7Th International Symposium on Launcher Technologies
Total Page:16
File Type:pdf, Size:1020Kb
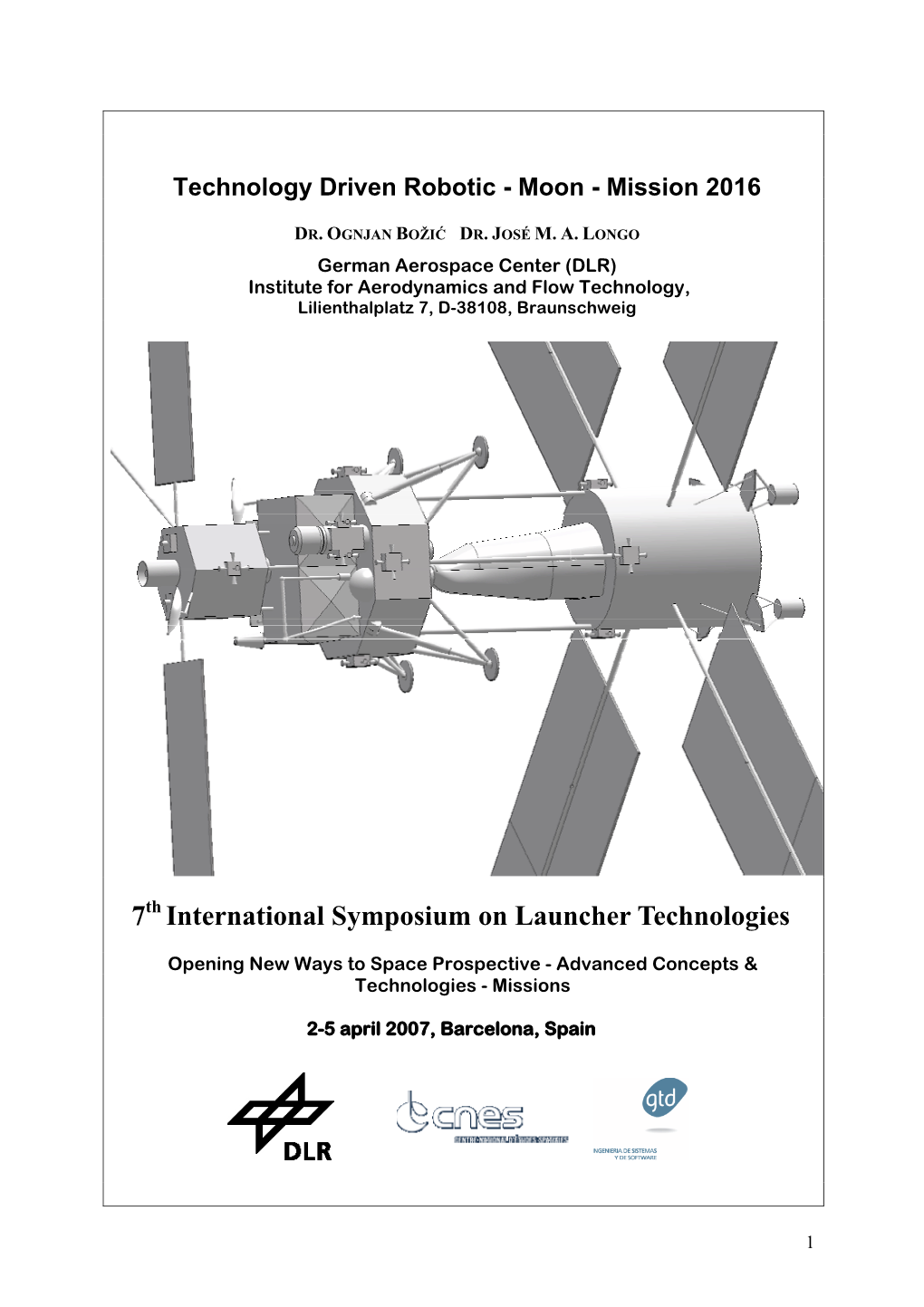
Load more
Recommended publications
-
Limitations of Spacecraft Redundancy: a Case Study Analysis
44th International Conference on Environmental Systems Paper Number 13-17 July 2014, Tucson, Arizona Limitations of Spacecraft Redundancy: A Case Study Analysis Robert P. Ocampo1 University of Colorado Boulder, Boulder, CO, 80309 Redundancy can increase spacecraft safety by providing the crew or ground with multiple means of achieving a given function. However, redundancy can also decrease spacecraft safety by 1) adding additional failure modes to the system, 2) increasing design “opaqueness”, 3) encouraging operational risk, and 4) masking or “normalizing” design flaws. Two Loss of Crew (LOC) events—Soyuz 11 and Challenger STS 51-L—are presented as examples of these limitations. Together, these case studies suggest that redundancy is not necessarily a fail-safe means of improving spacecraft safety. I. Introduction A redundant system is one that can achieve its intended function through multiple independent pathways or Aelements 1,2. In crewed spacecraft, redundancy is typically applied to systems that are critical for safety and/or mission success3,4. Since no piece of hardware can be made perfectly reliable, redundancy—in theory—allows for the benign (e.g. non-catastrophic) failure of critical elements. Redundant elements can be 1) similar or dissimilar to each other, 2) activated automatically (“hot spare”) or manually (“cold spare”), and 3) located together or separated geographically5-7. U.S. spacecraft have employed redundancy on virtually all levels of spacecraft design, from component to subsystem7,8. Redundancy has a successful history of precluding critical and catastrophic failures during human spaceflight. A review of NASA mission reports, from Mercury to Space Shuttle, indicates that redundancy has saved the crew or extended the mission over 160 times, or roughly once per flight9. -
Reentry Motion and Aerodynamics of the MUSES-C Sample Return Capsule
Trans. Japan Soc. Aero. Space Sci. Vol. 51, No. 172, pp. 65–70, 2008 Reentry Motion and Aerodynamics of the MUSES-C Sample Return Capsule By Nobuaki ISHII,1Þ Tetsuya YAMADA,1Þ Koju HIRAKI2Þ and Yoshifumi INATANI1Þ 1ÞThe Institute of Space and Astronautical Science, JAXA, Sagamihara, Japan 2ÞKyushu Institute of Technology, Kita-Kyushu, Japan (Received June 21st, 2006) The Hayabusa spacecraft (MUSES-C) carries a small capsule for bringing asteroid samples back to the earth. The initial spin rate of the reentry capsule together with the flight path angle of the reentry trajectory is a key parameter for the aerodynamic motion during the reentry flight. The initial spin rate is given by the spin-release mechanism attached between the capsule and the mother spacecraft, and the flight path angle can be modified by adjusting the earth approach orbit. To determine the desired values of both parameters, the attitude motion during atmospheric flight must be clarified, and angles of attack at the maximum dynamic pressure and the parachute deployment must be assessed. In previous studies, to characterize the aerodynamic effects of the reentry capsule, several wind-tunnel tests were conducted using the ISAS high-speed flow test facilities. In addition to the ground test data, the aerodynamic properties in hypersonic flows were analyzed numerically. Moreover, these data were made more accurate using the results of balloon drop tests. This paper summarized the aerodynamic properties of the reentry capsule and simulates the attitude motion of the full- configuration capsule during atmospheric flight in three dimensions with six degrees of freedom. The results show the best conditions for the initial spin rates and flight path angles of the reentry trajectory. -
