EDAG INSIGHTS 1/15 - EDAG Light Cocoon 1
Total Page:16
File Type:pdf, Size:1020Kb
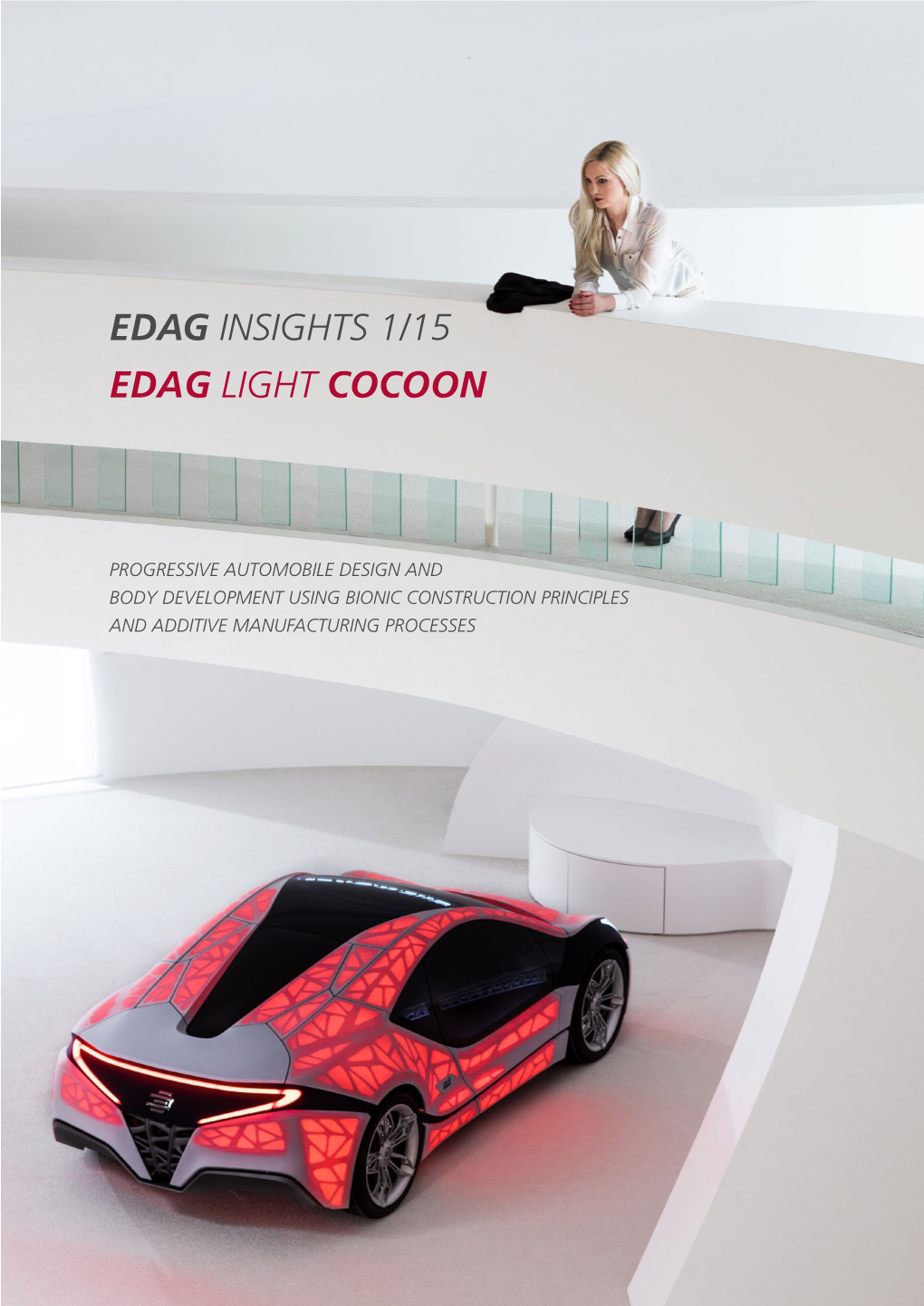
Load more
Recommended publications
-
Do You Want to Make Automotive Ideas Shine?
