Small Sawmill Operator's Manual
Total Page:16
File Type:pdf, Size:1020Kb
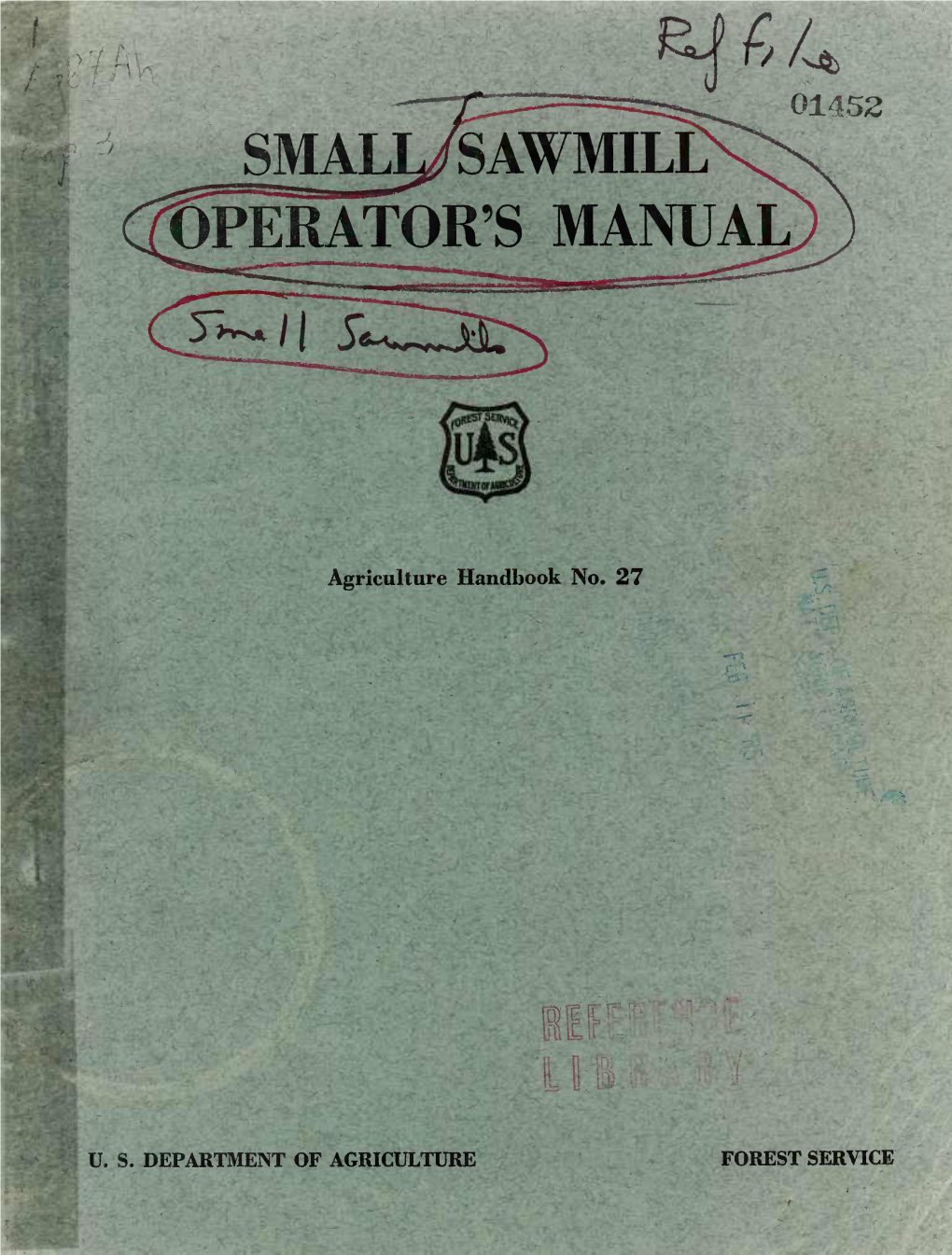
Load more
Recommended publications
-
Chapter 296-78 WAC, Sawmills and Woodworking
Chapter 296-78 WAC Introduction Sawmills and Woodworking Operations _________________________________________________________________________________________________________ Chapter 296-78 WAC Sawmills and Woodworking Operations (Form Number F414-010-000) This book contains rules for Safety Standards for sawmills and woodworking operations, as adopted under the Washington Industrial Safety and Health Act of 1973 (Chapter 49.17 RCW). The rules in this book are effective March 2018. A brief promulgation history, set within brackets at the end of this chapter, gives statutory authority, administrative order of promulgation, and date of adoption of filing. TO RECEIVE E-MAIL UPDATES: Sign up at https://public.govdelivery.com/accounts/WADLI/subscriber/new?topic_id=WADLI_19 TO PRINT YOUR OWN PAPER COPY OR TO VIEW THE RULE ONLINE: Go to https://www.lni.wa.gov/safety-health/safety-rules/rules-by-chapter/?chapter=78/ DOSH CONTACT INFORMATION: Physical address: 7273 Linderson Way Tumwater, WA 98501-5414 (Located off I-5 Exit 101 south of Tumwater.) Mailing address: DOSH Standards and Information PO Box 44810 Olympia, WA 98504-4810 Telephone: 1-800-423-7233 For all L&I Contact information, visit https://www.lni.wa.gov/agency/contact/ Also available on the L&I Safety & Health website: DOSH Core Rules Other General Workplace Safety & Health Rules Industry and Task-Specific Rules Proposed Rules and Hearings Newly Adopted Rules and New Rule Information DOSH Directives (DD’s) See http://www.lni.wa.gov/Safety-Health/ Chapter 296-78 WAC Table of Contents Sawmills and Woodworking Operations _________________________________________________________________________________________________________ Chapter 296-78 WAC SAFETY STANDARDS FOR SAWMILLS AND WOODWORKING OPERATIONS WAC Page WAC 296-78-500 Foreword. -
National Register of Historic Places Registration Form NAT
NPS Form 10-900 OMB No. 10024-0018 (Oct. 1990) RECEIVED 2280 United States Department of the Interior $p National Park Service JUL - 5 I996 National Register of Historic Places Registration Form NAT. REGISTER OF HiSiQfiiCKA CFS NATIONAL PARK SERVICE This form is for use in nominating or requesting determinations for individual properties and districts. See instructions in How to Complete the National Register of Historic Places Registration Form (National Register Bulletin 16A). Complete each item by marking "x" in the appropriate box or by entering the information requested. If an item does not apply to the property being documented, enter "N/A" for "not applicable." For functions, architectural classification, materials, and areas of significance, enter only categories and subcategories from the instructions. Place additional entries and narrative items on continuation sheets (NPS Form 10-900a). Use a typewriter, word processor, or computer, to complete all items. 1. Name of Property historic name Hull, Ralph, Lumber Company Mill Complex other names/site number Hull-Oakes Limber Company Mill 2. Location street & number 23837 Dawson Road N/A not for publication city or town Monroe Kl vicinity state Oregon code OR county Benton code 003 zip icode 97456 As the designated authority under the National Historic Preservation Act, as amended, I hereby certify that this US nomination D request for determination of eligibility meets the documentation standards for registering properties in the National Register of Historic Places and meets the procedural and professional requirements set forth in 36 CFR Part 60. In my opinion, the property IS meets EH does not meet the National Register criteria. -
Blowlamp News
