Design of Four Bar Chainless Bicycle -Anthroprometric and Kinematic Analysis K
Total Page:16
File Type:pdf, Size:1020Kb
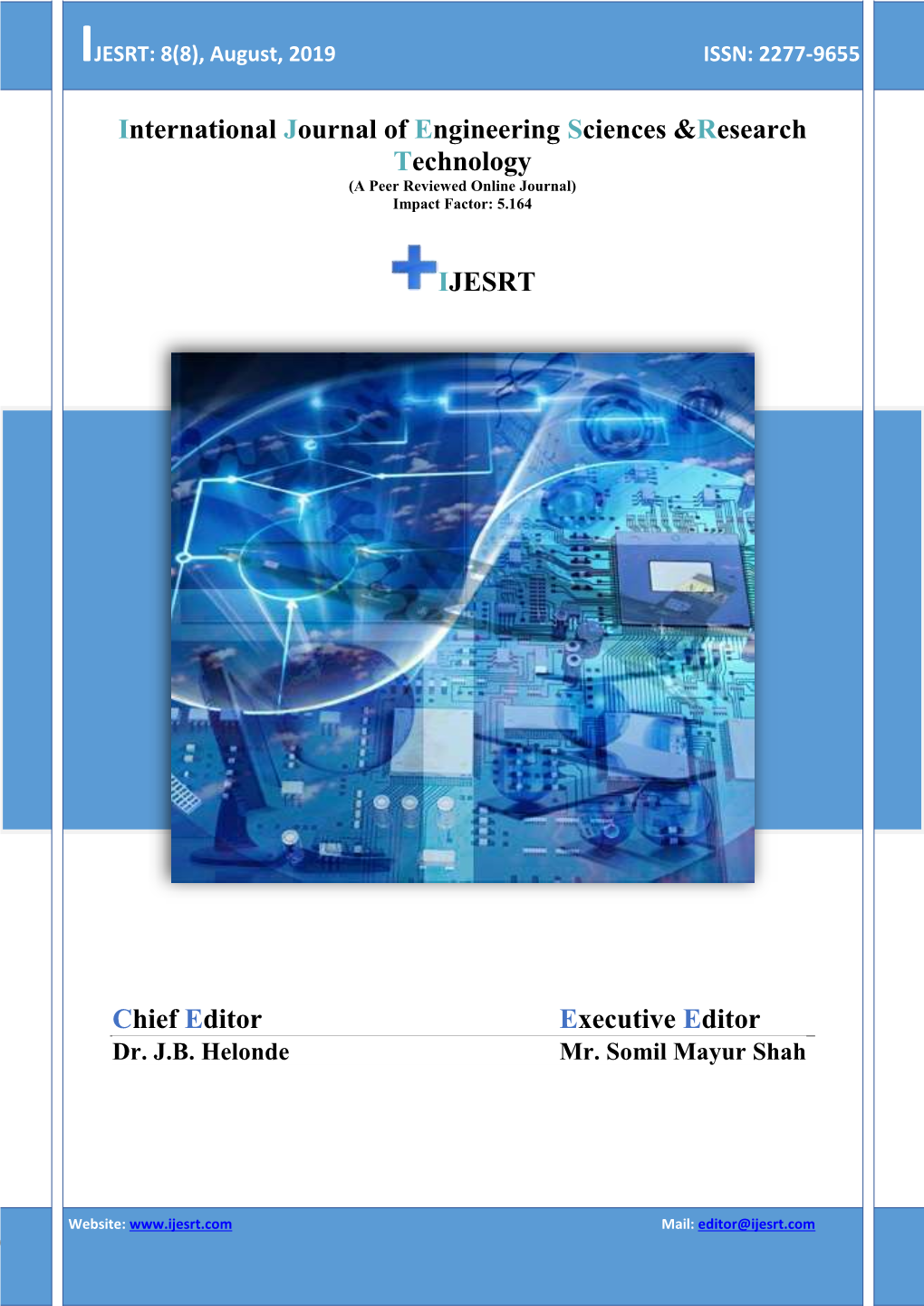
Load more
Recommended publications
-
Copake Auction Inc. PO BOX H - 266 Route 7A Copake, NY 12516
Copake Auction Inc. PO BOX H - 266 Route 7A Copake, NY 12516 Phone: 518-329-1142 December 1, 2012 Pedaling History Bicycle Museum Auction 12/1/2012 LOT # LOT # 1 19th c. Pierce Poster Framed 6 Royal Doulton Pitcher and Tumbler 19th c. Pierce Poster Framed. Site, 81" x 41". English Doulton Lambeth Pitcher 161, and "Niagara Lith. Co. Buffalo, NY 1898". Superb Royal-Doulton tumbler 1957. Estimate: 75.00 - condition, probably the best known example. 125.00 Estimate: 3,000.00 - 5,000.00 7 League Shaft Drive Chainless Bicycle 2 46" Springfield Roadster High Wheel Safety Bicycle C. 1895 League, first commercial chainless, C. 1889 46" Springfield Roadster high wheel rideable, very rare, replaced headbadge, grips safety. Rare, serial #2054, restored, rideable. and spokes. Estimate: 3,200.00 - 3,700.00 Estimate: 4,500.00 - 5,000.00 8 Wood Brothers Boneshaker Bicycle 3 50" Victor High Wheel Ordinary Bicycle C. 1869 Wood Brothers boneshaker, 596 C. 1888 50" Victor "Junior" high wheel, serial Broadway, NYC, acorn pedals, good rideable, #119, restored, rideable. Estimate: 1,600.00 - 37" x 31" diameter wheels. Estimate: 3,000.00 - 1,800.00 4,000.00 4 46" Gormully & Jeffrey High Wheel Ordinary Bicycle 9 Elliott Hickory Hard Tire Safety Bicycle C. 1886 46" Gormully & Jeffrey High Wheel C. 1891 Elliott Hickory model B. Restored and "Challenge", older restoration, incorrect step. rideable, 32" x 26" diameter wheels. Estimate: Estimate: 1,700.00 - 1,900.00 2,800.00 - 3,300.00 4a Gormully & Jeffery High Wheel Safety Bicycle 10 Columbia High Wheel Ordinary Bicycle C. -
Shooting Star: a Biography of a Bicycle
SHOOTING STAR: A BIOGRAPHY OF A BICYCLE Geoff Mentzer 2 SHOOTING STAR: A BIOGRAPHY OF A BICYCLE Copyright © 2020 by Geoff Mentzer All rights reserved. 3 In a scientific study of various living species and machines, the most efficient at locomotion – that is, the least amount of energy expended to move a kilometre – was found to be a man on a bicycle. –SS Wilson, Scientific American, March 1973, Volume 228, Issue 3, 90 The Dandy Horse of 1818, said to be the first velocipede man-motor carriage. Sharp, Bicycles & Tricycles: An Elementary Treatise On Their Design And Construction, Longmans, Green, and Co, London, New York and Bombay, 1896, 147 4 INTRODUCTION AND ACKNOWLEDGEMENTS What began as a brief biograph of the author's forebear Walter William Curties soon doubled into a study of two men, and expanded into an account of early bicycle – and a little motoring – history in New Zealand. Curties is mostly invisible to history, while Frederick Nelson Adams – who rose to national pre-eminence in motoring circles – by his reticence and reluctance for public exposure is also largely overlooked. Pioneering New Zealand cycling and motoring history – commercial, industrial and social – have been variously covered elsewhere, in cursory to comprehensive chronicles. Sadly, factual errors that persist are proof of copy and paste research. As examples, neither Nicky Oates nor Frederick Adams' brother Harry was the first person convicted in New Zealand for a motoring offence, nor was the world's first bicycle brass band formed in New Zealand. It must be said, however, that today we have one great advantage, ie Papers Past, that progeny of the Turnbull Library in Wellington. -
23Rd Annual Antique & Classic Bicycle Auction
