How Track Circuits Detect and Protect Trains Jodi Scalise November 2014 Railwaysignalling.Eu, Italy [email protected]
Total Page:16
File Type:pdf, Size:1020Kb
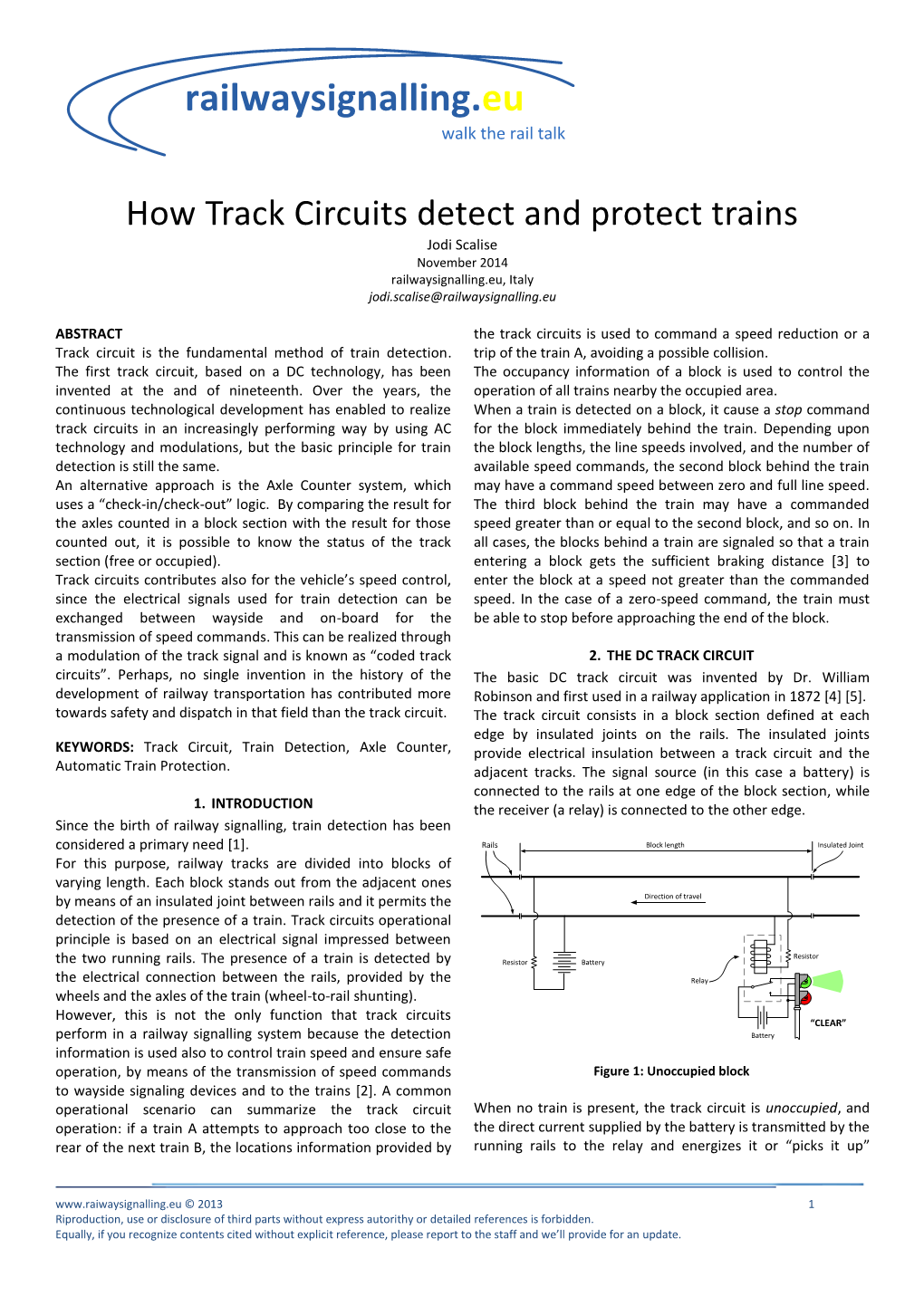
Load more
Recommended publications
-
Identification and Localization of Track Circuit False Occupancy Failures Based on Frequency Domain Reflectometry
sensors Article Identification and Localization of Track Circuit False Occupancy Failures Based on Frequency Domain Reflectometry Tiago A. Alvarenga 1 , Augusto S. Cerqueira 1 , Luciano M. A. Filho 1 , Rafael A. Nobrega 1 , Leonardo M. Honorio 1,* and Henrique Veloso 2 1 Electrical Engineering Department, Federal University of Juiz de Fora, Juiz de Fora 36036-900, MG, Brazil; [email protected] (T.A.A.); [email protected] (A.S.C.); luciano.ma.fi[email protected] (L.M.A.F.); [email protected] (R.A.N.) 2 MRS Logística, Juiz de Fora 36060-010, MG, Brazil; [email protected] * Correspondence: [email protected] Received: 15 October 2020; Accepted: 9 December 2020; Published: 18 December 2020 Abstract: Railway track circuit failures can cause significant train delays and economic losses. A crucial point of the railway operation system is the corrective maintenance process. During this operation, the railway lines have the circulation of trains interrupted in the respective sector, where traffic restoration occurs only after completing the maintenance process. Depending on the cause and length of the track circuit, identifying and solving the problem may take a long time. A tool that assists in track circuit fault detection during an inspection adds agility and efficiency in its restoration and cost reduction. This paper presents a new method, based on frequency domain reflectometry, to diagnose and locate false occupancy failures of track circuits. Initially, simulations are performed considering simplified track circuit approximations to demonstrate the operation of the proposed method, where the fault position is estimated by identifying the null points and through non-linear regression on signal amplitude response. -
Report on Railway Accident with Freight Car Set That Rolled Uncontrolledly from Alnabru to Sydhavna on 24 March 2010
Issued March 2011 REPORT JB 2011/03 REPORT ON RAILWAY ACCIDENT WITH FREIGHT CAR SET THAT ROLLED UNCONTROLLEDLY FROM ALNABRU TO SYDHAVNA ON 24 MARCH 2010 Accident Investigation Board Norway • P.O. Box 213, N-2001 Lillestrøm, Norway • Phone: + 47 63 89 63 00 • Fax: + 47 63 89 63 01 www.aibn.no • [email protected] This report has been translated into English and published by the AIBN to facilitate access by international readers. As accurate as the translation might be, the original Norwegian text takes precedence as the report of reference. The Accident Investigation Board has compiled this report for the sole purpose of improving railway safety. The object of any investigation is to identify faults or discrepancies which may endanger railway safety, whether or not these are causal factors in the accident, and to make safety recommendations. It is not the Board’s task to apportion blame or liability. Use of this report for any other purpose than for railway safety should be avoided. Photos: AIBN and Ruter As Accident Investigation Board Norway Page 2 TABLE OF CONTENTS NOTIFICATION OF THE ACCIDENT ............................................................................................. 4 SUMMARY ......................................................................................................................................... 4 1. INFORMATION ABOUT THE ACCIDENT ..................................................................... 6 1.1 Chain of events ................................................................................................................... -
