(12) Patent Application Publication (10) Pub. No.: US 2014/0290802 A1 Morita Et Al
Total Page:16
File Type:pdf, Size:1020Kb
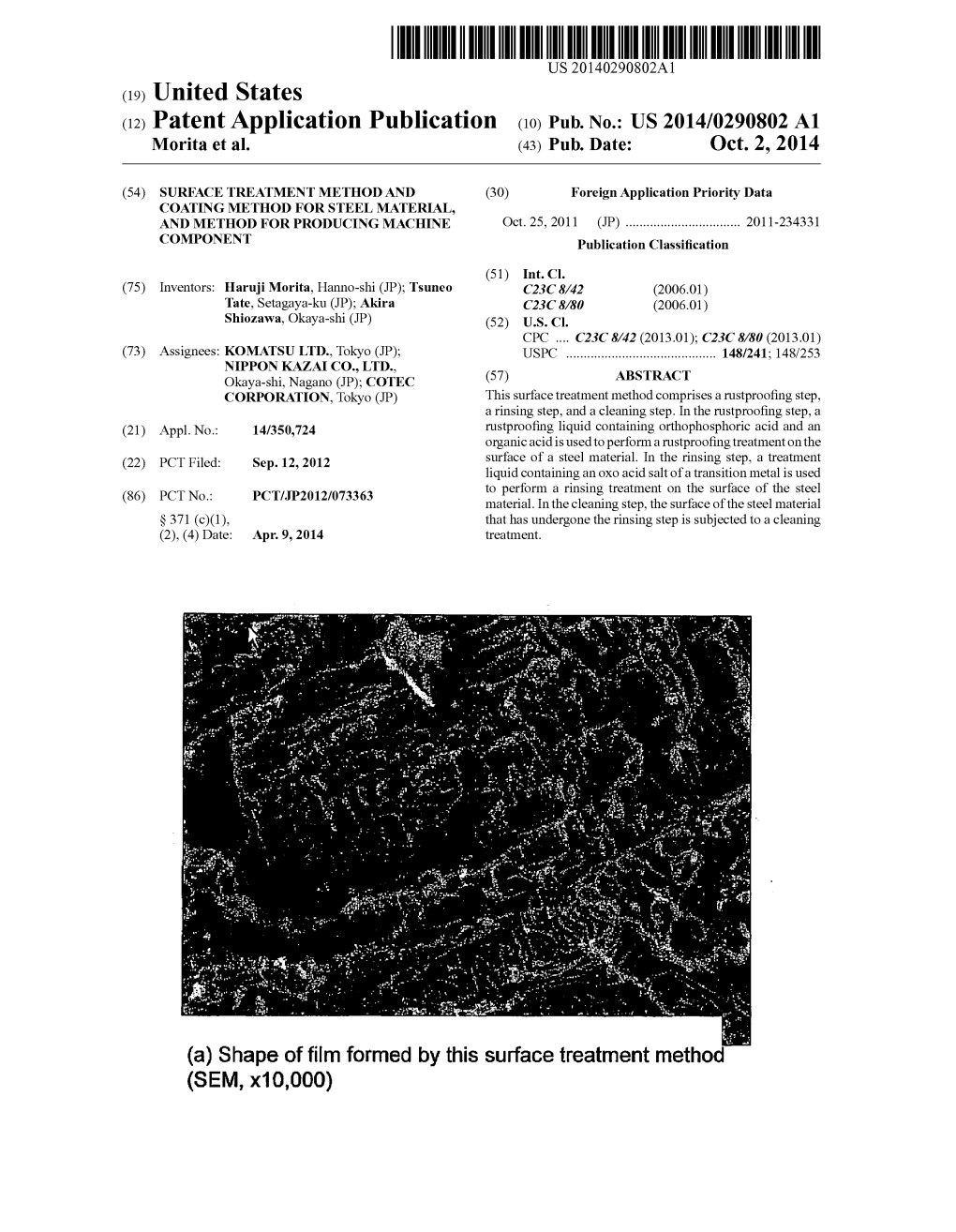
Load more
Recommended publications
-
Ahead of the Rest
2016 2017 Ahead of the Rest Welcome to our proud “Family of Products” Merging Finger Lakes, Castle, Econo, and Echo into one catalog displays www.CastleOctaServices.com America’s broadest line of professional products. Decades of research and development have helped us create a deep, multi-dimensional line. Five reasons why the Castle Group is your best value: PROFITS 1 Since 1967 our trademarked packaging and patented formulas have given exciting new profit opportunities. SUPPORT 2 Service menus, training seminars, POP displays, radio and TV tags, and apparel. FACTORY DIRECT 3 Strategically placed satellite warehouses provide service with no freight and no minimum. Battery HI-TECH Service 4 Product Technical Info is constantly updated. We help you satisfy your “User Right to Know” responsibilities! SAFETY 5 We help you comply with government regulations. The Castle Racing Team started in the early 1970’s with the inception of the Castle Dragon Fire Dragster. Over the years Castle cars and crews have been spotted at drag strips, dirt tracks, and asphalt circuits: 1980’s: J.D. McDuffie uses Castle in his shop and Castle on his #70 Pontiac in the Winston Cup Series. 2002 – 05: Castle unveils its “Racing for Clean Air” Campaign, with Andy Santerre as Racing Team Captain. Andy was NASCAR Busch North Series (BNS) Rookie-of-the-Year in 1993 and NASCAR Busch Series Rookie-of-the-Year in 1998. Santerre would go on to win four straight BNS Points Championships (2002-2005). 2006: Andy retires from racing to concentrate on building race cars and tutoring young drivers as Andy Santerre Motorsports (ASM). -
Corrosion Resistance of Hot-Dip Zn-6%Al-3%Mg Alloy Coated Steel Sheet Used in Automotive Parts
Corrosion resistance of hot-dip Zn-6%Al-3%Mg alloy coated steel sheet used in automotive parts Masaaki Uranaka, Takeshi Shimizu – Nishhin Steel, Osaka, Japan ABSTRACT RIASSUNTO For the purpose of applying hot-dip Zn-6%Al-3%Mg alloy Con lo scopo di applicare il rivestimento “Zn-Al-Mg” sui coated steel sheet (“Zn-Al-Mg”) to automotive parts, we laminati di acciaio per componenti di autoveicoli, mediante compared and investigated the corrosion resistance of Zn- “immersione a caldo” nel bagno della lega Zn-6%Al- Al-Mg and ordinary materials treated using a conventional 3Mg, gli Autori hanno studiato la resistenza a corrosione rustproofing method (“post-Zn-coated material”) exposed del rivestimento “Zn-Al-Mg” confrontandola con quella to accelerated corrosion test environments. We also dei materiali comuni trattati con metodi convenzionali di collected automotive parts made from Zn-Al-Mg from protezione alla corrosione (rivestimento di Zn) esposti vehicles that had been driven for three to five years in a test ambientali di corrosione accelerata. Sono state Canada to examine corrosion resistance capabilities when anche prelevate parti ricoperte con Zn-Al-Mg da veicoli exposed to actual vehicle environment conditions. We guidati da 3 a 5 anni in Canada, con lo scopo di valutare found that Zn-Al-Mg exhibited better corrosion resistance le prestazioni di resistenza alla corrosione quando sono than post-Zn-coated material, even at portions where the esposte alle condizioni ambientali di esercizio. Gli autori steel substrate was exposed (along cut edges and in bent hanno trovato che il rivestimento Zn-Al-Mg mostra migliore or spot-welded portions). -