CATALOG PRICE $4.00 Michael E. Fallon / Seth E. Fallon COPAKE AUCTION INC. 266 Rt. 7A - Box H, Copake, N.Y. 12516 PHONE (518) 329-1142 FAX (518) 329-3369 Email: [email protected] Website: www.copakeauction.com 23rd Annual Antique & Classic Bicycle Auction Featuring the David Metz Collection Also to include a selection of ephemera from the Pedaling History Museum, a Large collection of Bicycle Lamps from the Midwest and other quality bicycles, toys, accessories, books, medals, art and more! ************************************************** Auction: Saturday April 12, 2014 @ 9:00 am Swap Meet: Friday April 11th (dawn ‘til dusk) Preview: Thur. – Fri. April 10-11: 11-5pm, Sat. April 12, 8-9am TERMS: Everything sold “as is”. No condition reports in descriptions. Bidder must look over every lot to determine condition and authenticity. Cash or Travelers Checks - MasterCard, Visa and Discover Accepted First time buyers cannot pay by check without a bank letter of credit 17% buyer's premium (2% discount for Cash or Check) 20% buyer's premium for LIVE AUCTIONEERS Accepting Quality Consignments for All Upcoming Sales National Auctioneers Association - NYS Auctioneers Association CONDITIONS OF SALE 1. Some of the lots in this sale are offered subject to a reserve. This reserve is a confidential minimum price agreed upon by the consignor & COPAKE AUCTION below which the lot will not be sold. In any event when a lot is subject to a reserve, the auctioneer may reject any bid not adequate to the value of the lot. 2. All items are sold "as is" and neither the auctioneer nor the consignor makes any warranties or representations of any kind with respect to the items, and in no event shall they be responsible for the correctness of the catalogue or other description of the physical condition, size, quality, rarity, importance, medium, provenance, period, source, origin or historical relevance of the items and no statement anywhere, whether oral or written, shall be deemed such a warranty or representation. -
FABRICATION and DEVELOPMENT of CHAINLESS BI-CYCLE Dr.Raghavendra Joshi1,Mayur.D.Pawar2, Shahid Ali3, Mohammed Bilal.K4, Rizwan5,V Muneer Ahmed6
JASC: Journal of Applied Science and Computations ISSN NO: 1076-5131 FABRICATION AND DEVELOPMENT OF CHAINLESS BI-CYCLE Dr.Raghavendra Joshi1,Mayur.D.Pawar2, Shahid ali3, Mohammed bilal.k4, Rizwan5,V Muneer Ahmed6 Professor, mechanical engineering department, BITM, Ballari-583104, Karnataka Assistant professor, mechanical engineering department,BITM, Ballari-583104, Karnataka UG student, mechanical engineering department,BITM, Ballari-583104,Karnataka UG student, mechanical engineering department,BITM, Ballari-583104,Karnataka UG student, mechanical engineering department,BITM, Ballari-583104,Karnataka UG student, mechanical engineering department,BITM, Ballari-583104,Karnataka [email protected] [email protected] [email protected] [email protected] [email protected] [email protected] Abstract— This project is developed from the users to rotate the back wheel of bi-cycle using propeller shaft. Power transmission through chain drive is the oldest and widest method in case of bi-cycle . In this paper we implemented the chainless transmission to the bicycle to overcome the various disadvantages of chain drive. Shaft drive were introduced over a century ago , but were mostly supplanted by chain driven bi-cycle . Usually in bicycle chain and sprocket is used to drive the back wheel. The shaft drive only need periodic lubrication using grease gun to keep the gears running quite and smooth. A shaft driven bi-cycle is a bi-cycle that uses a shaft drive instead of a join which consist two sprockets with bearings at the both end of shaft connected to pedal crank and rear wheel gear to make a new kind of transmission system for bi-cycle for getting high reliability system, and more safe system. -
