E-- I REPORTG975 15 APRIL 1969 I SERIAL N O.- -- I OPTIMIZEDCOST/PERFORMANCE I DESIGNMETHODOLOGY I
Total Page:16
File Type:pdf, Size:1020Kb
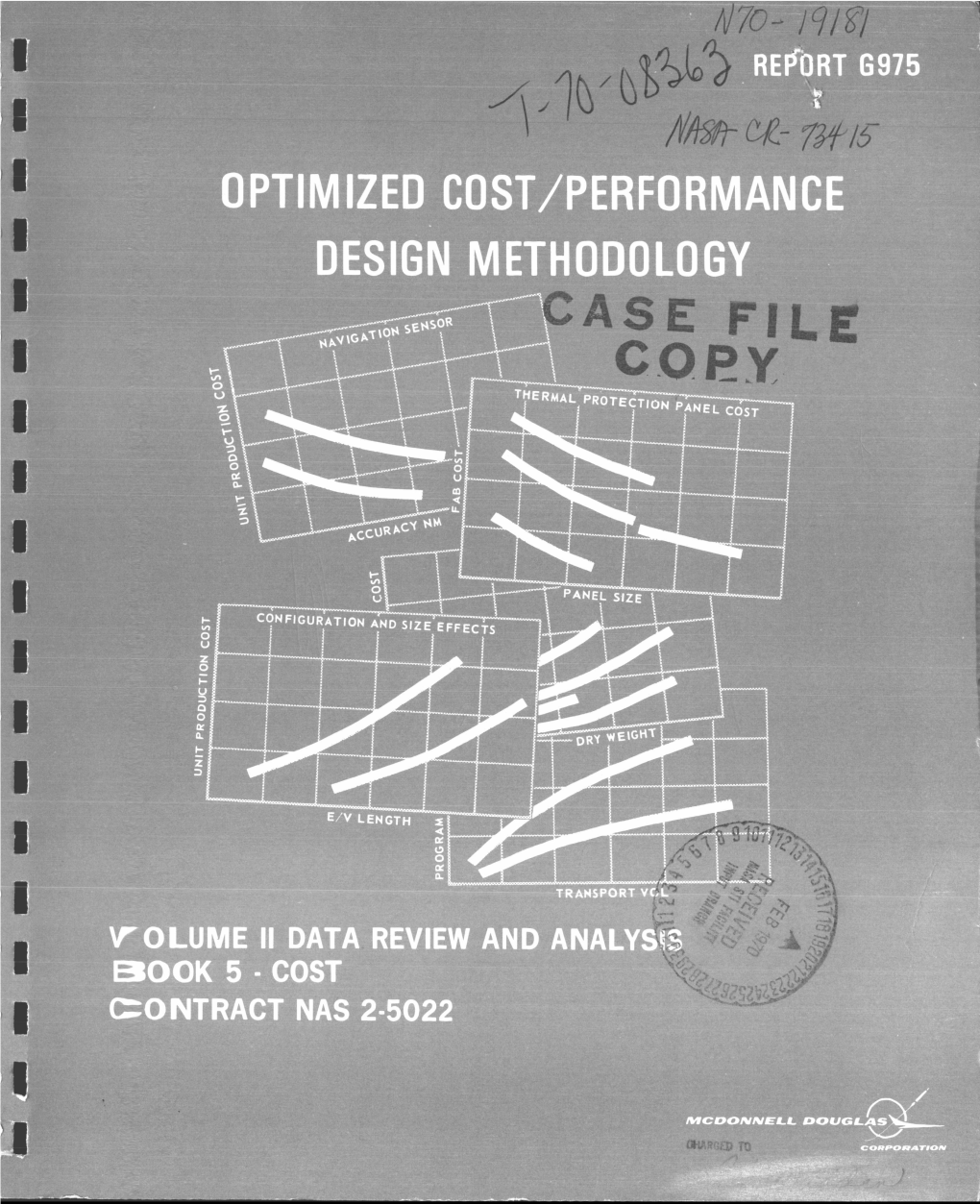
Load more
Recommended publications
-
Sab 2012 Mecbpn
Dos-Santos,W.A., et al. PROPOSTA DE UMA MISSÃO ESPACIAL PARA PICOSATÉLITES E ... PROPOSTA DE UMA MISSÃO ESPACIAL COMPLETA PARA PICOSATÉLITES E NANOSATÉLITES UTILIZANDO LANÇADORES NACIONAIS Walter Abrahão dos Santos, Fernanda Sayuri Yamasaki, Wilson Yamaguti Instituto Nacional de Pesquisas Espaciais – Av. dos Astronautas,1758 - CP515 - CEP 12227-010 São José dos Campos - SP, [email protected] , [email protected] , [email protected] Flávio de Azevedo Corrêa Jr. Instituto de Aeronáutica e Espaço – DCTA/IAE/SESP/PE, Praça Mal. Eduardo Gomes, 50 - Vila das Acácias, 12.228-904 - São José dos Campos - SP - Brasil - [email protected] Resumo: Devido ao mercado emergente de aplicações para pico e nanosatélites nas áreas de Espaço e Defesa, este trabalho se inspira na Missão Espacial Completa Brasileira (MECB), um programa conjunto de satélites e lançadores brasileiros, para propor um programa indutor de lançadores e plataformas voltados para satélites miniaturizados com missões sofisticadas devido a avanços em nanotecnologia e computação, entre outros. O trabalho considera dois grandes segmentos: (1) o segmento de lançadores focado na análise de viabilidade de veículos lançadores de pequenas cargas a uma altitude de aproximadamente 300 km e (2) o segmento relativo aos satélites objetivando embarcar cargas úteis com as seguintes aplicações em vista: um radiômetro, uma microcâmera e formação em voo. A análise foi basicamente concentrada nos envelopes de massa, tamanho, potência. A sustentabilidade do programa para estes satélites requer um acesso barato e regular ao espaço e é atrativa pela projeção futura deste nicho de mercado que pode contribuir com objetivos estratégicos do país. -
Small Satellite Launchers
SMALL SATELLITE LAUNCHERS NewSpace Index 2020/04/20 Current status and time from development start to the first successful or planned orbital launch NEWSPACE.IM Northrop Grumman Pegasus 1990 Scorpius Space Launch Demi-Sprite ? Makeyev OKB Shtil 1998 Interorbital Systems NEPTUNE N1 ? SpaceX Falcon 1e 2008 Interstellar Technologies Zero 2021 MT Aerospace MTA, WARR, Daneo ? Rocket Lab Electron 2017 Nammo North Star 2020 CTA VLM 2020 Acrux Montenegro ? Frontier Astronautics ? ? Earth to Sky ? 2021 Zero 2 Infinity Bloostar ? CASIC / ExPace Kuaizhou-1A (Fei Tian 1) 2017 SpaceLS Prometheus-1 ? MISHAAL Aerospace M-OV ? CONAE Tronador II 2020 TLON Space Aventura I ? Rocketcrafters Intrepid-1 2020 ARCA Space Haas 2CA ? Aerojet Rocketdyne SPARK / Super Strypi 2015 Generation Orbit GoLauncher 2 ? PLD Space Miura 5 (Arion 2) 2021 Swiss Space Systems SOAR 2018 Heliaq ALV-2 ? Gilmour Space Eris-S 2021 Roketsan UFS 2023 Independence-X DNLV 2021 Beyond Earth ? ? Bagaveev Corporation Bagaveev ? Open Space Orbital Neutrino I ? LIA Aerospace Procyon 2026 JAXA SS-520-4 2017 Swedish Space Corporation Rainbow 2021 SpinLaunch ? 2022 Pipeline2Space ? ? Perigee Blue Whale 2020 Link Space New Line 1 2021 Lin Industrial Taymyr-1A ? Leaf Space Primo ? Firefly 2020 Exos Aerospace Jaguar ? Cubecab Cab-3A 2022 Celestia Aerospace Space Arrow CM ? bluShift Aerospace Red Dwarf 2022 Black Arrow Black Arrow 2 ? Tranquility Aerospace Devon Two ? Masterra Space MINSAT-2000 2021 LEO Launcher & Logistics ? ? ISRO SSLV (PSLV Light) 2020 Wagner Industries Konshu ? VSAT ? ? VALT -
Redalyc.Status and Trends of Smallsats and Their Launch Vehicles
