Development and Progress of Hydrogen Metallurgy
Total Page:16
File Type:pdf, Size:1020Kb
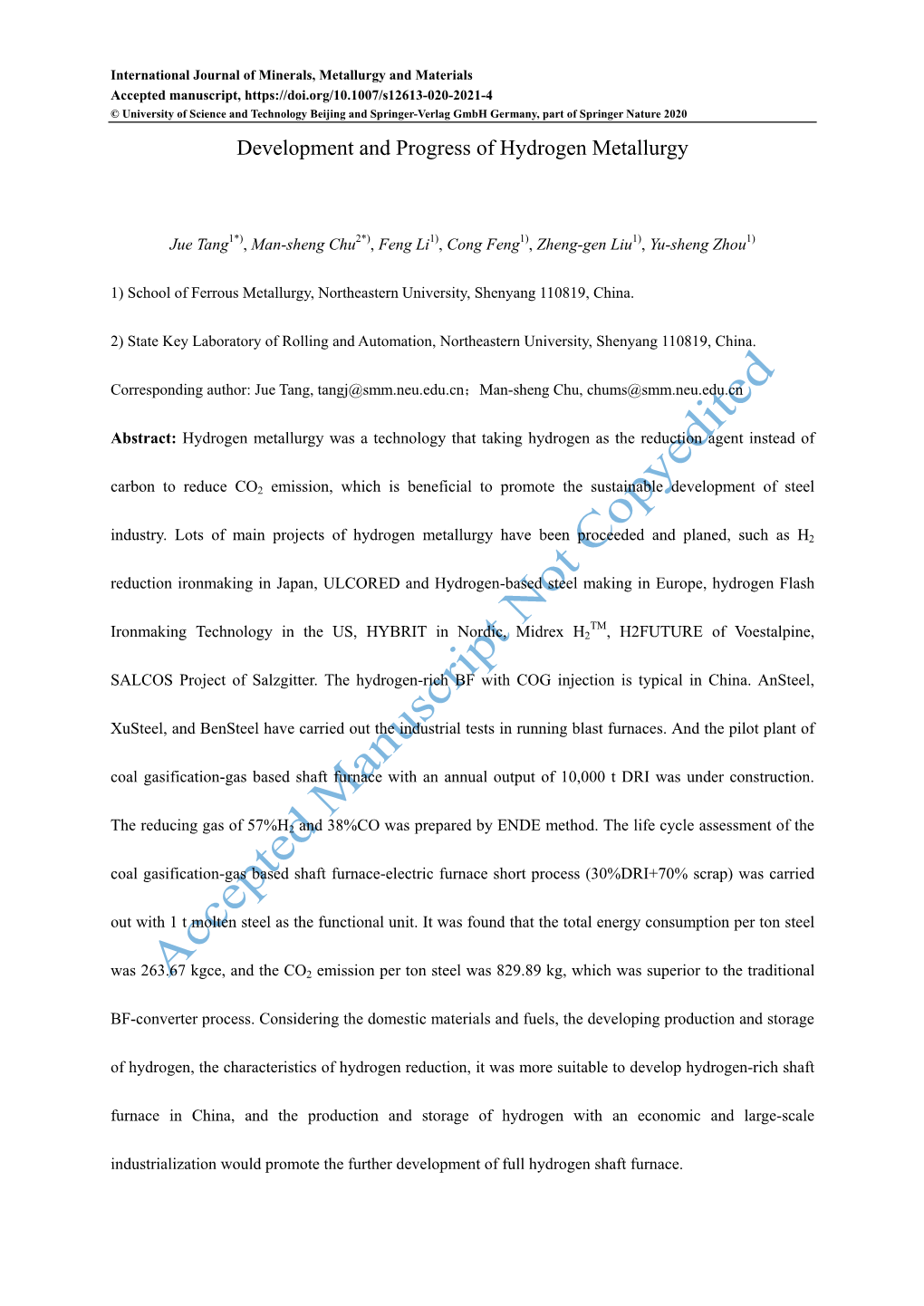
Load more
Recommended publications
-
Elegancy D5.2.5
ACT Project Number: 271498 Project name: ELEGANCY Project full title: Enabling a Low-Carbon Economy via Hydrogen and CCS ERA-Net ACT project Starting date: 2017-08-31 Duration: 36 months D5.2.5 Evaluation of the potential for hydrogen and CCS in the decarbonization of the Dutch steel industry Date: 2020-08-31 Organization name of lead participant for this deliverable: Utrecht University ACT ELEGANCY, Project No 271498, has received funding from DETEC (CH), BMWi (DE), RVO (NL), Gassnova (NO), BEIS (UK), Gassco, Equinor and Total, and is cofunded by the European Commission under the Horizon 2020 programme, ACT Grant Agreement No 691712. Dissemination Level PU Public x CO Confidential, only for members of the consortium (including the Commission Services) Page iii Deliverable number: D5.2.5 Deliverable title: Evaluation of the potential for hydrogen and CCS in the decarbonization of the Dutch steel industry Work package: WP5 Case Studies Lead participant: UU Authors Name Organisation E-mail Lukas Weimann* UU [email protected] Matteo Gazzani UU [email protected] Gert Jan Kramer UU Joep Matser UU Annika Boldrini UU *Mark lead author with asterisk Keywords Integrated steelworks, decarbonization of steel industry, process optimization, Hisarna, electric- arc furnace, carbon capture and storage, hydrogen. Abstract The iron and steel industry accounts for 5 % of worldwide CO2 emissions. With 13 MtCO2eq annually, TATA Steel, which employs the traditional blast furnace – basic oxygen furnace steel making route, is one of the largest single point emitters in the Netherlands (and EU). Given the role of steel in present and future society, decarbonizing the steel industry is of paramount importance for a CO2 net-zero society. -
Steel Pickling: a Profile
December 1993 Steel Pickling: A Profile Draft Report Prepared for John Robson U.S. Environmental Protection Agency Office of Air Quality Planning and Standards Cost and Economic Impact Section Research Triangle Park, NC 27711 EPA Contract Number 68-D1-0143 RTI Project Number 35U-5681-58 DR EPA Contract Number RTI Project Number 68-D1-0143 35U-5681-58 DR Steel Pickling: A Profile Draft Report December 1993 Prepared for John Robson U.S. Environmental Protection Agency Office of Air Quality Planning and Standards Cost and Economic Impact Section Research Triangle Park, NC 27711 Prepared by Tyler J. Fox Craig D. Randall David H. Gross Center for Economics Research Research Triangle Institute Research Triangle Park, NC 27709 TABLE OF CONTENTS Section Page 1 Introduction .................. 1-1 2 The Supply Side of the Industry ......... 2-1 2.1 Steel Production .............. 2-1 2.2 Steel Pickling .............. 2-3 2.2.1 Hydrochloric Acid Pickling ..... 2-5 2.2.1.1 Continuous Pickling .... 2-8 2.2.1.1.1 Coils ...... 2-8 2.2.1.1.2 Tube, Rod, and Wire ...... 2-9 2.2.1.2 Push-Pull Pickling ..... 2-10 2.2.1.3 Batch Pickling ....... 2-11 2.2.1.4 Emissions from Steel Pickling 2-11 2.2.2 Acid Regeneration of Waste Pickle Liquor .............. 2-12 2.2.2.1 Spray Roaster Regeneration Process .......... 2-13 2.3 Types of Steel .............. 2-14 2.3.1 Carbon Steels ............ 2-15 2.3.2 Alloy Steels ............ 2-15 2.3.3 Stainless Steels .......... 2-15 2.4 Costs of Production ........... -
Vacuum Technology Book Volume II
