Scanned Document
Total Page:16
File Type:pdf, Size:1020Kb
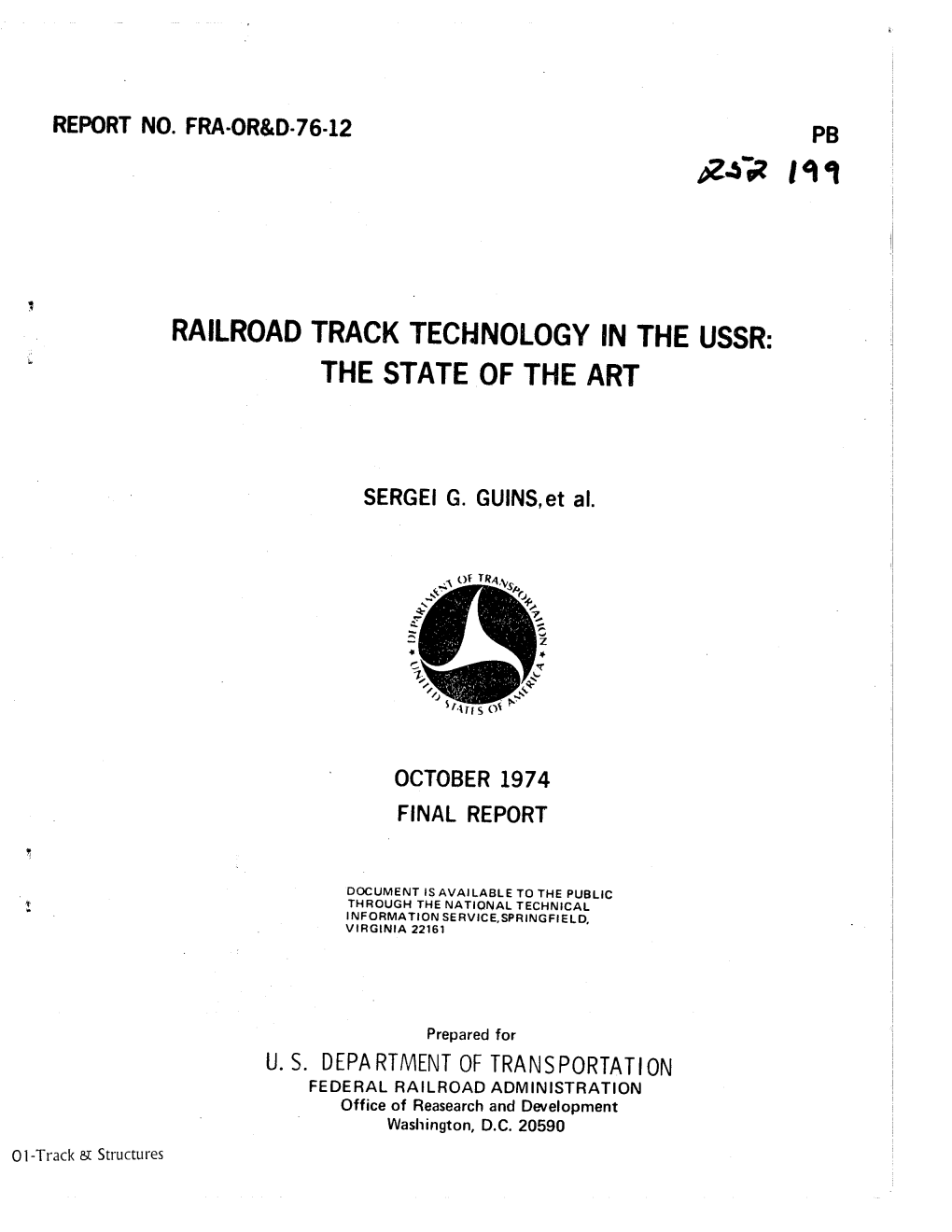
Load more
Recommended publications
-
CSX Transportation (CSX) Lynchburg, VA April 30, 2014
Federal Railroad Administration Office of Railroad Safety Accident and Analysis Branch Accident Investigation Report HQ-2014-4 CSX Transportation (CSX) Lynchburg, VA April 30, 2014 Note that 49 U.S.C. §20903 provides that no part of an accident or incident report, including this one, made by the Secretary of Transportation/Federal Railroad Administration under 49 U.S.C. §20902 may be used in a civil action for damages resulting from a matter mentioned in the report. U.S. Department of Transportation FRA File #HQ-2014-4 Federal Railroad Administration FRA FACTUAL RAILROAD ACCIDENT REPORT TRAIN SUMMARY 1. Name of Railroad Operating Train #1 1a. Alphabetic Code 1b. Railroad Accident/Incident No. CSX Transportation CSX 000129247 GENERAL INFORMATION 1. Name of Railroad or Other Entity Responsible for Track Maintenance 1a. Alphabetic Code 1b. Railroad Accident/Incident No. CSX Transportation CSX 000129247 2. U.S. DOT Grade Crossing Identification Number 3. Date of Accident/Incident 4. Time of Accident/Incident 4/30/2014 1:54 PM 5. Type of Accident/Incident Derailment 6. Cars Carrying 7. HAZMAT Cars 8. Cars Releasing 9. People 10. Subdivision HAZMAT 104 Damaged/Derailed 17 HAZMAT 1 Evacuated 400 Huntington East 11. Nearest City/Town 12. Milepost (to nearest tenth) 13. State Abbr. 14. County Lynchburg VA LYNCHBURG 15. Temperature (F) 16. Visibility 17. Weather 18. Type of Track 53 ̊ F Day Rain Main 19. Track Name/Number 20. FRA Track Class 21. Annual Track Density 22. Time Table Direction (gross tons in millions) No. 2 Freight Trains-25, Passenger Trains-30 East 50 U.S. -
Section 10 Locomotive and Rolling Stock Data
General Instruction Pages Train Operating Conditions Manual SECTION 10 LOCOMOTIVE AND ROLLING STOCK DATA Version: 3.0 Issued: January 2016 CRN TOC Section 10 V3.0 Locomotive & Rolling Stock Data.docx © JHR UNCONTROLLED WHEN PRINTED SECTION 10 Version: 3.0 General Instruction Pages Locomotive and Rolling Stock Data Train Operating Conditions Manual Document control Revision Date of Issue Summary of change 1.0 18/10/11 For publication 1.1 25/11/11 Updated 25/11/11 1.2 10/1/12 Updated for current rolling stock 1.3 13/5/12 Updated for current rolling stock 1.4 14/8/12 Updated for current rolling stock 1.5 16/8/12 Corrections to El Zorro vehicles 1.6 25/8/12 T333 added to the Seymour Rail Heritage Centre Note covering NGXH / GGXH wagons operating on Class 2 1.7 13/9/12 track at 23 tonne axle load, deleted. 1.8 1/8/13 General update with currently approved vehicles 2.1 1/12/14 General update with currently approved vehicles 2.2 19/12/14 Amended as shown below 2.3 12/1/15 Amended as shown below 2.4 11/10/15 Amended as shown below 3.0 16/1/16 Amended as shown below Summary of significant changes from previous version Page Summary of change All pages General update to include approved vehicles for publishing and covered on TOC waivers: Speed of vehicles covered by Note R1 between Stockinbingal and Griffith, reduced from 4 70 km/h to 65 km/h for consistency with Note R20 (originally Note R18) 4 Note R1 Joppa Junction and Queanbeyan amended to Joppa Junction and Canberra Note R20 amended to absorb Notes R3 and R18 and wagons covered by R3 and R18 -
Section 10 Locomotive and Rolling Stock Data
