Chapter 10 'SYNTHETIC' FUELS, OIL SHALE and TAR SANDS
Total Page:16
File Type:pdf, Size:1020Kb
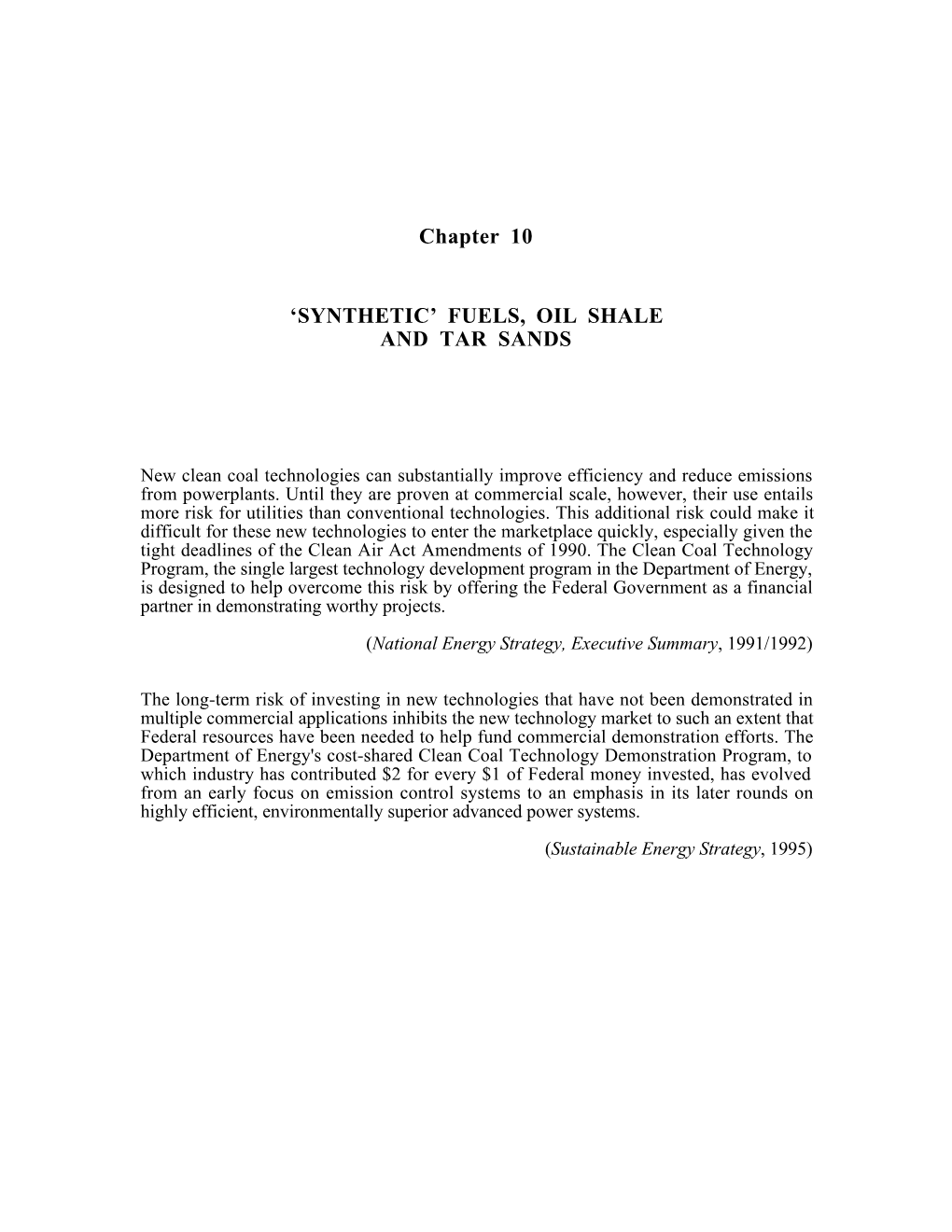
Load more
Recommended publications
-
Coal and Oil: the Dark Monarchs of Global Energy – Understanding Supply and Extraction Patterns and Their Importance for Futur
nam et ipsa scientia potestas est List of Papers This thesis is based on the following papers, which are referred to in the text by their Roman numerals. I Höök, M., Aleklett, K. (2008) A decline rate study of Norwe- gian oil production. Energy Policy, 36(11):4262–4271 II Höök, M., Söderbergh, B., Jakobsson, K., Aleklett, K. (2009) The evolution of giant oil field production behaviour. Natural Resources Research, 18(1):39–56 III Höök, M., Hirsch, R., Aleklett, K. (2009) Giant oil field decline rates and their influence on world oil production. Energy Pol- icy, 37(6):2262–2272 IV Jakobsson, K., Söderbergh, B., Höök, M., Aleklett, K. (2009) How reasonable are oil production scenarios from public agen- cies? Energy Policy, 37(11):4809–4818 V Höök M, Söderbergh, B., Aleklett, K. (2009) Future Danish oil and gas export. Energy, 34(11):1826–1834 VI Aleklett K., Höök, M., Jakobsson, K., Lardelli, M., Snowden, S., Söderbergh, B. (2010) The Peak of the Oil Age - analyzing the world oil production Reference Scenario in World Energy Outlook 2008. Energy Policy, 38(3):1398–1414 VII Höök M, Tang, X., Pang, X., Aleklett K. (2010) Development journey and outlook for the Chinese giant oilfields. Petroleum Development and Exploration, 37(2):237–249 VIII Höök, M., Aleklett, K. (2009) Historical trends in American coal production and a possible future outlook. International Journal of Coal Geology, 78(3):201–216 IX Höök, M., Aleklett, K. (2010) Trends in U.S. recoverable coal supply estimates and future production outlooks. Natural Re- sources Research, 19(3):189–208 X Höök, M., Zittel, W., Schindler, J., Aleklett, K. -
Oil Shale in Jordan 1 2.1
MINISTRY OF ENERGY AND MINERAL RESOURCES Mineral Status and Future Opportunity OIL SHALE Prepared By Dr Jamal Alali Geo. Abdelfattah Abu Salah Dr. Suha M. Yasin Geo. Wasfi Al Omari Edited By Geo. Julia Sahawneh Geo. Marwan Madanat 2014 Oil Shale Ministry of Energy and Mineral Resources, 2014 CONTENTS List of Contents I List of Figures II List of Tables II 1. Introduction 1 2. Geology of Oil Shale in Jordan 1 2.1. Origin and Definition 1 2.2. Mineralogy and Chemistry of Oil Shale 2 2.3. Uses and Industrial Applications of Oil Shale 3 3. Oil Shale Deposits 3 3.1. El-Lajjun Deposit 4 3.2. Sultani Oil Shale Deposit 6 3.3. Attarat Umm Ghudran Oil Shale Deposit 8 3.4. Wadi Maghar Oil Shale Deposit 9 3.5. Khan Az Zabib Deposit 10 3.6. Jurf Ed Darawish Deposit 11 3.7. Siwaqa Deposit 11 3.8. El Hasa Deposit 12 3.9. Eth Thamad/ Madaba Area 4. Summary of Previous Technical Activities 12 5. Mining Aspects 14 5.1. Overburden 14 5.2. Ore Body of the Oil Shale 14 5.3. Reserves 14 5.4. Mining Method 15 6. Oil shale Technologies and Exploitation Worldwide 17 6.1. Crude Oil Production 17 6.2. Power Generation 18 7. Investment Opportunities and Outlook 19 7.1. Crude Oil Production 20 7.2. Direct Combustion 20 8. References 23 I Oil Shale Ministry of Energy and Mineral Resources, 2014 List of Figures Figure (1): Location map of the major oil shale deposits. 5 Figure (2): Oil Shale outcrop in El-Lajjun deposit. -
U.S. Energy in the 21St Century: a Primer
