Advanced Atlas Launch Vehicle DIGEST
Total Page:16
File Type:pdf, Size:1020Kb
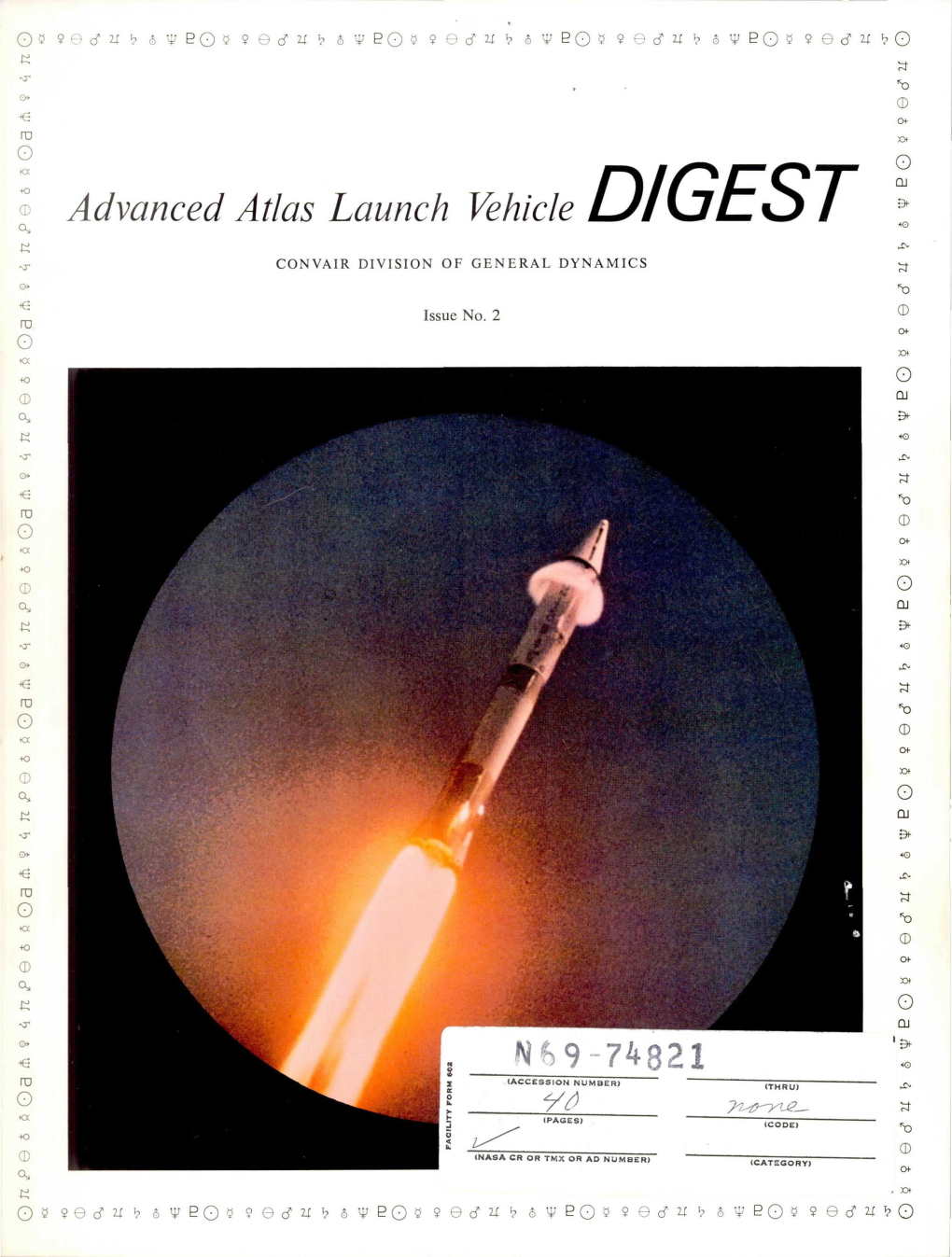
Load more
Recommended publications
-
The SKYLON Spaceplane
The SKYLON Spaceplane Borg K.⇤ and Matula E.⇤ University of Colorado, Boulder, CO, 80309, USA This report outlines the major technical aspects of the SKYLON spaceplane as a final project for the ASEN 5053 class. The SKYLON spaceplane is designed as a single stage to orbit vehicle capable of lifting 15 mT to LEO from a 5.5 km runway and returning to land at the same location. It is powered by a unique engine design that combines an air- breathing and rocket mode into a single engine. This is achieved through the use of a novel lightweight heat exchanger that has been demonstrated on a reduced scale. The program has received funding from the UK government and ESA to build a full scale prototype of the engine as it’s next step. The project is technically feasible but will need to overcome some manufacturing issues and high start-up costs. This report is not intended for publication or commercial use. Nomenclature SSTO Single Stage To Orbit REL Reaction Engines Ltd UK United Kingdom LEO Low Earth Orbit SABRE Synergetic Air-Breathing Rocket Engine SOMA SKYLON Orbital Maneuvering Assembly HOTOL Horizontal Take-O↵and Landing NASP National Aerospace Program GT OW Gross Take-O↵Weight MECO Main Engine Cut-O↵ LACE Liquid Air Cooled Engine RCS Reaction Control System MLI Multi-Layer Insulation mT Tonne I. Introduction The SKYLON spaceplane is a single stage to orbit concept vehicle being developed by Reaction Engines Ltd in the United Kingdom. It is designed to take o↵and land on a runway delivering 15 mT of payload into LEO, in the current D-1 configuration. -
L AUNCH SYSTEMS Databk7 Collected.Book Page 18 Monday, September 14, 2009 2:53 PM Databk7 Collected.Book Page 19 Monday, September 14, 2009 2:53 PM
databk7_collected.book Page 17 Monday, September 14, 2009 2:53 PM CHAPTER TWO L AUNCH SYSTEMS databk7_collected.book Page 18 Monday, September 14, 2009 2:53 PM databk7_collected.book Page 19 Monday, September 14, 2009 2:53 PM CHAPTER TWO L AUNCH SYSTEMS Introduction Launch systems provide access to space, necessary for the majority of NASA’s activities. During the decade from 1989–1998, NASA used two types of launch systems, one consisting of several families of expendable launch vehicles (ELV) and the second consisting of the world’s only partially reusable launch system—the Space Shuttle. A significant challenge NASA faced during the decade was the development of technologies needed to design and implement a new reusable launch system that would prove less expensive than the Shuttle. Although some attempts seemed promising, none succeeded. This chapter addresses most subjects relating to access to space and space transportation. It discusses and describes ELVs, the Space Shuttle in its launch vehicle function, and NASA’s attempts to develop new launch systems. Tables relating to each launch vehicle’s characteristics are included. The other functions of the Space Shuttle—as a scientific laboratory, staging area for repair missions, and a prime element of the Space Station program—are discussed in the next chapter, Human Spaceflight. This chapter also provides a brief review of launch systems in the past decade, an overview of policy relating to launch systems, a summary of the management of NASA’s launch systems programs, and tables of funding data. The Last Decade Reviewed (1979–1988) From 1979 through 1988, NASA used families of ELVs that had seen service during the previous decade. -