BEARING LINKAGE POWERED BICYCLE Prof
BEARING LINKAGE POWERED BICYCLE Prof. S. V. Deshpande¹, Ajinkya V. Waghade², Mayur D. Wadulkar³, Madhusudan M. Sonwane4 Sunilkumar Wagh5 1Asst. Professor, 2,3,4,5Student, Dept of Mechanical Engg, GSMCOE Balewadi, Pune (India) ABSTRACT Considering the depletion of fossil fuel resulting into pollution it is a need of time to minimize conventional power and boost the utilization of mechanical non-conventional power sources. Currently, fuel powered bicycle are available but they are using conventional source. The research entitled “BEARING LINKAGE POWERED BICYCLE” includes concept of renewable energy. Power is generated through alternator mounted at periphery of rear wheel. A chainless bicycle using bearing linkage assembly is provided for pedalling. In addition to this two small rotary fan are mounted upon the front wheel of bicycle generating power by using wind source. This generated power is supplied to mechanical motor through battery which are mounted on carrier of rear wheel. When the rider is pedalling a bicycle, a motion is transmitted from sprocket of extended shaft of motor to rear wheel through chain drive. The outcome of this system is to relief the human efforts by transmitting high speed rotation using non conventional powered motor which is also applicable for long drives. It does not affect the environment (GWG) with no fuel consumption & cost of utilization is zero. Keywords: Mechanical powered motor, non conventional power, speed ratio. I. INTRODUCTION India is the second-largest country of the world, undergoing explosive growth. Like many other countries where agriculture is the main activity, biomass and other non – commercial fuels constitute around 40% of energy requirements in India. -
1990) Through 25Th (2014
CUMULATIVE INDEX TO THE PROCEEDINGS OF THE INTERNATIONAL CYCLE HISTORY CONFERENCES 1st (1990) through 25th (2014) Prepared by Gary W. Sanderson (Edition of February 2015) KEY TO INDEXES A. Indexed by Authors -- pp. 1-14 B. General Index of Subjects in Papers - pp. 1-20 Copies of all volumes of the proceedings of the International Cycling History Conference can be found in the United States Library of Congress, Washington, DC (U.S.A.), and in the British National Library in London (England). Access to these documents can be accomplished by following the directions outlined as follows: For the U.S. Library of Congress: Scholars will find all volumes of the International Cycling History Conference Proceedings in the collection of the United States Library of Congress in Washington, DC. To view Library materials, you must have a reader registration card, which is free but requires an in-person visit. Once registered, you can read an ICHC volume by searching the online catalog for the appropriate call number and then submitting a call slip at a reading room in the Library's Jefferson Building or Adams Building. For detailed instructions, visit www.loc.gov. For the British Library: The British Library holds copies of all of the Proceedings from Volume 1 through Volume 25. To consult these you will need to register with The British Library for a Reader Pass. You will usually need to be over 18 years of age. You can't browse in the British Library’s Reading Rooms to see what you want; readers search the online catalogue then order their items from storage and wait to collect them. -
Spring 2019 Student Sustainability Grant Total Funds Requested: $85,848.00 Total Funds Allocated: $68,553.94
