Arvi D Ralpheckberg; INVENTOR by Ma?A/W
Total Page:16
File Type:pdf, Size:1020Kb
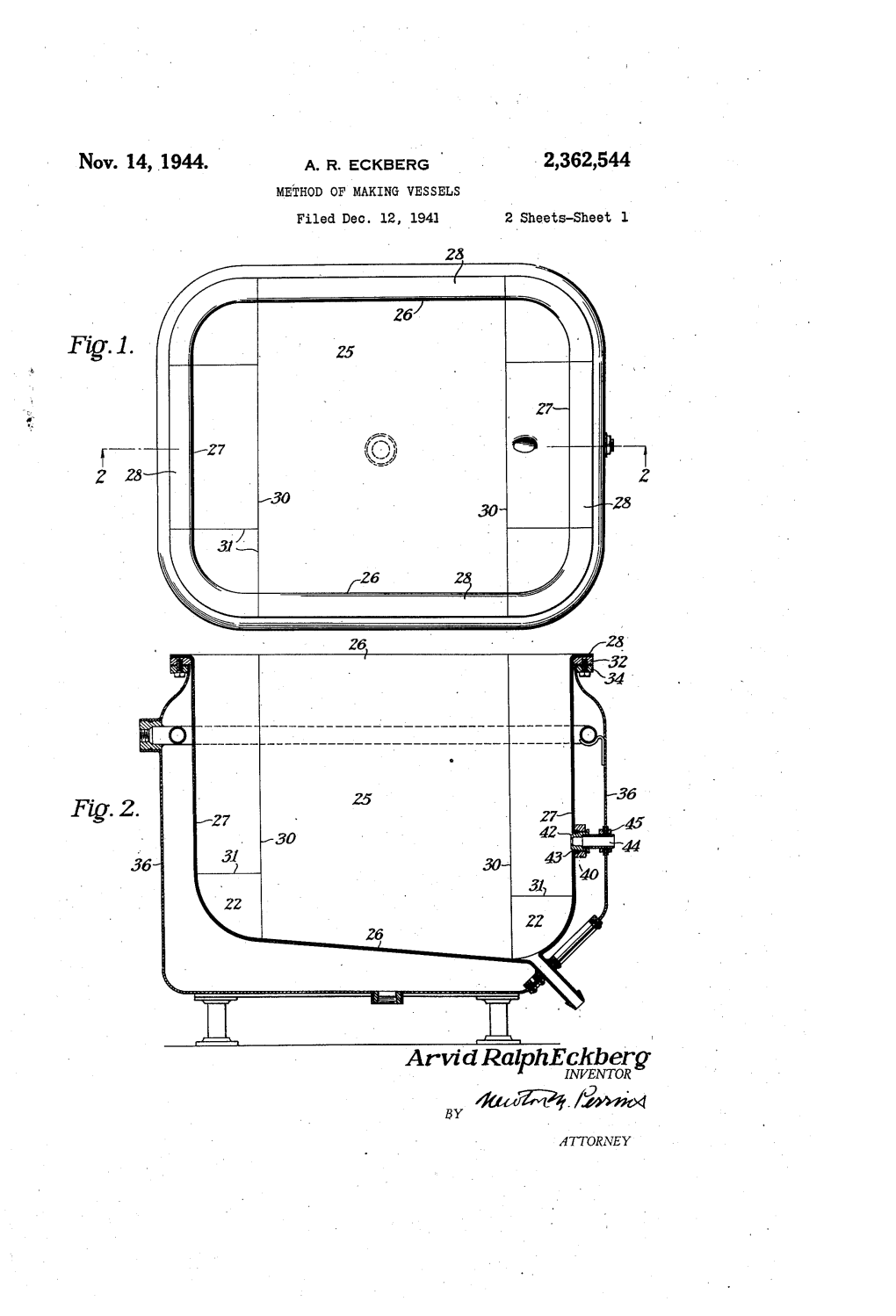
Load more
Recommended publications
-
Fundamentals of Joining Processes
Outline ME3072 – MANUFACTURING ENGINEERING II BSc Eng (Hons) in Mechanical Engineering • Introduction to Welding Semester - 4 • Fusion-Welding Processes • Solid-State Welding Processes Fundamentals of Joining • Metallurgy of Welding Processes • Weld Quality • Brazing & Soldering Prepared By : R.K.P.S Ranaweera BSc (Hons) MSc Lecturer - Department of Mechanical Engineering University of Moratuwa 2 (for educational purpose only) Joining Processes Classification of Joining Processes 3 4 1 Introduction to Welding • Attention must be given to the cleanliness of the metal surfaces prior to welding and to possible • Is a process by which two materials, usually metals oxidation or contamination during welding process. are permanently joined together by coalescence, which is induced by a combination of temperature, • Production of high quality weld requires: pressure and metallurgical conditions. Source of satisfactory heat and/or pressure Means of protecting or cleaning the metal • Is extensively used in fabrication as an alternative Caution to avoid harmful metallurgical effects method for casting or forging and as a replacement for bolted and riveted joints. Also used as a repair • Advantages of welding over other joints: medium to reunite metals. Lighter in weight and has a great strength • Types of Welding: High corrosion resistance Fusion welding Fluid tight for tanks and vessels Solid-state (forge) welding Can be altered easily (flexibility) and economically 5 6 • Weldability has been defined as the capacity of • Steps in executing welding: metal to be welded under the fabrication conditions Identification of welds, calculation of weld area by stress imposed into a specific, suitably designed structure analysis, preparation of drawings & to perform satisfactorily in the intended service. -
Welding Technology a Suncam Continuing Education Course
033.pdf Welding Technology A SunCam Continuing Education Course Welding Technology By Roger Cantrell www.SunCam.com Page 1 of 35 033.pdf Welding Technology A SunCam Continuing Education Course Learning Objectives This course introduces the student to the concept of developing procedures for welding and brazing. Welding and brazing variables are introduced and some example concepts for applying each variable are highlighted to pique the student’s interest and perhaps lead to further study. Upon completion of this course, the student should be able to: • Understand the concept of creating a welding/brazing procedure • Identify several commonly used welding/brazing processes • Identify the more common welding/brazing variables • Appreciate some of the considerations for applying each variable 1.0 INTRODUCTION This course highlights the basic concepts of developing a welding or brazing procedure specification (WPS/BPS). There are a number of ways to approach this subject such as by process, base material, etc. It will be convenient to organize our thoughts in the format of ASME Section IX. The various factors that might influence weld quality are identified in ASME Section IX as "Welding Variables". "Brazing Variables" are treated in a separate part of Section IX in a manner similar to welding variables. The listing of variables for welding procedures can be found in ASME Section IX, Tables QW-252 through QW-265 (a table for each process). The layout of each table is similar to Figure No. 1. www.SunCam.com Page 2 of 35 033.pdf Welding Technology A SunCam Continuing Education Course Process Variable Variation (Description) Essential Supplementary Essential Nonessential Joint Backing X Root Spacing X Base P Number X Metal G Number X Filler F Number X Metal A Number X Continued in this fashion until all relevant variables for the subject process are listed. -
