Relaxed Mass Limits: a New Option for Reducing Spacecraft Costs
Total Page:16
File Type:pdf, Size:1020Kb
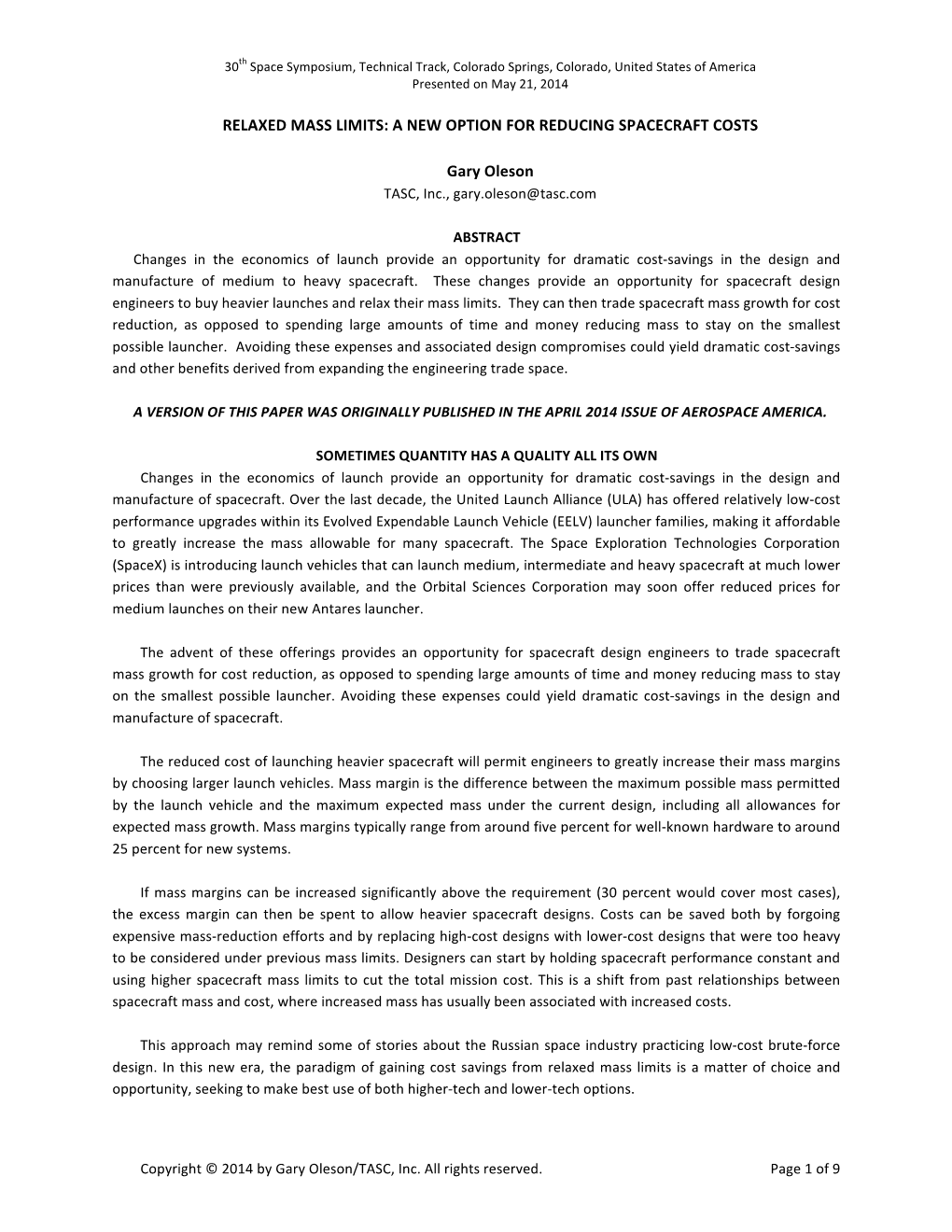
Load more
Recommended publications
-
Do Not Circulate
LA-7328-PR Progress Report a . Laser Fusion Program July 1—December 31, 1977 ,- .. .. .. ..-— — DO NOT CIRCULATE PERMANENT RETENTION ! REQUIREDBY CONTRACT v LOS ALAMOS SCIENTIFIC LABORATORY Lail!lik — post Office Box 1663 Los Alamos, New Mexico 87545 An AffumativeAction/EqualOpportunityEmployex . The four most recent reports in this series,un- classified, are LA-65 10-PR, LAY6 16-PR, LA4834-PR, and LA-6982-PR. This work was supported by the US Department of Energy, Office of Laser Fusion. TM. report was prep.rcd as m .CLWUII1O( work sponsored by the United SUICS Go”enlme”l. Neither the Un,ted Stiles I nor the United Slates Department cd Enersy. nor any of their employees. nor any 0( their CO.114C10rS. subcontrar tom. or their ●w.loyecs. makes any warranty. .xD,,!s O, irnPlled. ., P .isume. any Iesal Ii. biiity or responsibkbw for the accuracy. cmnpletcncm. y usefulness of any information. app.; .t.s. product. or Pro..= dl=losed. or rrpreacnm that its w would “.1 i“fri”le privately owned rlthls. UNITED STATES DEPARTMENT OF CNCRGV CONTRACT W-7408 -CNO. S6 LA-7328-PR Progress Report UC-21 IssI,W: December 1978 . Laser Fusion Program at LASL July 1—December 31, 1977 Compiled by Frederick Skoberne 4 .! L-. — .— - . ABSTRACT . ...”” 1 SUMMARY . ...0000oo 2 Introduction . 2 CO, Laser Program . 2 Antares . 2 CO, Laser Technology . 3 Laser Fusion Theory, Experiments, and Target Design . 3 Laser Fusion Target Fabrication . 4 1, CO, LASER PROGRAM . 6 Single-Beam System . 6 llvo-Beam System . 6 Eight-Beam System . 8 II. ANTARES-HIGH-ENERGY GAS IJM3ERFAClLITY . -
Orbital Sciences 2013 Annual Report Final Version.Pdf
Orbital Sciences Corporation 2013 ANNUAL REPORT Antares Test Flight Launched 9 Research Rockets Launched in Second Wallops Island, VA Quarter Orbital Sciences Corporation YEAR IN REVIEW 41 Space Missions Conducted and 37 Rockets and Satellites Sold in 2013 Coyote Target Launched Azerspace/Africasat-1a San Nicolas Island, CA Satellite Launched Orbital Wins Order for Kourou, French Guiana Thaicom 8 Satellite Missile Defense Interceptor Launched Vandenberg AFB, CA Orbital Selected to Develop Stratolaunch Vehicle Coyote Target Launched San Nicolas Island, CA JANUARY FEBRUARY MARCH APRIL MAY JUNE Landsat 8 Satellite 3 Coyote Targets Launched Orbital Wins NASA Launched Vandenberg AFB, CA TESS Satellite Contract San Nicolas Island, CA Orbital Wins New Satellite to identify Earth- Interceptor Order like planets Antares Stage One Hot-Fire Test Conducted Wallops Island, VA Orbital Wins NASA ICON Satellite Contract Satellite to study the Sun’s effect on the Ionosphere Coyote Target Launched 5 Antares Engines Tested 3 Research Rockets San Nicolas Island, CA Launched in First Quarter 9 Research Rockets 4 Research Rockets Launched in Second Launched in Third Quarter Quarter 2 Coyote Targets Launched Orbital Receives New San Nicolas Island, CA Target Vehicle Order Pegasus Launched IRIS Satellite Vandenberg AFB, CA Minotaur V Debut Additional Military Launched LADEE Lunar SES-8 Satellite Satellite Order Received Probe Launched 2 Coyote Targets Wallops Island, VA Cape Canaveral, FL Launched Kauai, HI JULY AUGUST SEPTEMBER OCTOBER NOVEMBER DECEMBER Antares -
The ANTARES Collaboration
