Potential Use of Ohio Limestones and Dolomites for Architectural Aggregate
Total Page:16
File Type:pdf, Size:1020Kb
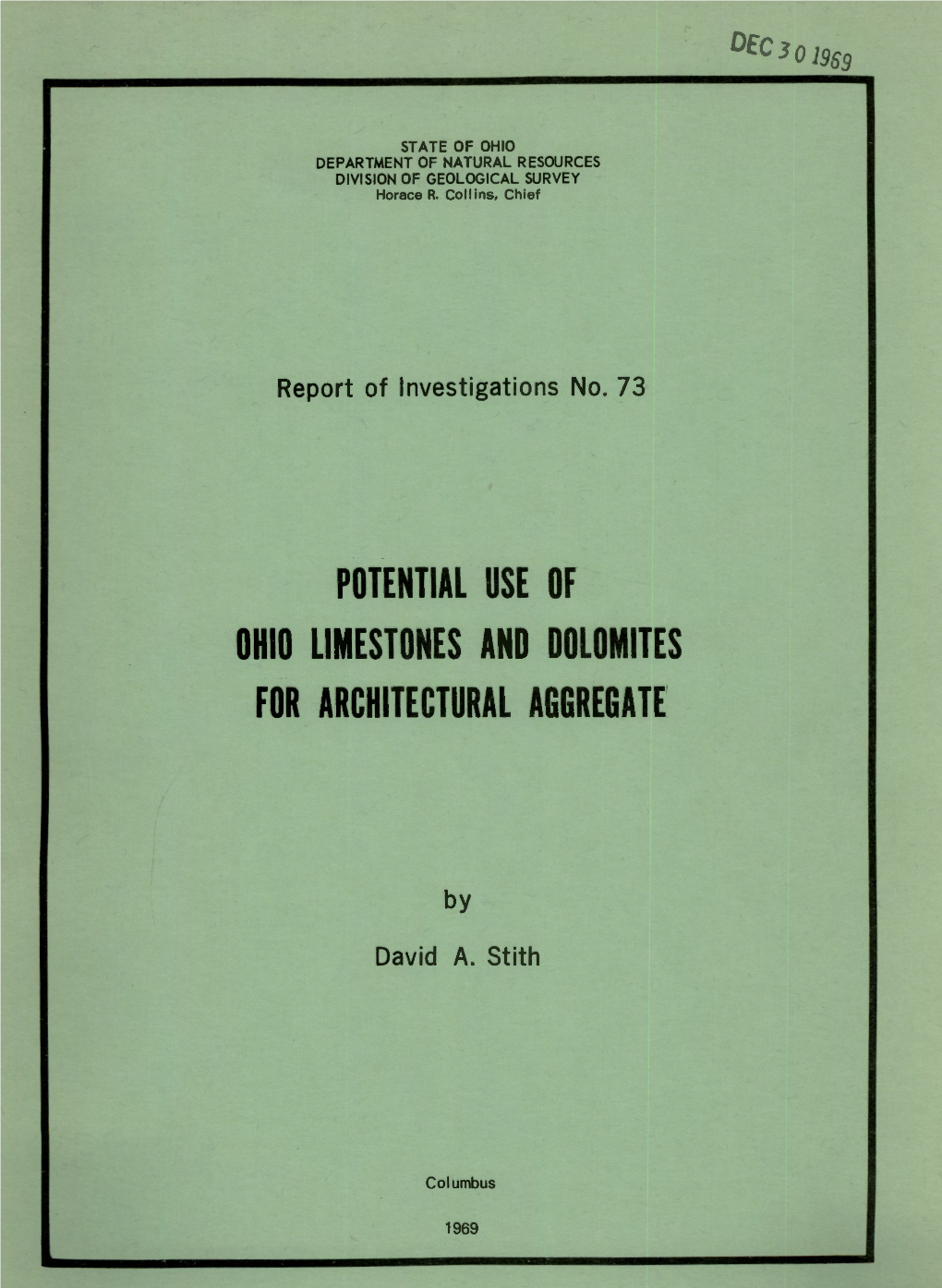
Load more
Recommended publications
-
Waddle Ditch Rattlesnake Creek
Nine-Element Nonpoint Source Implementation Strategy (NPS-IS) for Waddle Ditch-Rattlesnake Creek HUC-12 (05060003 03 05) Prepared for: Fayette Soil and Water Conservation District Prepared by: Civil & Environmental Consultants, Inc. Toledo, Ohio Version 1.0 Approved: June 29, 2021 This page intentionally left blank. Acknowledgements Version 1.0 prepared and written by: Deanna Bobak Civil & Environmental Consultants, Inc. 4841 Monroe Street, Suite 103 Toledo, OH 43623 Brigitte Hisey Fayette Soil & Water Conservation District 1415 US 22 SW, Suite 500 Washington Court House, OH 43160 The Fayette Soil & Water Conservation District (SWCD) would like to acknowledge the collaboration of multiple partners in the preparation of this Nonpoint Source Implementation Strategy (NPS-IS) for the Waddle Ditch-Rattlesnake Creek HUC-12 (05060003 03 05). The Fayette SWCD appreciates those individuals and organizations that contributed background information, insight into objectives and projects for inclusion in this NPS-IS. Thank you to Rick Wilson, Ohio Environmental Protection Agency – Division of Surface Water, for guidance throughout the NPS-IS development process, as well as Jessica D’Ambrosio and the staff of The Nature Conservancy for providing modeling data generated by the Agricultural Conservation Planning Framework (ACPF). This product or publication was financed in part or totally through a grant from the United States Environmental Protection Agency through an assistance agreement with the Ohio Environmental Protection Agency. The contents and views, including any opinions, findings, conclusions or recommendations, contained in this product or publication are those of the authors and have not been subject to any Ohio Environmental Protection Agency or United States Environmental Protection Agency peer or administrative review and may not necessarily reflect the views of the Ohio Environmental Protection Agency or the United States Environmental Protection Agency and no official endorsement should be inferred. -
Xerox University Microfilms
information t o u s e r s This material was produced from a microfilm copy of the original document. While the most advanced technological means to photograph and reproduce this document have been used, the quality is heavily dependent upon the quality of the original submitted. The following explanation of techniques is provided to help you understand markings or patterns which may appear on this reproduction. 1.The sign or "target” for pages apparently lacking from the document photographed is "Missing Page(s)". If it was possible to obtain the missing page(s) or section, they are spliced into the film along with adjacent pages. This may have necessitated cutting thru an image and duplicating adjacent pages to insure you complete continuity. 2. When an image on the film is obliterated with a large round black mark, it is an indication that the photographer suspected that the copy may have moved during exposure and thus cause a blurred image. You will find a good image of the page in the adjacent frame. 3. When a map, drawing or chart, etc., was part of the material being photographed the photographer followed a definite method in "sectioning" the material. It is customary to begin photoing at the upper left hand corner of a large sheet and to continue photoing from left to right in equal sections with a small overlap. If necessary, sectioning is continued again - beginning below the first row and continuing on until complete. 4. The majority of usefs indicate that the textual content is of greatest value, however, a somewhat higher quality reproduction could be made from "photographs" if essential to the understanding of the dissertation. -
