Investigation of Gravure Printed Cardboard
Total Page:16
File Type:pdf, Size:1020Kb
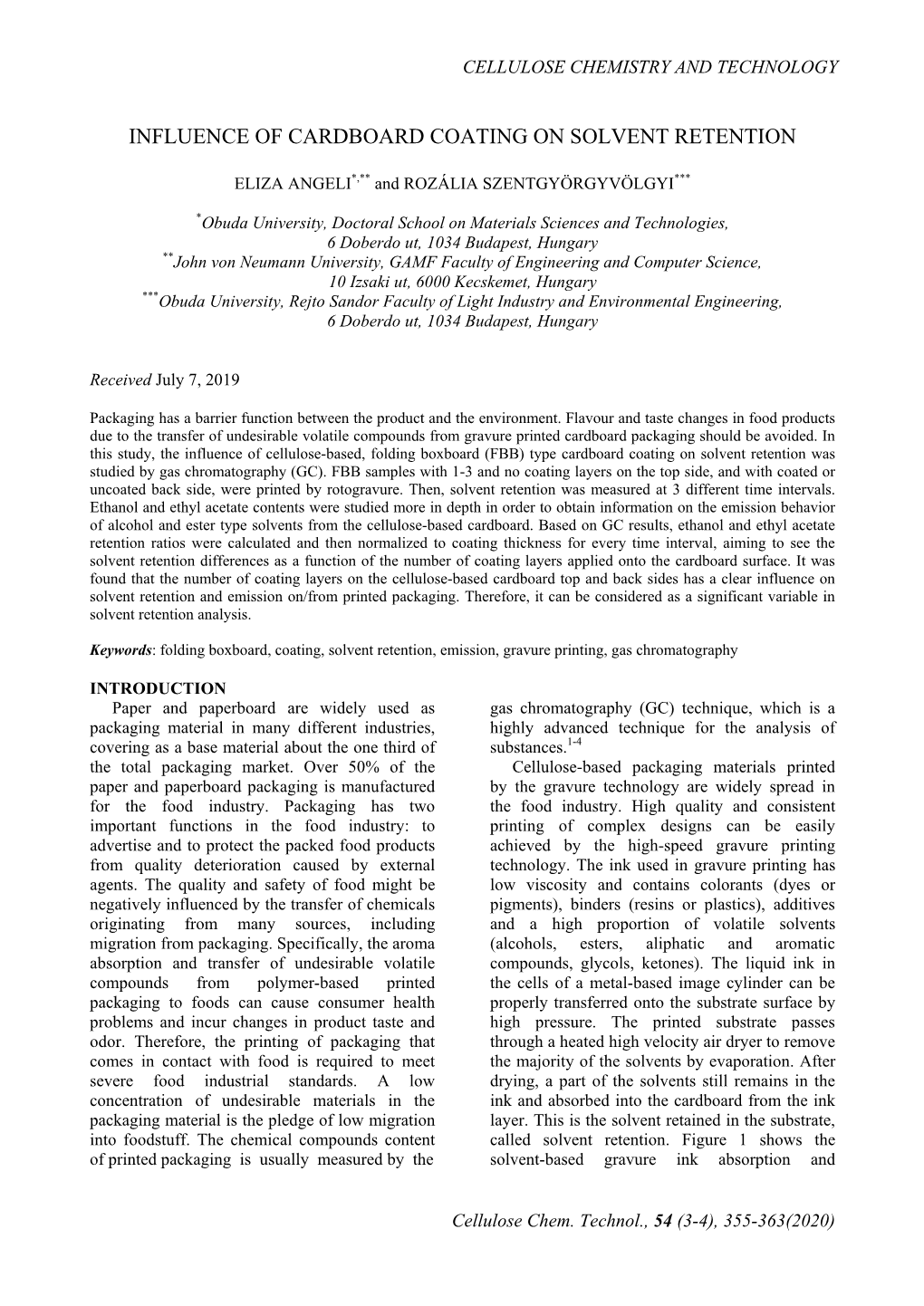
Load more
Recommended publications
-
Cardboard and Brown Paper Bags Office Paper, Newspaper, Junk Mail, Magazines, and Catalogs
Recycling Center 801 Diamond Valley Drive Open: Daily to the public during daylight hours This guide will help you properly prepare your recyclable materials for drop-off at the Town of Windsor Recycle Center. This is a drop-off facility. It does not have a buy-back option and is for use by residents and small businesses. Following this information will help maintain the facility and the recycling program for the benefit of the community. IMPORTANT… • Do not leave your recyclables in plastic bags. Plastic bags are NOT recyclable! • The plastic item must be a BOTTLE or JAR. with a #1 or #2 on the bottom. • 99 percent of these will have a screw-on plastic lid (which isn’t recyclable). • Plastic containers with a #3 - #7 on the bottom are NOT acceptable. • Tubs, buckets, deli plates, microwave/fast food trays, wrappers, Styrofoam, toys, patio furniture, etc. are NOT acceptable. • Plastic bottles larger than 2.5 gallons are NOT acceptable. • Syringes and other medical supplies are NOT acceptable. Cardboard and Brown Paper Bags Corrugated cardboard is easy to recognize. It is made of paper and has an arched layer called “fluting” between smooth sheets called “liners”. The drop-off site has two 40-yard hydraulic compactor units for collecting corrugated cardboard and brown paper bags. The compaction system is self-activated by depositing the prepared materials into a six-inch tall slot. Flatten boxes. Cut or tear large boxes into sections no larger than 4 feet by 4 feet to prevent jamming the machine. No wet, waxed-coated or food-contaminated boxes. -
Decreased Wet Strength in Retorted Liquid Packaging Board Master of Science Thesis in the Master Degree Programme Materials and Nanotechnology
Decreased Wet Strength in Retorted Liquid Packaging Board Master of Science thesis in the Master Degree Programme Materials and Nanotechnology MARIA GUNNARSSON Department of Chemical and Biological Engineering Division of Organic chemistry CHALMERS UNIVERSITY OF TECHNOLOGY Göteborg, Sweden 2012 Report No. 2012:001 Decreased wet strength in retorted liquid packaging board Master of Science Thesis MARIA GUNNARSSON SUPERVISOR: Gunnar Westman EXAMINER: Gunnar Westman Department of Chemical and Biological engineering CHALMERS UNIVERSITY OF TECHNOLOGY Göteborg, Sweden, 2012 Decreased wet strength in retorted liquid packaging board MARIA GUNNARSSON ©MARIA GUNNARSSON, 2012 Report no 2012:001 Department of Chemical and Biological Engineering Chalmers University of Technology SE-412 96 Göteborg Sweden Telephone +46 (0)31-7721000 Cover: The Tetra Recart packaging. Department of Chemical and Biological Engineering Göteborg, Sweden 2012 Decreased wet strength in retorted liquid packaging board Maria Gunnarsson Department of Chemical and Biological Engineering Division of Organic Chemistry CHALMERS UNIVERSITY OF TECHNOLOGY ABSTRACT The Tetra Recart is a retortable food packaging, suitable for high viscous products, making it able to replace most food cans used for storage of food today. The packaging is built up by a paperboard, consisting of an unbleached bottom layer and a bleached top layer. Polymers and aluminium further cover the paperboard in order to protect the food against moisture and light, causing degradation. During the retorting process, the packaging develops a certain wet strength making it hard to disintegrate the pulp fibres in the board. The phenomenon of the developed wet strength is of high interest when inventing and developing new packaging materials. To investigate why and how the phenomenon occurs, a series of trials were made through production of laboratory sheets with subsequent disintegration. -
