A New Vertical Tailplane Design Procedure Through Cfd
Total Page:16
File Type:pdf, Size:1020Kb
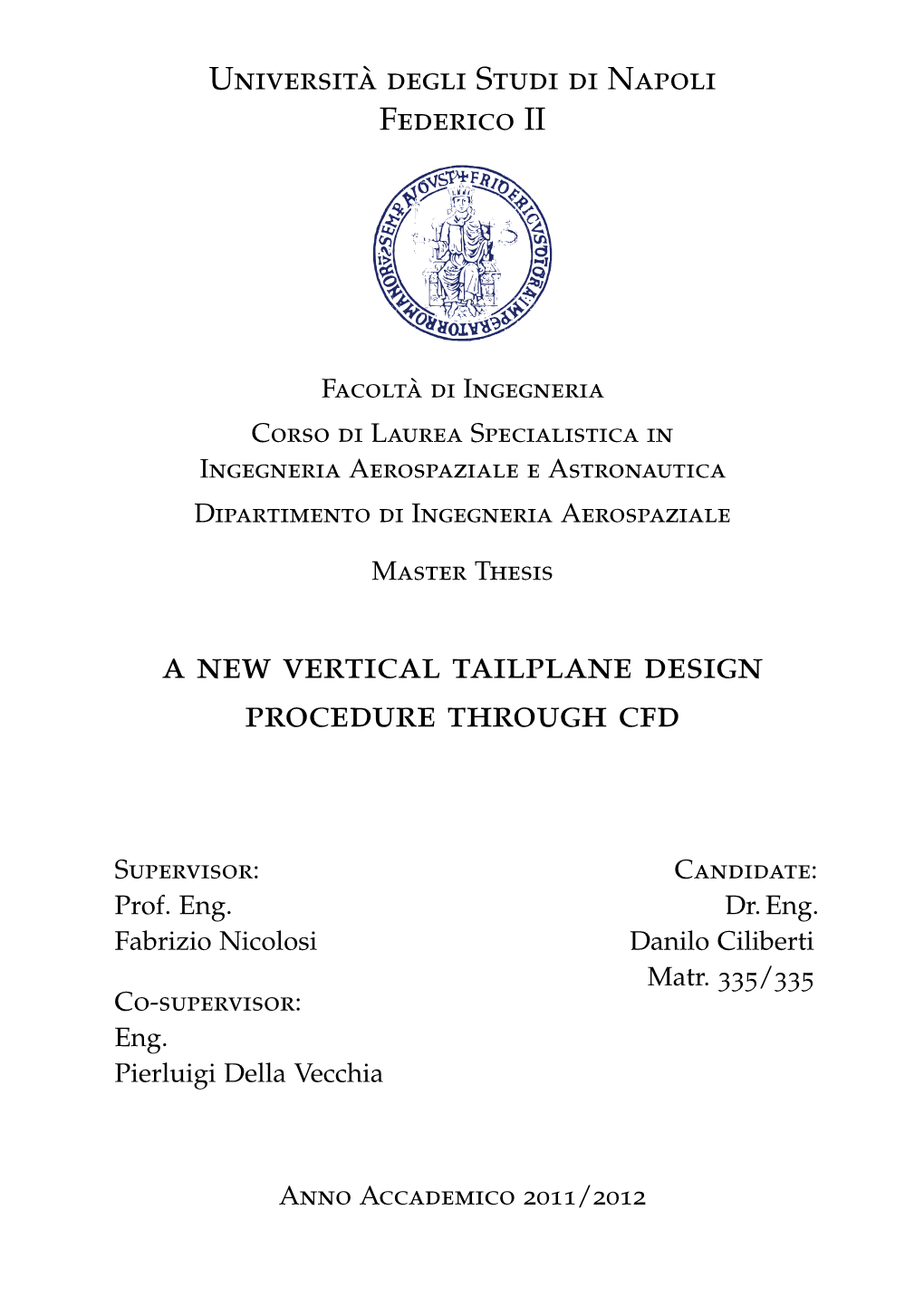
Load more
Recommended publications
-
Robust Fly-By-Wire Under Horizontal Tail Damage
Robust Fly-by-Wire under Horizontal Tail Damage by Zinhle Dlamini Thesis presented in partial fulfilment of the requirements for the degree of Doctor of Philosophy in Electronic Engineering in the Faculty of Engineering at Stellenbosch University Department of Electrical and Electronic Engineering, University of Stellenbosch, Private Bag X1, Matieland 7602, South Africa. Supervisor: Prof T Jones December 2016 Stellenbosch University https://scholar.sun.ac.za Declaration By submitting this thesis electronically, I declare that the entirety of the work contained therein is my own, original work, that I am the sole author thereof (save to the extent explicitly otherwise stated), that reproduction and publication thereof by Stellenbosch University will not infringe any third party rights and that I have not previously in its entirety or in part submitted it for obtaining any qualification. Date: . Copyright © 2016 Stellenbosch University All rights reserved. i Stellenbosch University https://scholar.sun.ac.za Abstract Aircraft damage modelling was conducted on a Boeing 747 to examine the effects of asymmetric horizontal stabiliser loss on the flight dynamics of a commercial fly-by-Wire (FBW) aircraft. Change in static stability was investigated by analysing how the static margin is reduced as a function of percentage tail loss. It is proven that contrary to intuition, the aircraft is longitudinally stable with 40% horizontal tail removed. The short period mode is significantly changed and to a lesser extent the Dutch roll mode is affected through lateral coupling. Longitudinal and lateral trimmability of the damaged aircraft are analysed by comparing the tail-loss-induced roll, pitch, and yaw moments to available actuator force from control surfaces. -
The Effects of Design, Manufacturing Processes, and Operations Management on the Assembly of Aircraft Composite Structure by Robert Mark Coleman
The Effects of Design, Manufacturing Processes, and Operations Management on the Assembly of Aircraft Composite Structure by Robert Mark Coleman B.S. Civil Engineering Duke University, 1984 Submitted to the Sloan School of Management and the Department of Aeronautics and Astronautics in Partial Fulfillment of the Requirements for the Degrees of Master of Science in Management and Master of Science in Aeronautics and Astronautics in conjuction with the LEADERS FOR MANUFACTURING PROGRAM at the MASSACHUSETTS INSTITUTE OF TECHNOLOGY June 1991 © 1991, MASSACHUSETTS INSTITUTE OF TECHNOLOGY ALL RIGHTS RESERVED Signature of Author_ .• May, 1991 Certified by Stephen C. Graves Professor of Management Science Certified by A/roJ , Paul A. Lagace Profes s Aeron icand Astronautics Accepted by Jeffrey A. Barks Associate Dean aster's and Bachelor's Programs I.. Jloan School of Management Accepted by - No U Professor Harold Y. Wachman Chairman, Department Graduate Committee Aero Department of Aeronautics and Astronautics MASSACHiUSEITS INSTITUTE OFN Fr1 1'9n.nry JUJN 12: 1991 1 UiBRARIES The Effects of Design, Manufacturing Processes, and Operations Management on the Assembly of Aircraft Composite Structure by Robert Mark Coleman Submitted to the Sloan School of Management and the Department of Aeronautics and Astronautics in Partial Fulfillment of the Requirements for the Degrees of