FED-STD-297E T SUPERSEDING FED-STD-297D October 1
Downloaded from http://www.everyspec.com FED-STD-297E t SUPERSEDING FED-STD-297D October 1. 1985 FEDERAL STANDARD RUSTPROOFINGOF COMMERCIAL (NONTACZICAL)VEHICLES ~. Approved fo~ pu~l.icrelease: distribution is unlimited. ,,- -~ -. Downloaded from http://www.everyspec.com FED-STB297E GENERAL SERVICES AIMINISTRATION Washington. D- C. 20301 Rustproofing of Commercial (Nontactical)Vehicles. 1. This Federal Standard is approved by the Commissioner, Federal Supply Service. General Services Administration. for the use of all Federal Agencies. 2. Beneficial comments (recommendations?additions. deletions) ~d my pertinent data which may be of use in improving this document should be addressed to: US Army Tank-Automotive Conmand, A’I’TN:AMSTA-UED, Warren. MI 48397-5000. by using the self-addressed Standardization Document Improvement proposal (.DD~orm 1426) appearti at the end ‘f ‘his ‘ocment ‘r W letter- ii Downloaded from http://www.everyspec.com FRD=STD-Z9’7E FOREWRD This standard establishes requirements for rustproofing of commercial. nontactical, self-propelled and towed vehicles procured for Government use. ------ iii Downloaded from http://www.everyspec.com FED-STW297E Paragraph 1.. SCOPE -------------- ------- 1 2. REFERENCEDDOCUMENTS . ---- ------- 2 2.1 Issues of documents . ---’ ------ 2 2.1.1 Government documents . - - - - . - - - 2 2.1.2 Other Government documents . - . - - -’- 2 3. DEFINITIONS ----------- ------ 3 4. GENERAL REQUIREMENTS .’----- ------- 4 4.1 I?ustproofing---------- ------- 4 .4.2 Identification -------- -------- 4 4.3 Materials ---------- --” ------ 4 4.4 Instructions . ---- -------- 4-5 4.5 Contractor inspection system . - . 5 4.6 Workmanship ---------- ------- 5 5. DETAILED ------------ ------- 5 5.1 Application equipment - . - . - - . - - - - 5 5.1-1 Spray gun ---------- -------- 5 5.1.2 Wands ------------- ------” 6 5.1.3 Spray nozzles . .. ---- -------- 6 5.2 Application procedure . -
Selder & Company Ab
Page 1 of 3 SELDER & COMPANY AB WORK MANUAL FOR RUSTPROOFING OIL www.selder.com 23.3.2021 The work differs significantly from that with other rustproofing oils. READ CAREFULLY FOR A GOOD RESULT. TABLE OF CONTENTS CLEAN, NON-CORRODED METAL SURFACES TO BE PAINTED .............................................................. 1 CORRODED (RUSTED) METAL SURFACES, TREATMENT WITH OIL AT ROOM TEMPERATURE ................ 1 LINSEED OIL BURNING OF IRON AND STEEL .......................................................................................... 2 MAINTENANCE ....................................................................................................................................... 2 GENERAL................................................................................................................................................. 2 WORKER PROTECTION ........................................................................................................................... 3 SAFETY ..................................................................................................................................................... 3 CLEAN, NON-CORRODED METAL SURFACES TO BE PAINTED are automatically rustproofed by painting with Selder's linseed oil paints. Half of them is a binder which has the same composition and properties as RUSTPROOFING OIL. CORRODED (RUSTED) METAL SURFACES, TREATMENT WITH OIL AT ROOM TEMPERATURE Remove loose rust, paint residue, grease, lichens, algae, etc. The surface can be burned off with a blow torch, -