A Guide to Packaging Material Flows and Terminology Pollution Is Nothing but the Resources We Are Not Harvesting
A Guide to PAckAGinG MAteriAl Flows And terMinoloGy Pollution is nothing but the resources we are not harvesting. We allow them to disperse because we’ve been ignorant of their value. R. Buckminster Fuller A Guide to Packaging Material Flows and Terminology The work upon which this publication is based was funded, in whole, through grants awarded by the California Department of Conservation and GreenBlue through its Sustainable Packaging Coalition®. The statements and conclusions of this report are those of GreenBlue and not necessarily those of the Department of Conservation or its employees. The Department makes no warranties, express or implied, and assumes no liability for the information contained in the succeeding text. The Guide to Packaging Material Flows and Terminology is issued “as is” and with all faults. We give no express warranties, guarantees or conditions. You may have additional rights under local laws which this disclaimer cannot change. However, to the extent permitted under applicable laws, the Green Blue Institute makes no warranty of any kind, either express or implied, including but not limited to, any implied warranties of merchantability, fitness for a particular purpose or non–infringement. The Scrap Specifications Circular 2008 is © 2008 Institute of Scrap Recycling Industries, Inc. (ISRI), 1615 L Street, N.W., Suite 600, Washington, DC 20036, and portions were used by permission. ISRI’s Scrap Specifications Circular is subject to change; therefore, readers should contact ISRI or go to http://www.isri. org/specs to make certain they are reading the most recent version of the Scrap Specifications Circular. Closing the Loop: A Guide to Packaging Material Flows and Terminology Closing the Loop: A Guide to Packaging Material Flows and Terminology was developed by GreenBlue®, a nonprofit institute that works with the private sector to enable the positive redesign of industrial systems. -
26 the Carton Packaging Fact File CARTONBOARD
26 The Carton Packaging Fact File CARTONBOARD 5 The Carton Packaging Fact File 27 KEY FACTS Cartonboard is a multilayered material. The main types of cartonboard are solid bleached board, solid unbleached board, folding boxboard and white lined chipboard. Cartonboard usually has a white, pigmented coating on one or both surfaces Cartonboard specifications Cartonboard can be vary with respect to the pulp combined with other composition of the various materials to vary the visual layers and by the grammage appearance and to extend (weight per sq. metre in the protective properties grammes) and thickness (microns or 0.001 millimetre) Laminations, coatings and impregnations can be added to extend the range of carton applications 28 The Carton Packaging Fact File CARTONBOARD COMMON ABBREVIATIONS SBB Solid Bleached Board SUB Solid Unbleached Board FBB Folding Box Board WLC White Lined Chipboard Different types and grades the range 200-600g/m 2 for grammage product aroma, flavour and hygiene are of cartonboard and their and 350-800µm for thickness. critical. Examples of cartons where abbreviations. The principles SBB is used are perfumes, cosmetics, of cartonboard manufacture, What are the main characteristics chocolates, pharmaceuticals, frozen developments and treatments of cartonboard? foods and cigarettes. Cartonboard is mechanically strong. What is cartonboard? Its stiffness, rigidity and toughness SBB is sometimes referred to as SBS Cartonboard is a multilayer material provide compression strength to protect or GZ. with, usually, three or more layers, or products in distribution and use. It can plies, of cellulose fibre (pulp) derived be cut, creased, folded and glued, giving What is Solid Unbleached Board? from wood. -