General Instruction Pages Locomotive and Rolling Stock Data SECTION 10 LOCOMOTIVE AND ROLLING STOCK DATA General Instruction Pages Locomotive and Rolling Stock Data SECTION 10 Contents 3801 Limited Eveleigh - Locomotives................................................................................................................3 3801 Limited Eveleigh - Passenger Rolling Stock...............................................................................................3 3801 Limited Eveleigh - Freight Rolling Stock ...................................................................................................3 Australian Traction Corporation - Locomotives ................................................................................................3 Australian Traction Corporation - Freight Rolling Stock....................................................................................3 Australian Railway Historical Society A.C.T. Division – Locomotives................................................................3 Australian Railway Historical Society A.C.T. Division – Rail Motors ..................................................................4 Australian Railway Historical Society A.C.T. Division – Passenger Rolling Stock...............................................4 Australian Railway Historical Society A.C.T. Division – Freight Rolling Stock....................................................4 Australian Rail Track Corporation Ltd - Special Purpose Rolling Stock..............................................................4 -
Federal Railroad Administration Office of Railroad Safety Accident and Analysis Branch
Federal Railroad Administration Office of Railroad Safety Accident and Analysis Branch Accident Investigation Report HQ-2013-13 Union Pacific (UP) Chafee, MO May 25, 2013 Note that 49 U.S.C. §20903 provides that no part of an accident or incident report, including this one, made by the Secretary of Transportation/Federal Railroad Administration under 49 U.S.C. §20902 may be used in a civil action for damages resulting from a matter mentioned in the report. U.S. Department of Transportation FRA File #HQ-2013-13 Federal Railroad Administration FRA FACTUAL RAILROAD ACCIDENT REPORT TRAIN SUMMARY 1. Name of Railroad Operating Train #1 1a. Alphabetic Code 1b. Railroad Accident/Incident No. Union Pacific Railroad Company UP 0513SL011 2. Name of Railroad Operating Train #2 2a. Alphabetic Code 2b. Railroad Accident/Incident No. BNSF Railway Company BNSF SF0513118 GENERAL INFORMATION 1. Name of Railroad or Other Entity Responsible for Track Maintenance 1a. Alphabetic Code 1b. Railroad Accident/Incident No. Union Pacific Railroad Company UP 0513SL011 2. U.S. DOT Grade Crossing Identification Number 3. Date of Accident/Incident 4. Time of Accident/Incident 5/25/2013 2:35 AM 5. Type of Accident/Incident Side Collision 6. Cars Carrying 7. HAZMAT Cars 8. Cars Releasing 9. People 10. Subdivision HAZMAT Damaged/Derailed HAZMAT Evacuated Chester 11. Nearest City/Town 12. Milepost (to nearest tenth) 13. State Abbr. 14. County Chafee 131.1 MO SCOTT 15. Temperature (F) 16. Visibility 17. Weather 18. Type of Track 50 ̊ F Dark Clear Main 19. Track Name/Number 20. FRA Track Class 21. -
Taskload Report Outline
