Solar Decathlon Africa: Building Envelope Design Alyssa Jordyn Konsko Worcester Polytechnic Institute
Total Page:16
File Type:pdf, Size:1020Kb
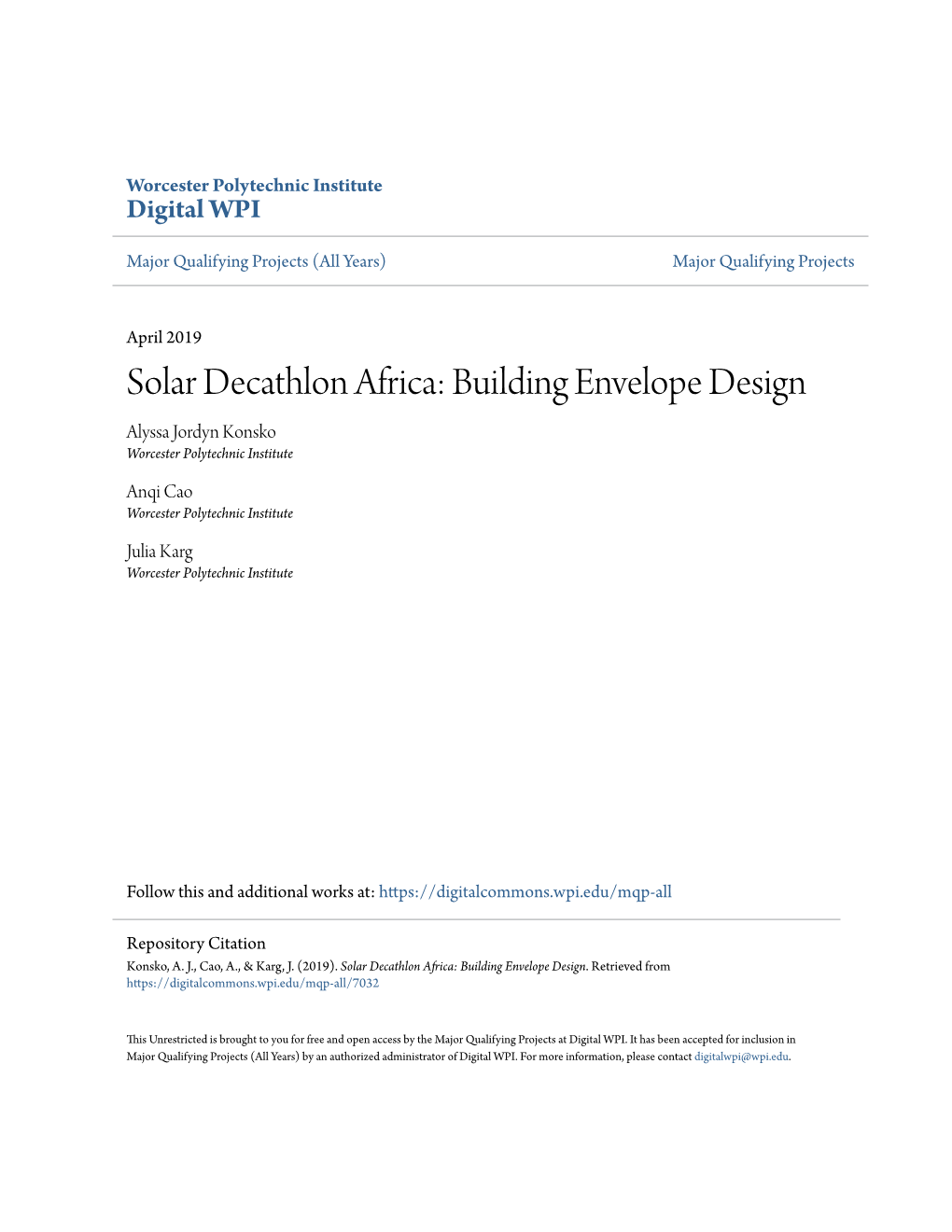
Load more
Recommended publications
-
The Art of Natural Building — Revised and Updated
Praise for The Art of Natural Building — Revised and Updated The Art of Natural Building — Second Edition is an epic adventure through the world of natural building. No stone is left unturned in presenting the beauty, inclusiveness, human, socially and environmentally responsible world of building with what the earth gives us, where we are. As a whole, it’s a bit overwhelming — so much to take in — and yet each subject is complete within itself. The spirit of this book is attuned to its subject — gentle, simple, embracing, humble, caring, and infused with love for each other, our communities, and the earth. It’s really about creating a humane world, a beacon to guide us through difficult times. — Bill Hutchins, founder/principal, Helicon Works Architects This is a book to live your life by — to improve your life in every aspect. No single problem is overlooked, from global warming to the imbalance of wealth and poverty. [This book] draws from a variety of tried-and-true methods while bringing us into today’s world — anyone, anywhere can build an affordable home from the practical details in this volume. — Marion Bridge, author, Passion for Earth: Earth Houses in New Zealand This is a well-illustrated and comprehensive, wide-ranging book on many methods and aspects of natural building, drawing on materials from many parts of the world and written by prominent practitioners and proponents. It will be 2 much anticipated by those who are either keen to promote natural building, or who are simply wishing to find out a whole lot more about it, what it means, and to see a whole range of examples. -
Solar Decathlon Africa - Team OCULUS
Solar Decathlon Africa - Team OCULUS Mechanical Design Team: Edward Andrews Ermina Damlamayan Nathan Rogers Faculty Advisors: Prof. Steven Van Dessel Prof. Tahar El Korchi Design of the Mechanical Systems for Team OCULUS in Solar Decathlon Africa 2019 A Major Qualifying Project Submitted to the Faculty of the WORCESTER POLYTECHNIC INSTITUTE in partial fulfillment of the requirements for the Degrees of Bachelor of Science in Architectural Engineering, Mechanical Engineering, and Civil Engineering April 25, 2019 By: Edward Andrews Ermina Damlamayan Nathan Rogers Advisors: Prof. Steven Van Dessel Prof. Tahar El Korchi This report represents work of WPI undergraduate students submitted to the faculty as evidence of a degree requirement. WPI routinely publishes these reports on its web site without editorial or peer review. For more information about the projects program at WPI, please see http://www.wpi.edu/academics/ugradstudies/project-learning.html 1 Abstract The Solar Decathlon is an international, net-zero building design competition that seeks to raise awareness about the importance of energy efficiency and sustainability. Competing teams are tasked with designing, building, and showcasing a residential structure that meet the requirements of the competition’s ten contests. Team OCULUS, comprised of college students from Worcester Polytechnic Institute in Worcester, MA, two Moroccan universities, and one Nigerian university, will compete in the Solar Decathlon Africa 2019 which will take place in Ben Guerir, Morocco in September 2019. Team OCULUS is divided into smaller teams based on student expertise. This report details the work of the Mechanical Team of Team OCULUS. The Mechanical Team was responsible for the design of the heating, ventilation, and air-conditioning (HVAC) system, the sizing and selection of mechanical equipment and appliances, the design of the photovoltaic system, and the development of a whole-house energy balance. -
