3 Elements of Contact Mechanics
Total Page:16
File Type:pdf, Size:1020Kb
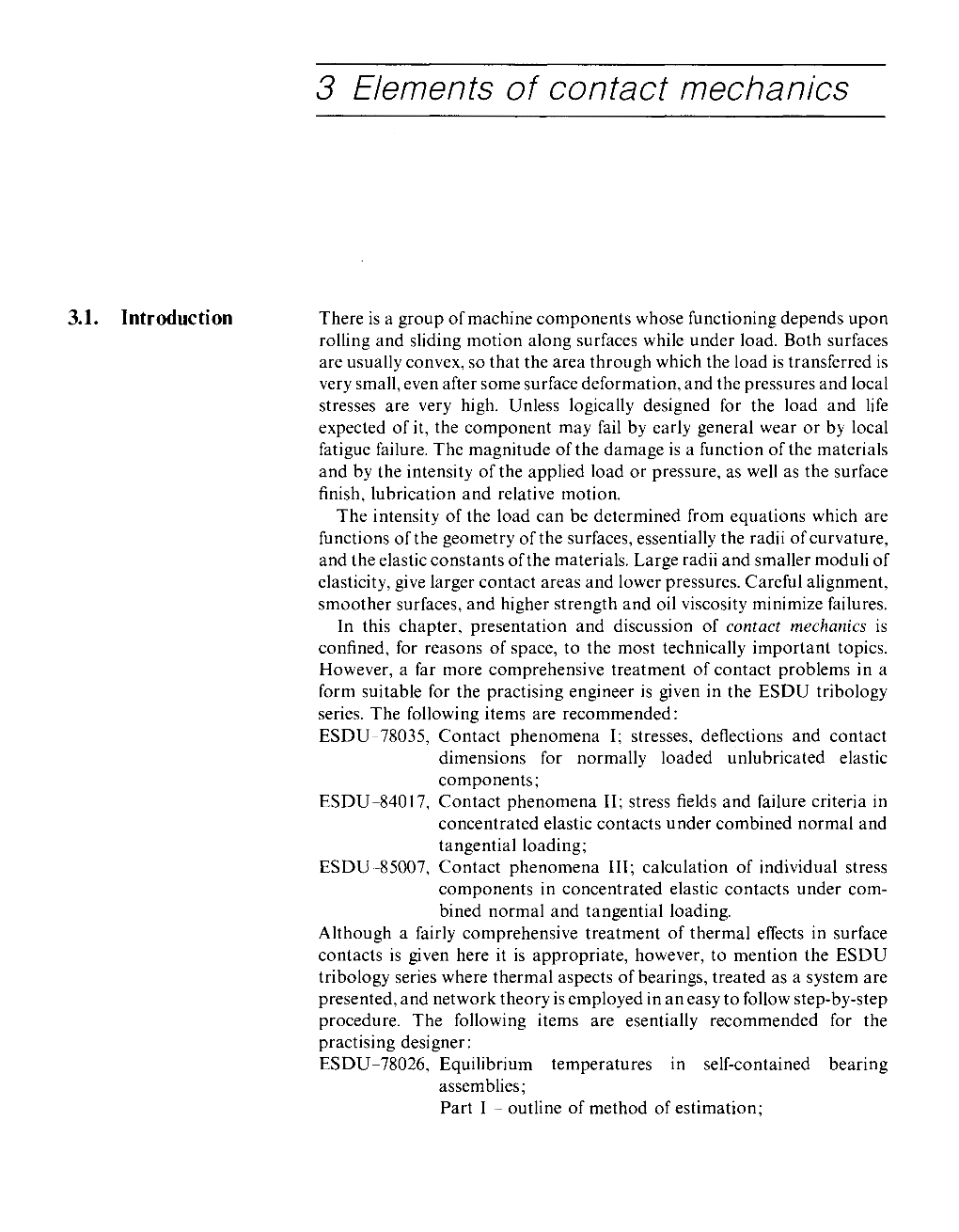
Load more
Recommended publications
-
Contact Mechanics in Gears a Computer-Aided Approach for Analyzing Contacts in Spur and Helical Gears Master’S Thesis in Product Development
Two Contact Mechanics in Gears A Computer-Aided Approach for Analyzing Contacts in Spur and Helical Gears Master’s Thesis in Product Development MARCUS SLOGÉN Department of Product and Production Development Division of Product Development CHALMERS UNIVERSITY OF TECHNOLOGY Gothenburg, Sweden, 2013 MASTER’S THESIS IN PRODUCT DEVELOPMENT Contact Mechanics in Gears A Computer-Aided Approach for Analyzing Contacts in Spur and Helical Gears Marcus Slogén Department of Product and Production Development Division of Product Development CHALMERS UNIVERSITY OF TECHNOLOGY Göteborg, Sweden 2013 Contact Mechanics in Gear A Computer-Aided Approach for Analyzing Contacts in Spur and Helical Gears MARCUS SLOGÉN © MARCUS SLOGÉN 2013 Department of Product and Production Development Division of Product Development Chalmers University of Technology SE-412 96 Göteborg Sweden Telephone: + 46 (0)31-772 1000 Cover: The picture on the cover page shows the contact stress distribution over a crowned spur gear tooth. Department of Product and Production Development Göteborg, Sweden 2013 Contact Mechanics in Gears A Computer-Aided Approach for Analyzing Contacts in Spur and Helical Gears Master’s Thesis in Product Development MARCUS SLOGÉN Department of Product and Production Development Division of Product Development Chalmers University of Technology ABSTRACT Computer Aided Engineering, CAE, is becoming more and more vital in today's product development. By using reliable and efficient computer based tools it is possible to replace initial physical testing. This will result in cost savings, but it will also reduce the development time and material waste, since the demand of physical prototypes decreases. This thesis shows how a computer program for analyzing contact mechanics in spur and helical gears has been developed at the request of Vicura AB. -
AC Fischer-Cripps
A.C. Fischer-Cripps Introduction to Contact Mechanics Series: Mechanical Engineering Series ▶ Includes a detailed description of indentation stress fields for both elastic and elastic-plastic contact ▶ Discusses practical methods of indentation testing ▶ Supported by the results of indentation experiments under controlled conditions Introduction to Contact Mechanics, Second Edition is a gentle introduction to the mechanics of solid bodies in contact for graduate students, post doctoral individuals, and the beginning researcher. This second edition maintains the introductory character of the first with a focus on materials science as distinct from straight solid mechanics theory. Every chapter has been 2nd ed. 2007, XXII, 226 p. updated to make the book easier to read and more informative. A new chapter on depth sensing indentation has been added, and the contents of the other chapters have been completely overhauled with added figures, formulae and explanations. Printed book Hardcover ▶ 159,99 € | £139.99 | $199.99 The author begins with an introduction to the mechanical properties of materials, ▶ *171,19 € (D) | 175,99 € (A) | CHF 189.00 general fracture mechanics and the fracture of brittle solids. This is followed by a detailed description of indentation stress fields for both elastic and elastic-plastic contact. The discussion then turns to the formation of Hertzian cone cracks in brittle materials, eBook subsurface damage in ductile materials, and the meaning of hardness. The author Available from your bookstore or concludes with an overview of practical methods of indentation. ▶ springer.com/shop MyCopy Printed eBook for just ▶ € | $ 24.99 ▶ springer.com/mycopy Order online at springer.com ▶ or for the Americas call (toll free) 1-800-SPRINGER ▶ or email us at: [email protected]. -