Track Inspection Time Study* U.S. Department of Transportation Federal Railroad * Required by Section 403 of the Rail Safety Improvement Act of 2008 (Public Law 110- Administration 432, Div. A.) Office of Railroad Policy and Development Washington, DC 20590 DOT/FRA/ORD-11/15 Final Report July 2011 NOTICE This document is disseminated under the sponsorship of the Department of Transportation in the interest of information exchange. The United States Government assumes no liability for its contents or use thereof. Any opinions, findings and conclusions, or recommendations expressed in this material do not necessarily reflect the views or policies of the United States Government, nor does mention of trade names, commercial products, or organizations imply endorsement by the United States Government. The United States Government assumes no liability for the content or use of the material contained in this document. NOTICE The United States Government does not endorse products or manufacturers. Trade or manufacturers‘ names appear herein solely because they are considered essential to the objective of this report. REPORT DOCUMENTATION PAGE Form Approved OMB No. 0704-0188 Public reporting burden for this collection of information is estimated to average 1 hour per response, including the time for reviewing instructions, searching existing data sources, gathering and maintaining the data needed, and completing and reviewing the collection of information. Send comments regarding this burden estimate or any other aspect of this collection of information, including suggestions for reducing this burden, to Washington Headquarters Services, Directorate for Information Operations and Reports, 1215 Jefferson Davis Highway, Suite 1204, Arlington, VA 22202-4302, and to the Office of Management and Budget, Paperwork Reduction Project (0704-0188), Washington, DC 20503. -
A Round up of Recent Activities in Our Sections
Section Activities A round up of recent activities in our Sections AS PUBLISHED IN The Journal April 2018 Volume 136 Part 2 Sections BIRMINGHAM CROYDON & BRIGHTON DARLINGTON & NORTH EAST EDINBURGH Our online events calendar holds all GLASGOW of our Section meetings. IRISH LANCASTER, BARROW & CARLISLE You’ll also find full contact details on LONDON our website. MANCHESTER & LIVERPOOL MILTON KEYNES NORTH WALES NOTTINGHAM & DERBY SOUTH & WEST WALES THAMES VALLEY WESSEX WEST OF ENGLAND WEST YORKSHIRE YORK SECTION ACTIVITIES lighting Towers that sprang up on the railway organisation. On one occasion, John was landscape during the modernisation days of called into to record Pickfords moving the A round up the 1960s and 70s. Dickens Inn from one end of St. Catherine’s Dock in London to the other. Photographers were based at the regional of recent offices and in the various railway workshops A less glamorous assignment, but nonetheless which were around at that time. John was fascinating (and unnerving) was recording called in to take pictures of work in progress on the water jets spraying out of the brickwork in activities in new trains and then at their launch. Abbotscliffe Tunnel. This required elaborate lighting to ensure a clear shot could be On some occasions, it was just a case of recorded. Works for the opening of the our Sections. being in the right place at the right time. On Channel Tunnel including over bridge deck his way to another job in Gloucester he was raising and tunnel floor lowering provided a lot able to get in position on a signal gantry at of work in the early 1990s. -
Network Rail Infrastructure Limited – Annual Return 2011 3 MB