Iea Pvps Annual Report 2019 Photovoltaic Power Systems Programme
Cover photo THE INTERNATIONAL OLYMPIC COMMITTEE’S (IOC) NEW HEADQUARTERS’ PV ROOFTOP, BUILT BY SOLSTIS, LAUSANNE SWITZERLAND One of the most sustainable buildings in the world, featuring a PV rooftop system built by Solstis, Lausanne, Switzerland. At the time of its certification in June 2019, the new IOC Headquarters in Lausanne, Switzerland, received the highest rating of any of the LEED v4-certified new construction project. This was only possible thanks to the PV system consisting of 614 mono-Si modules, amounting to 179 kWp and covering 999 m2 of the roof’s surface. The approximately 200 MWh solar power generated per year are used in-house for heat pumps, HVAC systems, lighting and general building operations. Photo: Solstis © IOC/Adam Mork COLOPHON Cover Photograph Solstis © IOC/Adam Mork Task Status Reports PVPS Operating Agents National Status Reports PVPS Executive Committee Members and Task 1 Experts Editor Mary Jo Brunisholz Layout Autrement dit Background Pages Normaset Puro blanc naturel Type set in Colaborate ISBN 978-3-906042-95-4 3 / IEA PVPS ANNUAL REPORT 2019 PHOTOVOLTAIC POWER SYSTEMS PROGRAMME PHOTOVOLTAIC POWER SYSTEMS PROGRAMME ANNUAL REPORT 2019 4 / IEA PVPS ANNUAL REPORT 2019 CHAIRMAN'S MESSAGE CHAIRMAN'S MESSAGE A warm welcome to the 2019 annual report of the International Energy Agency Photovoltaic Power Systems Technology Collaboration Programme, the IEA PVPS TCP! We are pleased to provide you with highlights and the latest results from our global collaborative work, as well as relevant developments in PV research and technology, applications and markets in our growing number of member countries and organizations worldwide. -
Advocating for Net-Zero Energy Sustainable Houses Through the International Solar Decathlon Competition
Proceedings of the 3rd World Congress on Civil, Structural, and Environmental Engineering (CSEE'18) Budapest, Hungary – April 8 - 10, 2018 DOI: 10.11159/icsenm18.1 Advocating for Net-Zero Energy Sustainable Houses through the International Solar Decathlon Competition Timothy J McCarthy, Brendan J Banfield, Yeganeh Baghi, Luca Faidutti, Clayton McDowell University of Wollongong NSW Australia Abstract - The US Department of Energy has been running the Solar Decathlon since 2000. This contest challenges teams of university students to design, build and operate a solar powered net-zero energy house. The contests are held in the US and at locations around the world. Transporting the house to the contest location is a major challenge for the teams. The University of Wollongong became the first Australian team to enter the Solar Decathlon when it’s house was constructed at Datong, China for the SD China 2013 competition. Team UOW won that competition against 18 other universities from around the world. The university will be in the final of the Solar Decathlon Middle East 2018 to be held in Dubai in October/November of that year. The new house, named Desert Rose, is a net-zero energy, dementia friendly eco house designed for the harsh Gulf climate. This paper will summarise the history of the 16 Solar Decathlon contests to date. The impact of the competition on the 235 international teams will be examined to demonstrate how the Solar Decathlon is a vehicle for educating engineers, architects and universities about sustainable and net-zero energy buildings. Case studies, including Team UOW’s winning entry to SD China 2013 will examine the value of such a large educational initiative from multiple perspectives. -
