W Oltoria Di Un Uo Non Man at Taman Antonio La D
Total Page:16
File Type:pdf, Size:1020Kb
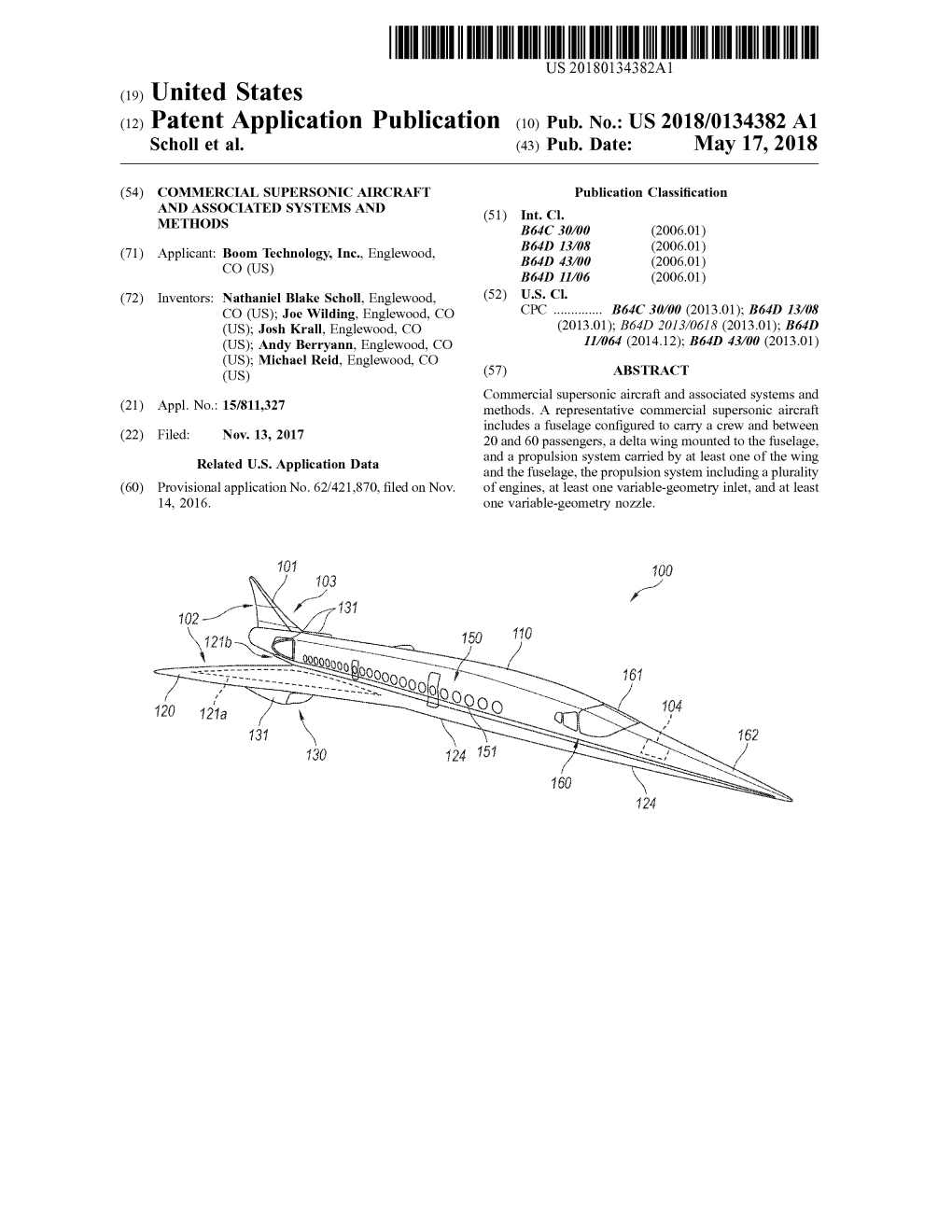
Load more
Recommended publications
-
Concorde Is a Museum Piece, but the Allure of Speed Could Spell Success
CIVIL SUPERSONIC Concorde is a museum piece, but the allure Aerion continues to be the most enduring player, of speed could spell success for one or more and the company’s AS2 design now has three of these projects. engines (originally two), the involvement of Air- bus and an agreement (loose and non-exclusive, by Nigel Moll but signed) with GE Aviation to explore the supply Fourteen years have passed since British Airways of those engines. Spike Aerospace expects to fly a and Air France retired their 13 Concordes, and for subsonic scale model of the design for the S-512 the first time in the history of human flight, air trav- Mach 1.5 business jet this summer, to explore low- elers have had to settle for flying more slowly than speed handling, followed by a manned two-thirds- they used to. But now, more so than at any time scale supersonic demonstrator “one-and-a-half to since Concorde’s thunderous Olympus afterburn- two years from now.” Boom Technology is working ing turbojets fell silent, there are multiple indi- on a 55-seat Mach 2.2 airliner that it plans also to cations of a supersonic revival, and the activity offer as a private SSBJ. NASA and Lockheed Martin appears to be more advanced in the field of busi- are encouraged by their research into reducing the ness jets than in the airliner sector. severity of sonic booms on the surface of the planet. www.ainonline.com © 2017 AIN Publications. All Rights Reserved. For Reprints go to Shaping the boom create what is called an N-wave sonic boom: if The sonic boom produced by a supersonic air- you plot the pressure distribution that you mea- craft has long shaped regulations that prohibit sure on the ground, it looks like the letter N. -
S U Personics + Clim a Te
MOON LANDING 36 HYPERSONICS 14 SPACE ECONOMY 30 What Apollo can teach Artemis Predicting overheating A new role for space-faring governments ICS + ON CL RS IM E A P T U E S Mach 1 passenger jets could exacerbate aviation’s carbon footprint. The search for solutions is underway. PAGE 22 REPORTER’S PICKS PAGE 18 Your IAC preview OCTOBER 2019 | A publication of the American Institute of Aeronautics and Astronautics | aerospaceamerica.aiaa.org SECURE YOUR AIAA CORPORATE MEMBERSHIP TODAY! Take advantage of being a Corporate Member: › Industry recognition › Transformative conversations › Automatically elevate your staff to AIAA Senior Members › Annual forum registration allotment and discounted registrations › Recruit students and young professionals at Meet the Employer events › Plus so much more! LEARN MORE: aiaa.org/corporatemembership CONTACT US TO TODAY TO LEARN WHAT AIAA CAN DO FOR YOU! Chris Semon • Vickie Singer • Paul doCarmo 703.264.7510 | [email protected] FEATURES | October 2019 MORE AT aerospaceamerica.aiaa.org 18 30 36 22 IAC preview Seismic shift in Apollo’s lessons satellite market for Artemis Supersonic transports Our staff reporter describes the Space-faring Experience gleaned International and climate change governments are during the 20th- Astronautical taking a new role century moon program The industry has creative ideas for Congress events she in the satellite can help sustain addressing the warming infl uence of doesn’t want to miss. market as startups today’s momentum proposed Mach 1 passenger jets. and established toward a 2024 lunar By Cat Hofacker companies vie for landing. By Adam Hadhazy investors. By John M. Logsdon By Debra Werner On the cover: Photo illustration aerospaceamerica.aiaa.org | OCTOBER 2019 | 1 RENO, NEVADA 15–19 June 2020 | Reno-Sparks Convention Center CALL FOR PAPERS The AIAA AVIATION Forum is the only global event that covers the entire integrated spectrum of aviation business, research, development, and technology. -
