Richard Nakka's Experimental Rocketry Web Site
Total Page:16
File Type:pdf, Size:1020Kb
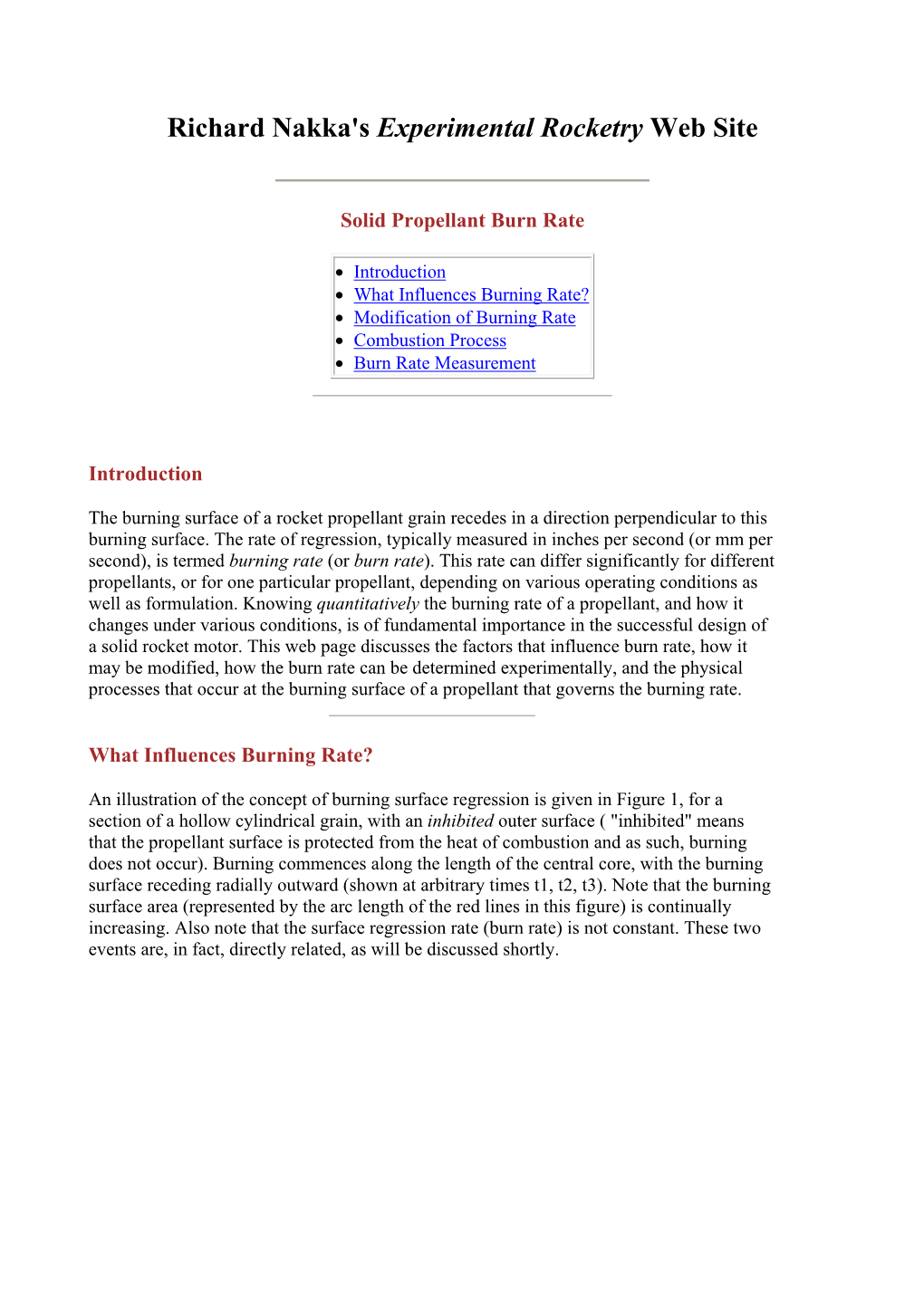
Load more
Recommended publications
-
The SKYLON Spaceplane
The SKYLON Spaceplane Borg K.⇤ and Matula E.⇤ University of Colorado, Boulder, CO, 80309, USA This report outlines the major technical aspects of the SKYLON spaceplane as a final project for the ASEN 5053 class. The SKYLON spaceplane is designed as a single stage to orbit vehicle capable of lifting 15 mT to LEO from a 5.5 km runway and returning to land at the same location. It is powered by a unique engine design that combines an air- breathing and rocket mode into a single engine. This is achieved through the use of a novel lightweight heat exchanger that has been demonstrated on a reduced scale. The program has received funding from the UK government and ESA to build a full scale prototype of the engine as it’s next step. The project is technically feasible but will need to overcome some manufacturing issues and high start-up costs. This report is not intended for publication or commercial use. Nomenclature SSTO Single Stage To Orbit REL Reaction Engines Ltd UK United Kingdom LEO Low Earth Orbit SABRE Synergetic Air-Breathing Rocket Engine SOMA SKYLON Orbital Maneuvering Assembly HOTOL Horizontal Take-O↵and Landing NASP National Aerospace Program GT OW Gross Take-O↵Weight MECO Main Engine Cut-O↵ LACE Liquid Air Cooled Engine RCS Reaction Control System MLI Multi-Layer Insulation mT Tonne I. Introduction The SKYLON spaceplane is a single stage to orbit concept vehicle being developed by Reaction Engines Ltd in the United Kingdom. It is designed to take o↵and land on a runway delivering 15 mT of payload into LEO, in the current D-1 configuration. -
19940015753.Pdf
National Aeronautics and Educational Product Space Administration Teachers I Grades 2-6 I Office of Education and Human Resources Education Division _o N N cO 0 u_ 0 N t_ I ,.-, CO ,4" U O" 0_ _ Z _ 0 0 tM < u Is LIJ I-. _-.q4" W_ O ul ,,_ W;Z. INWel I I,,-. UJ .... 0,. i,-,{ .... u4 uJ I-,- .. IU_ Z_ .1 i ! I i I j | ] ROCKETS Physical Science Teacher's Guide with Activities National Aeronautics and Space Administration Office of Human Resources and Education Education Division This publication is in the Public Domain and is not protected by copyright. Permission is not required for duplication. EP-291 July 1993 Acknowledgments This publication was developed for the National Aeronautics and Space Administra- tion with the assistance of the many educa- tors of the Aerospace Education Services Program, Oklahoma State University. Writer: Gregory L. Vogt, Ed.D. Teaching From Space Program NASA Johnson Space Center Houston, TX Editor: Carla R. Rosenberg Teaching From Space Program NASA Headquarters Washington, DC Table of Contents How To Use This Guide ............................... 1 Activities and Demonstration Matrix ............. 2 Brief History of Rockets ................................ 3 Rocket Principles ......................................... 8 Practical Rocketry ...................................... 12 Activities and Demonstrations .................... 19 Glossary ..................................................... 40 NASA Educational Materials And Suggested Readings .......................... 41 NASA Educational Resources ................... 42 Evaluation Card ..................................... Insert ii How To Use This Guide vehiclesockets arein theexistence.oldest formEarlyofrocketsself-containedwere in use more than two thousand years ago. Over a long and exciting history, rockets have evolved from simple tubes filled with black powder into mighty vehicles capable of launching a spacecraft out into the galaxy. -
