Pilot's Operating Handbook; ICON A5; ICA012347 Issue A3
Total Page:16
File Type:pdf, Size:1020Kb
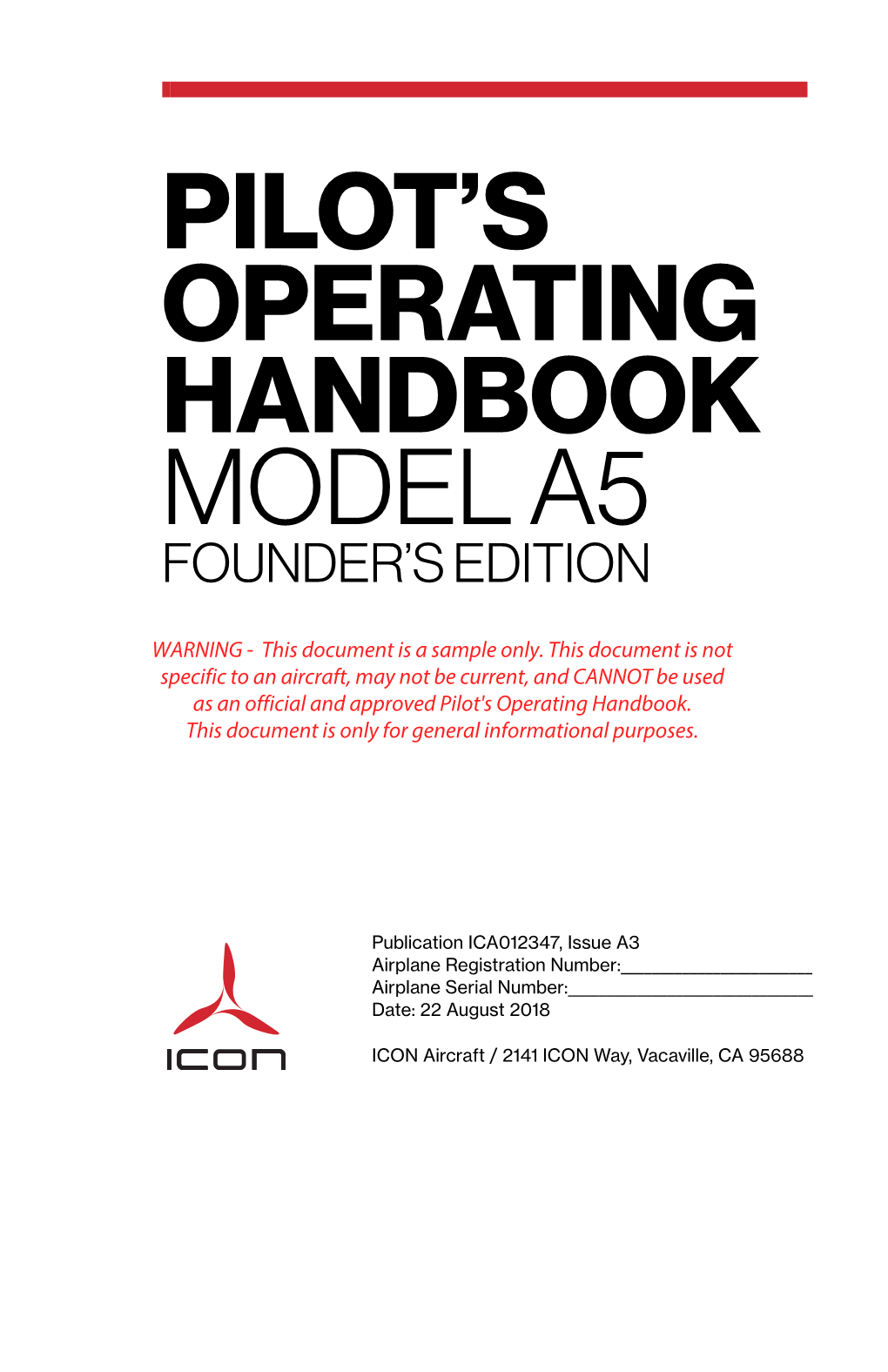
Load more
Recommended publications
-
Wing Root & Landing Gear Door Seal Replacement
Wing Root & Landing Gear Door Seal Replacement One of the oldest original components remaining on my Baron (and likely other members planes) was surely the stiff and ragged wing root seal. In researching this component I learned that the wing root and tail seals were installed on the wings and tails before the marriage to the airframe. What lies below the top skin of the wing and tail is a length of rubber “finger” (Figure 1) as an integral part of the seal. Figure 1 This “finger” holds the seal in place and was likely glued at the factory, grabbing the backside of the wing and tail skin. With time and age these original rubber seals have taken quite a beating. With an extended winter annual downtime this year I chose to tackle this really tedious project while waiting for other components that were out for overhaul. A word of caution, this is as tedious as it gets if you choose to dig out the finger from below the top surface skins using the very narrow gap between the skin and the fuselage. Here is a pirep from a Bonanza A36 owner on how he tackled his seal replacement: “I cut the majority of the old seal off using razor blade, leaving a small lip sticking above the wing. I then used a small pick bent at a 90 degree angle, with about a 3/8" 'hook' on the end. Using the hook, I stuck it under the wing skin, between the skin and the old rubber wing seal lip under the skin, and forced it along the chord of the wing. -
Design of Seaplanes
APPENDIX C3: Design of Seaplanes This appendix is a part of the book General Aviation Aircraft Design: Applied Methods and Procedures by Snorri Gudmundsson, published by Elsevier, Inc. The book is available through various bookstores and online retailers, such as www.elsevier.com, www.amazon.com, and many others. The purpose of the appendices denoted by C1 through C5 is to provide additional information on the design of selected aircraft configurations, beyond what is possible in the main part of Chapter 4, Aircraft Conceptual Layout. Some of the information is intended for the novice engineer, but other is advanced and well beyond what is possible to present in undergraduate design classes. This way, the appendices can serve as a refresher material for the experienced aircraft designer, while introducing new material to the student. Additionally, many helpful design philosophies are presented in the text. Since this appendix is offered online rather than in the actual book, it is possible to revise it regularly and both add to the information and new types of aircraft. The following appendices are offered: C1 – Design of Conventional Aircraft C2 – Design of Canard Aircraft C3 – Design of Seaplanes (this appendix) C4 – Design of Sailplanes C5 – Design of Unusual Configurations Figure C3-1: A Lake LA-250 Renegade, shown here during climb after T-O, is a popular option for amphibious aircraft. The large deflected flap on the horizontal tail is a hydraulically actuated trim tab used for slow speed operations only. It trims out the thrust effect of the highly mounted piston-propeller, improving its handling. -
