Effects of Selected Casting Methods on Mechanical Behaviour of Al-Mg-Si Alloy
Total Page:16
File Type:pdf, Size:1020Kb
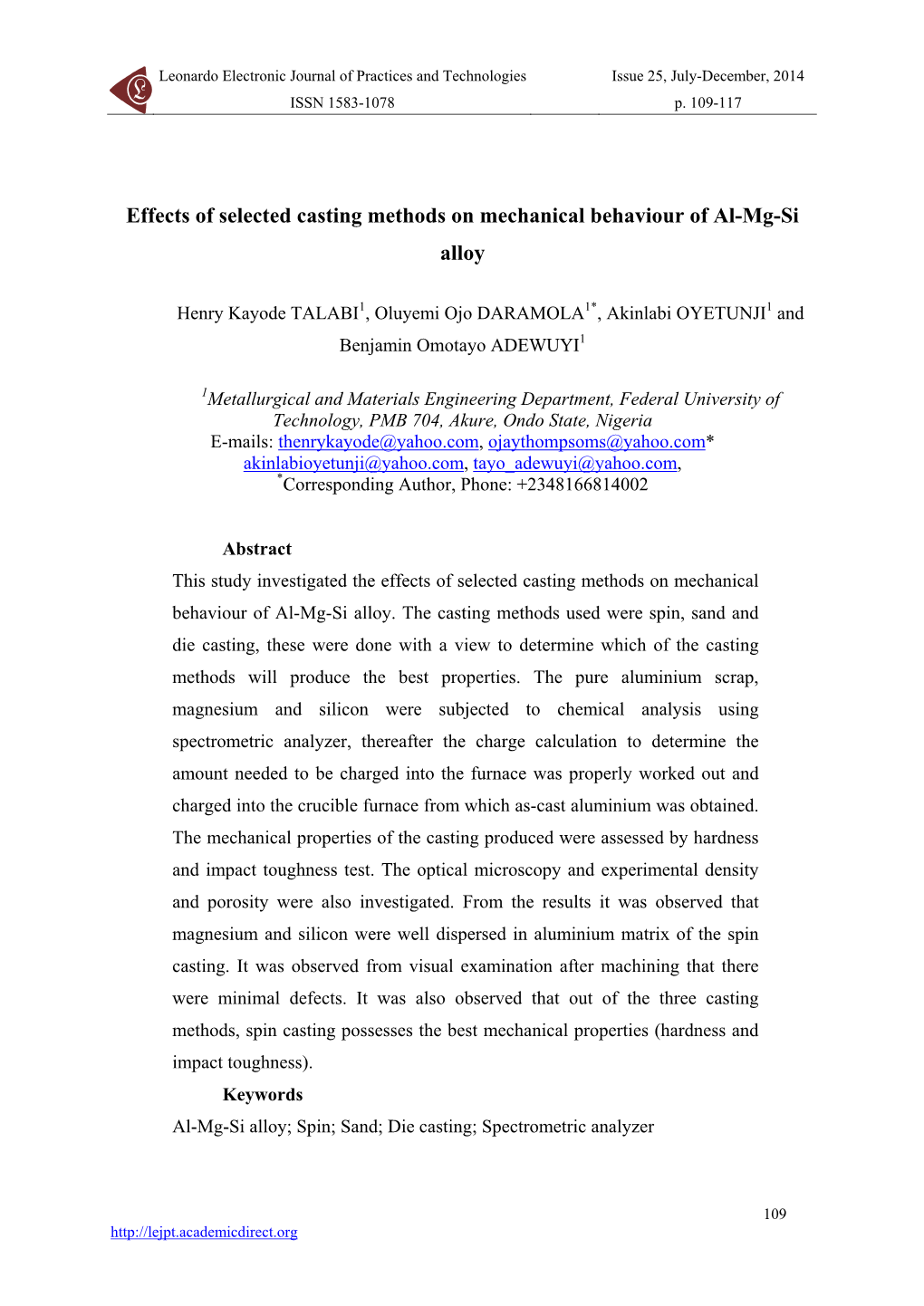
Load more
Recommended publications
-
Extrusion Blow Molding ___Fiberg
Woman Owned Small Busines • ITAR Certified 710 South Patrick Drive • Satellite Beach, Florida 32937 321.536.2611 • [email protected] • www.rapidps.com ABS • POLYCARBONATE • POLYPHENYLSULFONE • ULTEM ADVANCED APPLICATIONS _____________________________ RTV MOLDS __________________________ Parts produced can be used in lots of different manufacturing applications. Parts built using RPS provide the fast, accurate and af- Parts can be painted, electroplated and drilled. They can also be used in ad- fordable patterns that drive RTV molding. By replacing vanced applications such as investment castings, RTV molding and sand cast- machined patterns, the entire process can be com- ing. Each application includes the benefits to using an RPS part with detailed pleted in 2-3 days. And unlike machining, complex instructions. and intricate shapes have no effect on the time or cost for the RPS pattern. ELECTROPLATING ____________________ Electroplating deposits a thin layer of metal on the RTV MOLDING SOLUBLE CORE _________ surface of a part built. This improves the part’s me- Complex geometries normally requiring core removal chanical properties and gives the appearance of pro- such as curved hoses, water tanks, bottles, and arterial duction metal or plated parts and provides a hard, structures are good examples where it may be helpful wear-resistant surface with reflective properties. to use this alternative method. Instead of building the core in thermoplastic material (traditional RPS build EXTRUSION BLOW MOLDING __________ process) the mold is built in the Water Soluble sup- Polycarbonate RPS molds are used in the blow port material making it easy to dissolve away the mate- molding process, reducing lead time and expense. -
6 Simple Steps to Becoming a Lost Wax Casting Pro,The Evolution Of
6 Simple Steps to Becoming a Lost Wax Casting Pro Lost wax casting blends old and new in truly remarkable fashion. Our industry is constantly changing, adapting ancient techniques to modern technology. So, we’ve asked our experts to walk us through lost wax casting: STEP 1 – PATTERN Wax patterns are made by one of the following ways: carving, build-up, hand forming, or mold reproduction. STEP 2 – SPRUING OR SETTING UP Spruing is the leading cause of shrinkage porosity, or the pits you see during polishing. Fix this by ensuring the following: • The sprue should be thicker than the heaviest part of the pattern. • It should also be attached to the heaviest part of the pattern as well. • The sprue should be no longer than is absolutely necessary. These are much more effective than looking for that optimum (magical) cast temp. STEP 3 – INVESTING Investing is more chemistry than craft. Measure your powder and water and follow your supplier’s instructions for mixing, curing, and burnout. Keep this in mind: your casting surface is only as good as your wax and investing procedures. • Weigh investment material and measure water according to manufacturer’s recommendation. • Fill flask containing wax pattern and either vacuum or vibrate to remove air from the slurry. • Allow invested mold to air-dry for two hours or more before starting the burnout. STEP 4 – BURNOUT • Place invested flask in furnace preheated to 300ºF. Hold at this temperature for one hour or until the wax has drained. • Raise temperature at the rate of 300º/400ºF per hour until temperature of 1350ºF is reached. -