Spring 2019 Student Sustainability Grant Total Funds Requested: $85,848.00 Total Funds AlloCated: $68,553.94 1. Bird-Friendly Window Design Principal Investigators: Mary Clare Griffith & Jonathon Eiseman FaCulty/Staff Advisor: Denise Keele Abstract: Up to one billion birds are killed by window collisions in the United States annually. Based on preliminary research, certain loCations on WMU’s Campus are known to result in Collisions and avian mortality. WMU has a Commitment to minimize environmental impaCt, and building Collisions resulting in bird deaths are not consistent with sustainability goals. Bird-window collisions are preventable, as low-cost materials and solutions are available for implementation, to mitigate existing buildings. This projeCt seeks to implement bird- friendly modifiCations on existing windows at two walkway/Bridgeway loCations on WMU Campus: 1) HaeniCke-Wood Hall and 2) Wood Hall-Chemistry. These modifiCations would decrease avian mortality, provide opportunity for post-installation monitoring, and serve as demonstration areas to eduCate our Campus Community to hopefully inspire future planning and further appliCation of bird-friendly design standards at WMU. Two materials (bird tape and window film) will be applied (one at eaCh loCation) in order to demonstrate potential options and gain experienCe to better inform potential future produCt choices. Amount Requested: $35,400 Amount AlloCated: $16,100 2. Sunbolt Campus XL Solar Work Station: AdvanCing and Studying Sustainability on Campus. PrinCipal Investigator: Sage Campbell & Chantel Oah FaCulty/Staff Advisor: Dr. Heather MCGee Abstract: This study will investigate the effeCts of graphiC prompts with integrated quiCk response (QR) Codes posted to a solar Charging benCh. The hypothesis is that posted prompts and the benCh itself will inCrease website traffiC and visibility of sustainable aCtions at Western MiChigan University. -
20Th Annual Antique & Classic Bicycle Auction
CATALOG PRICE $4.00 Michael E. Fallon Seth E. Fallon COPAKE AUCTION INC. 266 Rt. 7A - Box H, Copake, N.Y. 12516 PHONE (518) 329-1142 FAX (518) 329-3369 Email: [email protected] Website: www.copakeauction.com 20th Annual Antique & Classic Bicycle Auction ************************************ Auction: Saturday April 16, 2011 at 10 am Swap Meet: Friday April 15th Dawn ‘til Dusk Always Accepting Quality Consignments – Contact Us! TERMS: Everything sold “as is”. No condition reports in descriptions. Bidder must look over every lot to determine condition and authenticity. Cash or Travelers Checks Mastercard, Visa and Discover Accepted First time buyers cannot pay by check without a bank letter of credit 15% BUYERS PREMIUM (2% discount for payment of cash or check) National Auctioneers Association - NYS Auctioneers Association CONDITIONS OF SALE 1. Some of the lots in this sale are offered subject to a reserve. This reserve is a confidential minimum price agreed upon by the consignor & COPAKE AUCTION below which the lot will not be sold. In any event when a lot is subject to a reserve, the auctioneer may reject any bid not adequate to the value of the lot. 2. All items are sold "as is" and neither the auctioneer nor the consignor makes any warranties or representations of any kind with respect to the items, and in no event shall they be responsible for the correctness of the catalogue or other description of the physical condition, size, quality, rarity, importance, medium, provenance, period, source, origin or historical relevance of the items and no statement anywhere, whether oral or written, shall be deemed such a warranty or representation. -
Dynamic Chainless Bicycle