The Silurian of Central Kentucky, U.S.A.: Stratigraphy, Palaeoenvironments and Palaeoecology
The Silurian of central Kentucky, U.S.A.: Stratigraphy, palaeoenvironments and palaeoecology FRANK R. ETTENSOHN, R. THOMAS LIERMAN, CHARLES E. MASON, WILLIAM M. ANDREWS, R. TODD HENDRICKS, DANIEL J. PHELPS & LAWRENCE A. GORDON ETTENSOHN, F.R., LIERMAN, R.T., MASON, C.E., ANDREWS, W.M., HENDRICKS, R.T., PHELPS, D.J. & GORDON, L.A., 2013:04:26. The Silurian of central Kentucky, U.S.A.: Stratigraphy, palaeoenvironments and palaeoecology. Memoirs of the Association of Australasian Palaeontologists 44, 159-189. ISSN 0810-8889. Silurian rocks in Kentucky are exposed on the eastern and western flanks of the Cincinnati Arch, a large-wavelength cratonic structure separating the Appalachian foreland basin from the intracratonic Illinois Basin. The Cincinnati Arch area experienced uplift during latest Ordovician-early Silurian time, so that the exposed Silurian section is relatively thin due to onlap and post- Silurian erosional truncation on the arch. On both flanks of the arch, dolomitic carbonates predominate, but the section on the eastern side reflects a more shale-rich ramp that faced eastern Appalachian source areas. In the Silurian section on the western side of the arch, which apparently developed across a platform-like isolation-accommodation zone, shales are rare except dur- ing some highstand episodes, and rocks in the area reflect deposition across a broad, low-gradient shelf area, interrupted by structurally controlled topographic breaks. Using the progression of interpreted depositional environments and nearshore faunal communities, a relative sea-level curve, which parallels those of previous workers, was generated for the section in Kentucky. While the curve clearly shows the influence of glacial eustasy, distinct indications of the far-field, flexural influence of Taconian and Salinic tectonism are also present. -
View of Pa Element, OSU 41751, X 28, Collection
INFORMATION TO USERS The most advanced technology has been used to photo graph and reproduce this manuscript from the microfilm master. UMI films the original text directly from the copy submitted. Thus, some dissertation copies are in typewriter face, while others may be from a computer printer. In the unlikely event that the author did not send UMI a complete manuscript and there are missing pages, these will be noted. Also, if unauthorized copyrighted material had to be removed, a note will indicate the deletion. Oversize materials (e.g., maps, drawings, charts) are re produced by sectioning the original, beginning at the upper left-hand comer and continuing from left to right in equal sections with small overlaps. Each oversize page is available as one exposure on a standard 35 mm slide or as a 17" x 23" black and white photographic print for an additional charge. Photographs included in the original manuscript have been reproduced xerographically in this copy. 35 mm slides or 6" x 9" black and white photographic prints are available for any photographs or illustrations appearing in this copy for an additional charge. Contact UMI directly to order. Accessing theUMI World’s Information since 1938 300 North Zeeb Road, Ann Arbor, Ml 48106-1346 USA Order Number 8820S06 Taxonomy and biostratigraphic significance of Wenlockian and Ludlovian (Silurian) conodonts in the midcontinent outcrop area, North America Kleffner, Mark Alan, Ph.D. The Ohio State University, 1988 UMI 300 N. Zeeb Rd. Ann Arbor, MI 48106 PLEASE NOTE: In all cases this material has been filmed in the best possible way from the available copy. -