Tall Oil Rosin (TOR) Version Number: 8 Issued: 2021-03-15 Replaces SDS: 2019-01-16
SAFETY DATA SHEET According to Regulation (EC) No 1907/2006 Tall Oil Rosin (TOR) Version number: 8 Issued: 2021-03-15 Replaces SDS: 2019-01-16 SECTION 1: Identification of the substance/mixture and of the company/undertaking 1.1. Product identifier Trade name Tall Oil Rosin (TOR) CAS No. 8050-09-7 UFI code 5SDP-7PGU-G604-3JPD EC number 232-475-7 REACH registration number 01-2119480418-32 Index No. 650-015-00-7 1.2. Relevant identified uses of the substance or mixture and uses advised against Use Manufacture rosin Rubber production Binders and release agents Coatings Production of paper and cardboard 1.3. Details of the supplier of the safety data sheet Supplier SunPine AB Street address Box 76 941 22 Piteå Sweden Telephone 0911-23 28 00 Email [email protected] Web site www.sunpine.se 1.4. Emergency telephone number NHS 111 1 / 15 SAFETY DATA SHEET According to Regulation (EC) No 1907/2006 Tall Oil Rosin (TOR) Version number: 8 Issued: 2021-03-15 Replaces SDS: 2019-01-16 Available outside office hours Yes SECTION 2: Hazards identification 2.1. Classification of the substance or mixture Classification according to Regulation (EC) No 1272/2008 Danger classes Skin sensitisation, hazard category 1 Hazard statements H317 2.2. Label elements Labelling according to Regulation (EC) No 1272/2008 Hazard pictograms Signal word Warning Hazard statements H317 May cause an allergic skin reaction. Precautionary statements P261 Avoid breathing smoke/fog/vapors/spray. P280 Wear protective gloves/protective clothing/eye protection/face protection. P302 + P352 IF ON SKIN: Wash with plenty of water/soap. -
Corrugated Board Structure: a Review M.C
ISSN: 2395-3594 IJAET International Journal of Application of Engineering and Technology Vol-2 No.-3 Corrugated Board Structure: A Review M.C. Kaushal1, V.K.Sirohiya2 and R.K.Rathore3 1 2 Assistant Prof. Mechanical Engineering Department, Gwalior Institute of Information Technology,Gwalior, Assistant Prof. Mechanical Engineering 3 Departments, Gwalior Engineering College, Gwalior, M. Tech students Maharanapratap College of Technology, Gwalior, [email protected] [email protected] [email protected] ABSTRACT Corrugated board is widely used in the packing industry. The main advantages are lightness, recyclability and low cost. This makes the material the best choice to produce containers devoted to the shipping of goods. Furthermore examples of structure design based on corrugated boards can be found in different fields. Structural analysis of paperboard components is a crucial topic in the design of containers. It is required to investigate their strength properties because they have to protect the goods contained from lateral crushing and compression loads due to stacking. However in this paper complete and detailed information are presented. Keywords: - corrugated boards, recyclability, compression loads. Smaller flutes offer printability advantages as well as I. INTRODUCTION structural advantages for retail packaging. Corrugated board is essentially a paper sandwich consisting of corrugated medium layered between inside II. HISTORY and outside linerboard. On the production side, corrugated In 1856 the first known corrugated material was patented is a sub-category of the paperboard industry, which is a for sweatband lining in top hats. During the following four sub-category of the paper industry, which is a sub-category decades other forms of corrugated material were used as of the forest products industry. -
