Marking out Tools
Total Page:16
File Type:pdf, Size:1020Kb
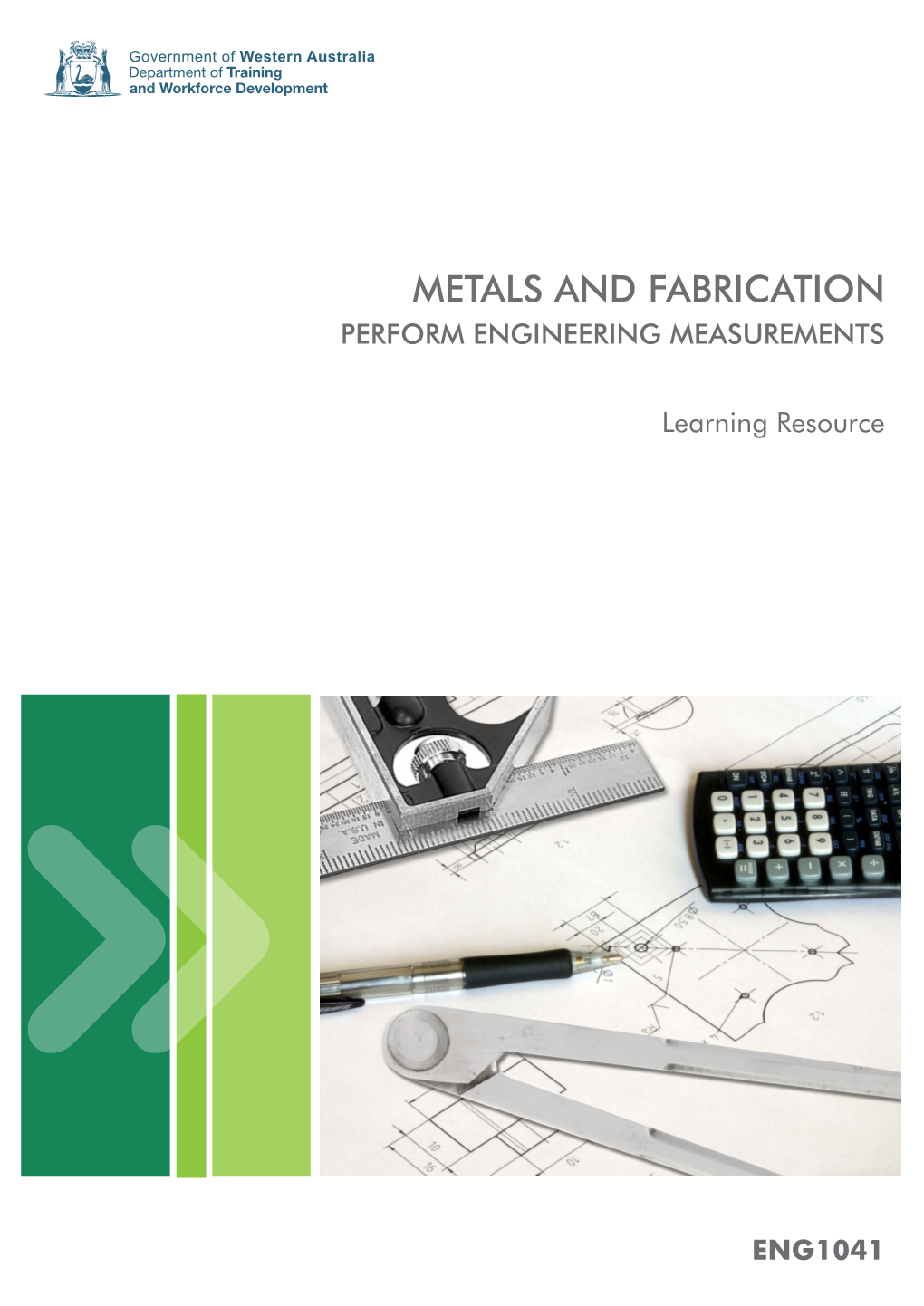
Load more
Recommended publications
-
Magazine Lip Forming Tools
MAGAZINE LIP FORMING TOOLS Brownells Lip Forming Anvil and Yoke help the gunsmith alter original equipment-style, .45 caliber, 1911 Auto magazines to properly feed ammuni- tion with semi-wadcutter bullets. Issue-style feed lips are designed for round nose, 230 grain, jacketed bul- lets which have a long ogive and ride up the barrel’s feed ramp easily. Rounds loaded with shorter, lighter, blunt nosed or semi-wadcutter bullets can ei- ther run into the feed ramp as the slide carries them forward or “stand up” too soon and cause a smokestack jam. Changing the lip contour with these tools causes the magazine to release the rear of the cartridge sooner so the extractor can pick it up and help direct it up the ramp and into the chamber. Most aftermarket magazines like those made by Metalform, Wilson, Mc- Cormick, Pachmayr and others, already have a similar feed lip shape. The Lip Forming Anvil and Yoke can often be used to restore the lips on these magazines if they get damaged. READ & FOLLOW THESE m WARNING m Never attempt to disassemble or reassemble a firearm unless you are INSTRUCTIONS absolutely certain that it is empty and unloaded. Visually inspect the chamber, the magazine and firing mechanism to be absolutely certain that no ammunition remains in the firearm. Disassembly and reas- BROWNELLS GUNSMITHS DATA RING BINDER GUNSMITHS BROWNELLS DATA sembly should follow the manufacturer’s instructions. If such instruc- tions are not immediately available, contact the manufacturer to see if they are available. If they are not available at all, then you should 200 S. -
AABTKJX0 Giesecke ©2004 by Prentice Hall, Inc
Figure Number: 03-01 AABTKJX0 Giesecke ©2004 by Prentice Hall, Inc. Engineering Graphics, 8E A Pearson Company Page Number: Principal Items of Equipment. Figure Number: 03-02 AABTKJY0 Giesecke ©2004 by Prentice Hall, Inc. Engineering Graphics, 8E A Pearson Company Page Number: The T-square. Figure Number: 03-03 AABTKJZ0 Giesecke ©2004 by Prentice Hall, Inc. Engineering Graphics, 8E A Pearson Company Page Number: Testing the Working Edge of the Drawing Board. Figure Number: 03-04 AABTKKA0 Giesecke ©2004 by Prentice Hall, Inc. Engineering Graphics, 8E A Pearson Company Page Number: Testing the T-square. Figure Number: 03-05 AABTKKB0 Giesecke ©2004 by Prentice Hall, Inc. Engineering Graphics, 8E A Pearson Company Page Number: Placing Paper on Drawing Board. Figure Number: 03-06 AABTKKC0 Giesecke ©2004 by Prentice Hall, Inc. Engineering Graphics, 8E A Pearson Company Page Number: Positions of Drafting Tape. Figure Number: 03-07 a-c AABTKKD0 Giesecke ©2004 by Prentice Hall, Inc. Engineering Graphics, 8E A Pearson Company Page Number: Drawing Pencils. Hard Medium Soft The hard leads in this group (left) These grades are for general These leads are too soft to be useful are used where extreme accuracy purpose work in technical drawing. in mechanical drafting. Their use for is required, as on graphical com- The softer grades (right) are used such work results in smudged, rough putations and charts and diagrams. for technical sketching, for letter- lines that are hard to erase, and the The softer leads in this group ing, arrowheads, and other free- lead must be sharpened continually. (right) are sometimes used for line hand work on mechanical These grades are used for art work work on engineering drawings, but drawings. -