PROCEEDINGS OF THE 31st ICRC, ŁOD´ Z´ 2009 1 The ANTARES Collaboration: contributions to the 31st International Cosmic Ray Conference (ICRC 2009), Lodz, Poland, July 2009 Abstract The Antares neutrino telescope, operating at 2.5 km depth in the Mediterranean Sea, 40 km off the Toulon shore, represents the world’s largest operational underwater neutrino telescope, optimized for the detection of Cerenkov light produced by neutrino-induced muons. The main goal of Antares is the search of high energy neutrinos from astrophysical point or transient sources. Antares is taking data in its full 12 lines configuration since May 2008: in this paper we collect the 16 contributions by the ANTARES collaboration that were submitted to the 31th International Cosmic Ray Conference ICRC 2009. These contributions includes the detector performances, the first preliminary results on neutrino events and the current physics analysis including the sensitivity to point like sources, the possibility to detect high energy neutrinos in coincidence with GRB, the search for dark matter or exotic particles. arXiv:1002.0701v1 [astro-ph.HE] 3 Feb 2010 2 THE ANTARES COLLABORATION ANTARES Collaboration J.A. Aguilar1, I. Al Samarai2, A. Albert3, M. Anghinolfi4, G. Anton5, S. Anvar6, M. Ardid7, A.C. Assis Jesus8, T. Astraatmadja8; a, J.J. Aubert2, R. Auer5, B. Baret9, S. Basa10, M. Bazzotti11; 12, V. Bertin2, S. Biagi11; 12, C. Bigongiari1, M. Bou-Cabo7, M.C. Bouwhuis8, A. Brown2, J. Brunner2; b, J. Busto2, F. Camarena7, A. Capone13; 14, C.C^arloganu15, G. Carminati11; 12, J. Carr2, E. Castorina16; 17, V. Cavasinni16; 17, S. Cecchini12; 18, Ph. -
Sale Price Drives Potential Effects on DOD and Commercial Launch Providers
United States Government Accountability Office Report to Congressional Addressees August 2017 SURPLUS MISSILE MOTORS Sale Price Drives Potential Effects on DOD and Commercial Launch Providers Accessible Version GAO-17-609 August 2017 SURPLUS MISSILE MOTORS Sale Price Drives Potential Effects on DOD and Commercial Launch Providers Highlights of GAO-17-609, a report to congressional addressees Why GAO Did This Study What GAO Found The U.S. government spends over a The Department of Defense (DOD) could use several methods to set the sale billion dollars each year on launch prices of surplus intercontinental ballistic missile (ICBM) motors that could be activities as it strives to help develop a converted and used in vehicles for commercial launch if current rules prohibiting competitive market for space launches such sales were changed. One method would be to determine a breakeven and assure its access to space. Among price. Below this price, DOD would not recuperate its costs, and, above this others, one launch option is to use price, DOD would potentially save. GAO estimated that DOD could sell three vehicles derived from surplus ICBM Peacekeeper motors—the number required for one launch, or, a “motor set”—at motors such as those used on the Peacekeeper and Minuteman missiles. a breakeven price of about $8.36 million and two Minuteman II motors for about The Commercial Space Act of 1998 $3.96 million, as shown below. Other methods for determining motor prices, such prohibits the use of these motors for as fair market value as described in the Federal Accounting Standards Advisory commercial launches and limits their Board Handbook, resulted in stakeholder estimates ranging from $1.3 million per use in government launches in part to motor set to $11.2 million for a first stage Peacekeeper motor. -
ANTARES: Spacecraft Simulation for Multiple User Communities and Facilities