Journal of Aerospace Technology and Management ISSN: 1984-9648 [email protected] Instituto de Aeronáutica e Espaço Brasil Wekerle, Timo; Bezerra Pessoa Filho, José; Vergueiro Loures da Costa, Luís Eduardo; Gonzaga Trabasso, Luís Status and Trends of Smallsats and Their Launch Vehicles — An Up-to-date Review Journal of Aerospace Technology and Management, vol. 9, núm. 3, julio-septiembre, 2017, pp. 269-286 Instituto de Aeronáutica e Espaço São Paulo, Brasil Available in: http://www.redalyc.org/articulo.oa?id=309452133001 How to cite Complete issue Scientific Information System More information about this article Network of Scientific Journals from Latin America, the Caribbean, Spain and Portugal Journal's homepage in redalyc.org Non-profit academic project, developed under the open access initiative doi: 10.5028/jatm.v9i3.853 Status and Trends of Smallsats and Their Launch Vehicles — An Up-to-date Review Timo Wekerle1, José Bezerra Pessoa Filho2, Luís Eduardo Vergueiro Loures da Costa1, Luís Gonzaga Trabasso1 ABSTRACT: This paper presents an analysis of the scenario of small satellites and its correspondent launch vehicles. The INTRODUCTION miniaturization of electronics, together with reliability and performance increase as well as reduction of cost, have During the past 30 years, electronic devices have experienced allowed the use of commercials-off-the-shelf in the space industry, fostering the Smallsat use. An analysis of the enormous advancements in terms of performance, reliability and launched Smallsats during the last 20 years is accomplished lower prices. In the mid-80s, a USD 36 million supercomputer and the main factors for the Smallsat (r)evolution, outlined. -
A Brazilian Space Launch System for the Small Satellite Market
aerospace Article A Brazilian Space Launch System for the Small Satellite Market Pedro L. K. da Cás 1 , Carlos A. G. Veras 2,* , Olexiy Shynkarenko 1 and Rodrigo Leonardi 3 1 Chemical Propulsion Laboratory, University of Brasília, Brasília 70910-900, DF, Brazil; [email protected] (P.L.K.d.C.); [email protected] (O.S.) 2 Mechanical Engineering Department, University of Brasília, Brasília 70910-900, DF, Brazil 3 Directorate of Satellites, Applications and Development, Brazilian Space Agency, Brasília 70610-200, DF, Brazil; [email protected] * Correspondence: [email protected] Received: 8 July 2019; Accepted: 8 October 2019; Published: 12 November 2019 Abstract: At present, most small satellites are delivered as hosted payloads on large launch vehicles. Considering the current technological development, constellations of small satellites can provide a broad range of services operating at designated orbits. To achieve that, small satellite customers are seeking cost-effective launch services for dedicated missions. This paper deals with performance and cost assessments of a set of launch vehicle concepts based on a solid propellant rocket engine (S-50) under development by the Institute of Aeronautics and Space (Brazil) with support from the Brazilian Space Agency. Cost estimation analysis, based on the TRANSCOST model, was carried out taking into account the costs of launch system development, vehicle fabrication, direct and indirect operation cost. A cost-competitive expendable launch system was identified by using three S-50 solid rocket motors for the first stage, one S-50 engine for the second stage and a flight-proven cluster of pressure-fed liquid engines for the third stage. -
Vol 24 Issue 5