Weldability of High Strength Aluminium Alloys
Muyiwa Olabode WELDABILITY OF HIGH STRENGTH ALUMINIUM ALLOYS Thesis for the degree of Doctor of Science (Technology) to be presented with due permission for public examination and criticism in lecture hall 1382 at Lappeenranta University of Technology, Lappeenranta, Finland on the 1st of December, 2015, at noon. Acta Universitatis Lappeenrantaensis 666 Supervisors Professor Jukka Martikainen Laboratory of Welding Technology LUT School of Energy Systems Lappeenranta University of Technology Finland Associate Professor Paul Kah Laboratory of Welding Technology LUT School of Energy Systems Lappeenranta University of Technology Finland Reviewers Professor Leif Karlsson Department of Engineering Science University West Sweden Professor Thomas Boellinghaus Department of Component Safety Federal Institute of Material Research and Testing Germany Opponent Professor Leif Karlsson Department of Engineering Science University West Sweden ISBN 978-952-265-865-4 ISBN 978-952-265-866-1 (PDF) ISSN-L 1456-4491 ISSN 1456-4491 Lappeenrannan teknillinen yliopisto Yliopistopaino 2015 Abstract Muyiwa Olabode Weldability of high strength aluminium alloys Lappeenranta 2015 59 pages Acta Universitatis Lappeenrantaensis 666 Diss. Lappeenranta University of Technology ISBN 978-952-265-865-4, ISBN 978-952-265-866-1 (PDF), ISSN-L 1456-4491, ISSN 1456-4491 The need for reduced intrinsic weight of structures and vehicles in the transportation industry has made aluminium research of interest. Aluminium has properties that are favourable for structural engineering, including good strength-to-weight ratio, corrosion resistance and machinability. It can be easily recycled saving energy used in smelting as compared to steel. Its alloys can have ultimate tensile strength of up to 750 MPa, which is comparable to steel. -
Love That Door Catalog
Welcome Home. Nothing adds a “wow” factor to a new home design like wrought iron doors and this is the #1 reason many homeowners make this front door statement. The juxtaposition of iron with brick construction visually suggests a permanence that no synthetic building material can emulate. The single or double wrought iron doors, manufactured by Love That Door and available from Acme Brick Stone & Tile stores, have multi-hued designs that demand attention, especially when framed by the rich patina of brick. We have over 100 designs to choose from and can custom design and build anything you desire in wrought iron access doors, iron garages and access gates, iron wine cellar doors, lighting fixtures and more. Wrought Iron Access Gates and Doors offer greater security than traditional wood doors. Keep your family and office more secure with a low maintenance, durable and custom iron door while increasing your curb appeal. Wrought Iron makes a fine choice for many reasons, but none more important than security. 2 lovethatdoor.com • brick.com 3 Transform Your Home Customers are amazed by the transformation that their iron dooor makes to their property. Versatile, robust and beautiful, it’s little wonder that a growing number of individuals are deciding on iron doors as the best option. We ensure that every single component of your iron entry door is tested and styled for optimal performance and durability. From compression tested locks to heavy duty barrel hinges, every part of the products we produce is fashioned with an exemplary end result in mind. 4 lovethatdoor.com • brick.com 5 Within an Arm’s Reach. -