Automated Generic Parameterized Design of Aircraft Fairing and Windshield
Automated generic parameterized design of aircraft fairing and windshield Vijaykumar Govindharajan Aakash Narender Singh LIU-IEI-TEK-A-12/01271-SE Department of Management and Engineering Division of Flumes Department of Management and Engineering SE-581 83 Linköping, Sweden i ii Upphovsrätt Detta dokument hålls tillgängligt på Internet – eller dess framtida ersättare – under 25 år från publiceringsdatum under förutsättning att inga extraordinära omständigheter uppstår. Tillgång till dokumentet innebär tillstånd för var och en att läsa, ladda ner, skriva ut enstaka kopior för enskilt bruk och att använda det oförändrat för ickekommersiell forskning och för undervisning. Överföring av upphovsrätten vid en senare tidpunkt kan inte upphäva detta tillstånd. All annan användning av dokumentet kräver upphovsmannens medgivande. För att garantera äktheten, säkerheten och tillgängligheten finns lösningar av teknisk och administrativ art. Upphovsmannens ideella rätt innefattar rätt att bli nämnd som upphovsman i den omfattning som god sed kräver vid användning av dokumentet på ovan beskrivna sätt samt skydd mot att dokumentet ändras eller presenteras i sådan form eller i sådant sammanhang som är kränkande för upphovsmannens litterära eller konstnärliga anseende eller egenart. För ytterligare information om Linköping University Electronic Press se förlagets hemsida http://www.ep.liu.se/. Copyright The publishers will keep this document online on the Internet – or its possible replacement – for a period of 25 years starting from the date of publication barring exceptional circumstances. The online availability of the document implies permanent permission for anyone to read, to download, or to print out single copies for his/her own use and to use it unchanged for non-commercial research and educational purpose. -
Crossmedia Adaptation and the Development of Continuity in the Dc Animated Universe
“INFINITE EARTHS”: CROSSMEDIA ADAPTATION AND THE DEVELOPMENT OF CONTINUITY IN THE DC ANIMATED UNIVERSE Alex Nader A Thesis Submitted to the Graduate College of Bowling Green State University in partial fulfillment of the requirements for the degree of MASTER OF ARTS May 2015 Committee: Jeff Brown, Advisor Becca Cragin © 2015 Alexander Nader All Rights Reserved iii ABSTRACT Jeff Brown, Advisor This thesis examines the process of adapting comic book properties into other visual media. I focus on the DC Animated Universe, the popular adaptation of DC Comics characters and concepts into all-ages programming. This adapted universe started with Batman: The Animated Series and comprised several shows on multiple networks, all of which fit into a shared universe based on their comic book counterparts. The adaptation of these properties is heavily reliant to intertextuality across DC Comics media. The shared universe developed within the television medium acted as an early example of comic book media adapting the idea of shared universes, a