SOLAR DECATHLON AFRICA 2019 English Version
SOLAR DECATHLON AFRICA 2019 P A R T N E R S H I P D O S S I E R JUA HOUSE PROJECT www.juajamii.com Preface This dossier contains information on partnership opportunities supporting Jua Jamii in competing in the first SOLAR DECATHLON AFRICA to be held in September 2019 at Green Energy Park, BenGuerir, MOROCCO. TEAM Jau Jamii is a Swahili expression which means "solar community". The Jua Jamii team is a DESCRIPTION multidisciplinary team working in an interdisciplinary approach. The jamii is composed of 25 (and growing) talented young Africans enrolled in various Master’s degree courses at the Pan African University Institute of Water and Energy Sciences (PAUWES) and the University of Tlemcen in Algeria, Our team members come from eight different countries in Africa representing all five sub-regions of the continent: North, South, East, West and Central. The team boost of gender balance with women occupying strategic positions and offering a valuable contribution towards actualizing the Jau Jamii dream. This team is dedicated to the Jua dream- which is to design, build and compete in the Solar Decathlon competition in Morocco in 2019. The vision of this team is to become the first Pan African greenhouse construction company, that provides unique architectural design that reflects the African heritage while offering comfort to users in line with international standards. PROJECT JUA JAMII TEAM DESCRIPTION The Jua House is a cutting-edge solution to the ever-widening housing deficit in Africa. The house has flexible and spacious room setting fitted with localized African materials that give value for money and African experience. -
Telecharger La Version
B.T.P ENERGIES EFFICACITÉ ENERGÉTIQUE PAGE : 10 RENOUVELABLES PAGE : 50 Saad Dine El Otmani et PAGE : 20 APEBI : Rencontre pour Un Cluster national L’efficacité énergétique et le création d’emploi dans de l’hydrogène vert « pompage solaire dans le secteur les métiers du digital et GreenH2 Maroc » voit de l’agriculture de l’Offshoring. le jour N°98 • MARS • 2021 • 50 dh • 5€ • www.innovantmagazine.ma PAGE 12 EN EXERGUE PAGE 08 LES HYDROCARBURES : UNE SATISFACTION DE BESOIN EST MÉRITOIRE INDUSTRIE PRODUCTION TOURISME PAGE : 26 ALIMENTAIRE PAGE : 44 PAGE : 30 Relance industrielle Des avancées / Banque de projets : considérables dans le Les femmes pour les femmes : Signature de 52 conventions domaine de la recherche Le potentiel des coopératives d’investissement sur l’arganier féminines, mis en exergue ! PUB 04 32 •EDITO •FINANCES LA RECHERCHE SCIENTIFIQUE EN ÉNERGIE : UN BENCHAÂBOUN À LA CHAMBRE DES DOMAINE EN PLEINE CROISSANCE AU MAROC CONSEILLERS : 51 MMDH PAR AN POUR LA GÉNÉRALISATION DE LA PROTECTION SOCIALE 06 •ACTIVITÉS ROYALES 35 APRÈS LE LANCEMENT PAR SM LE ROI •FORMATION ET ENSEIGNEMENT MOHAMMED VI DE LA CAMPAGNE NATIONALE DE LA RÉFORME EN PROFONDEUR DU SYSTÈME VACCINATION CONTRE LA COVID-19. ÉDUCATIF : UN CHANTIER D’URGENCE CONTRIBUTION DU ROYAUME DU MAROC : UN DON D’UN MILLION DE DOLLARS AU PROFIT DU 38 PEUPLE YÉMÉNITE. •INTERNATIONAL DIRECTEUR DE LA LE MAROC PARTICIPE AUX TRAVAUX DU 155ÈME PUBLICATION CONSEIL DE LA LIGUE ARABE AU NIVEAU DES Jamal KORCH MINISTRES DES AE 08 RÉDACTEUR EN CHEF •EN EXERGUE Jamal KORCH LES HYDROCARBURES : UNE SATISFACTION DE 40 [email protected] BESOIN EST MÉRITOIRE •EAU GSM: 0661 34 58 85 PRÉSERVATION DE NOS RESSOURCES EN EAU : ACTIONS DE SENSIBILISATION JOURNALISTES 10 Meryem KORCH •BTP innovant.meryem@ SAAD DINE EL OTMANI ET APEBI : RENCONTRE 41 gmail.com POUR CRÉATION D’EMPLOI DANS LES MÉTIERS •RICHESSE NATURELLE Hajar BRAYCH DU DIGITAL ET DE L’OFFSHORING. -
