On Horizontal Curves Final Technical Report Volume I1
Total Page:16
File Type:pdf, Size:1020Kb
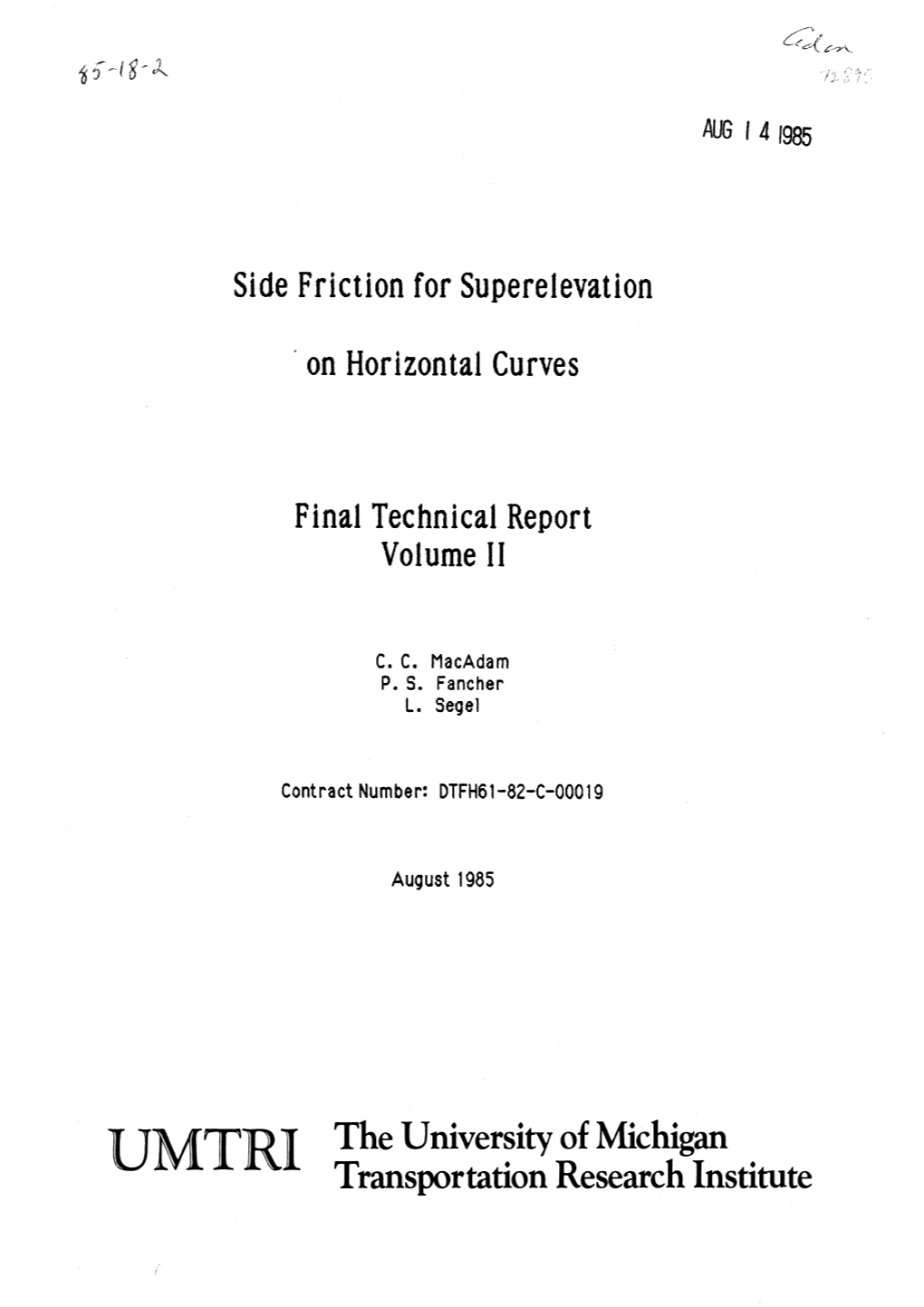
Load more
Recommended publications
-
Estudio De Un Sistema Aerodinámico Activo En Automóviles: Control Y Automatización Del Sistema
TRABAJO FINAL DE GRADO Grado en Ingeniería Mecánica ESTUDIO DE UN SISTEMA AERODINÁMICO ACTIVO EN AUTOMÓVILES: CONTROL Y AUTOMATIZACIÓN DEL SISTEMA Memoria y Anexos Autor: Antonio Rodríguez Noriega Director: Sebastián Tornil Convocatoria: Junio 2018 Estudio de un sistema aerodinámico activo en automóviles: control y automatización del sistema Resumen A lo largo de este proyecto se tratará el diseño desde cero de un sistema de aerodinámica activa para automóviles. El proceso consta de tres partes diferenciadas: el estudio aerodinámico, donde se caracteriza la interacción fluidodinámica de un perfil alar; el estudio mecánico, donde se diseña el conjunto de mecanismos que forman el sistema mecánico, así como su posterior validación; y la automatización y el control del sistema, donde se modeliza el comportamiento del vehículo y se implementa en un sistema electrónico de control regulado. Estas partes se presentan como tres Trabajos Finales de Grado distintos relacionados entre sí. En esta memoria se desarrolla la tercera de ellas: la automatización y el control del sistema. El objetivo principal ha sido completar la fase de diseño de un sistema que mejore el comportamiento dinámico de un vehículo de carácter deportivo en el mayor número posible de situaciones. Esto se ha conseguido variando la repartición de cargas normales por rueda a partir de la modificación de las características geométricas del propio conjunto aerodinámico, mediante el uso de actuadores lineales regulados por un sistema de control en función de las condiciones del automóvil en tiempo real. I Memoria Resum Durant el transcurs d’aquest projecte es tractarà el disseny des de zero d’un sistema d’aerodinàmica activa per a automòbils. -
The Benefits of Four-Wheel Drive for a High-Performance FSAE Electric Racecar Elliot Douglas Owen
The Benefits of Four-Wheel Drive for a High-Performance FSAE Electric Racecar by Elliot Douglas Owen Submitted to the Department of Mechanical Engineering in partial fulfillment of the requirements for the degree of Bachelor of Science in Mechanical Engineering at the MASSACHUSETTS INSTITUTE OF TECHNOLOGY June 2018 c Elliot Douglas Owen, MMXVIII. All rights reserved. The author hereby grants to MIT permission to reproduce and to distribute publicly paper and electronic copies of this thesis document in whole or in part in any medium now known or hereafter created. Author.................................................................... Department of Mechanical Engineering May 18, 2018 Certified by . David L. Trumper Professor Thesis Supervisor Accepted by . Rohit Karnik Associate Professor of Mechanical Engineering Undergraduate Officer 2 The Benefits of Four-Wheel Drive for a High-Performance FSAE Electric Racecar by Elliot Douglas Owen Submitted to the Department of Mechanical Engineering on May 18, 2018, in partial fulfillment of the requirements for the degree of Bachelor of Science in Mechanical Engineering Abstract This thesis explores the performance of Rear-Wheel Drive (RWD) and Four-Wheel Drive (4WD) FSAE Electric racecars with regards to acceleration and regenerative braking. The benefits of a 4WD architecture are presented along with the tools for further optimization and understanding. The goal is to provide real, actionable information to teams deciding to pursue 4WD vehicles and quantify the results of difficult engineering tradeoffs. Analytical bicycle models are used to discuss the effect of the Center of Gravity location on vehicle performance, and Acceleration-Velocity Phase Space (AVPS) is introduced as a useful tool for optimization. -