MSL Engineering Limited Platinum Blue House 1St Floor, 18 the Avenue Egham, Surrey, TW20 9AB
SMR Final Report 121404 Purpose of Issue Rev Date of Issue Author Agreed Approved Issued for information 0 Aug 2004 SM Issued for internal comment 1 November 2004 AFD DJM JB Issued as Final Report 2 December 2004 AFD DJM JB This Final report has been reviewed and approved by the Mineral Management Service. Approval does not signify that the contents necessarily reflect the views and policies of the Service, nor does mention of trade names or commercial products constitute endorsement or recommendation for use. This study was funded by the Mineral Management Service, U.S. Department of the Interior, Washington, D.C., under Contract Number 1435-01-04-CT-35320 ASSESSMENT OF REPAIR TECHNIQUES FOR AGEING OR DAMAGED STRUCTURES Project #502 DOC REF C357R001 Rev 1 NOV 2004 MSL Engineering Limited Platinum Blue House 1st Floor, 18 The Avenue Egham, Surrey, TW20 9AB Tel: +44 (0)1784 439194 Fax: +44 (0)1784 439198 E-mail: [email protected] C357R001Rev 2, December 2004 MMS Project #502 NUMBER DETAILS OF REVISION 0 Issued for information, August 2004 1 Issued for comment, November 2004. Extensive revisions throughout, including restructuring of report. 2 Issued as Final Report, December 2004. Conversion table added, Figure showing clamp details to avoid added, and general editorial revisions. C357R001Rev 2, December 2004 MMS Project #502 Assessment of Repair Techniques for Ageing or Damaged Structures By Dr. Adrian F Dier MSL Services Corporation Final Project Report: ASSESSMENT OF REPAIR TECHNIQUES FOR AGEING OR DAMAGED STRUCTURES MMS Project Number 502 November 2004 C357R001Rev 2, December 2004 i This Final report has been reviewed a nd approved by the Mineral Management Service. -
Morphing Loops
SPRING SM 2014 The Loop THE JOURNAL OF FLY CASTING PROFESSIONALS MORPHING LOOPS “All loops morph throughout the cast, from when the loop first begins to bud until it turns over and straightens. Mac Brown - Page 12 Cover Photo: Leslie Holmes, Cross-Body Cast Photo: Gardiner Mitchell THE LOOP - SPRING 2014 SM Policy Making - And Making Your Voice Heard IN THIS ISSUE The heart of the IFFF Casting Instructors’ Certification are creating policy for. A list of the committees and Program (CICP) is its committee members - those committee descriptions can be found at: Letter To The who create the framework for policies which affect http://www.fedflyfishers.org/Casting/ Editors P. 3 all certified instructors. Ultimately, the Casting HistoryGovernance/CastingCommittees.aspx Board of Governors signs off on policy (by way of From Don Simonson with the 2014 CBOG Awards review and vote for implementation), but committee From CI to MCI P. 5 committee: members create the ideas, which then mature through committee discussion. The Casting Board of Governors (CBOG) would like The Trouble you to submit nominations for the 2014 CBOG Awards With Skagit P. 8 When new casting policy is announced, often the by March 25. announcement does not include a justification for the • Lifetime Achievement in Fly Casting Instruction Loop Morphing new policy, no history, no discussion about why the P.11 • Mel Krieger Fly Casting Instructor policy is needed. And we instructors are sometimes • Governor’s Mentoring and the Governor’s Pin. left wondering why this policy came about. The Flyfishing editorial staff at The Loop feels that this journal can Redfish P.16 To learn more about the criteria for the awards provide a much needed look at the policies which and the nomination process go to the FFF Website affect everyone in the casting instruction program. -
