Modeling and Simulation of Tricycle Landing Gear at Normal and Abnormal Conditions
Total Page:16
File Type:pdf, Size:1020Kb
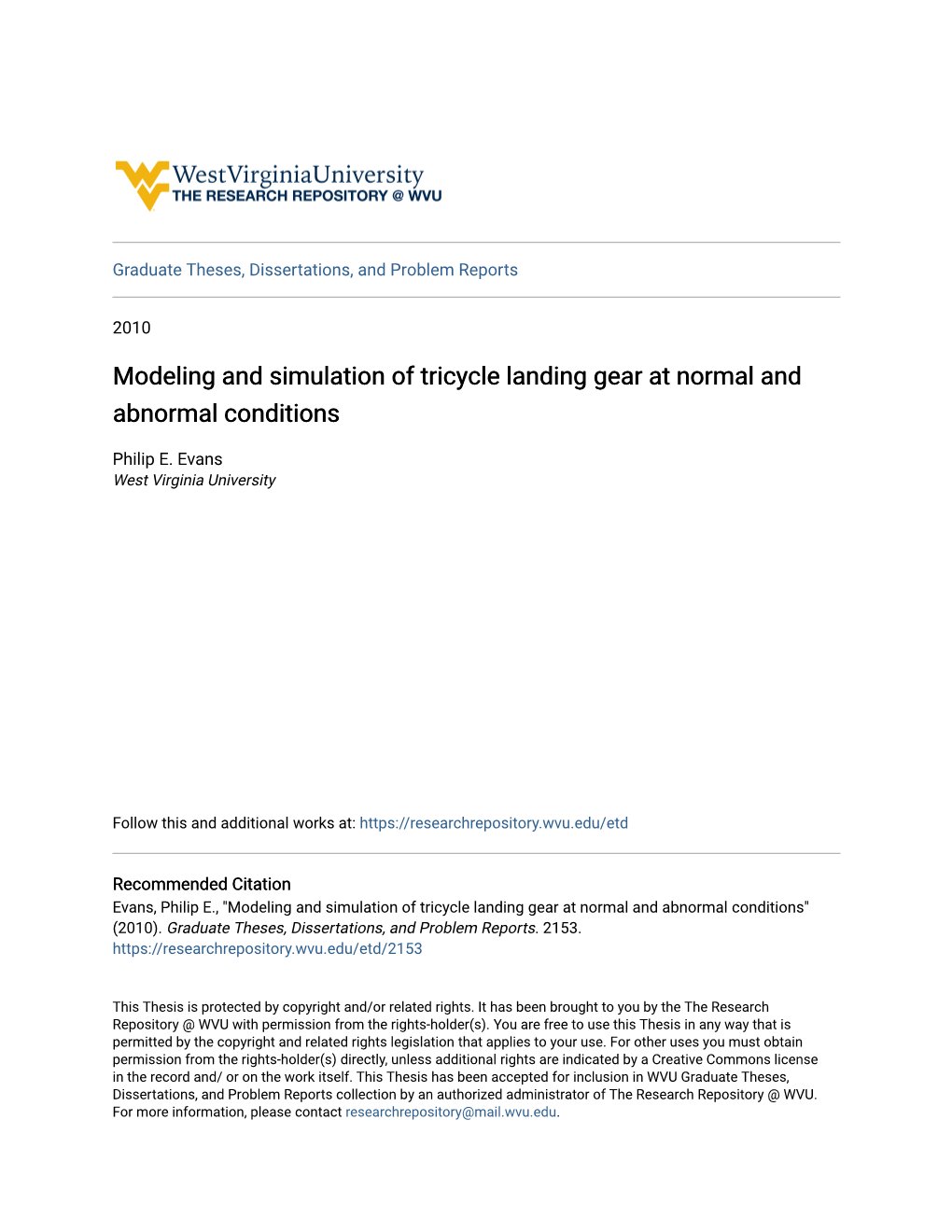
Load more
Recommended publications
-
EWIS Practices Job Aid 2.0
Aircraft EWIS Practices Job Aid 2.0 Federal Aviation Administration Aircraft Electrical Wiring Interconnect System (EWIS) Best Practices Job Aid Revision: 2.0 This job aid covers applicable 14 CFR part 25 aircraft (although it is also widely acceptable for use with other types of aircraft such as military, small airplanes, and rotorcraft). This job aid addresses policy; industry EWIS practices; primary factors associated with EWIS degradation; information on TC/STC data package requirements; EWIS selection and protection; routing, splicing and termination practices; and EWIS maintenance concepts (including how to perform a EWIS general visual inspection). The job aid also includes numerous actual aircraft EWIS photos and examples. UNCONTROLLED COPY WHEN DOWNLOADED 1 Aircraft EWIS Practices Job Aid 2.0 Additional Notes • This presentation contains additional speaker notes for most slides • It’s advisable to read these notes while viewing the slide presentation Aircraft EWIS Best Practices Job Aid 2.0 Federal Aviation 2 Administration UNCONTROLLED COPY WHEN DOWNLOADED 2 Aircraft EWIS Practices Job Aid 2.0 Printing the Additional Notes To print the slides and accompanying speaker notes: – Navigate back to the FAA Aircraft Certification job aids web page – Open and print Printable Slides and Notes Aircraft EWIS Best Practices Job Aid 2.0 Federal Aviation 3 Administration UNCONTROLLED COPY WHEN DOWNLOADED 3 Aircraft EWIS Practices Job Aid 2.0 Background • Why the need for EWIS best practices Job Aid? – Accident/Incident Service History – Aging Transport Systems Rulemaking Advisory Committee (ATSRAC) – Enhanced Airworthiness Program for Airplane System (EAPAS) – EAPAS Rule Making Aircraft EWIS Best Practices Job Aid 2.0 Federal Aviation 4 Administration Historically, wiring and associated components were installed without much thought given to the aging aspects: • Fit and forget. -
Hero Or the Zero1
“Hero or the Zero” Chapter 1 A True Story By COL GREGORY MARSTON (ret) Aviation is an exciting profession that has short, intense, high-energy periods that are often followed by fairly routine and even boring phases of flight. Yet, it is important to remember always that you’re flying a machine at relatively high speeds and/or high altitudes versus other man-made equipment like a car. Your happy little pilot bubble can be interrupted in a Nano- second by the rare, heart-stopping, bowel-loosening, emergency that must be dealt with correctly, quickly and coolly or you may die. Sometimes you die, even if you do everything right! This story is about one such moment. I was leading a routine flight of two A-37B “Dragonfly” aircraft on a cool, clear and very dark, early morning at Davis-Monthan Air Force Base (DMAFB) in Tucson, Arizona on January 3rd, 1985. The A-37 was a relic from the Vietnam War, a small, green/grey camouflage, two-seat, two-engine, jet aircraft that was used for Attack (dropping bombs) or Forward Air Control (FAC – shooting rockets). As the solo Instructor Pilot (flying in the left seat) the plan was for me to takeoff first, followed 10 seconds later by my wingman (a student in the left seat and his Instructor Pilot in the right side). After takeoff, my wingman he would rejoin on me for a Close Air Support (CAS) training flight. I would lead the two-aircraft flight out to one of the massive bombing ranges located in southern Arizona. -