Circular of the Bureau of Standards No. 80: Protective Metallic Coatings For
DEPARTMENT OF COMMERCE Circular Bureau of Standards protective metallic coatings for the RUSTPROOFING OF IRON AND STEEL DEPARTMENT OF COMMERCE Circular OF THE Bureau of Standards S. W. STRATTON, Director No. 80 PROTECTIVE METALLIC COATINGS FOR THE RUSTPROOFING OF IRON AND STEEL ISSUED OCTOBER 4, 1919 PRICE, 10 CENTS Sold only by the Superintendent of Documents, Government Printing Office Washington, D. C. WASHINGTON GOVERNMENT PRINTING OFFICE 1919 ) 1 PROTECTIVE METALLIC COATINGS FOR THE RUSTPROOFING OF IRON AND STEEL CONTENTS Page I. Introduction 4 1. Nature of corrosion 4 2 . Principles underlying methods of prevention of corrosion 4 II. Types of coatings and methods of application 6 1. Metallic coatings 6 () Zinc 6 Hot dipping, sherardizing, plating, etc 6 Comparison of coatings 6 () Aluminum 7 (c) Soft, fusible metals 8 Tin, lead, and their alloys 8 (d) Hard metals 8 Copper, nickel, cobalt, and brass 8 2. Oxides and salts of iron 9 (a) Oxides 9 Bower-Barff type 9 Heating with oil, etc 10 ** “ Etching (“ Browning, Bluing, ” etc.) 10 Niter bath n Temper colors 11 Hot oxidizing solutions 1 Miscellaneous n (&) Salts 12 Parker or Coslett process 12 III. Microstructure 12 1. Theoretical microstructure of zinc coatings 12 2. Variations in microstructure of commercial coatings 14 (a) Hot-dipped material 14 ( b ) Sherardized coatings 16 (c) Sprayed coatings 16 ( d Plated zinc coatings 17 3. Significance of structure of coatings 18 IV. Preparation of the surface before coating, and accompanying effects upon the mechanical properties of the steel 20 V. Methods of testing coatings 22 1. Description of methods 22 () Stripping tests 23 () Salt spray 24 2. -
Corrosion Protection Textbook
Corrosion Protection Textbook Version:3.3 ©2001-2014Inter-IndustryConferenceOnAutoCollisionRepair CPS01-STMAN1-E Thispageisintentionallyleftblank. Textbook CorrosionProtection Contents Introduction..............................................................................................................................7 ObligationsToTheCustomerAndLiability.......................................................................... 7 Module1-CorrosionOriginsAndPrevention.......................................................................13 CausesOfCorrosion...........................................................................................................13 OEMCorrosionProtection..................................................................................................14 PreventingCorrosionDuringRepairs..................................................................................19 ModuleWrap-Up............................................................................................................... 26 Module2-CorrosionProtectionDuringRepairs................................................................... 29 Cleaning..............................................................................................................................29 PartPreparations................................................................................................................. 31 JoiningSurfaces.................................................................................................................. 33 Primers................................................................................................................................36 -