process that has been replicated with extreme financial success by DC and Marvel (in various stages of fruition). I address the process of adapting DC Comics properties in television, dividing it into “strict” or “loose” adaptations, as well as derivative adaptations that add new material to the comic book canon. This process was initially slow, exploding after the first series (Batman: The Animated Series) changed networks and Saturday morning cartoons flourished, allowing for more opportunities for producers to create content. References, crossover episodes, and the later series Justice League Unlimited allowed producers to utilize this shared universe to develop otherwise impossible adaptations that often became lasting additions to DC Comics publishing. -
Effects of Gurney Flap on Supercritical and Natural Laminar Flow Transonic Aerofoil Performance
Effects of Gurney Flap on Supercritical and Natural Laminar Flow Transonic Aerofoil Performance Ho Chun Raybin Yu March 2015 MPhil Thesis Department of Mechanical Engineering The University of Sheffield Project Supervisor: Prof N. Qin Thesis submitted to the University of Sheffield in partial fulfilment of the requirements for the degree of Master of Philosophy Abstract The aerodynamic effect of a novel combination of a Gurney flap and shockbump on RAE2822 supercritical aerofoil and RAE5243 Natural Laminar Flow (NLF) aerofoil is investigated by solving the two-dimensional steady Reynolds-averaged Navier-Stokes (RANS) equation. The shockbump geometry is predetermined and pre-optimised on a specific designed condition. This study investigated Gurney flap height range from 0.1% to 0.7% aerofoil chord length. The drag benefits of camber modification against a retrofit Gurney flap was also investigated. The results indicate that a Gurney flap has the ability to move shock downstream on both types of aerofoil. A significant lift-to-drag improvement is shown on the RAE2822, however, no improvement is illustrated on the RAE5243 NLF. The results suggest that a Gurney flap may lead to drag reduction in high lift regions, thus, increasing the lift-to-drag ratio before stall. Page 2 Dedication I dedicate this thesis to my beloved grandmother Sandy Yip who passed away during the course of my research, thank you so much for the support, I love you grandma. This difficult journey would not have completed without the deep understanding, support, motivation, encouragement and unconditional love from my beloved parents Maggie and James and my brother Billy. -
Icons of Survival: Metahumanism As Planetary Defense." Nerd Ecology: Defending the Earth with Unpopular Culture
Lioi, Anthony. "Icons of Survival: Metahumanism as Planetary Defense." Nerd Ecology: Defending the Earth with Unpopular Culture. London: Bloomsbury Academic, 2016. 169–196. Environmental Cultures. Bloomsbury Collections. Web. 25 Sep. 2021. <http:// dx.doi.org/10.5040/9781474219730.ch-007>. Downloaded from Bloomsbury Collections, www.bloomsburycollections.com, 25 September 2021, 20:32 UTC. Copyright © Anthony Lioi 2016. You may share this work for non-commercial purposes only, provided you give attribution to the copyright holder and the publisher, and provide a link to the Creative Commons licence. 