National Reconnaissance Office Review and Redaction Guide
NRO Approved for Release 16 Dec 2010 —Tep-nm.T7ymqtmthitmemf- (u) National Reconnaissance Office Review and Redaction Guide For Automatic Declassification Of 25-Year-Old Information Version 1.0 2008 Edition Approved: Scott F. Large Director DECL ON: 25x1, 20590201 DRV FROM: NRO Classification Guide 6.0, 20 May 2005 NRO Approved for Release 16 Dec 2010 (U) Table of Contents (U) Preface (U) Background 1 (U) General Methodology 2 (U) File Series Exemptions 4 (U) Continued Exemption from Declassification 4 1. (U) Reveal Information that Involves the Application of Intelligence Sources and Methods (25X1) 6 1.1 (U) Document Administration 7 1.2 (U) About the National Reconnaissance Program (NRP) 10 1.2.1 (U) Fact of Satellite Reconnaissance 10 1.2.2 (U) National Reconnaissance Program Information 12 1.2.3 (U) Organizational Relationships 16 1.2.3.1. (U) SAF/SS 16 1.2.3.2. (U) SAF/SP (Program A) 18 1.2.3.3. (U) CIA (Program B) 18 1.2.3.4. (U) Navy (Program C) 19 1.2.3.5. (U) CIA/Air Force (Program D) 19 1.2.3.6. (U) Defense Recon Support Program (DRSP/DSRP) 19 1.3 (U) Satellite Imagery (IMINT) Systems 21 1.3.1 (U) Imagery System Information 21 1.3.2 (U) Non-Operational IMINT Systems 25 1.3.3 (U) Current and Future IMINT Operational Systems 32 1.3.4 (U) Meteorological Forecasting 33 1.3.5 (U) IMINT System Ground Operations 34 1.4 (U) Signals Intelligence (SIGINT) Systems 36 1.4.1 (U) Signals Intelligence System Information 36 1.4.2 (U) Non-Operational SIGINT Systems 38 1.4.3 (U) Current and Future SIGINT Operational Systems 40 1.4.4 (U) SIGINT -
A Tool for Preliminary Design of Rockets Aerospace Engineering
A Tool for Preliminary Design of Rockets Diogo Marques Gaspar Thesis to obtain the Master of Science Degree in Aerospace Engineering Supervisor : Professor Paulo Jorge Soares Gil Examination Committee Chairperson: Professor Fernando José Parracho Lau Supervisor: Professor Paulo Jorge Soares Gil Members of the Committee: Professor João Manuel Gonçalves de Sousa Oliveira July 2014 ii Dedicated to my Mother iii iv Acknowledgments To my supervisor Professor Paulo Gil for the opportunity to work on this interesting subject and for all his support and patience. To my family, in particular to my parents and brothers for all the support and affection since ever. To my friends: from IST for all the companionship in all this years and from Coimbra for the fellowship since I remember. To my teammates for all the victories and good moments. v vi Resumo A unica´ forma que a humanidade ate´ agora conseguiu encontrar para explorar o espac¸o e´ atraves´ do uso de rockets, vulgarmente conhecidos como foguetoes,˜ responsaveis´ por transportar cargas da Terra para o Espac¸o. O principal objectivo no design de rockets e´ diminuir o peso na descolagem e maximizar o payload ratio i.e. aumentar a capacidade de carga util´ ao seu alcance. A latitude e o local de lanc¸amento, a orbita´ desejada, as caracter´ısticas de propulsao˜ e estruturais sao˜ constrangimentos ao projecto do foguetao.˜ As trajectorias´ dos foguetoes˜ estao˜ permanentemente a ser optimizadas, devido a necessidade de aumento da carga util´ transportada e reduc¸ao˜ do combust´ıvel consumido. E´ um processo utilizado nas fases iniciais do design de uma missao,˜ que afecta partes cruciais do planeamento, desde a concepc¸ao˜ do ve´ıculo ate´ aos seus objectivos globais. -
Materials for Liquid Propulsion Systems