The Vacuum Technology Book Volume II Know how book Part 2 Know how book Page 2 / Part 2 www.pfeiffer-vacuum.com 2 Vacuum Technology and Know how / Contents Contents Vacuum Technology and Know how 1 Introduction to vacuum technology 1.1 General 9 1.1.1 Vacuum – Definition .................................................9 1.1.2 Overview of vacuum .................................................9 1.2 Fundamentals 9 1.2.1 Definition of vacuum .................................................9 1.2.2 General gas equation ................................................11 1.2.3 Molecular number density ............................................12 1.2.4 Thermal velocity ....................................................12 1.2.5 Mean free path .....................................................12 1.2.6 Types of flow ......................................................14 1.2.7 pV throughput .....................................................15 1.2.8 Conductance ......................................................16 1.3 Influences in real vacuum systems 18 1.3.1 Contamination .....................................................18 1.3.2 Condensation and vaporization ........................................18 1.3.3 Desorption, diffusion, permeation and leaks ..............................19 1.3.4 Bake-out ..........................................................20 1.3.5 Residual gas composition ............................................20 1.3.6 Venting ...........................................................20 2 Basic calculations -
Low Carbon Alternative Technologies – Global Perspective IEA Latin American Expert Dialogue 22Nd August 2018 São Paulo, Brazil Disclaimer
Low carbon alternative technologies – global perspective IEA Latin American Expert Dialogue 22nd August 2018 São Paulo, Brazil Disclaimer This document is protected by copyright. Distribution to third parties or reproduction in any format is not permitted without written permission from worldsteel. worldsteel operates under the strictest antitrust guidelines. Visit worldsteel.org\About us for detailed antitrust guidelines. 2 Presentation outline . Background . Ongoing activities outside of Latin America . Barriers to implementation . Observations 3 Background . The steel industry is energy and material intensive and the management of its energy efficiency and efforts to increase the use of scrap have always been a focus. The sector has thereby achieved significant reductions in energy intensity over the last decades . However, the steel industry understood early that breakthrough technologies would be needed to achieve additional and drastic reductions. The development of breakthrough technologies requires a considerable amount of time before possible commercial deployment . The identification of promising technologies and their development began in the early 2000s but slowed down significantly after the economic crisis . Though a few programmes have been cancelled due to a lack of funding others have come in their place and a large number of options are being explored in parallel. 4 Carbon “CCS” I&S HISARNA CCS Hydrogen Electricity 5 Carbon Capture and Storage (CCS) . BHP Billiton and Peking University study ongoing into the potential of carbon capture, use and storage (CCUS) for steel production in China. CCS looked in in other areas eg. ULCOS-TGR BF . China Steel Corp . Posco . COURSE50 and others . Cost, storage and infrastructure remain an issue for steelmakers 6 HIsarna Top gas . -
Plate MTD® and Tool Steels: for Mold, Tool and Die Applications