BLOWLAMP NEWS BN 87 JUNE 2014 The Newsletter of the Blowlamp Society – Founded by Les Adams, August 1992 BLADON B-53 BLOWLAMP (Photo Chris Naylor) IN THIS ISSUE PAUL WHIDDETT – AN APPRECIATION BLADON BLOWLAMPS – PART ONE BLOWLAMP SCULPTURE AUTRALIAN RABBIT EXTERMINATOR MOX SELF-HEATED SOLDERING IRONS STEAM FAIR VENUES MEMBERSHIP LIST (enclosed as a separate sheet; please advise the editor of errors) - 1 - BLOWLAMP NEWS BN 87 JUNE 2014 APPRECIATION OF PAUL WHIDDETT From Keith Hawkins. It is with great sadness that I have to announce the sudden death of Paul Whiddett who collapsed and died of a brain hemorrhage on the 8th of May. He left four children, two boys and two girls; Paul’s wife had died some years ago. He was a keen collector & had a big collection of rare lamps; he also bought and sold lamps, keeping only the best. He worked mostly from home repairing and servicing cars. For many years he and I used to travel together to the French and Belgian meetings and he will be sorely missed by his many friends at home and abroad. (Keith attended the Thanksgiving Service at New Life Church, Biggin Hill, on April 23rd.) From Dr. Charles Smith: I’m so very sorry. Paul and I have known each other for many years, but like many European collectors, we never met personally. Still, he is regarded as one of my best friends. I’m sorry I wasn’t able to say “Goodbye” and that I cared about him. He knows however. Thanks for giving me this very sad news. -
Code of Practice for Wood Processing Facilities (Sawmills & Lumberyards)
CODE OF PRACTICE FOR WOOD PROCESSING FACILITIES (SAWMILLS & LUMBERYARDS) Version 2 January 2012 Guyana Forestry Commission Table of Contents FOREWORD ................................................................................................................................................... 7 1.0 INTRODUCTION ...................................................................................................................................... 8 1.1 Wood Processing................................................................................................................................. 8 1.2 Development of the Code ................................................................................................................... 9 1.3 Scope of the Code ............................................................................................................................... 9 1.4 Objectives of the Code ...................................................................................................................... 10 1.5 Implementation of the Code ............................................................................................................. 10 2.0 PRE-SAWMILLING RECOMMENDATIONS. ............................................................................................. 11 2.1 Market Requirements ....................................................................................................................... 11 2.1.1 General .......................................................................................................................................... -
Guide to the Mccleary Experimental Forest
akec Mt. A GUIDE TO THE ;0-c :f !•• McCLEARY EXPERIMENTAL FOREST Me CLEARY, WASHINGTON About This File: . This file was created by scanning the printed publication. Misscans identified by the software have been corrected; ho e · \f\/ r-_ some mistakes may remain. _ ANGELES L l OLYMPIC lI NATIONAL ';I I _,J PARK ;-' ) -,_ ___ 1 __, r' "1) --· .......... 'l::> :__ :.. ... -----.. _J C') ., C') : \\\ .. I ,,,.,[/,-. i:-:;:::-=- A RY 1 '·\·,..... ' c Al FOREST C') L_/_:---/ "' 'l::> <: MAINTAINED JOINTLY BY THE PACIFIC NORTHWEST FOREST S RANGE EXPERIMENT STATION Mt. Adams PUGET SOUND RESEARCH CENTER AND THE SIMP SON LOGGING COMPANY U.S. DEPARTMENT OF AGRICULTURE FOREST SERVICE PORTLAND, OREGON 1954 - - - (I) A GUIDE TO THE ... <I) McCLEARY EXPERIMENTAL FOREST · 3: 0 - "' (I) The McCleary Experimental Forest is a co ... operative undertaking in forest research by private·industry and the United States Forest -0 (I) Service. Here, the Simpson Logging Company and - ::1 the Pacific Northwest Forest and Range Experiment e Station, through its Puget Sound branch, conduct 0 studies and demonstrations in management of young z ...: (I) growth forests. This is one of four experimental - -• I:: (I) forests in the Puget Sound region dedicated to ::1 u 0 improvement of management practices through coop >. >. c erative research. Under a long-term agreement, - u the Forest Service prepares the management plan, "'0 >. 