Camber Effect Study on Combined Tire Forces
Camber effect study on combined tire forces Shiruo Li Master Thesis in Vehicle Engineering Department of Aeronautical and Vehicle Engineering KTH Royal Institute of Technology TRITA-AVE 2013:33 ISSN 1651-7660 Postal address Visiting Address Telephone Telefax Internet KTH Teknikringen 8 +46 8 790 6000 +46 8 790 6500 www.kth.se Vehicle Dynamics Stockholm SE-100 44 Stockholm, Sweden Abstract Considering the more and more concerned climate change issues to which the greenhouse gas emission may contribute the most, as well as the diminishing fossil fuel resource, the automotive industry is paying more and more attention to vehicle concepts with full electric or partly electric propulsion systems. Limited by the current battery technology, most electrified vehicles on the roads today are hybrid electric vehicles (HEV). Though fully electrified systems are not common at the moment, the introduction of electric power sources enables more advanced motion control systems, such as active suspension systems and individual wheel steering, due to electrification of vehicle actuators. Various chassis and suspension control strategies can thus be developed so that the vehicles can be fully utilized. Consequently, future vehicles can be more optimized with respect to active safety and performance. Active camber control is a method that assigns the camber angle of each wheel to generate desired longitudinal and lateral forces and consequently the desired vehicle dynamic behavior. The aim of this study is to explore how the camber angle will affect the tire force generation and how the camber control strategy can be designed so that the safety and performance of a vehicle can be improved. -
Influence of Body Stiffness on Vehicle Dynamics Characteristics In
Influence of Body Stiffness on Vehicle Dynamics Characteristics in Passenger Cars Master's thesis in Automotive Engineering OSKAR DANIELSSON ALEJANDRO GONZALEZ´ COCANA~ Department of Applied Mechanics Division of Vehicle Engineering and Autonomous Systems Vehicle Dynamics group CHALMERS UNIVERSITY OF TECHNOLOGY G¨oteborg, Sweden 2015 Master's thesis 2015:68 MASTER'S THESIS IN AUTOMOTIVE ENGINEERING Influence of Body Stiffness on Vehicle Dynamics Characteristics in Passenger Cars OSKAR DANIELSSON ALEJANDRO GONZALEZ´ COCANA~ Department of Applied Mechanics Division of Vehicle Engineering and Autonomous Systems Vehicle Dynamics group CHALMERS UNIVERSITY OF TECHNOLOGY G¨oteborg, Sweden 2015 Influence of Body Stiffness on Vehicle Dynamics Characteristics in Passenger Cars OSKAR DANIELSSON ALEJANDRO GONZALEZ´ COCANA~ c OSKAR DANIELSSON, ALEJANDRO GONZALEZ´ COCANA,~ 2015 Master's thesis 2015:68 ISSN 1652-8557 Department of Applied Mechanics Division of Vehicle Engineering and Autonomous Systems Vehicle Dynamics group Chalmers University of Technology SE-412 96 G¨oteborg Sweden Telephone: +46 (0)31-772 1000 Cover: Volvo S60 model reinforced with bars for the multibody dynamics simulation tool MSC Adams Chalmers Reproservice G¨oteborg, Sweden 2015 Influence of Body Stiffness on Vehicle Dynamics Characteristics in Passenger Cars Master's thesis in Automotive Engineering OSKAR DANIELSSON ALEJANDRO GONZALEZ´ COCANA~ Department of Applied Mechanics Division of Vehicle Engineering and Autonomous Systems Vehicle Dynamics group Chalmers University of Technology Abstract Automotive industry is a highly competitive market where details play a key role. Detecting, understanding and improving these details are needed steps in order to create sustainable cars capable of giving people a premium driving experience. Body stiffness is one of this important specifications of a passenger car which affects not only weight thus fuel consumption but also handling, steering and ride characteristics of the vehicle. -