Letter Circular 192: Corrosion Resistance of Iron and Steel
• - - Letter HWG : MGL : LTQ DEPARTMENT OF COMMERCE " " ' \ BDREAU- -Op’S OTfDARDS Circular : •..- ~ ™ • 1&2 ’ ' • ' v • 7 • April 1336 ' • v ; yc-^s. ' COFRQSIQN- RESISTANCE ~CF "IRON AND STEEL . ; : • • •. V ; -a; . The /Lett-er- C.iTC.uliars are designed to answer .specific in- ; quiries and at the same.; t irae- to-'obylate .the necessity "for pre^ paratlon.-of a large number. of letters- on. .the same, subject There Is" no guarantee- it hat .the. 'Information .given In- the Letter r Circulars- ls , correct except as of .the date of issue,. - ilat-erlal of a permanent value appears in- the printed publications of the-, ^ -j ;.- • Bureah. r f 1 r:- 5 r Iv-rmc v. -. Letter. Circulars are not' available sin' the Government Print- ing Office, and the supply at the Bureau of -Standards Is- -limited Many inquiries' are- received- by- this. Bureau -in (regard to the resistance to corrosion of- ."cas.t iron, and of . steel, wrought iron, commercially pure-/ open-hearth iron. 'and copper-bearing -. iron or* steel in sheet - -pipe;,; wir.e-;..;andrsther forms both bare , : . and zinc : coat ed dr otherwise, trust' propled-t, : : Some inquirers request opinions on the suitability of specif - in makes or brands of these -materials , for specific uses. "It -is not the policy .of the -.Bur eau to recommend or. -de- cry specific mates or brands .of any article; Its .tests and. investi gallons deal with ..types of material, not- with, the merits or demerits of a .particular .maker* s product. ;--Thls . Letter - Circular is prepared to put those making such inquiries on types of material in touch with -published data -and opinions on the 'subject. -
Reduction of Cavitation Damage by Surface Treatment
UNIVERSITY OF MINNESOTA ST. ANTHONY FALLS HYDRAULIC LABORATORY Project Report No. 81 Reduction of Cavitation Damage by Surface Treatment by JOHN F. RIPKEN Distribution 01 this Document is Unlimited Prepared for DAVID TAYLOR MODEL BASIN Department of the Navy Washington, D.C. under Bureau of Ships General Hydromechanics Research Program S-R009-01-01 Office of Naval Research Contract Nonr 710(64) July 1966 Minneapolis, Minnesota Reproduction in whole or in part is permitted for any purpose of the United States Government ~~-~~~~~~~~~~~~~~~~~~~~~~~~----------- ------- -------- --- , .(. I ' ABSTRACT It was rationalized, with limited supporting evidence, that 1 I ~. I most damage due to cavitation stems from cavities which are the consequence of outgassing nuclei growing from fissures in a body's surface. To minimize this damage, it was proposed that body surfaces be treated to reduce the number and activity of these surface faults. Vibratory cavitation damage tests of specimens treated to seal, neutralize, or compress the test surface indicated that these protective measures were inadequate for the severe conditions of a vibratory test. Light shot peening of a work hardening stainless steel prior to cavitation exposure substantially reduced the normal rate of cavitation erosion. i I' < I iii ---------------------------------- ------------ CONTENTS Page Abstract • • • • • • • • II " ,. II ,. • • 'iI'.''''''''·''·- iii List of Illustrations • • • • • ,., .. ", .... "" vii I. INTRODUCTION • • , •• , ••••• ".'.11.·,."." 1 II. THE OUTGASSING OF METALLIC SURFACES AND THE RELATION TO CAVITATION . ,. ,. ,. ,. ,. , • , ,. ,. • ,. ,. , ,. • • .. , • II • • 2 III. SURFACE TREATMENT FOR SUPPRESSION OF OUTGASSING • ,. ,. ,. ; II .. 9 A. General Considerations •• • • • • • • • • • • • • • 9 B. Applied Non-Metallic Films ••••• • • • • • • 10 C. Chemical Treatment of Metallic Surfaces • • • • • 11 D. Physical Treatment of Metallic Surfaces • • -. • • 11 E. Applied Metallic Coatings of Metallic Substrate • 13 IV. -