Advanced Aluminum Powder Metallurgy Alloys and Composites
ASM Handbook, Volume 7: Powder Metal Technologies and Applications Copyright © 1998 ASM International® P.W. Lee, Y. Trudel, R. Iacocca, R.M. German, B.L. Ferguson, W.B. Eisen, K. Moyer, All rights reserved. D. Madan, and H. Sanderow, editors, p 840-858 www.asminternational.org DOI: 10.1361/asmhba0001577 Advanced Aluminum Powder Metallurgy Alloys and Composites Ram B. Bhagat, The Pennsylvania State University POWDER METALLURGICAL PROCESS- bide whisker, however, is currently the most Selection of suitable composition of the ma- ING provides much finer and homogeneous widely utilized reinforcement for the DRA com- trix material is important to meet mechanical and microstructure, better mechanical properties, posites for obtaining high resistance to creep and physical property requirements of the aluminum- and near-net shape parts producibility for alumi- higher use temperatures. Early work on whisker matrix composites. Minor alloying additions in num alloys in comparison with ingot metallurgy reinforcement started in the 1960s. Brenner (Ref the wrought alloys are generally detrimental to (I/M). In addition to the conventional blending 7, 8) and Sutton (Ref 9, 10) used tx-Al203 the mechanical properties of the composites be- and consolidation of elemental or prealloyed whiskers to fabricate metal-matrix composites cause of undesirable interfacial reaction (Ref powders into near-net shape parts, emerging (MMCs). These early composites were not at- 26-28) during the P/M consolidation. The P/M processes such as mechanical alloying and rapid tractive because of their relatively low strength route for producing the discontinuously rein- solidification (RS) create composite powders and the high cost of the whisker. -
Implementation of Metal Casting Best Practices
Implementation of Metal Casting Best Practices January 2007 Prepared for ITP Metal Casting Authors: Robert Eppich, Eppich Technologies Robert D. Naranjo, BCS, Incorporated Acknowledgement This project was a collaborative effort by Robert Eppich (Eppich Technologies) and Robert Naranjo (BCS, Incorporated). Mr. Eppich coordinated this project and was the technical lead for this effort. He guided the data collection and analysis. Mr. Naranjo assisted in the data collection and analysis of the results and led the development of the final report. The final report was prepared by Robert Naranjo, Lee Schultz, Rajita Majumdar, Bill Choate, Ellen Glover, and Krista Jones of BCS, Incorporated. The cover was designed by Borys Mararytsya of BCS, Incorporated. We also gratefully acknowledge the support of the U.S. Department of Energy, the Advanced Technology Institute, and the Cast Metals Coalition in conducting this project. Disclaimer This report was prepared as an account of work sponsored by an Agency of the United States Government. Neither the United States Government nor any Agency thereof, nor any of their employees, makes any warranty, expressed or implied, or assumes any legal liability or responsibility for the accuracy, completeness, or usefulness of any information, apparatus, product, or process disclosed, or represents that its use would not infringe privately owned rights. Reference herein to any specific commercial product, process, or service by trade name, trademark, manufacturer, or otherwise does not necessarily constitute or imply its endorsement, recommendation, or favoring by the United States Government or any Agency thereof. The views and opinions expressed by the authors herein do not necessarily state or reflect those of the United States Government or any Agency thereof. -
