A Study of Aircraft Lateral Dynamics & Ground Stability
Total Page:16
File Type:pdf, Size:1020Kb
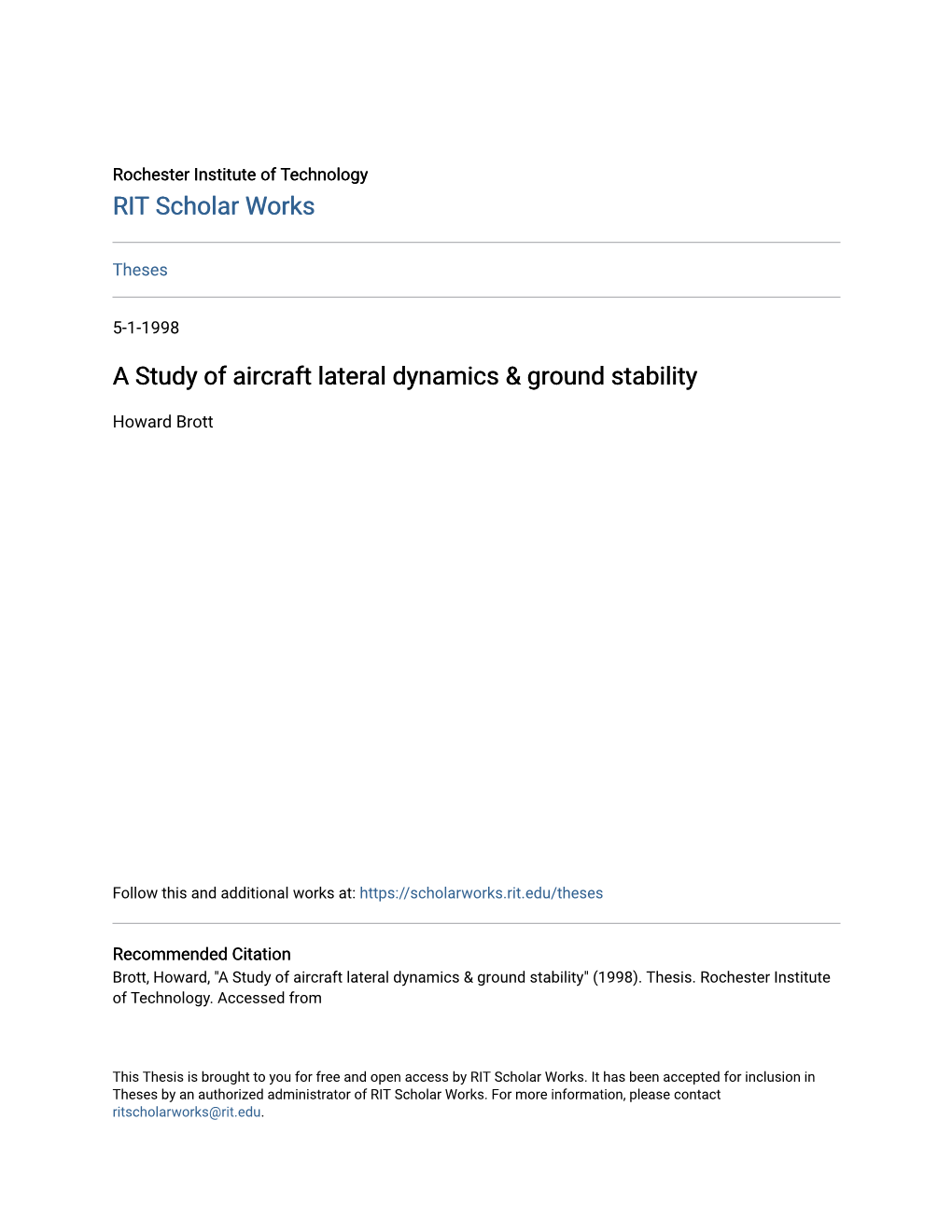
Load more
Recommended publications
-
Hero Or the Zero1
“Hero or the Zero” Chapter 1 A True Story By COL GREGORY MARSTON (ret) Aviation is an exciting profession that has short, intense, high-energy periods that are often followed by fairly routine and even boring phases of flight. Yet, it is important to remember always that you’re flying a machine at relatively high speeds and/or high altitudes versus other man-made equipment like a car. Your happy little pilot bubble can be interrupted in a Nano- second by the rare, heart-stopping, bowel-loosening, emergency that must be dealt with correctly, quickly and coolly or you may die. Sometimes you die, even if you do everything right! This story is about one such moment. I was leading a routine flight of two A-37B “Dragonfly” aircraft on a cool, clear and very dark, early morning at Davis-Monthan Air Force Base (DMAFB) in Tucson, Arizona on January 3rd, 1985. The A-37 was a relic from the Vietnam War, a small, green/grey camouflage, two-seat, two-engine, jet aircraft that was used for Attack (dropping bombs) or Forward Air Control (FAC – shooting rockets). As the solo Instructor Pilot (flying in the left seat) the plan was for me to takeoff first, followed 10 seconds later by my wingman (a student in the left seat and his Instructor Pilot in the right side). After takeoff, my wingman he would rejoin on me for a Close Air Support (CAS) training flight. I would lead the two-aircraft flight out to one of the massive bombing ranges located in southern Arizona. -
Bicycle Landing Gear Is Useful for High-Wing Airplanes with Long Span
Aeronautical Engineering Design I Landing Gear Sizing and Placement Prof. Dr. Serkan Özgen Dept. Aerospace Engineering December 2017 Landing gear configurations 2 Tricycle landing gear 3 Tricycle landing gear • Advantages of tricycle landing gear: ⁻ Cabin floor is horizontal when the airplane is on the ground. ⁻ Forward visibility is improved for the pilot when the airplane is on the gound. ⁻ The CG is ahead of the main wheels and this enhances stability during the ground roll. 4 Tricycle landing gear 5 Tricycle landing gear • The length of the landing gear must be set so that the tail doesn’t hit the ground during landing. • This is measured from the wheel in the static position assuming an angle of attack for landing that gives 90% of maximum lift, usually 10o-15o. • The tipback angle is the maximum aircraft nose-up attitude when the tail is touching the ground and the landing gear strut is fully extended. • To prevent the aircraft from tipping back on its tail, the angle of the vertical from the main wheel position to the cg should be greater than the tipback angle or 15o, whichever is greater. 6 Tricycle landing gear • Tipback angle should not be greater than 25o, otherwise porpoising will occur and a high elevator deflection will be required for rotation during takeoff. • This means that more than 20% of aircraft weight is carried by the nose wheel. • The optimum range for the percentage of aircraft weight that is carried by the nose wheel is 8-15% for the most aft and most forward CG positions. -
Landing Gear.Pdf
Study of Evolution and Details of Landing Gear INDEX CHAPTER 1 1.1.1 INTRODUCTION 3 1.1.2 EVOLUTION 3 CHAPTER 2 2.1 DIFFERENT TYPES OF LANDING GEARS 6 2.1.1 TRICYCLE LANDING GEAR 7 2.1.2 CONVENTIONAL LANDING GEAR 7 2.1.3 UNCONVENTIONAL LANDING GEAR 8 2.2 DIFFERENCE BETWEEN MAIN AND NOSE LANDING GEAR 9 2.3 SHOCK STRUTS 10 2.3.1 TYPES OF SHOCK STRUTS 1. METERING PIN TYPE 10 2. METERING TUBE TYPE 11 3. NOSE GEAR STRUTS 12 4. DOUBLE-ACTING SHOCK ABSORBER 12 2.4 OPERATION OF SHOCK STRUTS 13 CHAPTER 3 3.1 HYDRAULIC SYSTEM FOR AIRCRAFT LANDING GEAR 15 3.2 LANDING GEAR EXTENSION AND RETRACTION 15 3.2.1 LANDING GEAR EXTENSION AND RETRACTING MECHANISMS 15 3.3 EMERGENCY SYSTEMS 16 NIMRA INSTITUTE OF SCIENCE & TECHNOLOGY, A.E - 1 - Study of Evolution and Details of Landing Gear CHAPTER 4 4.1 BRAKING SYSTEM IN LANDING GEAR 18 4.2 DIFFERENT TYPES OF BRAKES AND THEIR EVOLUTION 4.2.1 CARBON AND BERYLLIUM BRAKES 18 4.2.2 AUTO-BRAKE AND BRAKE-BY-WIRE SYSTEM 19 4.3 DESCRIPTION OF A HYDRAULIC BRAKING SYSTEM 20 4.4 ADVANCED BRAKE CONTROL SYSTEM (ABCS) 21 4.5 PNEUMATIC BRAKING 21 4.6 DIFFERENTIAL BRAKING 22 CHAPTER 5 LUBRICANTS USED IN LANDING GEAR 23 CONCLUSION 24 REFERENCES 25 FIGURES FIG. 1 LANDING GEARS IN THE INITIAL STAGES 26 FIG. 2 BASIC TYPES OF LANDING GEARS 26 FIG. 3 TU-144 MAIN LANDING GEAR 27 FIG. 4 TRACK-TYPE GEAR 27 FIG. -
P 6 ^/ Summary Report on the C Preliminary Design Studies of an Advanced General Aviation Aircraft
NASW_443 5 )L P 6 ^/ SUMMARY REPORT ON THE C PRELIMINARY DESIGN STUDIES OF AN ADVANCED GENERAL AVIATION AIRCRAFT PREPARED FOR: NASA USRA ADVANCED DESIGN PROGRAM PREPARED BY: RON BARRETI' SHANE DEMOS S AB DIRKZWAGER I DARRYL EVANS CHARLES GOMER JERRY KEITER DARREN KNIPP iL GLEN SEIER STEVE SMITH ED WENNTNGER THE UNIVERSITY OF KANSAS MAY 1991 TEAM LEADER: CHARLES GOMER FACULTY ADVISOR: JAN ROSKAM NASA ADVISOR: JACK MORRIS (NASA-C-190024) PRELIMINARY DEI',N STUDIES N92-200ô4 OF AN ADVANCED GENERAL AVIATION AIRCRAFT Summary Report (Kansas Univ.) 204 p CSCL OIC Unci as G3/05 0073949 ABSTRACT The purpose of this report is to present the preliminary design results of the advanced aircraft design project at the University of Kansas. The goal of the project is to take a revolutionary look into the design of a general aviation aircraft. This project was conducted as a graduate level design class under the auspices of the KUINASA/USRA Advanced Design Program in Aeronautics. The class is open to aerospace and electrical engineering seniors and first level graduate students. Phase I of the design procedure (fall semester 1990) included the preliminary design of two configurations, a pusher and a tractor. The references listed in Section 1.1 of this report document this preliminary airframe design as well as other (more detailed) design studies, such as a pilot workload study, an advanced guidance and display study, a market survey, structural layout and manufacturing, and others. Phase II (spring semester 1991) included the selection of only one configuration for further study. The pusher configuration was selected on the basis of performance characteristics, cabin noise considerations, natural laminar flow considerations, and system layouts. -
Project Hegaasus
PROJECT HEGAASUS Loughborough University, UK Virginia Tech, USA Powertrain Department Structures Department Aircraft Systems Department Aircraft Performance Department Business and Sales Department Modelling Department HYBRID ELECTRIC GENERAL AVIATION AIRCRAFT 2018 AIAA UNDERGRADUATE DESIGN COMPETITION Hybrid Electric General Aviation Aircraft Proposal HAMSTERWORKS DESIGN TEAM Sammi Rocker (USA) Daniel Guerrero (UK) Kyle Silva (USA) Design and Modelling Aircraft Integration Landing Gear & Certification AIAA – 543803 AIAA – 921916 AIAA –921097 Ashley Peyton-Bruhl (UK) Danny Fritsch (USA) Nathaniel Marsh (UK) Business & Sales Flight Physics Propulsion Design AIAA – 921913 AIAA-921435 AIAA-921919 Troy Bergin (USA) Jennifer Glover (UK) Alexander Mclean (USA) Structural Design Powertrain Design Stability & Performance AIAA – 736794 AIAA - 921554 AIAA - 921291 Dhirun Mistry (UK) Pradeep Raj, Ph.D. (USA) James Knowles, Ph.D. (UK) Avionic Systems Virginia Tech Advisor Loughborough University Advisor AIAA – 921917 i Hybrid Electric General Aviation Aircraft Proposal CONTENTS HAMSTERWORKS DESIGN TEAM ................................................................................................................ I LIST OF FIGURES .............................................................................................................................................V LIST OF TABLES ........................................................................................................................................... VII LIST OF ABBREVIATIONS -