International Journal of Advance Research in Engineering, Science & Technology(IJAREST), ISSN(O):2393-9877, ISSN(P): 2394-2444, Volume 2,Issue 5, May- 2015 , Impact Factor:2.125 DYNAMIC CHAINLESS BICYCLE Mayur Linagariya1,Dignesh Savsani2 1 Mechanical Department, Noble Group Of Institute, Junagadh, [email protected] 2 Mechanical Department, Noble Group Of Institute, Junagadh, [email protected] Abstract A shaft-driven bicycle is a bicycle that uses a driven shaft instead of a chain to transmit power from the pedals to the wheel. Shaft drives were introduced over a century ago, but were mostly supplanted by chain-driven bicycles due to the gear ranges possible with sprockets and derailleur. Recently, due to advancements in internal gear technology, a small number of modern shaft-driven bicycles have been introduced. The shaft drive only needs periodic lubrication using a grease gun to keep the gears running quiet and smooth. This “chainless” drive system provides smooth, quite and efficient transfer of energy from the pedals to the rear wheel. It is attractive in look compare with chain driven bicycle. It replaces the traditional method. Keywords – Bevel Gears, Shaft drive, Dynamometer, Chainless technology, Reliable and Durable I. INTRODUCTOIN II. WORKING The shaft connected between the pair of The shaft connected between the pair of spiral spiral bevel gears. The main application of the bevel gears. The main application of the spiral spiral bevel gear is in a vehicle differential, where bevel gear is in a vehicle differential, where the the direction of drive from the drive shaft must be direction of drive from the drive shaft must be turned 90 degrees to drive the wheels. -
Bulletin 176. Manufactures. Bicycles and Tricycles
Twelfth Census of the United States. CENSUS 8ULl_ETINa No~ 176. WASHINGTON, D. C. MAY 81, 1902. MANUFACTURES. BICYCLES AND TRICYCLES. Hon. WILLIAM R. MERRIAl\1, Table 5 showing stn,tist1cs of capital for 1890 and 1900; Dfrecto'l' of tlw Census. Table 6 showing the kinds, quantity, and vahie of prod Sm: I transmit herewith, for publication in bulletin ucts miLnufacturecl iii the factories engaged exclusively form, a report on the manufacture of bicycles and tri in the manufacture of cycles for 1900; Table 7 showing cycles for the census year moo, prepared under my the number of establishments reporting cyeles as a 1)y direction by Mr. Axel J osephsson, of the Census Office. product and the quantity and value of their cycle prod The statistics included in the report were collected, uct, 1900; Table 8 showing the combined quantity and as in the previous census, upon the schedule used for value of products shown in Tables I~ and 7, the per cent general statistics of manufactures. But owing to the of each kind to the total number, ancl of the value of each extmorclinary development of the bicycle industry kind to the total value; all(l Table 9 presenting the de during the last decade, it was deeided to supplement the tailed statistics for the industry, by states, fol' 1900. canvass made by the enumerators and local special As the methods of taking the censuses of 1890 and agent8 with a 8pecial report. The manufacture of bi 1900 were almost identical, with the exceptions noted cycles and tricycle8 was first reported 1-Ls a separate below, the rate of growth in the·m1111nfactnre of bicy industry 11t the cernms of 1890, and this is the first time cles and tricycles nuty be practically inferred :from the it is made the subject of a special report. -
In Hub Gearbox Front Wheel Drive Cycles