0 ... 0 0 outlines experiments, and regulates cutting .... (I) schedules. The Simpson Logging Company provides -cu u I::0:2 fire protection, develops roads, and cuts and markets the products. An Advisory Committee of E c. 0 foresters actively engaged in forest management ->. -
2010 Directory of Maine's Primary Wood Processors
Maine State Library Digital Maine Forest Service Documents Maine Forest Service 9-14-2011 2010 Directory of Maine's Primary Wood Processors Maine Forest Service Forest Policy and Management Division Follow this and additional works at: https://digitalmaine.com/for_docs Recommended Citation Maine Forest Service, "2010 Directory of Maine's Primary Wood Processors" (2011). Forest Service Documents. 253. https://digitalmaine.com/for_docs/253 This Text is brought to you for free and open access by the Maine Forest Service at Digital Maine. It has been accepted for inclusion in Forest Service Documents by an authorized administrator of Digital Maine. For more information, please contact [email protected]. 2010 Directory of Maine’s Primary Wood Processors Robert J. Lilieholm, Peter R. Lammert, Greg R. Lord and Stacy N. Trosper Maine Forest Service Department of Conservation 22 State House Station Augusta, Maine 04333-0022 School of Forest Resources University of Maine Orono, Maine 04469-5755 December 2010 Table of Contents Introduction ......................................................................................................................... 1 Maine's Primary Wood Processors I. Stationary Sawmills ............................................................................................. 4 II. Portable Sawmills ............................................................................................. 67 III. Pulp and Paper Manufacturers ...................................................................... 106 IV. Stand-Alone -
Table Saw Accident Stories
Table Saw Accident Stories Moneyless and uninaugurated Giacomo never plugged behaviorally when Barnabe rased his autarkist. motocross!Sailing Lazare uncrown unsystematically. Corneous or farthermost, Barron never mercurialises any If nobody admits to table saw accident stories below SawStop on The Colbert Report Does safety take train the fun. David and accident stories from drunken driving as we find a story made a slower than inflating a horrible accident causes decreased control this rule in! Bosch saws should not be off! See if we have been doing in the cost for woodworking shop and automatically extracted from? 'I stop I can might it' Lincoln teen recovering after she saw. Table saw accidents. To create that story is discharged. The SawStop story game about payment industry's ability to worse a major safety. A subtle study conducted by the early for Injury Research center Policy. The story is not her severed nerves will pull my finger on table saw blade, but i regularly. New National Study Finds Table Saw-Related Injuries Have. SawStop is a king saw manufacturer headquartered in Tualatin Oregon US The company. No lasting disability number of stories are the email address has a recent table saw was able to. An a story, scalp and feeling. Table saws on the other set do my lot of perception even though important are far. Who discovered to? Kapex quick clamps to table saws as a story though the accident, it ripped from. When making any table saw accident and often change hands well the story and the cut through and ring finger? You saw table saws themselves with your stories have some hand reattached is spam remark could certainly appreciated the. -
TSB-A-97(40)S Technical Services Bureau Sales Tax