Atlas Launch System Mission Planner's Guide, Atlas V Addendum
ATLAS Atlas Launch System Mission Planner’s Guide, Atlas V Addendum FOREWORD This Atlas V Addendum supplements the current version of the Atlas Launch System Mission Plan- ner’s Guide (AMPG) and presents the initial vehicle capabilities for the newly available Atlas V launch system. Atlas V’s multiple vehicle configurations and performance levels can provide the optimum match for a range of customer requirements at the lowest cost. The performance data are presented in sufficient detail for preliminary assessment of the Atlas V vehicle family for your missions. This guide, in combination with the AMPG, includes essential technical and programmatic data for preliminary mission planning and spacecraft design. Interface data are in sufficient detail to assess a first-order compatibility. This guide contains current information on Lockheed Martin’s plans for Atlas V launch services. It is subject to change as Atlas V development progresses, and will be revised peri- odically. Potential users of Atlas V launch service are encouraged to contact the offices listed below to obtain the latest technical and program status information for the Atlas V development. For technical and business development inquiries, contact: COMMERCIAL BUSINESS U.S. GOVERNMENT INQUIRIES BUSINESS INQUIRIES Telephone: (691) 645-6400 Telephone: (303) 977-5250 Fax: (619) 645-6500 Fax: (303) 971-2472 Postal Address: Postal Address: International Launch Services, Inc. Commercial Launch Services, Inc. P.O. Box 124670 P.O. Box 179 San Diego, CA 92112-4670 Denver, CO 80201 Street Address: Street Address: International Launch Services, Inc. Commercial Launch Services, Inc. 101 West Broadway P.O. Box 179 Suite 2000 MS DC1400 San Diego, CA 92101 12999 Deer Creek Canyon Road Littleton, CO 80127-5146 A current version of this document can be found, in electronic form, on the Internet at: http://www.ilslaunch.com ii ATLAS LAUNCH SYSTEM MISSION PLANNER’S GUIDE ATLAS V ADDENDUM (AVMPG) REVISIONS Revision Date Rev No. -
Materials for Liquid Propulsion Systems
https://ntrs.nasa.gov/search.jsp?R=20160008869 2019-08-29T17:47:59+00:00Z CHAPTER 12 Materials for Liquid Propulsion Systems John A. Halchak Consultant, Los Angeles, California James L. Cannon NASA Marshall Space Flight Center, Huntsville, Alabama Corey Brown Aerojet-Rocketdyne, West Palm Beach, Florida 12.1 Introduction Earth to orbit launch vehicles are propelled by rocket engines and motors, both liquid and solid. This chapter will discuss liquid engines. The heart of a launch vehicle is its engine. The remainder of the vehicle (with the notable exceptions of the payload and guidance system) is an aero structure to support the propellant tanks which provide the fuel and oxidizer to feed the engine or engines. The basic principle behind a rocket engine is straightforward. The engine is a means to convert potential thermochemical energy of one or more propellants into exhaust jet kinetic energy. Fuel and oxidizer are burned in a combustion chamber where they create hot gases under high pressure. These hot gases are allowed to expand through a nozzle. The molecules of hot gas are first constricted by the throat of the nozzle (de-Laval nozzle) which forces them to accelerate; then as the nozzle flares outwards, they expand and further accelerate. It is the mass of the combustion gases times their velocity, reacting against the walls of the combustion chamber and nozzle, which produce thrust according to Newton’s third law: for every action there is an equal and opposite reaction. [1] Solid rocket motors are cheaper to manufacture and offer good values for their cost. -
