Chapter 6 Spin Casting of Zinc Alloy
Total Page:16
File Type:pdf, Size:1020Kb
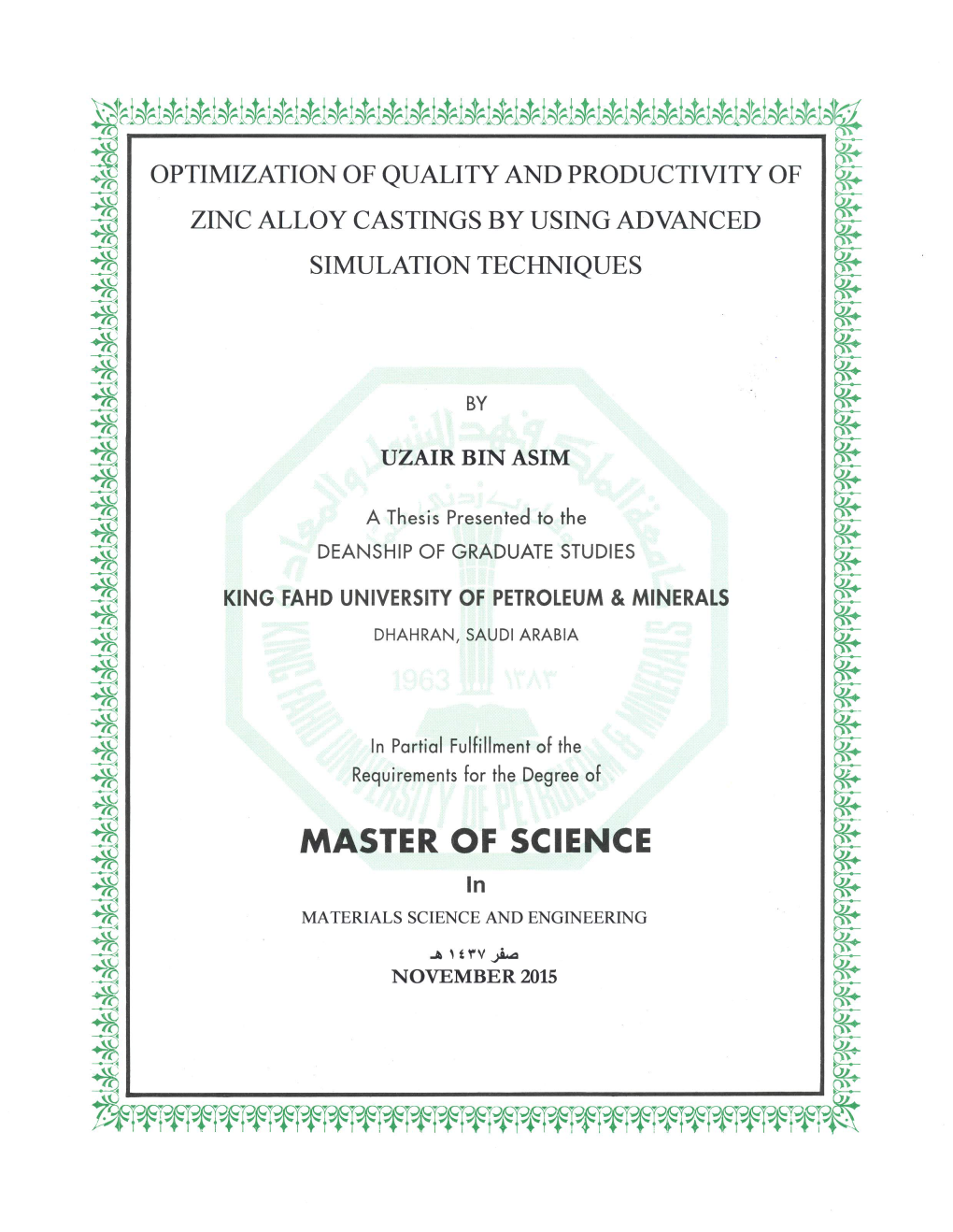
Load more
Recommended publications
-
Chapter 11: Metal Casting Processes and Equipment
Manufacturing Engineering Technology in SI Units, 6th Edition Chapter 11: Metal Casting Processes and Equipment Copyright © 2010 Pearson Education South Asia Pte Ltd Chapter Outline ¨ Introduction ¨ Expendable-mold, Permanent-pattern Casting Processes ¨ Expendable-mold, Expendable-pattern Casting Processes ¨ Permanent-mold Casting Processes ¨ Casting Techniques for Single-crystal Components ¨ Rapid Solidification ¨ Inspection of Castings ¨ Melting Practice and Furnaces ¨ Foundries and Foundry Automation Copyright © 2010 Pearson Education South Asia Pte Ltd Introduction ¨ Various casting processes developed over time to meet specific design requirements Copyright © 2010 Pearson Education South Asia Pte Ltd Introduction ¨ Molding categories: 1. Expendable molds 2. Permanent molds 3. Composite molds Copyright © 2010 Pearson Education South Asia Pte Ltd Introduction ¨ General characteristics of sand casting and casting processes are summarized Copyright © 2010 Pearson Education South Asia Pte Ltd Expendable-mold, Permanent-pattern Casting Processes: Sand Casting ¨ Most prevalent form of casting ¨ Application for machine bases, large turbine impellers, propellers, plumbing fixtures Copyright © 2010 Pearson Education South Asia Pte Ltd Expendable-mold, Permanent-pattern Casting Processes: Sand Casting Sand ¨ Sand-casting operations use silica sand as the mold material ¨ Sand is inexpensive and suitable high melting point process ¨ 2 types of sand: naturally bonded (bank sand) and synthetic (lake sand) ¨ Fine grained sand enhances mold strength and lower mold permeability Copyright © 2010 Pearson Education South Asia Pte Ltd Expendable-mold, Permanent-pattern Casting Processes: Sand Casting Types of Sand Molds 3 basic types: 1. Green-sand mold Sand in the mold is moist or damp while the metal is being poured into it 2. Cold-box mold Organic and inorganic binders are blended into the sand to bond the grains chemically 3. -
Extrusion Blow Molding ___Fiberg
Woman Owned Small Busines • ITAR Certified 710 South Patrick Drive • Satellite Beach, Florida 32937 321.536.2611 • [email protected] • www.rapidps.com ABS • POLYCARBONATE • POLYPHENYLSULFONE • ULTEM ADVANCED APPLICATIONS _____________________________ RTV MOLDS __________________________ Parts produced can be used in lots of different manufacturing applications. Parts built using RPS provide the fast, accurate and af- Parts can be painted, electroplated and drilled. They can also be used in ad- fordable patterns that drive RTV molding. By replacing vanced applications such as investment castings, RTV molding and sand cast- machined patterns, the entire process can be com- ing. Each application includes the benefits to using an RPS part with detailed pleted in 2-3 days. And unlike machining, complex instructions. and intricate shapes have no effect on the time or cost for the RPS pattern. ELECTROPLATING ____________________ Electroplating deposits a thin layer of metal on the RTV MOLDING SOLUBLE CORE _________ surface of a part built. This improves the part’s me- Complex geometries normally requiring core removal chanical properties and gives the appearance of pro- such as curved hoses, water tanks, bottles, and arterial duction metal or plated parts and provides a hard, structures are good examples where it may be helpful wear-resistant surface with reflective properties. to use this alternative method. Instead of building the core in thermoplastic material (traditional RPS build EXTRUSION BLOW MOLDING __________ process) the mold is built in the Water Soluble sup- Polycarbonate RPS molds are used in the blow port material making it easy to dissolve away the mate- molding process, reducing lead time and expense. -