ANTARES: Spacecraft Simulation for Multiple User Communities and Facilities Amanda Acevedo Jason Arnold NASA – Johnson Space Center NASA – Johnson Space Center [email protected] [email protected] Jon Berndt Robert Gay Jacobs Engineering NASA – Johnson Space Center [email protected] [email protected] William Othon NASA – Johnson Space Center [email protected] ABSTRACT The Advanced NASA Technology Architecture for Exploration Studies (ANTARES) simulation is the primary tool being used for requirements assessment of the NASA Orion spacecraft by the Guidance Navigation and Control (GN&C) teams at Johnson Space Center (JSC). ANTARES is a collection of packages and model libraries that are assembled and executed by the Trick simulation environment. Currently, ANTARES is being used for spacecraft design assessment, performance analysis, requirements validation, Hardware In the Loop (HWIL) and Human In the Loop (HIL) testing. Keywords Modeling and Simulation, Vision for Space Exploration, Crew Exploration Vehicle, Project Orion 1 Introduction With the Constellation program ramping up, NASA is well into building up a simulation and analysis capability to support a broad set of needs. At the lowest level, engineers at various centers need to be able to execute short, single vehicle runs (such as a Crew Launch Vehicle (CLV) ascent run, or for a Launch Abort System (LAS) run) on a desktop workstation. On a broader scale, distributed simulations will be implemented, tying together the efforts of various centers. Underlying the development of these capabilities is a desire to avoid duplication of efforts, and adhering to agreed-upon conventions and established standards to maximize compatibility. -
Undergraduate Thesis Prospectus Design And
Undergraduate Thesis Prospectus Design and Construction of an Amateur Radio CubeSat (technical research project in Aerospace Engineering) The Right Rocket for the Job: Small Launch Providers Target Small Satellites (STS research project) by Gabriel Norris October 31, 2019 technical project collaborators: MAE 4690/4700 Spacecraft Design Team On my honor as a University student, I have neither given nor received unauthorized aid on this assignment as defined by the Honor Guidelines for Thesis-Related Assignments. signed: __________________________________________ date: ________________ approved: ________________________________________ date: ________________ Peter Norton, Department of Engineering and Society approved: ________________________________________ date: ________________ Christopher Goyne, Department of Aerospace Engineering 2 General Research Problem: Small Satellites in Low Earth Orbit How can we efficiently and reliably put scientific and communications equipment into orbit? The development of radio telecommunications transformed human communication. The line-of-sight propagation of most radio signals, however, kept the technology from enabling truly global communication for some time. By 1927, it was possible to bounce high-energy radio waves off the ionosphere, which enabled transcontinental radiotelephony, but at a very high cost and with poor signal quality. In October 1945, Arthur C. Clarke published an article proposing the concept of a satellite constellation for the purpose of relaying signals around the world, a full twelve years before the launch of Sputnik 1 (Clarke, 1945). In 1958, Clarke’s vision came to pass with the launch of the first communications satellite SCORE, which broadcast a Christmas greeting from President Eisenhower to the entire world (Martin, 2007). Now over 2,000 satellites orbit the Earth and the world is more interconnected than ever. -