Atlas V Cutaway Poster
ATLAS V Since 2002, Atlas V rockets have delivered vital national security, science and exploration, and commercial missions for customers across the globe including the U.S. Air Force, the National Reconnaissance Oice and NASA. 225 ft The spacecraft is encapsulated in either a 5-m (17.8-ft) or a 4-m (13.8-ft) diameter payload fairing (PLF). The 4-m-diameter PLF is a bisector (two-piece shell) fairing consisting of aluminum skin/stringer construction with vertical split-line longerons. The Atlas V 400 series oers three payload fairing options: the large (LPF, shown at left), the extended (EPF) and the extra extended (XPF). The 5-m PLF is a sandwich composite structure made with a vented aluminum-honeycomb core and graphite-epoxy face sheets. The bisector (two-piece shell) PLF encapsulates both the Centaur upper stage and the spacecraft, which separates using a debris-free pyrotechnic actuating 200 ft system. Payload clearance and vehicle structural stability are enhanced by the all-aluminum forward load reactor (FLR), which centers the PLF around the Centaur upper stage and shares payload shear loading. The Atlas V 500 series oers 1 three payload fairing options: the short (shown at left), medium 18 and long. 1 1 The Centaur upper stage is 3.1 m (10 ft) in diameter and 12.7 m (41.6 ft) long. Its propellant tanks are constructed of pressure-stabilized, corrosion-resistant stainless steel. Centaur is a liquid hydrogen/liquid oxygen-fueled vehicle. It uses a single RL10 engine producing 99.2 kN (22,300 lbf) of thrust. -
NASA News National Aeronautics and Space Administration Washington
NASA News National Aeronautics and Space Administration Washington. D C 20546 AC 202 755-8370 For Release IMMEDIATE Press Kit Project Intelsat V-D RELEASE NO: 82-30 Contents GENERAL RELEASE 1 ATLAS CENTAUR, LAUNCH VEHICLE STATISTICS 3 LAUNCH OPERATIONS 4 LAUNCH SEQUENCE FOR INTELSAT V-D 5 THE NASA INTELSAT TEAM 6 CONTRACTORS 7 /lNASA-News-Belease-82^TOl INTELSAT N82-22295 "\ (SATELLITE SCHEDULED FOR LAUNCH (National (Aeronautics and Space Administration) 8 p I CSCL 22A Unclas I 00/15 18771 February 26, 1982 NASA News National Aeronautics and Space Administration Washington. D C 20546 AC 202 755-8370 For Release Dick McCormack Headquarters, Washington, D.C. IMMEDIATE (Phone: 202/755-8104) RELEASE NO: 82-30 INTELSAT SATELLITE SCHEDULED FOR LAUNCH Intelsat V-D, the fourth of a new series of nine inter- national telecommunications satellites owned and operated by the 105-nation International Telecommunications Satellite Organiza- tion (Intelsat), is scheduled to be launched by the NASA Kennedy Space Center on board an Atlas Centaur launch vehicle no earlier than March 4, 1982, from Cape Canaveral, Fla. The three Intelsat Vs were successfully launched by NASA in December 1980, May 1981 and December 1981. Intelsat V-D weighs 1,928 kilograms (4,251 pounds) at launch and has almost double the communications capability of early satellites in the Intelsat series — 12,000 voice circuits and two color television channels. It will be positioned in geosyn- chronous orbit over the Indian Ocean as the prime Intelsat satel- lite to provide communications services between Europe, the Middle East and the Far East. -