DO YOU WANT TO MAKE AUTOMOTIVE IDEAS SHINE? THE CHALLENGE FOR GRADUATES AND PROFESSIONALS IN AUTOMOTIVE DEVELOPMENT – AT EDAG. WHAT DO WE DO? ADVANCE MOBILITY! As one of Germany‘s largest independent Cars shape society, they alter our lives and our engineering service providers, we develop vehicle future. And since all cars are different, we are an components, modules, complete vehicles and extreme agile company with a constant strive for production systems for the major vehicle change. In other words: even our professionals manufacturers. That is the technical side. continuously learn. We are always taking new But we take things further than that: we want directions, looking for ways to improve. to move people! This means that, we not only That‘s why we are not just any engineering focus on the technical aspects of mobility, we service provider, but possibly the most exciting also concentrate on the value of our work. That one in the world! sounds idealistic but cars are no longer there just to be driven. WHO WE ARE: EDAG AT A GLANCE In 1969, Horst Eckard founded the company Our clients are the most reputable car „eckard design“ in Groß-Zimmern near manufacturers in the world. Darmstadt. Soon after this, our headquarters has Audi, BMW, Bugatti, Chrysler, Daimler, Fiat, Ford, moved to Fulda, where we started to specialise in Honda, Hyundai, Mitsubishi, Opel, Porsche, vehicle and production plant development. Since Renault, Seat, Skoda, Toyota, Volkswagen then, EDAG has grown enormously, and is now rely on our know-how. represented on four continents. In 2014, our headquarters moved to Wiesbaden. -
Engineering Analysis Q2 2020
Engineering Service Providers & ISVs Q2 2020 Analysis Pareekh Jain September 2020 Agenda Q2 2020 Analysis ▪ Indian Engineering Service Providers ▪ European Engineering Service Providers ▪ Global Engineering ISVs © 2020 Pareekh Consulting. All rights reserved. 2 Revenue and growth of Indian Engineering Service Providers in Q2 2020 Q2 2020 Service Provider Engineering Services Revenue Million QoQ Growth Persistent USD 131 3.1% HCL ERS USD 378 -9.0% LTTS USD 171 -12.5% Cyient USD 131 -12.5% Tata Elxsi USD 53 -13.0% KPIT USD 65 -13.8% Note: TCS, Wipro, Infosys, Tech Mahindra, QuEST Global, Tata Technologies, Cognizant, and Global Logic will also make in the list of India-centric ESP with quarterly revenue > USD 50 Million. Their financial details of engineering business are not available. © 2020 Pareekh Consulting 3 Summary of engineering services landscape for Indian providers Summary of engineering service providers' industry wise growth trends based on Q2 2020 (FY Q1, 2020) results and discussion with stakeholders. ▪ Growth: Software/ ISV, Medical device/ healthcare ▪ Flat: Telecom/ media ▪ Decline: Automotive, Aerospace, Industrial/ Oil & Gas News of large deals/ carve outs in ISV, Automotive and Telecom from Persistent, KPIT, LTTS and HCL. Hope Q1 has bottomed out and service providers start showing some QoQ growth in Q2. Bottom Line: The deal signing and pipeline is encouraging. © 2020 Pareekh Consulting. 4 Agenda Q2 2020 Analysis ▪ Indian Engineering Service Providers ▪ European Engineering Service Providers ▪ Global Engineering ISVs -
EDAG Group Company Presentation
EDAG Group Partner to the International Mobility Industry Agenda Presentation of the EDAG Group 1 Expertise - Key figures - Sites Range of EDAG Services 2 Portfolio and References Why choose EDAG? 3 Innovations, Awards, Certification Page 2 © Copyright 2018 EDAG Engineering GmbH. All rights reserved. Development with passion – that's what we stand for EDAG. One of the largest independent engineering experts in the automotive industry „ We are the experts in the development of vehicles, production plants and the optimisation of your processes. We see mobility as an integral approach. „ Our expertise covers the integrated development and optimisation of vehicles, production facilities, derivatives and modules. This has made us what we are today: the acknowledged, independent engineering experts for the automotive industry. Page 3 © Copyright 2018 EDAG Engineering GmbH. All rights reserved. Our history Founding of the Horst Germany: ATON Group Acquisition of the BFFT Eckard design office 10 facilities close to becomes the main Group in Groß-Zimmern the major automobile shareholder of manufacturers EDAG. 1969 1995 2006 2013 