Identification and Localization of Track Circuit False Occupancy Failures Based on Frequency Domain Reflectometry
Total Page:16
File Type:pdf, Size:1020Kb
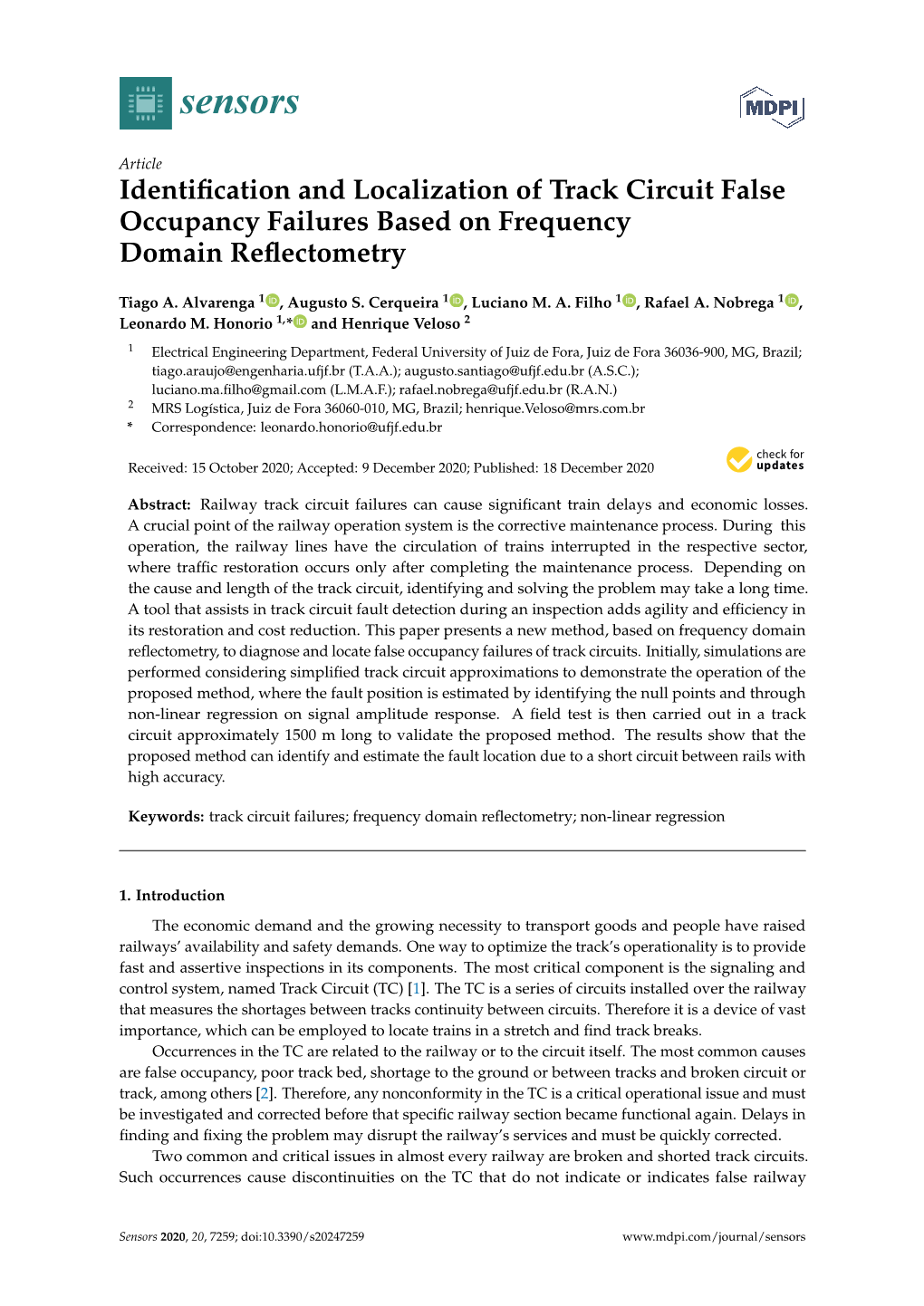
Load more
Recommended publications
-
Report on Railway Accident with Freight Car Set That Rolled Uncontrolledly from Alnabru to Sydhavna on 24 March 2010
Issued March 2011 REPORT JB 2011/03 REPORT ON RAILWAY ACCIDENT WITH FREIGHT CAR SET THAT ROLLED UNCONTROLLEDLY FROM ALNABRU TO SYDHAVNA ON 24 MARCH 2010 Accident Investigation Board Norway • P.O. Box 213, N-2001 Lillestrøm, Norway • Phone: + 47 63 89 63 00 • Fax: + 47 63 89 63 01 www.aibn.no • [email protected] This report has been translated into English and published by the AIBN to facilitate access by international readers. As accurate as the translation might be, the original Norwegian text takes precedence as the report of reference. The Accident Investigation Board has compiled this report for the sole purpose of improving railway safety. The object of any investigation is to identify faults or discrepancies which may endanger railway safety, whether or not these are causal factors in the accident, and to make safety recommendations. It is not the Board’s task to apportion blame or liability. Use of this report for any other purpose than for railway safety should be avoided. Photos: AIBN and Ruter As Accident Investigation Board Norway Page 2 TABLE OF CONTENTS NOTIFICATION OF THE ACCIDENT ............................................................................................. 4 SUMMARY ......................................................................................................................................... 4 1. INFORMATION ABOUT THE ACCIDENT ..................................................................... 6 1.1 Chain of events ................................................................................................................... -
HOW to REDUCE the IMPACT of TRACK CIRCUIT FAILURES Stanislas Pinte, Maurizio Palumbo, Emmanuel Fernandes, Robert Grant ERTMS Solutions/Nxgen Rail Services
S. Pinte, M. Palumbo, E. Fernandes, R. Grant HOW TO REDUCE THE IMPACT OF TRACK CIRCUITS FAILURES ERTMS Solutions/NxGen Rail Services HOW TO REDUCE THE IMPACT OF TRACK CIRCUIT FAILURES Stanislas Pinte, Maurizio Palumbo, Emmanuel Fernandes, Robert Grant ERTMS Solutions/NxGen Rail Services Summary Every year, thousands of track circuit failures are reported by railway infrastructure managers in Europe and worldwide, resulting in significant delays which can also lead to substantial economic costs and penalties. For this reason, the ability to detect and diagnose the health of track circuits to prevent or provide a fast response to these failures, can generate a significant benefit for infrastructure managers. In many countries, a process of periodic manual inspection of wayside assets (including track circuits) is in place, but the benefits of this strategy are limited by several factors related to safety, the time required to perform the inspection, and difficulties associated with making manual measurements. With the purpose of minimizing economic loss and operational delay, as well as offering railway infrastructure managers a tool that can provide an automated and effective maintenance strategy, ERTMS Solutions has designed the TrackCircuitLifeCheck (TLC). The TrackCircuitLifeCheck is a track circuit measurement instrument that can be installed on track inspection or commercial trains to automatically diagnose AC, DC, and pulsed track circuits, thus enabling a preventive maintenance strategy, based on the analysis of multi-pass data from each track circuit over time, and the application of standard deviation analysis. KEYWORDS: Track Circuits, Preventive Maintenance, Train Detection, Train Protection, In-Cab Signaling, UM-71, TVM, TrackCircuitLifeCheck. INTRODUCTION This paper presents a high level functional and architectural description of track circuits, with a In order to detect the presence of trains on a special focus on AC track circuits. -