National Reconnaissance Office Review and Redaction Guide
NRO Approved for Release 16 Dec 2010 —Tep-nm.T7ymqtmthitmemf- (u) National Reconnaissance Office Review and Redaction Guide For Automatic Declassification Of 25-Year-Old Information Version 1.0 2008 Edition Approved: Scott F. Large Director DECL ON: 25x1, 20590201 DRV FROM: NRO Classification Guide 6.0, 20 May 2005 NRO Approved for Release 16 Dec 2010 (U) Table of Contents (U) Preface (U) Background 1 (U) General Methodology 2 (U) File Series Exemptions 4 (U) Continued Exemption from Declassification 4 1. (U) Reveal Information that Involves the Application of Intelligence Sources and Methods (25X1) 6 1.1 (U) Document Administration 7 1.2 (U) About the National Reconnaissance Program (NRP) 10 1.2.1 (U) Fact of Satellite Reconnaissance 10 1.2.2 (U) National Reconnaissance Program Information 12 1.2.3 (U) Organizational Relationships 16 1.2.3.1. (U) SAF/SS 16 1.2.3.2. (U) SAF/SP (Program A) 18 1.2.3.3. (U) CIA (Program B) 18 1.2.3.4. (U) Navy (Program C) 19 1.2.3.5. (U) CIA/Air Force (Program D) 19 1.2.3.6. (U) Defense Recon Support Program (DRSP/DSRP) 19 1.3 (U) Satellite Imagery (IMINT) Systems 21 1.3.1 (U) Imagery System Information 21 1.3.2 (U) Non-Operational IMINT Systems 25 1.3.3 (U) Current and Future IMINT Operational Systems 32 1.3.4 (U) Meteorological Forecasting 33 1.3.5 (U) IMINT System Ground Operations 34 1.4 (U) Signals Intelligence (SIGINT) Systems 36 1.4.1 (U) Signals Intelligence System Information 36 1.4.2 (U) Non-Operational SIGINT Systems 38 1.4.3 (U) Current and Future SIGINT Operational Systems 40 1.4.4 (U) SIGINT -
A Tool for Preliminary Design of Rockets Aerospace Engineering
A Tool for Preliminary Design of Rockets Diogo Marques Gaspar Thesis to obtain the Master of Science Degree in Aerospace Engineering Supervisor : Professor Paulo Jorge Soares Gil Examination Committee Chairperson: Professor Fernando José Parracho Lau Supervisor: Professor Paulo Jorge Soares Gil Members of the Committee: Professor João Manuel Gonçalves de Sousa Oliveira July 2014 ii Dedicated to my Mother iii iv Acknowledgments To my supervisor Professor Paulo Gil for the opportunity to work on this interesting subject and for all his support and patience. To my family, in particular to my parents and brothers for all the support and affection since ever. To my friends: from IST for all the companionship in all this years and from Coimbra for the fellowship since I remember. To my teammates for all the victories and good moments. v vi Resumo A unica´ forma que a humanidade ate´ agora conseguiu encontrar para explorar o espac¸o e´ atraves´ do uso de rockets, vulgarmente conhecidos como foguetoes,˜ responsaveis´ por transportar cargas da Terra para o Espac¸o. O principal objectivo no design de rockets e´ diminuir o peso na descolagem e maximizar o payload ratio i.e. aumentar a capacidade de carga util´ ao seu alcance. A latitude e o local de lanc¸amento, a orbita´ desejada, as caracter´ısticas de propulsao˜ e estruturais sao˜ constrangimentos ao projecto do foguetao.˜ As trajectorias´ dos foguetoes˜ estao˜ permanentemente a ser optimizadas, devido a necessidade de aumento da carga util´ transportada e reduc¸ao˜ do combust´ıvel consumido. E´ um processo utilizado nas fases iniciais do design de uma missao,˜ que afecta partes cruciais do planeamento, desde a concepc¸ao˜ do ve´ıculo ate´ aos seus objectivos globais. -