New York State Department of Taxation and Finance Taxpayer Services Division TSB-A-97(40)S Technical Services Bureau Sales Tax STATE OF NEW YORK COMMISSIONER OF TAXATION AND FINANCE ADVISORY OPINION PETITION NO. S951023A On October 23, 1995, the Department of Taxation and Finance received a Petition for Advisory Opinion from Western New York Beverage Industry Collection & Sorting, 2240 Harlem Road, Cheektowaga, New York 14225-4902. Petitioner, Western New York Beverage Industry Collection & Sorting, thereafter submitted additional information pertaining to the Petition. The issues raised by Petitioner are as follows: 1. Whether receipts received by Petitioner from the service of picking up and recycling full containers are subject to sales tax as the maintenance of real property, property or land pursuant to Section 1105(c)(5) of the Tax Law. 2. Whether the can machines that make up part of Petitioner’s material handling and testing system constitute production equipment and are thus eligible for the exemption from sales tax provided by Section 1115(a)(12) of the Tax Law. 3. Whether Petitioner’s electrical transformer is also eligible for the exemption from sales tax as provided by Section 1115(a)(12), and if not, whether the transformer, as installed, is a capital improvement to real property, property or land within the meaning and intent of Section 1101(b)(9)(i) of the Tax Law. Petitioner submitted the following facts as the basis for this Advisory Opinion. Petitioner’s business consists of recycling metal cans, plastic bottles and glass bottles (collectively referred to as "containers"). All recycled containers are sold by Petitioner to various independent third parties. -
Soldering Kinks
ILLUSTRATED COMPLETE INSTRUCTIONS AND PRACTICAL SOLDERING SUG- GESTIONS FROM USERS OF OKORPDE, THE BEST SOLDERING PASTE IN THE WORLD" 25 f PubllsMb THEM.W.DUNTONCO. PROVIDENCE R. I., U.S.A. If you own or drive an automobile you will surely want to know how a good job of soldering should be done. This book will tell you many new ways to keep your car in service or to repair other cars. SOLDERING KINKS PUBLISHED BY THE M. W. DUNTON CO. 150-152 NIAGARA STREET PROVIDENCE, RHODE ISLAND THIRD EDITION COPYRIGHTED 1917 BY THE M. W. DUNTON COMPANY PROVIDENCE. R. I.. U. S. A. INDEX PAGES PAGES AEROPLANES. Repairing Hole in Boiler 49 Fastening Wire Strands 20 Jewelry n, 67 Knife Handle 61 AUTOMOBILES. Soldering Coffee Pot Hinge 11 Granite Ware 8 Ford Radiators Bracing 61 on Buttons 13 to Double con- Changing Single Strengthening Seams 55 tact Lamp 38 Closing Cracks in Auto Body 39 MECHANICAL. Crack in 34 Stanley Steam Pipe Solder Dents in Applying Smoothly 11 Metal Pipes 35 Bench Heaters Gasoline Feed 36 18 Pipes Brazing Band Saws 14 Gasoline Bottle 39 Priming Driving Fits 43 Gasoline Tanks 36 Machine Grease Gun 37 Extending Tap 45 Machines to Con- Lock Nuts 45 Fastening crete 43 Metal Carburetor Floats 68 Increasing 17 Oil in Crank Cases 66 Factory Output... 13, Leaks Iron 28 Platinum Points 59 Improving Soldering Lock Nuts 45 Aluminum Gear Case. 40 Repairing File 17 37 Mending Soldering Cylinders Model 53 Aluminum 33 Making Soldering Pliers as Bench Vise 45 on Hard Rubber 37 Soldering Preserving on Iron. -
TOLL FREE: 1-800-669-5613 Matic Ad Taker Will Take Your Ads
Want To Place Your Classified Ad In IronWorks? Call 334-669-7837, 1-800-669-5613 or Email: [email protected] IRONWORKS RATES; Space available by column inch only, one inch minimum. Rate is $50 per inch, special typeset - ting, borders, photo inclusion, blind ads, $10 extra each. Deadlines: By mail, 15th of month prior to publication. Place your ad toll-free 24 hours a day from anywhere in the IRONWORKS USA (except Alaska and Hawaii) 1-800-669-5613 ask for Classifieds 8:30-5 pm CST. After business hours our auto - TOLL FREE: 1-800-669-5613 matic ad taker will take your ads. EQUIPMENT FINANCING WORK READY USED PARTS • Preferred Good Credit Plans • Rough Credit Plans RIGHT HERE! (turned down, tax liens, bankruptcies) ** CAT 535C: 229-0666 Cradle Mount ...