Constant Warning Time Concept Development for Motorist Warning at Grade Crossings
Total Page:16
File Type:pdf, Size:1020Kb
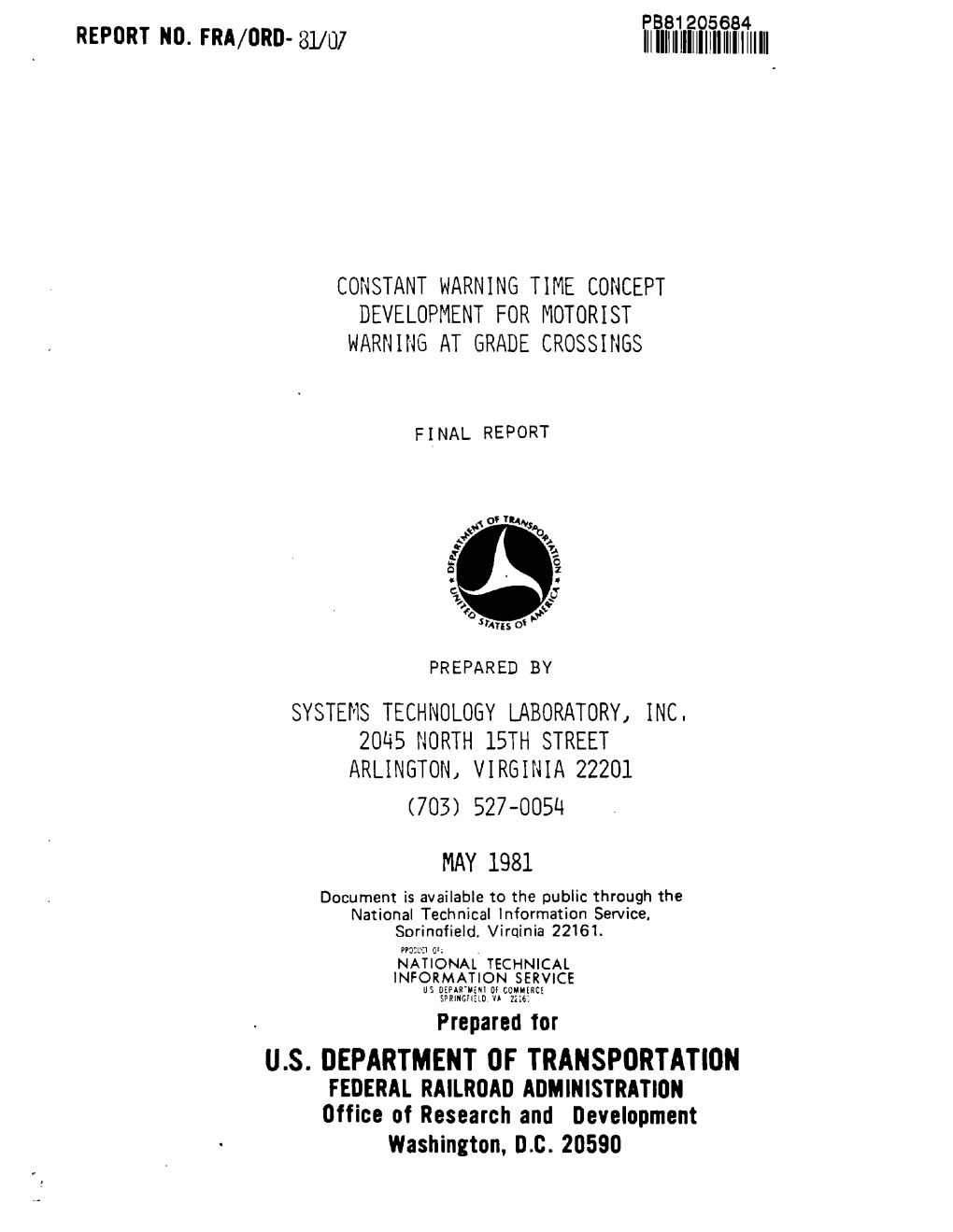
Load more
Recommended publications
-
Identification and Localization of Track Circuit False Occupancy Failures Based on Frequency Domain Reflectometry
sensors Article Identification and Localization of Track Circuit False Occupancy Failures Based on Frequency Domain Reflectometry Tiago A. Alvarenga 1 , Augusto S. Cerqueira 1 , Luciano M. A. Filho 1 , Rafael A. Nobrega 1 , Leonardo M. Honorio 1,* and Henrique Veloso 2 1 Electrical Engineering Department, Federal University of Juiz de Fora, Juiz de Fora 36036-900, MG, Brazil; [email protected] (T.A.A.); [email protected] (A.S.C.); luciano.ma.fi[email protected] (L.M.A.F.); [email protected] (R.A.N.) 2 MRS Logística, Juiz de Fora 36060-010, MG, Brazil; [email protected] * Correspondence: [email protected] Received: 15 October 2020; Accepted: 9 December 2020; Published: 18 December 2020 Abstract: Railway track circuit failures can cause significant train delays and economic losses. A crucial point of the railway operation system is the corrective maintenance process. During this operation, the railway lines have the circulation of trains interrupted in the respective sector, where traffic restoration occurs only after completing the maintenance process. Depending on the cause and length of the track circuit, identifying and solving the problem may take a long time. A tool that assists in track circuit fault detection during an inspection adds agility and efficiency in its restoration and cost reduction. This paper presents a new method, based on frequency domain reflectometry, to diagnose and locate false occupancy failures of track circuits. Initially, simulations are performed considering simplified track circuit approximations to demonstrate the operation of the proposed method, where the fault position is estimated by identifying the null points and through non-linear regression on signal amplitude response. -
Report on Railway Accident with Freight Car Set That Rolled Uncontrolledly from Alnabru to Sydhavna on 24 March 2010
Issued March 2011 REPORT JB 2011/03 REPORT ON RAILWAY ACCIDENT WITH FREIGHT CAR SET THAT ROLLED UNCONTROLLEDLY FROM ALNABRU TO SYDHAVNA ON 24 MARCH 2010 Accident Investigation Board Norway • P.O. Box 213, N-2001 Lillestrøm, Norway • Phone: + 47 63 89 63 00 • Fax: + 47 63 89 63 01 www.aibn.no • [email protected] This report has been translated into English and published by the AIBN to facilitate access by international readers. As accurate as the translation might be, the original Norwegian text takes precedence as the report of reference. The Accident Investigation Board has compiled this report for the sole purpose of improving railway safety. The object of any investigation is to identify faults or discrepancies which may endanger railway safety, whether or not these are causal factors in the accident, and to make safety recommendations. It is not the Board’s task to apportion blame or liability. Use of this report for any other purpose than for railway safety should be avoided. Photos: AIBN and Ruter As Accident Investigation Board Norway Page 2 TABLE OF CONTENTS NOTIFICATION OF THE ACCIDENT ............................................................................................. 4 SUMMARY ......................................................................................................................................... 4 1. INFORMATION ABOUT THE ACCIDENT ..................................................................... 6 1.1 Chain of events ................................................................................................................... -