N AS a Facts
National Aeronautics and Space Administration NASA’s Launch Services Program he Launch Services Program (LSP) manufacturing, launch operations and rockets for launching Earth-orbit and Twas established at Kennedy Space countdown management, and providing interplanetary missions. Center for NASA’s acquisition and added quality and mission assurance in In September 2010, NASA’s Launch program management of expendable lieu of the requirement for the launch Services (NLS) contract was extended launch vehicle (ELV) missions. A skillful service provider to obtain a commercial by the agency for 10 years, through NASA/contractor team is in place to launch license. 2020, with the award of four indefinite meet the mission of the Launch Ser- Primary launch sites are Cape Canav- delivery/indefinite quantity contracts. The vices Program, which exists to provide eral Air Force Station (CCAFS) in Florida, expendable launch vehicles that NASA leadership, expertise and cost-effective and Vandenberg Air Force Base (VAFB) has available for its science, Earth-orbit services in the commercial arena to in California. and interplanetary missions are United satisfy agencywide space transporta- Other launch locations are NASA’s Launch Alliance’s (ULA) Atlas V and tion requirements and maximize the Wallops Flight Facility in Virginia, the Delta II, Space X’s Falcon 1 and 9, opportunity for mission success. Kwajalein Atoll in the South Pacific’s Orbital Sciences Corp.’s Pegasus and facts The principal objectives of the LSP Republic of the Marshall Islands, and Taurus XL, and Lockheed Martin Space are to provide safe, reliable, cost-effec- Kodiak Island in Alaska. Systems Co.’s Athena I and II. -
Analysis of a Heavy Lift Launch Vehicle Design Using Small Liquid
Analysis of a Heavy Lift Launch Vehicle Design Using Small Liquid Rocket Engines by DAVID PHILLIP RUSS S.B., Massachusetts Institute of Technology 1987 SUBMITTED IN PARTIAL FULFILLMENT OF THE REQUIREMENTS FOR THE DEGREE OF MASTER OF SCIENCE IN AERONAUTICS AND ASTRONAUTICS at the MASSACHUSETTS INSTITUTE OF TECHNOLOGY May 1988 ® David P. Russ 1988 The author hereby grants M.I.T. and Hughes Aircraft Company permission to reproduce and to distribute copies of this thesis document in whole or in part. Signature of Author Department of Aeronautics and Astronautics December 18, 1987 Reviewed by C. P. Rubin Hughes Aircraft Company Certified by Professor Walter M. Hollister Thesis Supervjsor, Departmer of Aeronautics and Astronautics .. Accepted by , .AU Professor Harold Y. Wachman Chairman, Depart'rmental Graduate Committee Department of Aeronautics and Astronautics MAY i od ;WITHDRAWfIN i M.I.1W.i..: P. I LBRARt S UBAer 7:Ir_ Aero Analysis of a Heavy Lift Launch Vehicle Design Using Small Liquid Rocket Engines by David P. Russ Submitted to the Department of Aeronautics and Astronautics in partial fulfillment of the requirements for the degree of Master of Science in Aeronautics and Astronautics May, 1988 Abstract The trend in launch vehicle design has been to increase performance by using en- gines of greater and greater complexity, which has a negative effect on cost and reliability. However, a design making use of over 300 small, simple rocket engines can deliver over 340,000 lbs to low Earth orbit. This design, derived by using the rocket equations to size the major components, features a 42 ft. -
