A Comparative Analysis of Confederate Ironclad Steam Engines, Boilers, and Propulsion Systems by Saxon T
Total Page:16
File Type:pdf, Size:1020Kb
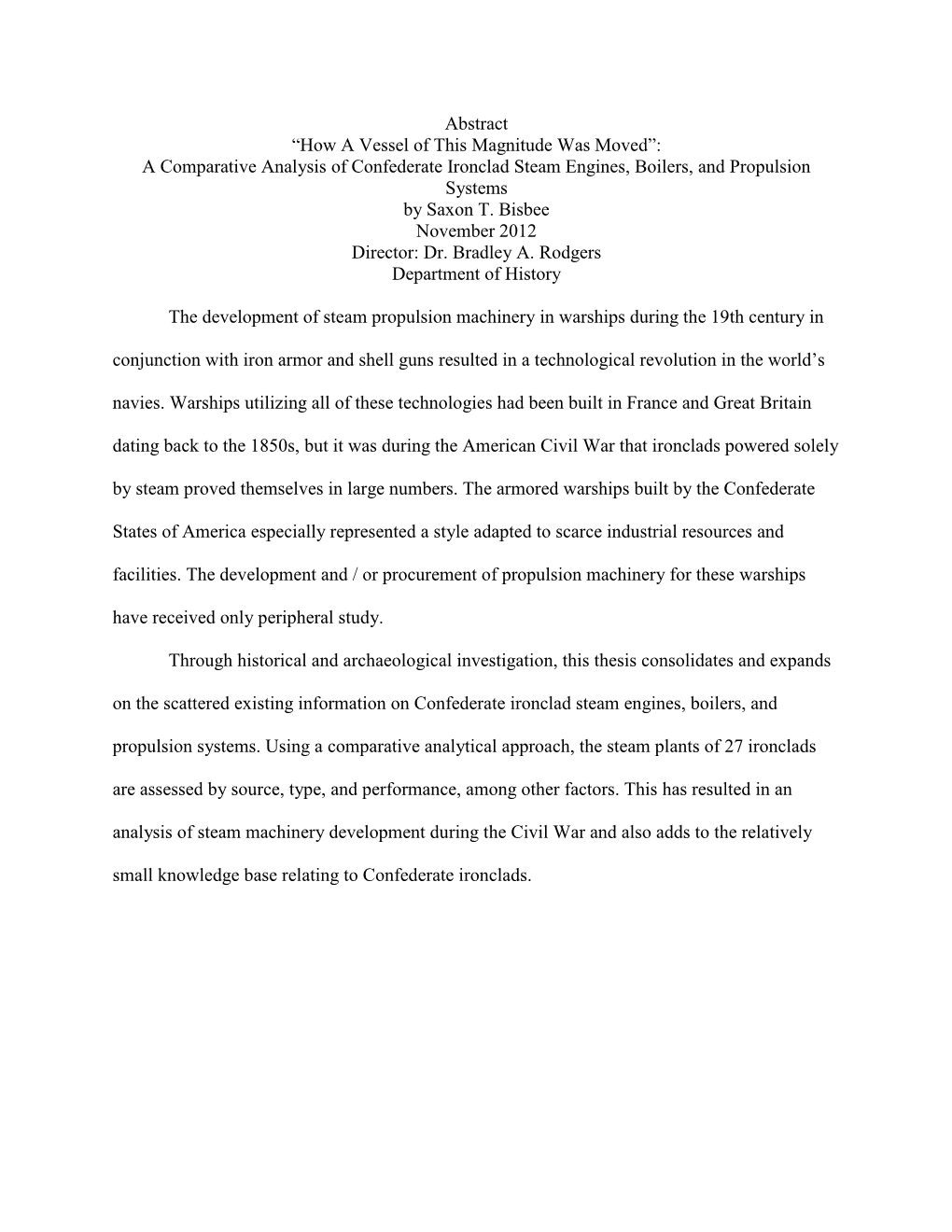
Load more
Recommended publications
-
Officers and Crew Jack L
Marshall University Marshall Digital Scholar C.S.S. Alabama: An Illustrated History Library Special Collections Fall 10-10-2017 Part 2: Officers and Crew Jack L. Dickinson Marshall University, [email protected] Follow this and additional works at: http://mds.marshall.edu/css_al Part of the Military History Commons, and the United States History Commons Recommended Citation Dickinson, Jack L., "Part 2: Officers and Crew" (2017). C.S.S. Alabama: An Illustrated History. 2. http://mds.marshall.edu/css_al/2 This Article is brought to you for free and open access by the Library Special Collections at Marshall Digital Scholar. It has been accepted for inclusion in C.S.S. Alabama: An Illustrated History by an authorized administrator of Marshall Digital Scholar. For more information, please contact [email protected], [email protected]. CSS Alabama : An Illustrated History In Six Parts: You are here Part 1: Building of Ship 290 ---> Part 2: Officers and Crew Part 3: Cruise of the Alabama Part 4: Battle with USS Kearsarge Part 5: Wreck Exploration & Excavation Part 6: Miscellaneous and Bibliography (the Alabama Claims, poems, music, sword of Raphael Semmes) To read any of the other parts, return to the menu and select that part to be downloaded. Designed and Assembled by Jack L. Dickinson Marshall University Special Collections 2017 1 CSS Alabama: An Illustrated History Officers and CREW OF THE CSS ALABAMA During the Civil War naval officers were divided into four categories for purposes of berthing and messing aboard ship: cabin, wardroom, steerage, and forward officers. The captain had a private state room, and higher ranking officers had small cabins, while lower ranks only had individual lockers. -
A Many-Storied Place
A Many-storied Place Historic Resource Study Arkansas Post National Memorial, Arkansas Theodore Catton Principal Investigator Midwest Region National Park Service Omaha, Nebraska 2017 A Many-Storied Place Historic Resource Study Arkansas Post National Memorial, Arkansas Theodore Catton Principal Investigator 2017 Recommended: {){ Superintendent, Arkansas Post AihV'j Concurred: Associate Regional Director, Cultural Resources, Midwest Region Date Approved: Date Remove not the ancient landmark which thy fathers have set. Proverbs 22:28 Words spoken by Regional Director Elbert Cox Arkansas Post National Memorial dedication June 23, 1964 Table of Contents List of Figures vii Introduction 1 1 – Geography and the River 4 2 – The Site in Antiquity and Quapaw Ethnogenesis 38 3 – A French and Spanish Outpost in Colonial America 72 4 – Osotouy and the Changing Native World 115 5 – Arkansas Post from the Louisiana Purchase to the Trail of Tears 141 6 – The River Port from Arkansas Statehood to the Civil War 179 7 – The Village and Environs from Reconstruction to Recent Times 209 Conclusion 237 Appendices 241 1 – Cultural Resource Base Map: Eight exhibits from the Memorial Unit CLR (a) Pre-1673 / Pre-Contact Period Contributing Features (b) 1673-1803 / Colonial and Revolutionary Period Contributing Features (c) 1804-1855 / Settlement and Early Statehood Period Contributing Features (d) 1856-1865 / Civil War Period Contributing Features (e) 1866-1928 / Late 19th and Early 20th Century Period Contributing Features (f) 1929-1963 / Early 20th Century Period -