HOW to REDUCE the IMPACT of TRACK CIRCUIT FAILURES Stanislas Pinte, Maurizio Palumbo, Emmanuel Fernandes, Robert Grant ERTMS Solutions/Nxgen Rail Services
S. Pinte, M. Palumbo, E. Fernandes, R. Grant HOW TO REDUCE THE IMPACT OF TRACK CIRCUITS FAILURES ERTMS Solutions/NxGen Rail Services HOW TO REDUCE THE IMPACT OF TRACK CIRCUIT FAILURES Stanislas Pinte, Maurizio Palumbo, Emmanuel Fernandes, Robert Grant ERTMS Solutions/NxGen Rail Services Summary Every year, thousands of track circuit failures are reported by railway infrastructure managers in Europe and worldwide, resulting in significant delays which can also lead to substantial economic costs and penalties. For this reason, the ability to detect and diagnose the health of track circuits to prevent or provide a fast response to these failures, can generate a significant benefit for infrastructure managers. In many countries, a process of periodic manual inspection of wayside assets (including track circuits) is in place, but the benefits of this strategy are limited by several factors related to safety, the time required to perform the inspection, and difficulties associated with making manual measurements. With the purpose of minimizing economic loss and operational delay, as well as offering railway infrastructure managers a tool that can provide an automated and effective maintenance strategy, ERTMS Solutions has designed the TrackCircuitLifeCheck (TLC). The TrackCircuitLifeCheck is a track circuit measurement instrument that can be installed on track inspection or commercial trains to automatically diagnose AC, DC, and pulsed track circuits, thus enabling a preventive maintenance strategy, based on the analysis of multi-pass data from each track circuit over time, and the application of standard deviation analysis. KEYWORDS: Track Circuits, Preventive Maintenance, Train Detection, Train Protection, In-Cab Signaling, UM-71, TVM, TrackCircuitLifeCheck. INTRODUCTION This paper presents a high level functional and architectural description of track circuits, with a In order to detect the presence of trains on a special focus on AC track circuits. -
Approved Signalling Items for the ARTC Network ESA-00-01
Division / Business Unit: Corporate Services & Safety Function: Signalling Document Type: Catalogue Approved Signalling Items for the ARTC Network ESA-00-01 Applicability ARTC Network Wide SMS Publication Requirement Internal / External Primary Source Existing ARTC Type Approvals Document Status Version # Date Reviewed Prepared by Reviewed by Endorsed Approved 1.3 03 May 2021 Standards Stakeholders Manager General Manager Signalling Technical Standards Standards 03/05/2021 Amendment Record Amendment Date Reviewed Clause Description of Amendment Version # 1.0 23 Mar 20 First issue of catalogue that lists signalling items and communication items related to signalling systems approved for use on the ARTC network. 1.1 26 Jun 20 New approved items added based on type approval and compliance to ARTC specification 1.2 24 Nov 20 New approved items added based on type approval and compliance to ARTC specification © Australian Rail Track Corporation Limited (ARTC) Disclaimer This document has been prepared by ARTC for internal use and may not be relied on by any other party without ARTC’s prior written consent. Use of this document shall be subject to the terms of the relevant contract with ARTC. ARTC and its employees shall have no liability to unauthorised users of the information for any loss, damage, cost or expense incurred or arising by reason of an unauthorised user using or relying upon the information in this document, whether caused by error, negligence, omission or misrepresentation in this document. This document is uncontrolled when printed. Authorised users of this document should visit ARTC’s extranet (www.artc.com.au) to access the latest version of this document. -