Network Rail Annual Return 2011 “More trains would take the pressure off at busy times. They nearly all seem to be crowded.” The railways have never been more popular. The result is that we need more capacity. More trains. Longer trains. We spent £1.7bn in the year on capacity enhancements and plan to invest £12bn over the five years to 2014 *Passenger comment, December 2010 Helping Britain run better Contents 1 Executive Summary 8 Introduction 11 Section 1 – Operational performance and stakeholder relationships 25 Section 2 – Network capability and network availability 37 Section 3 – Asset management 75 Section 4 – Activity volumes 89 Section 5 – Safety and environment 98 Section 6 – Enhancement Programme “Projects designed to increase capacity and improve services range from the new Airdrie-Bathgate rail link in Scotland to Thameslink across London, from platform lengthening on the East Coast to the redevelopment of Reading and entirely new stations such as Newport.” Contents Executive Summary 1 Track failures 50 Overall performance in 2010/11 1 Condition of asset temporary speed restriction sites (M4) 51 Operational performance and stakeholder relationships 2 Track geometry faults (M5) 54 Network capability and network availability 3 Earthwork failures (M6) 57 Asset management 4 Earthwork condition (M33) 58 Safety and environment 5 Tunnel condition 59 Expenditure and efficiency 6 Bridge condition (M8) 61 Enhancements schemes 7 Signalling failures (M9) 64 Signalling asset condition (M10) 64 Introduction 8 Alternating current traction -
UPRR - General Code of Operating Rules
Union Pacific Rules UPRR - General Code of Operating Rules Seventh Edition Effective April 1, 2020 Includes Updates as of September 28, 2021 PB-20280 1.0: GENERAL RESPONSIBILITIES 2.0: RAILROAD RADIO AND COMMUNICATION RULES 3.0: Section Reserved 4.0: TIMETABLES 5.0: SIGNALS AND THEIR USE 6.0: MOVEMENT OF TRAINS AND ENGINES 7.0: SWITCHING 8.0: SWITCHES 9.0: BLOCK SYSTEM RULES 10.0: RULES APPLICABLE ONLY IN CENTRALIZED TRAFFIC CONTROL (CTC) 11.0: RULES APPLICABLE IN ACS, ATC AND ATS TERRITORIES 12.0: RULES APPLICABLE ONLY IN AUTOMATIC TRAIN STOP SYSTEM (ATS) TERRITORY 13.0: RULES APPLICABLE ONLY IN AUTOMATIC CAB SIGNAL SYSTEM (ACS) TERRITORY 14.0: RULES APPLICABLE ONLY WITHIN TRACK WARRANT CONTROL (TWC) LIMITS 15.0: TRACK BULLETIN RULES 16.0: RULES APPLICABLE ONLY IN DIRECT TRAFFIC CONTROL (DTC) LIMITS 17.0: RULES APPLICABLE ONLY IN AUTOMATIC TRAIN CONTROL (ATC) TERRITORY 18.0: RULES APPLICABLE ONLY IN POSITIVE TRAIN CONTROL (PTC) TERRITORY GLOSSARY: Glossary For business purposes only. Unauthorized access, use, distribution, or modification of Union Pacific computer systems or their content is prohibited by law. Union Pacific Rules UPRR - General Code of Operating Rules 1.0: GENERAL RESPONSIBILITIES 1.1: Safety 1.1.1: Maintaining a Safe Course 1.1.2: Alert and Attentive 1.1.3: Accidents, Injuries, and Defects 1.1.4: Condition of Equipment and Tools 1.2: Personal Injuries and Accidents 1.2.1: Care for Injured 1.2.2: Witnesses 1.2.3: Equipment Inspection 1.2.4: Mechanical Inspection 1.2.5: Reporting 1.2.6: Statements 1.2.7: Furnishing Information -
METHODS of CLEANING STONE BALLAST Report of Committee