Federal Register / Vol. 60, No. 155 / Friday, August 11, 1995 / Proposed Rules
41160 Federal Register / Vol. 60, No. 155 / Friday, August 11, 1995 / Proposed Rules DEPARTMENT OF TRANSPORTATION The comments should identify the foster and promote general aviation while regulatory docket or notice number and continuing to improve its safety record. Federal Aviation Administration should be submitted in triplicate to the These goals are neither contradictory nor Rules Docket address specified above. separable. They are best achieved by 14 CFR Parts 1, 61, 141, and 143 cooperating with the aviation community to All comments received on or before the define mutual concerns and joint efforts to [Docket No. 25910; Notice No. 95±11] closing date for comments will be accomplish objectives. We will strive to considered by the Administrator before achieve the goals through voluntary RIN: 2120±AE71 action is taken on the proposed compliance and methods designed to reduce amendments, and the proposals the regulatory burden on general aviation. Pilot, Flight Instructor, Ground contained in this notice may be changed The FAA's general aviation programs Instructor, and Pilot School in light of comments received. All will focus on: Certification Rules comments received as well as a report 1. SafetyÐTo protect recent gains and AGENCY: Federal Aviation summarizing any substantive public aim for a new threshold. Administration (FAA), DOT. contact with FAA personnel on this 2. FAA ServicesÐTo provide the rulemaking will be filed in the docket. general aviation community with ACTION: Notice of proposed rulemaking The docket is available for public responsive, customer-driven (NPRM). inspection before and after the closing certification, air traffic, and other SUMMARY: This action proposes to revise date for submitting comments. -
Chapter 6 Fuselage and Tail Sizing - 8 Lecture 30 Topics
Airplane design(Aerodynamic) Prof. E.G. Tulapurkara Chapter-6 Chapter 6 Fuselage and tail sizing - 8 Lecture 30 Topics 6.5 Fuel system 6.6 Landing gear 6.6.1 Tricycle type or nosewheel landing gear 6.6.2 Retractable and non-retractable landing gear 6.6.3 Tail wheel type landing gear 6.6.4 Bicycle type landing gear 6.7 Subsystems Example 6.3 6.5 Fuel system The fuel system includes fuel tanks, fuel pumps, fuel lines, vents and fuel flow controls. The fuel tanks are of three types.They are : (a) Discrete (b) bladder and (c) integral. Discrete tanks are fuel containers fabricated separately and fixed inside the airplane. These are used for general aviation aircraft and home built airplanes. Bladder tanks consist of rubber bags inserted into the space available for storage of fuel. They are also self sealing – if a bullet pierces the tank; the rubber fills in the hole and prevents large loss of fuel and fire hazard. Integral tanks are cavities within the wing/fuselage which are sealed to form a fuel tank. Note : To calculate the space required for fuel, the following guidelines are followed. (Ref.1.18, chapter 10) the weight of the fuel required is known from the consideration of the range. The volume of the fuel can be calculated knowing it’s relative density which varies between 0.77 to 0.82; a value of 0.8 can be taken for the first estimate. Decide the type of fuel tank, to arrive at the space for fuel in Dept. -
Aviation Pioneer, Fred E. Weick