1970 1987 2012 2016 Foundation of First steps toward Acquisition of New technology company globalisation, first Rücker Group centre with room for headquarters in European subsidiary in with 2500 1500 employees is Fulda Barcelona employees built in Wolfsburg 49 years' experience in automotive engineering! Page 4 © Copyright 2018 EDAG Engineering GmbH. All rights reserved. The Executive Board of EDAG Engineering GmbH Harald Poeschke Cosimo De Carlo Jürgen Vogt COO CEO CFO Page 5 © Copyright 2018 EDAG Engineering GmbH. All rights reserved. EDAG Worldwide Sales / project office Locations Company headquarters Gothenbur g Helmond Kaluga Royal Warsaw Leamington Spa Mladá Boleslav Troy Wiesbaden Prague Changchun Belmont Arbon Györ Turin Seoul Yokohama Spartanburg Sant´Agata B. -
We Develop the Future Edag Annual Report 2016 Selected Performance Figures from Consolidated Financial Statement
WE DEVELOP THE FUTURE EDAG ANNUAL REPORT 2016 SELECTED PERFORMANCE FIGURES FROM CONSOLIDATED FINANCIAL STATEMENT (in € million or %) 2016 2015 Vehicle Engineering 454.3 455.0 Production Solutions 118.4 119.8 Electrics/Electronics 152.3 158.9 Consolidation/Others - 10.1 - 11.7 Total revenues and changes in inventories 714.9 722.0 Growth of core business: Vehicle Engineering - 0.2 % 9.0 % Production Solutions - 1.2 % 12.6 % Electrics/Electronics - 4.2 % 28.4 % Total change of revenues and changes in inventories - 1.0 % 13.7 % Vehicle Engineering 28.1 45.7 Production Solutions 11.9 15.7 Electrics/Electronics 4.2 11.5 Others - 0.4 - 0.3 Adjusted EBIT 43.8 72.6 Vehicle Engineering 6.2 % 10.0 % Production Solutions 10.0 % 13.1 % Electrics/Electronics 2.8 % 7.2 % Adjusted EBIT-margin 6.1 % 10.1 % Profit or loss 18.0 36.3 Earnings per share (€) 0.72 1.45 (in € million or %) 12/31/2016 12/31/2015 Fixed assets 186.8 190.5 Net working capital 99.6 95.2 Net financial debt - 98.1 - 93.4 Provisions - 39.6 - 37.7 Held for sale 4.1 0.6 Equity 152.8 155.2 Balance sheet total 430.4 475.5 Equity/BS total 35.5 % 32.6 % Net financial debt/Equity 64.2 % 60.2 % (in € million or %) 2016 2015 Operating cash flow 51.8 27.6 Investing cash flow - 27.3 13.7 Free cash flow 24.5 41.3 Financing cash flow - 76.4 - 9.7 Adjusted Cash Conversion Rate1 57.0 % 66.7 % CapEx 27.9 30.3 CapEx/Revenues and changes in inventories 3.9 % 4.2 % 1 Adjusted Cash Conversion is defined as Adjusted EBIT before depreciation and amortization less capital expenditures divided by Adjusted EBIT before depreciation and amortization. -
Medical Electronics 2 | Medical Electronics
Henkel Solutions Medical Electronics 2 | Medical Electronics Overview Accurate diagnostics, improved alternative treatments and patient monitoring are all critical needs of the medical electronics industry. But, none of this is possible without the high-reliability medical devices used to facilitate these objectives. Henkel’s advanced semiconductor packaging and assembly materials are delivering the solutions needed to address the demanding requirements of next- generation medical electronics. There’s no doubt that improving access to patients’ data has enabled medical professionals to provide personalized care and has expanded early intervention programs for the treatment of chronic conditions. Technologies such as implantable medical devices and patient monitoring sensors that make this type of patient care possible now require a form factor that is only achieved through advanced electronic devices, materials and assembly methods. Henkel’s technical expertise, low-risk partnership proposition, innovation philosophy, world-class global support infrastructure and history as a leading formulator of market-leading materials ensure that we will enable the future advancement of the medical electronics industry. Medical Electronics | 3 4 | Medical Electronics Index Medical Inks & Coatings Adhesives COB Encapsulants PCB Protection Solder Materials Underfills Silver/ Electrically Non- Low Electrically Non- Glob Tops Conformal Liquid Silver Water-Based Conductive Conductive Dam Fill Pressure Pastes Wires Capillary Flow Edgebond Conductive Inks -
Edag Annual Report 2018 Selected Performance Figures from Consolidated Financial Statement
