Unpolymerized, Unsaturated Polyester ‘ Resin
Total Page:16
File Type:pdf, Size:1020Kb
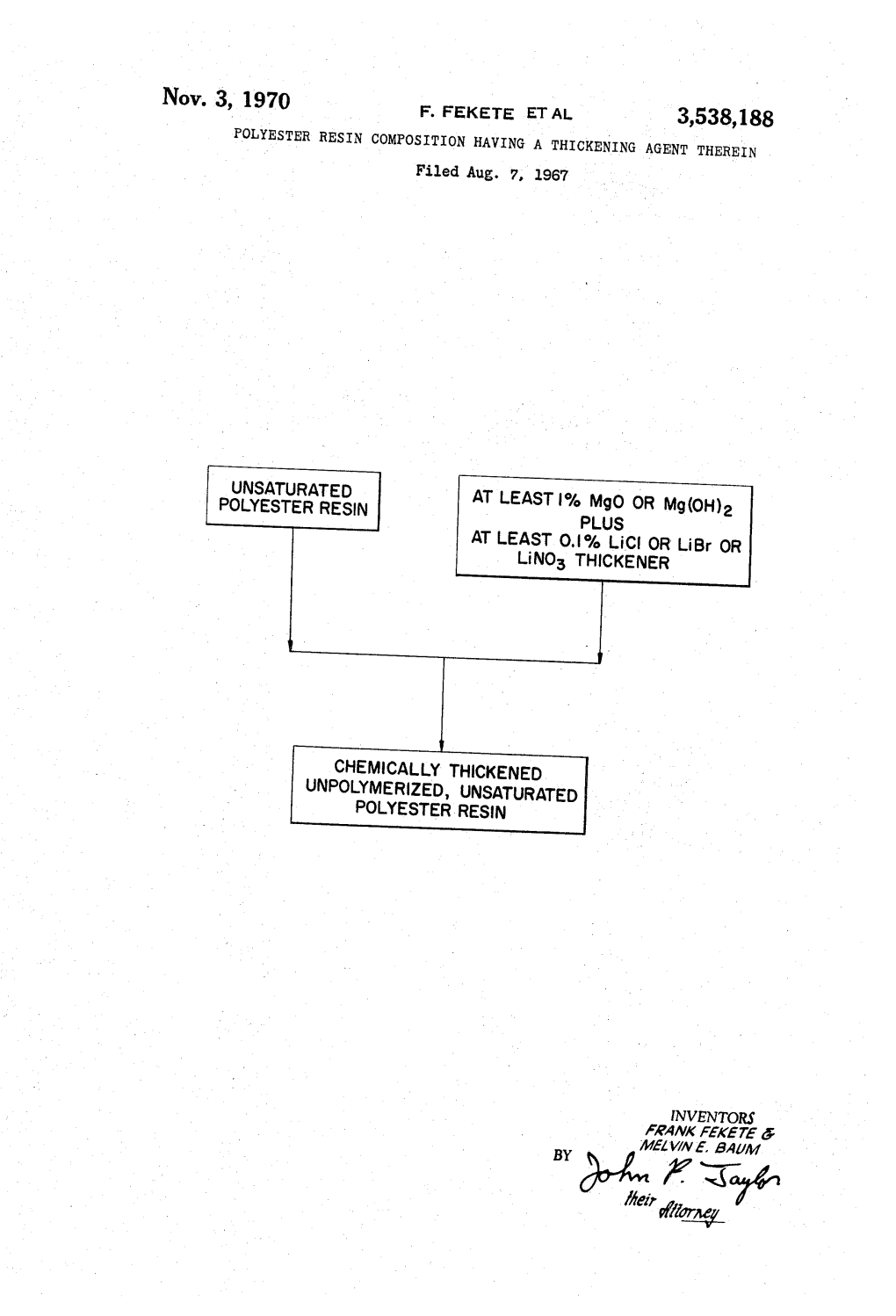
Load more
Recommended publications
-
WO 2017/106925 Al 29 June 2017 (29.06.2017) P O P C T
(12) INTERNATIONAL APPLICATION PUBLISHED UNDER THE PATENT COOPERATION TREATY (PCT) (19) World Intellectual Property Organization International Bureau (10) International Publication Number (43) International Publication Date WO 2017/106925 Al 29 June 2017 (29.06.2017) P O P C T (51) International Patent Classification: BZ, CA, CH, CL, CN, CO, CR, CU, CZ, DE, DJ, DK, DM, C22B 26/12 (2006.01) C22B 3/06 (2006.01) DO, DZ, EC, EE, EG, ES, FI, GB, GD, GE, GH, GM, GT, HN, HR, HU, ID, IL, IN, IR, IS, JP, KE, KG, KH, KN, (21) International Application Number: KP, KR, KW, KZ, LA, LC, LK, LR, LS, LU, LY, MA, PCT/AU20 16/05 1278 MD, ME, MG, MK, MN, MW, MX, MY, MZ, NA, NG, (22) International Filing Date: NI, NO, NZ, OM, PA, PE, PG, PH, PL, PT, QA, RO, RS, 22 December 2016 (22. 12.2016) RU, RW, SA, SC, SD, SE, SG, SK, SL, SM, ST, SV, SY, TH, TJ, TM, TN, TR, TT, TZ, UA, UG, US, UZ, VC, VN, (25) Filing Language: English ZA, ZM, ZW. (26) Publication Language: English (84) Designated States (unless otherwise indicated, for every (30) Priority Data: kind of regional protection available): ARIPO (BW, GH, 20159053 17 22 December 201 5 (22. 12.2015) AU GM, KE, LR, LS, MW, MZ, NA, RW, SD, SL, ST, SZ, 2016900774 2 March 2016 (02.03.2016) AU TZ, UG, ZM, ZW), Eurasian (AM, AZ, BY, KG, KZ, RU, TJ, TM), European (AL, AT, BE, BG, CH, CY, CZ, DE, (72) Inventor; and DK, EE, ES, FI, FR, GB, GR, HR, HU, IE, IS, IT, LT, LU, (71) Applicant : HUNWICK, Richard [AU/AU]; 59 Abing LV, MC, MK, MT, NL, NO, PL, PT, RO, RS, SE, SI, SK, don Road, Roseville, New South Wales 2069 (AU). -
Table of Contents
TABLE OF CONTENTS ACKNOWLEDGEMENTS iii TABLE OF CONTENTS iv LIST OF TABLES vi LIST OF FIGURES viii ABSTRACT xii CHAPTER 1 INTRODUCTION 1 1.1 Overview 1 1.2 Research Objectives and Organization of the Dissertation 2 CHAPTER 2 ALKLI SILICA REACTION AND RECYCLED CONCRETE 4 AGGREGATE 2.1 Alkali Silica Reaction (ASR) 4 2.1.1 ASR essentials 4 2.1.2 ASR mechanisms 5 2.1.3 ASR test methods review 7 2.1.4 Potential mitigation methods 9 2.2 Recycled Concrete Aggregate (RCA) 11 2.2.1 Recycled aggregate preview 11 2.2.2 RCA with ASR distress 13 2.2.3 RCA alkali contribution and alkali leaching 17 CHAPTER 3 PORE SOLUTION 19 3.1 Pore solution extraction 19 3.1.1 Instrumental introduction and description 19 3.1.2 Sample preparation 24 3.1.3 Extraction method and load scheme 25 3.2 Pore Solution Chemical Analysis 27 3.2.1 Alkali evolution process in pore solution 27 3.2.2 Pore solution test schemes and methods 29 3.2.3 Test results and analysis 32 iv CHAPTER 4 RCA ASR MITIGATION USING MINERAL ADMIXTURES 35 4.1 Fly Ash Mitigation 35 4.1.1 Fly ash as a concrete admixture 35 4.1.2 Mortar bar expansion test 38 4.1.3 Expansion results and comparison 42 4.1.4 Pore solution analysis 45 4.1.5 Mitigation mechanism analysis 49 4.2 Ground Granulated Blast Furnace Slag (GGBFS) Mitigation 54 4.2.1 Slag production and use in concrete 54 4.2.2 Expansion test results and comparison 55 4.2.3 Pore solution analysis and TGA 57 4.3 Silica Fume Mitigation 59 4.3.1 Expansion results and comparison 60 4.3.2 Pore solution analysis and TGA 65 4.3.3 Particle size issue 66 4.4 -