1 Classical Theory and Atomistics
1 1 Classical Theory and Atomistics Many research workers have pursued the friction law. Behind the fruitful achievements, we found enormous amounts of efforts by workers in every kind of research field. Friction research has crossed more than 500 years from its beginning to establish the law of friction, and the long story of the scientific historyoffrictionresearchisintroducedhere. 1.1 Law of Friction Coulomb’s friction law1 was established at the end of the eighteenth century [1]. Before that, from the end of the seventeenth century to the middle of the eigh- teenth century, the basis or groundwork for research had already been done by Guillaume Amontons2 [2]. The very first results in the science of friction were found in the notes and experimental sketches of Leonardo da Vinci.3 In his exper- imental notes in 1508 [3], da Vinci evaluated the effects of surface roughness on the friction force for stone and wood, and, for the first time, presented the concept of a coefficient of friction. Coulomb’s friction law is simple and sensible, and we can readily obtain it through modern experimentation. This law is easily verified with current exper- imental techniques, but during the Renaissance era in Italy, it was not easy to carry out experiments with sufficient accuracy to clearly demonstrate the uni- versality of the friction law. For that reason, 300 years of history passed after the beginning of the Italian Renaissance in the fifteenth century before the friction law was established as Coulomb’s law. The progress of industrialization in England between 1750 and 1850, which was later called the Industrial Revolution, brought about a major change in the production activities of human beings in Western society and later on a global scale. -
C: Contact Mechanics, in "Principles and Techniques for Desiging Precision Machines." MIT Phd Thesis, 1999
C Contact MechanicsI The theory developed by Hertz in 1880 remains the foundation for most contact problems encountered in engineering. It applies to normal contact between two elastic solids that are smooth and can be described locally with orthogonal radii of curvature such as a toroid. Further, the size of the actual contact area must be small compared to the dimensions of each body and to the radii of curvature. Hertz made the assumption based on observations that the contact area is elliptical in shape for such three-dimensional bodies. The equations simplify when the contact area is circular such as with spheres in contact. At extremely elliptical contact, the contact area is assumed to have constant width over the length of contact such as between parallel cylinders. The first three sections present the Hertz equations for these distinct cases. In addition, Section C.4 presents the equations for a sphere contacting a conical socket. Hertz theory does not account for tangential forces that may develop in applications where the surfaces slide or carry traction. Extensions to Hertz theory approximate this behavior to reasonable accuracy. Section C.5 presents the more useful equations. The final section C.6 contains MathcadÔ documents that implement these equations for computer analysis. The Hertz equations are important in the engineering of kinematic couplings particularly if the loads carried are relatively high. For a particular choice of material and contact geometry, the pertinent calculations reduce to families of curves that are convenient for sizing purposes. The typical material used is hardened bearing steel, for example, 52100 steel or 440C stainless steel heat treated to 58-62 Rockwell C. -