20#Cross Framed Walk in 3714 V19K14.Cdr
TOURE Fixed Alcove Shower Door with window panel design Installation Instructions Size:39"x77" ●Please read these instructions in full before installation IMPORTANT ●Check that the shower surround has been installed to the manufacturer’s instructions. Please note - All product is supplied without a tray. ●Opening wall adjustments Adjustment =38.58"-38.97"x77"[(980-990)x1950mm] GENERAL SAFETY INSTRUCTIONS ● Do not fix the wall profile to newly plastered, painted or papered walls as chemical reaction may cause discoloration to the surface finish. ● lmportant: The wall plugs included in this pack are for solid walls only. If the product is to be mounted on a partition or stud wall, specialized fixings should be purchased separately. ●Fixing tips; A piece of insulating tape or a couple of layers of masking tape applied to the wall before marking out the fixing holes will help stop the drill from wandering, particularly on tiled surfaces. ●When working near a basin or bath insert the plug into the drain, this will help you avoid losing small parts. Also take care not to drop accessories or tools onto the bath or basin, use a towel or bathmat to protect delicate surfaces. ●CAUTION! Before drilling into any walls check that there are no hidden cables or pipes. Exercise great care when using power tools near water. The use of a residual current device (RCD) or cordless drill is recommended. Always double check the positioning and measurements before drilling holes. ●This product is heavy and requires two people during lifting and operations. ●Glass is delicate, support on cardboard to minimize risk of damage. -
Surveying and Drawing Instruments
SURVEYING AND DRAWING INSTRUMENTS MAY \?\ 10 1917 , -;>. 1, :rks, \ C. F. CASELLA & Co., Ltd II to 15, Rochester Row, London, S.W. Telegrams: "ESCUTCHEON. LONDON." Telephone : Westminster 5599. 1911. List No. 330. RECENT AWARDS Franco-British Exhibition, London, 1908 GRAND PRIZE AND DIPLOMA OF HONOUR. Japan-British Exhibition, London, 1910 DIPLOMA. Engineering Exhibition, Allahabad, 1910 GOLD MEDAL. SURVEYING AND DRAWING INSTRUMENTS - . V &*>%$> ^ .f C. F. CASELLA & Co., Ltd MAKERS OF SURVEYING, METEOROLOGICAL & OTHER SCIENTIFIC INSTRUMENTS TO The Admiralty, Ordnance, Office of Works and other Home Departments, and to the Indian, Canadian and all Foreign Governments. II to 15, Rochester Row, Victoria Street, London, S.W. 1911 Established 1810. LIST No. 330. This List cancels previous issues and is subject to alteration with out notice. The prices are for delivery in London, packing extra. New customers are requested to send remittance with order or to furnish the usual references. C. F. CAS ELL A & CO., LTD. Y-THEODOLITES (1) 3-inch Y-Theodolite, divided on silver, with verniers to i minute with rack achromatic reading ; adjustment, telescope, erect and inverting eye-pieces, tangent screw and clamp adjustments, compass, cross levels, three screws and locking plate or parallel plates, etc., etc., in mahogany case, with tripod stand, complete 19 10 Weight of instrument, case and stand, about 14 Ibs. (6-4 kilos). (2) 4-inch Do., with all improvements, as above, to i minute... 22 (3) 5-inch Do., ... 24 (4) 6-inch Do., 20 seconds 27 (6 inch, to 10 seconds, 403. extra.) Larger sizes and special patterns made to order. -