Zonation in Tourmaline from Granitic Pegmatites & the Occurrence of Tetrahedrally Coordinated Aluminum and Boron in Tourmaline
ZONATION IN TOURMALINE FROM GRANITIC PEGMATITES & THE OCCURRENCE OF TETRAHEDRALLY COORDINATED ALUMINUM AND BORON IN TOURMALINE by Aaron J. Lussier A Thesis submitted to the Faculty of Graduate Studies of The University of Manitoba in partial fulfilment of the requirements of the degree of DOCTOR OF PHILOSOPHY Department of Geological Sciences University of Manitoba Winnipeg Copyright © 2011 by Aaron J. Lussier ABSTRACT [1] Four specimens of zoned tourmaline from granitic pegmatites are characterised in detail, each having unusual compositional and/or morphologic features: (1) a crystal from Black Rapids Glacier, Alaska, showing a central pink zone of elbaite mantled by a thin rim of green liddicoatite; (2) a large (~25 cm) slab of Madagascar liddicoatite cut along (001) showing complex patterns of oscillatory zoning; and (3) a wheatsheaf and (4) a mushroom elbaite from Mogok, Myanmar, both showing extensive bifurcation of fibrous crystals originating from a central core crystal, and showing pronounced discontinuous colour zoning. Crystal chemistry and crystal structure of these samples are characterised by SREF, EMPA, and 11B and 27Al MAS NMR and Mössbauer spectroscopies. For each sample, compositional change, as a function of crystal growth, is characterised by EMPA traverses, and the total chemical variation is reduced to a series of linear substitution mechanisms. Of particular interest are substitutions accommodating the variation in [4]B: (1) TB + YAl ↔ TSi + Y(Fe, Mn)2+, where T Y T Y transition metals are present, and (2) B2 + Al ↔ Si2 + Li, where transition metals are absent. Integration of all data sets delineates constraints on melt evolution and crystal growth mechanisms. -
Winter 2007 Gems & Gemology
G EMS & G VOLUME XLIII WINTER 2007 EMOLOGY CVD Synthetic Diamonds Canary Tourmaline W Fluorescence Spectroscopy INTER Napoleon Necklace 2007 P AGES 291–408 V OLUME 43 N O. 4 THE QUARTERLY JOURNAL OF THE GEMOLOGICAL INSTITUTE OF AMERICA ® Winter 2007 VOLUME 43, NO. 4 291 LETTERS ________ FEATURE ARTICLES _____________ 294 Latest-Generation CVD-Grown Synthetic Diamonds from Apollo Diamond Inc. Wuyi Wang, Matthew S. Hall, Kyaw Soe Moe, Joshua Tower, and Thomas M. Moses Presents the gemological and spectroscopic properties of Apollo’s latest products, which show significant improvements in size, color, and clarity. 314 Yellow Mn-rich Tourmaline from the Canary Mining Area, Zambia pg. 295 Carat Points Brendan M. Laurs, William B. Simmons, George R. Rossman, Eric A. Fritz, John I. Koivula, Björn Anckar, and Alexander U. Falster Explores the vivid “canary” yellow elbaite from the Lundazi District of eastern Zambia, the most important source of this tourmaline. 