Los Motores Aeroespaciales, A-Z
Sponsored by L’Aeroteca - BARCELONA ISBN 978-84-608-7523-9 < aeroteca.com > Depósito Legal B 9066-2016 Título: Los Motores Aeroespaciales A-Z. © Parte/Vers: 1/12 Página: 1 Autor: Ricardo Miguel Vidal Edición 2018-V12 = Rev. 01 Los Motores Aeroespaciales, A-Z (The Aerospace En- gines, A-Z) Versión 12 2018 por Ricardo Miguel Vidal * * * -MOTOR: Máquina que transforma en movimiento la energía que recibe. (sea química, eléctrica, vapor...) Sponsored by L’Aeroteca - BARCELONA ISBN 978-84-608-7523-9 Este facsímil es < aeroteca.com > Depósito Legal B 9066-2016 ORIGINAL si la Título: Los Motores Aeroespaciales A-Z. © página anterior tiene Parte/Vers: 1/12 Página: 2 el sello con tinta Autor: Ricardo Miguel Vidal VERDE Edición: 2018-V12 = Rev. 01 Presentación de la edición 2018-V12 (Incluye todas las anteriores versiones y sus Apéndices) La edición 2003 era una publicación en partes que se archiva en Binders por el propio lector (2,3,4 anillas, etc), anchos o estrechos y del color que desease durante el acopio parcial de la edición. Se entregaba por grupos de hojas impresas a una cara (edición 2003), a incluir en los Binders (archivadores). Cada hoja era sustituíble en el futuro si aparecía una nueva misma hoja ampliada o corregida. Este sistema de anillas admitia nuevas páginas con información adicional. Una hoja con adhesivos para portada y lomo identifi caba cada volumen provisional. Las tapas defi nitivas fueron metálicas, y se entregaraban con el 4 º volumen. O con la publicación completa desde el año 2005 en adelante. -Las Publicaciones -parcial y completa- están protegidas legalmente y mediante un sello de tinta especial color VERDE se identifi can los originales. -
A Breath of Fresh Air: Air-Scooping Electric Propulsion in Very Low Earth Orbit
A BREATH OF FRESH AIR: AIR-SCOOPING ELECTRIC PROPULSION IN VERY LOW EARTH ORBIT Rostislav Spektor and Karen L. Jones Air-scooping electric propulsion (ASEP) is a game-changing concept that extends the lifetime of very low Earth orbit (VLEO) satellites by providing periodic reboosting to maintain orbital altitudes. The ASEP concept consists of a solar array-powered space vehicle augmented with electric propulsion (EP) while utilizing ambient air as a propellant. First proposed in the 1960s, ASEP has attracted increased interest and research funding during the past decade. ASEP technology is designed to maintain lower orbital altitudes, which could reduce latency for a communication satellite or increase resolution for a remote sensing satellite. Furthermore, an ASEP space vehicle that stores excess gas in its fuel tank can serve as a reusable space tug, reducing the need for high-power chemical boosters that directly insert satellites into their final orbit. Air-breathing propulsion can only work within a narrow range of operational altitudes, where air molecules exist in sufficient abundance to provide propellant for the thruster but where the density of these molecules does not cause excessive drag on the vehicle. Technical hurdles remain, such as how to optimize the air-scoop design and electric propulsion system. Also, the corrosive VLEO atmosphere poses unique challenges for material durability. Despite these difficulties, both commercial and government researchers are making progress. Although ASEP technology is still immature, it is on the cusp of transitioning between research and development and demonstration phases. This paper describes the technical challenges, innovation leaders, and potential market evolution as satellite operators seek ways to improve performance and endurance. -