U.S. Energy in the 21st Century: A Primer March 16, 2021 Congressional Research Service https://crsreports.congress.gov R46723 SUMMARY R46723 U.S. Energy in the 21st Century: A Primer March 16, 2021 Since the start of the 21st century, the U.S. energy system has changed tremendously. Technological advances in energy production have driven changes in energy consumption, and Melissa N. Diaz, the United States has moved from being a net importer of most forms of energy to a declining Coordinator importer—and a net exporter in 2019. The United States remains the second largest producer and Analyst in Energy Policy consumer of energy in the world, behind China. Overall energy consumption in the United States has held relatively steady since 2000, while the mix of energy sources has changed. Between 2000 and 2019, consumption of natural gas and renewable energy increased, while oil and nuclear power were relatively flat and coal decreased. In the same period, production of oil, natural gas, and renewables increased, while nuclear power was relatively flat and coal decreased. Overall energy production increased by 42% over the same period. Increases in the production of oil and natural gas are due in part to technological improvements in hydraulic fracturing and horizontal drilling that have facilitated access to resources in unconventional formations (e.g., shale). U.S. oil production (including natural gas liquids and crude oil) and natural gas production hit record highs in 2019. The United States is the largest producer of natural gas, a net exporter, and the largest consumer. Oil, natural gas, and other liquid fuels depend on a network of over three million miles of pipeline infrastructure. -
Oil Shale and Tar Sands
Fundamentals of Materials for Energy and Environmental Sustainability Editors David S. Ginley and David Cahen Oil shale and tar sands James W. Bunger 11 JWBA, Inc., Energy Technology and Engineering, Salt Lake City, UT, USA 11.1 Focus 11.2 Synopsis Tar sands and oil shale are “uncon- Oil shale and tar sands occur in dozens of countries around the world. With in-place ventional” oil resources. Unconven- resources totaling at least 4 trillion barrels (bbl), they exceed the world's remaining tional oil resources are characterized petroleum reserves, which are probably less than 2 trillion bbl. As petroleum becomes by their solid, or near-solid, state harder to produce, oil shale and tar sands are finding economic and thermodynamic under reservoir conditions, which parity with petroleum. Thermodynamic parity, e.g., similarity in the energy cost requires new, and sometimes of producing energy, is a key indicator of economic competitiveness. unproven, technology for their Oil is being produced on a large commercial scale by Canada from tar sands, recovery. For tar sands the hydrocar- and to a lesser extent by Venezuela. The USA now imports well over 2 million barrels bon is a highly viscous bitumen; for of oil per day from Canada, the majority of which is produced from tar sands. oil shale, it is a solid hydrocarbon Production of oil from oil shale is occurring in Estonia, China, and Brazil albeit on called “kerogen.” Unconventional smaller scales. Importantly, the USA is the largest holder of oil-shale resources. oil resources are found in greater For that reason alone, and because of the growing need for imports in the USA, quantities than conventional petrol- oil shale will receive greater development attention as petroleum supplies dwindle. -