Signal Box Register Series
Signal Box Registers Publication schedule and current state of play as at 10th July 2019 Item Publication dateStatus 1. Great Western PB: 22 December 2007 Out of Print HB: 28 December 2007 Out of Print 1. Great Western PB: 10 May 2011 Published (Revised Edition) HB: 24 May 2011 Published 2. Midland Railway latest draft is version E22 dated Substantially complete. 18th September 2017 Publication expected 2020-2021 3. LNER (Southern Area) PB: 29 May 2012 Published. HB: 6 Nov 2012 Published. 4. Southern Railway PB & HB: 23 April 2009 Published 5. LNWR (includes NSR, Sources include NSR (1998), No work started yet. MCR, FR and L&Y) LNWR (240-599), L&Y (1999). 6. Scotland PB: 31 Oct 2012 Published. HB: 7 Nov 2012 Published. 7. North Eastern Region Work in hand (includes H&B) 8. London Transport PB: 12 Jul 2019 Published. HB: 26 Jul 2019 Published. 9. Ireland PB & HB: 3 August 2015 Published CD-ROM CD: 1 January 2008 Includes Volume 1 CDROM updates #1: 2 February 2008 Corr. Sht 1 & updated vol. 1 GW. #2: 16 September 2008 Corr. Sht 2 & updated vol. 1 GW. #3: 23 April 2009 Plus Volume 4 Southern Railway #4: 24 May 2011 Plus corr. sheet 3 & the GW register (revised edition) #5: 21 June 2012 As above plus correction sheet 4 and volume 3 LNER (Southern) #6: 15 Nov 2012 (DVD-ROM) As above plus correction sheet 5 and volume 6 Scotland #7: 25 Jul 2013 (DVD-ROM) As above plus correction sheet 6 #8: 31 May 2014 (DVD-ROM) As above plus correction sheet 7 #9: 3 Aug 2015 (DVD-ROM) As above plus correction sheet 8 #9: 3 Aug 2015 (CD-ROM) Volume 9 Ireland & Isle of Man #10: 21 Nov 2015 (DVD-ROM) As above plus correction sheet 9 #11: 10 Jul 2019 (DVD-ROM) As above plus correction sheet 10 Volume 8 London Transport Correction sheets 1: 16 January 2008 Amended vol. -
Chapter 5 Signals
CALTRAIN DESIGN CRITERIA CHAPTER 5 – SIGNALS CHAPTER 5 SIGNALS A. GENERAL When the Southern Pacific Railroad (SP) owned and operated the Caltrain corridor, the signal system had been designed based on the mixed operation of freight and passenger trains. The signal system spacing was based upon single direction running, with braking distances for 80 Ton per Operative Brake (TPOB) freight trains at 60 MPH (miles per hour). The Santa Clara, College Park, Fourth Street, and San Jose operators' positions were consolidated into a single dispatch center, with Centralized Traffic Control (CTC) from Santa Clara (Control Point or CP Coast) to CP Tamien. San Francisco Control Points, namely Fourth Street, Potrero, Bayshore, and Brisbane were operated as Manual Interlockings under the control of the San Jose Dispatcher with bi-directional automatic block signaling between Fourth Street and Potrero, and single direction running between control points from Potrero southward. After State Department of Transportation (Caltrans) completed the freeway I-280 retrofit, bi- directional CTC was in effect between Fourth Street and Bayshore. Between 1992 and 1997, signal design was performed by various designers, as a by product of third party contracts on the railroad. There was little consistency between projects, and little overview as to how the projects tied together, and how they would fare with future projects. In 1997, the Caltrain's two signal engineering designers, and the contract operator developed the Caltrain Signal Engineering Design Standards. The new standards have become one of migration. 1.0 SIGNAL SYSTEM MIGRATION The migration of the Caltrain Signal System was defined as follows: a. -