Master of Science in Management and Master of Science in Aeronautics and Astronautics June 1991 ABSTRACT Composite materials have many characteristics well-suited for aerospace applications. Advanced graphite/epoxy composites are especially favored due to their high stiffness, strength-to-weight ratios, and resistance to fatigue and corrosion. Research emphasis to date has been on the design and fabrication of composite detail parts, with considerably less attention given to the cost and quality issues in their subsequent assembly. -
Fly-By-Wire - Wikipedia, the Free Encyclopedia 11-8-20 下午5:33 Fly-By-Wire from Wikipedia, the Free Encyclopedia
Fly-by-wire - Wikipedia, the free encyclopedia 11-8-20 下午5:33 Fly-by-wire From Wikipedia, the free encyclopedia Fly-by-wire (FBW) is a system that replaces the Fly-by-wire conventional manual flight controls of an aircraft with an electronic interface. The movements of flight controls are converted to electronic signals transmitted by wires (hence the fly-by-wire term), and flight control computers determine how to move the actuators at each control surface to provide the ordered response. The fly-by-wire system also allows automatic signals sent by the aircraft's computers to perform functions without the pilot's input, as in systems that automatically help stabilize the aircraft.[1] Contents Green colored flight control wiring of a test aircraft 1 Development 1.1 Basic operation 1.1.1 Command 1.1.2 Automatic Stability Systems 1.2 Safety and redundancy 1.3 Weight saving 1.4 History 2 Analog systems 3 Digital systems 3.1 Applications 3.2 Legislation 3.3 Redundancy 3.4 Airbus/Boeing 4 Engine digital control 5 Further developments 5.1 Fly-by-optics 5.2 Power-by-wire 5.3 Fly-by-wireless 5.4 Intelligent Flight Control System 6 See also 7 References 8 External links Development http://en.wikipedia.org/wiki/Fly-by-wire Page 1 of 9 Fly-by-wire - Wikipedia, the free encyclopedia 11-8-20 下午5:33 Mechanical and hydro-mechanical flight control systems are relatively heavy and require careful routing of flight control cables through the aircraft by systems of pulleys, cranks, tension cables and hydraulic pipes. -
Glider Handbook, Chapter 2: Components and Systems
Chapter 2 Components and Systems Introduction Although gliders come in an array of shapes and sizes, the basic design features of most gliders are fundamentally the same. All gliders conform to the aerodynamic principles that make flight possible. When air flows over the wings of a glider, the wings produce a force called lift that allows the aircraft to stay aloft. Glider wings are designed to produce maximum lift with minimum drag. 2-1 Glider Design With each generation of new materials and development and improvements in aerodynamics, the performance of gliders The earlier gliders were made mainly of wood with metal has increased. One measure of performance is glide ratio. A fastenings, stays, and control cables. Subsequent designs glide ratio of 30:1 means that in smooth air a glider can travel led to a fuselage made of fabric-covered steel tubing forward 30 feet while only losing 1 foot of altitude. Glide glued to wood and fabric wings for lightness and strength. ratio is discussed further in Chapter 5, Glider Performance. New materials, such as carbon fiber, fiberglass, glass reinforced plastic (GRP), and Kevlar® are now being used Due to the critical role that aerodynamic efficiency plays in to developed stronger and lighter gliders. Modern gliders the performance of a glider, gliders often have aerodynamic are usually designed by computer-aided software to increase features seldom found in other aircraft. The wings of a modern performance. The first glider to use fiberglass extensively racing glider have a specially designed low-drag laminar flow was the Akaflieg Stuttgart FS-24 Phönix, which first flew airfoil. -