Synoptic Taxonomy of Major Fossil Groups
APPENDIX Synoptic Taxonomy of Major Fossil Groups Important fossil taxa are listed down to the lowest practical taxonomic level; in most cases, this will be the ordinal or subordinallevel. Abbreviated stratigraphic units in parentheses (e.g., UCamb-Ree) indicate maximum range known for the group; units followed by question marks are isolated occurrences followed generally by an interval with no known representatives. Taxa with ranges to "Ree" are extant. Data are extracted principally from Harland et al. (1967), Moore et al. (1956 et seq.), Sepkoski (1982), Romer (1966), Colbert (1980), Moy-Thomas and Miles (1971), Taylor (1981), and Brasier (1980). KINGDOM MONERA Class Ciliata (cont.) Order Spirotrichia (Tintinnida) (UOrd-Rec) DIVISION CYANOPHYTA ?Class [mertae sedis Order Chitinozoa (Proterozoic?, LOrd-UDev) Class Cyanophyceae Class Actinopoda Order Chroococcales (Archean-Rec) Subclass Radiolaria Order Nostocales (Archean-Ree) Order Polycystina Order Spongiostromales (Archean-Ree) Suborder Spumellaria (MCamb-Rec) Order Stigonematales (LDev-Rec) Suborder Nasselaria (Dev-Ree) Three minor orders KINGDOM ANIMALIA KINGDOM PROTISTA PHYLUM PORIFERA PHYLUM PROTOZOA Class Hexactinellida Order Amphidiscophora (Miss-Ree) Class Rhizopodea Order Hexactinosida (MTrias-Rec) Order Foraminiferida* Order Lyssacinosida (LCamb-Rec) Suborder Allogromiina (UCamb-Ree) Order Lychniscosida (UTrias-Rec) Suborder Textulariina (LCamb-Ree) Class Demospongia Suborder Fusulinina (Ord-Perm) Order Monaxonida (MCamb-Ree) Suborder Miliolina (Sil-Ree) Order Lithistida -
Sectional Meetings Details of Technical Meetings Follow
Sectional Meetings Details of technical meetings follow. See map for building locations. Bus- iness meetings are scheduled for each section. An important item of business is the election of officers. A. ZOOLOGY MORNING SESSION 1 KAUKE HALL F. LEE ST. JOHN, PRESIDING EFFECTS OF CALCIUM MODULATING DRUGS ON INSECT CENTRAL NERVOUS TISSUE. Kevin M. Hoffman & George F. Shambaugh, Department of Entomology, Ohio Agricultural Research & Development CEnter, Wooster, OHIO 44691 9:00 Drugs which modulate the movements of calcium ions into or within cells were perfused over the desheathed, last abdominal ganglion of the cockroach, Nauphoeta cinerea (Olivier). Synaptic transmission, endogenous spike activity, summed post-synaptic potentials and ganglionic polarization were measured. Sodium nitroprusside in low concentrations caused repetitive firing of giant interneurons after faradic stimulation. CONNECTIONS BETWEEN THE NUCLEUS BASALIS AND THE ARCHISTRIATUM IN THE MALLARD. Patrick Work, Department of Biological Sciences, Kent State University, Kent, Ohio 44242. 9:15 Research reported here is part of a study of the feeding mechanism of the mallard duck (Anas platyrhynchos) which is being conducted at the University of Leiden in the Netherlands. It was done through a Kent State University-Leiden University student exchange program in the summer of 1980. The research consisted of a neuroanatomical and histochemical investigation of the relationship between the forebrain nuclei basalis and archistriatum anterior. These are believed to be important elements in neural control of the feeding mecha- nism in the duck. Anatomical connections between these nuclei were studied with the aid of horseradish peroxidase injected into the archistriatum anterior nucleus, Peroxidase-labeled cells were found only in the most medial portions of the nucleus basalis from the level of the posterior commissure to the rostral border of the archistriatum anterior. -