AS 7651 Axle Counters
AS 7651:2020 Axle Counters Train Control Systems Standard Please note this is a RISSB Australian Standard® draft Document content exists for RISSB product development purposes only and should not be relied upon or considered as final published content. Any questions in relation to this document or RISSB’s accredited development process should be referred to RISSB. AS 7651:2020 RISSB Office Phone: AxleEmail: Counters Web: (07) 3724 0000 [email protected] www.rissb.com.au Overseas: +61 7 3724 0000 AS 7651 Assigned Standard Development Manager Name: Cris Fitzhardinge Phone: 0419 916 693 Email: [email protected] Draft for Public Comment AS 7651:2020 Axle Counters This Australian Standard® AS 7651 Axle Counters was prepared by a Rail Industry Safety and Standards Board (RISSB) Development Group consisting of representatives from the following organisations: Sydney Trains United Goninian Limited Queensland Rail Aldridge Transport for NSW Metro Trains Melbourne ARC Infrastructure Mott MacDonald Frauscher Australia Thales PTV Siemens PTA WA NJT Rail Services The Standard was approved by the Development Group and the Enter Standing Committee Standing Committee in Select SC approval date. On Select Board approval date the RISSB Board approved the Standard for release. Choose the type of review Development of the Standard was undertaken in accordance with RISSB’s accredited process. As part of the approval process, the Standing Committee verified that proper process was followed in developing the Standard RISSB wishes to acknowledge the positive contribution of subject matter experts in the development of this Standard. Their efforts ranged from membership of the Development Group through to individuals providing comment on a draft of the Standard during the open review. -
Signal Box Register Series
Signal Box Registers Publication schedule and current state of play as at 10th July 2019 Item Publication dateStatus 1. Great Western PB: 22 December 2007 Out of Print HB: 28 December 2007 Out of Print 1. Great Western PB: 10 May 2011 Published (Revised Edition) HB: 24 May 2011 Published 2. Midland Railway latest draft is version E22 dated Substantially complete. 18th September 2017 Publication expected 2020-2021 3. LNER (Southern Area) PB: 29 May 2012 Published. HB: 6 Nov 2012 Published. 4. Southern Railway PB & HB: 23 April 2009 Published 5. LNWR (includes NSR, Sources include NSR (1998), No work started yet. MCR, FR and L&Y) LNWR (240-599), L&Y (1999). 6. Scotland PB: 31 Oct 2012 Published. HB: 7 Nov 2012 Published. 7. North Eastern Region Work in hand (includes H&B) 8. London Transport PB: 12 Jul 2019 Published. HB: 26 Jul 2019 Published. 9. Ireland PB & HB: 3 August 2015 Published CD-ROM CD: 1 January 2008 Includes Volume 1 CDROM updates #1: 2 February 2008 Corr. Sht 1 & updated vol. 1 GW. #2: 16 September 2008 Corr. Sht 2 & updated vol. 1 GW. #3: 23 April 2009 Plus Volume 4 Southern Railway #4: 24 May 2011 Plus corr. sheet 3 & the GW register (revised edition) #5: 21 June 2012 As above plus correction sheet 4 and volume 3 LNER (Southern) #6: 15 Nov 2012 (DVD-ROM) As above plus correction sheet 5 and volume 6 Scotland #7: 25 Jul 2013 (DVD-ROM) As above plus correction sheet 6 #8: 31 May 2014 (DVD-ROM) As above plus correction sheet 7 #9: 3 Aug 2015 (DVD-ROM) As above plus correction sheet 8 #9: 3 Aug 2015 (CD-ROM) Volume 9 Ireland & Isle of Man #10: 21 Nov 2015 (DVD-ROM) As above plus correction sheet 9 #11: 10 Jul 2019 (DVD-ROM) As above plus correction sheet 10 Volume 8 London Transport Correction sheets 1: 16 January 2008 Amended vol. -