ICE PROTECTION Incomplete
ICE PROTECTION GENERAL The Ice and Rain Protection Systems allow the aircraft to operate in icing conditions or heavy rain. Aircraft Ice Protection is provided by heating in critical areas using either: Hot Air from the Pneumatic System o Wing Leading Edges o Stabilizer Leading Edges o Engine Air Inlets Electrical power o Windshields o Probe Heat . Pitot Tubes . Pitot Static Tube . AOA Sensors . TAT Probes o Static Ports . ADC . Pressurization o Service Nipples . Lavatory Water Drain . Potable Water Rain removal from the Windshields is provided by two fully independent Wiper Systems. LEADING EDGE THERMAL ANTI ICE SYSTEM Ice protection for the wing and horizontal stabilizer leading edges and the engine air inlet lips is ensured by heating these surfaces. Hot air supplied by the Pneumatic System is ducted through perforated tubes, called Piccolo tubes. Each Piccolo tube is routed along the surface, so that hot air jets flowing through the perforations heat the surface. Dedicated slots are provided for exhausting the hot air after the surface has been heated. Each subsystem has a pressure regulating/shutoff valve (PRSOV) type of Anti-icing valve. An airflow restrictor limits the airflow rate supplied by the Pneumatic System. The systems are regulated for proper pressure and airflow rate. Differential pressure switches and low pressure switches monitor for leakage and low pressures. Each Wing's Anti Ice System is supplied by its respective side of the Pneumatic System. The Stabilizer Anti Ice System is supplied by the LEFT side of the Pneumatic System. The APU cannot provide sufficient hot air for Pneumatic Anti Ice functions. -
V-Tails for Aeromodels
Please see the V-Tails for Aeromodels recommendations for Yet Another Attempt to Explain Them the browser settings Watching the RCSE forum during November 1998 I felt, that the discussion on V-tails is not always governed by facts and knowledge, but feelings and sometimes even by irritation. I think, some theory of V-tails should be compiled and written down for aeromodellers such that we can answer most of the questions by ourselves. V- tails are almost never used with full scale airplanes but not all of the reasons for this are also valid for aeromodels. As a consequence V-tails are not treated appropriately in standard literature. This article contains well known and also some not so well known facts on V-tails and theoretical explanations for them; I don't claim anything to be "new". I also list some occasionally to be heard statements, which are simply not true. If something is wrong or missing: Please let me know ([email protected]), or, if you think that this article is a valuable contribution to make V- tails clearer for aeromodellers. Introduction Almost always designing a V-tail means converting a standard tail into a V-tail; the reasons are clear: Calculations yield specifications of a standard tail or an existing model is really to be converted (the photo above documents the end of the 2nd life of this glider;-). The task is to find a V-tail, which behaves "exactly like its corresponding" standard- or T-tail - we will see, that this is not possible. We can design the V-tail to have the same behaviour in many respects, we might get some advantages, but we have to pay a price. -