6 Simple Steps to Becoming a Lost Wax Casting Pro,The Evolution Of
6 Simple Steps to Becoming a Lost Wax Casting Pro Lost wax casting blends old and new in truly remarkable fashion. Our industry is constantly changing, adapting ancient techniques to modern technology. So, we’ve asked our experts to walk us through lost wax casting: STEP 1 – PATTERN Wax patterns are made by one of the following ways: carving, build-up, hand forming, or mold reproduction. STEP 2 – SPRUING OR SETTING UP Spruing is the leading cause of shrinkage porosity, or the pits you see during polishing. Fix this by ensuring the following: • The sprue should be thicker than the heaviest part of the pattern. • It should also be attached to the heaviest part of the pattern as well. • The sprue should be no longer than is absolutely necessary. These are much more effective than looking for that optimum (magical) cast temp. STEP 3 – INVESTING Investing is more chemistry than craft. Measure your powder and water and follow your supplier’s instructions for mixing, curing, and burnout. Keep this in mind: your casting surface is only as good as your wax and investing procedures. • Weigh investment material and measure water according to manufacturer’s recommendation. • Fill flask containing wax pattern and either vacuum or vibrate to remove air from the slurry. • Allow invested mold to air-dry for two hours or more before starting the burnout. STEP 4 – BURNOUT • Place invested flask in furnace preheated to 300ºF. Hold at this temperature for one hour or until the wax has drained. • Raise temperature at the rate of 300º/400ºF per hour until temperature of 1350ºF is reached. -
MSL Engineering Limited Platinum Blue House 1St Floor, 18 the Avenue Egham, Surrey, TW20 9AB
SMR Final Report 121404 Purpose of Issue Rev Date of Issue Author Agreed Approved Issued for information 0 Aug 2004 SM Issued for internal comment 1 November 2004 AFD DJM JB Issued as Final Report 2 December 2004 AFD DJM JB This Final report has been reviewed and approved by the Mineral Management Service. Approval does not signify that the contents necessarily reflect the views and policies of the Service, nor does mention of trade names or commercial products constitute endorsement or recommendation for use. This study was funded by the Mineral Management Service, U.S. Department of the Interior, Washington, D.C., under Contract Number 1435-01-04-CT-35320 ASSESSMENT OF REPAIR TECHNIQUES FOR AGEING OR DAMAGED STRUCTURES Project #502 DOC REF C357R001 Rev 1 NOV 2004 MSL Engineering Limited Platinum Blue House 1st Floor, 18 The Avenue Egham, Surrey, TW20 9AB Tel: +44 (0)1784 439194 Fax: +44 (0)1784 439198 E-mail: [email protected] C357R001Rev 2, December 2004 MMS Project #502 NUMBER DETAILS OF REVISION 0 Issued for information, August 2004 1 Issued for comment, November 2004. Extensive revisions throughout, including restructuring of report. 2 Issued as Final Report, December 2004. Conversion table added, Figure showing clamp details to avoid added, and general editorial revisions. C357R001Rev 2, December 2004 MMS Project #502 Assessment of Repair Techniques for Ageing or Damaged Structures By Dr. Adrian F Dier MSL Services Corporation Final Project Report: ASSESSMENT OF REPAIR TECHNIQUES FOR AGEING OR DAMAGED STRUCTURES MMS Project Number 502 November 2004 C357R001Rev 2, December 2004 i This Final report has been reviewed a nd approved by the Mineral Management Service. -