Assessing the Impact of US Air Force National Security Space Launch Acquisition Decisions
C O R P O R A T I O N BONNIE L. TRIEZENBERG, COLBY PEYTON STEINER, GRANT JOHNSON, JONATHAN CHAM, EDER SOUSA, MOON KIM, MARY KATE ADGIE Assessing the Impact of U.S. Air Force National Security Space Launch Acquisition Decisions An Independent Analysis of the Global Heavy Lift Launch Market For more information on this publication, visit www.rand.org/t/RR4251 Library of Congress Cataloging-in-Publication Data is available for this publication. ISBN: 978-1-9774-0399-5 Published by the RAND Corporation, Santa Monica, Calif. © Copyright 2020 RAND Corporation R® is a registered trademark. Cover: Courtesy photo by United Launch Alliance. Limited Print and Electronic Distribution Rights This document and trademark(s) contained herein are protected by law. This representation of RAND intellectual property is provided for noncommercial use only. Unauthorized posting of this publication online is prohibited. Permission is given to duplicate this document for personal use only, as long as it is unaltered and complete. Permission is required from RAND to reproduce, or reuse in another form, any of its research documents for commercial use. For information on reprint and linking permissions, please visit www.rand.org/pubs/permissions. The RAND Corporation is a research organization that develops solutions to public policy challenges to help make communities throughout the world safer and more secure, healthier and more prosperous. RAND is nonprofit, nonpartisan, and committed to the public interest. RAND’s publications do not necessarily reflect the opinions of its research clients and sponsors. Support RAND Make a tax-deductible charitable contribution at www.rand.org/giving/contribute www.rand.org Preface The U.S. -
2013 Commercial Space Transportation Forecasts
Federal Aviation Administration 2013 Commercial Space Transportation Forecasts May 2013 FAA Commercial Space Transportation (AST) and the Commercial Space Transportation Advisory Committee (COMSTAC) • i • 2013 Commercial Space Transportation Forecasts About the FAA Office of Commercial Space Transportation The Federal Aviation Administration’s Office of Commercial Space Transportation (FAA AST) licenses and regulates U.S. commercial space launch and reentry activity, as well as the operation of non-federal launch and reentry sites, as authorized by Executive Order 12465 and Title 51 United States Code, Subtitle V, Chapter 509 (formerly the Commercial Space Launch Act). FAA AST’s mission is to ensure public health and safety and the safety of property while protecting the national security and foreign policy interests of the United States during commercial launch and reentry operations. In addition, FAA AST is directed to encourage, facilitate, and promote commercial space launches and reentries. Additional information concerning commercial space transportation can be found on FAA AST’s website: http://www.faa.gov/go/ast Cover: The Orbital Sciences Corporation’s Antares rocket is seen as it launches from Pad-0A of the Mid-Atlantic Regional Spaceport at the NASA Wallops Flight Facility in Virginia, Sunday, April 21, 2013. Image Credit: NASA/Bill Ingalls NOTICE Use of trade names or names of manufacturers in this document does not constitute an official endorsement of such products or manufacturers, either expressed or implied, by the Federal Aviation Administration. • i • Federal Aviation Administration’s Office of Commercial Space Transportation Table of Contents EXECUTIVE SUMMARY . 1 COMSTAC 2013 COMMERCIAL GEOSYNCHRONOUS ORBIT LAUNCH DEMAND FORECAST . -