Virginia Aviation History Project By: Norm Crabill Published with permission of Mr. Donald V. Weick, March 14, 2019 Aviation Pioneer, Fred E. Weick This article is based on Norman Crabill’s notes from Fred Weick’s autobiography “From the Ground Up”, with contributions from Raymond Gill, Vice President, VAHS. Mr. Crabill’s notes were shared with Ray Gill and Hall of Fame member (1998) Ray Tyson at a recent meeting in the Robin’s Nest Café on Fredericksburg’s Shannon Airport campus. Norm Crabill is a Life Member of the Virginia Aeronautical Historical Society and a member of the VAHS Hall of Fame (2008). He generously agreed to allow us to share his notes with our membership. Fred Weick came to the National Advisory Committee for Aeronautics (NACA) in the 1920s and contributed to significant changes in aircraft design worldwide, including: 1. Improvement in propeller design. One report for the US Naval Bureau of Aeronautics (1925) and two reports for NACA, TN212 (January 1925) and TN225 (September 1925). 2. Development of a propeller testing facility at NACA Langley in 1923. 3. Development of the NACA cowling for engines. In 1929, the first Collier Trophy was awarded for development of the cowling in the Propeller Research Tunnel. The NACA cowling drastically reduced aircraft drag, improved cylinder cooling and is being used world-wide today. Responding to a growing interest for an easy-to-fly airplane, Fred put together a team of six NACA engineers to design and build a single engine, easy-to-fly, aircraft that would not stall nor spin; that would also be easy to land due to its steering wheel at the nose and remaining two wheels behind the center of gravity. -
Sp4409-Vol2-2.Pdf
308 Chapter 3: The Design Revolution Document 3-15(a-e) 309 INTO THE NacELLE The problem becomes easiest when there are outboard engine nacelles, for the nacelle usually provides ample space for housing the gear and gives the proper tread with the wheels located under the concenetrated loads On a high wing monoplane design with engines in the leading edge, the landing gear must be very high Because of the great height it is almost impossible to take the side loads as a cantilever, and therefore the design must be complicated by side struts to the fuselage as on the General YO-27 (see illustration) where they remain out in the air-stream when the wheel is retracted In the new Dutch built Fokker F-XX a compromise apparently has been reached by retaining the high wing and lowering the engine nacelles below the wing so that a completely retractable gear can be obtained with no side struts to the fuselage, the nacelles carrying all the load Fokker seems to have decided that the slightly increased drag of the lowered nacelles did not offset the advantages of the high wing, with its inherently less drag and greater lift as well as its absence of buffeting and better passenger vision (see page 59 and references 3, 4 and 5) How- ever, some designers have reached a compromise in another fashion, locating the nacelle in the best position with reference to the landing gear and then lowering the wing to have the engine in the leading edge Examples of this are the new Martin bomber, the Boeing bomber and the new Boeing transport, and the new Douglas -
Landing Gear, Numerical Model, FEM, Static and Dynamic Analysis
INTERNATIONAL DESIGN CONFERENCE - DESIGN 2002 Dubrovnik, May 14 - 17, 2002. SELECTION OF DYNAMICS CHARAKTERISTICS FOR LANDING GEAR WITH THE USE OF NUMERICAL MODEL T. Niezgoda , J. Malachowski and W. Kowalski Keywords: Landing gear, numerical model, FEM, static and dynamic analysis 1. Introduction Despite the amazing development of computer capabilities in recent years, it is still very difficult and expensive to create a model off overall aircraft structure. Usually less precise global model is used for preliminary analysis. More detailed analysis is conducted for extreme loaded units. Such a unit is landing gear. The primary purpose of the landing gear units is to absorb the impact energy of the aircraft when it lands and taxes. Landing is the most dangerous phase of aircraft flight. Therefore landing gear design comprises very difficult and responsible unit of overall project. This unit has to sustain appropriate strength to guarantee safety and fatigue life that assures the number of takeoff- lands prescribed in the technical specification. Each type of aircraft needs a unique landing gear with a specific structural system, which can complete demands described