METHODS OF CLEANING STONE BALLAST Report of Committee L. J. Drumeller division engineer, C. & 0., Hinton, W. Va. Probably one of the most important problems that has confronted maintenance officers during the last five years has been that of keeping the ballast section cleaned, particularly in stone-ballasted territories. This condition was largely brought about by a curtailed labor allowance which made it necessary to direct practically all available funds to line and surface, tie renewals, and such other maintenance work as was necessary for the safe operation of trains. These conditions resulted in the usual ballast cleaning and renewal cycle being prolonged two and, in some cases, three fold. Clean, crushed stone ballast is recognized as the most satisfactory ballast in dense-traffic territory, and one of the underlying requirements of a well maintained railroad is clean, live ballast. Those railroads which were able to maintain such a condition through the past few years are fortunate. Before discussing the various methods of cleaning stone ballast, it may be well to outline briefly some of the major conditions that cause ballast to become foul. They include the following: 1. Inadequate surface and subsurface drainage. 2. Battered rail ends, causing joints to vibrate excessively under wheel loads. 3. Burned rail, due to slipping drivers, bringing about the same condition as in Item 2. 4. Front-end sparks from locomotives operating on heavy grades. 5. Commodities such as coal, coke, etc., in territories close to the points of loading. 6. Leakage through floors and hopper-bottoms of cars. 7. The elements, causing the deposit of wind-blown dirt, etc., on ballast. -
Finished Vehicle Logistics by Rail in Europe
Finished Vehicle Logistics by Rail in Europe Version 3 December 2017 This publication was prepared by Oleh Shchuryk, Research & Projects Manager, ECG – the Association of European Vehicle Logistics. Foreword The project to produce this book on ‘Finished Vehicle Logistics by Rail in Europe’ was initiated during the ECG Land Transport Working Group meeting in January 2014, Frankfurt am Main. Initially, it was suggested by the members of the group that Oleh Shchuryk prepares a short briefing paper about the current status quo of rail transport and FVLs by rail in Europe. It was to be a concise document explaining the complex nature of rail, its difficulties and challenges, main players, and their roles and responsibilities to be used by ECG’s members. However, it rapidly grew way beyond these simple objectives as you will see. The first draft of the project was presented at the following Land Transport WG meeting which took place in May 2014, Frankfurt am Main. It received further support from the group and in order to gain more knowledge on specific rail technical issues it was decided that ECG should organise site visits with rail technical experts of ECG member companies at their railway operations sites. These were held with DB Schenker Rail Automotive in Frankfurt am Main, BLG Automotive in Bremerhaven, ARS Altmann in Wolnzach, and STVA in Valenton and Paris. As a result of these collaborations, and continuous research on various rail issues, the document was extensively enlarged. The document consists of several parts, namely a historical section that covers railway development in Europe and specific EU countries; a technical section that discusses the different technical issues of the railway (gauges, electrification, controlling and signalling systems, etc.); a section on the liberalisation process in Europe; a section on the key rail players, and a section on logistics services provided by rail. -
Wayside Condition Monitoring System for Railway Wheel Profiles: Applications and Performance Assessment