Global Challenges
6–10 JANUARY 2020 | ORLANDO, FL DRIVING AEROSPACE SOLUTIONS FOR GLOBAL CHALLENGES What’s going on in Page 25 aiaa.org/scitech #aiaaSciTech From the forefront of innovation to the frontlines of the mission. No matter the mission, Lockheed Martin uses a proven approach: engineer with purpose, innovate with passion and define the future. We take time to understand our customer’s challenges and provide solutions that help them keep the world secure. Their mission defines our purpose. Learn more at lockheedmartin.com. © 2019 Lockheed Martin Corporation FG19-23960_002 AIAA sponsorship.indd 1 12/10/19 3:20 PM Live: n/a Trim: H: 8.5in W: 11in Job Number: FG18-23208_002 Bleed: .25 all around Designer: Kevin Gray Publication: AIAA Sponsorship Gutter: None Communicator: Ryan Alford Visual: Male and female in front of screens. Resolution: 300 DPI Due Date: 12/10/19 Country: USA Density: 300 Color Space: CMYK NETWORK NAME: SciTech ON-SITE Wi-Fi From the forefront of innovation › PASSWORD: 2020scitech to the frontlines of the mission. CONTENTS Technical Program Committee .................................................................4 Welcome ........................................................................................................5 Sponsors and Supporters ..........................................................................7 Forum Overview ...........................................................................................8 Pre-Forum Activities ................................................................................. -
Human Perception of Sonic Booms from Supersonic Aircraft
Human Perception of Sonic Booms from Supersonic Aircraft Alexandra Loubeau Advances in human response research will help pave the way for a new Address: era of commercial supersonic flight. Structural Acoustics Branch NASA Langley Research Center Introduction MS 463 The lure of faster speeds and reduced travel time for commercial flights may Hampton, Virginia 23681 come to fruition soon with advances in low-boom technology. The Concorde USA “was a technological marvel that astounded the world with its beauty of design and speed, halving passenger flight times to distant destinations” (Rogers and Email: Maglieri, 2015). Its last flight on October 24, 2003, ended the first era in supersonic [email protected] commercial travel. Although supersonic flight of the Concorde resulted in loud sonic booms, decades of low-boom research have demonstrated the feasibility of adapting the aerodynamic shape and tailoring the off-body pressure distribution Juliet Page from a supersonic vehicle to decrease or control the sonic boom, a technique Address: known as sonic boom shaping. Sparrow (2006) provides a snapshot of the history Environmental Measurement of sonic boom minimization. With this new technology, research of the human and Modeling response to sonic boom noise is being conducted to better understand the factors Volpe National Transportation that contribute to annoyance from sonic boom sounds so that they can be “shaped” Systems Center for minimal disturbance, thereby potentially resulting in a new era in supersonic US Department of Transportation commercial travel. Indeed, recent advances in understanding and predicting 55 Broadway human perception of sonic booms have coincided with renewed interest from Cambridge, Massachusetts 02142 industry in pursuing development of a new generation of quiet commercial USA supersonic aircraft and have also led to the new lexicon “sonic thump” that reflects their quieter sounds (explained in Unique Qualities of Sonic Booms). -