50 YEARS OF ENGINEERING PERFORMANCE EDAG ANNUAL REPORT 2018 SELECTED PERFORMANCE FIGURES FROM CONSOLIDATED FINANCIAL STATEMENT (in € million or %) 2018 2017 revised* Vehicle Engineering 490.3 452.1 Production Solutions 159.2 130.8 Electrics/Electronics 155.5 148.5 Consolidation/Others - 12.7 - 12.9 Total revenues1 792.3 718.5 Growth of core business: Vehicle Engineering 8.4% -0.5% Production Solutions 21.7% 10.5% Electrics/Electronics 4.7% -2.5% Total revenues1 10.3% 0.6% Vehicle Engineering 30.4 19.6 Production Solutions 9.8 8.9 Electrics/Electronics 7.4 5.8 Others - - Adjusted EBIT 47.6 34.3 Vehicle Engineering 6.2% 4.3% Production Solutions 6.1% 6.8% Electrics/Electronics 4.8% 3.9% Adjusted EBIT-margin 6.0% 4.8% Profit or loss 25.5 15.5 Earnings per share (€) 1.02 0.62 1 The performance figure “revenues“ is used in the sense of gross performance (sales revenues and changes in inventories) in the following. * The previous year was adjusted due to amendments made to the international accounting standard IFRS 15. Comparability of the revenue changes from 2017 with the same period in the previous year (2016) is only marginally restricted by the first-time adoption of IFRS 15 on January 1, 2017. (in € million or %) 12/31/2018 12/31/2017 revised* Fixed assets 193.5 195.1 Net working capital 87.1 93.0 Net financial debt - 82.9 - 103.6 Provisions - 43.4 - 40.2 Held for sale - 3.2 Equity 154.3 147.5 Total assets 488.0 442.6 Equity/BS total 31.6% 33.3% Net financial debt/Equity 53.7% 70.2% (in € million or %) 2018 2017 revised* Operating Cash-Flow 68.9 51.6 Investing Cash-Flow - 21.5 - 28.5 Free Cash-Flow 47.4 23.1 Financing Cash-Flow 3.2 - 27.7 Adjusted Cash Conversion Rate2 68.1% 62.1% CapEx 22.2 21.7 CapEx/Revenues and changes in inventories 2.8% 3.0% 2 The key figure "adjusted cash conversion rate" is defined as the adjusted EBIT before depreciation, amortization and impairment less gross investments divided by the adjusted EBIT before depreciation, amortization and impairment. -
Edag Group Sustainability Report 2019 2 I Management Statement
EDAG GROUP SUSTAINABILITY REPORT 2019 2 I MANAGEMENT STATEMENT Holger Merz · CFO Cosimo De Carlo · CEO MANAGEMENT STATEMENT I 3 STATEMENT OF THE GROUP EXECUTIVE MANAGEMENT Dear Sir or Madam, With this Sustainability Report, we are for the first time publishing a separate document to inform you of our development, values and goals with regard to economic, ecological and social factors. Sustainability as a contribution to safeguarding the future of the EDAG Group Sustainability is of special importance at EDAG: it involves both a long-term business policy and the integration of ecological and social aspects in the management system. As a part of our corporate culture, it determines our actions with our business partners as well as our values, such as trust, transparency, reliability and fairness. It is therefore a contribution towards safeguarding the future of our company, and towards long-term economical and social development. As an internationally active company, EDAG makes a point of ensuring that human rights and accepted standards are complied with at our numerous locations across the globe, and affirms its support of the UN Global Compact. As one of the world's leading engineering companies in the automobile industry, it is also our intention to set benchmarks in the way we deal with each other, with business partners and the environment. In order to make this transparent for our partners, too, we have defined our standards of conduct in the EDAG Code of Conduct. It is in line with our value system to combine entrepreneurial action with ethical principles and thus, by acting with integrity, ensure compliance with legal regulations at all times. -
Virtual Performance Solution Optimizing Product Performance with Simulation
Virtual Performance Solution Optimizing Product Performance with Simulation Featuring PAM-CRASH www.esi-group.com Optimize your product development cycle thanks to Virtual Performance Solution multi-domain, concurrent engineering using a single helps improve the efficiency of your Computer Aided core model. Engineering workflows during product development. Gain time, flexibility, quality and lower costs while accelerating your development cycle. Leverage concurrent engineering and optimize Crash and safety design variants. NVH and dynamics . Account for manufacturing conditions to improve the accuracy and reliability of your results. “Using a single core Multi-domain model allows us to Single core model Comfort perform faster design