CHAPTER 12 Materials for Liquid Propulsion Systems John A. Halchak Consultant, Los Angeles, California James L. Cannon NASA Marshall Space Flight Center, Huntsville, Alabama Corey Brown Aerojet-Rocketdyne, West Palm Beach, Florida 12.1 Introduction Earth to orbit launch vehicles are propelled by rocket engines and motors, both liquid and solid. This chapter will discuss liquid engines. The heart of a launch vehicle is its engine. The remainder of the vehicle (with the notable exceptions of the payload and guidance system) is an aero structure to support the propellant tanks which provide the fuel and oxidizer to feed the engine or engines. The basic principle behind a rocket engine is straightforward. The engine is a means to convert potential thermochemical energy of one or more propellants into exhaust jet kinetic energy. Fuel and oxidizer are burned in a combustion chamber where they create hot gases under high pressure. These hot gases are allowed to expand through a nozzle. The molecules of hot gas are first constricted by the throat of the nozzle (de-Laval nozzle) which forces them to accelerate; then as the nozzle flares outwards, they expand and further accelerate. It is the mass of the combustion gases times their velocity, reacting against the walls of the combustion chamber and nozzle, which produce thrust according to Newton’s third law: for every action there is an equal and opposite reaction. [1] Solid rocket motors are cheaper to manufacture and offer good values for their cost. Liquid propellant engines offer higher performance, that is, they deliver greater thrust per unit weight of propellant burned. -
O51739533 1970.Pdf
MAR 2 6 1971 A J NASA BUDGET ANALYSIS FY 1970 DATA PUBLICATIONS West Building - Washington National Airport Washington, D.C. 20001 (703) 684-8270 NASA Headquarters Library 300 E St. SW Rm. 1120 Washington, DC 20546 TABLE OF CONTENTS OUTLOOK.. *. 5 NEW RESEARCH AND DEVELOPMENT PROGRAMS AND PROJECTS. 7 TENYEARGOALS. e . 10 TABLES Summary of Appropriations . 12 Summary of Appropriations (Adjusted). 13 Summary of Budget Plan by Appropriation by Budget Activity . - . 14 Budget Plan, Office of Manned Space Flight. e . * . 15 Budget Plan, Office of Space Science & Applications, Office of University Affairs. 16 Budget Plan, Office of Advanced Research and Technology Programs, Office of Tracking and Data Acquisition Programs, and Office of Technology Utilizatlon Program . 17,18 Number of Personnel Positions . 19 Research and Development - Program and Financing. 20-23 Summary of Research and Development Budget Plan by Cognizant Office. , . 24 Summary of Construction of Facilities Budget Plan by Locations. e . e e . 25 Research and Program Management - Program and Financing a . 26,27 Research and Program Management - Summary of Obligations by Installations. 28 NEW RESEARCH AND DEVELOPMENT PROJECTS . e . 29 PROGRAMS Apollo Program- .*.>.e./ 1 . 33 Space Flight Operations Program . I....... 40 Advanced Missions Program . I . 45 Physics and Astronomy Program . .......... 47 Lunar and Planetary Exploration Program . 52 Bioscience Program. , . - . I . 64 Space Applications Program. 70 Launch Vehicle Procurc>ment Program. e e . 79 Sustaining University Program . .I.... ..... 82 Basic Research Program. , a . .I ....... 86 Space Vehicles Systems Prc,yram. , LO..... 88 Electronic. Systtms Program. e . , - . 92 Human Factor Systems Program. ~ . 95 Space Power and Electric Propulsion Systems Program . -
Applications Technology Satellite Advanced Missions Study