332 Fluorescence Spectra of Colored Diamonds Using a Rapid, Mobile Spectrometer Sally Eaton-Magaña, Jeffrey E. Post, Peter J. Heaney, Roy A. Walters, Christopher M. Breeding, and James E. Butler Reports on the use of fluorescence spectroscopy to characterize colored diamonds from the Aurora Butterfly and other collections. NOTES AND NEW TECHNIQUES ________ 352 An Examination of the Napoleon Diamond Necklace Eloïse Gaillou and Jeffrey E. Post pg. 329 Provides a history and gemological characterization of this historic necklace. REGULAR FEATURES _____________________ 358 Lab Notes Apatite in spessartine • Atypical photoluminescence feature in a type IIa diamond • Diamond with “holiday” inclusions • Diamond with large etch channels containing iron sulfides • Black diamond with an oriented etch channel • The pareidolia of diamonds • Notable emerald carving • Gold coated onyx • Double-star sapphire • Imitation turquoise 366 Gem News International Record auction prices for diamonds • Namibian diamond mining pg. -
Molten Salts : Volume 1, Electrical Conductance, Density, and Viscosity
$ ! i v i A111D2 14bD5b NAT'L INST OF A111021 46056 * : :-• >. f. 5 i >2 > * i I v : : J, ; ; t i r t » * ? w &? * f 4 ?i ? >t»t wm W «il NBS PUBLICATIONS :• •• s r. • ? f ? ? •/? . ; f rrx: •:sn>ri r in; t 5 n * f\ p - ujuirxs) •«»': ts xrnm'ivtj: UNITED STATES DEPARTMENT OF COMMERCE C. R. Smith, Secretary NATIONAL BUREAU OF STANDARDS • A. V. Astin, Director U Molten Salts: Volume 1, Electrical Conductance, Density, and Viscosity Data G. J. Janz,* F. W. Dampier,* G. R. Lakshminarayanan,* P. K. Lorenz,* and R. P. T. Tomkins* *This report was prepared under contract at the Molten Salts Data Center Rensselaer Polytechnic Institute, Troy, N.Y. 12180 NSRDS-NBS 15 National Standard Reference Data Series- National Bureau of Standards 15 Issued October 1968 For sale by the Superintendent of Documents, U.S. Government Printing Office Washington, D.C. 20402 - Price S3. 00 National NOV 2 9 1968 142552 Q1IOO \)^i No - /i> 6 / Library of Congress Catalog Card Number: 68-60051 Foreword The National Standard Reference Data System is a Government-wide effort to provide for the technical community of the United States effective access to the quantitative data of physical science, critically evaluated and compiled for convenience, and readily accessible through a variety of distribution channels. The System was established in 1963 by action of the President’s Office of Science and Technology and the Federal Council for Science and Technology. The responsibility to administer the System was assigned to the National Bureau of Standards and an Office of Standard Reference Data was set up at the Bureau for this purpose. -
Wo 2009/148640 A2