Commercial Space Launch and Northrop Grumman Launch Solutions
Commercial Space Launch and Northrop Grumman Launch Solutions Wernher von Braun Symposium October 2018 John Steinmeyer Director, Space Launch Business Development, Launch Vehicle Division Flight System Group Evolution of Commercial Space Launch 2 Government and Commercial are Symbiotic • Government experience facilitated development and successful flight demonstration of components later used in commercial systems • Significant current synergy with NASA and defense programs enables economies of scale 3 Northrup Grumman Space Launch Services • Active Launch Vehicle Programs ‒ Pegasus: Proven class 3 air-launch ‒ Minotaur USAF: Tailorable government launch ‒ Minotaur Commercial: Affordable commercial small launch ‒ Antares: International Space Station cargo resupply • New launch system under development (intermediate and heavy class) • Northrop Grumman space launch programs serve DoD, NASA and commercial markets 4 Successful NASA/Commercial Partnership • Successful COTS development and CRS-1 cargo delivery • More than 50,000 lbs. delivered to date • Optimized volume solution provides maximum utility • Awarded multiple follow-on missions including at least six CRS-2 missions 5 Cygnus spacecraft Antares launch vehicle 5M Diameter Composite Payload Fairing 3rd Stage - LOx/H2 Cryogenic Liquid Propulsion Using RL10-C-5 Engines 2nd Stage -Solid, Single Segment CASTOR 300 Motor 1st Stage - Solid, Two-Segment CASTOR 600 Motor - Four-Segment CASTOR 1200 Motor for Heavy Vehicle GEM 63XLT Strap-On Solid Motors to Augment Performance – 0-6 6 Future NASA/Commercial Cooperation Integrated solutions for cislunar and other exploration goals SLS booster production and performance enhancements Continued execution of cargo resupply missions 7 . -
Current Space Launch Vehicles Used by The
Current Space Launch Vehicles Used by the HEET United States S Nathan Daniels April 2014 At present, the United States relies on Russian rocket engines to launch satellites ACT into space. F The U.S. also relies on Russia to transport its astronauts to the International Space Station (as the U.S. Space Shuttle program ended in 2011). Not only does this reliance have direct implications for our launch capabilities, but it also means that we are funding Russian space and missile technology while we could be investing in U.S. based jobs and the defense industrial base. These facts raises national security concerns, as the United States’ relationship with Russia is ever-changing - the situation in Ukraine is a prime example. This paper serves as a brief, but factual overview of active launch vehicles used by the United States. First, are the three vehicles with the payload capability to launch satellites into orbit: the Atlas V, Delta IV, and the Falcon 9. The other active launch vehicles will follow in alphabetical order. www.AmericanSecurityProject.org 1100 New York Avenue, NW Suite 710W Washington, DC AMERICAN SECURITY PROJECT Atlas Launch Vehicle History and the Current Atlas V • Since its debut in 1957 as America’s first operational intercon- tinental ballistic missile (ICBM) designed by the Convair Divi- sion of General Dynamics, the Atlas family of launch vehicles has logged nearly 600 flights. • The missiles saw brief ICBM service, and the last squadron was taken off of operational alert in 1965. • From 1962 to 1963, Atlas boosters launched the first four Ameri- can astronauts to orbit the Earth. -