11 AIR rcvicwU N I VERSI TY THE PROFESSIONAl JOURNAL Of THE UNITED STATES AIR FORCE U.S. M il it a r y Stratecy: P aradoxes in Per spect ive...................................................................... 2 Maj. Edd D. Wheeler, US.AF Mish a p Analysis: An Impr o ved Appr o a c h to Air c r a f t Accident Prevention . 13 Col. David L. Nichols, US.AF T he Many Faces of the Spa c e Shuttle........................................................................................23 Williani G. Holder T he Lea d-Time Problem: T heory .and Appl ic a t io n s ................................................................ 36 Lt. Kenneth C. Stoehrmann, US.AF Lvtel l igence and Information Pr o c essin g in Co un t er insur c en c y................................... 46 Dr. Charles A. Russell Maj. Robert E. Hildner, US.AF T he Middle East, 1973: C old W.ar Chances and Amer ic a n Interests........................ 57 Capt. Bard E. O Neill, US.AF Air Force Review Modern Communications, a Wise Investment......................................................................... 63 Maj. Gen. Paul R. Stonev, US.AF ln My Opinion O rcaniz.atio.nal Devel o pmen t : C an It Be Effective in the Armed Forces? ... 68 Lt. Col. Peter E. LaSota, US.AF Capt. Robert A. Zawacki, USAF Syst ema t ic Reso l ut ion of Social Problems within the Mil it .ary............................. 73 Capt. Jon M. Samuels, US.AF Books and Ideas A chtunc! Fuecer th vppex! ...................................................................................................................80 Dr. Alfred Goldberg A C o mmun t t y within “A Nation of Strangers" .......................................................................89 Col. Andrew J. Dougherty, US.AF Marjorie M. -
Challenges of the Brazilian National Space Law and Policy
United Nations/Brazil Symposium on Basic Space Technology Creating Novel Opportunities with Small Satellite Space Missions 11-14 September 2018, Natal-RN, Brazil Small Satellites: Challenges of the Brazilian National Space Law and Policy Ms. Ana Cristina Galhego Rosa Founder & CEO at Dipteron UG United Dr. Himilcon de C. Carvalho, Nations/Brazil COO at Visiona – Space Technology Symposium on Basic Space Technology “Creating Novel "I was born and raised in the middle of the war. I saw violence and a lot of people dying. I was afraid, very afraid. I did not want to see hate ever again. What I want is that the humanity live in peace“ - Vietnamese broadcast on Castro's satellite. Voice message from children around the world who asked for peace between nations. Júnior Torres de Castro (1933-2018), a Brazilian engineer who, using own resources, build the first Brazilian satellite for educational and humanitarian Oscar-Dove17 purposes that was launched in 1990. He was nominated for the Nobel Peace Prize. He was the first and (so far) the only private person to launch a satellite. OUTLINE • Brazilian Small Satellite Program • Legal Framework Overview • Policy Framework: The Brazilian National Plan For Space Activities (PNAE 2012 – 2021) • The Provisional Draft of the Brazilian National Legislation for Space Activities - a Non- Governmental Initiative • Recommendations for establishing a National Space Legislation • Recommendations for establishing a Brazilian National Policy for Small Satellite Brazilian Small Satellite Program Begining 1993-1997: -
Annex 7. Orbit Modelling and Analysis, Simulated Mission Planning