(12) INTERNATIONAL APPLICATION PUBLISHED UNDER THE PATENT COOPERATION TREATY (PCT) (19) World Intellectual Property Organization International Bureau (10) International Publication Number (43) International Publication Date 10 December 2009 (10.12.2009) WO 2009/148640 A2 (51) International Patent Classification [US/US], 293 1 Horizon Ln, Rochester Hills, MI 48309 F28D 20/02 (2006 01) (US) (21) International Application Number (74) Agent FINERMAN, Terry, M., Dobrusm & Thennisch PCT/US2009/034647 PC, 29 W Lawrence Street, Suite 210, Pontiac, MI 48342 (US) (22) International Filing Date 20 February 2009 (20 02 2009) (81) Designated States (unless otherwise indicated, for every kind of national protection available) AE, AG, AL, AM, (25) Filing Language English AO, AT, AU, AZ, BA, BB, BG, BH, BR, BW, BY, BZ, (26) Publication Language English CA, CH, CN, CO, CR, CU, CZ, DE, DK, DM, DO, DZ, EC, EE, EG, ES, FI, GB, GD, GE, GH, GM, GT, HN, (30) Priority Data HR, HU, ID, IL, IN, IS, JP, KE, KG, KM, KN, KP, KR, 61/030,755 22 February 2008 (22 02 2008) US KZ, LA, LC, LK, LR, LS, LT, LU, LY, MA, MD, ME, 61/061,908 16 June 2008 (16 06 2008) US MG, MK, MN, MW, MX, MY, MZ, NA, NG, NI, NO, 61/074,869 23 June 2008 (23 06 2008) us NZ, OM, PG, PH, PL, PT, RO, RS, RU, SC, SD, SE, SG, 61/074,889 23 June 2008 (23 06 2008) us SK, SL, SM, ST, SV, SY, TJ, TM, TN, TR, TT, TZ, UA, 61/074,799 23 June 2008 (23 06 2008) us UG, US, UZ, VC, VN, ZA, ZM, ZW 61/074,840 23 June 2008 (23 06 2008) us 61/090,084 19 August 2008 (19 08 2008) us (84) Designated States (unless otherwise indicated, for every 12/389,598 20 February 2009 (20 02 2009) us kind of regional protection available) ARIPO (BW, GH, GM, KE, LS, MW, MZ, NA, SD, SL, SZ, TZ, UG, ZM, (71) Applicant (for all designated States except US) DOW ZW), Eurasian (AM, AZ, BY, KG, KZ, MD, RU, TJ, GLOBAL TECHNOLOGIES INC. -
Mitigating Alkali Silica Reaction in Recycled Concrete Xinghe Li University of New Hampshire, Durham
University of New Hampshire University of New Hampshire Scholars' Repository Doctoral Dissertations Student Scholarship Winter 2005 Mitigating alkali silica reaction in recycled concrete Xinghe Li University of New Hampshire, Durham Follow this and additional works at: https://scholars.unh.edu/dissertation Recommended Citation Li, Xinghe, "Mitigating alkali silica reaction in recycled concrete" (2005). Doctoral Dissertations. 306. https://scholars.unh.edu/dissertation/306 This Dissertation is brought to you for free and open access by the Student Scholarship at University of New Hampshire Scholars' Repository. It has been accepted for inclusion in Doctoral Dissertations by an authorized administrator of University of New Hampshire Scholars' Repository. For more information, please contact [email protected]. MITIGATING ALKALI SILICA REACTION IN RECYCLED CONCRETE BY XINGI1E LI B.S. in Materials Engineering, Harbin University of Civil Engineering and Architecture, P. R. China 1995 M.S. in Civil Engineering, Harbin University of Civil Engineering and Architecture, P. R. China 1998 DISSERTATION Submitted to the University of New Hampshire in Partial Fulfillment of the Requirements for The Degree of Doctor of Philosophy in Civil Engineering December, 2005 Reproduced with permission of the copyright owner. Further reproduction prohibited without permission. UMI Number: 3198011 INFORMATION TO USERS The quality of this reproduction is dependent upon the quality of the copy submitted. Broken or indistinct print, colored or poor quality illustrations and photographs, print bleed-through, substandard margins, and improper alignment can adversely affect reproduction. In the unlikely event that the author did not send a complete manuscript and there are missing pages, these will be noted. Also, if unauthorized copyright material had to be removed, a note will indicate the deletion. -