THE FEASIBLITY of the OVER-THE-HORIZON AMPHIBIOUS ASSAULT for U.S. NAVY and MARINE CORPS FORCES a Thesis Presented To
THE FEASIBLITY OF THE OVER-THE-HORIZON AMPHIBIOUS ASSAULT FOR U.S. NAVY AND MARINE CORPS FORCES A thesis presented to the Faculty of the U.S. Army Command and General Staff Colege in partial fulfillment of the requirements for the degree MASTER OF MILITARY ART AND SCIENCE STEPHEN L. GOERTZEN, LCDR, USN B.S., U.S. Naval Academy, Annapolis, Maryland, 1982 Fort Leavenworth, Kansas 1993 Approved for public release; distribution is unlimited. MASTER OF MILITARY ART AND SCIENCE THESIS APPROVAL PAGE Name of Candidate: LCDR Stephen L. Goertzen, USN Thesis Title: The Feasibility of the Over-the-Horizon Amphibious Assault for the U.S. Navy and Marine Corps Forces Approved by: u , Thesis Committee Chaiman LTCOL W. A. Sp , Member Accepted this 4th day of June 1993 by: , Director, Graduate Degree Philip J. Brookes, Ph.D. Programs The opinions and conclusions expressed herein are those of the student author and do not necessarily represent the views of the U.S. Army Command and General Staff College or any other governmental agency. (References to this study should include the foregoing statement.) ABSTRACT THE FEASIBILITY OF THE OVER-THE-HORIZON AMPHIBIOUS ASSAULT FOR U.S. NAVY AND MARINE CORPS FORCES: An analysis of the doctrine, equipment, and technology contributing to the feasibility of the over-the-horizon amphibious assault. By Lieutenant Commander Stephen L. Goertzen, USN, 128 pages. This study is an analysis of the tactics,techniques, procedures, doctrine, equipment, and technology utilized in over-the-horizon amphibious assaults. The study examines the issues surrounding current feasibility of the assault, as well as future feasibility of the assault. -
Music and the American Civil War
“LIBERTY’S GREAT AUXILIARY”: MUSIC AND THE AMERICAN CIVIL WAR by CHRISTIAN MCWHIRTER A DISSERTATION Submitted in partial fulfillment of the requirements for the degree of Doctor of Philosophy in the Department of History in the Graduate School of The University of Alabama TUSCALOOSA, ALABAMA 2009 Copyright Christian McWhirter 2009 ALL RIGHTS RESERVED ABSTRACT Music was almost omnipresent during the American Civil War. Soldiers, civilians, and slaves listened to and performed popular songs almost constantly. The heightened political and emotional climate of the war created a need for Americans to express themselves in a variety of ways, and music was one of the best. It did not require a high level of literacy and it could be performed in groups to ensure that the ideas embedded in each song immediately reached a large audience. Previous studies of Civil War music have focused on the music itself. Historians and musicologists have examined the types of songs published during the war and considered how they reflected the popular mood of northerners and southerners. This study utilizes the letters, diaries, memoirs, and newspapers of the 1860s to delve deeper and determine what roles music played in Civil War America. This study begins by examining the explosion of professional and amateur music that accompanied the onset of the Civil War. Of the songs produced by this explosion, the most popular and resonant were those that addressed the political causes of the war and were adopted as the rallying cries of northerners and southerners. All classes of Americans used songs in a variety of ways, and this study specifically examines the role of music on the home-front, in the armies, and among African Americans. -