Highway-Rail Crossing Warning Systems and Traffic Signals Manual
Interconnection of Highway-Rail Grade Crossing Warning Systems and Highway Traffic Signals 1 INTRODUCTION Welcome to this seminar on Interconnection of Highway-Rail Grade Crossing Warning Systems and Highway Traffic Signals. Over the past eight years, I have had the opportunity to present this seminar to persons from the Federal Railroad Administration, the Federal Highway Administration, numerous state Departments of Transportation, city, county and state traffic engineering and signal departments as well as many railroads. Obviously, this is a highly specialized topic, one that receives very little attention in terms of available training. However, from the perspective of safety, it requires far more attention than it normally receives. Only when a catastrophic event occurs such as the Fox River Grove crash in October of 1995 does the need for training of this type become apparent. Following the Fox River Grove crash, I was approached by the Oklahoma Department of Transportation in 1996, inquiring if I would have an interest in assisting them with understanding interconnection and preemption. This seminar is the ongoing continuation of that effort. My background includes over 31 years of active involvement in both highway traffic signal and railroad signal application, design and maintenance. This workbook is a compilation of information, drawings, standards, recommended practices and my ideas to assist you in following with the presentation and to provide a future reference as you need it. It has been developed as I have presented seminars and I strive to continually update it to reflect the most current information available. Some sections have been reproduced from the Manual on Uniform Traffic Control Devices which exists in the public domain. -
LNW Route Specification 2017
Delivering a better railway for a better Britain Route Specifications 2017 London North Western London North Western July 2017 Network Rail – Route Specifications: London North Western 02 SRS H.44 Roses Line and Branches (including Preston 85 Route H: Cross-Pennine, Yorkshire & Humber and - Ormskirk and Blackburn - Hellifield North West (North West section) SRS H.45 Chester/Ellesmere Port - Warrington Bank Quay 89 SRS H.05 North Transpennine: Leeds - Guide Bridge 4 SRS H.46 Blackpool South Branch 92 SRS H.10 Manchester Victoria - Mirfield (via Rochdale)/ 8 SRS H.98/H.99 Freight Trunk/Other Freight Routes 95 SRS N.07 Weaver Junction to Liverpool South Parkway 196 Stalybridge Route M: West Midlands and Chilterns SRS N.08 Norton Bridge/Colwich Junction to Cheadle 199 SRS H.17 South Transpennine: Dore - Hazel Grove 12 Hulme Route Map 106 SRS H.22 Manchester Piccadilly - Crewe 16 SRS N.09 Crewe to Kidsgrove 204 M1 and M12 London Marylebone to Birmingham Snow Hill 107 SRS H.23 Manchester Piccadilly - Deansgate 19 SRS N.10 Watford Junction to St Albans Abbey 207 M2, M3 and M4 Aylesbury lines 111 SRS H.24 Deansgate - Liverpool South Parkway 22 SRS N.11 Euston to Watford Junction (DC Lines) 210 M5 Rugby to Birmingham New Street 115 SRS H.25 Liverpool Lime Street - Liverpool South Parkway 25 SRS N.12 Bletchley to Bedford 214 M6 and M7 Stafford and Wolverhampton 119 SRS H.26 North Transpennine: Manchester Piccadilly - 28 SRS N.13 Crewe to Chester 218 M8, M9, M19 and M21 Cross City Souh lines 123 Guide Bridge SRS N.99 Freight lines 221 M10 ad M22 -