NASA CR 120873 APPLICATIONS TECHNOLOGY SATELLITE ADVANCED MISSIONS STUDY CASE FILE FINAL REPORT COPY VOLUME I OF II SPACE & ELECTRONICS DIVISION prepared for NATIONAL AERONAUTICS AND SPACE ADMINISTRATION NASA Lewis Research Center Contract NAS 3-14360 NASA CR 120873 APPLICATIONS TECHNOLOGY SATELLITE ADVANCED MISSIONS STUDY FINAL REPORT VOLUME I OF II SPACE & ELECTRONICS DIVISION prepared for NATIONAL AERONAUTICS AND SPACE ADMINISTRATION NASA Lewis Research Center Contract NAS 3-14360 APPLICATIONS TECHNOLOGY SATELLITE ADVANCED MISSIONS STUDY CONTRACT NO. NAS 3-14360 NASA LEWIS RESEARCH CENTER 1. Report No. 2. Government Accession No. 3. Recipient's Catalog No. NASA CR 120873 4. Title and Subtitle 5. Report Date Applications Technology Satellites Advanced Mission Study 6. Performing Organization Code 7. Author(s) 8. Performing Organization Report No. D. L. Robinson et. al. 10. Work Unit No. 9. Performing Organization Name and Address Fairchild Industries 11. Contract or Grant No. Space and Electronics Division NAS 3-14360 Germantown, Maryland 20767 13. Type of Report and Period Covered 12. Sponsoring Agency Name and Address National Aeronautics and Space Administration 14. Sponsoring Agency Code Washington, D. C. 20546 15. Supplementary Notes Project Manager, Robert E. Alexovich, Division, NASA Lewis Research Center, Cleveland, Ohio 16. Abstract Four different spacecraft configurations were developed for geostationary service as a high power communications satellite. The first configuration is a Thor-Delta launch into a low orbit with a spiral ascent to synchronous altitude by ion engine propulsion. The spacecraft is earth oriented with rotating solar arrays. Configuration #2 is a direct injection Atlas/Centaur/Burner n vehicle which when in orbit is sun-oriented with a rotating transponder tower. -
Howard Seifert Papers
http://oac.cdlib.org/findaid/ark:/13030/tf0z09n4j4 No online items Guide to the Howard Seifert Papers Daniel Hartwig Stanford University. Libraries.Department of Special Collections and University Archives Stanford, California 2001 Copyright © 2015 The Board of Trustees of the Leland Stanford Junior University. All rights reserved. Note This encoded finding aid is compliant with Stanford EAD Best Practice Guidelines, Version 1.0. Guide to the Howard Seifert SC0173 1 Papers Overview Call Number: SC0173 Creator: Seifert, Howard, 1911-1977 Creator: Seifert,, 1911-1977. Title: Howard Seifert papers Dates: 1960-1977 Physical Description: 39.5 Linear feet Language(s): The materials are in English. Repository: Department of Special Collections and University Archives Green Library 557 Escondido Mall Stanford, CA 94305-6064 Email: [email protected] Phone: (650) 725-1022 URL: http://library.stanford.edu/spc Custodial History Gift of Mrs. Howard Seifert, 1977, and administrative transfer, Department of Aeronautics and Astronautics, 1979. Information about Access None. Ownership & Copyright Property rights reside with the repository. Literary rights reside with the creators of the documents or their heirs. To obtain permission to publish or reproduce, please contact the Public Services Librarian of the Dept. of Special Collections and University Archives. Cite As [Identification of item], Howard Seifert Papers, SC 173, Stanford University Archives, Stanford, Calif. Biography Howard Seifert, an authority on rocket propulsion of space vehicles, was professor of aeronautics and astronautics at Stanford from 1960 to 1976. He also directed the Physical Sciences Laboratory at the United Aircraft Corporation (1960-65) and was president of the American Rocket Society (1960). Before joining the Stanford faculty, he was on the staff at the Jet Propulsion Laboratory and Space Technology Laboratories and a visiting professor at UCLA. -