Contact Mechanics and Friction
Contact Mechanics and Friction Valentin L. Popov Contact Mechanics and Friction Physical Principles and Applications 1 3 Professor Dr. Valentin L. Popov Berlin University of Technology Institute of Mechanics Strasse des 17.Juni 135 10623 Berlin Germany [email protected] ISBN 978-3-642-10802-0 e-ISBN 978-3-642-10803-7 DOI 10.1007/978-3-642-10803-7 Springer Heidelberg Dordrecht London New York Library of Congress Control Number: 2010921669 c Springer-Verlag Berlin Heidelberg 2010 This work is subject to copyright. All rights are reserved, whether the whole or part of the material is concerned, specifically the rights of translation, reprinting, reuse of illustrations, recitation, broadcasting, reproduction on microfilm or in any other way, and storage in data banks. Duplication of this publication or parts thereof is permitted only under the provisions of the German Copyright Law of September 9, 1965, in its current version, and permission for use must always be obtained from Springer. Violations are liable to prosecution under the German Copyright Law. The use of general descriptive names, registered names, trademarks, etc. in this publication does not imply, even in the absence of a specific statement, that such names are exempt from the relevant protective laws and regulations and therefore free for general use. Cover design: WMXDesign GmbH Printed on acid-free paper Springer is part of Springer Science+Business Media (www.springer.com) Dr. Valentin L. Popov studied physics and obtained his doctorate from the Moscow State Lomonosow University. He worked at the Institute of Strength Physics and Materials Science of the Russian Academy of Sciences. -
Introduction the Failure Process
Introduction The subject of this thesis is the surface damage due to rolling contact fatigue. Surfaces that are repeatedly loaded by rolling and sliding motion may be exposed to contact fatigue. Typical mechanical applications where such contact arises are: gears; cams; bearings; rail/wheel contacts. These components are in general exposed to high contact stresses. Despite the different purposes, they will according to Tallian [1] sooner or later suffer to contact fatigue damage if other failure modes are avoided. Even if the contact stresses may be of the same magnitude for different applications the resulting fatigue damage may vary. This is due to the fact that the contact conditions differ between the applications. The objective with the work was to verify the asperity point load mechanism for surface initiated rolling contact fatigue damage. The main focus has been on surface fatigue damage in spur gears. However, similar surface damage has been found in the other applications as well. The hypothesis was that local surface contacts can be of importance for surface initiated contact damage. The hypothesis can be visualized as local contact between asperities. When two surfaces are brought into contact the real contact area will be smaller than the apparent, this due too the fact that the contact surface is not perfectly smooth. Thus, the asperities will support the contact; see for instance Johnson [2]. The local asperity contacts will introduce stress concentrations, which will change the nominal stress field. A single asperity contact can be viewed as a Boussinesq point contact [2]. For non-conformal mechanical contacts that are susceptible for rolling contact fatigue the nominal stress fields are of Hertzian type. -
