G-HARDENING of COMMERCIAL OFF the SHELF COMPONENTS for SMALL GUIDED PROJECTILES by JAKE DECOTO B.S. Aerospace Engineering, University of Washington, 2006
Total Page:16
File Type:pdf, Size:1020Kb
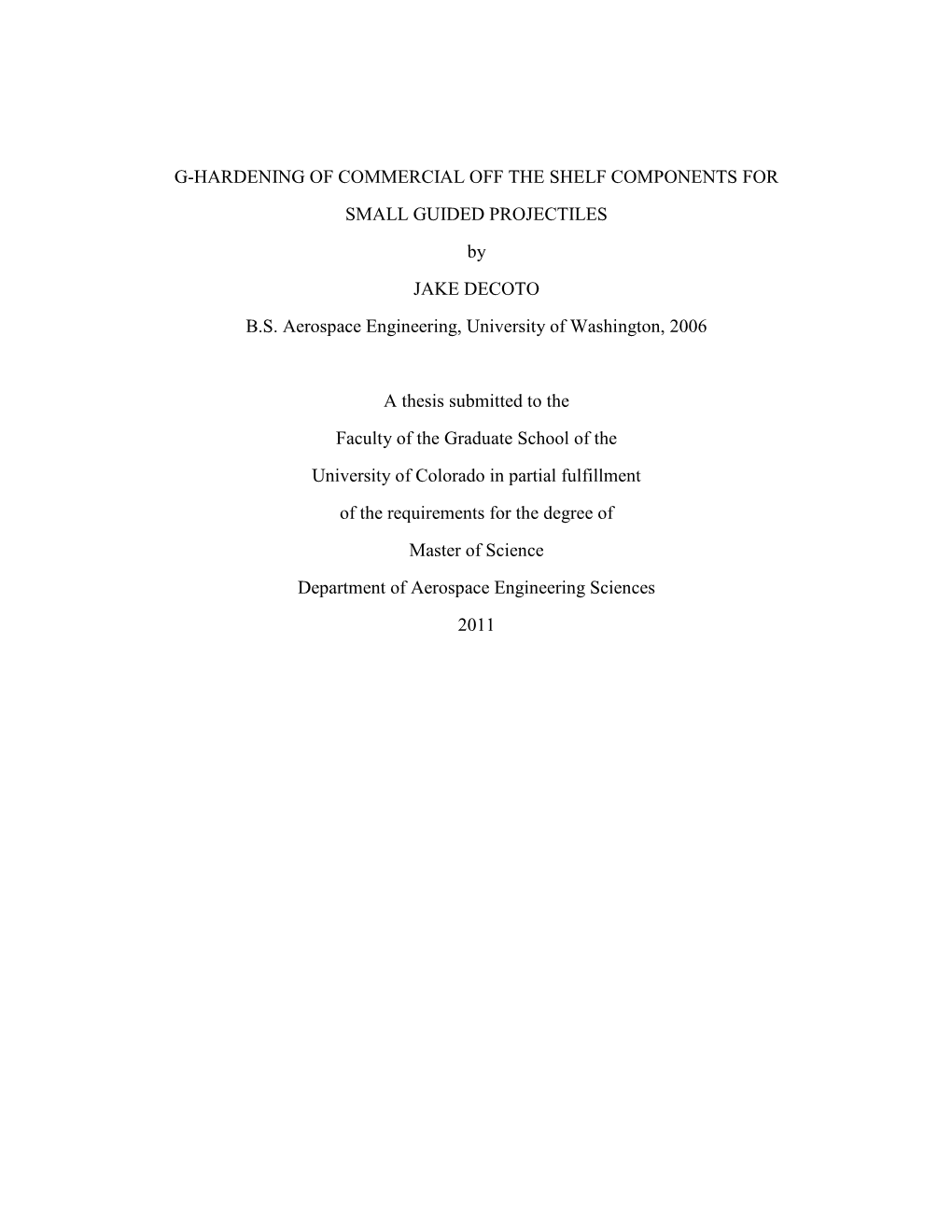
Load more
Recommended publications
-
Cbrn Protection Soldier Modernisation Debrief Malaysian Armed Forces Naval Guns Asia-Pacific Fighter Market Precision Guided Artillery
Volume 24/issue 3 april/may 2016 us$15 AsiA PA cific’s LA rgest c ircuLAted d efence MA g A Zine CBRN PROTECTION SOLDIER MODERNISATION DEBRIEF MALAYSIAN ARMED FORCES NAVAL GUNS ASIA-PACIFIC FIGHTER MARKET PRECISION GUIDED ARTILLERY www.asianmilitaryreview.com new Datron VHF ad FULL PAGE Armada.PDF 1 3/16/16 12:11 PM C M Y CM MY CY CMY K 02 | ASIAN MILITARY REVIEW | Contents april/may 2016 VOlUmE 24 / iSSUE 3 VexIng QueSTIonS 10 Malaysia faces both conventional and unconventional threats. Dzirhan Mahadzir examines how the country is meeting such risks in a fiscally-constrained climate. Front Cover Photo: Iraq’s army has increasingly been on the frontline of chemical weapons attack, as examined in Andy Oppenheimer’s Countering the Chemicals article in this issue © US DoD 16 34 40 44 Soldier The Hertz Cannon Fodder Countering Modernisation the Chemicals Modernisation of infantry Locker Naval gunfire support Andy Oppenheimer examines soldier equipment, particularly Thomas Withington examines is essential to naval and the continuing weapons of concerning individual weapons, some of the technical challenges amphibious operations. mass destruction threat to is afoot in the Asia-Pacific with presented to tactical radio Gerrard Cowan examines the Asia-Pacific, and the Andrew White giving a round- engineers when designing such recent developments in this measures being taken to up of the latest developments. equipment for the Asia-Pacific domain combat it. region. 22 28 05 Spot on! Role With It Stephen W. Miller reviews The market for new and some of the ongoing efforts to upgraded multi-role combat improve the precision of artillery aircraft is in rude health across fire to enhance its support of Thomas Withington’s regular column providing all of the latest news the Asia-Pacific region, Joetey ground manoeuvre. -
Downloaded April 22, 2006
SIX DECADES OF GUIDED MUNITIONS AND BATTLE NETWORKS: PROGRESS AND PROSPECTS Barry D. Watts Thinking Center for Strategic Smarter and Budgetary Assessments About Defense www.csbaonline.org Six Decades of Guided Munitions and Battle Networks: Progress and Prospects by Barry D. Watts Center for Strategic and Budgetary Assessments March 2007 ABOUT THE CENTER FOR STRATEGIC AND BUDGETARY ASSESSMENTS The Center for Strategic and Budgetary Assessments (CSBA) is an independent, nonprofit, public policy research institute established to make clear the inextricable link between near-term and long- range military planning and defense investment strategies. CSBA is directed by Dr. Andrew F. Krepinevich and funded by foundations, corporations, government, and individual grants and contributions. This report is one in a series of CSBA analyses on the emerging military revolution. Previous reports in this series include The Military-Technical Revolution: A Preliminary Assessment (2002), Meeting the Anti-Access and Area-Denial Challenge (2003), and The Revolution in War (2004). The first of these, on the military-technical revolution, reproduces the 1992 Pentagon assessment that precipitated the 1990s debate in the United States and abroad over revolutions in military affairs. Many friends and professional colleagues, both within CSBA and outside the Center, have contributed to this report. Those who made the most substantial improvements to the final manuscript are acknowledged below. However, the analysis and findings are solely the responsibility of the author and CSBA. 1667 K Street, NW, Suite 900 Washington, DC 20036 (202) 331-7990 CONTENTS ACKNOWLEGEMENTS .................................................. v SUMMARY ............................................................... ix GLOSSARY ………………………………………………………xix I. INTRODUCTION ..................................................... 1 Guided Munitions: Origins in the 1940s............. 3 Cold War Developments and Prospects ............ -