Road Level Crossing Protection Equipment
Engineering Procedure Signalling CRN SM 013 ROAD LEVEL CROSSING PROTECTION EQUIPMENT Version 2.0 Issued December 2013 Owner: Principal Signal Engineer Approved by: Stewart Rendell Authorised by: Glenn Dewberry Disclaimer. This document was prepared for use on the CRN Network only. John Holland Rail Pty Ltd makes no warranties, express or implied, that compliance with the contents of this document shall be sufficient to ensure safe systems or work or operation. It is the document user’s sole responsibility to ensure that the copy of the document it is viewing is the current version of the document as in use by JHR. JHR accepts no liability whatsoever in relation to the use of this document by any party, and JHR excludes any liability which arises in any manner by the use of this document. Copyright. The information in this document is protected by Copyright and no part of this document may be reproduced, altered, stored or transmitted by any person without the prior consent of JHR. © JHR UNCONTROLLED WHEN PRINTED Page 1 of 66 Issued December 2013 Version 2.0 CRN Engineering Procedure - Signalling CRN SM 013 Road Level Crossing Protection Equipment Document control Revision Date of Approval Summary of change 1.0 June 1999 RIC Standard SC 07 60 01 00 EQ Version 1.0 June 1999. 1.0 July 2011 Conversion to CRN Signalling Standard CRN SM 013. 2.0 December 2013 Inclusion of Safetran S40 and S60 Mechanisms, reformatting of figures and tables, and updating text Summary of changes from previous version Section Summary of change All Include automated -
Geographic Signaling System (Geo)
FIELD REFERENCE MANUAL GEOGRAPHIC SIGNALING SYSTEM (GEO) JULY 2008 (REVISED SEPTEMBER 2018) DOCUMENT NO. SIG-00-05-09 VERSION D Siemens Mobility 700 East Waterfront Drive Munhall, Pennsylvania 15120 1-800-793-SAFE Copyright © 2008-2018 Siemens Mobility, Inc. All rights reserved PRINTED IN THE U.S.A. PROPRIETARY INFORMATION The material contained herein constitutes proprietary and confidential information, and is the intellectual property of Siemens Mobility, Inc., Rail Automation (Siemens) protected under United States patent, copyright and/or other laws and international treaty provisions. This information and the software it describes are for authorized use only, and may not be: (i) modified, translated, reverse engineered, decompiled, disassembled or used to create derivative works; (ii) copied or reproduced for any reason other than specific application needs; or (iii) rented, leased, lent, sublicensed, distributed, remarketed, or in any way transferred; without the prior written authorization of Siemens. This proprietary notice and any other associated labels may not be removed. TRANSLATIONS The manuals and product information of Siemens Mobility, Inc. are intended to be produced and read in English. Any translation of the manuals and product information are unofficial and can be imprecise and inaccurate in whole or in part. Siemens Mobility, Inc. does not warrant the accuracy, reliability, or timeliness of any information contained in any translation of manual or product information from its original official released version in English and shall not be liable for any losses caused by such reliance on the accuracy, reliability, or timeliness of such information. Any person or entity that relies on translated information does so at his or her own risk. -