2 22 37 55 68 90 W Numerze 11 26 42 58 78
Dwumiesięcznik W NUMERZE Vol. XVIII, Nr 5/2011 (109) ISSN-1231-014X, Indeks 386138 Redaktor naczelny Jarosław Malinowski Juliusz Tomczak Pancernik wielkich nadziei – historia CSS 2 Kolegium redakcyjne Rafał Ciechanowski, Michał Jarczyk, „Virginia”, część II Maciej S. Sobański Współpracownicy w kraju Andrzej S. Bartelski, Jan Bartelski, Alejandro A. Anca, Nikołaj W. Mitiuckow Stanisław Biela, Jarosław Cichy, 11 Krążowniki Portugalii Andrzej Danilewicz, Józef Wiesław Dyskant, Maciej K. Franz, Przemysław Federowicz, Michał Glock, Tadeusz Górski, Jarosław Jastrzębski, Rafał Mariusz Kaczmarek, Jerzy Lewandowski, Oskar Myszor, Andrzej Nitka, Piotr Nykiel, Michał Jarczyk, Krzysztof Krzeszowiak Grzegorz Ochmiński, Jarosław Palasek, Jednostka torpedowa „Zieten” 22 Jan Radziemski, Marek Supłat, Cesarskiej marynarki wojennej Niemiec Tomasz Walczyk, Kazimierz Zygadło Współpracownicy zagraniczni BELGIA Leo van Ginderen Aleksandr Aleksandrow, Siergiej Bałakin CZECHY 26 „Asama” i kuzyni, częć IV Ota Janeček FRANCJA Gérard Garier, Jean Guiglini, Pierre Hervieux HISZPANIA Alejandro Anca Alamillo LITWA Jarosław Jastrzębski Aleksandr Mitrofanov O potrzebie wyodrębnienia w nomenklaturze 37 NIEMCY okrętowej klasy „hydroplanowca” Richard Dybko, Hartmut Ehlers, Jürgen Eichardt, Christoph Fatz, Zvonimir Freivogel, Reinhard Kramer ROSJA Siergiej W. Patjanin Siergiej A. Bałakin, Nikołaj W. Mitiuckow, 42 Od Sallum do Syrty. Flota w Kampanii Konstantin B. Strelbickij Północnoafrykańskiej lat 1940-1941 STANY ZJEDNOCZONE. A.P. Arthur D. Baker III UKRAINA Anatolij N. Odajnik, Władimir P. Zabłockij WŁOCHY Rafał Mariusz Karczmarek Maurizio Brescia, Achille Rastelli „Lancastery” nad Sassnitz 55 Adres redakcji Wydawnictwo „Okręty Wojenne” Krzywoustego 16, 42-605 Tarnowskie Góry Polska/Poland tel: +48 32 384-48-61 www.okretywojenne.pl Andrij Kharuk e-mail: [email protected] 58 Niszczyciele typu „Battle”, część II Skład, druk i oprawa: DRUKPOL sp. -
Burst of New Orleans
CONFEDERATE HISTORICAL ASSOCIATION OF BELGIUM NavalHistorical Center) ( battleof New Orleans The I I was ordered to report to Commodore W.C. Whittle, commanding the naval station at New Orleans, for duty afloat. A powerful fleet of ships of war and bomb vessels, under the command of Commodore (afterwards Admiral) D. G. Farragut, was then assembling at the mouth of the Mississippi, for an attack upon New Orleans, in which a large land force under General Ben Butler (afterwards called the Beast) was to cooperate. The citizens were under the impression that the place was impregnable. General J. Duncan1, commanding Forts Jackson and St. Philip, below the city, was considered one of the best artillerists in the service ; and the land defense was entrusted to General M. Lovell, with a well appointed force under his command. The people of that gay city were occupied as usual in business and pleasure, and continued unconscious of their peril up to the very time when the Federal fleet passed the forts. But the condition of affairs, so far as naval defense was concerned, was lamentable. The regular C. S. naval fleet consisted of the CSS Louisiana (Captain C.F. McIntosh2) and carrying the flag of Commodore Mitchell ; the steamer McRae (Captain T.B. Huger), carrying six light 32-pounders and nine-inch pivot gun ; the steamer Jackson (Captain F.B. Renshaw), with two pivoted smooth bore 32-pounders ; the small iron plated Ram Manassas (Captain A.F. Warley), carrying one 32-pounder carronade in the bow ; and two launches, each carrying a howitzer and a crew of twenty men. -
