Revealing Internal Flow Behaviour in Arc Welding and Additive
Total Page:16
File Type:pdf, Size:1020Kb
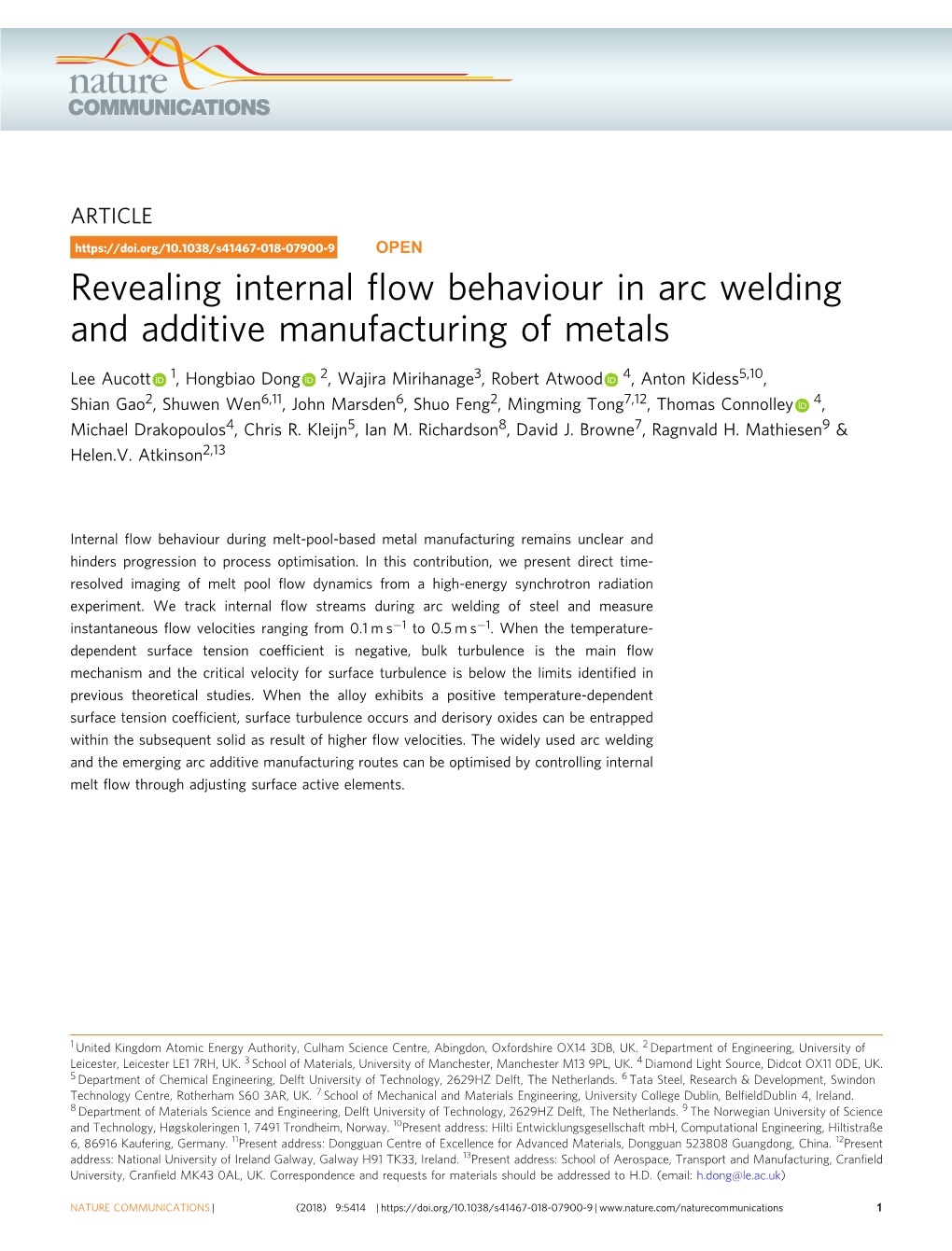
Load more
Recommended publications
-
Millimeter Wave Linac and Wiggler Structures
MM-Wave Linac and Wiggler Structures H. Henke Technical University Berlin Institut fuer Theoretische Elektrotechnik Einsteinufer 17, EN 2 D- 10587 Berlin Abstract In an international collaboration a new technology is kW RF peak power for 1 mA current. This is a reasonably being developed for a 50 MeV millimeter RF-wavelength low power level for designing new sources, for instance little electron linear accelerator complex for production of coherent sheet beam klystrinos also in planar technology. Then, the tunable synchrotron radiation. The accclcrator components and whole device would fit on a standardlab table. the wiggler are being designed with planar geometries suitable 2.5MeV F MeV for deep X-ray lithography and subsequent electroplating F5o”r:e bUrK’1P”l (LIGA) or for etching and electroplating silicon wafers. The b&c design ideas of different components for bunching, pre- acceleration, acceleration, focussing and the wiggler are presented. hem 1. INTRODUCTION Micromechanic technology has developed a vast range of fabricational methods for devices in the submillimeter range: high precision stamping, diamond lathes, laser cutting, diffusion bonding, lithography and etching of silicon wafers and deep X-ray lithography with subsequent electroplating Fig. 1 Conceptual design of an integrated mm-wave (LIGA [ll). So, the technology is available for studying and ndiaton source (IMIRAS) eventually building high precision accelerator components and struclures for very high RF frcquencics, let us say above 100 The paper presents different RF structures for acceleration GHz. In this context it is of great importance that the relative and pre-acceleration, possible focussing devices and structures dimensional and frequency tolerances increase with tie square for a microwave wiggler. -
Cutting Tools & Metalworking
17–268 Edge Finders, Wiggler Sets, Height Gauges, Surface Gauges, Bore Gauge Sets Edge Finders Surface Gauges Egde Finders Surface Gauges 0962311 0962312 3163164 7059268 7059269 7059270 Part No. Head Diameter Shank Diameter Style Type 0962311 0.500" 1/2" Single End Edge Finder 0962312 0.200" / 0.500" 1/2" Double End Edge Finder 3163164 0.200" 3/8" Single End Edge Finder 7059268 0.200" 3/8" Single End Edge Finder 7059269 0.200" 1/2" Single End Edge Finder 7059270 0.200" 3/8" Single End Edge/Center Finder Wiggler Sets Part No. Spindle Size Base Size Base Material 3163146 4" / 7" 2-3/16" x 1-5/8" Steel 5 Piece Wiggler Set 3163147 12" / 9" 3-1/8" x 2-1/2" Steel • Made from precision ground tool steel • Includes offset indicator holder and improved chuck design for holding Bore Gauge Sets attachments Telescoping Gage Sets • Range: 1/2-6" • Handle length: 2-3/8" except 3-1/4 on the largest • Each with a handle, one rigid contact arm Part No. Contents and one spring tensioned contact arm 0962313 Chuck, (4) Attachments • Hardened and ground radius on ends CUTTING Height Gauges Part No. Range Contents 0324730 1/2" - 6" 5 Piece Set Includes: 5 Telescoping Gauges Electronic Height Gage - T 3752 Series OOLS & METALWORKING • Clear bar graduations in .100" and Telescoping Gage Sets 5mm increments • Automatically self-centering • Carrier and scriber designed to read from zero, set • Has two telescoping contacts ZERO at any position • Constant spring tension gives uniform • Ability to retain and return to true zero reading contact pressure • In/mm conversion • Easily locked at any setting • Ability to assign minimum and maximum limits • RS232 output for data collection, analysis and hard Part No. -
Newsletter Volume 1, Issue 1
February 2010 MiniTech Engineering & Model Supplies Vol 2 No 1 Newsletter Volume 1, Issue 1 It seems that one of the more Well this edition of the popular items that sell well are Newsletter should solve that Job Interview Question books. In searching for new titles little issue once and for all. You are driving along in your car we have come across a supplier Another slightly different on a wild, stormy night. You pass issue deals with a tool that who is willing to send us their by a bus stop, and you see three How to use a many machinists already collection of volumes. Our have. Sitti ng in their shed people waiting for the bus: wiggler freight costs being reduced by “somewhere,” it doesn’t get a making purchases in bulk. jersey because the user 1. An old lady who looks as if she (wobbler) is about to die. doesn’t really know how to We ha ve listed the titles inside. 2. An old friend who once saved put it to work. That could be your life. Steady as she You may be interested to check the case for the ubiquitous them out and try something 3. The perfect man (or) woman goes or the method travelling steady. you have been dreaming about. completely different for your of using a travelling One person’s methodology steady. next project. for putting it to good use is Which one would you choose to also covered in this issue of offer a ride to, knowing that there There are a lot of tools out there Massive list of the Newsletter. -
February 18 Online Auction
09/30/21 04:21:28 February 18 Online Auction Auction Opens: Thu, Feb 13 4:00pm ET Auction Closes: Tue, Feb 18 7:00pm ET Lot Title Lot Title 1 Rustic Looking Old Hutch With One Drawer 101 Antique Primitives A Hand Forged Meat (Hay) and Two Doors, Pencil Sharpener Mounted On Hook With Steel Handle 10"L x 4 1/2"W Side, Would Be Cool If Remodeled, 40"W x Handle and Hand Forge Primitive All Steel 16"D x 54"H, Fair Condition - As-Is Hammer 8"L x 3 1/2"W, Both Very Unique and 10 Very Cool Plaster "Fishing Lure" Picture In Rare Finds 100 Years Old Each of Them, Good Good Condition, 10"Sq Condition 100 Fireplace Iron Log Tongs, All Steel 1010 1899 O Morgan Silver Dollar, Really Nice Construction, Two Large Brass Ends for Looking Coin Handles To Protect Your Hands From Heat, 1011 New Stamped 925 Silver Plated Ring Size 8, Could Also Be Used For Camping, Good Marquise Cut Black Sapphire Black on Black Condition, 23"L Gold Plated, Magnificent! 