GENERAL 1.1 Description of Work This Project Provides For
SECTION 01010 SUMMARY OF WORK PART 1 – GENERAL 1.1 Description of Work This project provides for the modernization and technology re-fresh of the existing, discrete phase selective track circuits on SEPTA’s Railroad Division’s, two (2) track, West Chester Line with new solid state electronic track circuits (ETC’s). These electronic track circuits shall be configured for cut-sections and end-of-siding (interlocking) operations. The scope of the tech refresh shall be from and not including Arsenal Interlocking (track circuits 301 and 302) to and Including Elwyn Interlocking. In addition, this scope shall include, but not be limited to the retirement of wired circuitry to the extent as directed by the SEPTA Project Manager and shall include: retirement of automatic colorlight signals (not including Interlocking signals), retirement of the signal lighting circuits, traffic line circuits, cab applications circuits, track cab signal code rate circuits, etc which shall be converted into software equations and driven by the ETC’s. The ETC’s shall be configured and provided to support those locations shown on the drawing “Arsenal to Elwyn, Automatic Signals, Signal Spacing Diagram, Sh’s 1 and 2” for which there are two track automatic signal locations and Interlocking locations. The new ETC’s shall form the basis of a new cab signals with no waysides and the cab signal four aspect, code rate progression shall remain the same. The ETC’s shall interface to the existing vital relays, 12 DC power supplies, impedance bonds and 2 conductor No. 6 twisted track wires. The locations circuit drawings shall be provided to the successful bidder at the time of Notice To Proceed. -
Western Route Strategic Plan V7
Route Strategic Plan Western Route Version 7.0: Strategic Business Plan submission 2nd February 2018 Western Route Strategic Plan Contents Section Title Description Page 1 Foreword and summary Summary of our plan giving proposed high level outputs and challenges in CP6 3 2 Stakeholder priorities Overview of customer and stakeholder priorities 14 3 Route objectives Summary of our objectives for CP6 using our scorecard 26 4 Activity prioritisation on a page Overview of the opportunities, constraints and risks associated with each objective area, the 32 controls for managing these and the resulting output across CP5 and CP6 5 Activities & expenditure High level summary of the cost and activity associated with our plan based on the prioritisation in 41 section 4 6 Customer focus & capacity strategy Summary of customer and capacity themed strategies that will be employed to deliver our plan 66 7 Cost competitiveness & delivery strategy Summary of delivery strategies that will be employed, and of headwinds and efficiency plans 69 accounted developed to date 8 Culture strategy Summary of the culture themed strategies that will be deployed to deliver our plan 80 9 Strategy for commercial focus Summary of our strategy and plans to source alternative investment 86 10 CP6 regulatory framework Information relating to our revenue requirement and access charging income 88 11 Sign-off Senior level commitment from relevant functions 91 Appendix A Joint performance activity prioritisation by Overview of the opportunities, constraints and risks associated -