Überschall-Passagierjets – Vergangenheit Und Zukunft Andreas Spaeth, Luftfahrtjournalist
Überschall-Passagierjets Vergangenheit und Zukunft Andreas Spaeth, Luftfahrtjournalist, Hamburg 2021 https://doi.org/10.5281/zenodo.4567392 Verein Deutscher Ingenieure Hamburger Bezirksverein e.V. Arbeitskreis Luft- und Raumfahrt Hamburg Aerospace Lecture Series Hamburger Luft- und Raumfahrtvorträge Der VDI lädt ein zum Vortrag in Kooperation mit DGLR, RAeS, ZAL und HAW Hamburg Überschall-Passagierjets – Vergangenheit und Zukunft Andreas Spaeth, Luftfahrtjournalist Anmledung erforderlich! Datum: Donnerstag, 18. Februar 2021, 18:30 Uhr Online GoTo-Meeting Online: https://bit.ly/3q8XiJv Im Vortrag berichtet Andreas Spaeth über die Geschichte und Technik des Überschallfliegens. Er beschreibt eigene Erfahrungen aus seinen Flügen mit der Concorde und gibt einen Ausblick auf die Neuentwicklungen der Überschall- flugzeuge. Der Vortrag wird gehalten aus Anlass des neuen Buches von Andreas Spaeth, das Ende 2020 herausgegeben wurde. Im Rahmen des Vortrages werden Bilder aus dem Buch gezeigt Foto: Andreas Spaeth werden. Andreas Spaeth ist seit 20 Jahren als Luftfahrtjournalist in Deutschland und international tätig. Er ist vernetzt mit Fluggesellschaften, Flughäfen und Flugzeugherstellern sowie verwandten Organisationen. Er schreibt zu Themen der zivilen Passagierluftfahrt in deutschen, englischen und amerikanischen Medien. Weitere Informationen gibt es auf seiner Homepage: http://aspapress.com. HAW/DGLR Prof. Dr.-Ing. Dieter Scholz Tel.: (040) 42875-8825 [email protected] RAeS Richard Sanderson Tel.: (04167) 92012 [email protected] VDI Dr.-Ing. Uwe Blöcker Tel.: 015112338411 [email protected] DGLR Bezirksgruppe Hamburg https://hamburg.dglr.de RAeS Hamburg Branch https://www.raes-hamburg.de ZAL TechCenter https://www.zal.aero VDI Hamburg, Arbeitskreis L&R https://www.vdi.de Die Hamburg Aerospace Lecture Series (http://www.AeroLectures.de) wird gemeinsam veranstaltet von DGLR, RAeS, ZAL, VDI und HAW Hamburg (Praxis-Seminar Luftfahrt, PSL). -
The Boeing 777X From
APRIL-MAY 2020 `100.00 AN SP GUIDE PUBLICATION (INDIA-bASED BUYER ONLY) VOLume 13 ISSue 2 SP’s www.spsairbuz.com RNI NUMBER: DELENG/2008/24198 AN EXCLUSIVE MAGAZINE ON CIVIL AVIATION FROM INDIA WINGS INDIA SPECIAL 2020 VISIT US AT StaLL 7 IN HALL B PAGE 11 GREENER SKIES ENGINE MANUFACTURERS’ INITIATIVES ARE WE AT AIRPORT THE CUSP OF DRONES AS PRIVATISATION & SUPERSONIC THE FUTURE OF MODERNISATION AIRLINERS? TRANSPORT P 7 P 20 P 24 TOMORROW’S MAINTENANCE SOLUTIONS. AVAILABLE TO YOU TODAY. ADVANCING THE PERFORMANCE, RELIABILITY AND HEALTH OF YOUR ENGINES. Pratt & Whitney’s complete EngineWise® service platform combines predictive technologies, tailored solutions and shared expertise to deliver unprecedented levels of support to your fleet. Reducing your costs and providing greater insights – it’s how we help you operate your engines worry-free. EXPLORE OUR DIGITAL SOLUTIONS AT ENGINEWISE.COM PW_AfterMarket_Maintenance_SPsAirbuz.indd 1 2/20/20 2:24 PM Client: Pratt & Whitney - Aftermarket Ad Title: Tomorrow’s Maintenance Filepath: /Volumes/GoogleDrive/Shared drives/Pratt and Whitney 2020/Aftermarket/_Aftermarket Ads /EngineWise_Tomorrow_Advance_Innovative/4c ads/PW_AfterMarket_Maintenance_SPsAirbuz.indd Publication: SP’s Airbuz - April/May Issue #2 Trim: 210 x 267 mm • Bleed: 220 x 277 mm • Live: APRIL-MAY 2020 `100.00 AN SP GUIDE PUBLICATION (INDIA-bASED BUYER ONLY) VOLume 13 ISSue 2 CONTENTS SP’s www.spsairbuz.com RNI NUMBER: DELENG/2008/24198 AN EXCLUSIVE M A G A ZINE ON C IVIL AVIA TION FROM I NDI A WINGS INDIA Cover: SPECIAL 2020 -