The Use of Old Corrugated Board in the Manufacture of High Quality White Papers
Western Michigan University ScholarWorks at WMU Paper Engineering Senior Theses Chemical and Paper Engineering 12-1983 The Use of Old Corrugated Board in the Manufacture of High Quality White Papers Rene H. Kapik Western Michigan University Follow this and additional works at: https://scholarworks.wmich.edu/engineer-senior-theses Part of the Wood Science and Pulp, Paper Technology Commons Recommended Citation Kapik, Rene H., "The Use of Old Corrugated Board in the Manufacture of High Quality White Papers" (1983). Paper Engineering Senior Theses. 209. https://scholarworks.wmich.edu/engineer-senior-theses/209 This Dissertation/Thesis is brought to you for free and open access by the Chemical and Paper Engineering at ScholarWorks at WMU. It has been accepted for inclusion in Paper Engineering Senior Theses by an authorized administrator of ScholarWorks at WMU. For more information, please contact wmu- [email protected]. THE USE OF OLD CORRUGATED BOARD IN THE MANUFACTURE OF HIGH QUALITY WHITE PAPERS by Rene' H. Kapik A Thesis submitted in partial fulfillment of the course requirements for The Bachelor of Science Degree Western Michigan University Kalamazoo, Michigan December, 1983 ABSTRACT Clean corrugated board waste was fractionated into its softwood/ hardwood fiber components, repulped using a kraft pulping process, and bleached using a CEHD bleaching sequence in an effort to produce high brightness fiber suitable for use in medium to high quality white paper. The papers produced had almost equivalent mechanical strengths and opacity, but possessed unsatisfactory brightness and cleanliness when compared to commercially manufactured,:. bleached kraft pulps of identical softwood/hardwood contents. Based on this experimental data, the use of recycled fiber from corrugated board as a fiber substitute in the manufacture of high quality printing and writing papers is not recommended due to its inferior brightness and cleanliness. -
Staff Paper Series Number 206 : United States Wood-Based Industry: a Review of Structure and Organization
UNITED STATES WOOD-BASED INDUSTRY: A REVIEW OF STRUCTURE AND ORGANIZATION by Paul V. Ellefson and Michael A. Kilgore January 2010 STAFF PAPER SERIES NUMBER 206 Department of Forest Resources College of Food, Agricultural and Natural Resources Sciences University of Minnesota St. Paul, MN 55108 For more information about the Department of Forest Resources and its teaching, research, and outreach programs, contact the Department at: Department of Forest Resources University of Minnesota 115 Green Hall 1530 N. Cleveland Avenue North St. Paul, MN 55108-6112 Ph: 612-624-3400 Fax: 612-625-5212 Email: [email protected] http://forestry.umn.edu/publications/staffpapers/index.html The University of Minnesota is committed to the policy that all persons shall have equal access to its programs, facilities, and employment without regard to race, color, creed, religion, national origin, sex, age, martial status, disability, public assistance status, veteran status, or sexual orientation UNITED STATES WOOD-BASED INDUSTRY: A REVIEW OF STRUCTURE AND ORGANIZATION by Paul V. Ellefson and Michael A. Kilgorea January 2010 a Professors, Department of Forest Resources, University of Minnesota, St. Paul, MN. Research supported by Minnesota Agricultural Experim ent Station; Research and Developm ent-RPA Assessment Program, Forest Service, U.S. Departm ent of Agriculture, Washington, DC; and the Southern Research Station, Forest Service, U.S. Department of Agricultural, New Orleans, LA. Contents Page INTRODUCTION 1 TIMBER GROWING INDUSTRY 1 General Character -
3. Baseboard Physical Properties