Dupont™ Kalrez® Chemical Resistance and Fluid Compatability, Including All Chemicals Under the Clean Air
DuPont™ Kalrez® Chemical Resistance and Fluid Compatibility, Including All Chemicals Under the Clean Air Act Technical Information—Rev. 4, July 2010 DuPont™ Kalrez® perfluoroelastomer parts combine the elastomeric properties of fluoroelastomers with the chemical resistance of DuPont™ Teflon® fluoropolymer resins. Due to its unique properties, Kalrez® parts should be considered for service in all applications and environments where dependable, long-term service is desired, as well as in hot or aggressive environments that are beyond the service ability of common elastomers. This guide is intended to provide assistance in determining the suitability of seven commercially available elastomers—nitrile (NBR), ethylene propylene (EPDM), silicone (VMQ), fluorosilicone (FVMQ), vinylidene fluoride-based fluoroelastomer (FKM), polysulfides (T), and Kalrez® perfluoroelastomer parts—for service in over 1,600 chemicals and fluids. The criteria used for these ratings included volume swell resistance based on laboratory immersion testing, laboratory aging tests, actual field experience, and informed judgments based on experience in similar chemical groups. The ratings for the six common elastomers are based on published literature and are offered for general comparative purposes only—we cannot guarantee their accuracy nor assume responsibility for their use. Thermal Stability The ratings for these six common elastomers may be overly optimistic for elevated temperature and/or high concentration applications because many are based on ambient temperature testing. Suitability of these elastomers for service at elevated temperatures rapidly diminishes because higher temperatures increase the effects of chemicals on the base polymer as well as the cross-link systems. Serviceability is further limited by the upper service temperature limit of each polymer. -
Technical Report for the Substantial Modification Rule for 62-730, F.A.C
Technical Report for the Substantial Modification Rule for 62-730, F.A.C. Prepared for the Hazardous Waste Regulation Section Florida Department of Environmental Protection By Kendra F. Goff, Ph. D. Stephen M. Roberts, Ph.D. Center for Environmental & Human Toxicology University of Florida Gainesville, Florida August 1, 2008 During an adverse event, such as a fire or explosion, hazardous materials from a storage or transfer facility may be released into the atmosphere. The potential human health impacts of such a release are assessed through air modeling coupled with chemical-specific inhalation criteria for