Signalling Control Table Design and Test Knowledge
CPD Series: Signalling Control Table Design and Test Knowledge Course Code: SC 20-038 30 October 2020 (Friday), 7:00 pm – 10:00 pm Objectives and Learning Outcomes This course aims to provide participants in-depth knowledge in signalling control table design and test. Upon completion of this course, participants will be able to: • Understand how to set a signalling route and call a point machine through a number of relay logic circuit sequences • Understand how to normalize a route through trains passing through and by route button pull with or without approaching train • Understand how the relay logic circuits and Solid Course Structure State Interlocking (SSI) data are implemented This course covers the following major according to the control tables topics: • Understand what tests will be conducted before an interlocking system is put into service • Route Relay Interlocking (RRI) principles and related relay circuit sequence for Who Should Attend route setting Those who are interested in railway signalling • Relationship between control tables technology in design, test and commissioning aspects design and signalling circuits on-site implementation Pre-requisites • Introduction of how the Solid State Participants with signalling knowledge and practical Interlocking (SSI) performs the safety experience are preferable* function in Interlocking design to ensure same integrity of RRI Language • What tests will be done in the signalling Cantonese with English terminologies (with presentation circuit during implementation stage slides in English) • How to do the signalling system control tests (Signal, Route & Point Machine) Venue before a signalling system is put into MTR Academy - Hung Hom Centre, Kowloon, Hong Kong service to ensure the signalling circuit is implemented according to the control Mode of Learning table design Classroom lecture and discussion Speaker Timothy Y.T. -
Education, Research and Collaboration in Railway Signalling, Control and Automation Yul Yunazwin Nazaruddin, Prof
International Webinar on “Railway-University Link: Railway Research and Education Outlook“, Thursday, 21 January’2021 Education, Research and Collaboration in Railway Signalling, Control and Automation Yul Yunazwin Nazaruddin, Prof. Chair of Instrumentation and Control Research Group, ITB Senior Research Fellow of the National Center for Sustainable Transportation Technology (NCSTT) e-mail : [email protected] OUTLINE 1. Graduate Program in Instrumentation and Control with Specialization in Railway Signalling, Control and Automation 2. Research Activities and Collaboration in Railway Signaling, Control and Automation 3. Collaboration with Research and Development Agency, MoT 2 Program Studi Magister Instrumentasi dan Kontrol, ITB, 2020 Graduate Program Master in Instrumentation and Control with special concentration in Railway Signalling, Control and Automation in collaboration with : Faculty of Industrial Technology Institut Teknologi Bandung 3 Master Program in Instrumentation & Control (I&C) • Master Program in Instrumentation dan Control (I&C) is a graduate program in the Faculty of Industrial Technology, Institut Teknologi Bandung (FTI ITB). • Established in 1991, this Program has produced more than hundreds of graduates who are currently working in various universities, industry, institutions / R&D. 4 Master Program in Instrumentation & Control (I&C) • Objectives of the Program “to produce qualified graduates with masters Dozens of graduates have obtained Doctorate degrees and are currently competency level who have the ability pursuing -