Rapport Moral 2019 Sommaire
ASSEMBLÉE GÉNÉRALE ORDINAIRE ÉLECTIVE RAPPORT MORAL 2019 SOMMAIRE MOT DU PRÉSIDENT 3 FAITS MARQUANTS 5 DIMENSION TRANSVERSALE 18 DIMENSION RÉGIONALE 49 DIMENSION SECtorieLLE 68 DIMENSION LégisLATIVE 121 DIMENSION INTERNATIONALE 124 MOT DU PRÉSIDENT Chers membres de la CGEM, Je signe l’Edito de ce rapport moral, en ma qualité de Président par intérim de la CGEM, une responsabilité dont m’ont honoré mes collègues administrateurs de la CGEM, en me désignant pour gérer la période de transition, suite au départ inattendu du Président élu de la CGEM, Monsieur Salaheddine Mezouar. Les activités évoquées dans ce rapport sont en grande partie le résultat des engagements qu’il a pris devant vous et je tiens, au nom de tous, à lui rendre un hommage appuyé pour toutes ses contributions au développement de notre Confédération. Assurer la continuité de l’action de notre Confédération fut le souci principal de notre Conseil d’Administration. Grâce à votre implication à tous, la CGEM est demeurée mobilisée pour servir ses membres. Ainsi, Bureau, Fédérations, CGEM- Mohamed BACHIRI Régions, Commissions et Groupe parlementaire ont tous fait Président par Intérim preuve d’une mobilisation exemplaire et continué à mettre en oeuvre leurs plans d’actions 2019. Tout au long de cette année, notre Confédération n’a cessé de consolider sa posture. Celle de représentant d’un secteur privé responsable qui milite pour le développement écono- mique et social de notre pays. Lors de la 2ème Université d’Été de la CGEM, nous avions rappelé, sans langue de bois, que nous étions, tout autant que les pouvoirs publics, soucieux de l’intérêt général. -
Developing an Interactive Communication Platform for the Oculus House in the Solar Decathlon Africa 2019 •Fi Ben Guerir-Moro
Worcester Polytechnic Institute Digital WPI Interactive Qualifying Projects (All Years) Interactive Qualifying Projects March 2019 Developing an Interactive Communication Platform for the Oculus House in the Solar Decathlon Africa 2019 – Ben Guerir-Morocco Tej Sheth Worcester Polytechnic Institute Follow this and additional works at: https://digitalcommons.wpi.edu/iqp-all Repository Citation Sheth, T. (2019). Developing an Interactive Communication Platform for the Oculus House in the Solar Decathlon Africa 2019 – Ben Guerir- Morocco. Retrieved from https://digitalcommons.wpi.edu/iqp-all/5349 This Unrestricted is brought to you for free and open access by the Interactive Qualifying Projects at Digital WPI. It has been accepted for inclusion in Interactive Qualifying Projects (All Years) by an authorized administrator of Digital WPI. For more information, please contact [email protected]. An Interactive Qualifying Project Report submitted to the faculty of the WORCESTER POLYTECHNIC INSTITUTE in partial fulfillment of the requirements for the Degree of Bachelor of Science in cooperation with Team OCULUS of Solar Decathlon Africa 2019 Developing an Interactive Communication Platform for the Oculus House in the Solar Decathlon Africa 2019 – Ben Guerir-Morocco By: Tej Sheth Project Advisor: Tahar El-Korchi Date: March 10, 2019 This report represents the work of WPI undergraduate students submitted to the faculty as evidence of completion of a degree requirement. WPI routinely publishes these reports on its website without editorial or peer review. For more information about the projects program at WPI, please see http://www.wpi.edu/academics/ugradstudies/project-learning.html i Abstract This Interactive Qualifying Project develops the communication strategy for visitors of the Team OCULUS smart house at Solar Decathlon Africa 2019. -