Texto Completo (5.304Mb)
UNIVERSIDADE FEDERAL DO RIO GRANDE DO SUL FACULDADE DE CIÊNCIAS ECONÔMICAS PROGRAMA PÓS-GRADUAÇÃO EM ESTUDOS ESTRATÉGICOS INTERNACIONAIS FABRÍCIO FLÔRES O OBUSEIRO AUTOPROPULSADO M109A5+BR NO BRASIL: POSSÍVEIS IMPACTOS DOUTRINÁRIOS Porto Alegre 2020 FABRÍCIO FLÔRES O OBUSEIRO AUTOPROPULSADO M109A5+BR NO BRASIL: POSSÍVEIS IMPACTOS DOUTRINÁRIOS Dissertação submetida ao Programa de Pós- Graduação em Estudos Estratégicos Internacionais da Faculdade de Ciências Econômicas da UFRGS, como requisito parcial para obtenção do título de Mestre em Estudos Estratégicos Internacionais. Orientador: Prof. Dr. José Miguel Quedi Martins Porto Alegre 2020 FABRÍCIO FLÔRES O OBUSEIRO AUTOPROPULSADO M109A5+BR NO BRASIL: POSSÍVEIS IMPACTOS DOUTRINÁRIOS Dissertação submetida ao Programa de Pós- Graduação em Estudos Estratégicos Internacionais da Faculdade de Ciências Econômicas da UFRGS, como requisito parcial para obtenção do título de Mestre em Estudos Estratégicos Internacionais. Aprovada em: Porto Alegre, 27 de dezembro de 2019. BANCA EXAMINADORA: _________________________________________________________________________ Prof. Dr. José Miguel Quedi Martins – Orientador UFRGS _________________________________________________________________________ Profa Dra. Analúcia Danilevicz Pereira UFRGS _________________________________________________________________________ Prof. Dr. Érico Esteves Duarte UFRGS _________________________________________________________________________ Prof. Dr. Edson José Neves Júnior UFU AGRADECIMENTOS Cumpre agradecer, antes de mais -
Modernisation of Artillery: Bigger Bang
BOOK YOUR COPY NOW! August-September 2019 Volume 16 No. 4 `100.00 (India-Based Buyer Only) SP’s ND Military AN SP GUIDE P UBLICATION 192 GUNNERS Yearbook 2019 SP’s DAY SPECIAL For details, go to page 7 WWW.SPSLANDFORCES.COM ROUNDUP THE ONLY MAGAZINE IN ASIA-PACIFIC DEDICATED to LAND FORCES IN THIS ISSUE >> LEAD STORY PAGE 4 Artillery Ammunition and Missiles: Destruction Power of Artillery Modernisation of Artillery: Bigger Bang During 1850, solid shot, which was for the Buck spherical in shape, and black powder were standard ammunition for guns. Howitzers ‘Future battlefield will be characterised by short and intense engagements requiring fired hollow powder-filled shells which were ignited by wooden fuses filled with slow- integrated and coordinated employment of all fire power resources including burning powder. precision and high lethality weapon systems in a hybrid warfare environment.’ Lt General Naresh Chand (Retd) PAGE 6 Indian Artillery Celebrates 192nd Gunners Day LT GENERAL NaresH CHAND (Retd) Artillery Rationalisation Plan 2000 in 1987 got embroiled in kickbacks and The Artillery is presently engaged in There had been no acquisition of guns corruption. This lead to large voids in fire modernising in terms of equipment and Role of Indian Artillery for the Indian Artillery since 1987 when power when on the other hand the war sce- support systems under ‘Make in India’ The artillery has always been a battle win- the acquisition of 39-calibre 155mm FH- nario visualised a two front war. This dic- initiative of the Modi Government. ning factor as it can shower death on the 77B howitzers from Sweden’s AB Bofors tated that the strength of artillery should troops in the open and also Lt General P.C. -