IUS/TUG ORBITAL OPERATIONS and MISSION SUPPORT STUDY FINAL REPORT
https://ntrs.nasa.gov/search.jsp?R=19750016720 2020-03-22T21:57:01+00:00Z Prepared for the MAY, 1975 GEORGE C MARSHALL SPACE FLIGHT CENTER Contract No NAS8-31009 Huntsville, Alabama IBM No 75W-00072 IUS/TUG ORBITAL OPERATIONS and MISSION SUPPORT STUDY FINAL REPORT Vol V of V - Cost Estimates (NASA-CR-143857) TUS/TUG ORBITAL OPEFATIONS N75-24792 AND M-ISSION SUPPORT STUDY. VOLUME 5: COST ESTI ATES Final Report (Internattonal Business Machines Corp.) 184 p HC $7.00 Unclas CSCL 22A G3/13 26227 Prepared for the MAY, 1975 GEORGE C MARSHALL SPACE FLIGHT CENTER Contract No NAS8-31009 Huntsville, Alabama IBM No 75W-00072 IUS/TUG ORBITAL OPERATIONS and MISSION SUPPORT STUDY FINAL REPORT Vol V of V - Cost Estimates Classification and Content Approval - '- Data Manager Approval Z2 Program Office Approval zC7 !4 PHILCO 490 Phico Fcrd Corporation Federal Systems Division, Space Systems/Huntsville, AlabmaWestr eopme Laorories son FOREWORD This final report of the IUS/Tug Orbital Operations and Mission Study was prepared for the National Aeronautics and Space Administration, George C Marshall Space Flight Center by the IBM Corporation in accordance with Contract NAS8-31009 The study effort described herein was conducted under the direction of NASA Contract Officer's Representative (COR), Mr. Sidney P Saucier This report was prepared by the IBM Corporation, Federal Systems Division, Huntsville, Alabama, under the direction of Mr Roy E Day, IBM Study Manager Technical support was provided to IBM by the Philco-Ford Corporation, Western Development Laboratories Division, Palo Alto, California, under the direction of Dr W E Waters, Philco-Ford Study Manager The study results were developed during the period from dune, 1974, through February, 1975, with the final report being distributed in May, 1975. -
The Annual Compendium of Commercial Space Transportation: 2017
Federal Aviation Administration The Annual Compendium of Commercial Space Transportation: 2017 January 2017 Annual Compendium of Commercial Space Transportation: 2017 i Contents About the FAA Office of Commercial Space Transportation The Federal Aviation Administration’s Office of Commercial Space Transportation (FAA AST) licenses and regulates U.S. commercial space launch and reentry activity, as well as the operation of non-federal launch and reentry sites, as authorized by Executive Order 12465 and Title 51 United States Code, Subtitle V, Chapter 509 (formerly the Commercial Space Launch Act). FAA AST’s mission is to ensure public health and safety and the safety of property while protecting the national security and foreign policy interests of the United States during commercial launch and reentry operations. In addition, FAA AST is directed to encourage, facilitate, and promote commercial space launches and reentries. Additional information concerning commercial space transportation can be found on FAA AST’s website: http://www.faa.gov/go/ast Cover art: Phil Smith, The Tauri Group (2017) Publication produced for FAA AST by The Tauri Group under contract. NOTICE Use of trade names or names of manufacturers in this document does not constitute an official endorsement of such products or manufacturers, either expressed or implied, by the Federal Aviation Administration. ii Annual Compendium of Commercial Space Transportation: 2017 GENERAL CONTENTS Executive Summary 1 Introduction 5 Launch Vehicles 9 Launch and Reentry Sites 21 Payloads 35 2016 Launch Events 39 2017 Annual Commercial Space Transportation Forecast 45 Space Transportation Law and Policy 83 Appendices 89 Orbital Launch Vehicle Fact Sheets 100 iii Contents DETAILED CONTENTS EXECUTIVE SUMMARY . -