Analysis of the Results: Final Technical Report
SDE _ FINAL TECHNICAL REPORT EC TENDER #: ENER / C2 / 2016-502 analysis of the results: final technical report PNO Consultants Energy Endeavour Foundation Universidad Politecnica Madrid Bergische Universität Wuppertal Technische Universiteit Delft Funded by: LEADER _ PG2 summary Solar Decathlon Europe | Tender ENER/C2/2016-502 | 2016 - 2020: Basis for this tender is Action 50 “Support to the European Innovation Partnership on Smart Cities and Communities and its Market Place”, Horizon 2020 Work Programme 2016 – 2017. Final objective is to ensure constant and high quality support to the Market Place of the European Innovation Partnership on Smart Cities and Communities (EIP-SCC) and the Solar Decathlon Europe (SDE) initiative. A consortium of former SDE organisers consolidated the results of the SDE competition event, held four times to date in Europe. In a series of four thematic reports, the group distilled the quintessential elements relevant to European partners. With fact sheets for specific audiences , the team has created a portfolio of documents that showcase actions, impact and importance of the SDE competition. The SDE has inspired millions through its unique combination of youthful enthusiasm, vigorous competition and innovative techno- logical solutions to real-world challenges. Participants have demonstrated that resource optimisation is possible by being intrepid, ingenious and responsible. Results of this tender will feed into the Smart Cities Information System, launched with the support of the European Commission to collect -
Pan African University - German Cooperation Programme Newsletter
Published by In Cooperation with: Issue No. 6 / July, 2019 Pan African University - German Cooperation Programme Newsletter Newsletter of German Development Cooperation Programme for the Pan African University A service by German Cooperation Programmes A quarterly newsletter by the German Development Cooperation Programme supporting the Pan African University (PAU) and the Pan African Institute of Water and Energy Sciences (PAUWES) informing about the development of the PAU as well as milestones and results of the support processes. This newsletter is developed and coordinated by GIZ with contributions from KfW. INSTITUTIONAL DEVELOPMENT ENTREPRENEURSHIP & EMPLOYABILITY PAUWES COMMUNITY EVENTS INSTITUTIONAL DEVELOPMENT The Pan African University Strategic Plan – Moving onto the implementation Phase After the final endorsement of the Pan African University Strategic Plan 2020-2024 by the Bureau of the PAU Council on June 7th, the Pan African University moves onto the implementation phase. With the support of GIZ, the Strategic Plan will be translated into operational planning at the Rectorate and institute level. Clear- cut key performance indicators, means of verification, responsibilities, timelines, risks/assumptions will be outlined for each institute as well as for the Rectorate. Since 2019 is considered as a preparatory year, the focus lies on tackling the major bottlenecks for the institutional development. Under the guidance and advisory of the Strategic Planning Committee, the PAU Rectorate jointly with the Human Resources, Science, and Technology (HRST) Department will steer the implementation of the Strategic Plan 2020-2024. The Bureau of the PAU Council met on 7th June to endorse the final version of the Strategic Plan and discuss the implementation steps. -
Developing an Inclusive Promotional Strategy for Solar Decathlon AFRICA in Morocco Erin Mae Morissette Worcester Polytechnic Institute