Gas-Shielded Arc Welding TIG Welding
Gas-Shielded Arc Welding Gas-shielded welding can be divided into the tungsten gas-shielded welding and the metal gas-shielded welding processes. The tungsten gas-shielded welding covers the processes − Tungsten plasma arc welding (PAW) − Inert-gas tungsten-arc welding (TIG), whereby TIG welding is the most widely used fusion welding process for aluminium. The plasma welding consists only of the plasma-arc welding process which works with a transferred arc. The metal shielded-gas welding is limited to the metal inert-gas welding process operating with an inert gas as shield, as well as a process combination with plasma welding (plasma metal shielded-gas welding - PMIG). The abbreviations used are: GAW Gas-shielded arc welding GMGMMA Gas-mixture shielded metal-arc welding GTAW Gas-shielded tungsten arc welding (MAGM) GMAW Gas-shielded metal arc welding MAGC CO2-shielded metal-arc welding AHW Atomic hydrogen welding NGW Narrow-gap welding CAW Constricted arc welding EGW Electro -gas welding TIG Tungsten inert-gas arc welding PMIG Plasma MIG welding MIG Metal inert-gas arc welding MAG Metal active-gas arc welding p Pulsed arc PJW Plasma jet welding sh Short arc PAW Plasma arc welding sp Spray arc PJPW Plasma jet plasma arc welding l Long arc TIG Welding Principle of TIG Welding TIG welding equipment Watercooled TIG welding torch Torch forms for TIG welding Shielding gases for welding and cutting Flow meters Flow meter for torches Effect of current and inert gas Argon consumption for TIG welding Tungsten electrodes -
Welding Process Reference Guide
Welding Process Reference Guide gas arc welding…………………..GMAW -pulsed arc…………….……….GMAW-P atomic hydrogen welding……..AHW -short circuiting arc………..GMAW-S bare metal arc welding…………BMAW gas tungsten arc welding…….GTAW carbon arc welding……………….CAW -pulsed arc……………………….GTAW-P -gas……………………………………CAW-G plasma arc welding……………..PAW -shielded……………………………CAW-S shielded metal arc welding….SMAW -twin………………………………….CAW-T stud arc welding………………….SW electrogas welding……………….EGW submerged arc welding……….SAW Flux cord arc welding…………..FCAW -series………………………..…….SAW-S coextrusion welding……………...CEW Arc brazing……………………………..AB cold welding…………………………..CW Block brazing………………………….BB diffusion welding……………………DFW Diffusion brazing…………………….DFB explosion welding………………….EXW Dip brazing……………………………..DB forge welding…………………………FOW Flow brazing…………………………….FLB friction welding………………………FRW Furnace brazing……………………… FB hot pressure welding…………….HPW SOLID ARC Induction brazing…………………….IB STATE BRAZING WELDING Infrared brazing……………………….IRB roll welding…………………………….ROW WELDING (8) ultrasonic welding………………….USW (SSW) (AW) Resistance brazing…………………..RB Torch brazing……………………………TB Twin carbon arc brazing…………..TCAB dip soldering…………………………DS furnace soldering………………….FS WELDING OTHER electron beam welding………….EBW induction soldering……………….IS SOLDERING PROCESS WELDNG -high vacuum…………………….EBW-HV infrared soldering…………………IRS (S) -medium vacuum………………EBW-MV iron soldering……………………….INS -non-vacuum…………………….EBW-NV resistance soldering…………….RS electroslag welding……………….ESW torch soldering……………………..TS -
UNIT-IV Metal Joining Processes