WAY of the FUTURE Airports at the Horizon of 2040 and 2070
WAY OF THE FUTURE Airports at the Horizon of 2040 and 2070 Photo: James Marvin Phelps, Flickr he population of the United in mobility but also will lead to new avia- GAËL LE BRIS States will reach about 375 tion megacities. The size of these conurba- million in 2040 and nearly 420 tions (Figure 1) and the congestion on the The author is a senior aviation million in 2070 (1). By 2050, this ground may promote the development planner and senior technical Tgrowth will result in the emer- of multiairport systems and secondary air- gence of 11 megaregions, identified by ports. Smaller and rural communities may principal, WSP USA, Raleigh, the Regional Planning Association as areas also revive and grow, with people seeking North Carolina, and a member of interrelated population and employ- another way of life. Local airports will of the TRB Aviation Group ment centers sharing common transpor- continue to play a vital role in connecting Executive Board. tation networks, cultures, and environ- residents to the world, using a variety of mental characteristics (2). new technologies. In the meantime, the worldwide This article is adapted from a presentation population will increase at an even faster Smart Airports and given at the TRB 99th Annual Meeting in pace—approximately 9 billion people in Intelligent Technologies January 2020. The Future of Airports: A Vision 2040 and approximately 10.5 billion in The information technology (IT) revolu- of 2040 and 2070 is a research initiative of 2070 (3). Most of this growth will occur tion in the passenger journey is already the Airport Think Tank of ENAC Alumni, which brings together aviation thought in Asia and Africa. -
Quieting the Boom : the Shaped Sonic Boom Demonstrator and the Quest for Quiet Supersonic Flight / Lawrence R
Lawrence R. Benson Lawrence R. Benson Library of Congress Cataloging-in-Publication Data Benson, Lawrence R. Quieting the boom : the shaped sonic boom demonstrator and the quest for quiet supersonic flight / Lawrence R. Benson. pages cm Includes bibliographical references and index. 1. Sonic boom--Research--United States--History. 2. Noise control-- Research--United States--History. 3. Supersonic planes--Research--United States--History. 4. High-speed aeronautics--Research--United States-- History. 5. Aerodynamics, Supersonic--Research--United States--History. I. Title. TL574.S55B36 2013 629.132’304--dc23 2013004829 Copyright © 2013 by the National Aeronautics and Space Administration. The opinions expressed in this volume are those of the authors and do not necessarily reflect the official positions of the United States Government or of the National Aeronautics and Space Administration. This publication is available as a free download at http://www.nasa.gov/ebooks. ISBN 978-1-62683-004-2 90000> 9 781626 830042 Preface and Acknowledgments v Introduction: A Pelican Flies Cross Country ix Chapter 1: Making Shock Waves: The Proliferation and Testing of Sonic Booms ............................. 1 Exceeding Mach 1 A Swelling Drumbeat of Sonic Booms Preparing for an American Supersonic Transport Early Flight Testing Enter the Valkyrie and the Blackbird The National Sonic Boom Evaluation Last of the Flight Tests Chapter 2: The SST’s Sonic Boom Legacy ..................................................... 39 Wind Tunnel Experimentation Mobilizing -
