Supersonic Commercial Aircraft
Total Page:16
File Type:pdf, Size:1020Kb
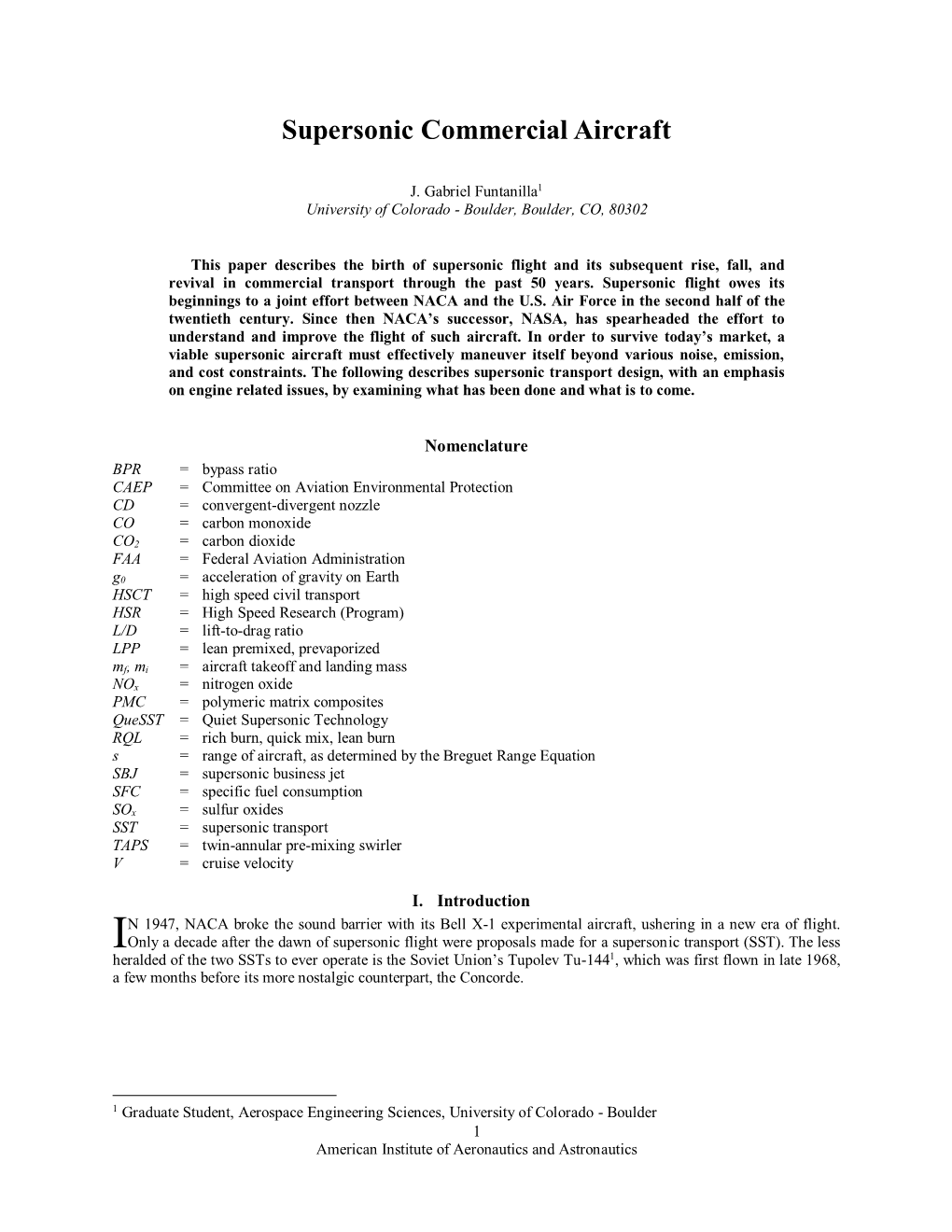
Load more
Recommended publications
-
A Nation of Aviation Pioneers
ICAO TIE-INS By Albert Pelsser Romania - A nation of aviation pioneers At the beginning of the 20th century, Romania was among the few nations in the world which brought essential contributions to aviation and flying because there were people who dedicated their life and work to fulfilling the human desire to fly and developing aviation. Among the most well-known inventors who contributed to the flight development by means of apparatuses heavier than the air, Traian Vuia, Aurel Vlaicu and Henri Coanda played a distinct role. In parallel to the above developments, schools of piloting were established and airships from other countries were purchased, with provision for specially designed workshops for the maintenance and repairing of aircraft. The first school of piloting was initiated by the Romanian lawyer Mihail Cerchez, after his return from Paris in the summer of 1909. It started its activity in the spring of 1910, on the field near Chitila, where the first aerodrome of the Romanian aviation was settled. Once the infrastructure for the construction and repair of the airships had been completed, Mihail Cerchez purchased four aircraft from France: two biplane Farman aircraft that were intended to carrying out the training flights of the future pilots, one Demoiselle aircraft and a Wright aircraft for the ground instruction. Second Lieutenants Ştefan Protopopescu and Gheorghe Negrescu were among the first six military pilots trained. Cerchez also obtained that the Farman aircraft be assembled in his workshops. Chitila’s infrastructure in 1911. Farman IV biplane. Having obtained their Pilot Licences in July 2011, Protopopescu and Negrescu, along with other pilots, participated in military maneuvers on Farmans in the fall of 1911 and carried out a series of raids to popularize aviation among youth and to maintain a high degree of readiness among pilots. -
Concorde Is a Museum Piece, but the Allure of Speed Could Spell Success
CIVIL SUPERSONIC Concorde is a museum piece, but the allure Aerion continues to be the most enduring player, of speed could spell success for one or more and the company’s AS2 design now has three of these projects. engines (originally two), the involvement of Air- bus and an agreement (loose and non-exclusive, by Nigel Moll but signed) with GE Aviation to explore the supply Fourteen years have passed since British Airways of those engines. Spike Aerospace expects to fly a and Air France retired their 13 Concordes, and for subsonic scale model of the design for the S-512 the first time in the history of human flight, air trav- Mach 1.5 business jet this summer, to explore low- elers have had to settle for flying more slowly than speed handling, followed by a manned two-thirds- they used to. But now, more so than at any time scale supersonic demonstrator “one-and-a-half to since Concorde’s thunderous Olympus afterburn- two years from now.” Boom Technology is working ing turbojets fell silent, there are multiple indi- on a 55-seat Mach 2.2 airliner that it plans also to cations of a supersonic revival, and the activity offer as a private SSBJ. NASA and Lockheed Martin appears to be more advanced in the field of busi- are encouraged by their research into reducing the ness jets than in the airliner sector. severity of sonic booms on the surface of the planet. www.ainonline.com © 2017 AIN Publications. All Rights Reserved. For Reprints go to Shaping the boom create what is called an N-wave sonic boom: if The sonic boom produced by a supersonic air- you plot the pressure distribution that you mea- craft has long shaped regulations that prohibit sure on the ground, it looks like the letter N. -