A Guide to Corrosion Protection
An analysis of corrosion- A Guide To Corrosion related issues for passenger car and light Protection truck underbody structural components. Auto/Steel Partnership A GUIDE TO CORROSION PROTECTION For Passenger Car and Light Truck Underbody Structural Components Prepared by Light Truck Frame Project Team Auto/Steel Partnership 2000 Town Center, Suite 320 Southfield, Michigan 48075-1123 1999 The following companies are members of the Auto/Steel Partnership: AK Steel Corporation Bethlehem Steel Corporation DaimlerChrysler Corporation Dofasco Inc. Ford Motor Company General Motors Corporation Ispat Inland Inc. LTV Steel Company National Steel Corporation Rouge Steel Company Stelco Inc. U.S. Steel Group, a Unit of USX Corporation WCI Steel, Inc. Weirton Steel Corporation This publication was prepared by: Auto/Steel Partnership Light Truck Frame Project Team 2000 Town Center, Suite 320 Southfield, Michigan, 48075-1123 First Edition, December 1999 This publication is for general information only. The material contained herein should not be used without first securing competent advice with respect to its suitability for any given application. This publication is not intended as a representation or warranty on the part of Auto/Steel Partnership - or any other person named herein - that the information is suitable for any general or particular use or freedom from infringement of any patent or patents. Anyone making use of the information assumes all liability arising from such use. For more information or additional copies of this publication, please contact the Auto/Steel Partnership, 2000 Town Center, Suite 320, Southfield, MI 48075-1123 or phone: 248-945-7777, fax: 248-356-8511, web site: www.a-sp.org Copyright 1999 Auto/Steel Partnership. -
Alsheettm Alsheet
www.nipponsteel.com Steel Sheet ALSHEET TM Hot-dip aluminum-coated steel sheets ALSHEETTM 2-6-1 Marunouchi, Chiyoda-ku,Tokyo 100-8071 Japan U034en_02_202004pU034en_02_202004f Tel: +81-3-6867-4111 © 2019, 2020 NIPPON STEEL CORPORATION Introduction Manufacturing Process Overall manufacturing Blast furnace TM process ALSHEET is a cold-rolled steel that has been hot-dipped in an aluminum/silicon alloy. It Acid Pickling offers the attractive surface of processed steel sheet that simultaneously affords some of Converter the features of aluminum, such as resistance to corrosion, attractive appearance, coupled Cold Rolling with superior heat resistance and heat reflection, cold-rolled steel’s mechanical attributes Continuous Casting and other physical characteristics. Hot-dip We have been manufacturing hot-dip aluminum-coated steel sheets under the name Hot Rolling aluminum plating “ALSHEETTM” since July 1961, and it has been widely adopted thanks to its superior features, such as for vehicle mufflers (silencers), toasters, and gas cookers. In recent years, there have been calls for the development of materials to succeed Cooling equipment stainless steel sheets to cope with exhaust gas restrictions, and inexpensive materials Post-Processing TM in order to cut costs, and accordingly the demand for ALSHEET with improved heat Hot-dip Aluminum Plating The quality and shape of the aluminum- resistance performance has grown in these fields as well. Process coated sheet are improved by the We have recently developed further improvements to our products in terms of heat <in order of process> skin pass and tension leveler, and post-processing is applied to the add resistance, strength at high temperature, colorfastness, and corrosion resistance, and corrosion resistance and enhance paint have extended our product lineup to meet the ever-diversifying needs of today’s market. -