Manufacturing Process - I UNIT –IV Metal Joining Processes Prepared By Prof. Shinde Vishal Vasant Assistant Professor Dept. of Mechanical Engg. NDMVP’S Karmaveer Baburao Thakare College of Engg. Nashik Contact No- 8928461713 E mail:- [email protected] Website:- www.vishalshindeblog.wordpress.com 06/09/2016 PROF.V.V.SHINDE NDMVP'S KBTCOE NASHIK JOINING PROCESSES • Joining includes welding, brazing, soldering, adhesive bonding of materials. • They produce permanent joint between the parts to be assembled. • They cannot be separated easily by application of forces. • They are mainly used to assemble many parts to make a system. • Welding is a metal joining process in which two or more parts are joined or coalesced at their contacting surfaces by suitable application of heat or/and pressure. • Some times, welding is done just by applying heat alone, with no pressure applied • In some cases, both heat and pressure are applied; and in other cases only pressure is applied, without any external heat. • In some welding processes a filler material is added to facilitate coalescence(Joining)06/09/2016 PROF.V.V.SHINDE NDMVP'S KBTCOE NASHIK Joining Processes: Welding, Brazing, Soldering 1. Brazing and Soldering: Melting of filler rod only • Brazing: higher temperature, ~brass filler, strong • Soldering: lower temp, ~tin-lead filler, weak 2. Welding: Melting of filler rod and base metals 06/09/2016 PROF.V.V.SHINDE NDMVP'S KBTCOE NASHIK Advantages of welding: • Welding provides a permanent joint. • Welded joint can be stronger than the parent materials if a proper filler metal is used that has strength properties better than that of parent base material and if defect less welding is done. -
Boilermaking Manual. INSTITUTION British Columbia Dept
DOCUMENT RESUME ED 246 301 CE 039 364 TITLE Boilermaking Manual. INSTITUTION British Columbia Dept. of Education, Victoria. REPORT NO ISBN-0-7718-8254-8. PUB DATE [82] NOTE 381p.; Developed in cooperation with the 1pprenticeship Training Programs Branch, Ministry of Labour. Photographs may not reproduce well. AVAILABLE FROMPublication Services Branch, Ministry of Education, 878 Viewfield Road, Victoria, BC V9A 4V1 ($10.00). PUB TYPE Guides Classroom Use - Materials (For Learner) (OW EARS PRICE MFOI Plus Postage. PC Not Available from EARS. DESCRIPTORS Apprenticeships; Blue Collar Occupations; Blueprints; *Construction (Process); Construction Materials; Drafting; Foreign Countries; Hand Tools; Industrial Personnel; *Industrial Training; Inplant Programs; Machine Tools; Mathematical Applications; *Mechanical Skills; Metal Industry; Metals; Metal Working; *On the Job Training; Postsecondary Education; Power Technology; Quality Control; Safety; *Sheet Metal Work; Skilled Occupations; Skilled Workers; Trade and Industrial Education; Trainees; Welding IDENTIFIERS *Boilermakers; *Boilers; British Columbia ABSTRACT This manual is intended (I) to provide an information resource to supplement the formal training program for boilermaker apprentices; (2) to assist the journeyworker to build on present knowledge to increase expertise and qualify for formal accreditation in the boilermaking trade; and (3) to serve as an on-the-job reference with sound, up-to-date guidelines for all aspects of the trade. The manual is organized into 13 chapters that cover the following topics: safety; boilermaker tools; mathematics; material, blueprint reading and sketching; layout; boilershop fabrication; rigging and erection; welding; quality control and inspection; boilers; dust collection systems; tanks and stacks; and hydro-electric power development. Each chapter contains an introduction and information about the topic, illustrated with charts, line drawings, and photographs. -