ArcelorMittal USA Plate MTD® and Tool Steels: for Mold, Tool and Die Applications Introduction ArcelorMittal USA MTD® Steels ArcelorMittal USA Tool Steels ArcelorMittal USA MTD steels com- ArcelorMittal USA produces the tool steels A2, A8 Mod., O1, S5, and prise a family of five pre-hardened S7** for use in applications where an air-hardening, oil-hardening alloy plate steels developed for a or shock-resisting tool steel is required. These steels are available variety of mold, tool and die ap- from ArcelorMittal USA in full-sized, annealed plates suitable for plications. These steels have been saw cutting and/or finishing. Parts can subsequently be machined available for over 20 years and pos- and heat treated to a range of hardness requirements. For improved sess the flexibility of the AISI 41XX internal cleanliness, all ArcelorMittal USA tool steels are produced steels. They are available in the with maximum sulfur levels of 0.010%, using Fineline® processing. 262-321 Brinell range* (unless otherwise noted) for optimum bal- These steels are also available as ArcelorMittal USA Finishline™, a ance between machinability and hardness. The use of pre-hardened prefinished plate product with decarb-free top and bottom surfaces MTD® steels eliminates the need for and risk associated with heat ground to a maximum 125 RMS. treating molds, holder blocks and other parts after machining. MTD * Brinell hardness (HB) readings are taken from standard test locations on the plate plates are routinely saw cut. surface after the decarburization layer is removed. This range of HB converts to 27-34 Rockwell “C”. ArcelorMittal USA uses HB measurement as its official test. -
Investigation on Boronizing of N80 Tube Steel
ISIJ International, Vol. 49 (2009), No. 11, pp. 1776–1783 Investigation on Boronizing of N80 Tube Steel Z. G. SU,1) X. TIAN,1) J. AN,1) Y. LU,1) Y. L. YANG2) and S. J. SUN2) 1) Key Laboratory of Automobile Materials, Ministry of Education, Department of Materials Science and Engineering, Nanling Campus of Jilin University, Changchun 130025, Peoples’ Republic of China. E-mail: [email protected] 2) Songyuan Daduo Oilfield Accessory Industry Co. Ltd., Songyuan, 138000, Peoples’ Republic of China. (Received on May 26, 2009; accepted on July 21, 2009) In present paper, boronizing was applied to N80 steel tube by pack boronizing, and its effect on mechani- cal properties, wear and corrosion of N80 tube steel was investigated. A dual-phase boride layer composed of FeB and F2B phases was formed on the surface of the steel substrate in a hardness range of 1 220–1 340 HV. A set-up was designed to reduce usage of the boriding agent and accelerate the pipe’s cooling process after boronizing treatment. In order to meet the tensile properties of N80 steel required by API SPEC 5L, different cooling methods were employed including annealing, normalizing, fan-cooling and graphite-bar assisted rapid cooling. Among these methods, graphite-bar assisted rapid cooling resulted in the highest amount of pearlite in the steel substrate and the highest mechanical properties, satisfying the mechanical properties of API SPEC 5L. The boronized N80 steel exhibited an abrasive wear mechanism and showed a higher wear resistance under a given sliding condition due to the great hardness and integrity of the boride layer, and it also displayed an excellent corrosion resistance in both H2SO4 and HCl acid environ- ments. -
Pumps and Compressors for the World Market 2016 with Compressed Air and Vacuum Technology