30th June 2013 SAR Formation Flying Annex 7. Orbit Modelling and Analysis, Simulated Mission Planning Document Version: V01_00 Dr Li Qiao Australian Centre for Space Engineering Research (ACSER) University of New South Wales, Sydney, 2052, Australia Revision History Version No. Date Author Description of Change V01_00 30th June 2013 Dr Li Qiao Initial Release TABLE OF CONTENT 1. EXECUTIVE SUMMARY .................................................................................................................... 8 2. INTRODUCTION ............................................................................................................................. 10 3. MISSION APPLICATION REQUIREMENTS....................................................................................... 12 3.1. Soil Moisture Monitoring of Murray Darling Basin (MDB) ................................................... 12 3.2. Power System Requirements ................................................................................................ 12 3.3. Orbit Lifetime ........................................................................................................................ 12 4. ORBIT SELECTION FOR GARADA.................................................................................................... 14 4.1. Orbit Definition ..................................................................................................................... 14 4.2. Orbit Type ............................................................................................................................ -
Reinventing Space Conference 2018
Journal of the British Interplanetary Society VOLUME 71 NO.11 NOVEMBER 2018 Reinventing Space Conference 2018 THE MARKET FOR A UK LAUNCHER Vadim Zakirov et al THE REMOVEDEBRIS SPACE HARPOON Alexander Hall RAPID CONSTELLATION DEPLOYMENT from the UK Christopher Loghry & Marissa Stender REDESIGN & SPACE QUALIFICATION OF A 3D-PRINTED SATELLITE STRUCTURE with Polietherimide Jonathan Becedas et al THE EPSILON LAUNCH VEHICLE: Status and Future Ryoma Yamashiro & Imoto Takayuki THE NORMS OF BEHAVIOUR IN SPACE: Our space – Whose rules? Lesley Jane Smith www.bis-space.com ISSN 0007-084X PUBLICATION DATE: 31 JANUARY 2019 Submitting papers International Advisory Board to JBIS JBIS welcomes the submission of technical Rachel Armstrong, Newcastle University, UK papers for publication dealing with technical Peter Bainum, Howard University, USA reviews, research, technology and engineering in astronautics and related fields. Stephen Baxter, Science & Science Fiction Writer, UK James Benford, Microwave Sciences, California, USA Text should be: James Biggs, The University of Strathclyde, UK ■ As concise as the content allows – typically 5,000 to 6,000 words. Shorter papers (Technical Notes) Anu Bowman, Foundation for Enterprise Development, California, USA will also be considered; longer papers will only Gerald Cleaver, Baylor University, USA be considered in exceptional circumstances – for Charles Cockell, University of Edinburgh, UK example, in the case of a major subject review. Ian A. Crawford, Birkbeck College London, UK ■ Source references should be inserted in the text in square brackets – [1] – and then listed at the Adam Crowl, Icarus Interstellar, Australia end of the paper. Eric W. Davis, Institute for Advanced Studies at Austin, USA ■ Illustration references should be cited in Kathryn Denning, York University, Toronto, Canada numerical order in the text; those not cited in the Martyn Fogg, Probability Research Group, UK text risk omission. -
Space Policies, Issues and Trends in 2014-2015