HOW to REDUCE the IMPACT of TRACK CIRCUIT FAILURES Stanislas Pinte, Maurizio Palumbo, Emmanuel Fernandes, Robert Grant ERTMS Solutions/Nxgen Rail Services
S. Pinte, M. Palumbo, E. Fernandes, R. Grant HOW TO REDUCE THE IMPACT OF TRACK CIRCUITS FAILURES ERTMS Solutions/NxGen Rail Services HOW TO REDUCE THE IMPACT OF TRACK CIRCUIT FAILURES Stanislas Pinte, Maurizio Palumbo, Emmanuel Fernandes, Robert Grant ERTMS Solutions/NxGen Rail Services Summary Every year, thousands of track circuit failures are reported by railway infrastructure managers in Europe and worldwide, resulting in significant delays which can also lead to substantial economic costs and penalties. For this reason, the ability to detect and diagnose the health of track circuits to prevent or provide a fast response to these failures, can generate a significant benefit for infrastructure managers. In many countries, a process of periodic manual inspection of wayside assets (including track circuits) is in place, but the benefits of this strategy are limited by several factors related to safety, the time required to perform the inspection, and difficulties associated with making manual measurements. With the purpose of minimizing economic loss and operational delay, as well as offering railway infrastructure managers a tool that can provide an automated and effective maintenance strategy, ERTMS Solutions has designed the TrackCircuitLifeCheck (TLC). The TrackCircuitLifeCheck is a track circuit measurement instrument that can be installed on track inspection or commercial trains to automatically diagnose AC, DC, and pulsed track circuits, thus enabling a preventive maintenance strategy, based on the analysis of multi-pass data from each track circuit over time, and the application of standard deviation analysis. KEYWORDS: Track Circuits, Preventive Maintenance, Train Detection, Train Protection, In-Cab Signaling, UM-71, TVM, TrackCircuitLifeCheck. INTRODUCTION This paper presents a high level functional and architectural description of track circuits, with a In order to detect the presence of trains on a special focus on AC track circuits. -
Integration of a Mechanical Interlocking Lever Frame Into a Signalling
MRes in Railway Systems Engineering and Integration College of Engineering, School of Civil Engineering University of Birmingham Integration of a Mechanical Interlocking Lever Frame into a Signalling Demonstrator By: Mersedeh Maksabi Supervisor: Prof. Felix Schmid DATE SUBMITTED: 2013-10-30 University of Birmingham Research Archive e-theses repository This unpublished thesis/dissertation is copyright of the author and/or third parties. The intellectual property rights of the author or third parties in respect of this work are as defined by The Copyright Designs and Patents Act 1988 or as modified by any successor legislation. Any use made of information contained in this thesis/dissertation must be in accordance with that legislation and must be properly acknowledged. Further distribution or reproduction in any format is prohibited without the permission of the copyright holder. Preliminaries Executive Summary Railway signalling has experienced numerous changes and developments, most of which were associated with its long evolutionary history. These changes have occurred gradually from the earliest days of the railway industry when fairly safe distances between the trains were controlled by signalmen with their rudimentary tools to multiple aspects colour light signalling systems and complicated operating systems as well as computerised traffic information systems. Nowadays signalling technology is largely affected by the presence of high performance electromechanical relays which provide the required logic on one hand and securely control the train movement on the other. However, this kind of control system is bulky and requires large space to accommodate. Therefore, such a technology will be expensive as it requires intensive efforts for manufacturing, installation and maintenance. -