Pine Tar & Wood Protection Asphalt & Roof Care
PINE TAR & WOOD PROTECTION ASPHALT & ROOF CARE PINE TAR NAture’s own wood PROTECTION Pine tar has been used in Scandinavia for hundreds of years to protect and preserve wooden buildings, boats, jetties and eve- ryday items. As well as protecting wooden structures against rot, natural tar is also mildly antiseptic. This characteristic means that pine tar is used in a number of different pharma- ceutical and veterinary products for treating skin complaints. It is therefore a common ingredient in skin ointments, soap and shampoo, etc. For a long time pine tar was one of Sweden’s most important export items. A protective oil – direct from the forest Pine tar is a viscous blackish-brown liquid consisting of vola- tile terpene oils, neutral oils, resin acids and fatty acids. It’s the combination of these substances that allows mediaeval wood- en buildings that have been regularly treated with pine tar to still stand today. The proportion of these constituents varies in different tar qualities, depending on the type of wood, its age and the part of the tree used. Historically, resin-rich pine stumps have always been considered to give the best pine tar, as resin contains substances that protect the living tree from rot, insect infestation and so on. Since it has become harder to get hold of stumps, tree trunks and branches are now used to a greater extent. Aromatic and easily soluble Pine tar is transparent in thin layers and has a natural aromatic scent. It’s pretty much fully soluble in alcohol and turpentine, as well as almost completely compatible with fatty oils. -
Husky Energy and BP Announce Integrated Oil Sands Joint Development
December 5, 2007 For immediate release Husky Energy and BP Announce Integrated Oil Sands Joint Development CALGARY, Alberta – Husky Energy Inc is pleased to announce that an agreement has been reached with BP to create an integrated, North American oil sands business consisting of pre-eminent upstream and downstream assets. The development will be comprised of two joint 50/50 partnerships, a Canadian oil sands partnership to be operated by Husky and a U.S. refining LLC to be operated by BP. Husky and BP will each contribute assets of equal value to the business. Husky will contribute its Sunrise asset located in the Athabasca oil sands in northeast Alberta, Canada and BP will contribute its Toledo refinery located in Ohio, USA. The transaction, which is subject to the execution of final definitive agreements and regulatory approval, is expected to close in the first quarter of 2008 and with effective date January 1, 2008. "This transaction completes Husky’s Sunrise Oil Sands total integration with respect to upstream and downstream solutions," said Mr. John C.S. Lau, President & Chief Executive Officer of Husky Energy Inc. “Husky is extremely pleased to be partnering with BP, a world class global E & P and Refining company. The joint venture will provide better monitoring of project execution, costs and completion timing for this mega project development.” “Toledo and Sunrise are excellent assets. BP’s move into oil sands with Husky is an opportunity to build a strategic, material position and the huge potential of Sunrise is the ideal entry point for BP into Canadian oil sands.” said Tony Hayward, BP’s group chief executive. -