3. Baseboard physical properties Performance properties 111 Laws of nature 112 Flatness and stability 116 Strength and toughness 123 Defi ned physical properties 125 Tensile strength 125 Compression strength 126 Complex physical properties 128 Tearing resistance 128 Impact burst strength 128 Delamination, interlaminar strength 129 Stiffness 134 Box compression strength 138 Performance properties 110 Reference Manual | IGGESUND PAPERBOARD Performance properties Performance properties The performance properties are related to the physical Measurable properties characteristics of the paperboard. These properties relate The measurable properties are those which are com- to how the paperboard will withstand the surrounding monly found when describing the technical data for a environment. The following performance properties are paperboard grade. The methods described are those described in this chapter: most commonly used. They are also used by Iggesund • fl atness and dimensional stability Paperboard. • strength and toughness For further information about specific testing equip- • stiffness ment see the manufacturers’ product catalogues • box compression strength. (e.g. Lorentzen & Wettre). The measuring methods for the properties listed are described in the following pages: • tensile strength • tearing resistance • interlayer strength, plybond • bending stiffness • bending resistance • bending moment • density • dimensional properties - Flatness • grammage • grammage (plastic-coated products) • thickness • compression strength • moisture content • stiffness • curl and twist. IGGESUND PAPERBOARD | Reference Manual 111 Laws of nature Laws of nature Two of the most basic physical properties that defi ne a pa- Test method and equipment perboard are grammage and thickness. These properties During production the grammage is measured con- tell us how much fibres and coating that is used for one tinuously on-line with an IR device. -
Corrugated 101! ! !Corrugated Vs
Corrugated 101! ! !Corrugated vs. Cardboard! • The term "cardboard box" is commonly misused when referring to a corrugated box. The correct technical term is "corrugated fiberboard carton.”! • Cardboard boxes are really chipboard boxes, and used primarily for packaging lightweight products, such as cereal or board games.! • Corrugated fiberboard boxes are widely utilized in retail packaging, shipping cartons, product displays and many other applications ! requiring lightweight, but sturdy materials.! !Corrugated Composition! Corrugated fiberboard is comprised of linerboard and heavy paper medium. Linerboard is the flat, outer surface that adheres to the medium. The medium is the wavy, fluted paper between the liners. Both are made of a special kind of heavy paper called !containerboard. Board strength will vary depending on the various linerboard and medium combinations.! • Single Face: Medium glued to 1 linerboard; flutes exposed! • Single Wall: Medium between 2 liners! • Double Wall: Varying mediums layered between 3 liners! !• Triple Wall: Varying mediums layered between 4 liners! !Flute Facts! !Corrugated board can be created with several different flute profiles. The five most common flute profiles are:! • A-Flute: Original corrugated flute design. Contains about 33 flutes per foot.! • B-Flute: Developed primarily for packaging canned goods. Contains about 47 flutes per foot and measures 1/8" thick! • C-Flute: Commonly used for shipping cartons. Contains about 39 flutes per foot and measures 5/32" thick! • E-Flute: Contains about 90 flutes per foot and measures 1/16" thick! • F-Flute: Developed for small retail packaging. Contains about 125 flutes per foot and measures 1/32" thick! • Generally, larger flute profiles deliver greater vertical compression strength and cushioning. -