Chapter 55 Stabilizers
EXTRA - FLUGZEUGBAU GmbH SERVICE MANUAL EXTRA 200 Chapter 55 Stabilizers PAGE DATE: 1. July 1996 CHAPTER 55 PAGE 1 EXTRA - FLUGZEUGBAU GmbH SERVICE MANUAL EXTRA 200 Table of Contents Chapter Title 55-00-00 GENERAL . 3 55-21-00 MAINTENANCE PRACTICES . 8 55-21-01 Horizontal Stabilizer . 8 55-21-02 Vertical Stabilizer . 10 PAGE DATE: 1. July 1996 CHAPTER 55 PAGE 2 EXTRA - FLUGZEUGBAU GmbH SERVICE MANUAL EXTRA 200 55-00-00 GENERAL The EXTRA 200 has a conventional empennage with stabilizers and moveable control surfaces. The spars con- sist of carbon roving caps, carbon fibre webs and PVC foam cores. The shells are built of honeycomb sandwich with glass fibre or optional carbon fibre laminate. Also buckling is prevented by plywood ribs. Deviating from this, the elevator is constructed in the same manner as the ailerons (refer to Chapter 57). On the R/H elevator half a trim tab is fitted with a piano hinge. The layer sequences of the stabilizers, the elevator and the rudder are shown in Figures 1-2. All composite parts, as protection against moisture and UV radiation, are coated with an unsaturated polyester gel- coat, an acrylic filler and finally with an acrylic paint. For repair of composite parts refer to Chapter 51. PAGE DATE: 1. July 1996 CHAPTER 55 PAGE 3 EXTRA - FLUGZEUGBAU GmbH GENERAL SERVICE MANUAL EXTRA 200 Layer Sequence Horizontal Tail Figure 1, Sheet 1 PAGE DATE: 1. July 1996 CHAPTER 55 PAGE 4 EXTRA - FLUGZEUGBAU GmbH GENERAL SERVICE MANUAL EXTRA 200 Layer Sequence Horizontal Tail Figure 1, Sheet 2 PAGE DATE: 1. -
A Service Publication of Lockheed Martin Aeronautical Systems Support Company
LOCKHEED MAaTIN 4 VOL. 24, NO. 1 JULY-SEPTEMBER 1997 A SERVICE PUBLICATION OF LOCKHEED MARTIN AERONAUTICAL SYSTEMS SUPPORT COMPANY - • Previous Page Table of Contents Next Page LOCKHEED MARTIN Service News It’s All in the Teamwork A SERVICE PUBLICATION OF t would be difficult to find an area of human endeavor that is more dependent upon team- LOCKHEED MARTIN AERONAUTICAL work for success than aviation. It is significant that mankind’s first conquest of the air was SYSTEMS SUPPORT COMPANY Inot achieved by an isolated visionary laboring in seclusion. Instead, the initial success came through the combined efforts of two gifted bicycle mechanics from Ohio, working with a team of Editor helpers and friends on a windswept beach in North Carolina. Charles I. Gale We at Lockheed Martin Aeronautical Systems Support Company (LMASSC) have never lost sight of the importance of just that kind Vol. 24, No. 1, July - September 1997 of teamwork in the way we operate our business. It is no coinci- dence that LMASSC is organized as a close partnership of two CONTENTS teams of specialists, both fully committed to meeting the total support needs of our customers. 2 Focal Point LMASSC’s Business Development and Each of the LMASSC organizations has its own special areas of Field Support units team up to provide expertise and responsibilities. Business Development, led by the best in total customer support. George Lowe, is the marketing arm for LMASSC and as such provides a remarkably broad range of customer support products. These include a com- 3 All About Power Plant Hoses prehensive spares provisioning program that offers new and overhauled spare parts and Both Teflon and elastomeric hoses are support/test equipment, rebuilt parts, an innovative parts exchange program, and complete used to connect power plant compo- component repair and overhaul. -