Aviation Week & Space Technology
$14.95 JUNE 29-JULY 12, 2020 Quest for Speed BOOM XB-1 TAKES SHAPE RICH MEDIA EXCLUSIVE Europe’s Hydrogen- Powered Aircraft Push PRIME TIME FOR How Safe Are HYPERSONICS Aircraft Cabins? Canada’s Fighter RICH MEDIA EXCLUSIVE Strategy Digital Edition Copyright Notice The content contained in this digital edition (“Digital Material”), as well as its selection and arrangement, is owned by Informa. and its affiliated companies, licensors, and suppliers, and is protected by their respective copyright, trademark and other proprietary rights. Upon payment of the subscription price, if applicable, you are hereby authorized to view, download, copy, and print Digital Material solely for your own personal, non-commercial use, provided that by doing any of the foregoing, you acknowledge that (i) you do not and will not acquire any ownership rights of any kind in the Digital Material or any portion thereof, (ii) you must preserve all copyright and other proprietary notices included in any downloaded Digital Material, and (iii) you must comply in all respects with the use restrictions set forth below and in the Informa Privacy Policy and the Informa Terms of Use (the “Use Restrictions”), each of which is hereby incorporated by reference. Any use not in accordance with, and any failure to comply fully with, the Use Restrictions is expressly prohibited by law, and may result in severe civil and criminal penalties. Violators will be prosecuted to the maximum possible extent. You may not modify, publish, license, transmit (including by way of email, facsimile or other electronic means), transfer, sell, reproduce (including by copying or posting on any network computer), create derivative works from, display, store, or in any way exploit, broadcast, disseminate or distribute, in any format or media of any kind, any of the Digital Material, in whole or in part, without the express prior written consent of Informa. -
Flight International – July 2021.Pdf
FlightGlobal.com July 2021 RISE of the open rotor Airbus, Boeing cool subsidies feud p12 Home US Air Force studies advantage resupply rockets p28 MC-21 leads Russian renaissance p44 9 770015 371327 £4.99 Sonic gloom Ton up Investors A400M gets pull plug a lift with on Aerion 100th delivery 07 p30 p26 Comment All together now Green shoots Irina Lavrishcheva/Shutterstock While CFM International has set out its plan to deliver a 20% fuel saving from its next engine, only the entire aviation ecosystem working in concert can speed up decarbonisation ohn Slattery, the GE Aviation restrictions, the RISE launch event governments have a key role to chief executive, has many un- was the first time that Slattery and play here through incentivising the doubted skills, but perhaps his Safran counterpart, Olivier An- production and use of SAF; avia- the least heralded is his abil- dries, had met face to face since tion must influence policy, he said. Jity to speak in soundbites while they took up their new positions. It He also noted that the engine simultaneously sounding natural. was also just a week before what manufacturers cannot do it alone: It is a talent that politicians yearn would have been the first day of airframers must also drive through for, but which few can master; the Paris air show – the likely launch aerodynamic and efficiency im- frequently the individual simply venue for the RISE programme. provements for their next-genera- sounds stilted, as though they were However, out of the havoc tion products. reading from an autocue. -