Bicycle Landing Gear Is Useful for High-Wing Airplanes with Long Span
Aeronautical Engineering Design I Landing Gear Sizing and Placement Prof. Dr. Serkan Özgen Dept. Aerospace Engineering December 2017 Landing gear configurations 2 Tricycle landing gear 3 Tricycle landing gear • Advantages of tricycle landing gear: ⁻ Cabin floor is horizontal when the airplane is on the ground. ⁻ Forward visibility is improved for the pilot when the airplane is on the gound. ⁻ The CG is ahead of the main wheels and this enhances stability during the ground roll. 4 Tricycle landing gear 5 Tricycle landing gear • The length of the landing gear must be set so that the tail doesn’t hit the ground during landing. • This is measured from the wheel in the static position assuming an angle of attack for landing that gives 90% of maximum lift, usually 10o-15o. • The tipback angle is the maximum aircraft nose-up attitude when the tail is touching the ground and the landing gear strut is fully extended. • To prevent the aircraft from tipping back on its tail, the angle of the vertical from the main wheel position to the cg should be greater than the tipback angle or 15o, whichever is greater. 6 Tricycle landing gear • Tipback angle should not be greater than 25o, otherwise porpoising will occur and a high elevator deflection will be required for rotation during takeoff. • This means that more than 20% of aircraft weight is carried by the nose wheel. • The optimum range for the percentage of aircraft weight that is carried by the nose wheel is 8-15% for the most aft and most forward CG positions. -
FAA-H-8083-3A, Airplane Flying Handbook -- 3 of 7 Files
Ch 04.qxd 5/7/04 6:46 AM Page 4-1 NTRODUCTION Maneuvering during slow flight should be performed I using both instrument indications and outside visual The maintenance of lift and control of an airplane in reference. Slow flight should be practiced from straight flight requires a certain minimum airspeed. This glides, straight-and-level flight, and from medium critical airspeed depends on certain factors, such as banked gliding and level flight turns. Slow flight at gross weight, load factors, and existing density altitude. approach speeds should include slowing the airplane The minimum speed below which further controlled smoothly and promptly from cruising to approach flight is impossible is called the stalling speed. An speeds without changes in altitude or heading, and important feature of pilot training is the development determining and using appropriate power and trim of the ability to estimate the margin of safety above the settings. Slow flight at approach speed should also stalling speed. Also, the ability to determine the include configuration changes, such as landing gear characteristic responses of any airplane at different and flaps, while maintaining heading and altitude. airspeeds is of great importance to the pilot. The student pilot, therefore, must develop this awareness in FLIGHT AT MINIMUM CONTROLLABLE order to safely avoid stalls and to operate an airplane AIRSPEED This maneuver demonstrates the flight characteristics correctly and safely at slow airspeeds. and degree of controllability of the airplane at its minimum flying speed. By definition, the term “flight SLOW FLIGHT at minimum controllable airspeed” means a speed at Slow flight could be thought of, by some, as a speed which any further increase in angle of attack or load that is less than cruise. -