A New Ceramic Casting Mold Made by Gel Casting Using Silica Sol As a Binder
BFSZU Zawrah et al. Vol.38-Dec.2016 A NEW CERAMIC CASTING MOLD MADE BY GEL CASTING USING SILICA SOL AS A BINDER Mahmoud F. Zawrah (1), Sayed A. Abdullah (2), Reham M. Khattab (1), Ibrahim M. Ibrahim (2), Waleed F. Youssef (3) (1) National Research Center, Department of Ceramics. (2) Shoubra Faculty of Engineering, Benha University, Department of Mechanical Engineering. (3) Faculty of Engineering, Sinai University, Department of Mechanical Engineering. ABSTRACT This Paper presents a new ceramic casting mold made by gel casting using silica sol as a binder. The new ceramic mold is consisted of an alumina- mullite-zirconia matrix with the ratios of 38.332 wt. % alumina, 34.378 wt. % mullite, and 27.294 wt. % zirconia respectively, the slurry is mixed then the gelling agent is added and poured into the pattern. After gelation the mold is extracted and left to dry, then sintered. There are three main defects appear in the mold fabrication process. The 1st defect is the mold cracking, as a result of forced shrinkage of mold into pattern. The 2nd defect is the bad gelation behavior of mold, as a result of non equal gelling time. The last defect is mold surface cracks, due to increased silica ratio added to the mixture. As zirconia increased the bulk density and apparent porosity is increased, leading to higher mold permeability which is important to eliminate trapping of residual gases. The increased zirconia content decreases the micro hardness and the cold crushing strength, but increases the thermal shock resistance due to phase transformation during sintering. The ceramic mold is applicable for nodular cast iron so that the mold is hard enough to withstand the forces of spheroidal graphite formation when nodular cast iron is poured into the ceramic mold. -
Morphing Loops
SPRING SM 2014 The Loop THE JOURNAL OF FLY CASTING PROFESSIONALS MORPHING LOOPS “All loops morph throughout the cast, from when the loop first begins to bud until it turns over and straightens. Mac Brown - Page 12 Cover Photo: Leslie Holmes, Cross-Body Cast Photo: Gardiner Mitchell THE LOOP - SPRING 2014 SM Policy Making - And Making Your Voice Heard IN THIS ISSUE The heart of the IFFF Casting Instructors’ Certification are creating policy for. A list of the committees and Program (CICP) is its committee members - those committee descriptions can be found at: Letter To The who create the framework for policies which affect http://www.fedflyfishers.org/Casting/ Editors P. 3 all certified instructors. Ultimately, the Casting HistoryGovernance/CastingCommittees.aspx Board of Governors signs off on policy (by way of From Don Simonson with the 2014 CBOG Awards review and vote for implementation), but committee From CI to MCI P. 5 committee: members create the ideas, which then mature through committee discussion. The Casting Board of Governors (CBOG) would like The Trouble you to submit nominations for the 2014 CBOG Awards With Skagit P. 8 When new casting policy is announced, often the by March 25. announcement does not include a justification for the • Lifetime Achievement in Fly Casting Instruction Loop Morphing new policy, no history, no discussion about why the P.11 • Mel Krieger Fly Casting Instructor policy is needed. And we instructors are sometimes • Governor’s Mentoring and the Governor’s Pin. left wondering why this policy came about. The Flyfishing editorial staff at The Loop feels that this journal can Redfish P.16 To learn more about the criteria for the awards provide a much needed look at the policies which and the nomination process go to the FFF Website affect everyone in the casting instruction program. -