North American Geology
DEPARTMENT OF THE INTERIOR FRANKLIN K. LANE, Secretary UNITED STATES GEOLOGICAL SURVEY GEORGE OTIS SMITH, Director Bulletin 684 BIBLIOGRAPHY OF NORTH AMERICAN GEOLOGY FOB 1917 WITH SUBJECT INDEX BY JOHN M. NICKLES i WASHINGTON.' GOVEENMENT PHINTING OFFICE 191 5 CONTENTS. Introduction................................................................. 3 Serials examined........................................................... 5 Bibliography............................................................... 9 Outline of subject headinga................................................. 89 Index.................................................................... 93 Lists..................................................................... 135 Chemical analyses...................................................... 135 Minerals described..................................................... 136 Rocks described.. '...................................................... 138 Geologic formations described........................................... 139 2 BIBLIOGRAPHY OF NORTH AMERICAN GEOLOGY FOR 1917, WITH SUBJECT INDEX. By JOHN M. NICKLES. INTRODUCTION. The bibliography of North American geology, including paleon tology, petrology, and mineralogy, for the year 1917 follows the plan and arrangement of its immediate predecessors. It includes publications bearing on the geology of the Continent of North America and adjoining islands; also Panama and the Hawaiian Islands. Papers by American writers on the geology of other parts of the world are not included. -
Environmental Problems and the Construction Aggregate Industry
State of Michigan ENVIRONMENTAL PROBLEMS AND Department of Natural Resources THE CONSTRUCTION AGGREGATE Geological Survey Division INDUSTRY Miscellany 1 Papers presented at Sixth Forum on Geology by William E. Hole, Jr., President of Industrial Minerals American Aggregate Company, Greenville, Ohio Theme II: BUILDING AND CONSTRUCTION STONES AND MINERALS Abstract Edited by The theme of the 70’s will be the environment. The W. A. Kneller construction aggregates industry, already in difficulty with local zoning control, will be further affected by the Cosponsored by requirements of the "new thing". However, it may well Department of Geology and Mineralogy, University of be that proposed legislation could be the vehicle which Michigan Department of Geology, University of Toledo not only satisfies the wants of the environmentalist but Convened at Horace H. Rackham Building also recognizes the need for a viable construction University of Michigan aggregates industry. Ann Arbor At the beginning of each new decade, wise men attempt April 2 and 3, 1970 to forecast the highlights of the upcoming ten years. In the past, there has been a lack of consensus upon the part of this honored group. However, there seems to be a general agreement upon the part of the Contents prognosticating community this year that the "Theme of THEME II: BUILDING AND CONSTRUCTION STONES the 70’s" will be the environment. AND MINERALS The actions of the Federal government generally reflect ENVIRONMENTAL PROBLEMS AND THE the concerns of the public body. Seldom has our CONSTRUCTION AGGREGATE INDUSTRY, William government realigned itself so dramatically as it has with E. Hole, Jr........................................................................ -
