes the application environment, approximate center distance, minimum helix angle, desired values of gear ratio, pinion speed and the power to be transmitted. The limits on each of the design variables and the constraints are imposed interactively during the first phase. A standard tooth form is 2 assumed for the design. -
Dictionary of Mathematics
Dictionary of Mathematics English – Spanish | Spanish – English Diccionario de Matemáticas Inglés – Castellano | Castellano – Inglés Kenneth Allen Hornak Lexicographer © 2008 Editorial Castilla La Vieja Copyright 2012 by Kenneth Allen Hornak Editorial Castilla La Vieja, c/o P.O. Box 1356, Lansdowne, Penna. 19050 United States of America PH: (908) 399-6273 e-mail: [email protected] All dictionaries may be seen at: http://www.EditorialCastilla.com Sello: Fachada de la Universidad de Salamanca (ESPAÑA) ISBN: 978-0-9860058-0-0 All rights reserved. No part of this book may be reproduced or transmitted in any form or by any means, electronic or mechanical, including photocopying, recording or by any informational storage or retrieval system without permission in writing from the author Kenneth Allen Hornak. Reservados todos los derechos. Quedan rigurosamente prohibidos la reproducción de este libro, el tratamiento informático, la transmisión de alguna forma o por cualquier medio, ya sea electrónico, mecánico, por fotocopia, por registro u otros medios, sin el permiso previo y por escrito del autor Kenneth Allen Hornak. ACKNOWLEDGEMENTS Among those who have favoured the author with their selfless assistance throughout the extended period of compilation of this dictionary are Andrew Hornak, Norma Hornak, Edward Hornak, Daniel Pritchard and T.S. Gallione. Without their assistance the completion of this work would have been greatly delayed. AGRADECIMIENTOS Entre los que han favorecido al autor con su desinteresada colaboración a lo largo del dilatado período de acopio del material para el presente diccionario figuran Andrew Hornak, Norma Hornak, Edward Hornak, Daniel Pritchard y T.S. Gallione. Sin su ayuda la terminación de esta obra se hubiera demorado grandemente. -
The Importance of Properly Manufactured Helix Plates The
The Importance of Properly Manufactured Helix Plates for Helical Pile Performance Continued from front . • Helix plates and shafts are smooth and absent of irregularities ™ that extend more than 1/16 inch from the surface excluding shapes including blunt (flat), sharpened, sea-shell cut, V-style cut, connecting hardware and fittings. etc. to provide options for changing soil conditions. The trailing edge is generally either blunt or sharpened and has no effect on • Helix spacing along the shaft shall be between 2.4 to 3.6 times installation in varying soils. the helix diameter. • The helix pitch is 3 inches ± 1/4 inches. A helix plate is formed by cold pressing the steel plate with • All helix plates shall have the same pitch. matching machined dies. Both the shape of the die press and the amount of applied force during the press operations is important • Helical plates are arranged such that they theoretically track to ensure parallel leading and trailing edges and the required the same path as the leading helix. FSI NEWSLETTER FOR DESIGN PROFESSIONALS pitch tolerances. The amount of die press force must also be • For shafts with multiple helices, the smallest diameter helix adjusted for changing plate thickness or steel grades. shall be mounted to the leading end of the shaft with progressively larger diameter helices above. The Importance of Properly Manufactured Helix Plates The International Code Council (ICC) has approved the • Helical foundation shaft advancement shall equal or exceed Acceptance Criteria for Helical Piles and Systems (AC358) which Don Deardorff, P.E. • Senior Application Engineer for Helical Pile Performance establishes design and manufacturing criteria for helical piles 85% of the helix pitch per revolution at time of final torque measurement. -
Glancing Angle Deposition of Thin Films Engineering the Nanoscale
Wiley Series in Materials for Electronic & Optoelectronic Applications Matthew M. Hawkeye Michael T. Taschuk Michael J. Brett Glancing Angle Deposition of Thin Films Engineering the Nanoscale Glancing Angle Deposition of Thin Films Wiley Series in Materials for Electronic and Optoelectronic Applications www.wiley.com/go/meoa Series Editors Professor Arthur Willoughby, University of Southampton, Southampton, UK Dr Peter Capper, SELEX Galileo Infrared Ltd, Southampton, UK Professor Safa Kasap, University of Saskatchewan, Saskatoon, Canada Published Titles Bulk Crystal Growth of Electronic, Optical and Optoelectronic Materials, Edited by P. Capper Properties of Group-IV, III–V and II–VI Semiconductors, S. Adachi Charge Transport in Disordered Solids with Applications in Electronics, Edited by S. Baranovski Optical Properties of Condensed Matter and Applications, Edited by J. Singh Thin Film Solar Cells: Fabrication, Characterization and Applications, Edited by J. Poortmans and V. Arkhipov Dielectric Films for Advanced Microelectronics, Edited by M. R. Baklanov, M. Green and K. Maex Liquid Phase Epitaxy of Electronic, Optical and Optoelectronic Materials, Edited by P. Capper and M. Mauk Molecular Electronics: From Principles to Practice, M. Petty CVD Diamond for Electronic Devices and Sensors, Edited by R. S. Sussmann Properties of Semiconductor Alloys: Group-IV, III–V and II–VI Semiconductors, S. Adachi Mercury Cadmium Telluride, Edited by P. Capper and J. Garland Zinc Oxide Materials for Electronic and Optoelectronic Device Applications, Edited by C. Litton, D. C. Reynolds and T. C. Collins Lead-Free Solders: Materials Reliability for Electronics, Edited by K. N. Subramanian Silicon Photonics: Fundamentals and Devices, M. Jamal Deen and P. K. Basu Nanostructured and Subwavelength Waveguides: Fundamentals and Applications, M.