The River Steam Boat: a Ticking Time Bomb out of the Experience of The
The River Steam Boat: A Ticking Time Bomb Out of the experience of the early years of the river steam boat, there emerged two architectures of steam-engine design and building. The first and for some years the predominant one was that provided by Boulton and Watt, with their low-pressure condensing steam engine. This was the architecture followed by Robert Fulton with his early success on the Hudson estuary. However, it was less than a decade after Fulton’s successful trip up the Hudson that steam engines based on designs using high pressure steam began to evolve. The result was largely to reshape the pattern of steamboat design and virtually eliminate the earlier low-pressure practices of Fulton, Boulton and Watt. The development of the high-pressure steam engine with its attendant steam boiler was governed almost entirely by practical considerations. The advantages of the simple, compact, low-cost high pressure engine over the low-pressure engine with its complicated condensing apparatus, greater size and weight, and heavy requirements of condensing water were clearly apparent and appropriate to American conditions. These conditions were (1) scarcity of capital and skilled labor, (2) scarcity of repair facilities and (3) limited scale of operation. All of these conditions, at one time or another, contributed to the fateful disasters that followed. Although explosions were by no means confined to boilers generating steam at high pressure, it was with this class of boiler that this type of operating hazard appeared in its most destructive and spectacular form. Every high-pressure boiler was in operation a storehouse of concentrated energy in the form of water and steam at high temperature confined under pressures ranging from 30 to 150 psi [i.e., pounds per square inch] and upward. -
Bibliography of North Carolina Underwater Archaeology
i BIBLIOGRAPHY OF NORTH CAROLINA UNDERWATER ARCHAEOLOGY Compiled by Barbara Lynn Brooks, Ann M. Merriman, Madeline P. Spencer, and Mark Wilde-Ramsing Underwater Archaeology Branch North Carolina Division of Archives and History April 2009 ii FOREWARD In the forty-five years since the salvage of the Modern Greece, an event that marks the beginning of underwater archaeology in North Carolina, there has been a steady growth in efforts to document the state’s maritime history through underwater research. Nearly two dozen professionals and technicians are now employed at the North Carolina Underwater Archaeology Branch (N.C. UAB), the North Carolina Maritime Museum (NCMM), the Wilmington District U.S. Army Corps of Engineers (COE), and East Carolina University’s (ECU) Program in Maritime Studies. Several North Carolina companies are currently involved in conducting underwater archaeological surveys, site assessments, and excavations for environmental review purposes and a number of individuals and groups are conducting ship search and recovery operations under the UAB permit system. The results of these activities can be found in the pages that follow. They contain report references for all projects involving the location and documentation of physical remains pertaining to cultural activities within North Carolina waters. Each reference is organized by the location within which the reported investigation took place. The Bibliography is divided into two geographical sections: Region and Body of Water. The Region section encompasses studies that are non-specific and cover broad areas or areas lying outside the state's three-mile limit, for example Cape Hatteras Area. The Body of Water section contains references organized by defined geographic areas. -