Landing Gear.Pdf
Study of Evolution and Details of Landing Gear INDEX CHAPTER 1 1.1.1 INTRODUCTION 3 1.1.2 EVOLUTION 3 CHAPTER 2 2.1 DIFFERENT TYPES OF LANDING GEARS 6 2.1.1 TRICYCLE LANDING GEAR 7 2.1.2 CONVENTIONAL LANDING GEAR 7 2.1.3 UNCONVENTIONAL LANDING GEAR 8 2.2 DIFFERENCE BETWEEN MAIN AND NOSE LANDING GEAR 9 2.3 SHOCK STRUTS 10 2.3.1 TYPES OF SHOCK STRUTS 1. METERING PIN TYPE 10 2. METERING TUBE TYPE 11 3. NOSE GEAR STRUTS 12 4. DOUBLE-ACTING SHOCK ABSORBER 12 2.4 OPERATION OF SHOCK STRUTS 13 CHAPTER 3 3.1 HYDRAULIC SYSTEM FOR AIRCRAFT LANDING GEAR 15 3.2 LANDING GEAR EXTENSION AND RETRACTION 15 3.2.1 LANDING GEAR EXTENSION AND RETRACTING MECHANISMS 15 3.3 EMERGENCY SYSTEMS 16 NIMRA INSTITUTE OF SCIENCE & TECHNOLOGY, A.E - 1 - Study of Evolution and Details of Landing Gear CHAPTER 4 4.1 BRAKING SYSTEM IN LANDING GEAR 18 4.2 DIFFERENT TYPES OF BRAKES AND THEIR EVOLUTION 4.2.1 CARBON AND BERYLLIUM BRAKES 18 4.2.2 AUTO-BRAKE AND BRAKE-BY-WIRE SYSTEM 19 4.3 DESCRIPTION OF A HYDRAULIC BRAKING SYSTEM 20 4.4 ADVANCED BRAKE CONTROL SYSTEM (ABCS) 21 4.5 PNEUMATIC BRAKING 21 4.6 DIFFERENTIAL BRAKING 22 CHAPTER 5 LUBRICANTS USED IN LANDING GEAR 23 CONCLUSION 24 REFERENCES 25 FIGURES FIG. 1 LANDING GEARS IN THE INITIAL STAGES 26 FIG. 2 BASIC TYPES OF LANDING GEARS 26 FIG. 3 TU-144 MAIN LANDING GEAR 27 FIG. 4 TRACK-TYPE GEAR 27 FIG. -
A Study on Landing Gear Arrangement of an Aircraft
ISSN(Online): 2319-8753 ISSN (Print): 2347-6710 International Journal of Innovative Research in Science, Engineering and Technology (A High Impact Factor & UGC Approved Journal) Website: www.ijirset.com Vol. 6, Issue 8, August 2017 A Study on Landing Gear Arrangement of an Aircraft Mohammad Afwan1, Danish S. Memon2, Yuvraj G. Pawar3, Shubham P. Kainge4 UG Students (B.E), Dept. of Mechanical Engineering, PRMIT&R, Amravati, India ABSTRACT: Landing gear is a vital structural unit of an aircraft which enables to take off and land safely on the ground. A variety of landing gear arrangements are used depending on the type and size of an aircraft. The most common type is the tri-cycle arrangement with one nose landing gear unit and two main landing gear units. Even during a normal landing operation heavy loads (equal to the weight of an aircraft) are to be absorbed by the landing gear. In turn joints are to be provided such that heavy concentrated loads are first received by the airframe and subsequently diffused to the surrounding areas. Normally heavy concentrated loads are received through a lug joint. Therefore design of a lug joint against failure under static and fatigue loading conditions assumes importance in the development of an aircraft structure. KEYWORDS: Landing Gear types and Arrangement. I. INTRODUCTION Aircraft is machine that is able to fly from one place to another place. Many researches were made to fly the machine since from mythology, many had lost their life during their experiments, and many failed to fly their machine. But finally in 1910 Wright Brothers build machine which is able to fly for 59seconds, which is very short duration but it is first milestone for development of aviation. -
History of Aircraft Track Landing Gear By: Tony Landis