Pumps + Systems Compressors, Compressed Air and Vacuum Technology VDMA Pumps and Compressors for the World Market 2016 with Compressed Air and Vacuum Technology Pumps and Compressors for the World Market 2016 Market World the for and Compressors Pumps 50 YEARS OF LEAK DETECTION Experience makes sense! Pfeiffer Vacuum is the supplier with the widest range of leak detectors on the market. We provide solutions for applications using helium and hydrogen as tracer gas. From portable devices to complex leak detection systems – we always offer the optimum solution to detect leakages in many different industrial sectors. Competence, quality and service from a single source. Learn everything about leak detection here: leak-detection.pfeiffer-vacuum.com Are you looking for a perfect vacuum solution? Please contact us: Pfeiffer Vacuum GmbH · Headquarters/Germany · T +49 6441 802-0 · F +49 6441 802-1202 [email protected] · www.pfeiffer-vacuum.com 16.01.25_PuK_VDMA_Lecksuche_210x297mm_EN.indd 1 25.01.16 11:14 Pumps + Systems Compressors, Compressed Air and Vacuum Technology Pumps and Compressors for the World Market 2016 with Compressed Air and Vacuum Technology 2 PUMPS & SYSTEMS / COMPRESSORS, COMPRESSED AIR & VACUUM TECHNOLOGY Contents Contents 4 Editorial: Pumps and Compressors for the World Market: still retrievable as e-magazine 6 German pump and compressor manufacturers in 2016: Well prepared for the future 12 International trade fairs and exhibitions 14 Third Rotating Equipment Conference in 2016 16 Fluid flow machinery 4.0: a two-way conversation 18 Part I: Pumps & Systems 18 Standardized chemical pump revised 25 Highly efficient speed regulation for centrifugal pumps 33 Oscillating displacement pumps: more safety thanks to two diaphragms Screw pumps with standardized geometrical dimensions can be 40 High-pressure plunger pumps in water hydraulics used as pumps in the chemical and petrochemical industry. -
Form 10-K Gibraltar Steel Corporation
SECURITIES AND EXCHANGE COMMISSION Washington, D. C. 20549 ______________________________ FORM 10-K (Mark One) ( X ) ANNUAL REPORT PURSUANT TO SECTION 13 or 15(d) OF THE SECURITIES ACT OF 1934 For The Fiscal Year Ended December 31, 2001 or ( ) TRANSITION REPORT PURSUANT TO SECTION 13 OR 15(d) OF THE SECURITIES EXCHANGE ACT OF 1934 For the Transition Period From ___________ to ____________ Commission File Number 0-22462 GIBRALTAR STEEL CORPORATION (Exact name of Registrant as specified in its charter) Delaware 16-1445150 (State or other jurisdiction of incorporation organization) (I.R.S. Employer Identification No.) 3556 Lake Shore Road, P.O. Box 2028, Buffalo, New 14219-0228 York (Zip Code) (address of principal executive offices) (716) 826-6500 Registrant's telephone number, including area code Securities registered pursuant to Section 12(b) of the Act: Title of each class Name of each exchange on which registered Common Stock, $.01 par value NASDAQ National Market System Securities registered pursuant to Section 12(g) of the Act: NONE Indicate by check mark whether the Registrant (1) has filed all reports required to be filed by Section 13 or 15(d) of the Securities Exchange Act of 1934 during the preceding 12 months (or for such shorter period that the Registrant was required to file such reports), and (2) has been subject to such filing requirements for the past 90 days. YES X NO Indicate by check mark if disclosure of delinquent filers pursuant to Item 405 of Regulation S-K is not contained herein, and will not be contained, to the best of the Registrant's knowledge, in definitive proxy or information statements incorporated by reference in Part III of the Form 10-K or any amendment to this Form 10-K. -
Energy Efficiency Improvement and Cost Saving Opportunities for the U.S