UNIT HISTORIES Regimental Histories and Personal Narratives
A Guide to the Microfiche Edition of CIVIL WAR UNIT HISTORIES Regimental Histories and Personal Narratives Part 1. The Confederate States of America and Border States A Guide to the Microfiche Edition of CIVIL WAR UNIT HISTORIES Regimental Histories and Personal Narratives Part 1. Confederate States of America and Border States Editor: Robert E. Lester Guide compiled by Blair D. Hydrick Library of Congress Cataloging-in-Publication Data Civil War unit histories. The Confederate states of America and border states [microform]: regimental histories and personal narratives / project editors, Robert E. Lester, Gary Hoag. microfiches Accompanied by printed guide compiled by Blair D. Hydrick. ISBN 1-55655-216-5 (microfiche) ISBN 1-55655-257-2 (guide) 1. United States--History~Civil War, 1861-1865--Regimental histories. 2. United States-History-Civil War, 1861-1865-- Personal narratives. I. Lester, Robert. II. Hoag, Gary. III. Hydrick, Blair. [E492] 973.7'42-dc20 92-17394 CIP Copyright© 1992 by University Publications of America. All rights reserved. ISBN 1-55655-257-2. TABLE OF CONTENTS Introduction v Scope and Content Note xiii Arrangement of Material xvii List of Contributing Institutions xix Source Note xxi Editorial Note xxi Fiche Index Confederate States of America Army CSA-1 Navy CSA-9 Alabama AL-15 Arkansas AR-21 Florida FL-23 Georgia GA-25 Kentucky KY-33 Louisiana LA-39 Maryland MD-43 Mississippi MS-49 Missouri MO-55 North Carolina NC-61 South Carolina SC-67 Tennessee TN-75 Texas TX-81 Virginia VA-87 Author Index AI-107 Major Engagements Index ME-113 INTRODUCTION Nothing in the annals of America remotely compares with the Civil War. -
Accident Investigation Reports Under the Locomotive Inspection Act of February 17, 1911, As Amended
INTERSTATE COMMERCE COMMISSION REPORT NO. 3309 IN THE MATTER OF MAKING- ACCIDENT INVESTIGATION REPORTS UNDER THE LOCOMOTIVE INSPECTION ACT OF FEBRUARY 17, 1911, AS AMENDED ATLANTIC COAST LINE RAILROAD March 27, 1950 Accident (boiler explosion) near Tarboro, N. C., on February 24, 1950, caused by overheating of the crown sheet due to low water. REPORT OF THE COMMISSION PATTERSON, Commissioner: On February 24, 1950, about 6:09 p.m., near Tarboro, N. C., the boiler of Atlantic Coast Line Railroad locomotive 411 ex ploded while the locomotive was hauling a freight train at an estimated speed of 20 miles per hour. The engineer, fireman and brakeman were killed. Under authority of section 17 (2) of the Interstate Commerce Act the above-entitled proceeding was referred by the Commission to Commissioner Patterson for consideration and disposition. - 1 - DESCRIPTION OF ACCIDENT Atlantic Coast Line Railroad locomotive 411 departed from South Rocky Mount, N. C, February 24, 1950, at 9r30 a.m., on local freight run known as the Williamston Turn. The run to Vjilliamston, N= C. , a distance of 47 miles, was made without any known unusual incident and the locomotive departed at 3:50 p.m., hauling southbound extra freight train No 411 en route to South Rocky Mount. The train departed from Tarboro, N. C., at 5.57 p.m. and, at about 6:09 p0me, when about 2 miles south of Tarboro, approximately 33 miles from Williams- ton, the boiler of the locomotive exploded iijhile the train was running at an estimated speed of 20 miles per hour. The en gineer, fireman, and brakeman were killed. -