Rolls for the Food Industry SIWACO Gmbh a Member of the Irle Group
ROLLS FOR THE FOOD INDUSTRY SIWACO GMBH A MEMBER OF THE IRLE GROUP We are specialised in wear resistant rolls and finished castings. Our technical expertise combined with the power of the IRLE GROUP offers cast rolls and products as well as reliable roll-services with an attractive price-performance ratio and short delivery times. Essential parts of our business are wear resistant rolls and finished castings as well as an optimal treatment of rolls, considering the specific requirements of every application. Our rolls are manufactured according to the utmost modern metallurgy MORE THAN 300 and technical treatment standards and by experienced and qualified ex- YEARS OF FOUNDRY perts by WALZEN IRLE in Germany and by its subcompany IRLE KAY JAY ROLLS in India. In 2007 a joint-venture was established with the Indian EXPERTISE, Company Kay Jay Rolls Pvt. Ltd., Panchkula, India. Both parties agreed 200 YEARS OF ROLL to build and operate an iron foundry near Chandigarh. For this „IRLE KAY CASTING JAY ROLLS Pvt. Ltd.“ has been founded to produce rolls for the food in- dustry and stretch reducing rolls for the tube and wire industry. 3 SIWACO ROLLS ARE PRODUCED FOR ROLLS FOR THE THE PROCESSING OF • cereals, FOOD INDUSTRY • cotton seed • cocoa beans, • coffee beans, The production of food using rolls for such processes as squeezing, milling, grating, breaking, refi- • oilseeds such as ning or flaking put special demands on the type of rolls used. • soybeans, • rape-oil seeds & canola, The performance and quality of the rolls determine the quality of the products to be produ- • sunflower seeds, ced and the economic efficiency of the production. -
March/April 2015 Issue
Issue 244 March/April 2015 Turkey B.A.S.S. DNR TIPS News Updates Outdoor Photos March/April 2015 ~ Page 2 Advertise in the ALSO ON THE W.Va. Sportsman INTERNET Promote Your Business Statewide In Business LOWER Advertise RATES Special THAN Sales SIMILARand Events PUBLICATIONS24 YEARS Reach Thousands of Potential Customers LOW ADVERTISING RATES /1/15 Page.......$28 6 WEEK RATES 1/4 Page..........$82 1/10 Page.......$39 1/3 Page........$100 Magazine 1/6 Page.........$65 1/2 Page........$135 1/5 Page.........$72 2/3 Page........$150 Volume 1 Issue 244 COLOR FULL PAGE INSIDE....$195 Publisher and Editor EXTRA BACK PAGE................$240 Mark A. Goudy For Advertising Information In Contributing Editors RATES START AT: The Number One Outdoor West Virginia Division Of Publication In West Virginia Natural Resources $28 for 6 weeks CONTACT: W. Va. Sportsman For This Size Ad No Subscriptions Offered P.O. Box 5521 Printed Every Six Weeks. Less Than A 62 Cents Vienna, WV 26105 A Day! 304-482-7217 W.Va. Sportsman [email protected] P.O. Box 5521 Vienna, WV 26105 100% OWNED & OPERATED IN WV 304-482-7217 Email [email protected] www.wvasportsman.net Attention Bass Fishermen! All Rights Reserved Get Your Name On Our Cover Photo Mail-List For Bass Tournaments Large muskies are often caught In 2015 in the winter months for those that don't mind the cold weather. Robert Thaxton was fishing on Fill Out The Form Below the Kanawha River on December To Be Placed On The Mail List 14th. He caught and released this Clip & Mail To: 51 inch musky that weighed 41 Bass Sportsman Name__________________________________________________ 1/2 pounds. -