George C. Marshall Space Flight Center Malshall Space Flight Center, Alabama
NASA TECHNICAL MEMORANDUM NASA TM X-53973 SPACE FLIGHT EVOLUTION By Georg von Tiesenhausen and Terry H. Sharpe Advanced Systems Analysis Office June 30,1970 NASA George C. Marshall Space Flight Center Malshall Space Flight Center, Alabama MSFC - Form 3190 (September 1968) j NASA TM X-53973 I [. TITLE AND SUBTITLE 5. REPORT DATE June 30,1970 Space Flight Evolution 6. PERFORMlNG ORGANIZATION CODE PD-SA 7. AUTHOR(S) 8. PERFORMING ORGANIZATION REPORT # Georg von Tiesenhausen and Terry H. Sharpe I 3. PERFORMlNG ORGANIZATION NAME AND ADDRESS lo. WORK UNIT, NO. Advanced Systems Analysis Office Program Development 1 1. CONTRACT OR GRANT NO. Marshall Space Flight Center, Alabama 35812 13. TYPE OF REPORT & PERIOD COVEREC 2. SPONSORING AGENCY NAME AND ADDRESS Technical Memorandum 14. SPONSORING AGENCY CODE I 15. SUPPLEMENTARY NOTES 16. ABSTRACT This report describes a possible comprehensive path of future, space flight evolution. The material in part originated from earlier NASA efforts to defme a space program in which earth orbital, lunar, and planetary programs are integrated. The material presented is not related to specific time schedules but provides an evolutionary sequence. The concepts of commonality of hardware and reusability of systems are introduced as keys to a low cost approach to space flight. The verbal descriptions are complemented by graphic interpretations in order to convey a more vivid impression of the concepts and ideas which make upthis program. 17. KEY WORDS 18. DISTRIBUTION STATEMENT STAR Announcement Advanced Systems Analysis Office 19. SECURITY CLASSIF. (of this rePmt> (20. SECURITY CLA ;IF. (of this page) 121. NO. OF PAGES 122. -
Technical Challenges and Study on Guided Reentry Flight for Capsule
21 JSTS Vol. 27, No. 2 30°and vertical velocity (descending velocity) of 10 m/s, which are nominal conditions for full-scale HRV water landing, were below 10g in the axial Z direction. At this condition, simulation and test Technical Challenges and Study on results showed good agreement. Test accelerometer results at pitch angles below 30° were unreadable or too high, and image analysis results were low compared with simulation results. The test model Guided Reentry Flight for Capsule Spacecraft and/or measurement methods need to be improved for future testing. Trends in maximum acceleration 1) 1) 1) 1) to pitch angle, vertical velocity and horizontal velocity were observed. Shuichi MATSUMOTO , Yoshinori KONDOH , Takane IMADA and Naoki SATO As described in section two, this paper presents the first phase of our research, which is to 1) estimate the magnitude of impact to the vehicle during water landing. In the future, we will also Japan Aerospace Exploration Agency (JAXA), 2-1-1, Sengen, Tsukuba, Ibaraki, 305-8505, Japan evaluate the impact during land landing, investigate the characteristics of impact TEL / FAX: +81-50-3362-7281 / +81-29-868-5969 transmission/attenuation to the vehicle and assess the load to the human body. We would like to progress this research, referring the research of not only manned space vehicle but also automobile crash, etc. ABSTRACT Previously-realized Japanese capsule spacecraft, OREX (Orbital Re-entry EXperiment), USERS ACKNOWLEDGMENTS capsule, and HAYABUSA reentry capsule, were all ballistic reentry capsules, which flew without any The authors express their great appreciation to Ms. Nozaki who designed and manufactured the guidance during reentry and had large splashdown areas. -
INTRODUCTION This Study of Reentry Vehicle (RV)