6 Icons of Survival: Metahumanism as Planetary Defense In which I argue that superhero comics, the most maligned of nerd genres, theorize the transformation of ethics and politics necessary to the project of planetary defense. The figure of the “metahuman,” the human with superpowers and purpose, embodies the transfigured nerd whose defects—intellect, swarm-behavior, abnormality, flux, and love of machines—become virtues of survival in the twenty-first century. The conflict among capitalism, fascism, and communism, which drove the Cold War and its immediate aftermath, also drove the Golden and Silver Ages of Comics. In the era of planetary emergency, these forces reconfigure themselves as different versions of world-destruction. The metahuman also signifies going “beyond” these economic and political systems into orders that preserve democracy without destroying the biosphere. Therefore, the styles of metahuman figuration represent an appeal to tradition and a technique of transformation. I call these strategies the iconic style and metamorphic style. The iconic style, more typical of DC Comics, makes the hero an icon of virtue, and metahuman powers manifest as visible signs: the “S” of Superman, the tiara and golden lasso of Wonder Woman. -
SBM20-322 2015 June 23 Temporary
MOONEY INTERNATIONAL CORPORATION SERVICE BULLETIN 165 Al Mooney Road North Kerrville, Texas 78028 SERVICE BULLETIN M20-322 Date: June 23, 2015 THIS BULLETIN IS FAA APPROVED FOR ENGINEERING DESIGN SUBJECT: Temporary Replacement of Icing System Stall Strip MODELS/ SN Mooney Aircraft with Known Icing System Installed AFFECTED: TIME OF AS SOON AS PRACTICABLE COMPLIANCE: INTRODUCTION: For instances involving missing icing system stall strips, airplanes are grounded. To remedy this situation, a temporary non-icing system stall strip can be installed in place of the icing stall strip to allow the aircraft to operate as a “Not Certified for Flight in Known Icing Conditions” aircraft until the icing strip can be installed. This Service Bulletin is to provide instructions for installing the temporary stall strip. The attached compliance card needs to be filled out and returned to Mooney International Corporation upon completion of this Service Bulletin M20-322. WARNING: Flight into known icing conditions and the use of the aircraft’s icing system is prohibited until the permanent icing system stall strip can be installed. This Service Bulletin only allows for a temporary non-icing stall strip to be installed for temporary flight until the permanent icing stall strip can be obtained. INSTRUCTIONS: Read entire procedures before beginning work. INSTALLING TEMPORARY STALL STRIP: 1.1. Disable and secure circuit breaker to prevent accidental operation of icing system. 1.2. Remove all old sealant and thoroughly clean the porous surface of the wing where the temporary stall strip is to be installed. Acceptable cleaning solvents are listed below. NOTE: The primary factor affecting the adhesion of the stall strip is absolute cleanliness of the porous panel. -
Superman: What Makes Him So Iconic?