A Historical Assessment of Amphibious Operations from 1941 to the Present
CRM D0006297.A2/ Final July 2002 Charting the Pathway to OMFTS: A Historical Assessment of Amphibious Operations From 1941 to the Present Carter A. Malkasian 4825 Mark Center Drive • Alexandria, Virginia 22311-1850 Approved for distribution: July 2002 c.. Expedit'onaryyystems & Support Team Integrated Systems and Operations Division This document represents the best opinion of CNA at the time of issue. It does not necessarily represent the opinion of the Department of the Navy. Approved for Public Release; Distribution Unlimited. Specific authority: N0014-00-D-0700. For copies of this document call: CNA Document Control and Distribution Section at 703-824-2123. Copyright 0 2002 The CNA Corporation Contents Summary . 1 Introduction . 5 Methodology . 6 The U.S. Marine Corps’ new concept for forcible entry . 9 What is the purpose of amphibious warfare? . 15 Amphibious warfare and the strategic level of war . 15 Amphibious warfare and the operational level of war . 17 Historical changes in amphibious warfare . 19 Amphibious warfare in World War II . 19 The strategic environment . 19 Operational doctrine development and refinement . 21 World War II assault and area denial tactics. 26 Amphibious warfare during the Cold War . 28 Changes to the strategic context . 29 New operational approaches to amphibious warfare . 33 Cold war assault and area denial tactics . 35 Amphibious warfare, 1983–2002 . 42 Changes in the strategic, operational, and tactical context of warfare. 42 Post-cold war amphibious tactics . 44 Conclusion . 46 Key factors in the success of OMFTS. 49 Operational pause . 49 The causes of operational pause . 49 i Overcoming enemy resistance and the supply buildup. -
The Navy in the Civil
The Navies of the Civil War Overview Anderson, Bern. By Sea and by River: the Naval History of the Civil War. New York: Knopf, 1962. F834 A545b Hearn, Chester G. Naval battles of the Civil War. San Diego: Thunder Bay Press, 2000. UN834 H436n 2000 Oversized Material Porter, David D. The Naval History of the Civil War. New York: Sherman Publishing Co., 1886. F834 P84n Union Joiner, Gary D. Mr. Lincoln’s Brown Water Navy: the Mississippi Squadron. Lanham: Rowman & Littlefield Publishers, 2007. UN834 J74m Merrill, James M. The Rebel Shore: the Story of Union Sea Power in the Civil War. Boston: Little, Brown, 1957. F834 M571r Taaffe, Stephen R. Commanding Lincoln's Navy: Union Naval Leadership During the Civil War. Annapolis, Maryland: Naval Institute Press, 2009. UN834 T111c Confederacy Campbell, R. Thomas, editor. Voices of the Confederate Navy: Articles, Letters, Reports, and Reminiscences. Jefferson, North Carolina: McFarland & Company, 2008. UN861 V889 Hearn, Chester G. Gray Raiders of the Sea: How Eight Confederate Warships Destroyed the Union's High Seas Commerce. Camden, Maine: International Marine Publishing, 1992. F834z H436g Scharf, J. Thomas. History of Confederate States Navy from Its Organization to the Surrender of Its Last Vessel. Albany, New York: Joseph McDonough, 1894. F834z S31h 1894 Gunboats Walke, Henry. Naval Scenes on the Western Waters. The gunboats Taylor, Carondelet and Lafayette. [S.l., 187-?] F8347 N318 Gosnell, Harpur Allen. Guns on the Western Waters: the Story of River Gunboats in the Civil War. Baton Rouge: Louisiana State University Press, [1949]. F834 G677g Joyner, Elizabeth Hoxie. The USS Cairo: History and Artifacts of a Civil War Gunboat.