Employing Optimization in Cae Vehicle Dynamics
Technical University of Crete School of Production Engineering & Management EMPLOYING OPTIMIZATION IN CAE VEHICLE DYNAMICS Alexandros Leledakis December 2014 ACKNOWLEDGEMENTS This thesis study was performed between March and October 2014 at Volvo Cars in Goteborg of Sweden, where I had the chance to work inside Volvo’s Research and Development Centre (in the Active Safety CAE department). I would like to thank my Volvo Cars supervisor Diomidis Katzourakis, CAE Active Safety Assignment Leader, for his constant guidance during this thesis. He always provided knowledge and ideas during all phases of the thesis; planning, modelling, setup of experiments, etc. It is with immense gratitude that I acknowledge the support and help of my academic supervisor Nikolaos Tsourveloudis, Professor and Dean of the school of Production engineering and management at Technical University of Crete, for his trust and guidance throughout my studies. The MSc thesis of Stavros Angelis and Matthias Tidlund served as-foundation of the current thesis: I would also like to thank Mathias Lidberg, Associate Professor in Vehicle Dynamics, Chalmers University of Technology. Field tests would have been impossible without the help of Per Hesslund, who installed the steering robot in the vehicle for our DLC verification testing session, conducted each test and guided me through the procedure of instrumenting a vehicle and performing a test. I share the credit of my work with Lukas Wikander and Josip Zekic, who helped with the setup of the Vehicle for the steering torque interventions test as well as Henrik Weiefors, from Sentient, for his support regarding the Control EPAS functionality. I would also like to thank Georgios Minos, manager of CAE Active Safety. -
University of Birmingham Multi-Chamber Tire Concept for Low
University of Birmingham Multi-chamber tire concept for low rolling- resistance Aldhufairi, Hamad; Essa, Khamis; Olatunbosun, Oluremi DOI: 10.4271/06-12-02-0009 License: None: All rights reserved Document Version Peer reviewed version Citation for published version (Harvard): Aldhufairi, H, Essa, K & Olatunbosun, O 2019, 'Multi-chamber tire concept for low rolling-resistance', SAE International Journal of Passenger Cars - Mechanical Systems, vol. 12, no. 2, 06-12-02-0009, pp. 111-126. https://doi.org/10.4271/06-12-02-0009 Link to publication on Research at Birmingham portal General rights Unless a licence is specified above, all rights (including copyright and moral rights) in this document are retained by the authors and/or the copyright holders. The express permission of the copyright holder must be obtained for any use of this material other than for purposes permitted by law. •Users may freely distribute the URL that is used to identify this publication. •Users may download and/or print one copy of the publication from the University of Birmingham research portal for the purpose of private study or non-commercial research. •User may use extracts from the document in line with the concept of ‘fair dealing’ under the Copyright, Designs and Patents Act 1988 (?) •Users may not further distribute the material nor use it for the purposes of commercial gain. Where a licence is displayed above, please note the terms and conditions of the licence govern your use of this document. When citing, please reference the published version. Take down policy While the University of Birmingham exercises care and attention in making items available there are rare occasions when an item has been uploaded in error or has been deemed to be commercially or otherwise sensitive. -