Contact Mechanics and Tribology Match
FEATURE ARTICLE Jeanna Van Rensselar / Contributing Editor Beneath the Why contact mechanics and tribology are a natural match KEY CONCEPTCONCEPTSS • CoContacntact mechanics iiss a sometimes oveoverlookedrlooked bbutut ccriticalritical asaspectpect of ttribology.ribology. • FriFrictionction rereductionduction iiss maximizmaximizeded by lleveragingeveraging the dydynaminamic bbetweenetween ssurfaceurface mmaterialaterial gengineeringg aandnd lublubricationrication genengineering. gineering. g. ••A Atetexturedxtured bbearinbearingg susurfacrface acts ass a lublubricantricant ,reservoirreservoir,, sstoringtoring daandnd ddispens-ispens- ing ththee llubricantubricant directly taatt ththee ppotinintt of ccontactontact wherwheree iitt makes mmostost ssense.ense. 52 • JULY 2015 TRIBOLOGY & LUBRICATION TECHNOLOGY WWW.STLE.ORG surface: Leveraging both disciplines together can yield results neither can achieve alone. WHEN THE THEORY OF CONTACT MECHANICS WAS FIRST DEVELOPED IN 1882, lubricants were not factored into the equation at all. Experts say that may be due to the lack of powerful ana- lytical and numerical tools that necessitated simplicity.1 The omission of lubrication from contact mechanics theory was resolved four years later when Osborne Reynolds developed what is now known as the Reynolds Equation. It describes the pressure distribution in nearly any type of fluid film bearing. WWW.STLE.ORG TRIBOLOGY & LUBRICATION TECHNOLOGY JULY 2015 • 53 Even with that breakthrough, how- WHY IS IT THE STRIBECK CURVE?4 ever, it was decades later before -
Contact Mechanics of Adhesive Beams. Part I: Moderate Indentation. Arxiv:1707.07543V1
Contact mechanics of adhesive beams. Part I: Moderate indentation. V. S. Punati∗, I. Sharma and P. Wahi Mechanics & Applied Mathematics Group, Department of Mechanical Engineering, Indian Institute of Technology Kanpur, Kanpur, Uttar Pradesh, India - 208016. Abstract We investigate the contact of a rigid cylindrical punch with an adhesive beam mounted on flexible end supports. Adhesion is modeled through an adhesive zone model. The resulting Fredholm integral equation of the first kind is solved by a Galerkin projection method in terms of Chebyshev polynomials. Results are re- ported for several combinations of adhesive strengths, beam thickness, and support flexibilities characterized through torsional and vertical translational spring stiff- nesses. Special attention is paid to the important extreme cases of clamped and simply supported beams. The popular Johnson-Kendall-Roberts (JKR) model for adhesion is obtained as a limit of the adhesive zone model. Finally, we compare our predictions with preliminary experiments and also demonstrate the utility of our approach in modeling complex structural adhesives. Keywords: contact mechanics; adhesive beams; integral transforms. 1 Introduction Research in patterned adhesives is often motivated by the structures of natural adhe- sives, such as those present in the feet of gekkos; see e.g. Hiller (1976), and Arul and Ghatak (2008). In conventional adhesives, such as thin, sticky tapes, only the top and bottom surfaces are active. However, multiple surfaces may be activated with appropri- ate patterning. With more surfaces participating in the adhesion process the adhesives show increased hysteresis and, so, better performance. One example of a patterned ad- hesive is the structural adhesive shown in Fig. -
Contact Mechanics