SUPERMAN: WHAT MAKES HIM SO ICONIC? Superman: What makes him so Iconic? Myriam Demers-Olivier George Brown College © 2009, Myriam Demers-Olivier SUPERMAN: WHAT MAKES HIM SO ICONIC? Introduction “Faster than a speeding bullet, more powerful than a locomotive, able to leap tall buildings in a single bound. Look! Up in the sky! It’s a bird, it’s a plane, it’s Superman! “ (Daniels, 1998, p. 1-7). Some people might not recognize the reference to early radio shows and cartoons, but most people will recognize the name Superman. Superman has become such an amazing cultural icon, that almost everyone knows his name, and often his weakness, his powers, the colors of his suit and the name of his arch nemesis. It’s part of common knowledge and everyone has been exposed to him at some time or another. Since the creation of Superman in 1938, comic book research and literary studies have come along way. These allows us to more deeply analyze and understand, as well as unravel the deeper signified meanings associated with the iconic Superman (Wandtke, 2007, p. 25). He is seen as a superhero, but also upholds “truth, justice and the American way” (Watt-Evans, 2006, p. 1). Some see him as Christ-like or Jewish, and even as a fascist. He fulfills some of our needs from the Maslow’s hierarchy of needs, and also expresses different messages depending on the medium in which he is portrayed. There is no end to the Superman merchandise, but Superman as an icon, can change a person. -
FAA Advisory Circular 20-97B
Subject: AIRCRAFT TIRE MAINTENANCE Date: 4/18/05 AC No.: 20-97B AND OPERATIONAL PRACTICES Initiated by: AFS-306 Change: 1. PURPOSE. This advisory circular (AC) provides recommended tire care and maintenance practices needed to assure the safety of support personnel and the continued airworthiness of aircraft. Specifically, this AC provides guidance on the installation, inflation, maintenance, and removal of aircraft tires. In addition, this AC provides guidance on those operational practices necessary to maintain safe aircraft operations. This AC is not mandatory and does not constitute a regulation. It is issued for guidance purposes and to outline acceptable tire maintenance and operational practices. In lieu of following this method without deviation, operators may elect to follow an alternative method that has also been found acceptable by the Federal Aviation Administration (FAA). 2. CANCELLATION. AC 20-97A, High-Speed Tire Maintenance and Operational Practices, dated May 13, 1987, is cancelled. 3. RELATED REGULATIONS AND DOCUMENTS. a. Title 14 of the Code of Federal Regulations (14 CFR): (1) Part 21, subpart O, Technical Standard Order Authorizations. (2) Part 23, Airworthiness Standards: Normal, Utility, Acrobatic, and Commuter Category Airplanes. (3) Part 25, Airworthiness Standards: Transport Category Airplanes. (4) Part 27, Airworthiness Standards: Normal Category Rotorcraft. (5) Part 29, Airworthiness Standards: Transport Category Rotorcraft. (6) Part 43, Maintenance, Preventive Maintenance, Rebuilding, and Alteration. (7) Part 145, Repair Stations. b. FAA ACs. Copies of the following ACs may be obtained from the U.S. Department of Transportation, Subsequent Distribution Center, Ardmore East Business Center, 3341 Q 75th Avenue, Landover, MD 20785, and may be downloaded at the following Web site: http://www.faa.gov/avr/afs/acs/ac-idx.htm. -
Comparison of Aircraft Tire Wear with Initial Wheel Rotational Speed
International Journal of Aviation, Aeronautics, and Aerospace Volume 2 Issue 1 Article 2 3-2-2015 Comparison of Aircraft Tire Wear with Initial Wheel Rotational Speed Abdurrhman A. Alroqi University of Sussex, [email protected] Weiji Wang University of Sussex, [email protected] Follow this and additional works at: https://commons.erau.edu/ijaaa Part of the Aeronautical Vehicles Commons Scholarly Commons Citation Alroqi, A. A., & Wang, W. (2015). Comparison of Aircraft Tire Wear with Initial Wheel Rotational Speed. International Journal of Aviation, Aeronautics, and Aerospace, 2(1). https://doi.org/10.15394/ ijaaa.2015.1043 This Article is brought to you for free and open access by the Journals at Scholarly Commons. It has been accepted for inclusion in International Journal of Aviation, Aeronautics, and