Centrifugal Casting
ASM Handbook, Volume 15: Casting Copyright © 2008 ASM International® ASM Handbook Committee, p 667-673 All rights reserved. DOI: 10.1361/asmhba0005257 www.asminternational.org Centrifugal Casting Sufei Wei, The Centrifugal Casting Machine Company, and Steve Lampman, ASM International CENTRIFUGAL CASTING is one of the density and freedom from oxides, gases, and the rotating mold. For example, with a vertical largest casting branches in the casting industry, other nonmetallic inclusions. When casting mold axis, the resultant force on the liquid is accounting for 15% of the total casting output solid parts, the pressure from rotation allows constant. This is not the case in a horizontal of the world in terms of tonnage. Centrifugal thinner details to be cast, making surface details mold. The other difference between horizontal casting was invented in 1918 by the Brazilian of the metal-cast components more prominent. and vertical mold orientation is the speed Dimitri Sensaud deLavaud, after whom the pro- Another advantage of centrifugal casting is the obtained by the molten metal as it spins around cess was named. DeLavaud’s invention elimi- elimination or minimization of gates and risers. the mold. When metal is poured into the hori- nated the need for a central core in the pipe zontally rotating mold, considerable slip occurs mold, and the mold was water cooled, allowing between the metal and the mold such that the for a high rate of repeated use. The technique Centrifugal Casting Methods metal does not move as fast as the rotating uses the centrifugal force generated by a rotat- mold. To overcome this inertia, the metal must ing cylindrical mold to throw molten metal Centrifugal casting machines are categorized be accelerated to reach the mold rotation speed. -
Developing a Bearing Spin-Casting Facility
Developing a Bearing Spin-Casting Facility Chanel O’Connor Dr. Nathan Scott School of Mechanical Engineering, University of Western Australia Mark Smart Verve Energy Abstract Verve Energy currently uses the pour casting technique to refurbish their steam and gas turbine whitemetal bearings. However the alternative of using spin-casting, which is currently not available in Western Australia, offers a number of potential benefits. The objective of the project therefore is to identify these benefits and provide technical details of the machinery, equipment and materials required to develop a spin-casting facility, together with estimates of the total expected capital and operating costs. Current estimates value the facility at $1.89 million dollars with an investment of $568,200 in equipment. The ultimate aim is to determine whether a spin-casting facility is a viable proposition in Western Australia, and if it is not, to identify the conditions in which it will become viable. The project will advance the current state of the art by providing the first design proposal for a purpose built bearing spin-casting facility in Australia. 1. Introduction Verve Energy is Western Australia’s leading energy provider, with a total generating capacity of just below 3000MW. The entity owns and operates several major power stations that are installed with a series of gas and steam turbines. Reliable operation of the turbines is critical to Verve’s business and as such it is essential that the turbines are maintained and that major components including the turbine rotor bearings are routinely repaired. The rotor bearings are made from steel and are internally lined with a tin-based whitemetal alloy several millimetres thick. -