Chapter 5 Signals
CALTRAIN DESIGN CRITERIA CHAPTER 5 – SIGNALS CHAPTER 5 SIGNALS A. GENERAL When the Southern Pacific Railroad (SP) owned and operated the Caltrain corridor, the signal system had been designed based on the mixed operation of freight and passenger trains. The signal system spacing was based upon single direction running, with braking distances for 80 Ton per Operative Brake (TPOB) freight trains at 60 MPH (miles per hour). The Santa Clara, College Park, Fourth Street, and San Jose operators' positions were consolidated into a single dispatch center, with Centralized Traffic Control (CTC) from Santa Clara (Control Point or CP Coast) to CP Tamien. San Francisco Control Points, namely Fourth Street, Potrero, Bayshore, and Brisbane were operated as Manual Interlockings under the control of the San Jose Dispatcher with bi-directional automatic block signaling between Fourth Street and Potrero, and single direction running between control points from Potrero southward. After State Department of Transportation (Caltrans) completed the freeway I-280 retrofit, bi- directional CTC was in effect between Fourth Street and Bayshore. Between 1992 and 1997, signal design was performed by various designers, as a by product of third party contracts on the railroad. There was little consistency between projects, and little overview as to how the projects tied together, and how they would fare with future projects. In 1997, the Caltrain's two signal engineering designers, and the contract operator developed the Caltrain Signal Engineering Design Standards. The new standards have become one of migration. 1.0 SIGNAL SYSTEM MIGRATION The migration of the Caltrain Signal System was defined as follows: a. -
Highway-Rail Crossing Warning Systems and Traffic Signals Manual
Interconnection of Highway-Rail Grade Crossing Warning Systems and Highway Traffic Signals 1 INTRODUCTION Welcome to this seminar on Interconnection of Highway-Rail Grade Crossing Warning Systems and Highway Traffic Signals. Over the past eight years, I have had the opportunity to present this seminar to persons from the Federal Railroad Administration, the Federal Highway Administration, numerous state Departments of Transportation, city, county and state traffic engineering and signal departments as well as many railroads. Obviously, this is a highly specialized topic, one that receives very little attention in terms of available training. However, from the perspective of safety, it requires far more attention than it normally receives. Only when a catastrophic event occurs such as the Fox River Grove crash in October of 1995 does the need for training of this type become apparent. Following the Fox River Grove crash, I was approached by the Oklahoma Department of Transportation in 1996, inquiring if I would have an interest in assisting them with understanding interconnection and preemption. This seminar is the ongoing continuation of that effort. My background includes over 31 years of active involvement in both highway traffic signal and railroad signal application, design and maintenance. This workbook is a compilation of information, drawings, standards, recommended practices and my ideas to assist you in following with the presentation and to provide a future reference as you need it. It has been developed as I have presented seminars and I strive to continually update it to reflect the most current information available. Some sections have been reproduced from the Manual on Uniform Traffic Control Devices which exists in the public domain. -