DOCTORAL T H E SIS Matthias Asplund Wayside Condition Monitoring System for Railway Wheel Profiles: Applications and Performance Assessment Applications and Performance Wheel Profiles: Condition Monitoring System for Railway Wayside Asplund Matthias Wayside Condition Monitoring System Department of Civil, Environmental and Natural Resources Engineering Wayside Condition Monitoring Division of Operation, Maintenance and Acoustics for Railway Wheel Profiles: System for Railway Wheel Profiles: Applications and Performance ISSN 1402-1544 ISBN 978-91-7583-745-1 (print) Applications and Performance Assessment ISBN 978-91-7583-746-8 (pdf) Assessment Luleå University of Technology 2016 Matthias Asplund Matthias Asplund Division of Operation, Maintenance and Acoustics LuleåOperation University and of Technology, Maintenance Sweden Wayside Condition Monitoring System for Railway Wheel Profiles: Applications and Performance Assessment Matthias Asplund Luleå University of Technology Department of Civil, Environmental and Natural Resources Engineering Division of Operation, Maintenance and Acoustics Printed by Luleå University of Technology, Graphic Production 2016 ISSN 1402-1544 ISBN 978-91-7583-745-1 (print) ISBN 978-91-7583-746-8 (pdf) Luleå 2016 www.ltu.se PREFACE The research work presented in this thesis was carried out between August 2011 and December 2016 at the Division of Operation and Maintenance Engineering of Luleå University of Technology and Luleå Railway Research Center (JVTC). The interest and financial support of Trafikverket (the Swedish Transport Administration) were the means to this end. ACKNOWLEDGEMENT I would like to express my gratitude to my supervisor, Professor Uday Kumar, and my co- supervisors, Dr Matti Rantatalo and Dr Jing Lin, for the great confidence which they have placed in my capability to conduct this research work, and for all their support through sharing their ideas, proposing improvements, proofreading manuscripts, finding new ways, and always adopting a positive approach. -
SAFETY FIRST Central Maine & Quebec Railway TIMETABLE NO. 6
SAFETY FIRST Central Maine & Quebec Railway TIMETABLE NO. 6 EFFECTIVE 00:01 EASTERN DAYLIGHT SAVINGS TIME March 25, 2019 Ryan Ratledge President & Chief Executive Officer Chad Mowery Vice President Operations Ron Marshall Vice President Engineering Dan Fransen Vice President Safety & Transportation GENERAL OFFICE 700 Main Street Suite 3 Bangor, Maine 04401 JOB BRIEFING Prior to performing any task requiring the coordination of two or more employees, those employees involved must hold a “job briefing” to ensure all have a clear understanding of the task to be performed and their individual responsibility and must discuss the following: 1. The job(s) to be done or move(s) to be made. 2. The responsibility of each employee. 3. Any additional instructions due to an unusual condition. 4. Any specific reminder due to a hazardous condition or unusual practice. 5. When on or near track, discuss how you are protected, what your limits are, what type and time given. If necessary, an additional briefing should be held as the work progresses or the situation changes. 2 STATEMENT OF SAFETY POLICY OUR COMMITMENT Knowledge vigilance and caring are the foundation to any successful safety process. An older and wiser mentor of mine said to me many years ago; "People don't care how much you know until they know how much you care." At Central Maine and Québec Railway, one of our highest priorities will be to create an environment that is conducive to continuous learning and continuous improvement. It will also incorporate safety, not as a slogan or phrase on a calendar, but as essential to how we conduct our business.