Geology of Ohio—The Silurian
A Quarterly Publication of the Division of Geological Survey Spring 1998 GEOLOGY OF OHIO—THE SILURIAN by Michael C. Hansen he Silurian Period occurred more than 400 million years ago in the middle of the Paleo- Tzoic Era. During this 30-million-year-long span, the climate and depositional environments were different than in any other span of time in Siberia Ohio’s geologic history. Sedimentary rocks of the Silurian System dominate the bedrock surface of Laurentia (North America) China the western half of Ohio, although their exposures are limited because thick glacial sediments cover all but the southernmost portion of the outcrop area. Baltica Australia Silurian rocks in Ohio are primarily carbonates— Ohio limestones and dolomites—and the many quarries in these rocks in western Ohio indicate their impor- tance. Silurian rocks in the subsurface of eastern Ohio contain extensive deposits of salt and accu- Africa mulations of natural gas and oil. In local areas in the Antarctica South America India western half of Ohio, magnificent scenery in the form of caves, cliffs, and waterfalls are unexpected Continental configuration during Silurian time (modified from C. R. Scotese and others, 1979, benefits of Silurian rocks. Paleozoic base maps, Journal of Geology, v. 87, fig. 14). The Silurian System was named by Roderick Impey Murchison, a Scotsman who eventually be- came the director of the Geological Survey of Great Britain. He first studied these rocks in Wales and NY named them after a Celtic tribe, the Silures. His MI monumental work, The Silurian System, was pub- platform/ lished in 1838. The lower part of Murchison’s Sil- pinnacle reef urian System overlapped with the upper part of PA Adam Sedgwick’s Cambrian System, a matter which became a great dispute between these two promi- OHIO nent geologists. -
Map of Ohio Karst Areas
STA5&0'0)*0 t %&PARTMENT OF NA563"-3&4063$&4 t %*7*4*0/0'(&0LOGICAL SURVEY OHIO KARST AREAS ASHTABULA LAKE WILLIAMS FULTON LUCAS GEAUGA OTTAWA TRUMBULL HENRY CUYAHOGA SANDUSKY DEFIANCE ERIE WOOD LORAIN PORTAGE PAULDING HURON MEDINA SUMMIT SENECA PUTNAM HANCOCK MAHONING ASHLAND VAN WERT WYANDOT CRAWFORD RICHL AND WAYNE STARK COLUMBIANA ALLEN HARDIN MERCER CARROLL MARION AUGLAIZE HOLMES MORROW TUSCARAWAS JEFFERSON LOGAN KNOX SHELBY UNION COSHOCTON HARRISON DELAWARE DARKE LICKING CHAMPAIGN MIAMI GUERNSEY MUSKINGUM BELMONT FRANKLIN MADISON CLARK PREBLE FAIRFIELD PERRY MONTGOMERY NOBLE MONROE GREENE PICKAWAY MORGAN FAYETTE HOCKING BUTLER WARREN WASHINGTON CLINTON ROSS ATHENS HIGHLAND VINTON HAMILTON CLERMONT PIKE MEIGS JACKSON BROWN ADAMS GALLIA SCIOTO 0 10 20 30 40 miles LAWRENCE 0 10 20 30 40 50 kilometers EXPLANATION Silurian- and Devonian-age carbonate bedrock overlain by less than 20 feet of glacial drift and/or alluvium Probable karst areas Silurian- and Devonian-age carbonate bedrock overlain Area not known to by more than 20 feet of glacial drift and/or alluvium contain karst features Interbedded Ordovician-age limestone and shale overlain Wisconsinan by less than 20 feet of glacial drift and/or alluvium Glacial Margin Illinoian Interbedded Ordovician-age limestone and shale overlain Glacial Margin by more than 20 feet of glacial drift and/or alluvium Recommended citation: Ohio Division of Geological Survey, 1999 (rev. 2002, 2006), Known and probable karst in Ohio: Ohio Department of Natural Resources, Division of Geological Survey Map EG-1, generalized page-size version with text, 2 p., scale 1:2,000,000. OHIO KARST AREAS Karst is a landform that develops on or in limestone, dolomite, or gypsum by dissolution and that is characterized by the presence of characteris- tic features such as sinkholes, underground (or internal) drainage through solution-enlarged fractures (joints), and caves. -