MICHIGAN STATE COLLEGE Paul W
A STUDY OF RECENT DEVELOPMENTS AND INVENTIONS IN ENGINEERING INSTRUMENTS Thai: for III. Dean. of I. S. MICHIGAN STATE COLLEGE Paul W. Hoynigor I948 This]: _ C./ SUPP! '3' Nagy NIH: LJWIHL WA KOF BOOK A STUDY OF RECENT DEVELOPMENTS AND INVENTIONS IN ENGINEERING’INSIRUMENTS A Thesis Submitted to The Faculty of MICHIGAN‘STATE COLLEGE OF AGRICULTURE AND.APPLIED SCIENCE by Paul W. Heyniger Candidate for the Degree of Batchelor of Science June 1948 \. HE-UI: PREFACE This Thesis is submitted to the faculty of Michigan State College as one of the requirements for a B. S. De- gree in Civil Engineering.' At this time,I Iish to express my appreciation to c. M. Cade, Professor of Civil Engineering at Michigan State Collegeafor his assistance throughout the course and to the manufacturers,vhose products are represented, for their help by freely giving of the data used in this paper. In preparing the laterial used in this thesis, it was the authors at: to point out new develop-ants on existing instruments and recent inventions or engineer- ing equipment used principally by the Civil Engineer. 20 6052 TAEEE OF CONTENTS Chapter One Page Introduction B. Drafting Equipment ----------------------- 13 Chapter Two Telescopic Inprovenents A. Glass Reticles .......................... -32 B. Coated Lenses .......................... --J.B Chapter three The Tilting Level- ............................ -33 Chapter rear The First One-Second.Anerican Optical 28 “00d011 ‘6- -------------------------- e- --------- Chapter rive Chapter Six The Latest Type Altineter ----- - ................ 5.5 TABLE OF CONTENTS , Chapter Seven Page The Most Recent Drafting Machine ........... -39.--- Chapter Eight Chapter Nine SmOnnB By Radar ....... - ------------------ In”.-- Chapter Ten Conclusion ------------ - ----- -. -
Methods to Check Dimensional Tolerances on Hollow Structural Sections
HSS METHODS TO CHECK DIMENSIONAL TOLERANCES ON HOLLOW STRUCTURAL SECTIONS HSS: TECHNICAL BROCHURE TABLE OF CONTENTS FOREWARD 1-2 Outside Dimensions The following is published as a guide 3-4 Wall Thickness for the purchaser of hollow structural 5 Length and Straightness sections (HSS). Methods of checking dimensional tolerances, stipulated 6 Squareness of Sides in Section 11 of ASTM A500-20,* are 7-8 Corner Radius discussed in detail. When checking tolerances for ASTM A847, ASTM 9-10 Twist A1085, ASTM A1065 or other material, 11 STI Member Producers the permissible variations may differ from what is given here; however, the method of measurement is the same. All excerpts from ASTM A500 are formatted For additional information, please with a gray background as seen here. contact the HSS manufacturer or the Steel Tube Institute. *Excerpts from ASTM A500 reprinted with permission from ASTM A500/A500M-20, copyright ASTM International, 100 Barr Harbor Drive, West Conshohocken, PA 19428. A copy of the complete standard can be obtained from ASTM International at www.astm.org. Steel Tube Institute Methods to Check Dimensional Tolerances on Hollow Structural Sections steeltubeinstitute.org Version: 11/20 OUTSIDE DIMENSIONS MEASURING ROUND TUBING 11. PERMISSIBLE VARIATIONS IN DIMENSIONS METHOD 11.1 Outside Dimensions: 11.1.1 Round Structural Tubing—The outside diameter shall not Refer to Example 1 for a typical application. vary more than ±0.5 %, rounded to the nearest 0.005 in. [0.1 1 Measure at a position at least 2 inches from either end mm], from the specified outside diameter for specified outside of the HSS. -
