Part Iii : Space Transportation, Propulsion and Pathway Options
Total Page:16
File Type:pdf, Size:1020Kb
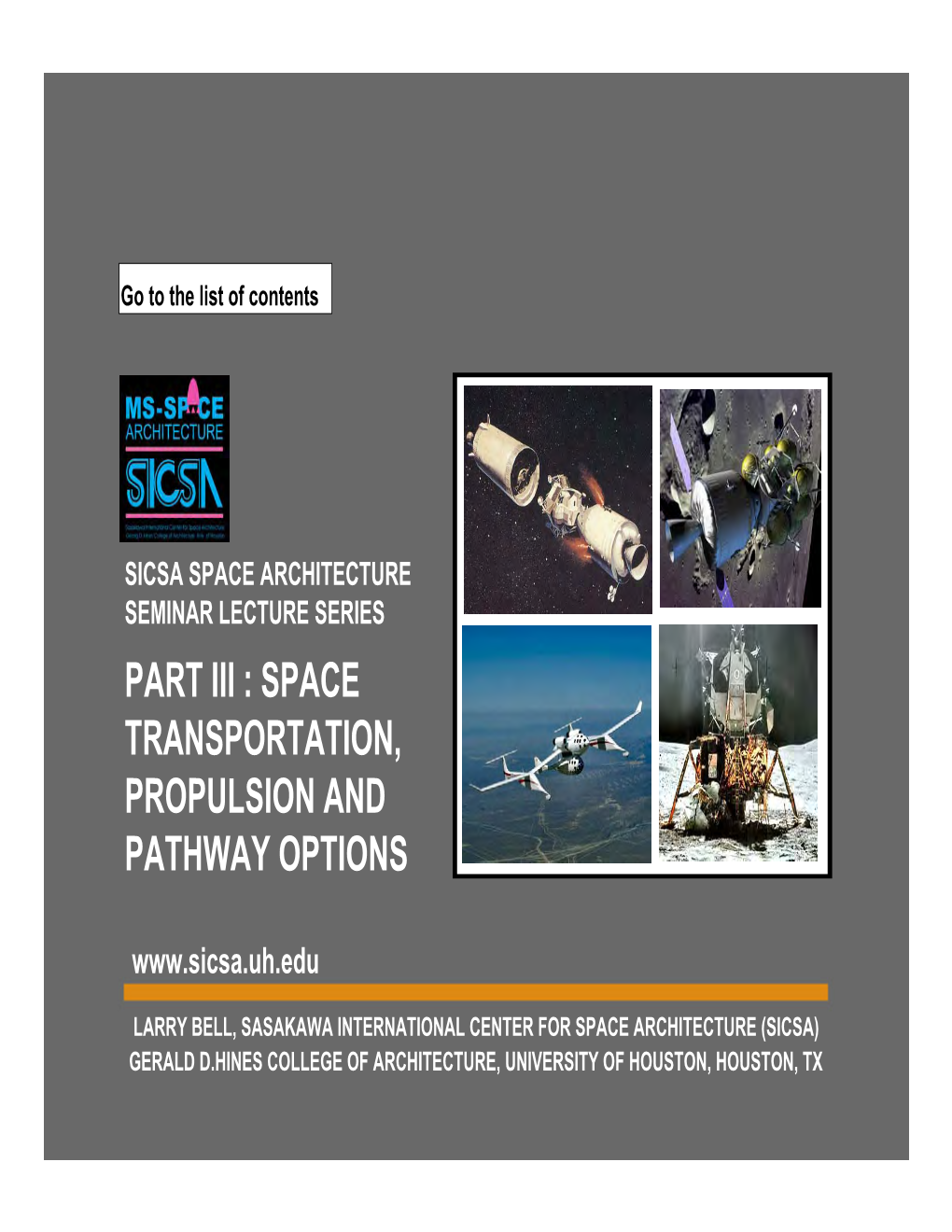
Load more
Recommended publications
-
Bibliography
Annotated List of Works Cited Primary Sources Newspapers “Apollo 11 se Vraci na Zemi.” Rude Pravo [Czechoslovakia] 22 July 1969. 1. Print. This was helpful for us because it showed how the U.S. wasn’t the only ones effected by this event. This added more to our project so we had views from outside the US. Barbuor, John. “Alunizaron, Bajaron, Caminaron, Trabajaron: Proeza Lograda.” Excelsior [Mexico] 21 July 1969. 1. Print. The front page of this newspaper was extremely helpful to our project because we used it to see how this event impacted the whole world not just America. Beloff, Nora. “The Space Race: Experts Not Keen on Getting a Man on the Moon.” Age [Melbourne] 24 April 1962. 2. Print. This was an incredibly important article to use in out presentation so that we could see different opinions. This article talked about how some people did not want to go to the moon; we didn’t find many articles like this one. In most everything we have read it talks about the advantages of going to the moon. This is why this article was so unique and important. Canadian Press. “Half-billion Watch the Moon Spectacular.” Gazette [Montreal] 21 July 1969. 4. Print. This source gave us a clear idea about how big this event really was, not only was it a big deal in America, but everywhere else in the world. This article told how Russia and China didn’t have TV’s so they had to find other ways to hear about this event like listening to the radio. -
Launch and Deployment Analysis for a Small, MEO, Technology Demonstration Satellite
46th AIAA Aerospace Sciences Meeting and Exhibit AIAA 2008-1131 7 – 10 January 20006, Reno, Nevada Launch and Deployment Analysis for a Small, MEO, Technology Demonstration Satellite Stephen A. Whitmore* and Tyson K. Smith† Utah State University, Logan, UT, 84322-4130 A trade study investigating the economics, mass budget, and concept of operations for delivery of a small technology-demonstration satellite to a medium-altitude earth orbit is presented. The mission requires payload deployment at a 19,000 km orbit altitude and an inclination of 55o. Because the payload is a technology demonstrator and not part of an operational mission, launch and deployment costs are a paramount consideration. The payload includes classified technologies; consequently a USA licensed launch system is mandated. A preliminary trade analysis is performed where all available options for FAA-licensed US launch systems are considered. The preliminary trade study selects the Orbital Sciences Minotaur V launch vehicle, derived from the decommissioned Peacekeeper missile system, as the most favorable option for payload delivery. To meet mission objectives the Minotaur V configuration is modified, replacing the baseline 5th stage ATK-37FM motor with the significantly smaller ATK Star 27. The proposed design change enables payload delivery to the required orbit without using a 6th stage kick motor. End-to-end mass budgets are calculated, and a concept of operations is presented. Monte-Carlo simulations are used to characterize the expected accuracy of the final orbit. -
Bibliography