OFR 2011-1, Central Ohio Geology Core Outcrop Workshop II
DEPARTMENT OF NATURAL RESOURCES DIVISION OF GEOLOGICAL SURVEY Lawrence H. Wickstrom, Chief Open-File Report 2011-1 Central Ohio’s Geology in Core and Outcrop Workshop II Hosted by Ohio Department of Natural Resources Division of Geological Survey Sponsored by Ohio Geological Society Horace R. Collins Laboratory Delaware, Ohio April 20, 2011 Ohio Department of Natural Resources Division of Geological Survey 2045 Morse Road, Bldg. C-1 Columbus, Ohio 43229-6693 2011 Agenda 9:00–9:05 A.M. Welcome 9:05–9:30 A.M. Geological Survey’s geohazards and geologic mapping programs 9:30–10:00 A.M. Central Ohio geology 10:00–10:15 A.M. Break 10:15–11:00 A.M. Group A exercise: The utility of Geological Survey map products Group B exercise: Core description 101; anatomy of a fact sheet 11:00–11:45 A.M. Group A exercise: Core description 101; anatomy of a fact sheet Group B exercise: The utility of Geological Survey map products 11:45–12:30 P.M. Lunch provided 12:30–2:00 P.M. Group A exercise: Soil Classifi cations—Unifi ed, AASHTO, USDA, ODOT’s version of AASHTO, and Rock Mass Classifi cation ASTM Group B exercise: Utility of fact sheets in fi eld-like settings; group discussion 2:00–2:15 P.M. Break 2:15–3:45 P.M. Group A exercise: Utility of fact sheets in fi eld-like settings; group discussion Group B exercise: Soil Classifi cations—Unifi ed, AASHTO, USDA, ODOT’s version of AASHTO, and Rock Mass Classifi cation ASTM 3:45–4:00 P.M. -
The Geologic Interpretation of Scenic Features in Ohio1
THE OHIO JOURNAL OF SCIENCE VOL. XLVI SEPTEMBER, 1946 No. 5 THE GEOLOGIC INTERPRETATION OF SCENIC FEATURES IN OHIO1 J. ERNEST CARMAN Department of Geology The Ohio State University TABLE OF CONTENTS PAGE Introduction 241 Some basic facts and principles 243 Gorges of Greene County 247 Hocking County park region 262 Lake Erie Basin and Islands 279 INTRODUCTION To the geologist there are no everlasting hills. The relief features of the earth's surface as we find them today are the result of the work of geologic agents, such as running water, wind, glacial ice; working by geologic processes such as weathering, erosion, transportation, deposition; on geologic materials, the rocks; through long intervals of geologic time. An even sky-line in a rugged region, a level bench on the side of a valley, an asymmetrical ridge and similar features, all have meaning and invite interpretation. Everyone may experience pleasure in seeing the beautiful colors, the symmet- rical forms, or even the fantastic shapes in scenic features but if one may also interpret and decipher the origin and history of these features, how much greater the pleasure and satisfaction derived, and the increased appreciation of the scenic features. The Grand Canyon of the ^Colorado as a scenic feature is beautiful in color of rock material and impressive in magnitude, but the Grand Canyon as the work of the river which occupies it; downcutting and dissecting during 10 to 20 million years; exposing in this downcutting, rock units which differ in lithology, in structure, age and origin;