Application of Communication Based Moving Block Systems on Existing Metro Lines
Computers in Railways X 391 Application of communication based Moving Block systems on existing metro lines L. Lindqvist1 & R. Jadhav2 1Centre of Excellence, Bombardier Transportation, Spain 2Sales, Bombardier Transportation, USA Abstract The unique features of Communication Based Train Control (CBTC) systems with Moving Block (MB) capability makes them uniquely suited for application ‘on top’ of existing Mass Transit or Metro systems, permitting a capacity increase in these systems. This paper defines and describes the features of modern CBTC Moving Block systems such as the Bombardier* CITYFLO* 450 or CITYFLO 650 solutions that make them suited for ‘overlay’ application ‘on top’ of the existing systems and gives an example of such an application in a main European Metro. Note: *Trademark (s) of Bombardier Inc. or its subsidiaries. Keywords: CBTC, Moving Block, CITYFLO, TRS, Movement Authority, norming point, headway. 1 Introduction The use of radio as a method of communication between the train and wayside in Mass Transit systems, instead of the traditional track circuits/axle counters and loops is gaining popularity. The radio based CBTC systems are uniquely suited for application ‘on top’ of existing Mass Transit or Metro systems for increased traffic capacity as CBTC systems normally do not interfere with the existing systems. This allows an installation of the CBTC system in a line in operation whilst maintaining full safety and capacity during the process. The fact that CBTC systems also allow Moving Block operation adds to the -
Modelling Interlocking Systems for Railway Stations
Modelling Interlocking Systems for Railway Stations Marie Le Bliguet Andreas Andersen Kjær Kongens Lyngby 2008 IMM-M.Sc.-2008-68 Technical University of Denmark Department of Informatics and Mathematical Modelling Building 321, DK-2800 Kongens Lyngby, Denmark Phone +45 45253351, Fax +45 45882673 [email protected] www.imm.dtu.dk Summary Interlocking systems are used for ensuring the safety of trains. This master thesis is made in cooperation with Banedanmark and deals with relay-based interlocking systems for railway stations. The goal of this project is to develop a formal method for verifying that such systems guarantee the safety of trains. By using RSL models of interlocking systems, this thesis deduces an automated procedure for making an RSL-SAL transition system that defines the dynamic behaviour of an interlocking system. Also, the procedure specifies how to auto- generate confidence conditions for the generated transition system, formulated using Linear Temporal Logic (LTL). Finally, a tool for computing such a transi- tion system and its associated confidence conditions is implemented using Java. Furthermore, this thesis develops patterns for specifying the behaviour of ex- ternal inputs to an interlocking system (e.g. a rule can define when a train can enter a station), formulated using RSL-SAL. Also, patterns for specifying safety properties are developed using LTL. Altogether, the tool and patterns define a method that uses the state-space based model checker SAL for verifying that interlocking systems guarantee the safety of trains. The method has successfully been applied to a Danish railway station. Keywords: Formal methods, Linear Temporal Logic, Model checking, Mod- elling, Railway interlocking systems, RAISE Specification Language, RSL-SAL, SAL. -
Communications-Based Train Control (Cbtc) Before/After Cost Effectiveness Study