Getting Shipshape
AER October 2020 OSPACE DOES AEROSPACE HAVE A RACE PROBLEM? SECRETS FROM THE FALKLANDS AIR WAR POWERING UP ELECTRIC FLIGHT www.aerosociety.com October 2020 GETTING SHIPSHAPE Volume 47 Number 10 Volume UK F-35B FORCE GETS READY FOR FIRST OPERATIONAL CARRIER DEPLOYMENT Royal AeronauticaSociety OCTOBER 2020 AEROSPACE COVER FINAL.indd 1 18/09/2020 14:59 RAeS 2020 Virtual Conference Programme Join us from wherever you are in the world to experience high quality, informative content. Book early for our special introductory offer rates. STRUCTURES & MATERIALS UAS / ROTORCRAFT / AIR TRANSPORT GREENER BY DESIGN 7th Aircraft Structural Urban Air Mobility RAeS Climate Change Design Conference Conference 2020 Conference 2020 DATE NEW DATE DATE 8 October 22 - 23 October 3 - 4 November TIME TIME TIME 14:00 - 17:00 13:00 - 18:00 13:00 - 18:00 SCAN USING SCAN USING SCAN USING YOUR PHONE YOUR PHONE YOUR PHONE FOR MORE INFO FOR MORE INFO FOR MORE INFO Embark on your virtual learning journey with the RAeS Connect and interact with our speakers and ask questions live Engage and network with other professionals from across the world Meet our sponsors at our virtual exhibitor booths Access content post-event to continue your professional development For the full virtual conference programme and further details on what to expect visit aerosociety.com/VCP Volume 47 Number 10 October 2020 EDITORIAL Contents When global rules unravel Regulars 4 Radome 12 Transmission What price global standards, rules and regulations? Pre-pandemic there were The latest aviation and Your letters, emails, tweets aeronautical intelligence, and social media feedback. -
Feeling Supersonic
FlightGlobal.com May 2021 How Max cuts hurt Boeing backlog Making throwaway Feeling aircraft aff ordable p32 Hydrogen switch for Fresson’s Islander p34 supersonic Will Overture be in tune with demand? p52 9 770015 371327 £4.99 Big worries Warning sign We assess A380 Why NOTAM outlook as last burden can delivery looms baffl e pilots 05 p14 p22 Comment Prospects receding Future dreaming Once thought of as the future of air travel, the A380 is already heading into retirement, but aviation is keenly focused on the next big thing Airbus t has been a rapid rise and fall for on who you ask. As we report else- Hydrogen is not without its the Airbus A380, which not so where in this issue, there are those issues, of course, but nonethe- long ago was being hailed as the banking on supersonic speeds be- less it appears more feasible as a future of long-haul air travel. ing the answer. power source for large transport IThe superjumbo would be, The likes of Aerion and Boom Su- aircraft than batteries do at pres- forecasts said, the perfect tool for personic view the ability to shave ent, even allowing for improving airlines operating into mega-hubs significant time from journeys as a energy densities. such as Dubai that were beginning unique selling point. However, there are others who to spring up. While projects are likely to be see hydrogen through a differ- But the planners at Airbus failed technologically feasible, to be able ent filter. They argue that so- to take into consideration the to sell these new aircraft in signif- called sub-regional aircraft – the efficiency gains available from icant volumes their manufacturers Britten-Norman Islander, among a new generation of widebody will have to ensure that supersonic others – can be given fresh impetus twinjets that allowed operators to flight is not merely the domain of if a fuel source can be found that is open up previously uneconomical the ultra-rich. -