New Carbon Emissions Allowance Allocation Method Based on Equilibrium Strategy for Carbon Emission Mitigation in the Coal-Fired Power Industry
sustainability Article New Carbon Emissions Allowance Allocation Method Based on Equilibrium Strategy for Carbon Emission Mitigation in the Coal-Fired Power Industry Qing Feng 1, Qian Huang 1, Qingyan Zheng 2 and Li Lu 1,2,* 1 Business School, Sichuan University, Chengdu 610064, China; [email protected] (Q.F.); [email protected] (Q.H.) 2 Tourism School, Sichuan University, Chengdu 610064, China; [email protected] * Correspondence: [email protected]; Tel.: +86-028-85996613 Received: 18 July 2018; Accepted: 17 August 2018; Published: 17 August 2018 Abstract: The carbon emissions from coal-fired power have become an increasing concern to governments around the world. In this paper, a carbon emissions allowances allocation based on the equilibrium strategy is proposed to mitigate coal-fired power generation carbon emissions, in which the authority is the lead decision maker and the coal-fired power plants are the follower decision makers, and an interactive solution approach is designed to achieve equilibrium. A real-world case study is then given to demonstrate the practicality and efficiency of this methodology. Sensitivity analyses under different constraint violation risk levels are also conducted to give authorities some insights into equilibrium strategies for different stakeholders and to identify the necessary tradeoffs between economic development and carbon emissions mitigation. It was found that the proposed method was able to mitigate coal-fired power generation carbon emissions significantly and encourage coal-fired power plants to improve their emissions performance. Keywords: carbon emission allowance allocation; emission mitigation; coal-fired power generation; cap and tax mechanism 1. Introduction Because of their major contribution to global climate change, there has been increased research to determine the best ways to reduce carbon emissions, which have been exponentially increasing due to the increased demand for energy [1–3]. -
Statoil ASA Statoil Petroleum AS
Offering Circular A9.4.1.1 Statoil ASA (incorporated with limited liability in the Kingdom of Norway) Notes issued under the programme may be unconditionally and irrevocably guaranteed by Statoil Petroleum AS (incorporated with limited liability in the Kingdom of Norway) €20,000,000,000 Euro Medium Term Note Programme On 21 March 1997, Statoil ASA (the Issuer) entered into a Euro Medium Term Note Programme (the Programme) and issued an Offering Circular on that date describing the Programme. The Programme has been subsequently amended and updated. This Offering Circular supersedes any previous dated offering circulars. Any Notes (as defined below) issued under the Programme on or after the date of this Offering Circular are issued subject to the provisions described herein. This does not affect any Notes issued prior to the date hereof. Under this Programme, Statoil ASA may from time to time issue notes (the Notes) denominated in any currency agreed between the Issuer and the relevant Dealer (as defined below). The Notes may be issued in bearer form or in uncertificated book entry form (VPS Notes) settled through the Norwegian Central Securities Depositary, Verdipapirsentralen ASA (the VPS). The maximum aggregate nominal amount of all Notes from time to time outstanding will not exceed €20,000,000,000 (or its equivalent in other currencies calculated as described herein). The payments of all amounts due in respect of the Notes issued by the Issuer may be unconditionally and irrevocably guaranteed by Statoil A6.1 Petroleum AS (the Guarantor). The Notes may be issued on a continuing basis to one or more of the Dealers specified on page 6 and any additional Dealer appointed under the Programme from time to time, which appointment may be for a specific issue or on an ongoing basis (each a Dealer and together the Dealers). -