Bibliography Books and reports Blandford, R.D. (Chair) New Worlds, New Horizons in Astronomy and Astrophysics Committee for a Decadal Survey of Astronomy and Astrophysics, National Research Council, 2010 Bondi, Hermann. et al Pioneering in Outer Space Heinemann Educational Books, 1971 Clarke, Arthur C. The Exploration of Space Temple Press, London, 1951 Department of Energy/NASA Satellite Power Systems Concept Development and Evaluation Program. DoE/NASA, October 1978 http://www.nss.org/settlement/ssp/library/1978DOESPS-ReferenceSystemReport.pdf Satellite Power Systems (SPS) Space Transportation Cost Analysis and Evaluation. DoE/NASA, November 1980 http://www.nss.org/settlement/ssp/library/1980DOESPS- SpaceTransportationCostAnalysis.pdf Dick, Steven J. (editor) Remembering the Space Age: Proceedings of the 50th Anniversary Conference. NASA SP-2008-4703, 2008 http://history.nasa.gov/Remembering_Space_Age_A.pdf © Springer International Publishing AG 2017 235 M. van Pelt, Dream Missions, Springer Praxis Books, DOI 10.1007/978-3-319-53941-6 236 Bibliography Dyson, George Project Orion: The True Story of the Atomic Spaceship Henry Holt & Company, Inc., USA, 2002 Ehricke, Krafft A. Solar Transportation In Space Age in Fiscal Year 2001, Proceedings of the Fourth AAS Goddard Memorial Symposium American Astronautical Society, 1966 Friedman, Louis. Human Spaceflight, from Mars to the Stars The University of Arizona Press, 2015 Gatland, Kenneth W. & Bono, Philip Frontiers of Space Blandford Press, UK, 1969 Hansen, James R. Chapter 9, Skipping “The Next Logical Step” in Spaceflight Revolution; NASA Langley Research Center from Sputnik to Apollo NASA History Series SP-4308, USA, 1994 http://history.nasa.gov/SP-4308/ch9.htm Koelle, Heinz-Hermann. Nova and Beyond, a Review of Heavy Lift Launch Vehicle Concepts in the Post-Saturn Class Technical University Berlin, Germany, 2001 Konecci, Eugene B. -
Electric Propulsion System Scaling for Asteroid Capture-And-Return Missions
Electric propulsion system scaling for asteroid capture-and-return missions Justin M. Little⇤ and Edgar Y. Choueiri† Electric Propulsion and Plasma Dynamics Laboratory, Princeton University, Princeton, NJ, 08544 The requirements for an electric propulsion system needed to maximize the return mass of asteroid capture-and-return (ACR) missions are investigated in detail. An analytical model is presented for the mission time and mass balance of an ACR mission based on the propellant requirements of each mission phase. Edelbaum’s approximation is used for the Earth-escape phase. The asteroid rendezvous and return phases of the mission are modeled as a low-thrust optimal control problem with a lunar assist. The numerical solution to this problem is used to derive scaling laws for the propellant requirements based on the maneuver time, asteroid orbit, and propulsion system parameters. Constraining the rendezvous and return phases by the synodic period of the target asteroid, a semi- empirical equation is obtained for the optimum specific impulse and power supply. It was found analytically that the optimum power supply is one such that the mass of the propulsion system and power supply are approximately equal to the total mass of propellant used during the entire mission. Finally, it is shown that ACR missions, in general, are optimized using propulsion systems capable of processing 100 kW – 1 MW of power with specific impulses in the range 5,000 – 10,000 s, and have the potential to return asteroids on the order of 103 104 tons. − Nomenclature -
The Speed of a Geosynchronous Satellite Is ___
