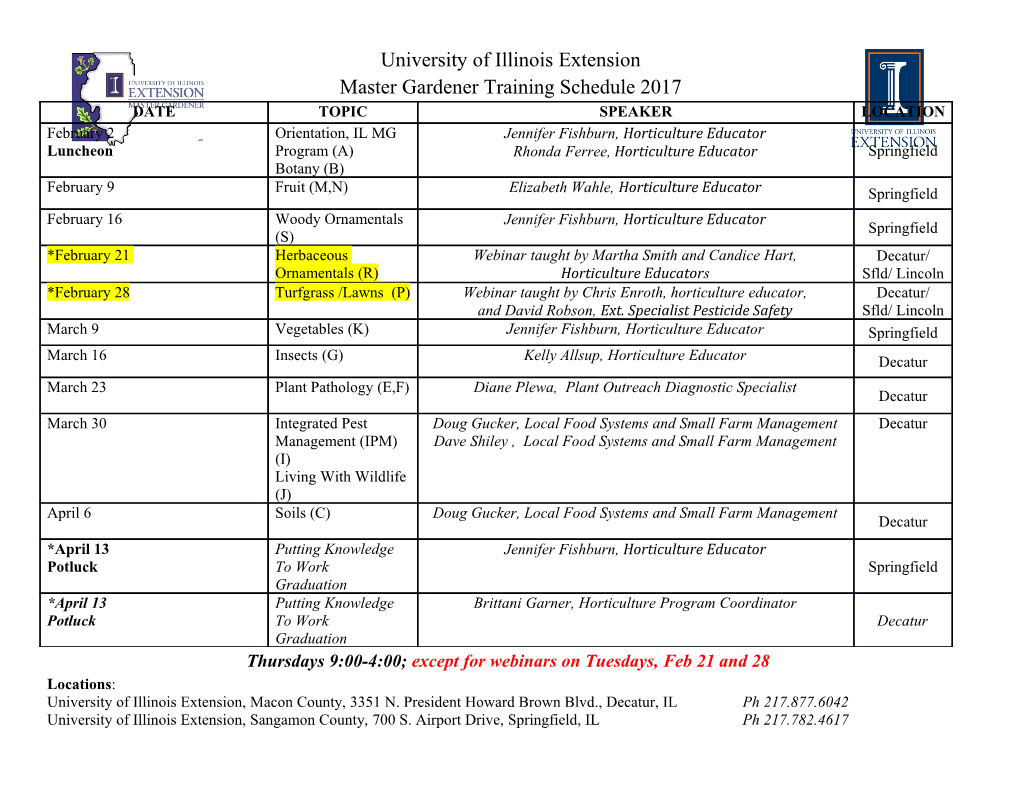
Richard Nakka's Experimental Rocketry Web Site Solid Propellant Burn Rate • Introduction • What Influences Burning Rate? • Modification of Burning Rate • Combustion Process • Burn Rate Measurement Introduction The burning surface of a rocket propellant grain recedes in a direction perpendicular to this burning surface. The rate of regression, typically measured in inches per second (or mm per second), is termed burning rate (or burn rate). This rate can differ significantly for different propellants, or for one particular propellant, depending on various operating conditions as well as formulation. Knowing quantitatively the burning rate of a propellant, and how it changes under various conditions, is of fundamental importance in the successful design of a solid rocket motor. This web page discusses the factors that influence burn rate, how it may be modified, how the burn rate can be determined experimentally, and the physical processes that occur at the burning surface of a propellant that governs the burning rate. What Influences Burning Rate? An illustration of the concept of burning surface regression is given in Figure 1, for a section of a hollow cylindrical grain, with an inhibited outer surface ( "inhibited" means that the propellant surface is protected from the heat of combustion and as such, burning does not occur). Burning commences along the length of the central core, with the burning surface receding radially outward (shown at arbitrary times t1, t2, t3). Note that the burning surface area (represented by the arc length of the red lines in this figure) is continually increasing. Also note that the surface regression rate (burn rate) is not constant. These two events are, in fact, directly related, as will be discussed shortly. Figure 1 -- Burning surface regression Propellant burning rate is influenced by certain factors, the most significant being: 1. Combustion chamber pressure 2. Initial temperature of the propellant grain 3. Velocity of the combustion gases flowing parallel to the burning surface 4. Local static pressure 5. Motor acceleration and spin These factors are discussed below. 1. Burn rate is profoundly affected by chamber pressure. For example, KNSU has a burning rate of 3.8 mm/sec. at 1 atmosphere. However, at 68 atmospheres (1000 psi), the burn rate is about 15 mm/sec., a four-fold increase. The usual representation of the pressure dependance on burn rate is the Saint Robert's Law (a.k.a. Vieille's Law): r = ro + a Pc n where r is the burn rate, ro is a constant (usually taken as zero), a is the burn rate coefficient, and n is the pressure exponent. The values of a and n are determined empirically for a particular propellant formulation, and cannot be theoretically predicted. Various means may be employed to determine these parameters, such as a Strand Burner or Ballistic Evaluation Motor (BEM). It is important to realize that a single set of a, n values are typically valid over a distinct pressure range. More than one set may be necessary to accurately represent the full pressure regime of interest, as illustrated in Figure 2. Figure 2 -- Saint Robert's model of burn rate v.s. pressure (example) When plotted on log-log scales, the Saint Robert's function is a straight line. Certain propellants (or with additives) deviate from this behaviour, and exhibit sharp changes in burn rate behaviour. These type of propellants are termed plateau or mesa propellants, as illustrated in Figure 3. Both the KNDX and KNSB propellants exhibit this behaviour, the former plateau, and the latter, mesa (see KNDX & KNSB Propellants -- Burn Rate Experimentation). Plateau and mesa effects may be the result of different rates of surface regression (as a function of pressure) of the binder compared to the oxidizer particles. Another explanation is that the condensed phase combustion products may "pool" and retard heat transfer to the surface at elevated pressure levels. Figure 3 -- Plateau and mesa behaviour Burning rate can be particularly sensitive to the value of the pressure exponent, n (the slope of the log-log curve in Fig.3). High values of n can produce large changes in burning rate with relatively small changes in chamber pressure, with potentially catastrophic consequences, as higher burning rate leads to even greater chamber pressure. Another reason why a high pressure exponent may be undesireable (at least for amateur motors) is due to the low sensitivity of burn rate, due to pressure, at the low end of the pressure regime. This can result in difficult starting, with the motor simply refusing to "come up to pressure". This low sensitivity to pressure, for high pressure exponents, becomes more clear if we consider a pressure exponent of unity (n=1). This implies burn rate beinging directly, or linearly, proportional to chamber pressure. The slope of the burn rate v.s. pressure curve is a straight line. Figure 4 illustrates the pressure profile for various values of n. It can be seen that with a low value of pressure exponent, for example n=0.2, the burn rate changes very rapidly at low pressure, providing excellent motor start-up capability. Figure 4 -- Effect of various pressure exponents on burning rate sensitivity to pressure If the value of the exponent is close to zero, the burning rate is largely insensitive to pressure, and unstable combustion may result. For these reasons, the pressure exponent for a practical propellant should have a value between 0.3 and 0.6 in the regime of the motor steady-state operating condition. 