Statics and strength changes, giving us a competitive advantage. Furthermore, the calculation with the Implicit module is two times faster and uses less memory.” Interior acoustics Eberhard Keim, CAE Department Non linear kinematics Manager, EDAG Ingolstadt. “Virtual Performance Solution allows cost BENEFITS and time savings in our . Master design iterations with a single core model and cut cost and time by saving model translation tasks between crash, safety, comfort, statics, Product Development dynamics, NVH, interior acoustics and durability. Cycle.” . Reduce design iterations and optimize safety margins by improving quality and predictability thanks to contacts, nonlinearities, and Mr. Kazuhiro Obayashi, Integrated manufacturing history handling. CAE Department Manager, . NISSAN MOTOR CO. LTD. Decrease -
Flyer Airbag
AIRBAG VEHICLE SAFETY TESTING YOUR GLOBAL MOBILITY ENGINEERING EXPERTS Nowadays a large number of different safety systems are Overview of our services installed in modern vehicles of all classes. The systems are • Conduction of airbag bench tests in various designed to prevent accidents (active systems) or reduce development phases for driver-, co-driver-, the impact of accidents (passive systems). As well as seat knee, curtain and side airbags at temperatures belts, airbags belong to the most important safety features from -40°C to +90°C of a vehicle. · Development tests with prototypes Many types of different airbags need to be integrated in a · Release tests with “new” and vehicle for the optimal protection of the occupants during “environmentally aged” parts a collision. · Series monitoring (quality control) · After Sales (e.g. cost reduction, Airbags are located in the steering wheel, the instrument further system development) panel, behind the pillar covers or inside the headliner. Depending on accident case, the usually invisible airbags • Test result analysis ignite within a few milliseconds. • Development and production for airbag environment (e.g. covers) What matters now is the right “unfolding”! We make sure that the airbags are opening correctly • Simultaneous testing with up to six and fulfil their protective function. high-speed cameras • Parallel development using CAE-simulation The proper test bench for all cases We are conducting the tests inside various climatic chambers within vehicle environment or in structural replicas (e.g. seats and covers). Tests will be recorded by most modern high- speed cameras, placed at various positions – optionally inside the climatic chamber. -
CAR: Identifying Real World Barriers to Implementing Lightweighting
Identifying Real World Barriers to Implementing Lightweighting Technologies and Challenges in Estimating the Increase in Costs JAY BARON, PH.D. CENTER FOR AUTOMOTIVE RESEARCH 3005 BOARDWALK, STE. 200 ANN ARBOR, MI 48108 JANUARY 2016 Table of Contents Executive Summary .......................................................................................................................................... 1 The Drive to Lightweighting: Implementing Lightweighting Technologies - Real World Barriers and Estimating Increased Cost ................................................................................................................................ 3 Lightweighting is Not New ............................................................................................................................... 5 New Technology Qualification Takes Time ...................................................................................................... 6 Global Platforms Limit Flexibility and Optimization Opportunity.................................................................... 7 Vehicles are Designed with Many Attributes................................................................................................. 10 Sunk Cost and Infrastructure Limit Speed of Introduction ............................................................................ 13 There is no Known Average U.S. Vehicle ....................................................................................................... 14 Conclusion ..................................................................................................................................................... -
Gibt Es Einen Europaspezifischen Entwicklungsweg in Der Automobilindustrie?