Worcester Polytechnic Institute Digital WPI Interactive Qualifying Projects (All Years) Interactive Qualifying Projects February 2018 Developing an Inclusive Promotional Strategy for Solar Decathlon AFRICA in Morocco Erin Mae Morissette Worcester Polytechnic Institute Karsten Hintz Roberts Worcester Polytechnic Institute Lillian H. Olsen Worcester Polytechnic Institute Nathan Andrew Rogers Worcester Polytechnic Institute Follow this and additional works at: https://digitalcommons.wpi.edu/iqp-all Repository Citation Morissette, E. M., Roberts, K. H., Olsen, L. H., & Rogers, N. A. (2018). Developing an Inclusive Promotional Strategy for Solar Decathlon AFRICA in Morocco. Retrieved from https://digitalcommons.wpi.edu/iqp-all/5231 This Unrestricted is brought to you for free and open access by the Interactive Qualifying Projects at Digital WPI. It has been accepted for inclusion in Interactive Qualifying Projects (All Years) by an authorized administrator of Digital WPI. For more information, please contact [email protected]. i Developing an Inclusive Promotional Strategy for Solar Decathlon AFRICA in Morocco An Interactive Qualifying Project Report submitted to the faculty of WORCESTER POLYTECHNIC INSTITUTE in partial fulfillment of the requirements for the Degree of Bachelor of Science Submitted by: Erin Morissette Lily Olsen Karsten Roberts Nathan Rogers Date: February, 2018 Submitted to: Samir Idrissi, Institut de Recherche en Energie Solaire et Energies Nouvelles (IRESEN) Project Advisors: Professor Bethel Eddy Professor Robert Kinicki Worcester Polytechnic Institute This report represents the work of four WPI undergraduate students submitted to the faculty as evidence of completion of a degree requirement. WPI routinely publishes these reports on its web site without editorial or peer review. The opinions presented in this report do not necessarily represent the opinions of WPI or IRESEN. -
Energy Efficiency and Economic Recovery
1 2 3 4 5 6 www.amee.ma I. Introductory Introducing the Energy 1 Letter Efficiency Magazine On behalf of the EE Global Alliance (EEGA) and the AOB Group, we are proud to issue this special edition of the Energy Efficiency Magazine focused on energy efficiency’s role in global economic recovery. As COVID-19 continues to devastate economies around the globe, it is critical to highlight how energy efficiency solutions can support 2 countries’ rapid and sustainable recovery. Because climate change remains one of the world’s greatest challenges even during the pandemic - and will outlive the current health and economic crisis - we are releasing this special digital edition during Climate Week NYC, an event run by the Climate Group in association with the United Nations and the City of New York. In addition to helping 3 countries get back on their feet economically, energy efficiency can provide more than 40% of the emissions abatement required by 2040 to meet the goals outlined in the Paris Agreement (IEA, 2018). In this magazine, you’ll read timely updates and ideas from a diverse suite of renowned international experts with one common theme: our collective global economic recovery efforts must prioritize energy efficiency. Authors reflect on lessons learned from recovery efforts following the 2008 Great Recession, the kinds of policies and programs 4 needed to sustainably recover today, and the private sector’s role. We are excited to share this magazine with you. 5 Hafid Boutaleb Laura Van Wie McGrory Business Research Manager Vice President, Strategic Initiatives 6 AOB Group Alliance to Save Energy/EEGA www.amee.ma The AOB Group is an international publisher focused on energy and climate change.