2. Temperature affects the rate of chemical reactions and thus the initial temperature of the propellant grain influences burning rate. If a particular propellant shows significant sensitivity to initial grain temperature, operation at temperature extremes will affect the time-thrust profile of the motor. This is a factor to consider for winter launches, for example, when the grain temperature may be 20 or more degrees (C.) lower than "normal" launch conditions. Both the KNDX & KNSB Propellants seem to show minor sensitivity to temperature over the range of 0oC to 40oC. (see KNDX & KNSB Propellants -- Burn Rate Experimentation). 3. For most propellants, certain levels of local combustion gas velocity (or mass flux) flowing parallel to the burning surface leads to an increased burning rate. This "augmentation" of burn rate is referred to as erosive burning, with the extent varying with propellant type and chamber pressure. The mechanism of increased convective heat transfer to the propellant surface due to turbulence is most likely responsible for this augmentation. For many propellants, a threshold flow velocity exists. Below this flow level, either no augmentation occurs, or a decrease in burn rate is experienced (negative erosive burning). This is illustrated in Figure 5. Figure 5 -- Erosive burning phenomenon In Figure 5, propellant "A" exhibits a threshold flow velocity of about 240 ft/sec. Propellant "B" (AP/polyurethane) exhibits a lower threshold velocity with higher chamber pressures. Below this threshold level, an interesting phenomenon occurs -- the burn rate decreases relative to the zero flow level. This is referred to as negative erosive burning, and is possibly the result of changing physical processes of heat transfer that controls the burning rate. At low flow velocity, mass transfer dominates, but as the flow velocity increases, the mechanism of convection becomes increasingly more significant (Figure 5). Figure 6 -- Heat transfer processes that influence burning rate An alternative explanation suggests that this effect may be due to partial coverage of the oxidizer (particle) surfaces by the melted binder under the effect of shear stresses in the boundary layer of combustion flow. The KNSB Propellant appears to be particularly susceptible to negative erosive burning. The effects of erosive burning can be minimized by designing the motor with a sufficiently large port-to-throat area ratio (Aport/At). The port area is the cross- section area of the flow channel(s) in a motor. For a hollow-cylindrical grain, this is the cross-section area of the core. As a rule of thumb, the ratio should be a minimum of 2, for a "typical" grain L/D ratio of 6. A greater Aport/At ratio should be used for grains with larger L/D ratios. To relate the erosive burning rate to the gas flow in the combustion chamber, various empirical laws are used: r = a Pc n [1 + k(G - G*) ] multiplicative law where k is a constant, and G is the specific mass flow rate of the main flow, and G* is a threshold flow rate. r = a Pc n + k u additive law where k is a constant, and u is the velocity of the main flow. 4. In an operating rocket motor, there is a pressure drop along the axis of the combustion chamber, a drop which is physically necessary to accelerate the increasing mass flow of combustion products toward the nozzle. The static pressure is greatest where gas flow is zero, that is, at the front (bulkhead) of the motor. Since burn rate is dependant upon the local pressure, the rate should be greatest at this location. However, this effect is relatively minor and is usually offset by the countereffect of erosive burning. 5. Burning rate is enhanced by acceleration of the motor. Whether the acceleration is a result of longitudinal force (e.g. thrust) or spin, burning surfaces that form an angle of about 60-90o with the acceleration vector are prone to increased burn rate. As the majority of the burning surface of most grain configurations is perpendicular to the motor axis, spin (rather than longitudinal acceleration) has a far more profound effect on burning rate. There are three main reasons why spin increases burn rate: 1. Rotation reduces the mass flux (flow) at the nozzle throat.
Details
-
File Typepdf
-
Upload Time-
-
Content LanguagesEnglish
-
Upload UserAnonymous/Not logged-in
-
File Pages103 Page
-
File Size-