INTRODUCTION This study of Reentry Vehicle (RV) systems and their associated operations was conducted for the Department of Transportation/Office of Commercial Space Transportation. The purpose of the study was to investigate and present an overview of reentry vehicle systems and to identify differences in mission requirements and operations. This includes reentry vehicle system background, system design considerations, description of past/present/future reentry systems, and hazards associated with reentry vehicles that attain orbit, reenter, and are recovered. A general literature search that included the OCST data base, NASA, Air Force, and other technical libraries and personal contact with various government or private industry organizations knowledgeable in reentry system vehicles was performed. A reference page is provided at the end of this report. A history of early manned reentry vehicle launches is shown in Appendix I. A listing of some of the agencies and companies found to be most knowledgeable in the reentry vehicle area is provided in Appendix II. The following sections provide more detailed information on reentry system vehicles. A. Background - The development of reentry vehicles began in the late 1950's due to the need for Department of Defense and Central Intelligence Agency photo reconnaissance of Soviet ICBM sites. NASA has also been involved in the use of reentry vehicles since the early 1960's, including manned space programs Mercury, Gemini and Apollo. The following sections describe the evolution of reentry system development in the United States and foreign countries: 1. Discoverer1 - The Discoverer program was of major importance because it provided a vehicle for testing orbital maneuvering capability and reentry techniques and it played a large role in enabling the first United States manned space flights to be conducted in Project Mercury. -
Date. Projeed Future NASA Programs Planned for the 1970'S Are Discussed Under the Headings Skylab, Space Shuttle, and Space Station
DOCURENT RESUME ED 050 993 SE 011 364 AUTHOR Froehlich, Walter TITLE Man in Space, Space in the Seventies. 7MSTITUTION National Aeronautics and Space Administration, Washington, D.C. REPORT NO EP-B1 PUB DATE Jan 71 NOTE 31p. AVAILABLE FROM Superintendent of Documents, U.S. Government Printing Office, Washington, D.C. 20402 ($1.00) . EDRS PRICE EDRS Price MF-$0.35 HC riot Available from EDRS. DESCRIPTORS Aerospace Technology, *Program rescriptions, *Resource Materials, *Space, *State Agencies IDENTIFIERS National Aeronautics and Space Administration ABSTRACT Included is a summary of the Apollo lunar program to date. Projeed future NASA programs planned for the 1970's are discussed under the headings Skylab, Space Shuttle, and Space Station. Possibilities for the 1980's are outlined in the final section. (Author/AL) JUN 2 1 U.S. DEPARTMENT OF HEALTH, EDUCATION . " & WELFARE OFFICE OF EDUCATION THIS DOCUMENT HAS SEEN REPRODUCED EXACTLY AS RECEIVED FROM THE PERSON OR ORGANIZATION ORIGINATING IT. POINTS OF VIEW OR OPINIONS STATED DO NOT NECES SARILY REPRESENT OFFICIAL OFFICE OF EOU MAN IN SPACE CATION POSITION OR POLICY Space In The Seventies Ilk National Aeronautics and Space Administration SPACE IN THE SEVENTIES Man has walked on the Moon, made scientific observations there, and brought back to Earth samples of the lunar surface. Unmanned scientific spacecraft have probed for facts about matter, radiation and magnetism in space, and have collected data relating to the Moon, Venus, Mars, the Sun and some of the stars, and reported their findings to ground stations on Earth. Spacecraft have been put into orbit around the Earth as weather observation stations, as communications relay stations for a world-wide telephone and television network, and as aids to navigation, In addition, the space program has accelerated the advance of technology for science and industry, contributing many new ideas, processes and materials. -