HSFP-R Contingency Planning
International Space Station National Research Council April 2013 Michael T. Suffredini Manager, ISS Program Office 1 ISS Facts and Figures Mass = 902,000 lbs Truss Length = 358 ft Altitude = 224 nautical miles Living space = 32,333 ft3 Velocity = 17,500 mph Solar array surface area = 38,400 ft2 (0.88 acre) generating 84 kW Assembly flights = 41 Spacewalks = 161 (1015 hours) Crew members = 205 different people from 15 countries Continuous human presence since November 2000 ISS Configuration 3 ISS TRANSPORTATION SYSTEMS H-IIB/ Falcon 9/ Antares/ Proton Soyuz / Ariane/ Progress ATV HTV Dragon Cygnus Commercial Crew Potential Candidates4 NASA: OC4/John Coggeshall For current baseline refer to ISS Flight Plan MAPI: OP/Scott Paul SSP 54100 Multi-Increment Planning Document (MIPD) Flight Planning Integration Panel (FPIP) Chart Updated: April 3rd, 2013 SSCN/CR: 13681A + Tact. Mods (In-Work) 2013 2014 2015 Mar Apr May Jun Jul Aug Sep Oct Nov Dec Jan Feb Mar Apr May Jun Jul Aug Sep Oct Nov Dec Jan Feb In Inc 35 Inc 36 Inc 37 Inc 38 Inc 39 Inc 40 Inc 41 Inc 42 (32S) R P. Vinogradov (CDR-36) 167 days (34S) R O. Kotov (CDR-38) 168 days (36S) N S. Swanson (CDR-40) 174 days (38S) N B. Wilmore (CDR-42) 167 days (40S) (32S) R Misurkin 167 days (34S) R S. Ryazanskiy 168 days (36S) R A. Skvortsov 174 days (38S) R Y. Serova 167 days (40S) (32S) N Cassidy 167 days (34S) N M. Hopkins 168 days (36S) R O. Artemyev 174 days (38S) R A. Samokutyayev 167 days (40S) C C. -
Commercial Space Race Heats Up
and built by veterans KB Yuzhnoye and Yuzhmash, both based in Dnipropetrovsk, Ukraine. Cygnus’s sensors come from Mit- subishi Electric in Tokyo and its pressurized cargo module was built at a Thales Alenia Space plant in Turin, Italy. “Orbital used more heritage technology,” says Alan Lindenmoyer, manager of NASA’s commercial crew and cargo programme. “That was less risky for us.” But the company did not enter COTS until 2008, two years after SpaceX. With the clock ticking, NASA allocated less money for Orbital and ordered a simpler ship. Unlike SpaceX’s Dragon capsule, Cygnus can’t carry sensitive biological experiments, such as those that grow protein crystals in microgravity. It burns up on re-entry, so it can’t return samples to Earth. And it can’t be modified to carry humans. CORPORATION SCIENCES ORBITAL A successful engine test last month means that the Antares rocket can proceed to its inaugural launch. Nor has it yet flown. Orbital chose to launch from NASA’s Wallops Flight Facility in Virginia; SPACE FLIGHT less crowded than Cape Canaveral in Florida, which hosts most NASA rocket launches, Wal- lops usually caters for smaller vehicles such as scientific balloons and sounding rockets. The Commercial space facility’s Mid-Atlantic Regional Spaceport had to build a new launch pad for Antares, which took longer than expected. Originally scheduled race heats up for 2010, the demonstration launch slipped to 2012, and then to 2013, after Hurricane Sandy hit the spaceport last October. Antares test could challenge dominance of Falcon 9 rocket. Antares’ engines, built half a century ago for Russia’s Moon programme and recently BY DEVIN POWELL California and former director of NASA’s Ames refurbished, have also proven finicky.