AP3456 the Central Flying School (CFS) Manual of Flying: Volume 4 Aircraft Systems
AP3456 – 4-1- Hydraulic Systems CHAPTER 1 - HYDRAULIC SYSTEMS Introduction 1. Hydraulic power has unique characteristics which influence its selection to power aircraft systems instead of electrics and pneumatics, the other available secondary power systems. The advantages of hydraulic power are that: a. It is capable of transmitting very high forces. b. It has rapid and precise response to input signals. c. It has good power to weight ratio. d. It is simple and reliable. e. It is not affected by electro-magnetic interference. Although it is less versatile than present generation electric/electronic systems, hydraulic power is the normal secondary power source used in aircraft for operation of those aircraft systems which require large power inputs and precise and rapid movement. These include flying controls, flaps, retractable undercarriages and wheel brakes. Principles 2. Basic Power Transmission. A simple practical application of hydraulic power is shown in Fig 1 which depicts a closed system typical of that used to operate light aircraft wheel brakes. When the force on the master cylinder piston is increased slightly by light operation of the brake pedals, the slave piston will extend until the brake shoe contacts the brake drum. This restriction will prevent further movement of the slave and the master cylinder. However, any increase in force on the master cylinder will increase pressure in the fluid, and it will therefore increase the braking force acting on the shoes. When braking is complete, removal of the load from the master cylinder will reduce hydraulic pressure, and the brake shoe will retract under spring tension. -
09 Stability and Control
Aircraft Design Lecture 9: Stability and Control G. Dimitriadis Introduction to Aircraft Design Stability and Control H Aircraft stability deals with the ability to keep an aircraft in the air in the chosen flight attitude. H Aircraft control deals with the ability to change the flight direction and attitude of an aircraft. H Both these issues must be investigated during the preliminary design process. Introduction to Aircraft Design Design criteria? H Stability and control are not design criteria H In other words, civil aircraft are not designed specifically for stability and control H They are designed for performance. H Once a preliminary design that meets the performance criteria is created, then its stability is assessed and its control is designed. Introduction to Aircraft Design Flight Mechanics H Stability and control are collectively referred to as flight mechanics H The study of the mechanics and dynamics of flight is the means by which : – We can design an airplane to accomplish efficiently a specific task – We can make the task of the pilot easier by ensuring good handling qualities – We can avoid unwanted or unexpected phenomena that can be encountered in flight Introduction to Aircraft Design Aircraft description Flight Control Pilot System Airplane Response Task The pilot has direct control only of the Flight Control System. However, he can tailor his inputs to the FCS by observing the airplane’s response while always keeping an eye on the task at hand. Introduction to Aircraft Design Control Surfaces H Aircraft control -
Issue No. 1, Jan-Mar