Space Policies, Issues and Trends in 2014—2015 Report 54 November 2015 Cenan Al-Ekabi Short title: ESPI Report 54 ISSN: 2218-0931 (print), 2076-6688 (online) Published in November 2015 Editor and publisher: European Space Policy Institute, ESPI Schwarzenbergplatz 6 • 1030 Vienna • Austria http://www.espi.or.at Tel. +43 1 7181118-0; Fax -99 Rights reserved – No part of this report may be reproduced or transmitted in any form or for any purpose with- out permission from ESPI. Citations and extracts to be published by other means are subject to mentioning “Source: ESPI Report 54; November 2015. All rights reserved” and sample transmission to ESPI before publish- ing. ESPI is not responsible for any losses, injury or damage caused to any person or property (including under contract, by negligence, product liability or otherwise) whether they may be direct or indirect, special, inciden- tal or consequential, resulting from the information contained in this publication. Design: Panthera.cc ESPI Report 54 2 November 2015 Space Policies, Issues and Trends in 2014—2015 Table of Contents Introduction 5 1. Global Political and Economic Trends 6 1.1 Global Economic Outlook 6 1.2 Political Developments 7 1.2.1 Geopolitics 7 1.2.2 Environment 7 1.2.3 Energy 9 1.2.4 Resources 9 1.2.5 Knowledge 11 1.2.6 Mobility 12 2. Global Space Economy 14 2.1 Global Space Budgets and Revenue 14 2.2 Overview of Institutional Space Budgets 14 2.3 Overview of Commercial Space Markets 18 2.3.1 Satellite Services 18 2.3.2 Satellite Manufacturing 20 2.3.3 Launch Sector 20 2.3.4 Ground Equipment 21 2.3.5 Insurance Sector 23 2.4 Sectoral Overview 23 2.4.1 Launch Sector 23 2.4.2 Manufacturing Sector 27 2.5 Transatlantic Industrial Comparison 30 2.5.1 State of the European Industry 30 2.5.2 State of the United States Space Industry 33 3. -
SMALL SATELLITE LAUNCHERS Cancelled Concept Dormant In
SMALL SATELLITE LAUNCHERS NewSpace Index 2020/03/09 Current status and time from development start to the first successful or planned orbital launch NEWSPACE.IM Northrop Grumman Pegasus 1990 Scorpius Space Launch Demi-Sprite ? Makeyev OKB Shtil 1998 Interorbital Systems NEPTUNE N1 ? SpaceX Falcon 1e 2008 Interstellar Technologies Zero 2021 MT Aerospace MTA, WARR, Daneo ? Rocket Lab Electron 2017 Nammo North Star 2020 CTA VLM 2020 Acrux Montenegro ? Frontier Astronautics ? ? Earth to Sky ? 2021 Zero 2 Infinity Bloostar ? CASIC / ExPace Fei Tian 1 / Kuaizhou-1A 2017 SpaceLS Prometheus-1 ? MISHAAL Aerospace M-OV ? CONAE Tronador II 2020 TLON Space Aventura I ? Rocketcrafters Intrepid-1 2020 ARCA Space Haas 2CA ? Aerojet Rocketdyne SPARK / Super Strypi 2015 Generation Orbit GoLauncher 2 ? PLD Space Miura 5 (Arion 2) 2021 Swiss Space Systems SOAR 2018 Heliaq ALV-2 ? Gilmour Space Eris-S 2021 Roketsan UFS 2023 Independence-X DNLV 2021 Beyond Earth ? ? Bagaveev Corporation Bagaveev ? Open Space Orbital Neutrino I ? LIA Aerospace Procyon 2026 JAXA SS-520-4 2017 Swedish Space Corporation Rainbow 2021 SpinLaunch ? 2022 Pipeline2Space ? ? Perigee Blue Whale 2020 Link Space New Line 1 2021 Lin Industrial Taymyr-1A ? Leaf Space Primo ? Firefly 2020 Exos Aerospace Jaguar ? Cubecab Cab-3A 2022 Celestia Aerospace Space Arrow CM ? bluShift Aerospace Red Dwarf 2022 Black Arrow Black Arrow 2 ? Tranquility Aerospace Devon Two ? Masterra Space MINSAT-2000 2021 LEO Launcher & Logistics ? ? ISRO SSLV (PSLV Light) 2020 Wagner Industries Konshu ? VSAT ? ? VALT -
Design Considerations for a Pressure-Driven Multi-Stage Rocket