A Service of Leibniz-Informationszentrum econstor Wirtschaft Leibniz Information Centre Make Your Publications Visible. zbw for Economics Jürgens, Ulrich Working Paper Gibt es einen europaspezifischen Entwicklungsweg in der Automobilindustrie? WZB Discussion Paper, No. SP III 2004-301 Provided in Cooperation with: WZB Berlin Social Science Center Suggested Citation: Jürgens, Ulrich (2004) : Gibt es einen europaspezifischen Entwicklungsweg in der Automobilindustrie?, WZB Discussion Paper, No. SP III 2004-301, Wissenschaftszentrum Berlin für Sozialforschung (WZB), Berlin This Version is available at: http://hdl.handle.net/10419/49644 Standard-Nutzungsbedingungen: Terms of use: Die Dokumente auf EconStor dürfen zu eigenen wissenschaftlichen Documents in EconStor may be saved and copied for your Zwecken und zum Privatgebrauch gespeichert und kopiert werden. personal and scholarly purposes. Sie dürfen die Dokumente nicht für öffentliche oder kommerzielle You are not to copy documents for public or commercial Zwecke vervielfältigen, öffentlich ausstellen, öffentlich zugänglich purposes, to exhibit the documents publicly, to make them machen, vertreiben oder anderweitig nutzen. publicly available on the internet, or to distribute or otherwise use the documents in public. Sofern die Verfasser die Dokumente unter Open-Content-Lizenzen (insbesondere CC-Lizenzen) zur Verfügung gestellt haben sollten, If the documents have been made available under an Open gelten abweichend von diesen Nutzungsbedingungen die in der dort Content Licence (especially -
Who's Who in European Automotive Design
July 21, 2008 www.autonewseurope.com Design 2008 Who’s who in European automotive design Thousands of men and women have had their hands on the cars we are driving today. They have created eye-pleas- ing winners such as the Fiat 500, Nissan Qashqai and Audi TT, but they also have given us flops such as the Peugeot 1007, Jaguar X-Type and Renault Modus. Regardless of whether their last cars were winners or losers, Europe’s top stylists are at work on what they hope will be their next masterpieces. Below is a comprehensive list of the industry’s top designers and where they are doing their work. ASTON MARTIN Advanced Design Sindelfingen Studio: JOHNSON CONTROLS Marek Reichman, design director Dept DE/APS, HPC X805 Merkenich Design Center Andreas Maashoff, design director industrial 71059 Sindelfingen, Germany John Andrews Entwicklungszentrum design & craftsmanship Europe Senior manager: Andreas Langenbeck Spessartstrasse Studio: 50725 Cologne, Germany Studio: Banbury Road, Gaydon, Largo Spluga, 1 Industrial Design Studio Europe Gaydon, Warwickshire CV35 0DB, UK 22100 Como, Italy Johnson Controls Studio director: Michele Jauch-Paganetti HEULIEZ Automotive Experience Alain Masquelet, research and development director European Headquarters AUDI 17742 Cowan Street Industriestrasse 20-30 Wolfgang Egger, head of Audi group design Irvine, California 92614, USA Jean-Marc Guillez, advanced engineering director 51399 Burscheid, Germany Studio director: Gorden Wagener Stefan Sielaff, head of Audi design Studio: Studios: Advanced Design Center of Japan