History of Aircraft Track Landing Gear By: Tony Landis *(Extracted from historical study No. 135: Case History of Track Landing Gear) The design of landing gear is closely related to an aircraft’s mission. In the 1940’s it was thought that heavy bombardment aircraft, if using conventional systems, would require thick, expensive runways. Track landing gear systems appeared to be a solution to this issue. Substitution of track landing gear for wheel gear would eliminate the need for long, heavily enforced runways and facilitate operations on rough terrain. In 1944, Military Requirement A-1-1 called for “a new type airplane landing gear effecting maximum practicable weight distribution” suitable for use on pavement and unprepared surfaces. The use of multiple wheel or track gear was suggested. In July 1948, Air Materiel Command advised that the policy for landing gear design should define the surface available for safe aircraft operations. The idea of applying track landing gear to an aircraft in order to achieve flotation was first presented to the Air Corps by J.W. Christie, inventor of the Christie tank, and representatives of the Dowty Equipment Corporation of Long Island, New York. After being interviewed by General H.H. Arnold in November 1939, Christie was directed to work at Wright Field on drawings for a track landing gear installation on a Douglas A-20. Christie planned to use a belt made by the Goodrich Corporation designed for heavy construction work. A contract was issued to Dowty Equipment Corporation in June 1941 for engineering design of the A-20 track gear in the amount of $20,000. -
Aircraft Technology Roadmap to 2050 | IATA
Aircraft Technology Roadmap to 2050 NOTICE DISCLAIMER. The information contained in this publication is subject to constant review in the light of changing government requirements and regulations. No subscriber or other reader should act on the basis of any such information without referring to applicable laws and regulations and/or without taking appropriate professional advice. Although every effort has been made to ensure accuracy, the International Air Transport Association shall not be held responsible for any loss or damage caused by errors, omissions, misprints or misinterpretation of the contents hereof. Furthermore, the International Air Transport Association expressly disclaims any and all liability to any person or entity, whether a purchaser of this publication or not, in respect of anything done or omitted, and the consequences of anything done or omitted, by any such person or entity in reliance on the contents of this publication. © International Air Transport Association. All Rights Reserved. No part of this publication may be reproduced, recast, reformatted or transmitted in any form by any means, electronic or mechanical, including photocopying, recording or any information storage and retrieval system, without the prior written permission from: Senior Vice President Member & External Relations International Air Transport Association 33, Route de l’Aéroport 1215 Geneva 15 Airport Switzerland Table of Contents Table of Contents .............................................................................................................................................................................................................. -
Ftlain LANDING GEAR RUB Field Service- Dedicated to Serve You