International Journal of Solids and Structures 37 (2000) 29±43 www.elsevier.com/locate/ijsolstr Contact mechanics J.R. Barber a,*, M. Ciavarella b, 1 aDepartment of Mechanical Engineering and Applied Mechanics, University of Michigan, Ann Arbor, MI 48109-2125, USA bDepartment of Engineering Science, University of Oxford, Parks Road, Oxford, OX1 3PJ, UK Abstract Contact problems are central to Solid Mechanics, because contact is the principal method of applying loads to a deformable body and the resulting stress concentration is often the most critical point in the body. Contact is characterized by unilateral inequalities, describing the physical impossibility of tensile contact tractions (except under special circumstances) and of material interpenetration. Additional inequalities and/or non-linearities are introduced when friction laws are taken into account. These complex boundary conditions can lead to problems with existence and uniqueness of quasi-static solution and to lack of convergence of numerical algorithms. In frictional problems, there can also be lack of stability, leading to stick±slip motion and frictional vibrations. If the material is non-linear, the solution of contact problems is greatly complicated, but recent work has shown that indentation of a power-law material by a power law punch is self-similar, even in the presence of friction, so that the complete history of loading in such cases can be described by the (usually numerical) solution of a single problem. Real contacting surfaces are rough, leading to the concentration of contact in a cluster of microscopic actual contact areas. This aects the conduction of heat and electricity across the interface as well as the mechanical contact process. -
Introduction to Contact Mechanics
4 Anthony C. Fischer-Cripps Introduction to Contact Mechanics With 93 Figures Springer Contents Series Preface vii Preface ix List of Symbols xvii History xix Chapter 1. Mechanical Properties of Materials 1 1.1 Introduction 1 1.2 Elasticity 1 1.2.1 Forces between atoms 1 7.2.2 Hooke's law 2 1.2.3 Strain energy 4 1.2.4 Surface energy 4 1.2.5 Stress 5 1.2.6 Strain 10 1.2.7 Poisson's ratio 14 1.2.8 Linear elasticity (generalized Hooke's law) 14 1.2.9 2-D Plane stress, plane strain 16 1.2.10 Principal stresses 18 1.2.11 Equations of equilibrium and compatibility 23 1.2.12 Saint-Venant's principle 25 1.2.13 Hydrostatic stress and stress deviation 25 1.2.14 Visualizing stresses 26 1.3 Plasticity 27 1.3.1 Equations of plastic flow 27 1.4 Stress Failure Criteria 28 1.4.1 Tresca failure criterion 28 1.4.2 Von Mises failure criterion 29 References 30 Chapter 2. Linear Elastic Fracture Mechanics 31 2.1 Introduction 31 2.2 Stress Concentrations 31 ^cii Contents 2.3 Energy Balance Criterion 32 2.4 Linear Elastic Fracture Mechanics 37 2.4.1 Stress intensity factor 37 2.4.2 Crack tip plastic zone 40 2.4.3 Crack resistance 41 2.4.4 KIC, the critical value ofK, 41 2.4.5 Equivalence ofG and K. 42 2.5 Determining Stress Intensity Factors 43 2.5.7 Measuring stress intensity factors experimentally 43 2.5.2 Calculating stress intensity factors from prior stresses 44 2.5.3 Determining stress intensity factors using the finite-element method 46 References 48 Chapter 3. -
Contact Mechanics and Elements of Tribology 5Pt Foreword