short-term exposures. With this approach, distances from the facility over which differing levels of health effects from inhalation of airborne hazardous materials are expected can be predicted. Because the movement in air and toxic potency varies among chemicals, the potential impact area for a facility is dependent upon the chemicals present and their quantities. The impact area can be calculated for a facility under current and possible future conditions. This information can be used to determine whether proposed changes in storage conditions or the nature and quantities of chemicals handled would result in a substantial difference in the area of potential impact. The following sections provide technical guidance on how impact areas for facilities handling hazardous materials under Chapter 62-730, F.A.C. should be determined. Air modeling. Any model used for the purposes of demonstration must be capable of producing results in accordance with worst-case scenario provisions of Program 3 of the Accidental Release Prevention Program of s. 112(r)(7) of the Clean Air Act. -
O-Ring Chemical Compatibility
O-Ring Chemical Compatibility buna-n | capfe | chemraz® | epdm | fetfe | kalrez® | silicone | viton® a The information in this document is intended to be for general reference purposes only and is not intended to be a specific recommendation for any individual application. Any reliance on information is therefore at the user‘s own risk. In no event will Ace Glass Incorporated be liable for any loss, damage, claim or expense directly or indirectly arising or resulting from the use of any information provided in this document. While every effort is made to ensure the accuracy of information contained herewith, Ace Glass www.aceglass.com Incorporated cannot warrant the accuracy or completeness of information. Specifications are subject to change without prior notice. Although they are represented to be accurate, it is best to verify product specifications with ACE prior to purchase in the event they have been changed since publication of this catalog. Table of Contents Elastomers .....................................................4-5 Chemical Compatibility ................................ 6-20 Cross Reference .............................................. 21 Size Reference ........................................... 22-31 O-Rings Kalrez ........................................................ 32 Chemraz .................................................... 33 CAPFE ....................................................... 34 Viton A .................................................. 36-37 Silicone ................................................ -
Write the Formula for Each Compound, Atom Or Ion 1. Acetate Ion 2. Calcium