New IDEAS for High-Speed Rail
IDEA Innovations Deserving Exploratory Analysis Programs HIGH-SPEED RAIL New IDEAS for High-Speed Rail Annual Progress Report JANUARY 2005 TRANSPORTATION RESEARCH BOARD EXECUTIVE COMMITTEE 2004 OFFICERS CHAIR: MICHAEL S. TOWNES, President and CEO, Hampton Roads PHILIP A. SHUCET, Commissioner, Virginia DOT Transit, Hampton, VA C. MICHAEL WALTON, Ernest H. Cockrell Centennial Chair in VICE CHAIR: JOSEPH H. BOARDMAN, Commissioner, New York Engineering, University of Texas, Austin State DOT LINDA S. WATSON, Executive Director, LYNX—Central Florida EXECUTIVE DIRECTOR: ROBERT E. SKINNER, JR., Transportation Regional Transportation Authority, Orlando, FL Research Board MARION C. BLAKEY, Federal Aviation Administrator, U.S.DOT MEMBERS (ex officio) MICHAEL W. BEHRENS, Executive Director, Texas DOT SAMUEL G. BONASSO, Acting Administrator, Research and Special Programs Administration, U.S.DOT (ex officio) SARAH C. CAMPBELL, President, TransManagement, Inc., Washington, DC REBECCA M. BREWSTER, President and COO, American Transportation Research Institute, Smyrna, GA (ex officio) E. DEAN CARLSON, Director, Carlson Associates, Topeka, KS GEORGE BUGLIARELLO, Chancellor, Polytechnic University and Foreign JOHN L. CRAIG, Director, Nebraska Department of Roads Secretary, National Academy of Engineering (ex officio) DOUGLAS G. DUNCAN, President and CEO, FedEx Freight, Memphis, TN THOMAS H. COLLINS (Adm., U.S. Coast Guard), Commandant, U.S. GENEVIEVE GIULIANO, Director, Metrans Transportation Center and Coast Guard (ex officio) Professor, School of Policy, -
Signal Box Register Series
Signal Box Registers Publication schedule and current state of play as at 10th July 2019 Item Publication dateStatus 1. Great Western PB: 22 December 2007 Out of Print HB: 28 December 2007 Out of Print 1. Great Western PB: 10 May 2011 Published (Revised Edition) HB: 24 May 2011 Published 2. Midland Railway latest draft is version E22 dated Substantially complete. 18th September 2017 Publication expected 2020-2021 3. LNER (Southern Area) PB: 29 May 2012 Published. HB: 6 Nov 2012 Published. 4. Southern Railway PB & HB: 23 April 2009 Published 5. LNWR (includes NSR, Sources include NSR (1998), No work started yet. MCR, FR and L&Y) LNWR (240-599), L&Y (1999). 6. Scotland PB: 31 Oct 2012 Published. HB: 7 Nov 2012 Published. 7. North Eastern Region Work in hand (includes H&B) 8. London Transport PB: 12 Jul 2019 Published. HB: 26 Jul 2019 Published. 9. Ireland PB & HB: 3 August 2015 Published CD-ROM CD: 1 January 2008 Includes Volume 1 CDROM updates #1: 2 February 2008 Corr. Sht 1 & updated vol. 1 GW. #2: 16 September 2008 Corr. Sht 2 & updated vol. 1 GW. #3: 23 April 2009 Plus Volume 4 Southern Railway #4: 24 May 2011 Plus corr. sheet 3 & the GW register (revised edition) #5: 21 June 2012 As above plus correction sheet 4 and volume 3 LNER (Southern) #6: 15 Nov 2012 (DVD-ROM) As above plus correction sheet 5 and volume 6 Scotland #7: 25 Jul 2013 (DVD-ROM) As above plus correction sheet 6 #8: 31 May 2014 (DVD-ROM) As above plus correction sheet 7 #9: 3 Aug 2015 (DVD-ROM) As above plus correction sheet 8 #9: 3 Aug 2015 (CD-ROM) Volume 9 Ireland & Isle of Man #10: 21 Nov 2015 (DVD-ROM) As above plus correction sheet 9 #11: 10 Jul 2019 (DVD-ROM) As above plus correction sheet 10 Volume 8 London Transport Correction sheets 1: 16 January 2008 Amended vol. -