Aerospace by an authorized administrator of Scholarly Commons. For more information, please contact [email protected]. Comparison of Aircraft Tire Wear with Initial Wheel Rotational Speed Cover Page Footnote The authors would like to acknowledge University of Sussex for its support with the literature and related resources. This article is available in International Journal of Aviation, Aeronautics, and Aerospace: https://commons.erau.edu/ ijaaa/vol2/iss1/2 Alroqi and Wang: Comparison of Aircraft Tire Wear with Initial Wheel Rotational Speed In this paper, the landing impact of an aircraft is described using a physical model of a single wheel in the main landing gear. The purpose of this study is to understand potential tire-life improvements that could be made by reducing abrasive skidding between aircraft tires and runway surfaces immediately after touchdown. -
Amphibious Lsa
HANDS ON | TRAINING IN THE ICON A5 AMPHIBIOUS LSA. HANDS ON Training in the Icon A5 Amphibious LSA Does the pilot training program match Icon Aircraft’s ambitious goals? AIN travels to Vacaville to find the answer. by Matt Thurber them so far, in Vacaville and Tampa, Fla., with a The Icon A5 light-sport amphibious airplane prom- third slated to open in Texas this year, likely in the ises adventure, and that is indeed what this unique Austin area). The IFCs train new Icon pilots and light-sport airplane (LSA) delivers. AIN was invited those who are adding a seaplane rating to their tickets, and they offer multiple ways to experience to experience full immersion in the A5 world, and the A5, from a demo flight to ab initio LSA train- www.ainonline.com I recently spent four days at Icon Aircraft’s head- ing for new pilots and LSA seaplane transition quarters in Vacaville, Calif., learning how to fly the courses for existing floatplane pilots or pilots with A5 and earning my LSA seaplane rating. no water experience. Having never flown a float- For Icon Aircraft, which markets the A5 as plane or amphibian, I went through the course the ultimate fun device for the adventure sports for those with no water experience. fanatic, a significant challenge is balancing that Until production ramps up later this year, the sporty attitude with helping buyers, especially IFCs are the place where buyers can experience those new to flying, develop a strong dedication what it’s like to fly the airplane they want to own. -
Propulsion and Flight Controls Integration for the Blended Wing Body Aircraft
Cranfield University Naveed ur Rahman Propulsion and Flight Controls Integration for the Blended Wing Body Aircraft School of Engineering PhD Thesis Cranfield University Department of Aerospace Sciences School of Engineering PhD Thesis Academic Year 2008-09 Naveed ur Rahman Propulsion and Flight Controls Integration for the Blended Wing Body Aircraft Supervisor: Dr James F. Whidborne May 2009 c Cranfield University 2009. All rights reserved. No part of this publication may be reproduced without the written permission of the copyright owner. Abstract The Blended Wing Body (BWB) aircraft offers a number of aerodynamic perfor- mance advantages when compared with conventional configurations. However, while operating at low airspeeds with nominal static margins, the controls on the BWB aircraft begin to saturate and the dynamic performance gets sluggish. Augmenta- tion of aerodynamic controls with the propulsion system is therefore considered in this research. Two aspects were of interest, namely thrust vectoring (TVC) and flap blowing. An aerodynamic model for the BWB aircraft with blown flap effects was formulated using empirical and vortex lattice methods and then integrated with a three spool Trent 500 turbofan engine model. The objectives were to estimate the effect of vectored thrust and engine bleed on its performance and to ascertain the corresponding gains in aerodynamic control effectiveness. To enhance control effectiveness, both internally and external blown flaps were sim- ulated. For a full span internally blown flap (IBF) arrangement using IPC flow, the amount of bleed mass flow and consequently the achievable blowing coefficients are limited. For IBF, the pitch control effectiveness was shown to increase by 18% at low airspeeds.