Manufacturing Technology I Unit I Metal Casting
MANUFACTURING TECHNOLOGY I UNIT I METAL CASTING PROCESSES Sand casting – Sand moulds - Type of patterns – Pattern materials – Pattern allowances – Types of Moulding sand – Properties – Core making – Methods of Sand testing – Moulding machines – Types of moulding machines - Melting furnaces – Working principle of Special casting processes – Shell – investment casting – Ceramic mould – Lost Wax process – Pressure die casting – Centrifugal casting – CO2 process – Sand Casting defects. UNIT II JOINING PROCESSES Fusion welding processes – Types of Gas welding – Equipments used – Flame characteristics – Filler and Flux materials - Arc welding equipments - Electrodes – Coating and specifications – Principles of Resistance welding – Spot/butt – Seam – Projection welding – Percusion welding – GS metal arc welding – Flux cored – Submerged arc welding – Electro slag welding – TIG welding – Principle and application of special welding processes – Plasma arc welding – Thermit welding – Electron beam welding – Friction welding – Diffusion welding – Weld defects – Brazing – Soldering process – Methods and process capabilities – Filler materials and fluxes – Types of Adhesive bonding. UNIT III BULK DEFORMATION PROCESSES Hot working and cold working of metals – Forging processes – Open impression and closed die forging – Characteristics of the process – Types of Forging Machines – Typical forging operations – Rolling of metals – Types of Rolling mills – Flat strip rolling – Shape rolling operations – Defects in rolled parts – Principle of rod and wire drawing – Tube drawing – Principles of Extrusion – Types of Extrusion – Hot and Cold extrusion – Equipments used. UNIT IV SHEET METAL PROCESSES Sheet metal characteristics – Typical shearing operations – Bending – Drawing operations – Stretch forming operations –– Formability of sheet metal – Test methods – Working principle and application of special forming processes – Hydro forming – Rubber pad forming – Metal spinning – Introduction to Explosive forming – Magnetic pulse forming – Peen forming – Super plastic forming. -
Rolls for the Food Industry SIWACO Gmbh a Member of the Irle Group
ROLLS FOR THE FOOD INDUSTRY SIWACO GMBH A MEMBER OF THE IRLE GROUP We are specialised in wear resistant rolls and finished castings. Our technical expertise combined with the power of the IRLE GROUP offers cast rolls and products as well as reliable roll-services with an attractive price-performance ratio and short delivery times. Essential parts of our business are wear resistant rolls and finished castings as well as an optimal treatment of rolls, considering the specific requirements of every application. Our rolls are manufactured according to the utmost modern metallurgy MORE THAN 300 and technical treatment standards and by experienced and qualified ex- YEARS OF FOUNDRY perts by WALZEN IRLE in Germany and by its subcompany IRLE KAY JAY ROLLS in India. In 2007 a joint-venture was established with the Indian EXPERTISE, Company Kay Jay Rolls Pvt. Ltd., Panchkula, India. Both parties agreed 200 YEARS OF ROLL to build and operate an iron foundry near Chandigarh. For this „IRLE KAY CASTING JAY ROLLS Pvt. Ltd.“ has been founded to produce rolls for the food in- dustry and stretch reducing rolls for the tube and wire industry. 3 SIWACO ROLLS ARE PRODUCED FOR ROLLS FOR THE THE PROCESSING OF • cereals, FOOD INDUSTRY • cotton seed • cocoa beans, • coffee beans, The production of food using rolls for such processes as squeezing, milling, grating, breaking, refi- • oilseeds such as ning or flaking put special demands on the type of rolls used. • soybeans, • rape-oil seeds & canola, The performance and quality of the rolls determine the quality of the products to be produ- • sunflower seeds, ced and the economic efficiency of the production. -