Kabila, Laurent-Desiré (1939–2001). Congolese Politician. a Guerilla and Bandit for 30 Years, His Forces Overthrew *Mobutu In
1912 and 1917, he had a relationship with Felice Bauer (1887–1960). They were twice engaged but never married. (He wrote her 500 letters but they only met 17 times.) Kafka had the smallest output of any K major writer, three short novels (all unfinished), one novella, 23 short stories, diaries and five collections of Kabila, Laurent-Desiré (1939–2001). Congolese letters, almost all published posthumously. He lived politician. A guerilla and bandit for 30 years, his forces briefly with two unhappily married women. overthrew *Mobutu in July 1997 and he became The novella Metamorphosis (Die Verwandlung), President of the Democratic Republic of the Congo published in 1915, is famous for the image of the (formerly Zaire). Assassinated in January 2001 by his central character Gregor Samsa waking to find bodyguard, 135 people were tried, mostly convicted himself transformed into ‘a monstrous vermin’, which but apparently not executed. His son Joseph is usually rendered in English as an insect or beetle. Kabila Kabange (1971– ) was President of the DRC Kafka does not explain why the transformation 2001–19. In 2018, a corrupt and violent election was occurred. won by an opposition candidate Félix Tshisekedi; a bizarre result that appeared to be a democratic He suffered from tuberculosis of the larynx, died transition but was engineered to guarantee Kabila’s —essentially of starvation—in a sanatorium at continuing influence and preservation of his family’s Klosterneuburg, near Vienna, and was buried in wealth. Prague. He left instructions that his literary works be burnt, unread, but his friend and executor Max Brod Kaczyński, Jarosław (1949– ) and Lech Aleksander (1882–1968) ignored the direction and published Kaczyński (1949–2010). -
Chapter 6 Arc Welding
Revised Edition: 2016 ISBN 978-1-283-49257-7 © All rights reserved. Published by: Research World 48 West 48 Street, Suite 1116, New York, NY 10036, United States Email: [email protected] Table of Contents Chapter 1 - Welding Chapter 2 - Fabrication (Metal) Chapter 3 - Electron Beam Welding and Friction Welding Chapter 4 - Oxy-Fuel Welding and Cutting Chapter 5 - Electric Resistance Welding Chapter 6 - Arc Welding Chapter 7 - Plastic Welding Chapter 8 - Nondestructive Testing Chapter 9 - Ultrasonic Welding Chapter 10 - Welding Defect Chapter 11 - Hyperbaric Welding and Orbital Welding Chapter 12 - Friction Stud Welding Chapter 13 WT- Welding Joints ________________________WORLD TECHNOLOGIES________________________ Chapter 1 Welding WT Gas metal arc welding ________________________WORLD TECHNOLOGIES________________________ Welding is a fabrication or sculptural process that joins materials, usually metals or thermoplastics, by causing coalescence. This is often done by melting the workpieces and adding a filler material to form a pool of molten material (the weld pool) that cools to become a strong joint, with pressure sometimes used in conjunction with heat, or by itself, to produce the weld. This is in contrast with soldering and brazing, which involve melting a lower-melting-point material between the workpieces to form a bond between them, without melting the workpieces. Many different energy sources can be used for welding, including a gas flame, an electric arc, a laser, an electron beam, friction, and ultrasound. While often an industrial process, welding can be done in many different environments, including open air, under water and in outer space. Regardless of location, welding remains dangerous, and precautions are taken to avoid burns, electric shock, eye damage, poisonous fumes, and overexposure to ultraviolet light. -