In Hub Gearbox Front Wheel Drive Cycles Stephen Nurse 10 Abbott Grove, Clifton Hill, Vic 3068 Email for correspondence: [email protected] Abstract In 1999, Bike Culture Quarterly magazine and Thomas Kretschmer introduced the concept of a chainless bicycle featuring a wide range, front wheel drive gearbox hub. Twenty years later, the European company Kervelo are making production versions of these chainless gearbox cycles (Fig.1). This paper dis- cusses how Kervelos were developed by meeting needs and through dedica- ted individuals and companies. It considers effective uses for human power based on front wheel drive chainless gearbox technology. Figure 1: Thomas Kretschmer in 1999, Kervelo Cycle 2018 (Kretschmer, Kervelo) 1. Introduction Change is taking place in human- and low-powered transport, especially cargo- and e-bikes. More bike styles are becoming accepted for more uses as we realize exercise and low carbon economies are essential (Cox 2015). Change in the way we do things is sociotechnical change. It depends on emerging socio-technical frames and the ingenuity and emotional commit- ment of individuals who consider readily available, established products inadequate (Bijker 1995, p. 4, Nurse 2016). This paper discusses a cycle style currently gaining acceptance and looks forward to newer designs. 2. Background Direct front wheel drive cycles date back to Pierre Michaux’s wooden bone- shaker of 1865 (Bijker 1995, p. 27), and variations with speed-increasing gearboxes have existed since the 1891 Crypto Bantam. The Bantam was a form of safety cycle (Sharp 2003, p. 158), invented to make the liberating technology of the high wheel penny farthing less challenging and accessible to more people (Fig.2). -
24Th Annual Antique & Classic Bicycle Auction
CATALOG PRICE $4.00 Michael E. Fallon / Seth E. Fallon COPAKE AUCTION INC. 266 Rt. 7A - Box H, Copake, N.Y. 12516 PHONE (518) 329-1142 FAX (518) 329-3369 Email: [email protected] Website: www.copakeauction.com 24th Annual Antique & Classic Bicycle Auction Featuring the Howie Cohen Collection from Lafayette, Colorado, A Templeton, MA Collection, Select Additions from several European Museums, a Hollywood California collection of Bowden bicycles with memorabilia and over 200 bicycle lamps from the mid-west. ************************************************** Auction: Saturday April 18, 2015 @ 9:00 am Swap Meet: Friday April 17th (dawn ‘til dusk) Preview: Thur. – Fri. April 16-17: 11-5pm, Sat. April 18, 8-9am TERMS: Everything sold “as is”. No condition reports in descriptions. Bidder must look over every lot to determine condition and authenticity. Cash or Travelers Checks - MasterCard, Visa and Discover Accepted First time buyers cannot pay by check without a bank letter of credit 17% buyer's premium - 20% buyer's premium for LIVE AUCTIONEERS Accepting Quality Consignments for All Upcoming Sales National Auctioneers Association - NYS Auctioneers Association CONDITIONS OF SALE 1. Some of the lots in this sale are offered subject to a reserve. This reserve is a confidential minimum price agreed upon by the consignor & COPAKE AUCTION below which the lot will not be sold. In any event when a lot is subject to a reserve, the auctioneer may reject any bid not adequate to the value of the lot. 2. All items are sold "as is" and neither the auctioneer nor the consignor makes any warranties or representations of any kind with respect to the items, and in no event shall they be responsible for the correctness of the catalogue or other description of the physical condition, size, quality, rarity, importance, medium, provenance, period, source, origin or historical relevance of the items and no statement anywhere, whether oral or written, shall be deemed such a warranty or representation.