Notice of Solicitation Gs-2020-4 for the Furnishing
NOTICE OF SOLICITATION GS-2020-4 FOR THE FURNISHING AND DELIVERY OF One (1) 4-Wheel Drive 18,000 lb GVWR Cab, Utility Body and Accessories; AND/OR One (1) 37,600 lb GVWR Cab and Chassis with (8) Cubic Yard Dump Body; AND/OR Three (3) 16K Tilt Deck Equipment Trailers; AND/OR One (1) Rubber Track Open Cab Excavator January 2020 CONTENTS NOTICE OF SOLICITATION ....................................................................................................... 1 OFFER ............................................................................................................................................ 2 SCOPE OF WORK AND AWARD ............................................................................................... 7 CERTIFICATION OF COMPLIANCE FOR FINAL PAYMENT ............................................. 15 SPECIFICATIONS ....................................................................................................................... 16 GENERAL TERMS AND CONDITIONS FOR GOODS AND SERVICES ............................. 26 NOTICE OF SOLICITATION SEALED OFFERS will be received up to and publicly opened at 2:00 p.m. (Hawaiʻi Standard Time) on Thursday, February 06, 2020, at the Department of Water Office of the County of Kauaʻi (“Department of Water” or “Department”), 4398 Pua Loke Street, Līhuʻe, Kauaʻi, Hawaiʻi, for the furnishing and delivery of GS-2020-4 One (1) 4-Wheel Drive 18,000 lb GVWR Cab, Utility Body and Accessories; AND/OR One (1) 37,600 lb GVWR Cab and Chassis with (8) Cubic Yard Dump Body; AND/OR Three (3) -
Alphabetical List of Goods A
ALPHABETICAL LIST OF GOODS A SERIAL SERIAL BASIC SERIAL SERIAL BASIC Cl. INDICATION OF GOODS Cl. INDICATION OF GOODS N° (E) N° (F) N° N° (E) N° (F) N° 09 A 0001 AbacusesA B 0709 090627 01 A 0047 Acidulated water for recharging E 0027 010251 10 A 0002 Abdominal belts A 0004 100001 batteries 10 A 0003 Abdominal corsets C 1303 100003 05 A 0048 Aconitine A 0080 050002 10 A 0004 Abdominal pads P 0294 100098 09 A 0049 Acoustic [sound] alarms A 0855 090014 08 A 0005 Abrading instruments [hand A 0008 080002 09 A 0050 Acoustic conduits C 1134 090015 instruments] 09 A 0051 Acoustic couplers C 1378 090593 03 A 0006 Abrasive cloth T 0315 030160 17 A 0052 Acrylic resins [semi-finished A 0089 170002 21 A 0007 Abrasive pads for kitchen T 0085 210259 products] purposes 01 A 0053 Acrylic resins, unprocessed A 0090 010461 03 A 0008 Abrasive paper P 0119 030166 01 A 0054 Actinium A 0092 010018 01 A 0009 Abrasives (Auxiliary fluids for F 0307 010004 09 A 0055 Actinometers A 0093 090018 use with –) 01 A 0056 Activated carbons C 0492 010025 05 A 0010 Abrasives (Dental –) A 0012 050001 10 A 0057 Acupuncture needles A 0201 100199 03 A 0011 Abrasives * A 0011 030165 09 A 0058 Adding machines A 0101 090019 05 A 0012 Absorbent cotton H 0196 050176 01 A 0059 Additives (Detergent –) to A 0097 010021 34 A 0013 Absorbent paper for tobacco P 0085 340011 gasoline [petrol] pipes 05 A 0060 Additives to fodder for medical A 0099 050293 05 A 0014 Absorbent wadding H 0196 050176 purposes 01 A 0015 Absorbing oil (Synthetic A 0015 010620 31 A 0061 Additives to fodder, not for