Brazilian 14-Xs Hypersonic Unpowered Scramjet Aerospace Vehicle
ISSN 2176-5480 22nd International Congress of Mechanical Engineering (COBEM 2013) November 3-7, 2013, Ribeirão Preto, SP, Brazil Copyright © 2013 by ABCM BRAZILIAN 14-X S HYPERSONIC UNPOWERED SCRAMJET AEROSPACE VEHICLE STRUCTURAL ANALYSIS AT MACH NUMBER 7 Álvaro Francisco Santos Pivetta Universidade do Vale do Paraíba/UNIVAP, Campus Urbanova Av. Shishima Hifumi, no 2911 Urbanova CEP. 12244-000 São José dos Campos, SP - Brasil [email protected] David Romanelli Pinto ETEP Faculdades, Av. Barão do Rio Branco, no 882 Jardim Esplanada CEP. 12.242-800 São José dos Campos, SP, Brasil [email protected] Giannino Ponchio Camillo Instituto de Estudos Avançados/IEAv - Trevo Coronel Aviador José Alberto Albano do Amarante, nº1 Putim CEP. 12.228-001 São José dos Campos, SP - Brasil. [email protected] Felipe Jean da Costa Instituto Tecnológico de Aeronáutica/ITA - Praça Marechal Eduardo Gomes, nº 50 Vila das Acácias CEP. 12.228-900 São José dos Campos, SP - Brasil [email protected] Paulo Gilberto de Paula Toro Instituto de Estudos Avançados/IEAv - Trevo Coronel Aviador José Alberto Albano do Amarante, nº1 Putim CEP. 12.228-001 São José dos Campos, SP - Brasil. [email protected] Abstract. The Brazilian VHA 14-X S is a technological demonstrator of a hypersonic airbreathing propulsion system based on supersonic combustion (scramjet) to fly at Earth’s atmosphere at 30km altitude at Mach number 7, designed at the Prof. Henry T. Nagamatsu Laboratory of Aerothermodynamics and Hypersonics, at the Institute for Advanced Studies. Basically, scramjet is a fully integrated airbreathing aeronautical engine that uses the oblique/conical shock waves generated during the hypersonic flight, to promote compression and deceleration of freestream atmospheric air at the inlet of the scramjet. -
HISTORICAL PERSPECTIVE a Need for Speed
n HISTORICAL PERSPECTIVE A need for speed Mach 0.8 to 1.2 and above the speed of powerful turbine engine available. To mit- Skystreak taught lots sound, respectively). The U.S. Army Air igate as much risk as possible, the team Forces took responsibility for supersonic kept the design simple, using a conven- about flight near research—which resulted in Chuck Yea- tional straight wing rather than the new ger breaking the sound barrier in the Bell and mostly unproven swept wing. The the sound barrier X-1 on Oct. 14, 1947. That historic event 5,000-lb.-thrust (22-kilonewton) Allison overshadowed the highly successful re- J35-A-11 engine filled the fuselage, leav- BY MICHAEL LOmbARDI search conducted by the pilots who flew ing just enough room to house instrumen- s World War II was coming to a the Douglas D-558-1 Skystreak to the edge tation and a pilot in a cramped cockpit. close, advances in high-speed aero- of the sound barrier while capturing new Because of the lack of knowledge about Adynamics were rapidly progressing world speed records. the survivability of a high-altitude, high- beyond the ability of the wind tunnels of The D-558-1 was developed by the speed bailout, Douglas engineers designed the day, prompting a dramatic expansion Douglas Aircraft Company, today a part a jettisonable nose section that could pro- of flight-test research and experimental of Boeing, at its El Segundo (Calif.) tect the pilot until a safe bailout speed was aircraft. Division. It was designed by a team led reached. -