Contact Mechanics and Elements of Tribology Foreword Vladislav A. Yastrebov MINES ParisTech, PSL Research University, Centre des Matériaux, CNRS UMR 7633, Evry, France @ Centre des Matériaux February 8, 2016 Outline Acquaintance Questionnaire Course content Historical remark Complexity Notations Questionnaire Please fill in the questionnaire Message to DMS students : Rank all suggested topics1 for your report in the order of decreasing attractiveness Before the lunch one topic will be assigned to everybody On Friday (12/02) you will have 10 minutes to present briefly your topic to other students If you are not a DMS student but would like to follow, you are welcome Basava, Andrei and Paolo will also present rapidly their research projects on 12/02 By Friday (19/02) you will need to send me your report on your topic ( 10 pages in Français/English) ≈ Criteria of evaluation : no plagiarism, scientifically sound report 1or suggest a different one but not related to your master project V.A. Yastrebov 3/10 Course content Lectures : 1 Motivation : industrial applications 2 Contact Mechanics I & II 3 Contact at small scales : surface roughness 4 Computational Contact Mechanics 5 Contact rheology & friction laws 6 Elements of tribology : friction, adhesion, wear 7 Wear and fretting (by Henry Proudhon) 8 Multiphysical problems in contact 9 Your presentations V.A. Yastrebov 4/10 Course content Lectures : 1 Motivation : industrial applications 2 Contact Mechanics I & II 3 Contact at small scales : surface roughness 4 Computational Contact Mechanics 5 Contact rheology & friction laws 6 Elements of tribology : friction, adhesion, wear 7 Wear and fretting (by Henry Proudhon) 8 Multiphysical problems in contact 9 Your presentations Practice : 1 Chalk and blackboard : Boussinesq, Cerruti, Flamant 2 Chalk and blackboard : Hertz contact 3 Computer : rough contact 4 Computer : frictionless and frictional cylindrical contact 5 Computer : elasto-plastic spherical indentation V.A. -
Mechanical Engineering Series
Mechanical Engineering Series Frederick F. Ling Editor-in-Chief Mechanical Engineering Series A.C. Fischer-Cripps, Introduction to Contact Mechanics, 2nd ed. W. Cheng and I. Finnie, Residual Stress Measurement and the Slitting Method J. Angeles, Fundamentals of Robotic Mechanical Systems: Theory Methods and Algorithms, 3rd ed. J. Angeles, Fundamentals of Robotic Mechanical Systems: Theory, Methods, and Algorithms, 2nd ed. P. Basu, C. Kefa, and L. Jestin, Boilers and Burners: Design and Theory J.M. Berthelot, Composite Materials: Mechanical Behavior and Structural Analysis I.J. Busch-Vishniac, Electromechanical Sensors and Actuators J. Chakrabarty, Applied Plasticity K.K. Choi and N.H. Kim, Structural Sensitivity Analysis and Optimization 1: Linear Systems K.K. Choi and N.H. Kim, Structural Sensitivity Analysis and Optimization 2: Nonlinear Systems and Applications G. Chryssolouris, Laser Machining: Theory and Practice V.N. Constantinescu, Laminar Viscous Flow G.A. Costello, Theory of Wire Rope, 2nd ed. K. Czolczynski, Rotordynamics of Gas-Lubricated Journal Bearing Systems M.S. Darlow, Balancing of High-Speed Machinery W.R. DeVries, Analysis of Material Removal Processes J.F. Doyle, Nonlinear Analysis of Thin-Walled Structures: Statics, Dynamics, and Stability J.F. Doyle, Wave Propagation in Structures: Spectral Analysis Using Fast Discrete Fourier Transforms, 2nd ed. P.A. Engel, Structural Analysis of Printed Circuit Board Systems A.C. Fischer-Cripps, Introduction to Contact Mechanics A.C. Fischer-Cripps, Nanoindentation, 2nd ed. (continued after index) Anthony C. Fischer-Cripps Introduction to Contact Mechanics Second Edition 1 3 Anthony C. Fischer-Cripps Fischer-Cripps Laboratories Pty Ltd. New South Wales, Australia Introduction to Contact Mechanics, Second Edition Library of Congress Control Number: 2006939506 ISBN 0-387-68187-6 e-ISBN 0-387-68188-4 ISBN 978-0-387-68187-0 e-ISBN 978-0-387-68188-7 Printed on acid-free paper.