VOL. 25, NO. 1 JANUARY – MARCH 1998 ServiceService NewsNews A SERVICE PUBLICATION OF LOCKHEED MARTIN AERONAUTICAL SYSTEMS SUPPORT COMPANY Previous Page Table of Contents Next Page LOCKHEED MARTIN Service News HOC 1997 A SERVICE PUBLICATION OF uring the week of 13 - 17 October 1997, the ninth Hercules LOCKHEED MARTIN AERONAUTICAL Operators Conference (HOC) was held in Marietta. Judging from SYSTEMS SUPPORT COMPANY D the surveys of approximately 330 attendees, the conference was an overall success. Lockheed Martin is most pleased to Editor Charles E. Wright, II have hosted this event and trusts each participant ben- efitted greatly from the proceedings. Vol. 25, No. 1, January - March 1998 Lockheed Martin is committed to continuation of the CONTENTS conference on a regular basis. We see the conference 2 Focal Point as a valuable forum for sharing of technical informa- L. D. “Dave” Holcomb, Co-Chairman tion and in-service experiences of Hercules operators. Airlift Field Service We also see the importance of having a variety of atten- Alex Gibbs, Squadron Leader dees to Please turn to page 15, column 1 RAAF Technical Liaison Officer L. D. Holcomb 3 Troubleshooting Pressurization Problems HOC Co-Chairman Comments A guide to understanding and solving pressurization problems. or the last three years I have had the privilege of attending the HOC as the International Operator’s Co-Chairman. The increase in rep- 9 Cumulative Index 1974 - 1997 A complete, alphabetical listing of F resentation and presentations from operators each year confirms my Service News technical articles. strong belief in the need and value for operators and Lockheed Martin in the HOC. -
A Historical Overview of Flight Flutter Testing
tV - "J -_ r -.,..3 NASA Technical Memorandum 4720 /_ _<--> A Historical Overview of Flight Flutter Testing Michael W. Kehoe October 1995 (NASA-TN-4?20) A HISTORICAL N96-14084 OVEnVIEW OF FLIGHT FLUTTER TESTING (NASA. Oryden Flight Research Center) ZO Unclas H1/05 0075823 NASA Technical Memorandum 4720 A Historical Overview of Flight Flutter Testing Michael W. Kehoe Dryden Flight Research Center Edwards, California National Aeronautics and Space Administration Office of Management Scientific and Technical Information Program 1995 SUMMARY m i This paper reviews the test techniques developed over the last several decades for flight flutter testing of aircraft. Structural excitation systems, instrumentation systems, Maximum digital data preprocessing, and parameter identification response algorithms (for frequency and damping estimates from the amplltude response data) are described. Practical experiences and example test programs illustrate the combined, integrated effectiveness of the various approaches used. Finally, com- i ments regarding the direction of future developments and Ii needs are presented. 0 Vflutte r Airspeed _c_7_ INTRODUCTION Figure 1. Von Schlippe's flight flutter test method. Aeroelastic flutter involves the unfavorable interaction of aerodynamic, elastic, and inertia forces on structures to and response data analysis. Flutter testing, however, is still produce an unstable oscillation that often results in struc- a hazardous test for several reasons. First, one still must fly tural failure. High-speed aircraft are most susceptible to close to actual flutter speeds before imminent instabilities flutter although flutter has occurred at speeds of 55 mph on can be detected. Second, subcritical damping trends can- home-built aircraft. In fact, no speed regime is truly not be accurately extrapolated to predict stability at higher immune from flutter.