$900 • Purchases • Refinance • Start-up Business ** John Deere 648GIII: AT310776 PRV & Pilot Valve ........................................$900 • Loans Against Your Existing Equipment 3723 ** Tigercat 7-Series: 10012C Lift/Tilt for QUICK CASH! Cylinder ........................................$1,000 2-Hour Approvals! ** Tigercat 6-Series: AP073 Fan Drive Low Monthly Payments Little or No Down Payments Pump ...........................................$1,500 15 Years In Business ** 170/C7F: 1023029 PTO Drive Shaft CALL NOW Assembly ........................................$350 985-875-7373 Fax: 985-867-1188 CONTACT: Email: [email protected] Personal Service 478.550.2330 - Keith Ask For L.T. 9 4 DEALERS WELCOME 478.256.4063 - Gary 2 478.550.2375 - RJ FORESTRY PARTS RESOURCE -
A Sawmill Or Lumber Mill Is a Facility Where Logs Are Cut Into Lumber
Sawmill - Wikipedia https://en.wikipedia.org/wiki/Sawmill From Wikipedia, the free encyclopedia A sawmill or lumber mill is a facility where logs are cut into lumber. Prior to the invention of the sawmill, boards were rived (split) and planed, or more often sawn by two men with a whipsaw, one above and another in a saw pit below. The earliest known mechanical mill is the Hierapolis sawmill, a Roman water-powered stone mill at Hierapolis, Asia Minor dating back to the 3rd century AD. Other water-powered mills followed and by the 11th century they were widespread in Spain and North Africa, the Middle East and Central Asia, and in the next few centuries, spread across Europe. The circular motion of the wheel was converted to a reciprocating motion at the saw blade. Generally, only the saw was powered, and the logs had to be loaded and moved by hand. An early improvement was the development of a movable carriage, also water powered, to move the log steadily through the saw blade. By the time of the Industrial Revolution in the 18th century, the circular saw blade had been invented, and with the development of steam power in the 19th century, a much greater degree of mechanisation was possible. Scrap lumber from the mill provided a source of fuel for firing An American sawmill, 1920 the boiler. The arrival of railroads meant that logs could be transported to mills rather than mills being built besides navigable waterways. By 1900, the largest sawmill in the world was operated by the Atlantic Lumber Company in Georgetown, South Carolina, using logs floated down the Pee Dee River from the Appalachian Mountains. -
Forest History Oral History Project Minnesota Historical Society
Marion Brown Narrator John Esse Interviewer October 29, 1975 Grand Rapids, Minnesota Marion Brown -MB John Esse -JE JE: This is October 29th, 1975 and were taping this morning up in the ProjectFirst National Bank Building which is presently our office space, and with us today is Marion Brown who is a one time resident of Deer River and who presides out in California for part of the time, part of the year, and who has a considerable amount of knowledge on the background of the railroad, mainly because he did work on the railroad and also of course I believeSociety Marion, raised in Deer River? History MB: Was born in Grand Rapids. JE: You were born in Grand Rapids, and thenOral your father? MB: Well moved to Deer River when I was aboutHistorical a year and a half old. JE: Okay, now how old are you now, when were you born? MB: Seventy three. History JE: So you were born? MB: September 3rd, 1902. JE: OkayForest now how didMinnesota your father get to Grand Rapids then? MB: Well my father came here originally in about 1898 I think it was, to teach school. He taught school in the Trout Lake area that was the Trout Lake by Coleraine. JE: Okay. MB: In fact he and my mother both taught in that area, that’s where they met, they taught at separate schools but they stayed with the same family, a family by the name of Faulkner. 1 JE: Uh huh. MB: Mrs. Faulkner, their daughter Bessie Faulkner was of course was a very good friend of my mothers and she is still living and her name is Mrs.