DEPA 2050 Study Report
DEPA 2050 Study Report DEPA 2050 Development Pathways for Aviation up to 2050 - Final Report - DEPA 2050 Study Report Title Development Pathways for Aviation up to 2050 – Study Report Project Acronym DEPA 2050 Publisher German Aerospace Center Authors Leipold, Alexandra; Aptsiauri, Gubaz; Ayazkhani, Amir; Bauder, Uwe; Becker, Richard-Gregor; Berghof, Ralf; Claßen, Axel; Dadashi, Alireza; Dahlmann, Katrin; Dzikus, Niclas; Flüthmann, Nico; Grewe, Volker; Göhlich, Lukas; Grimme, Wolfgang; Günther; Yves; Jaksche, Roman; Jung, Martin; Knabe, Franz; Kutne, Peter; Le Clercq, Patrick; Pabst, Holger; Poggel, Steffen; Staggat, Martin; Wicke, Kai; Wolters, Florian; Zanger, Jan; Zill, Thomas Page 2 DEPA 2050 Study Report A note on Covid-19 The DEPA 2050 study was conceptualised and, to a large extent, already conducted before the full impact of the Covid-19 pandemic became apparent. Thus, the results of this study have to be regarded and interpreted in the light of a pre-Covid 19 environment. However, major changes through the Covid-19 pandemic are illustrated and discussed in the relevant sections of this report to provide additional information on potential impacts on the results and the situation of air transport as it is today. Page 3 DEPA 2050 Study Report Content 1. Introduction ................................................................................................................... 11 1.1. Motivation for the Project ........................................................................................ 11 1.2. State of Research -
Forecasting the Global Supersonic Business Aviation Flight Movements up to 2050
AIAA SciTech Forum 10.2514/6.2021-1273 11–15 & 19–21 January 2021, VIRTUAL EVENT AIAA Scitech 2021 Forum Forecasting the Global Supersonic Business Aviation Flight Movements Up to 2050 Jiajie (Terry) Wen ∗ Aerospace Systems Design Laboratory at Georgia Tech Lorraine (ASDL@GTL), International Research Lab Georgia Tech-CNRS, UMI 2958, Georgia Tech Lorraine, 57070 Metz, France Turab A. Zaidi † Aerospace Systems Design Laboratory at Georgia Tech Lorraine (ASDL@GTL), Georgia Tech Lorraine, 57070 Metz, France Dimitri N. Mavris‡ Aerospace Systems Design Laboratory (ASDL), School of Aerospace Engineering, Georgia Institute of Technology, Atlanta, GA, 30332, USA Business aviation is typically the primary travel mode chosen by ultra-high-net-worth (UHNW) individuals and top executives. Business aviation passengers prefer the exclusivity associated with business jets, and are typically constrained by time and not cost when traveling. Numerous studies have found that business jets are worthwhile investments for corporations to increase connectivity and boost productivity. With the resurgence of efforts to bring back supersonic civil transport in the past decade, the supersonic business jet (SSBJ) poses to create significant value as a means of transport for these time-constrained travelers. However, the demand forecast for supersonic business aviation is not well-addressed in the publicly available literature. To better understand the potential size of the supersonic business aviation market and the extent of the future supersonic business flight network, this study utilizes a unique methodology that combines top-down and bottom-up approaches to forecast global supersonic business flight movements up to 2050. I. Introduction Among the remarkable achievements of mankind during the first century of aviation, the design, manufacturing, and service of the supersonic airliner Aérospatiale/BAC Concorde is certainly a noteworthy one. -