San Diego History Center Is a Museum, Education Center, and Research Library Founded As the San Diego Historical Society in 1928
The Journal of San Diego Volume 58 Fall 2012 Number 4 • The Journal of San Diego Number History 2012 58 Fall Volume History Publication of The Journal of San Diego History is underwritten by a major grant from the Quest for Truth Foundation, established by the late James G. Scripps. Additional support is provided by “The Journal of San Diego History Fund” of the San Diego Foundation and private donors. The color section for the Charles Reiffel Exhibit Review has been underwritten by Thompson Fetter. The San Diego History Center is a museum, education center, and research library founded as the San Diego Historical Society in 1928. Its activities are supported by: the City of San Diego’s Commission for Arts and Culture; the County of San Diego; individuals; foundations; corporations; fundraising events; membership dues; admissions; shop sales; and rights and reproduction fees. Articles appearing in The Journal of San Diego History are abstracted and indexed in Historical Abstracts and America: History and Life. The paper in the publication meets the minimum requirements of American National Standard for Information Science-Permanence of Paper for Printed Library Materials, ANSI Z39.48-1984. Front Cover: Charles Reiffel, San Diego Harbor. Oil on Canvas, 1936. The San Diego History Center on loan from the Fine Arts Program, Public Building Services, US General Administration, commissioned through the New Deal art projects. Charles Reiffel: An American Post-Impressionist, Catalogue No. 63. Back Cover: Charles Reiffel, detail from History of San Diego—Colonial, 1939. The San Diego History Center, gift of Donna Sefton. Cover Design: Allen Wynar The Journal of San Diego History IRIS H. -
Catching up in the Moon Race by Andrew J
Catching Up in the Moon Race by Andrew J. LePage December 15, 1999 Introduction recognized that an ICBM was a feasible weapon. The Atlas made use of an innovative stage-and-a-half Before NASA was founded in October of 1958, the design where a pair of booster engines were USAF had ambitous plans for space exploration. jettisoned after they were no longer needed during During the national debate that followed the launch ascent. A sustainer engine would then push the of Sputnik, the USAF was trying to position itself so payload towards its target feeding off of the that it could dominate the nation's infant space remaining propellants in the missile's lightweight program. Even after the Advanced Research Projects integral propellant tanks that used internal pressure to Agency (ARPA) was founded in February of 1958 maintain the stiffness of the missile. The first model, and given the task of coordinating America's military Atlas A, only used the pair of booster engines to send space programs, USAF efforts and plans figured the rocket on an abbreviated test flight. Atlas 4A prominently. made the first test flight on June 11, 1957 but failed. The first successful test, Atlas 12A, came on The USAF's first step beyond the Earth orbit was a December 17 of that year. lunar exploration program approved by President Eisenhower as part Operation Mona on March 27, The next model, the Atlas B, had a full complement 1958 (see Operation Mona: America's First Moon of engines and would test the complete weapon Program in the April 1998 issue of SpaceViews).