Unscented Kalman Filter for Real-Time Vehicle Lateral Tire Forces And
Unscented Kalman filter for real-time vehicle lateral tire forces and sideslip angle estimation Moustapha Doumiati, Alessandro Victorino, Ali Charara and Daniel Lechner Abstract— Knowledge of vehicle dynamic parameters is im- trajectories, and to better vehicle control. Moreover, it makes portant for vehicle control systems that aim to enhance vehicle possible the development of a diagnostic tool for evaluating handling and passenger safety. Unfortunately, some fundamen- the potential risks of accidents related to poor adherence or tal parameters like tire-road forces and sideslip angle are difficult to measure in a car, for both technical and economic dangerous maneuvers. reasons. Therefore, this study presents a dynamic modeling and Vehicle dynamic estimation has been widely discussed in observation method to estimate these variables. The ability to the literature. Several studies have been conducted regarding accurately estimate lateral tire forces and sideslip angle is a crit- the estimation of tire-road forces, sideslip angle and the ical determinant in the performances of many vehicle control friction coefficient. For example, in [9], the authors esti- system and making vehicle’s danger indices. To address system nonlinearities and unmodeled dynamics, an observer derived mate longitudinal and lateral vehicle velocities and evaluate from unscented Kalman filtering technique is proposed. The sideslip angle and lateral forces. In [13] and [5], sideslip estimation process method is based on the dynamic response of angle estimation is discussed in detail. More recently, the a vehicle instrumented with easily-available standard sensors. sum of front and rear lateral forces have been estimated in Performances are tested using an experimental car in real [4] and [6]. -
Annual Report 2015 the Specialist in Demanding Conditions
Annual Report 2015 The specialist in demanding conditions Nokian Tyres is the world’s northern- of competitive advantage: an image of most tyre manufacturer. It promotes and quality based on innovations, state-of- facilitates safe driving in demanding the-art technology, decades of customer conditions. Whether driving through a experience, a strong distributor network winter storm or heavy summer rain, and logistical expertise. our tyres offer reliability, performance, Central Europe and North America are and peace of mind. We are the only also important market areas in which we Drive tyre manufacturer to focus on products are seeking profitable growth. for demanding conditions and customer We mainly sell our products in requirements. the aftermarket. Nokian Tyres group Innovative tyres for passenger cars, includes the Vianor tyre retail chain with trucks, and heavy machinery are mainly wholesale and retail business in Nokian safely! marketed in areas with snow, forests and Tyres’ primary markets. Nokian Tyres has challenging driving conditions caused by factories in Finland and Russia. In 2005– varying seasons. We develop our products 2015, we invested more than EUR 1 billion with the goals of sustainable safety and in our factories, whose productivity and Our unique expertise creates the safest environmental friendliness throughout the product quality are top-notch in the premium products and services for the product’s entire life cycle. industry. Nokian Hakkapeliitta has been the In 2015, the company’s Net sales everyday life. As a pioneer in the tyre leading brand of winter tyres for more were approximately EUR 1,4 billion, and industry, we want to be the best in than 80 years. -