IAA Situation Report on Space Debris - 2016
IAA Situation Report on Space Debris - 2016 Editors: Christophe Bonnal Darren S. McKnight International A cadem y of A stronautics Notice: The cosmic study or position paper that is the subject of this report was approved by the Board of Trustees of the International Academy of Astronautics (IAA). Any opinions, findings, conclusions, or recommendations expressed in this report are those of the authors and do not necessarily reflect the views of the sponsoring or funding organizations. For more information about the International Academy of Astronautics, visit the IAA home page at www.iaaweb.org. Copyright 2017 by the International Academy of Astronautics. All rights reserved. The International Academy of Astronautics (IAA), an independent nongovernmental organization recognized by the United Nations, was founded in 1960. The purposes of the IAA are to foster the development of astronautics for peaceful purposes, to recognize individuals who have distinguished themselves in areas related to astronautics, and to provide a program through which the membership can contribute to international endeavours and cooperation in the advancement of aerospace activities. © International Academy of Astronautics (IAA) May 2017. This publication is protected by copyright. The information it contains cannot be reproduced without written authorization. Title: IAA Situation Report on Space Debris - 2016 Editors: Christophe Bonnal, Darren S. McKnight Printing of this Study was sponsored by CNES International Academy of Astronautics 6 rue Galilée, Po Box 1268-16, 75766 Paris Cedex 16, France www.iaaweb.org ISBN/EAN IAA : 978-2-917761-56-4 Cover Illustration: NASA IAA Situation Report on Space Debris - 2016 Editors Christophe Bonnal Darren S. -
Human Spaceflight
Human Spaceflight Space System Design, MAE 342, Princeton University Robert Stengel • Historical concepts and mis-concepts • Manned spacecraft and space stations • Extravehicular activity • Physiological and metabolic issues – Health and space medicine – Radiation exposure – Life support systems • Control capabilities and human error Copyright 2016 by Robert Stengel. All rights reserved. For educational use only. 1 http://www.princeton.edu/~stengel/MAE342.html 1 Impey Barbicane Captain Nicholl 1865 Jules Verne (1828-1905) 2 2 1 Princeton, ‘38 3 3 A Voyage to the Moon Cyrano de Bergerac (1619-1655) • Hercule-Savinien Cyrano de Bergerac • “Comical History of the States and Empires of the Moon”, written about 1649, published 1656 or 1657 • English translation, 1687 • In Firestone Library (below & left) 4 4 2 Cyrano's Voyage to the Moon and Back 5 5 1952 Rocket Ship/Space Station Concept C. Ryan, W. von Braun, et al, Across the Space Frontier, Collier’s Magazine Launch weight: 14M lb 6 6 3 Trouble in the Spacecraft: Ejection Capsule 7 7 Why Humans in Space? • Exploration • Scientific discovery • Engineering development • Construction, maintenance, and repair • Pilots, tourists, and tour guides 8 8 4 Man vs. Machine (Handbook of Astronautical Engineering, 1961) 9 9 Performance Issues for Manned Spaceflight • Flexibility, learning, • Physical labor and judgment • Endurance • Information bandwidth, • Ergonomics display, and • Control systems communication • Re-entry systems and • Pre-flight training recovery • Performance variation • Tools and equipment • Extra-vehicular activity • Recycling • Physical labor 10 10 5 Cooper-Harper Pilot Opinion Rating (NASA TN D-5153, 1969) 11 11 Cooper-Harper Pilot Opinion Rating (NASA TN D-5153, 1969) 12 12 6 Human Space Experience to April 2016 § Continuous human space presence since Oct.