LBNL-4779E ERNEST ORLANDO LAWRENCE BERKELEY NATIONAL LABORATORY Energy Efficiency Improvement and Cost Saving Opportunities for the U.S. Iron and Steel Industry An ENERGY STAR® Guide for Energy and Plant Managers Ernst Worrell, Paul Blinde, Maarten Neelis, Eliane Blomen, and Eric Masanet Environmental Energy Technologies Division Sponsored by the U.S. Environmental Protection Agency October 2010 Disclaimer This document was prepared as an account of work sponsored by the United States Government. While this document is believed to contain correct information, neither the United States Government nor any agency thereof, nor The Regents of the University of California, nor any of their employees, makes any warranty, express or implied, or assumes any legal responsibility for the accuracy, completeness, or usefulness of any information, apparatus, product, or process disclosed, or represents that its use would not infringe privately owned rights. Reference herein to any specific commercial product, process, or service by its trade name, trademark, manufacturer, or otherwise, does not necessarily constitute or imply its endorsement, recommendation, or favoring by the United States Government or any agency thereof, or The Regents of the University of California. The views and opinions of authors expressed herein do not necessarily state or reflect those of the United States Government or any agency thereof, or The Regents of the University of California. Ernest Orlando Lawrence Berkeley National Laboratory is an equal opportunity employer. LBNL-Report Energy Efficiency Improvement and Cost Saving Opportunities for the U.S. Iron and Steel Industry An ENERGY STAR® Guide for Energy and Plant Managers Ernst Worrell, Paul Blinde, Maarten Neelis, Eliane Blomen, and Eric Masanet Energy Analysis Department Environmental Energy Technologies Division Ernest Orlando Lawrence Berkeley National Laboratory University of California Berkeley, CA 94720 October 2010 This work was funded by U.S. -
Selected Heat Treating Terms
2008 THERMAL PROCESS INFORMATION BOOK SELECTED HEAT TREATING TERMS 36 HEAT TREATMENT OF FERROUS METALS 37 HEAT TREATING PROCESSES 38 SURFACE ENGINEERING 39 FURNACE ATMOSPHERES 40 INDUCTION HEAT TREATING OF STEEL 42 COMBUSTION 44 QUENCHING 45 CONTROLS/INSTRUMENTATION 46 FLOWMETERS 48 SELECTED HEAT TREATING TERMS atmosphere controlled furnaces. In many heat treating operations, drogen in a 90-10 blend, where the hydrogen serves as a re- the atmosphere must be controlled to prevent workpieces from ducing gas. oxidizing and/or decarburizing. Steel becomes more active as dissociated ammonia. Dissociated ammonia (N2 + H2) is produced the temperature increases, and severe oxidation of carbon steel from anhydrous ammonia (NH3) by raising the temperature begins at about 425°C (795°F). Above 1200°C (2190°F), the ox- to 900–980°C (1650–1795°F) in a catalyst filled retort. The gas is idation rate increases exponentially. At high temperatures the then cooled for metering and transport. Dissociated ammonia at- carbon in steel also can react with the atmosphere to lower the mospheres are about 75% H2 and 25% N2,with less than 300 carbon content. ppm residual ammonia at a dew point below –60°C (–75°F). carbon potential. A measure of the ability of an environment con- The atmosphere provides a dry, carbon-free source of reducing taining carbon to alter or maintain, under prescribed condi- gas. Uses include bright copper and silver brazing, bright heat tions, the carbon level in steel. Control of carbon potential is treating of carbon steels and selected nickel and copper alloys, important in carburizing furnaces. -
IMPACTS Steel