Write the formula for each compound, atom or ion 1. acetate ion 27. barium chloride 2. calcium hydroxide 28. calcium oxide 3. magnesium sulfate 29. barium ion 4. aluminum 30. magnesium phosphate 5. lithium carbonate 31. lithium sulfide 6. barium nitrate 32. barium sulfite 7. aluminum ion 33. calcium nitrate 8. calcium bromide 34. magnesium iodide 9. magnesium fluoride 35. beryllium ion 10. ammonium ion 36. lithium chloride 11. lithium oxide 37. barium nitrite 12. barium phosphate 38. calcium phosphate 13. antimony (III) ion 39. magnesium sulfide 14. calcium sulfate 40. bicarbonate ion 15. magnesium carbonate 41. lithium sulfite 16. lithium nitrate 42. barium phosphite 17. barium iodide 43. calcium iodide 18. antimony (V) ion 44. biphosphate ion 19. calcium fluoride 45. magnesium chloride 20. magnesium oxide 46. lithium nitrite 21. lithium phosphate 47. barium dichromate 22. barium sulfide 48. calcium sulfide 23. arsenide ion 49. bismuth (III) ion 24. calcium carbonate 50. magnesium sulfite 25. magnesium nitrate 51. lithium phosphite 26. lithium iodide 52. barium chromate 53. calcium chloride 79. bromine 54. magnesium nitrite 80. potassium carbonate 55. bismuth (V) ion 81. ammonium nitrate 56. lithium dichromate 82. aluminum iodide 57. barium bicarbonate 83. sodium chloride 58. calcium sulfite 84. cadmium ion 59. magnesium phosphite 85. potassium oxide 60. bisulfate ion 86. ammonium phosphate 61. lithium chromate 87. aluminum sulfide 62. barium hydrogen sulfate 88. calcium 63. potassium phosphite 89. sodium sulfite 64. ammonium chromate 90. potassium nitrate 65. bisulfite ion 91. ammonium iodide 66. potassium bromide 92. aluminum chloride 67. ammonium fluoride 93. sodium nitrite 68. aluminum oxide 94. -
Table 4: Protective Action Criteria (PAC) Rev 27 Based on Applicable 60-Minute Aegls, Erpgs, Or Teels
Table 4: Protective Action Criteria (PAC) Rev 27 based on applicable 60-minute AEGLs, ERPGs, or TEELs. The chemicals are listed in 3 alphabetical order and the values are presented in mg/m . February 2012 Table 4 is an alphabetical list of the chemical substances and their corresponding PAC values in mass per unit volume (mg/m3). The conversion of ppm to mg/m3 was carried out assuming normal temperature and pressure, 25°C and 760 mm Hg. The columns presented in Table 4 provide the following information: Heading Definition No. The ordered numbering of the chemicals as they appear in this alphabetical listing Chemical Name The name of the chemical substance submitted to the PAC development team CASRN The Chemical Abstracts Service Registry Number1 for this chemical PAC-1 Based on the applicable AEGL-1, ERPG-1, or TEEL-1 value PAC-2 Based on the applicable AEGL-2, ERPG-2, or TEEL-2 value PAC-3 Based on the applicable AEGL-3, ERPG-3, or TEEL-3 value Chemicals for which AEGLs are available have their chemical name, CASRN, and AEGL values displayed in a bolded and larger font. Chemicals for which ERPGs are available, but not AEGLs, have their chemical name, CASRN, and ERPG values displayed in a bolded font. Chemicals for which TEELs are available, but no AEGLs or ERPGs, have their chemical name, CASRN, and values displayed using a regular font. Additional information on PAC values and TEEL values and links to other sources of information is provided on the Subcommittee on Consequence Assessment and Protective Actions (SCAPA) webpage at: http://orise.orau.gov/emi/scapa/teels.htm.