On Guidance and Control for Guided Artillery Projectiles, Part 1: General Considerations
On Guidance and Control for Guided Artillery Projectiles, Part 1: General Considerations JOHN W.C. ROBINSON, FREDRIK BEREFELT FOI, Swedish Defence Research Agency, is a mainly assignment-funded agency under the Ministry of Defence. The core activities are research, method and technology development, as well as studies conducted in the interests of Swedish defence and the safety and security of society. The organisation employs approximately 1000 per- sonnel of whom about 800 are scientists. This makes FOI Sweden’s largest research institute. FOI gives its customers access to leading-edge expertise in a large number of fi elds such as security policy studies, defence and security related analyses, the assessment of various types of threat, systems for control and management of crises, protection against and management of hazardous substances, IT security and the potential offered by new sensors. FOI Defence Research Agency Phone: +46 8 555 030 00 www.foi.se Defence & Security, Systems and Technology Fax: +46 8 555 031 00 FOI-R--3291--SE Technical report Defence & Security,Systems and Technology SE-164 90 Stockholm ISSN 1650-1942 October 2011 John W.C. Robinson, Fredrik Berefelt On Guidance and Control for Guided Artillery Projectiles, Part 1: General Considerations Titel Om Styrning av Artilleriprojektiler, Del 1: Generella Overv¨ aganden¨ Title On Guidance and Control for Guided Artillery Pro- jectiles, Part 1: General Considerations Rapportnummer / Report no FOI-R--3291--SE Rapporttyp / Report type Technical report / Teknisk rapport Manad˚ / Month October Utgivningsar˚ / Year 2011 Antal sidor / Pages 29 ISSN ISSN-1650-1942 Kund / Customer Swedish Armed Forces Projektnummer / Project no E20675 Godkand¨ av / Approved by Maria Sjoblom¨ Head, Aeronautics and Systems Integration FOI Swedish Defence Research Agency Defence & Security, Systems and Technology SE-164 90 STOCKHOLM 2 FOI-R--3291--SE Abstract The problem of adding guidance, navigation and control capabiltities to spin- ning artillery projectiles is discussed from a fairly general perspective. -
Fires Bulletin November-December 2011
January - February 2012 A Joint Publication for U.S. Artillery Professionals sill-www.army.mil/firesbulletin/ www.facebook.com/firesbulletin Adapting young leaders through learning, training concepts, the Profession of Arms Campaign Approved for public release; distribution is unlimited. • Headquarters, Department of the Army • PB644-12-1 CONTENTS JANUARY-FEBRUARY Success through Soldiers, leaders 4 By MG David D. Halverson Adaptable, flexible, agile air defense professionals 6 By COL Daniel Karbler Distinguishing the unique profession of field artillerymen 8 By COL Mike Cabrey 10 US Army Air Defense and Field Artillery Award Winners 10 Fires change of command ceremonies An interview with COL Dan Pinnell, US Army Field Artillery 11 2nd BCT, 1st AD brigade combat team commander By Shirley Dismuke Employment of the M982 in Afghanistan: US Army and Marine Corps differences 16 by MG (RET) Toney Stricklin Meeting the fire support challenge 20 By COL Gene Meredith and COL Richard M. Cabrey Things you must get right as a battalion commander 24 By COL Steve Maranian 27 Fires Author’s Guide A chief warrant officer’s advice about promotion boards 28 By CW5 Manuel Vasquez DISCLAIMER: F i r e s , a professional bulletin, is PURPOSE: Founded in 2007, Fires serves as a forum for the professional discussions of all published bimonthly by Headquarters, Department Fires professionals, both active and Reserve Component (RC); disseminates professional of the Army under the auspices of the Fires Center of Excellence (Building 652, Hamilton knowledge about progress, developments and best use in campaigns; cultivates a common Road), Fort Sill, Okla. The views expressed are those of the authors and not the Department understanding of the power, limitations and application of joint Fires, both lethal and of Defense or its elements. -