S2P Conference
The 9th International Conference on Semi-Solid Processing of Alloys and Composites —S2P Busan, Korea, Conference September 11-13, 2006 Qingyue Pan, Research Associate Professor Metal Processing Institute, WPI Worcester, Massachusetts Busan, a bustling city of approximately 3.7 million resi- Pusan National University, in conjunction with the Korea dents, is located on the Southeastern tip of the Korean Institute of Industrial Technology, and the Korea Society peninsula. It is the second largest city in Korea. Th e natu- for Technology of Plasticity hosted the 9th S2P confer- ral environment of Busan is a perfect example of harmony ence. About 180 scientists and engineers coming from 23 between mountains, rivers and sea. Its geography includes countries attended the conference to present and discuss all a coastline with superb beaches and scenic cliff s, moun- aspects on semi-solid processing of alloys and composites. tains which provide excellent hiking and extraordinary Eight distinct sessions contained 113 oral presentations views, and hot springs scattered throughout the city. and 61 posters. Th e eight sessions included: 1) alloy design, Th e 9th International Conference on Semi-Solid Pro- 2) industrial applications, 3) microstructure & properties, cessing of Alloys and Composites was held Sept. 11-13, 4) novel processes, 5) rheocasting, 6) rheological behavior, 2006 at Paradise Hotel, Busan. Th e fi ve-star hotel off ered a modeling and simulation, 7) semi-solid processing of high spectacular view of Haeundae Beach – Korea’s most popular melting point materials, and 8) semi-solid processing of resort, which was the setting for the 9th S2P conference. -
MEASURING and MARKING Tools
Measuring & Marking Measuring & Marking OUTLETS NATIONWIDE 522 Measuring & Marking Solutions for every aspect of measuring and marking for professionals in any business. All products are accurate to international specifications and carry our comprehensive warranty and lifetime replacement policy. 524-527 527 528-530 530-534 534-536 Tapes & Rules Measuring Wheels Squares & Bevels Measuring Gauges Dial Indicators & Stands 536 536-544 545-547 547-548 549 Counters Micrometers Verniers Calipers, Dividers & Scribers Compasses 550 551 551-553 553 554 Specialised Marking Tools Chalks, Crayons & Pencils Chalklines & Refills Marking Gauges Stencils 554-555 556 Levels Surveyors Tools Measuring & Marking AVAILABLE FROM SELECTED 523 Quick Find Index DISTRIBUTORS NATIONWIDE POWER TAPE - SOFT GRIP WITH AUTOLOCK MEASURING TAPE - RUBBER ! Magnetic hook ! Top stop secures tape in place ! Non-slip grip rubber case is robust and impact resistant ! Clearly marked blade with ! Automatic blade lock (BLADE LOCKS ITSELF WHEN PULLED OUT) metric graduations ! ! Push button retrieval Extra tough impact resistant ABS case with sure-grip ! Chrome belt clip rubber shroud ! Power return blade glides back into case automatically with smooth rewind action Code Size MTS4800 3m x 16mm Code Size MTS4805 5m x 19mm RIC4167 3m x 13mm MTS4810 7.5m x 25mm RIC4170 5m x 19mm MTS4815 10m x 25mm RIC4180 7.5m x 25mm TAPE - SHOX MEASURING TAPE - ABS ! Positive brake action locks ! Expert quality, finely engineered tapes blade solidly in hand are renowned for reliability ! Sliding end