Physics 106 Lecture 9 Newton’s Law of Gravitation SJ 7th Ed.: Chap 13.1 to 2, 13.4 to 5 • Historical overview • N’Newton’s inverse-square law of graviiitation Force Gravitational acceleration “g” • Superposition • Gravitation near the Earth’s surface • Gravitation inside the Earth (concentric shells) • Gravitational potential energy Related to the force by integration A conservative force means it is path independent Escape velocity Example A geosynchronous satellite circles the earth once every 24 hours. If the mass of the earth is 5.98x10^24 kg; and the radius of the earth is 6.37x10^6 m., how far above the surface of the earth does a geosynchronous satellite orbit the earth? G=6.67x10-11 Nm2/kg2 The speed of a geosynchronous satellite is ______. 1 Goal Gravitational potential energy for universal gravitational force Gravitational Potential Energy WUgravity= −Δ gravity Near surface of Earth: Gravitational force of magnitude of mg, pointing down (constant force) Æ U = mgh Generally, gravit. potential energy for a system of m1 & m2 G Gmm12 mm F = Attractive force Ur()=− G12 12 r 2 g 12 12 r12 Zero potential energy is chosen for infinite distance between m1 and m2. Urg ()012 = ∞= Æ Gravitational potential energy is always negative. 2 mm12 Urg ()12 =− G r12 r r Ug=0 1 U(r1) Gmm U =− 12 g r Mechanical energy 11 mM EKUrmvMVG=+ ( ) =22 + − mech 22 r m V r v M E_mech is conserved, if gravity is the only force that is doing work. 1 2 MV is almost unchanged. If M >>> m, 2 1 2 mM ÆWe can define EKUrmvG=+ ( ) = − mech 2 r 3 Example: A stone is thrown vertically up at certain speed from the surface of the Moon by Superman. -
Optimisation of Propellant Consumption for Power Limited Rockets
Delft University of Technology Faculty Electrical Engineering, Mathematics and Computer Science Delft Institute of Applied Mathematics Optimisation of Propellant Consumption for Power Limited Rockets. What Role do Power Limited Rockets have in Future Spaceflight Missions? (Dutch title: Optimaliseren van brandstofverbruik voor vermogen gelimiteerde raketten. De rol van deze raketten in toekomstige ruimtevlucht missies. ) A thesis submitted to the Delft Institute of Applied Mathematics as part to obtain the degree of BACHELOR OF SCIENCE in APPLIED MATHEMATICS by NATHALIE OUDHOF Delft, the Netherlands December 2017 Copyright c 2017 by Nathalie Oudhof. All rights reserved. BSc thesis APPLIED MATHEMATICS \ Optimisation of Propellant Consumption for Power Limited Rockets What Role do Power Limite Rockets have in Future Spaceflight Missions?" (Dutch title: \Optimaliseren van brandstofverbruik voor vermogen gelimiteerde raketten De rol van deze raketten in toekomstige ruimtevlucht missies.)" NATHALIE OUDHOF Delft University of Technology Supervisor Dr. P.M. Visser Other members of the committee Dr.ir. W.G.M. Groenevelt Drs. E.M. van Elderen 21 December, 2017 Delft Abstract In this thesis we look at the most cost-effective trajectory for power limited rockets, i.e. the trajectory which costs the least amount of propellant. First some background information as well as the differences between thrust limited and power limited rockets will be discussed. Then the optimal trajectory for thrust limited rockets, the Hohmann Transfer Orbit, will be explained. Using Optimal Control Theory, the optimal trajectory for power limited rockets can be found. Three trajectories will be discussed: Low Earth Orbit to Geostationary Earth Orbit, Earth to Mars and Earth to Saturn. After this we compare the propellant use of the thrust limited rockets for these trajectories with the power limited rockets. -