COUNTINGWORLD the Customer Magazine for Axle Counter Systems 09.2018
COUNTINGWORLD The Customer Magazine for Axle Counter Systems 09.2018 www.thalesgroup.com/germany CHALLENGING THE STATUS QUO LITECE™ PAVING THE WAY FOR SMART SENSING TECHNOLOGIES A RAILWAY ACROSS THE DESERT MOBILITY SOLUTIONS FOR THE TOUGHEST ENVIRONMENT ON THE PLANET THE “WARRIORS” CHOOSE THALES THALES FLAGSHIP AXLE COUNTER SYSTEM DEBUTS IN SAN FRANCISCO maintenance multiply? Is an increase in train In addition, finite element calculations and density justifiable when the operational cost simulation of environmental conditions are rises, but the number of passengers does not? suitable methodical instruments to get the basic It is, after all, the minimum level of safety required design right from the beginning. and affordable costs, i.e. the expected life cycle costs or investment costs, that determine Nothing replaces real life a supplier’s selection of signalling system or experience to confirm resilience product. and reliability Availability and punctuality become With the new Lite4ce™ smart sensor, Thales measurable decision criteria is introducing an entirely new concept of wheel sensing for Axle Counting Systems: an Neglected in contract award decisions in the unprecedented challenge for a track-based past due to a lack of success criteria, both signalling system – innovative and fascinating punctuality and availability are slowly becoming – but with limited ability to rely on decades of the evaluation pillars for performance-based operational experience. contracts. Fully redundant “2 out of 3” signalling system concepts have been on the signalling Lite4ce™ – at the forefront of Dear Readers, market for many years and have drastically sensor technology reduced if not mitigated the effects of single points RELIABILITY BY DESIGN of failures. -
West Midlands and Chilterns Route Utilisation Strategy Draft for Consultation Contents 3 Foreword 4 Executive Summary 9 1
November 2010 West Midlands and Chilterns Route Utilisation Strategy Draft for Consultation Contents 3 Foreword 4 Executive summary 9 1. Background 11 2. Dimensions 20 3. Current capacity, demand, and delivery 59 4. Planned changes to infrastructure and services 72 5. Planning context and future demand 90 6. Gaps and options 149 7. Emerging strategy and longer-term vision 156 8. Stakeholder consultation 157 Appendix A 172 Appendix B 178 Glossary Foreword Regional economies rely on investment in transport infrastructure to sustain economic growth. With the nation’s finances severely constrained, between Birmingham and London Marylebone, as any future investment in transport infrastructure well as new journey opportunities between Oxford will have to demonstrate that it can deliver real and London. benefits for the economy, people’s quality of life, This RUS predicts that overall passenger demand in and the environment. the region will increase by 32 per cent over the next 10 This draft Route Utilisation Strategy (RUS) sets years. While Network Rail’s Delivery Plan for Control out the priorities for rail investment in the West Period 4 will accommodate much of this demand up Midlands area and the Chiltern route between to 2019, this RUS does identify gaps and recommends Birmingham and London Marylebone for the next measures to address these. 30 years. We believe that the options recommended Where the RUS has identified requirements for can meet the increased demand forecast by this interventions to be made, it seeks to do so by making RUS for both passenger and freight markets and the most efficient use of capacity. -