VOi.. 1$, HO. 1, JAMIWIY- MARCH 1tM ftlAIN LANDING GEAR RUB Field Service- Dedicated to Serve You A SERVICE PUBLICATION OF The first operational Hercules aircraft was delivered in December LOCKHEED-GEORGIA COMPANY 1956 to Ardmore. Oklahoma. Almost 1800 Hercules airlifters and A DIVISION OF over 17 million flying hours later, the Lockheed-Georgia Company LOCKHEED CORPORATION # continues with a strong commitment to provide the support neces- sary for every operator to achieve maximum utilization of their air- Editor craft and associated equipment. Charles I. Gale Having been associated with Lockheed for averthirty years and in my present posItion, keenly aware of the Lockheed Associate Editors I am commitment and dedication to support its products. We have a Field Service organization designed to provide technical Doug Brashear assistance to world-wide, through on-site service representatives, regional James A. Loftin every customer, service representatives, and at the factory. Vera A. Taylor The history, and remarkable record of the Hercules Art Direction & Production long outstanding accomplishments, is not only a tribute to the aircraft, hut a tribute to the personnel of the many operators of Teri L. Mohr the aircraft throughout the world. Vol. 13, No. 1, January - March 1986 We like to think that our Field Service Representatives playedhave an importantand vital role in maklng these achievements possible. We are proud of the unique contribution CONTENTS Lockheed-Georgia Field Service Representatives have made to this record of success. A tra- 2 Focal Point ditionofservice born with the delivery of that first Hercules Iives today through the personaI Howard Burnette dedication of these specialists to the success of the aircraft and the operators who fly them. -
P 6 ^/ Summary Report on the C Preliminary Design Studies of an Advanced General Aviation Aircraft
NASW_443 5 )L P 6 ^/ SUMMARY REPORT ON THE C PRELIMINARY DESIGN STUDIES OF AN ADVANCED GENERAL AVIATION AIRCRAFT PREPARED FOR: NASA USRA ADVANCED DESIGN PROGRAM PREPARED BY: RON BARRETI' SHANE DEMOS S AB DIRKZWAGER I DARRYL EVANS CHARLES GOMER JERRY KEITER DARREN KNIPP iL GLEN SEIER STEVE SMITH ED WENNTNGER THE UNIVERSITY OF KANSAS MAY 1991 TEAM LEADER: CHARLES GOMER FACULTY ADVISOR: JAN ROSKAM NASA ADVISOR: JACK MORRIS (NASA-C-190024) PRELIMINARY DEI',N STUDIES N92-200ô4 OF AN ADVANCED GENERAL AVIATION AIRCRAFT Summary Report (Kansas Univ.) 204 p CSCL OIC Unci as G3/05 0073949 ABSTRACT The purpose of this report is to present the preliminary design results of the advanced aircraft design project at the University of Kansas. The goal of the project is to take a revolutionary look into the design of a general aviation aircraft. This project was conducted as a graduate level design class under the auspices of the KUINASA/USRA Advanced Design Program in Aeronautics. The class is open to aerospace and electrical engineering seniors and first level graduate students. Phase I of the design procedure (fall semester 1990) included the preliminary design of two configurations, a pusher and a tractor. The references listed in Section 1.1 of this report document this preliminary airframe design as well as other (more detailed) design studies, such as a pilot workload study, an advanced guidance and display study, a market survey, structural layout and manufacturing, and others. Phase II (spring semester 1991) included the selection of only one configuration for further study. The pusher configuration was selected on the basis of performance characteristics, cabin noise considerations, natural laminar flow considerations, and system layouts. -