Recommended Practices for Human Space Flight Occupant Safety
Recommended Practices for Human Space Flight Occupant Safety Version 1.0 August 27, 2014 Federal Aviation Administration Office of Commercial Space Transportation 800 Independence Avenue, Room 331 7 3 Washington, DC 20591 0 0 - 4 1 C T Recommended Practices for Human Space Flight Page ii Occupant Safety – Version 1.0 Record of Revisions Version Description Date 1.0 Baseline version of document August 27, 2014 Recommended Practices for Human Space Flight Page iii Occupant Safety – Version 1.0 Recommended Practices for Human Space Flight Page iv Occupant Safety – Version 1.0 TABLE OF CONTENTS A. INTRODUCTION ............................................................................................................... 1 1.0 Purpose ............................................................................................................................. 1 2.0 Scope ................................................................................................................................ 1 3.0 Development Process ....................................................................................................... 2 4.0 Level of Risk and Level of Care ...................................................................................... 2 4.1 Level of Risk ................................................................................................................ 2 4.2 Level of Care ................................................................................................................ 3 5.0 Structure and Nature of the -
Evolution of the Rendezvous-Maneuver Plan for Lunar-Landing Missions
NASA TECHNICAL NOTE NASA TN D-7388 00 00 APOLLO EXPERIENCE REPORT - EVOLUTION OF THE RENDEZVOUS-MANEUVER PLAN FOR LUNAR-LANDING MISSIONS by Jumes D. Alexunder und Robert We Becker Lyndon B, Johnson Spuce Center ffoaston, Texus 77058 NATIONAL AERONAUTICS AND SPACE ADMINISTRATION WASHINGTON, D. C. AUGUST 1973 1. Report No. 2. Government Accession No, 3. Recipient's Catalog No. NASA TN D-7388 4. Title and Subtitle 5. Report Date APOLLOEXPERIENCEREPORT August 1973 EVOLUTIONOFTHERENDEZVOUS-MANEUVERPLAN 6. Performing Organizatlon Code FOR THE LUNAR-LANDING MISSIONS 7. Author(s) 8. Performing Organization Report No. James D. Alexander and Robert W. Becker, JSC JSC S-334 10. Work Unit No. 9. Performing Organization Name and Address I - 924-22-20- 00- 72 Lyndon B. Johnson Space Center 11. Contract or Grant No. Houston, Texas 77058 13. Type of Report and Period Covered 12. Sponsoring Agency Name and Address Technical Note I National Aeronautics and Space Administration 14. Sponsoring Agency Code Washington, D. C. 20546 I 15. Supplementary Notes The JSC Director waived the use of the International System of Units (SI) for this Apollo Experience I Report because, in his judgment, the use of SI units would impair the usefulness of the report or I I result in excessive cost. 16. Abstract The evolution of the nominal rendezvous-maneuver plan for the lunar landing missions is presented along with a summary of the significant developments for the lunar module abort and rescue plan. A general discussion of the rendezvous dispersion analysis that was conducted in support of both the nominal and contingency rendezvous planning is included. -
An Assessment of Aerocapture and Applications to Future Missions