Municiones Guiadas De Artillería De Campaña Y Morteros
Abril 2017 Apoyo de Fuego Cercano en el Siglo XXI Municiones Guiadas de Artillería de Campaña y Morteros. AUTOR : Cap Infantería Fernando Daniel QUINODOZ. Observador Tecnológico del CEPTM El empleo de las armas de tiro indirecto se remonta a los primeros conflictos armados, su evolución tecnológica ha ido modificando no sólo las tácticas utilizadas por los ejércitos, sino que también han marcado el rumbo de la historia como factor decisorio en el resultado de muchas guerras. Podemos nombrar así cronológicamente al arco y flecha en la edad antigua, las catapultas romanas, la pólvora y su empleo en los cañones otomanos que hicieron caer los milenarios muros de Constantinopla. El obús en las guerras napoleónicas, el ánima rayada y los cañones de acero en las guerras prusianas, los cartuchos con vaina y los primeros cañones con amortiguación de retroceso durante la 1ra Guerra Mundial (IGM). La aparición del mortero como un arma de tiro indirecto para el apoyo cercano de la Infantería, el mejoramiento de los sistemas de adquisición de blancos y procesamiento de los datos de tiro por medio del cálculo de la trayectoria mediante sistemas computarizados que evolucionaron desde la 2da Guerra Mundial (IIGM) y las sucesivas generaciones de cohetería y misiles. Cada una de estas tecnologías, fueron el resultado de la búsqueda de mayor letalidad, movilidad, alcance y precisión sobre los blancos a batir. De todas ellas la precisión fue el desafío más grande al que se enfrentó la ingeniería militar. 1. Municiones Guiadas de Precisión (PGMs): reseña y conceptos generales Durante el siglo XX, y principalmente durante la carrera armamentística producto de la Guerra Fría, las grandes innovaciones tecnológicas de las armas de tiro indirecto se orientaron fundamentalmente a desarrollos en las áreas de alcance, precisión y letalidad. -
Artillery in the Digital Age
mil tech Military technology Dr Carlo Kopp Artillery in the digital age The digital age has brought about profound changes in long established areas of weapons technology, and artillery is no exception, with digital technology now penetrating into guided artillery rounds and navigation systems in self propelled artillery pieces. A key milestone was the first operational use of the M982 Excalibur guided artillery round in Iraq during 2007. While laser guided artillery rounds have been in use for decades, newer satellite aided inertially guided rounds offer much more flexibility and genuine all weather operations. Guided artillery rounds, range- extending munitions designs, and advanced navigation equipment have reinvigorated artillery capability, which prior to the post-2001 global counter-insurgency campaign was slowly stagnating. The advent of advanced guided artillery ammunition fundamentally changes how artillery is used, and indeed when it can be used. For decades, artillery pieces could be divided into precise direct fire weapons, such as anti-tank, anti-aircraft and infantry support assault guns along with indirect fire howitzers used to bombard opposing positions from standoff ranges. This division remains although direct fire weapons have increasingly been displaced by modern tank guns or larger calibre weapons on armoured fighting vehicles. Indirect fire weapons, primarily howitzers, dominated artillery through the latter Cold War period but were challenged to compete against aerial bombs delivered by fixed wing aircraft. The niche occupied by these guns contracted to that of sustained area bombardment, as guns could not compete with the raw firepower of bombers, or the precision of aerial smart bombs. A good comparison is that a standard Mk.82 or FAB-250 500 lb class bomb, with around 90 kg of Tritonal or H-6 filler, is effectively five times the weight of a typical 155 mm artillery shell, and it is fifteen times the weight of a typical 105 mm shell. -