EELV Phase 2 – an Old Configuration Option with New Relevance To
Phase 2 EELV – An Old Configuration Option with New Relevance to Future Heavy Lift Cargo Jonathan Barr and Bernard Kutter United Launch Alliance (ULA) 9100 E. Mineral Avenue Centennial, CO 80112 Abstract In 2004, the Atlas program of Lockheed Martin created a vision for performance evolution of the Atlas V family focused on NASA growth missions, with performance options ranging up to 140t. The 5m diameter, 70t class Phase 2 Atlas Heavy, assuming dual RD-180s, was a key vehicle in this evolution. With Constellation, this configuration was put on the back burner, but there is now renewed interest with Augustine Commission identifying this vehicle on its short list of candidate Heavy Lift Launch Vehicles (HLLVs). With a dearth of publicly available data on this vehicle concept, this paper summarizes this configuration and its merits. The creation of United Launch Alliance has created important synergies with the availability of 5m tank hardware and production facilities from Delta IV, allowing ULA to incorporate the best of Atlas and Delta. The Phase 2 design leverages existing assets, including the Delta IV factory and the Atlas V launch pad, makes this a true EELV evolution. Newer upper stages alternatives now conceptually exist that might leverage NASA developments from the Constellation program to further enhance the Phase II EELV concept. I. Introduction In the late 1990s, Boeing was developing the Delta IV and Lockheed Martin the Atlas V as competitors for the Evolved Expendable Launch Vehicle (EELV) Program. In the midst of that activity, the focus was on getting the Delta IV and Atlas V fleets developed and flying. -
RWTH Aachen University Institute of Jet Propulsion and Turbomachinery
RWTH Aachen University Institute of Jet Propulsion and Turbomachinery DLR - German Aerospace Center Institute of Space Propulsion Optimization of a Reusable Launch Vehicle using Genetic Algorithms A thesis submitted for the degree of M.Sc. Aerospace Engineering by Simon Jentzsch June 20, 2020 Advisor: Felix Wrede, M.Sc. External Advisors: Kai Dresia, M.Sc. Dr. Günther Waxenegger-Wilfing Examiner: Prof. Dr. Michael Oschwald Statutory Declaration in Lieu of an Oath I hereby declare in lieu of an oath that I have completed the present Master the- sis entitled ‘Optimization of a Reusable Launch Vehicle using Genetic Algorithms’ independently and without illegitimate assistance from third parties. I have used no other than the specified sources and aids. In case that the thesis is additionally submitted in an electronic format, I declare that the written and electronic versions are fully identical. The thesis has not been submitted to any examination body in this, or similar, form. City, Date, Signature Abstract SpaceX has demonstrated that reusing the first stage of a rocket implies a significant cost reduction potential. In order to maximize cost savings, the identification of optimum rocket configurations is of paramount importance. Yet, the complexity of launch systems, which is further increased by the requirement of a vertical landing reusable first stage, impedes the prediction of launch vehicle characteristics. Therefore, in this thesis, a multidisciplinary system design optimization approach is applied to develop an optimization platform which is able to model a reusable launch vehicle with a large variety of variables and to optimize it according to a predefined launch mission and optimization objective. -
COMPARATIVE EVALUATION of EXISTING EXPENDABLE UPPER STAGES for SPACE SHUTTLE by Vernon J