LNW Route Specification 2017
Delivering a better railway for a better Britain Route Specifications 2017 London North Western London North Western July 2017 Network Rail – Route Specifications: London North Western 02 SRS H.44 Roses Line and Branches (including Preston 85 Route H: Cross-Pennine, Yorkshire & Humber and - Ormskirk and Blackburn - Hellifield North West (North West section) SRS H.45 Chester/Ellesmere Port - Warrington Bank Quay 89 SRS H.05 North Transpennine: Leeds - Guide Bridge 4 SRS H.46 Blackpool South Branch 92 SRS H.10 Manchester Victoria - Mirfield (via Rochdale)/ 8 SRS H.98/H.99 Freight Trunk/Other Freight Routes 95 SRS N.07 Weaver Junction to Liverpool South Parkway 196 Stalybridge Route M: West Midlands and Chilterns SRS N.08 Norton Bridge/Colwich Junction to Cheadle 199 SRS H.17 South Transpennine: Dore - Hazel Grove 12 Hulme Route Map 106 SRS H.22 Manchester Piccadilly - Crewe 16 SRS N.09 Crewe to Kidsgrove 204 M1 and M12 London Marylebone to Birmingham Snow Hill 107 SRS H.23 Manchester Piccadilly - Deansgate 19 SRS N.10 Watford Junction to St Albans Abbey 207 M2, M3 and M4 Aylesbury lines 111 SRS H.24 Deansgate - Liverpool South Parkway 22 SRS N.11 Euston to Watford Junction (DC Lines) 210 M5 Rugby to Birmingham New Street 115 SRS H.25 Liverpool Lime Street - Liverpool South Parkway 25 SRS N.12 Bletchley to Bedford 214 M6 and M7 Stafford and Wolverhampton 119 SRS H.26 North Transpennine: Manchester Piccadilly - 28 SRS N.13 Crewe to Chester 218 M8, M9, M19 and M21 Cross City Souh lines 123 Guide Bridge SRS N.99 Freight lines 221 M10 ad M22 -
Western Route Strategic Plan Version 8.0: Delivery Plan Submission March 2019
Western Route Strategic Plan Version 8.0: Delivery Plan submission March 2019 Western Route Strategic Plan Contents Foreword and summary ........................................................................................................................................................................................................... 3 Route objectives ..................................................................................................................................................................................................................... 10 Safety ..................................................................................................................................................................................................................................... 14 Train performance .................................................................................................................................................................................................................. 19 Locally driven measures ........................................................................................................................................................................................................ 24 Sustainability & asset management capability ....................................................................................................................................................................... 27 Financial performance ...........................................................................................................................................................................................................