Textron Aviation Launches Next Generation of King Air Family
PUBLICATIONS Vol.49 | No.9 $9.00 SEPTEMBER 2020 | ainonline.com « From a glimpse at Aerion Supersonic’s AS3 airliner (pictured in contrast to the AS2 business jet) to NASA’s and Lockheed Martin’s research on low booms and Virgin Galactic’s ambitions to proceed with a Mach 3 jet, the field of supersonic research is fast growing. Meanwhile, regulators hope to keep up with the advances. (See report on Pages 26-36 and 44.) Finances Textron Aviation posts Textron Aviation launches next quarterly loss page 12 OEMs generation of King Air family Bombardier orders, shipments drop page 14 by Chad Trautvetter Textron Aviation announced the King Opinion Air 360/360ER, an upgrade of the Model How Covid is affecting 350/350ER that includes autothrottles, digital pressurization system, and a rede- flying safety page 16 signed cabin. The new turboprop twin models—priced at $7.9 million and $8.795 Air Transport million, respectively—are currently in production, with customer deliveries More rate cuts at Boeing expected to begin in the fourth quarter. page 38 The Innovative Solutions & Support (IS&S) ThrustSense autothrottles on the King Air 360/360ER—which reduce pilot Read Our SPECIAL REPORT workload by automatically managing engine power from the takeoff roll through the climb, cruise, descent, go-around, and Product Support landing phases of flight—are also being made available as a retrofit for 300-series AIN readers rate the support they King Airs with Collins Pro Line Fusion avi- Textron Aviation’s upgraded King Air 360/360ER features a completely redesigned cabin with received in the last 12 months for flight onics, Textron Aviation said. -
Aeronautical Engineering
https://ntrs.nasa.gov/search.jsp?R=19760003906 2020-03-22T19:15:02+00:00Z NASA SP-7037 (61) AERONAUTICAL ENGINEERING A SPECIAL BIBLIOGRAPHY WITH INDEXES Supplement 61 SEPTEMBER 1975 NATIONAL AERONAUTICS AND SPACE ADMINISTRATION ACCESSION NUMBER RANGES Accession numbers cited in this Supplement fall within the following ranges: STAR (N-10000 Series) N75-23470—N75-25862 IAA (A-10000Series) A75-32381 A75-35876 This bibliography was prepared by the NASA Scientific and Technical Information Facility operated for the National Aeronautics and Space Administration by Informatics Information Systems Company NASA SP-7037 (61) AERONAUTICAL ENGINEERING A Special Bibliography Supplement 61 A selection of annotated references to unclas- sified reports and journal articles that were introduced into the NASA scientific and tech- nical information system and announced in August 1975 in • Scientific and Technical Aerospace Reports (STAR) • International Aerospace Abstracts (IAAI Scientific and Technical Information Office SEPTEMBER !975 NATIONAL AERONAUTICS AND SPACE ADMINISTRATION Washington, D C. This Supplement is available from the National Technical Information Service (NTIS), Springfield, Virginia 22161,for $400 For copies mailed to addresses outside the United States, add $2 50 per copy for handling and postage INTRODUCTION Under the terms of an interagency agreement with the Federal Aviation Administra- tion this publication has been prepared by the National Aeronautics and Space Administra- tion for the joint use of both agencies and the scientific