Welding, Brazing, and Thermal Cutting
\j L i □ K n Criteria for a Recommended Standard Welding, Brazing, and Thermal Cutting U.S. DEPARTM f NT OF H E A LT H AND HUMAN SER V IC ES PUBLIC HEALTH SER V IC E CENTERS FOR DISEASE CONTROL NATIONAL INSTITUTE FOR OCCUPATIONAL SAFETY AND HEALTH' CRITERIA FOR A RECOMMENDED STANDARD (elding, Brazing, and Thermal Cutting U.S. DEPARTMENT OF HEALTH AND HUMAN SERVICES PUBLIC HEALTH SERVICE CENTERS FOR DISEASE CONTROL NATIONAL INSTITUTE FOR OCCUPATIONAL SAFETY AND HEALTH DIVISION OF STANDARDS DEVELOPMENT AND TECHNOLOGY TRANSFER ApriI 1988 DISCLAIMER Mention of the name of any company or product does not constitute endorsement by the National Institute for Occupational Safety and Health. DHHS (NIOSH) Publication No. 88-110 to r sat* by II» Superintendent of Documenti, U.S. Government Print Inc Office, »••hinglon. D.C. 20403 FOREWORD The purpose of the Occupational Safety and Health Act of 1970 (Public Law 91-596) is to ensure safe and healthful working conditions for every working person and to preserve our human resources by providing medical and other criteria that will ensure, insofar as practicable, that no worker will suffer diminished health, functional capacity, or life expectancy as a result of his or her work experience. The Act authorizes the National Institute for Occupational Safety and Health (NIOSH) to develop and recommend occupational safety and health standards and to develop criteria for improving them. By this means, NIOSH communicates these criteria both to regulatory agencies and others in the community of occupational safety and health. Criteria documents provide the basis for the occupational health and safety standards sought by Congress. -
Dispelling the Fears of Hydrogen in Shielding Gases for Corrosion Resistant Overlays on High Strength Steels
Dispelling the Fears of Hydrogen in Shielding Gases For Corrosion Resistant Overlays on High Strength Steels Introduction: Hydrogen-bearing shielding gases have been used for decades; however, with today’s awareness about hydrogen- induced cracking (HIC) and the need for low hydrogen consumables and welding practices, the suggestion of using a welding shielding gas containing hydrogen is rarely considered. The negativity associated with the use of this gas has long overshadowed its inherent benefits. In an attempt to overcome these inhibitions and prohibition by the welding academic/technical community, it was realized that a study of the effects of hydrogen additions to shielding gases to either confirm or dispel these concerns was justified. Such a study is especially interesting to the technical community involved with the use of the gas tungsten arc welding process with hot wire filler metal addition (GTAW-HW) for the welding of corrosion-resistant overlays (CROs) on high strength steels like 4130, 8630 and F22, all of which are common alloys used for components in the upstream sector (production) of the oil and gas industry. The CRO alloy of choice for many of these “oil patch” applications is INCONEL 625 (625). Another impression one gets when mentioning the use of hydrogen is the fear of explosions. While true that hydrogen is highly flammable, its flammability limit occurs at 4% concentration. For this study, 98% Ar – 2% H2 was used so the concern for fire or explosion is immediately eliminated. Hydrogen-induced cracking (HIC), however, is a more legitimate concern among metallurgists familiar with its potentially catastrophic consequences. -