Press Release
Press Release First quarter 2021 results With results of more than $3 billion, Total fully benefits from rebound in hydrocarbon prices LNG and renewables represent one-third of results Change Change 1Q21 1Q20 1Q19 vs 1Q20 vs 1Q19 Oil price - Brent ($/b) 61.1 50.1 +22% 63.1 -3% Average price of LNG ($/Mbtu) 6.1 6.3 -4% 7.2 -16% Variable cost margin - Refining Europe, VCM ($/t) 5.3 26.3 -80% 33.0 -84% Adjusted net income (Group share)1 - in billions of dollars (B$) 3.0 1.8 69% 2.8 +9% - in dollars per share 1.10 0.66 +68% 1.02 +8% DACF1 (B$) 5.8 4.3 +34% 6.3 -8% Cash Flow from operations (B$) 5.6 1.3 x4.3 3.6 +54% Net income (Group share) of 3.3 B$ in 1Q21 Net-debt-to-capital ratio of 19.5% at March 31, 2021 vs. 21.7% at December 31, 20202 Hydrocarbon production of 2,863 kboe/d in 1Q21, a decrease of 7% compared to 1Q20 First 2021 interim dividend set at 0.66 €/share 2 Paris, April 29, 2021 - The Board of Directors of Total SE, meeting on April 28, 2021, under the chairmanship of Chairman and Chief Executive Officer Patrick Pouyanné, approved the Group's first quarter 2021 accounts. On this occasion, Patrick Pouyanné said: « In the first quarter, the Group fully benefited from rising oil and gas prices, up 38% and 24%, respectively quarter-to- quarter, and its strategy to grow LNG and Renewables and Electricity. -
Organic-Rich Shale of the United States and World Land Areas Organic-Rich Shale of the United States and World Land Areas
GEOLOGICAL SURVEY CIRCULAR 523 Organic-Rich Shale of the United States and World Land Areas Organic-Rich Shale of the United States and World Land Areas By Donald C. Duncan and Vernon E. Swanson Geological Survey Circular 523 Washington 7965 United States Department of the Interior STEWART L. UDALL, Secretary Geological Survey William T. Pecora, Director REPRINTED 1966 Free on application to the U.S. Geological Survey, Washington, D.C. 20242 CONTENTS Page Page Abstract----- _ ____________ _ ____ 1 Shale oil resources Continued Introduction- ______________ _ _____ 1 North America Continued Acknowledgments __ ____________ _ 2 United States Continued Previous summaries______________ 2 Shale associated with coal ______ 14 Definitions _______________________ 2 Other shale deposits _ ______ 15 Organic -rich shale _____________ 2 Total shale oil resources.---- 16 Oil shale __ ____ __ ___ __ 3 Other areas in North America ____ 16 Other terms ___________________ 3 Africa-___--__-_-_----_--_----_--- 17 Types of deposits_________________ 4 Total shale oil resources of Potential energy, oil, or gas yield of Africa _______________________ 17 the organic matter in shale ______ 4 Asia _________ _ _____ ___ 19 Status of the shale industry ________ 5 China __________________ _ 19 World production _______________ 5 Israel, Jordan, and Syria _________ 19 Byproducts ____________________ 5 Siberia _________________________ 20 Activities in the United States ____ 5 Thailand and Burma-_____________ 20 Classification of resources ________ 5 Turkey ________ _____ -