Appendix 1: ITP-Sponsored Technologies Commercially Available Aluminum ........................................................................................................................................... 19 u Aluminum Reclaimer for Foundry Applications .................................................................................................................................. 20 u Isothermal Melting................................................................................................................................................................................ 21 Chemicals ........................................................................................................................................... 23 u Cavity-Enhanced Gas Analyzer for Process Control ............................................................................................................................ 24 u Hollow-Fiber Membrane Compressed Air Drying System .................................................................................................................. 25 u Improved Methods for the Production of Polyurethane Foam ............................................................................................................ 26 u Low-Cost, Robust Ceramic Membranes for Gas Separation ................................................................................................................ 27 u Low-Frequency Sonic Mixing Technology ......................................................................................................................................... -
Performance Enhancement in Borocarburized Low-Carbon Steel by Double Glow Plasma Surface Alloying
coatings Article Performance Enhancement in Borocarburized Low-Carbon Steel by Double Glow Plasma Surface Alloying Zheng Ding, Qiang Miao *, Wenping Liang, Zhengang Yang and Shiwei Zuo College of Materials Science and Technology, Nanjing University of Aeronautics and Astronautics, Nanjing 210000, China; [email protected] (Z.D.); [email protected] (W.L.); [email protected] (Z.Y.); [email protected] (S.Z.) * Correspondence: [email protected] Received: 12 October 2020; Accepted: 2 December 2020; Published: 10 December 2020 Abstract: In this paper, the performance of low-carbon steel is enhanced after introducing a·borocarburized diffusion layer via double glow plasma surface alloying technology. Due to the boron-carbon gradient structure of low-carbon steel, the protective coating exhibits an excellent wear and corrosion resistance. Interestingly, the borocarburized layer consists of a 64 µm carburized layer and a 27 µm boride layer, which plays an effective role in enhancing the microhardness of borocarburized low-carbon steel, exhibiting a 1440 Vickers hardness increase in the surface microhardness of low-carbon steel. The potentiodynamic polarization measurement and impedance measurement results indicate that the boride protective film can effectively prevent aggressive chloride ions from invading the substrate, which indicates an excellent property of corrosion resistance. This systematic study paves a promising way for the future application of hard coatings in severe environments. Keywords: borocarburizing; double glow; gradient structure; Fe2B; corrosion resistance 1. Introduction Due to the desirable weldability, plasticity and toughness, low-carbon steel has gained worldwide attention for its versatile applications in construction and mechanical parts. The surface hardened low-carbon steel can be widely used, for example, in wear-resistant parts of vehicles and ships [1–4].