University of Tennessee, Knoxville TRACE: Tennessee Research and Creative Exchange Doctoral Dissertations Graduate School 12-2002 Design considerations for a pressure-driven multi-stage rocket Steven Craig Sauerwein University of Tennessee Follow this and additional works at: https://trace.tennessee.edu/utk_graddiss Recommended Citation Sauerwein, Steven Craig, "Design considerations for a pressure-driven multi-stage rocket. " PhD diss., University of Tennessee, 2002. https://trace.tennessee.edu/utk_graddiss/6301 This Dissertation is brought to you for free and open access by the Graduate School at TRACE: Tennessee Research and Creative Exchange. It has been accepted for inclusion in Doctoral Dissertations by an authorized administrator of TRACE: Tennessee Research and Creative Exchange. For more information, please contact [email protected]. To the Graduate Council: I am submitting herewith a dissertation written by Steven Craig Sauerwein entitled "Design considerations for a pressure-driven multi-stage rocket." I have examined the final electronic copy of this dissertation for form and content and recommend that it be accepted in partial fulfillment of the equirr ements for the degree of Doctor of Philosophy, with a major in Aerospace Engineering. Gary A. Flandro, Major Professor We have read this dissertation and recommend its acceptance: Accepted for the Council: Carolyn R. Hodges Vice Provost and Dean of the Graduate School (Original signatures are on file with official studentecor r ds.) To the Graduate Council: I am submitting herewith a dissertation written by Steven Craig Sauerwein entitled "Design Considerations for a Pressure-Driven Multi-Stage Rocket." I have examined the final paper copy of this dissertation for form and content and recommend that it be accepted in partial fulfillment of the requirements for the degree of Doctor of Philosophy, with a major in Aerospace Engineering. -
MORABA – Overview on DLR's Mobile Rocket Base and Projects
MORABA – Overview on DLR’s Mobile Rocket Base and Projects L. Altenbuchner1, J. Ettl2, M. Hörschgen3, W. Jung4, R. Kirchhartz5, A. Stamminger6 and P. Turner7 DLR Mobile Rocket Base, Oberpfaffenhofen, 82234 Wessling, Germany Mobile Rocket Base (MORABA), a division of the Space Operations and Astronaut Training Department of DLR (Deutsches Zentrum für Luft- und Raumfahrt) provides the national and international scientific community with the opportunity to prepare and implement rocket- and balloon-borne experiments. The fields of research include aeronomy, astronomy, geophysics, material science and hypersonic research and are conducted in cooperation with a variety of international partners. In addition satellite missions can be supported by mobile tracking radars for trajectory determination and TT&C mobile ground stations. MORABA also offers a number of mechanical and electrical systems for use on rocket, balloon and short term satellite missions. During the last four decades more than 250 campaigns have been performed in Antarctica, Australia, Brazil, France, Greenland, India, Italy, Japan, Norway, Spain, Sweden and USA. Depending on the scientific objective, an appropriate launch range is selected and complemented or fully equipped with MORABA’s mobile infrastructure, such as launcher, telemetry and tracking stations. MORABA supplies the suitable converted military surplus or commercial launch vehicles, as well as all necessary mechanical and electrical subsystems to the customers. This paper gives an overview of the MORABA infrastructure for sounding rocket launching and satellite TT&C. A short survey of MORABA projects of the last two years and the next two years is also provided. I. Introduction HE Mobile Rocket Base (MORABA) was founded in 1967 as part of the Max Planck Society (Arbeitsgruppe T für Weltraumforschung) under the initiative of Professor Reimar Lüst.