The Destructive Distillation of Pine Sawdust
Scholars' Mine Bachelors Theses Student Theses and Dissertations 1903 The destructive distillation of pine sawdust Frederick Hauenstein Herbert Arno Roesler Follow this and additional works at: https://scholarsmine.mst.edu/bachelors_theses Part of the Mining Engineering Commons Department: Mining Engineering Recommended Citation Hauenstein, Frederick and Roesler, Herbert Arno, "The destructive distillation of pine sawdust" (1903). Bachelors Theses. 238. https://scholarsmine.mst.edu/bachelors_theses/238 This Thesis - Open Access is brought to you for free and open access by Scholars' Mine. It has been accepted for inclusion in Bachelors Theses by an authorized administrator of Scholars' Mine. This work is protected by U. S. Copyright Law. Unauthorized use including reproduction for redistribution requires the permission of the copyright holder. For more information, please contact [email protected]. FOR THE - ttl ~d IN SUBJECT, ••The Destructive Distillation of P ine Sawdust:• F . HAUENSTEIN AND H . A. ROESLER. CLASS OF 1903. DISTILLATION In pine of the South, the operation of m.ills to immense quanti waste , such and sawdust.. The sawdust especially, is no practical in vast am,ounte; very difficult to the camp .. s :ls to util the be of commercial .. folloWing extraction turpentine .. of the acid th soda and treat- products .. t .. the t.he turpentine to in cells between , or by tissues to alcohol, a soap which a commercial t this would us too the rd:- hydrochloric was through supposition being that it d form & pinene hydro- which produced~ But instead the hydrochl , a dark unl<:nown compound was The fourth experiment, however, brought out a number of possibilities, a few of Which have been worked up. -
Coal Characteristics
CCTR Indiana Center for Coal Technology Research COAL CHARACTERISTICS CCTR Basic Facts File # 8 Brian H. Bowen, Marty W. Irwin The Energy Center at Discovery Park Purdue University CCTR, Potter Center, 500 Central Drive West Lafayette, IN 47907-2022 http://www.purdue.edu/dp/energy/CCTR/ Email: [email protected] October 2008 1 Indiana Center for Coal Technology Research CCTR COAL FORMATION As geological processes apply pressure to peat over time, it is transformed successively into different types of coal Source: Kentucky Geological Survey http://images.google.com/imgres?imgurl=http://www.uky.edu/KGS/coal/images/peatcoal.gif&imgrefurl=http://www.uky.edu/KGS/coal/coalform.htm&h=354&w=579&sz= 20&hl=en&start=5&um=1&tbnid=NavOy9_5HD07pM:&tbnh=82&tbnw=134&prev=/images%3Fq%3Dcoal%2Bphotos%26svnum%3D10%26um%3D1%26hl%3Den%26sa%3DX 2 Indiana Center for Coal Technology Research CCTR COAL ANALYSIS Elemental analysis of coal gives empirical formulas such as: C137H97O9NS for Bituminous Coal C240H90O4NS for high-grade Anthracite Coal is divided into 4 ranks: (1) Anthracite (2) Bituminous (3) Sub-bituminous (4) Lignite Source: http://cc.msnscache.com/cache.aspx?q=4929705428518&lang=en-US&mkt=en-US&FORM=CVRE8 3 Indiana Center for Coal Technology Research CCTR BITUMINOUS COAL Bituminous Coal: Great pressure results in the creation of bituminous, or “soft” coal. This is the type most commonly used for electric power generation in the U.S. It has a higher heating value than either lignite or sub-bituminous, but less than that of anthracite. Bituminous coal