Project Hegaasus
PROJECT HEGAASUS Loughborough University, UK Virginia Tech, USA Powertrain Department Structures Department Aircraft Systems Department Aircraft Performance Department Business and Sales Department Modelling Department HYBRID ELECTRIC GENERAL AVIATION AIRCRAFT 2018 AIAA UNDERGRADUATE DESIGN COMPETITION Hybrid Electric General Aviation Aircraft Proposal HAMSTERWORKS DESIGN TEAM Sammi Rocker (USA) Daniel Guerrero (UK) Kyle Silva (USA) Design and Modelling Aircraft Integration Landing Gear & Certification AIAA – 543803 AIAA – 921916 AIAA –921097 Ashley Peyton-Bruhl (UK) Danny Fritsch (USA) Nathaniel Marsh (UK) Business & Sales Flight Physics Propulsion Design AIAA – 921913 AIAA-921435 AIAA-921919 Troy Bergin (USA) Jennifer Glover (UK) Alexander Mclean (USA) Structural Design Powertrain Design Stability & Performance AIAA – 736794 AIAA - 921554 AIAA - 921291 Dhirun Mistry (UK) Pradeep Raj, Ph.D. (USA) James Knowles, Ph.D. (UK) Avionic Systems Virginia Tech Advisor Loughborough University Advisor AIAA – 921917 i Hybrid Electric General Aviation Aircraft Proposal CONTENTS HAMSTERWORKS DESIGN TEAM ................................................................................................................ I LIST OF FIGURES .............................................................................................................................................V LIST OF TABLES ........................................................................................................................................... VII LIST OF ABBREVIATIONS -
Federal Register / Vol. 60, No. 155 / Friday, August 11, 1995 / Proposed Rules
41160 Federal Register / Vol. 60, No. 155 / Friday, August 11, 1995 / Proposed Rules DEPARTMENT OF TRANSPORTATION The comments should identify the foster and promote general aviation while regulatory docket or notice number and continuing to improve its safety record. Federal Aviation Administration should be submitted in triplicate to the These goals are neither contradictory nor Rules Docket address specified above. separable. They are best achieved by 14 CFR Parts 1, 61, 141, and 143 cooperating with the aviation community to All comments received on or before the define mutual concerns and joint efforts to [Docket No. 25910; Notice No. 95±11] closing date for comments will be accomplish objectives. We will strive to considered by the Administrator before achieve the goals through voluntary RIN: 2120±AE71 action is taken on the proposed compliance and methods designed to reduce amendments, and the proposals the regulatory burden on general aviation. Pilot, Flight Instructor, Ground contained in this notice may be changed The FAA's general aviation programs Instructor, and Pilot School in light of comments received. All will focus on: Certification Rules comments received as well as a report 1. SafetyÐTo protect recent gains and AGENCY: Federal Aviation summarizing any substantive public aim for a new threshold. Administration (FAA), DOT. contact with FAA personnel on this 2. FAA ServicesÐTo provide the rulemaking will be filed in the docket. general aviation community with ACTION: Notice of proposed rulemaking The docket is available for public responsive, customer-driven (NPRM). inspection before and after the closing certification, air traffic, and other SUMMARY: This action proposes to revise date for submitting comments.