The Bulletin BERNARD LINDER, 1918-2017
ERA BULLETIN — FEBRUARY, 2018 The Bulletin Electric Railroaders’ Association, Incorporated Vol. 61, No. 2 February, 2018 The Bulletin BERNARD LINDER, 1918-2017 Published by the Electric by Alexander Ivanoff Railroaders’ Association, Incorporated, PO Box Longtime ERA Bulletin Editor-in-Chief Ber- Despite having worked for New York City 3323, New York, New nard Linder (ERA #2668) passed away on Transit and having been a railfan, Bernie did York 10163-3323. the evening of December 12, 2017 at the age not hear about ERA until a chance encounter of 99, after a brief illness. Born on March 31, with the late Martin Schachne (ERA #1137). For general inquiries, or 1918, Bernie grew up in in the Bronx and He became a member in 1961 and since Bulletin submissions, became interested in electric traction through 1963, Bernie had been involved in some ca- contact us at bulletin@ erausa.org. ERA’s his parents. His father pacity with what started website is was a newsstand ven- out as the New York Divi- www.erausa.org. dor in the subway and sion Bulletin (now simply he would go with his the Bulletin). He was Editorial Staff: mother to help out. asked by Arthur Lonto to Editor-in-Chief: Jeffrey Erlitz From an early age become the Bulletin Edi- Tri-State News and Bernie collected news tor in 1980, and since Commuter Rail Editor: stories on transit and then his name had been Ronald Yee traction events, as far on well over 400 monthly North American and World as collecting car ros- issues, and until his News Editor: Alexander Ivanoff ters at the age of 13. -
Chapter 5 Signals
CALTRAIN DESIGN CRITERIA CHAPTER 5 – SIGNALS CHAPTER 5 SIGNALS A. GENERAL When the Southern Pacific Railroad (SP) owned and operated the Caltrain corridor, the signal system had been designed based on the mixed operation of freight and passenger trains. The signal system spacing was based upon single direction running, with braking distances for 80 Ton per Operative Brake (TPOB) freight trains at 60 MPH (miles per hour). The Santa Clara, College Park, Fourth Street, and San Jose operators' positions were consolidated into a single dispatch center, with Centralized Traffic Control (CTC) from Santa Clara (Control Point or CP Coast) to CP Tamien. San Francisco Control Points, namely Fourth Street, Potrero, Bayshore, and Brisbane were operated as Manual Interlockings under the control of the San Jose Dispatcher with bi-directional automatic block signaling between Fourth Street and Potrero, and single direction running between control points from Potrero southward. After State Department of Transportation (Caltrans) completed the freeway I-280 retrofit, bi- directional CTC was in effect between Fourth Street and Bayshore. Between 1992 and 1997, signal design was performed by various designers, as a by product of third party contracts on the railroad. There was little consistency between projects, and little overview as to how the projects tied together, and how they would fare with future projects. In 1997, the Caltrain's two signal engineering designers, and the contract operator developed the Caltrain Signal Engineering Design Standards. The new standards have become one of migration. 1.0 SIGNAL SYSTEM MIGRATION The migration of the Caltrain Signal System was defined as follows: a.