Tire - Wikipedia, the Free Encyclopedia
Tire - Wikipedia, the free encyclopedia http://en.wikipedia.org/wiki/Tire Tire From Wikipedia, the free encyclopedia A tire (or tyre ) is a ring-shaped covering that fits around a wheel's rim to protect it and enable better vehicle performance. Most tires, such as those for automobiles and bicycles, provide traction between the vehicle and the road while providing a flexible cushion that absorbs shock. The materials of modern pneumatic tires are synthetic rubber, natural rubber, fabric and wire, along with carbon black and other chemical compounds. They consist of a tread and a body. The tread provides traction while the body provides containment for a quantity of compressed air. Before rubber was developed, the first versions of tires were simply bands of metal that fitted around wooden wheels to prevent wear and tear. Early rubber tires were solid (not pneumatic). Today, the majority of tires are pneumatic inflatable structures, comprising a doughnut-shaped body of cords and wires encased in rubber and generally filled with compressed air to form an inflatable cushion. Pneumatic tires are used on many types of vehicles, including cars, bicycles, motorcycles, trucks, earthmovers, and aircraft. Metal tires are still used on locomotives and railcars, and solid rubber (or Stacked and standing car tires other polymer) tires are still used in various non-automotive applications, such as some casters, carts, lawnmowers, and wheelbarrows. Contents 1 Etymology and spelling 2 History 3 Manufacturing 4 Components 5 Associated components 6 Construction types 7 Specifications 8 Performance characteristics 9 Markings 10 Vehicle applications 11 Sound and vibration characteristics 12 Regulatory bodies 13 Safety 14 Asymmetric tire 15 Other uses 16 See also 17 References 18 External links Etymology and spelling Historically, the proper spelling is "tire" and is of French origin, coming from the word tirer, to pull. -
150/5220-10C AIRCRAFT RESCUE and FIRE FIGHTING VEHICLES Initiated By: AAS-100 Change
Advisory U.S. Department of Transportation Federal Aviation Circular Administration Subject: GUIDE SPECIFICATION FOR WATER/FOAM Date: 2/18/02 AC No: 150/5220-10C AIRCRAFT RESCUE AND FIRE FIGHTING VEHICLES Initiated by: AAS-100 Change: 1. PURPOSE. This advisory circular (AC) contains receiving Federal grant-in-aid assistance, the use of performance standards, specifications, and these standards is mandatory. At certificated airports, recommendations for the design, construction, and the use of equipment meeting these standards satisfies testing of a family of aircraft rescue and fire fighting the requirements of Title 14 Code of Federal (ARFF) vehicles. Regulations (CFR) Part 139, Certification and Operations, Land Airports Serving Certain Air Carriers, 2. CANCELLATION. AC 150/5220-10B, Guide Subpart D-Operations, Subparagraph 139.317, Specification for Water/Foam Aircraft Rescue and Fire “Aircraft Rescue and Fire Fighting: Equipment and Fighting Vehicles, dated October 20, 1997, is canceled. Agents.” Features or design details not listed as required or optional in this document are not 3. APPLICATION. The Federal Aviation considered necessary unless a justification acceptable to Administration (FAA) recommends the use of the the FAA is provided. guidance in this publication for the preparation of ARFF vehicle specifications. For airport projects DAVID L. BENNETT Director, Office of Airport Safety and Standards CANCELLED 1 CANCELLED 2/18/02 AC 150/5220-10C CONTENTS CHAPTER 1. INTRODUCTION ........................................................................................................................ -