COMMUNICATIONS-BASED TRAIN CONTROL (CBTC) BEFORE/AFTER COST EFFECTIVENESS STUDY March 2011 http://www.fta.dot.gov/research Report FTA-TX-26-7005.2010.01 1. REPORT DOCUMENTATION PAGE Form Approved OMB No. 0704-0188 1. AGENCY USE ONLY (Leave blank) 2. REPORT DATE 3. REPORT TYPE AND DATES COVERED March 2011 Final Draft Report, July 2009 - March 2011 4. TITLE AND SUBTITLE 5. FUNDING/GRANT NUMBER Communications-Based Train Control (CBTC) Before/After TX-26-7005 Cost Effectiveness Study 6. AUTHOR(S) David Rojas, P.E. and Eric Phillips, P.E. 7. PERFORMING ORGANIZATION NAME(S) AND 8. PERFORMING ORGANIZATION REPORT ADDRESS(ES) NUMBER Lea+Elliott, Inc. FTA-TX-26-7005.2010.01 785 Market Street, 12th Floor San Francisco, California 94103 9. SPONSORING/MONITORING AGENCY NAME(S) AND 10. SPONSORING/MONITORING ADDRESS(ES) AGENCY REPORT NUMBER Federal Transit Administration FTA-TX-26-7005.2010.01 U.S. Department of Transportation Website [http://www.fta.dot.gov/research] 1200 New Jersey Avenue, SE Washington, DC 20590 11. SUPPLEMENTARY NOTES 12a. DISTRIBUTION/AVAILABILITY STATEMENT 12b. DISTRIBUTION CODE Available From: National Technical Information Service TRI-20 (NTIS), Springfield, VA 22161. Phone 703.605.6000 Fax 703.605.6900 Email [[email protected]] 13. ABSTRACT San Francisco Municipal Railway (Muni) undertook a retrofit of a fixed-block signaling system with a communications-based train control (CBTC) system in the subway portion of their light rail system (Muni Metro subway) in 1998. This report presents the findings of an in-depth study of the effectiveness of implementing the project. Along with a project narrative, two forms of analysis are provided: a quantitative cost-benefit analysis (CBA) and a qualitative analysis. -
Next Generation Track Circuits DTFR53-11-D-00008L
86'HSDUWPHQWRI 7UDQVSRUWDWLRQ 1H[W*HQHUDWLRQ7UDFN&LUFXLWV )HGHUDO5DLOURDG $GPLQLVWUDWLRQ 2IILFHRI5HVHDUFK 'HYHORSPHQW DQG7HFKQRORJ\ :DVKLQJWRQ'& '27)5$25' )LQDO5HSRUW $SULO NOTICE This document is disseminated under the sponsorship of the Department of Transportation in the interest of information exchange. The United States Government assumes no liability for its contents or use thereof. Any opinions, findings and conclusions, or recommendations expressed in this material do not necessarily reflect the views or policies of the United States Government, nor does mention of trade names, commercial products, or organizations imply endorsement by the United States Government. The United States Government assumes no liability for the content or use of the material contained in this document. NOTICE The United States Government does not endorse products or manufacturers. Trade or manufacturers’ names appear herein solely because they are considered essential to the objective of this report. REPORT DOCUMENTATION PAGE Form Approved OMB No. 0704-0188 Public reporting burden for this collection of information is estimated to average 1 hour per response, including the time for reviewing instructions, searching existing data sources, gathering and maintaining the data needed, and completing and reviewing the collection of information. Send comments regarding this burden estimate or any other aspect of this collection of information, including suggestions for reducing this burden, to Washington Headquarters Services, Directorate for Information Operations and Reports, 1215 Jefferson Davis Highway, Suite 1204, Arlington, VA 22202-4302, and to the Office of Management and Budget, Paperwork Reduction Project (0704-0188), Washington, DC 20503. 1. AGENCY USE ONLY (Leave blank) 2. REPORT DATE 3. REPORT TYPE AND DATES COVERED April 2018 Technical Report 4.