by unique characteristics associated with each aircraft, i.e., geometry, weight, and mission requirements. They determine the design and positioning of the landing gear. In the paper considerations are made for a tricycle landing gear, which belongs to a small transport aircraft with maximum take-off weight of 7000kg and landing weight of 6500kg. This aircraft is able to land on a grassy runway. In general the landing gear can be divided according to four categories: load character, positioning of shock absorber and fork, attachment of wheel to fork character, positioning of wheel and fork. -
Light Sport Aircraft Control Systems, Folding Wings, and Landing Gear
1 Light Sport Aircraft Control Systems, Folding Wings, and Landing Gear Senior Project Final Design Report May 2008 David Brown __________________________ Brian Dahl_____________________________ Dustin Jefferies_________________________ 2 Abstract The airplanes currently used for medical mission work are typically expensive, require long runways and large storage areas. This project is an attempt to provide a new product for this purpose that will reduce the capital demands of such an airplane. The goal of this project is to design and build the landing gear, brakes, wing folding mechanism, and control system for a Light Sport Aircraft. The priorities in designing are low cost, durability, simplicity, and ease of use. 3 TABLE OF CONTENTS ABSTRACT .................................................................................................................................................. 2 Acknowledgements................................................................................................................................4 1 INTRODUCTION ..................................................................................................................................... 5 1.1 DESCRIPTION ........................................................................................................................................ 5 1.2 LITERATURE REVIEW............................................................................................................................ 5 1.3 SOLUTION ............................................................................................................................................ -
Basic Aircraft Construction
CHAPTER 4 AIRCRAFT BASIC CONSTRUCTION INTRODUCTION useless. All materials used to construct an aircraft must be reliable. Reliability minimizes the possibility of Naval aircraft are built to meet certain specified dangerous and unexpected failures. requirements. These requirements must be selected so they can be built into one aircraft. It is not possible for Many forces and structural stresses act on an one aircraft to possess all characteristics; just as it isn't aircraft when it is flying and when it is static. When it is possible for an aircraft to have the comfort of a static, the force of gravity produces weight, which is passenger transport and the maneuverability of a supported by the landing gear. The landing gear absorbs fighter. The type and class of the aircraft determine how the forces imposed on the aircraft by takeoffs and strong it must be built. A Navy fighter must be fast, landings. maneuverable, and equipped for attack and defense. To During flight, any maneuver that causes meet these requirements, the aircraft is highly powered acceleration or deceleration increases the forces and and has a very strong structure. stresses on the wings and fuselage. The airframe of a fixed-wing aircraft consists of the Stresses on the wings, fuselage, and landing gear of following five major units: aircraft are tension, compression, shear, bending, and 1. Fuselage torsion. These stresses are absorbed by each component of the wing structure and transmitted to the fuselage 2. Wings structure. The empennage (tail section) absorbs the 3. Stabilizers same stresses and transmits them to the fuselage.