Post-Exit Atmospheric Flight Cruise Approach An Assessment of Aerocapture and Applications to Future Missions February 13, 2016 National Aeronautics and Space Administration An Assessment of Aerocapture Jet Propulsion Laboratory California Institute of Technology Pasadena, California and Applications to Future Missions Jet Propulsion Laboratory, California Institute of Technology for Planetary Science Division Science Mission Directorate NASA Work Performed under the Planetary Science Program Support Task ©2016. All rights reserved. D-97058 February 13, 2016 Authors Thomas R. Spilker, Independent Consultant Mark Hofstadter Chester S. Borden, JPL/Caltech Jessie M. Kawata Mark Adler, JPL/Caltech Damon Landau Michelle M. Munk, LaRC Daniel T. Lyons Richard W. Powell, LaRC Kim R. Reh Robert D. Braun, GIT Randii R. Wessen Patricia M. Beauchamp, JPL/Caltech NASA Ames Research Center James A. Cutts, JPL/Caltech Parul Agrawal Paul F. Wercinski, ARC Helen H. Hwang and the A-Team Paul F. Wercinski NASA Langley Research Center F. McNeil Cheatwood A-Team Study Participants Jeffrey A. Herath Jet Propulsion Laboratory, Caltech Michelle M. Munk Mark Adler Richard W. Powell Nitin Arora Johnson Space Center Patricia M. Beauchamp Ronald R. Sostaric Chester S. Borden Independent Consultant James A. Cutts Thomas R. Spilker Gregory L. Davis Georgia Institute of Technology John O. Elliott Prof. Robert D. Braun – External Reviewer Jefferey L. Hall Engineering and Science Directorate JPL D-97058 Foreword Aerocapture has been proposed for several missions over the last couple of decades, and the technologies have matured over time. This study was initiated because the NASA Planetary Science Division (PSD) had not revisited Aerocapture technologies for about a decade and with the upcoming study to send a mission to Uranus/Neptune initiated by the PSD we needed to determine the status of the technologies and assess their readiness for such a mission. -
Documenting Apollo on The
NASA HISTORY DIVISION Office of External Relations volume 27, number 1 Fourth Quarter 2009/First Quarter 2010 FROM HOMESPUN HISTORY: THE CHIEF DOCUMENTING APOLLO HISTORIAN ON THE WEB By David Woods, editor, The Apollo Flight Journal Bearsden, Scotland In 1994 I got access to the Internet via a 0.014 Mbps modem through my One aspect of my job that continues to amaze phone line. As happens with all who access the Web, I immediately gravi- and engage me is the sheer variety of the work tated towards the sites that interested me, and in my case, it was astronomy we do at NASA and in the NASA History and spaceflight. As soon as I stumbled upon Eric Jones’s burgeoning Division. As a former colleague used to say, Apollo Lunar Surface Journal (ALSJ), then hosted by the Los Alamos NASA is engaged not just in human space- National Laboratory, I almost shook with excitement. flight and aeronautics; its employees engage in virtually every engineering and natural Eric was trying to understand what had been learned about working on science discipline in some way and often at the Moon by closely studying the time that 12 Apollo astronauts had spent the cutting edge. This breadth of activities is, there. To achieve this, he took dusty, old transcripts of the air-to-ground of course, reflected in the history we record communication, corrected them, added commentary and, best of all, man- and preserve. Thus it shouldn’t be surprising aged to get most of the men who had explored the surface to sit with him that our books and monographs cover such a and add their recollections. -
Up, Up, and Away by James J