Title of Thesis: a MANUFACTURING PROCESS and MATERIALS DESIGN ADVISOR
ABSTRACT Title of Thesis: A MANUFACTURING PROCESS AND MATERIALS DESIGN ADVISOR Name of degree candidate: Arnn Kunchithapatham Degree and Year: Master of Science, 1996 Thesis directed by: Dr. Edward B. Magrab Professor, Department of Mechanical Engineering. A computer assisted tool, called the DESIGN ADVISOR, has been developed to help obtain a compatible set of candidate materials and manufacturing processes in a fast and straightforward manner. Information for seventeen manufacturing processes includes animations, written descriptions, still pictures and geometric design rules; information for forty-two materials includes written information and data. The DESIGN ADVISOR determines candidate manufacturing processes based on user-specified levels of one or more of seven manufacturing attributes; namely, surface condition, dimensional accuracy, complexity of shape, size, production run or production rate, and cost. The determination of candidate materials is based on the user-specified levels of one or more of eleven material attributes; namely, yield strength/density, fracture toughness/density, elastic modulus/density, high temperature strength/density, density, magnetic properties, electrical resistivity, thermal distortion, thermal insulation, solvent resistance, and cost. It also determines the suitability of candidate manufacturing processes with the candidate materials, and ranks the suitability of each candidate material within each candidate manufacturing process. J A MANUFACTURING PROCESS AND MATERIALS DESIGN ADVISOR by Arun Kunchithapatham Thesis submitted to the Faculty of the Graduate School of the University of Maryland in partial fulfillment of the requirements for the degree of Master of Science 1996 (1 I Advisory Committee: Professor Edward Magrab, Chairman/Advisor Associate Professor David Bigio Assistant Professor Majorie Natishan ,, ' ' I'. DEDICATION To my parents ii ACKNOWLEDGMENTS I would like to thank my advisor Dr. -
103179644.Pdf
Metal Casting Basics Vol. 2 D I S CLLA I MER This information is provided "as is". The author, publishers and marketers of this information disclaim any loss or liability, either directly or indirectly as a consequence of applying the information presented herein, or in regard to the use and application of said information. No guarantee is given, either expressed or implied, in regard to the merchantability, accuracy, or acceptability of the information. Unauthorized duplication or distribution of this material in any form is strictly prohibited. Violators will be prosecuted to the fullest extent of the law. No part of this publication may be reproduced, stored in a retrieval system or transmitted in any form or by any means, electronic, mechanical, photocopying, recording or otherwise, without prior written permission from the author/publisher. The author, publisher, and distributor, of this product assume no responsibility for the misuse of this product, or for any injury, damage and/or financial loss sustained to persons or property as a result of using this book. While every effort has been made to ensure reliability of the information within, the liability, negligence or otherwise, or from any use, misuse, or abuse of the operation of any methods, strategies, instructions or ideas contained in the material herein is the sole responsibility of the reader. http://www.MetalCastingZone.com Page 2 Metal Casting Basics Vol. 2 Table of Contents DISCLAIMER .................................................................................... -