https://ntrs.nasa.gov/search.jsp?R=19740022194 2020-03-23T04:20:46+00:00Z NA 8 A TECH NICAL NASA TM X-71579 MEMORANDUM U', (NASA-TM-X-71579) COMPARATIVE EVALUATION N74-3 0307 OF EXISTING EXPENDABLE UPPER STAGES FOR SSPACE SHUTTLE (NASA) -- +-4-p HC $4.50 zO( CSCL 22B Unclas . -. _G3/31_ 544 45 COMPARATIVE EVALUATION OF EXISTING EXPENDABLE UPPER STAGES FOR SPACE SHUTTLE by Vernon J. Weyers, Gary D. Sagerman, Janos Borsody and Robert J. Lubick Lewis Research Center Cleveland, Ohio 44135 June 1974 TECHNICAL MEMORANDUM COMPARATIVE EVALUATION OF EXISTING EXPENDABLE UPPER STAGES FOR SPACE SHUTTLE by Vernon J. Weyers, Gary D. Sagerman, Janos Borsody and Robert J. Lubick ABSTRACT The use of existing expendable upper stages in the Space Shuttle during its early years of operation is evaluated. The Burner II, Scout, Delta, Agena, Transtage and Centaur were each studied under contract by their respective manufacturers to determine the extent and cost of the minimum modifications necessary to integrate the stage with the Shuttle Orbiter. A comparative economic analysis of thirty-five different families of these stages is discussed, The results show that the overall transportation system cost differences between many of the families are quite small. However, by considering several factors in addition to cost, it is possible to select one family as being representative of the capability of the minimum modif- ication existing stage approach. The selected family meets all of the specified mission requirements during the early years of Shuttle operation, i TABLE OF CONTENTS Page SUMMARY . ............................... I1 INTRODUCTION ... ... ....... ... ......... 2 GROUNDRULES & ASSUMPTIONS . -
Ranking Upper Stages in Low Earth Orbit for Active Removal
6TH EUROPEAN CONFERENCE FOR AERONAUTICS AND SPACE SCIENCES (EUCASS) Ranking upper stages in low Earth orbit for active removal L. Anselmo and C. Pardini Space Flight Dynamics Laboratory, ISTI/CNR Via G. Moruzzi 1, 56124 Pisa, Italy Abstract This paper addresses the problem of ranking the upper stages in orbit in order to evaluate their potential detrimental effects on the debris environment over the long-term, and the relative advantage of having them actively de-orbited. To do so, a new ranking scheme is introduced, applicable to any object in low Earth orbit (LEO) and able to prioritize the target objects potentially most critical for the future preservation of the LEO protected region. Applying the proposed approach, it was found, for instance, that the 22 most massive upper stages abandoned in LEO, at the beginning of 2015, are on the whole equivalent to several hundred average intact objects in sun-synchronous orbit, regarding their latent detrimental effects on the debris environment over the next 200 years. Most of them could therefore be the top priority targets of any worldwide coordinated effort for active removal and the prevention of new collisional debris. The ranking scheme was also applied to other main models of rocket bodies currently in orbit, trying to identify the combinations of orbital elements and upper stage types requiring particular attention. 1. Introduction Currently, spent upper stages represent more than 42% of the intact objects abandoned in orbit, accounting for 57% of the abandoned mass (and 48% of the total mass, including operational spacecraft). Due to the fact that they belong to a relatively small number of models, compared to spacecraft, and are typically much more symmetric and simple shaped, rocket bodies are ideal candidates for active debris removal missions.