Study of the Industrial Precision Manufacturing and Metallic Alloys with Respect to Economic Considerations
MPRA Munich Personal RePEc Archive Study of the Industrial Precision Manufacturing and Metallic Alloys with Respect to Economic Considerations Saha Choudhuri and Jian Shi Bangladesh University of Engineering and Technology 5 January 2017 Online at https://mpra.ub.uni-muenchen.de/77481/ MPRA Paper No. 77481, posted 13 March 2017 14:26 UTC Study of the Industrial Precision Manufacturing and Metallic Alloys with Respect to Economic Considerations Saha Choudhuri, Jian Shi Bangladesh University of Engineering and Technology 1 Abstract In this report according to the research results and approaches that used, it is utilized and illustrated why these papers are suitable for this research. The best position for explaining topic is here, because for understanding better the concept and the area of research, it is necessary to write briefly at the beginning of the article about topic. It is attempted to design new piston (porous piston) not only to have a good resistance in mechanical properties but also provide lower weight comparing to the previous ones. The most important thing in this work is to be aware of the effect of vibration, vacuum and over pressure during investment casting which by this way we can produce porous structure. By using the existing results of several papers, we will attempt to cast porous piston and optimize it to have the best mechanical properties. As we know engine pistons are one of the most complex components among all automotive or other industry field components. The engine can be called the heart of the car and piston maybe considered the most important part of an engine. -
Technology Reference Guide for Radioactively Contaminated Media
United States Office of Radiation and Indoor Air EPA 402-R-07-004 Environmental Radiation Protection Program October 2007 Protection Agency (6608J) Technology Reference Guide for Radioactively Contaminated Media TECHNOLOGY REFERENCE GUIDE FOR RADIOACTIVELY CONTAMINATED MEDIA EPA - 402-R-07-004 U.S. Environmental Protection Agency Office of Air and Radiation Office of Radiation and Indoor Air Radiation Protection Division Center for Radiation Site Cleanup Prepared Under: Contract No. 4W-2323-YTSX DISCLAIMER This Technology Guide, developed by USEPA, is meant to be a summary of information available for technologies demonstrated to be effective for treatment of radioactively contaminated media. Inclusion of technologies in this Guide should not be viewed as an endorsement of either the technology or the vendor by USEPA. Similarly, exclusion of any technology should not be viewed as not being endorsed by USEPA; it merely means that the information related to that technology was not so readily available during the development of this Guide. Also, the technology-specific performance and cost data presented in this document are somewhat subjective as they are from a limited number of demonstration projects and based on professional judgment. In addition, all images used in this document are from public domain or have been used with permission. i ACKNOWEDGEMENTS This Guide was developed by the Radiation Protection Division (RPD) of EPA’s Office of Radiation and Indoor Air (ORIA). Mr. Edward Feltcorn of ORIA’s Center for Radiation Site Cleanup, -