Military Analysis: Taiwan (Republic of China) Armed Forces and US Strategy Towards China
Military Analysis: Taiwan (Republic of China) Armed Forces and US Strategy towards China By South Front Region: Asia Global Research, February 05, 2016 Theme: Militarization and WMD South Front 4 February 2016 Despite the fact the official U.S. strategy towards China ignoring Taiwan issue,the island may easily become a flash point of the ongoing confrontation. The main stream media constantly disseminate reports that the Chinese military prepares to invade the island or, in light versions, conducts provocative military drills. In case of the further US-China confrontation in the Indo-Pacific regions, it’s possible to expect an attempt to use the island for strengthening of U.S military presence in the region. An aggressive activity of U.S. special services through Taiwan is also expected. Beijing would much prefer to reintegrate Taiwan without having to resort to force, but by cultural, economic and political tools. Moreover, it already has a successful experience of lost territories reintegration: Macau and Hong Kong. However, it will be thoughtlessly to ignore the possible crisis in the China-Taiwan relations. Taiwan Military The Republic of China Armed Forces (ROC Armed Forces or Taiwan Armed Forces), with 290,000 active personnel, ranks at number 16 for the world’s largest number of active personnel, with 1,657,000 personnel in reserve. The Republic of China or Taiwan, with a population of over 23 million people, is a sovereign island state close to Mainland China. There have been many political status disputes going on for decades between the Republic of China and the People’s Republic of China. -
Free-Flight Projectile Behaviour: LPV Modelling and Global Sensitivity
Free-flight projectile behaviour : LPV modelling and global sensitivity analysis Dawid Machala To cite this version: Dawid Machala. Free-flight projectile behaviour : LPV modelling and global sensitivity analysis. Automatic. Université de Lorraine, 2019. English. NNT : 2019LORR0165. tel-02499324 HAL Id: tel-02499324 https://hal.univ-lorraine.fr/tel-02499324 Submitted on 5 Mar 2020 HAL is a multi-disciplinary open access L’archive ouverte pluridisciplinaire HAL, est archive for the deposit and dissemination of sci- destinée au dépôt et à la diffusion de documents entific research documents, whether they are pub- scientifiques de niveau recherche, publiés ou non, lished or not. The documents may come from émanant des établissements d’enseignement et de teaching and research institutions in France or recherche français ou étrangers, des laboratoires abroad, or from public or private research centers. publics ou privés. AVERTISSEMENT Ce document est le fruit d'un long travail approuvé par le jury de soutenance et mis à disposition de l'ensemble de la communauté universitaire élargie. Il est soumis à la propriété intellectuelle de l'auteur. Ceci implique une obligation de citation et de référencement lors de l’utilisation de ce document. D'autre part, toute contrefaçon, plagiat, reproduction illicite encourt une poursuite pénale. Contact : [email protected] LIENS Code de la Propriété Intellectuelle. articles L 122. 4 Code de la Propriété Intellectuelle. articles L 335.2- L 335.10 http://www.cfcopies.com/V2/leg/leg_droi.php -