The Newcomen Society
The Newcomen Society for the history of engineering and technology Welcome! This Index to volumes 1 to 32 of Transactions of the Newcomen Society is freely available as a PDF file for you to print out, if you wish. If you have found this page through the search engines, and are looking for more information on a topic, please visit our online archive (http://www.newcomen.com/archive.htm). You can perform the same search there, browse through our research papers, and then download full copies if you wish. By scrolling down this document, you will get an idea of the subjects covered in Transactions (volumes dating from 1920 to 1960 only), and on which pages specific information is to be found. The most recent volumes can be ordered (in paperback form) from the Newcomen Society Office. If you would like to find out more about the Newcomen Society, please visit our main website: http://www.newcomen.com. The Index to Transactions (Please scroll down) GENERAL INDEX Advertising puffs of early patentees, VI, 78 TRANSACTIONS, VOLS. I-XXXII Aeolipyle. Notes on the aeolipyle and the Marquis of Worcester's engine, by C.F.D. Marshall, XXIII, 133-4; of Philo of 1920-1960 Byzantium, 2*; of Hero of Alexandria, 11; 45-58* XVI, 4-5*; XXX, 15, 20 An asterisk denotes an illustrated article Aerodynamical laboratory, founding of, XXVII, 3 Aborn and Jackson, wood screw factory of, XXII, 84 Aeronautics. Notes on Sir George Cayley as a pioneer of aeronautics, paper J.E. Acceleration, Leonardo's experiments with Hodgson, 111, 69-89*; early navigable falling bodies, XXVIII, 117; trials of the balloons, 73: Cayley's work on airships, 75- G.E.R. -
Introduction to Welding Engineering
1 Introduction to Welding Engineering 1.1. History and Development of Welding The first historical reference about welding is given in Bible and Tubal-Cain was the first smith who forged the instruments of bronze and iron. About 5000 years back the forge, hammer, anvil, bellows and fire heaters were used for forging. It was in the year 1887 that Thomas Fletcher of Warrington invented various blow pipes for burning hydrogen or coal gas with air or oxygen. The bicycle frames were manufactured with the help of these blow pipes. This type of blow pipe is used even today where acetylene gas is used in place of hydrogen or coal gas. In 1892, acetylene gas was first discovered by Thomas Leopold Wilson of North Carolina. In 1886, two Frenchmen, the Brins brothers formed a company for the liquefaction of air from which pure oxygen was obtained. The only acetylene welding blow pipe was invented by Fouche and Picard. Volta, after whom the term volt is named, demonstrated in 1800 that the electric arc could be used for melting iron wire and the process of fusion of metals by electricity was born. A swedish marine engineer thought of protecting the arc with an inert gas. This gas, he produced by applying a flux to the electrode. The flux melts and vaporises in the intense heat of the welding arc, protects the molten metal from the air and can be used to add alloying elements to the welding wire. Many advances have been made since these early days. Auto- mation has added to them, welding arcs and cutting flames, electronically guided arc, gas combined with electricity in hydrogen, helium and argon arcs.