Rod & Gun Gazette, September 2005
Fin Fur & Feather Club, Inc. September 2005 Volume 7, Issue 1 Charles Bruckerhoff Editor-in-Chief Matt Bruckerhoff Mike Bruckerhoff Copy Editors Rod & Gun Gazette Letter from the Vice-President Dear Members, very fine leadership. Fishing, shooting challenge with pistol, Inside this issue: Service on the Club’s Execu- ever the great joy of young and rifle, and carbine; skirmishers tive Board for several years and old, continues to provide are popping and cracking at members with relaxation breakable as well as paper tar- 2005 FFF Picnic 2 as the Vice-President for the past four years have been a whether they are serious about gets. The bar tends to show a distinct pleasure for me. Dur- landing a fresh catch for dinner profit, which is a good thing. Skirmshing Update 3 ing this time, we accomplished or for much-needed practice The Club’s adoption of quality a number of very notable ob- with a fly rod or spin-casting software and systematic data Trap—Summer League 4 jectives. The skeet field renova- reel. Rifle continues its unique entry and analysis keeps mem- tion project, long in the dream- offerings in high power, with bers well-informed about our ing stage, is now a remarkably special time set aside for the finances. And, events for our Beef Brisket BBQ 6 beautiful shooting sports facil- Garand match and recently the children are nothing less than ity, including opportunity for long range .22 caliber match. outstanding, whether embed- Membership News 6 trap shooting. We bought the Likewise, pistol continues to ded in the Annual Picnic or last remaining contiguous piece attract the hand gun shooters. -
Catania Medallic Specialty Inc 2018 Catalog
Spin Cast Medals 1-5 day delivery. See page 30 and call for production availability. PRIORITY PRODUCTION! 3 Days 5 Days or Less! 2 Days 2 Days 1 Day 2 Days Antique Antique Antique Pewter Gold Silver Bronze 3 Days Page 1 Specialty Spin Cast Medals Photo Image Spin Cast Medals Page 2 Spin Cast Medals Single-Faced Spin casting involves using centrifugal force to make castings from a rubber or a silicone mold. Spin cast products are a great option for customers who are seeking medals at an economical price. Price Includes: Antique gold, silver, or bronze with laser engravable plating. 0.125” thick 2D artwork Shrink packaging See additional options on page 28. Art Charge: $80 (A) if usable vector line art with converted type is not provided. Production Time: 4 weeks from approved art plus delivery. Rushes are available. See page 30. SIZE 25 50 75 100 125 150 175 200 300 400 500 750 1000 (13A) 1-1/2" 12.63 6.63 5.14 4.28 3.85 3.53 3.25 3.10 2.76 2.50 2.42 2.20 2.14 1-3/4" 13.59 6.98 5.46 4.71 4.26 3.92 3.70 3.64 3.19 3.00 2.95 2.68 2.61 2" 14.77 7.38 5.89 5.14 4.71 4.49 4.28 4.07 3.64 3.40 3.32 3.21 3.06 2-1/4" 15.19 8.24 6.42 5.89 5.35 4.92 4.71 4.58 4.15 3.96 3.83 3.75 3.64 2-1/2" 16.05 9.10 7.49 6.42 5.93 5.67 5.46 5.33 4.86 4.71 4.58 4.41 4.32 2-3/4" 16.26 9.48 8.03 7.28 6.85 6.40 6.18 6.03 5.76 5.50 5.35 5.22 5.11 3" 16.67 10.59 9.10 8.30 7.90 7.58 7.34 7.17 6.78 6.63 6.46 6.40 6.25 3-1/4" 16.88 11.13 9.61 8.77 8.35 8.03 7.75 7.60 7.28 7.00 6.89 6.74 6.68 3-1/2" 17.55 12.20 10.68 9.95 9.42 9.18 8.99 8.75 8.35 8.17 8.09 7.92 7.83 Page 3 Spin Cast Medals Double-Faced Price Includes: Antique gold, silver, or bronze with laser engravable plating.