The Economics of the UK Aerospace Industry: a Transaction Cost Analysis
The economics of the UK aerospace industry: A transaction cost analysis of defence and civilian firms Ian Jackson PhD Department of Economics and Related Studies University of York 2004 Abstract The primaryaim of this thesisis to assessvertical integration in the UK aerospace industrywith a transactioncost approach. There is an extensivetheoretical and conceptualliterature on transactioncosts, but a relativelack of empiricalwork. This thesisapplies transaction cost economics to the UK aerospaceindustry focusing on the paradigmproblem of the make-or-buydecision and related contract design. It assesses whetherthe transactioncost approachis supported(or rejected)by evidencefrom an originalsurvey of theUK aerospaceindustry. The centralhypothesis is that UK aerospacefirms are likely to makecomponents in- housedue to higherlevels of assetspecificity, uncertainty, complexity, frequency and smallnumbers, which is reflectedin contractdesign. The thesismakes these concepts operational.The empiricalmethodology of the thesisis basedon questionnairesurvey dataand econometric tests using Ordinary Least Squares (OLS) andlogit regressions to analysethe make-or-buy decision and the choiceof contracttype. The resultsfrom this thesisfind limited evidencein supportof the transactioncost approachapplied to the UK aerospaceindustry, in spiteof a bespokedataset. The empiricaltests of verticalintegration for both make-or-buyand contracttype as the dependentvariable yield insufficientevidence to concludethat the transactioncost approachis an appropriateframework -
W Oltoria Di Un Uo Non Man at Taman Antonio La D
W OLTORIA DI UN USUO NON20180134382A1 MAN AT TAMAN ANTONIOLA D ( 19) United States (12 ) Patent Application Publication ( 10) Pub . No. : US 2018 /0134382 A1 Scholl et al. (43 ) Pub . Date : May 17 , 2018 ( 54 ) COMMERCIAL SUPERSONIC AIRCRAFT Publication Classification AND ASSOCIATED SYSTEMS AND (51 ) Int. Cl. METHODS B64C 30 / 00 (2006 .01 ) B64D 13 /08 ( 2006 . 01) ( 71) Applicant: Boom Technology, Inc. , Englewood , B64D 43 / 00 (2006 . 01 ) CO (US ) B64D 11 /06 ( 2006 .01 ) (72 ) Inventors : Nathaniel Blake Scholl, Englewood , (52 ) U . S . CI. CO (US ) ; Joe Wilding, Englewood , CO CPC . .. .. B64C 30 / 00 ( 2013 .01 ) ; B64D 13 / 08 (US ) ; Josh Krall, Englewood , CO (2013 .01 ) ; B64D 2013 /0618 (2013 .01 ) ; B64D (US ) ; Andy Berryann , Englewood , CO 11 / 064 (2014 . 12 ); B64D 43 / 00 ( 2013 .01 ) (US ) ; Michael Reid , Englewood , CO (US ) (57 ) ABSTRACT Commercial supersonic aircraft and associated systems and ( 21 ) Appl. No. : 15 /811 ,327 methods . A representative commercial supersonic aircraft includes a fuselage configured to carry a crew and between ( 22 ) Filed : Nov . 13 , 2017 20 and 60 passengers, a delta wing mounted to the fuselage , and a propulsion system carried by at least one of the wing Related U . S . Application Data and the fuselage , the propulsion system including a plurality (60 ) Provisional application No . 62 /421 , 870 , filed on Nov . of engines , at least one variable - geometry inlet , and at least 14 , 2016 . one variable - geometry nozzle . 101 103 100 102 51216 Chen 110 - - - - 000000 - - -