March/April 2015 Issue
Issue 244 March/April 2015 Turkey B.A.S.S. DNR TIPS News Updates Outdoor Photos March/April 2015 ~ Page 2 Advertise in the ALSO ON THE W.Va. Sportsman INTERNET Promote Your Business Statewide In Business LOWER Advertise RATES Special THAN Sales SIMILARand Events PUBLICATIONS24 YEARS Reach Thousands of Potential Customers LOW ADVERTISING RATES /1/15 Page.......$28 6 WEEK RATES 1/4 Page..........$82 1/10 Page.......$39 1/3 Page........$100 Magazine 1/6 Page.........$65 1/2 Page........$135 1/5 Page.........$72 2/3 Page........$150 Volume 1 Issue 244 COLOR FULL PAGE INSIDE....$195 Publisher and Editor EXTRA BACK PAGE................$240 Mark A. Goudy For Advertising Information In Contributing Editors RATES START AT: The Number One Outdoor West Virginia Division Of Publication In West Virginia Natural Resources $28 for 6 weeks CONTACT: W. Va. Sportsman For This Size Ad No Subscriptions Offered P.O. Box 5521 Printed Every Six Weeks. Less Than A 62 Cents Vienna, WV 26105 A Day! 304-482-7217 W.Va. Sportsman [email protected] P.O. Box 5521 Vienna, WV 26105 100% OWNED & OPERATED IN WV 304-482-7217 Email [email protected] www.wvasportsman.net Attention Bass Fishermen! All Rights Reserved Get Your Name On Our Cover Photo Mail-List For Bass Tournaments Large muskies are often caught In 2015 in the winter months for those that don't mind the cold weather. Robert Thaxton was fishing on Fill Out The Form Below the Kanawha River on December To Be Placed On The Mail List 14th. He caught and released this Clip & Mail To: 51 inch musky that weighed 41 Bass Sportsman Name__________________________________________________ 1/2 pounds. -
Centrifugal Casting
ASM Handbook, Volume 15: Casting Copyright © 2008 ASM International® ASM Handbook Committee, p 667-673 All rights reserved. DOI: 10.1361/asmhba0005257 www.asminternational.org Centrifugal Casting Sufei Wei, The Centrifugal Casting Machine Company, and Steve Lampman, ASM International CENTRIFUGAL CASTING is one of the density and freedom from oxides, gases, and the rotating mold. For example, with a vertical largest casting branches in the casting industry, other nonmetallic inclusions. When casting mold axis, the resultant force on the liquid is accounting for 15% of the total casting output solid parts, the pressure from rotation allows constant. This is not the case in a horizontal of the world in terms of tonnage. Centrifugal thinner details to be cast, making surface details mold. The other difference between horizontal casting was invented in 1918 by the Brazilian of the metal-cast components more prominent. and vertical mold orientation is the speed Dimitri Sensaud deLavaud, after whom the pro- Another advantage of centrifugal casting is the obtained by the molten metal as it spins around cess was named. DeLavaud’s invention elimi- elimination or minimization of gates and risers. the mold. When metal is poured into the hori- nated the need for a central core in the pipe zontally rotating mold, considerable slip occurs mold, and the mold was water cooled, allowing between the metal and the mold such that the for a high rate of repeated use. The technique Centrifugal Casting Methods metal does not move as fast as the rotating uses the centrifugal force generated by a rotat- mold. To overcome this inertia, the metal must ing cylindrical mold to throw molten metal Centrifugal casting machines are categorized be accelerated to reach the mold rotation speed.