Development of a Scale Vehicle Dynamics Test Bed
University of Windsor Scholarship at UWindsor Electronic Theses and Dissertations Theses, Dissertations, and Major Papers 2010 Development of a Scale Vehicle Dynamics Test Bed Andrew Liburdi University of Windsor Follow this and additional works at: https://scholar.uwindsor.ca/etd Recommended Citation Liburdi, Andrew, "Development of a Scale Vehicle Dynamics Test Bed" (2010). Electronic Theses and Dissertations. 195. https://scholar.uwindsor.ca/etd/195 This online database contains the full-text of PhD dissertations and Masters’ theses of University of Windsor students from 1954 forward. These documents are made available for personal study and research purposes only, in accordance with the Canadian Copyright Act and the Creative Commons license—CC BY-NC-ND (Attribution, Non-Commercial, No Derivative Works). Under this license, works must always be attributed to the copyright holder (original author), cannot be used for any commercial purposes, and may not be altered. Any other use would require the permission of the copyright holder. Students may inquire about withdrawing their dissertation and/or thesis from this database. For additional inquiries, please contact the repository administrator via email ([email protected]) or by telephone at 519-253-3000ext. 3208. Development of a Scale Vehicle Dynamics Test Bed by Andrew Liburdi A Thesis Submitted to the Faculty of Graduate Studies through Mechanical, Automotive, and Materials Engineering in Partial Fulfillment of the Requirements for the Degree of Master of Applied Science at the University of Windsor Windsor, Ontario, Canada 2010 © 2010 Andrew Liburdi Development of a Scale Vehicle Dynamics Test Bed by Andrew Liburdi APPROVED BY: ______________________________________________ Dr. Xiaohong, Xu, Outside Program Reader Department of Civil and Environmental Engineering ______________________________________________ Dr. -
Chassis Newsletter
The Mark Ortiz Automotive CHASSIS N EW SLETTER PRESENTED FREE OF CHARGE AS A SERVICE TO THE MOTORSPORTS COMMUNITY September November 2004 WELCOME Mark Ortiz Automotive is a chassis consulting service primarily serving oval track and road racers. This newsletter is a free service intended to benefit racers and enthusiasts by offering useful insights into chassis engineering and answers to questions. Readers may mail questions to: 155 Wankel Dr., Kannapolis, NC 28083-8200; submit questions by phone at 704-933-8876; or submit questions by e-mail to: [email protected]. Readers are invited to subscribe to this newsletter by e-mail. Just e-mail me and request to be added to the list. ERRATA AND ADDENDA Thank you to readers who have pointed out some detail discrepancies in my recent columns in Racecar Engineering, which are drawn from this newsletter. In the April newsletter I originally stated that for least bearing loads with an outboard brake, the caliper should be somewhere in the upper rear quadrant of the disc. Shortly after sending out that issue, I sent out a correction saying that should be the lower rear quadrant. This correction was supposed to be incorporated when the material was published in the magazine, but unfortunately the original version was what ran (July 2004 issue). So a correction is in order on this point, for those who read me in the magazine. In my October 2004 column, drawn from the June 2004 newsletter, there was some disagreement between what I said about the Williams Formula 1 suspension and the second picture that ran in the magazine, showing the suspension from above and behind.