Judging Permanence for Reformatting Projects: Paper and Inks
ConserveO Gram September 1995 Number 19/14 Judging Permanence For Reformatting Projects: Paper And Inks Many permanently valuable NPS documents fibered, high alpha-cellulose cotton and linen such as correspondence, drawings, maps, plans, rags. Early rag papers were strong, stable, and reports were not produced using permanent and durable with relatively few impurities. and durable recording media. When selecting In the mid-17th century, damaging alum paper items for preservation duplication, items sizing was added to control bacteria and marked on the list below with a " - " are at mold growth in paper. By 1680, shorter highest risk and should have special priority for fiber rag papers were being produced due to duplication. Document types marked with a the use of mechanical metal beaters to shred "+" are lower priorities for reformatting as they the rag fibers. By about 1775, damaging tend to be more stable and durable. See chlorine bleaches were added to rag papers Conserve O Gram 19/10, Reformatting for to control the paper color. Acidic alum Preservation and Access: Prioritizing Materials rosin sizing was introduced around 1840 to for Duplication, for a full discussion of how to speed the papermaking process thus leading select materials for duplication. NOTE: Avoid to even shorter-lived papers. Rag papers using materials and processes marked " - " when became less common after the introduction producing new documents. of wood pulp paper around 1850. Compared to rag paper, most wood pulp papers have Paper much poorer chemical chemical and mechanical strength, durability, and stability. All permanently valuable original paper - documents should be produced on lignin-free, Ground or mechanical wood pulp paper: high alpha-cellulose papers with a pH between After 1850, most paper produced was 7.5 and 8.0, specifically those papers meeting machine-made paper with a high proportion the American National Standards Institute of short-fibered and acidic wood pulp. -
THE REVISION of EU ECOLABEL CRITERIA for Converted Paper Products
THE REVISION OF EU ECOLABEL CRITERIA for Converted Paper Products Draft Preliminary Report Malgorzata Kowalska, Antonios Konstantas, Oliver Wolf Marzia Traverso, Rose Nangah Mankaa, Sabrina Neugebauer November 2018 EUR xxxxx xx 1 This publication is a Science for Policy report by the Joint Research Centre, the European Commission’s in-house science service. It aims to provide evidence-based scientific support to the European policy-making process. The scientific output expressed does not imply a policy position of the European Commission. Neither the European Commission nor any person acting on behalf of the Commission is responsible for the use which might be made of this publication. Contact information Name: Address: E-mail: Tel.: JRC Science Hub https://ec.europa.eu/jrc JRCxxxxx EUR xxxxx xx PDF ISBN xxx-xx-xx-xxxxx-x ISSN xxxx-xxxx doi:xx.xxxx/xxxxxx XX-NA-xxxxx-EN-N Print ISBN xxx-xx-xx-xxxxx-x ISSN xxxx-xxxx doi:xx.xxxxx/xxxxxx XX-NA-xxxxx-EN-C © European Union, 20xx Reproduction is authorised provided the source is acknowledged. How to cite: Authors; title; EUR; doi All images © European Union 20xx, except: 2 Table of contents ABSTRACT ............................................................................................................ 3 Executive summary ............................................................................................... 3 1. Introduction ...................................................................................................... 4 2. Task 1: Scope and definition analysis ..................................................................