www.astrosociety.org/uitc No. 34 - Spring 1996 © 1996, Astronomical Society of the Pacific, 390 Ashton Avenue, San Francisco, CA 94112. Up, Up, and Away by James J. Secosky, Bloomfield Central School and George Musser, Astronomical Society of the Pacific Want to take a tour of space? Then just flip around the channels on cable TV. Weather Channel forecasts, CNN newscasts, ESPN sportscasts: They all depend on satellites in Earth orbit. Or call your friends on Mauritius, Madagascar, or Maui: A satellite will relay your voice. Worried about the ozone hole over Antarctica or mass graves in Bosnia? Orbital outposts are keeping watch. The challenge these days is finding something that doesn't involve satellites in one way or other. And satellites are just one perk of the Space Age. Farther afield, robotic space probes have examined all the planets except Pluto, leading to a revolution in the Earth sciences -- from studies of plate tectonics to models of global warming -- now that scientists can compare our world to its planetary siblings. Over 300 people from 26 countries have gone into space, including the 24 astronauts who went on or near the Moon. Who knows how many will go in the next hundred years? In short, space travel has become a part of our lives. But what goes on behind the scenes? It turns out that satellites and spaceships depend on some of the most basic concepts of physics. So space travel isn't just fun to think about; it is a firm grounding in many of the principles that govern our world and our universe. -
Magnetoshell Aerocapture: Advances Toward Concept Feasibility
Magnetoshell Aerocapture: Advances Toward Concept Feasibility Charles L. Kelly A thesis submitted in partial fulfillment of the requirements for the degree of Master of Science in Aeronautics & Astronautics University of Washington 2018 Committee: Uri Shumlak, Chair Justin Little Program Authorized to Offer Degree: Aeronautics & Astronautics c Copyright 2018 Charles L. Kelly University of Washington Abstract Magnetoshell Aerocapture: Advances Toward Concept Feasibility Charles L. Kelly Chair of the Supervisory Committee: Professor Uri Shumlak Aeronautics & Astronautics Magnetoshell Aerocapture (MAC) is a novel technology that proposes to use drag on a dipole plasma in planetary atmospheres as an orbit insertion technique. It aims to augment the benefits of traditional aerocapture by trapping particles over a much larger area than physical structures can reach. This enables aerocapture at higher altitudes, greatly reducing the heat load and dynamic pressure on spacecraft surfaces. The technology is in its early stages of development, and has yet to demonstrate feasibility in an orbit-representative envi- ronment. The lack of a proof-of-concept stems mainly from the unavailability of large-scale, high-velocity test facilities that can accurately simulate the aerocapture environment. In this thesis, several avenues are identified that can bring MAC closer to a successful demonstration of concept feasibility. A custom orbit code that dynamically couples magnetoshell physics with trajectory prop- agation is developed and benchmarked. The code is used to simulate MAC maneuvers for a 60 ton payload at Mars and a 1 ton payload at Neptune, both proposed NASA mis- sions that are not possible with modern flight-ready technology. In both simulations, MAC successfully completes the maneuver and is shown to produce low dynamic pressures and continuously-variable drag characteristics.