The Future of the Russian Military Russia’S Ground Combat Capabilities and Implications for U.S.-Russia Competition Appendixes
ARROYO CENTER The Future of the Russian Military Russia’s Ground Combat Capabilities and Implications for U.S.-Russia Competition Appendixes Andrew Radin, Lynn E. Davis, Edward Geist, Eugeniu Han, Dara Massicot, Matthew Povlock, Clint Reach, Scott Boston, Samuel Charap, William Mackenzie, Katya Migacheva, Trevor Johnston, Austin Long Prepared for the United States Army Approved for public release; distribution unlimited For more information on this publication, visit www.rand.org/t/RR3099 Published by the RAND Corporation, Santa Monica, Calif. © Copyright 2019 RAND Corporation R® is a registered trademark. Limited Print and Electronic Distribution Rights This document and trademark(s) contained herein are protected by law. This representation of RAND intellectual property is provided for noncommercial use only. Unauthorized posting of this publication online is prohibited. Permission is given to duplicate this document for personal use only, as long as it is unaltered and complete. Permission is required from RAND to reproduce, or reuse in another form, any of its research documents for commercial use. For information on reprint and linking permissions, please visit www.rand.org/pubs/permissions. The RAND Corporation is a research organization that develops solutions to public policy challenges to help make communities throughout the world safer and more secure, healthier and more prosperous. RAND is nonprofit, nonpartisan, and committed to the public interest. RAND’s publications do not necessarily reflect the opinions of its research clients and sponsors. Support RAND Make a tax-deductible charitable contribution at www.rand.org/giving/contribute www.rand.org Preface This document presents the results of a project titled U.S.-Russia Long Term Competition, spon- sored by the Deputy Chief of Staff, G-3/5/7, U.S. -
Vigilancia Tecnológica Sobre Munición Guiada Para Armas De Apoyo De
ESTUDIOS DE VIGILANCIA Y PROSPECTIVA TECNOLÓGICA EN EL ÁREA DE DEFENSA Y SEGURIDAD 4.2 Vigilancia tecnológica sobre munición guiada para armas de apoyo de fuego de artillería y morteros Por el Vigía Tecnológico: Teniente Primero Infantería Fernando Daniel Quinodoz* Munición guiada para armas de apoyo de fuego de artillería y morteros Autor: Teniente Primero Infantería Fernando Daniel Quinodoz. Alumno de segundo año de Ingeniería Mecánica (Especialidad Armamentos) RESUMEN El daño colateral, los costos de la munición, los problemas logísticos y la acumulación de municiones no guiadas en los inventarios han promovido el desarrollo de sistemas de apoyo de fuego de Artillería G-RAMM (Guided – Rocket Artillery Mortar and Missiles), los que han evidenciado un crecimiento notable en los últimos diez años; se puede observar incluso que se priorizan importantes asignaciones presupuestarias frente a otros sistemas guiados de largo alcance. El presente trabajo de investigación se refiere a la “Munición Guiada para armas de apoyo de fuego de Artillería y Morteros”. Se realiza una revisión histórica de los desarrollos en este campo, su evolución y el estado del arte alcanzado en la actualidad. Se describen conceptual- mente las principales tecnologías desarrolladas y aplicadas a los proyectiles guiados, su fun- cionamiento, clasificación y su evolución en los últimos treinta años. Se presentan también aquellos programas y proyectos que resultan más representativos e importantes para cada tipo de tecnología y su grado de avance a la fecha. Algunos de ellos fueron recientemente probados con éxito en combate, mientras que el resto se encuentra ya en producción o lo estará a partir del próximo año.