CHAPTER 11 Subsonic and Supersonic Aircraft Emissions
CHAPTER 11 Subsonic and Supersonic Aircraft Emissions Lead Authors: A. Wahner M.A. Geller Co-authors: F. Arnold W.H. Brune D.A. Cariolle A.R. Douglass C. Johnson D.H. Lister J.A. Pyle R. Ramaroson D. Rind F. Rohrer U. Schumann A.M. Thompson CHAPTER 11 SUBSONIC AND SUPERSONIC AIRCRAFT EMISSIONS Contents SCIENTIFIC SUMMARY ......................................................................................................................................... 11.1 11.1 INTRODUCTION ............................................................................................................................................ 11.3 11.2 AIRCRAFT EMISSIONS ................................................................................................................................. 11.4 11.2.1 Subsonic Aircraft .................................................................................................................................. 11.5 11.2.2 Supersonic Aircraft ............................................................................................................................... 11.6 11.2.3 Military Aircraft .................................................................................................................................... 11.6 11.2.4 Emissions at Altitude ............................................................................................................................ 11.6 11.2.5 Scenarios and Emissions Data Bases ................................................................................................... -
Diffusion Flames and Supersonic Combustion
DIFFUSION FLAMES AND SUPERSONIC COMBUSTION BY I.DA-RIVA A.LINAN E. FRAGA J. L. URRUTI A INSTITUTO NACIONAL DE TECNICA AEROESPACIAL «ESTEBAN TERRA DAS» MADRID (SPAIN) October i, 1566 ABSTRACT The paper describes some analytical work connected with the purely diffusive mode of supersonic combustion. The basic problems considered have been: the study of the hydrogen-air diffusion flames, under hoth close to and far from equilibrium conditions, and the study of the aerodynamic field near the injector exit when the ratio of injected to outer total pressures is small. The internal structure of hydrogen-oxygen diffusion flames close to equilibrium has been studied using the first order approximation of an asymptotic expansion method, in which the large parameter represents the ratio between a characteris tic mechanical time and a chemical time. Far from equilibrium conditions, the above mentioned solution fails. However, when a free jet of hydrogen.parallel to the air stream is used for injection purposes, a very simple near frozen approach may be used. The main simplifying features of such an approach being; the use of an overall chemical reaction, the assumption that fuel and oxidizer jnix without appreciable depletion and chemical heat release, and the linearization of the mixing problem. Finally a discussion of some means of improving the mixing process, near the injector exit, is made, using some experimental evidence from work on related problems by other groups. TABLE OF CONTENTS Pa INTRODUCTION 1 1 HYDROGEN AIR DIFFUSION FLAME CLOSE TO EQUILIBRIUM . 3 1A Structure of the Diffusion Flames 4 IB Hydrogen-Oxygen Chemical Kinetics 7 IC Structure of the Hydrogen-Air Diffusion Flames.