1000 1880 P Morgan Silver Dollar, Great Looking 1012 Indian Head $5. Half Eagle in 1 Oz. .999 Fine Collectible Coin Copper Copy 1001 New Exquisite Emerald Cut Pink Ice Black 1013 New Size 8 Ring, 925 Stamped Sterling Silver Gold Plated Setting, Extraordinary Beauty, Size Plated, Emerald Cut CZ, Lavish And Gorgeous 9 1014 2010 Canadian Maple Leaf .999 Fine Silver, 1 1002 1893 Carson City Morgan Silver Dollar Troy Oz. Mintage 667,000 Fine Condition, Harder To 1015 New Size 6 Black Gold Filled Ring, Get Key Date, Great Circulated Piece With Extraordinarily Beautiful, Very Unique, Great Eye Appeal, A Real Prize Aquamarine, It Speaks For Itself 1003 New Oval Cut Aquamarine With Iridescent 1016 1904 O Morgan Dollar 90% Silver New Sapphires, Gleaming Black Gold Plated Size 6 Orleans Mint Ring 1017 New Silver Plated Ring Size 8, Princess Cut 1004 1982 Engelhard Prospector 1 Troy Oz. -
Drill Press Operator: Instructor's Guide
DOCUMENT RESUME 2D 109 N77 CE 004 335 AUTHOR Kagan, Alfre d; And Others TITLE -Drill Press Operator: Instructor's Guide. INSTITUTION New York State Education Dept., Albany. Bureau of Continuing Education Curriculum Development.; New York State Education Dept., Albany. Bureau of Secondary,Curriculum Development. PUB DATE 75 NOTE . 85p.; Part of SingleTool Skills Program, Machine Industries Occupations EDRS PPICE MIP-$0.76 HC-$4.43 PLUS POSTAGE DESCRIPTORS Adult Education; *Curriculum Guides; Machine Tool Operators; *Machine Tools; Metal Working Occupations; Post Secondary Education; Secondary Education; Shop Curriculum; *Trade and Industrial Education IDENTIFIERS *Drill Press Operators ABSTRACT The course is intended to kelp meet, in a relatively short time, the need for trained operators in metalworking. It can be used by students with little education or experience and is suitable far use in adult education programs and in manpower development and training progress. The course is designed' to be completed in approximately 30 weeks and can be adapted for use in secondary 'schools. On successful completion of the course the student will be qualified for an entry-level job as operator in a drill press; he will not qualify as a eachinist. The guide includes h general job content outline for the teacher to use in explaining what the operator's job includes. There are Il shop projects (comprising 19 jobs) accompanied by 32 pages of drawings for the projects. Three of the jobs introducb students to the use of metric measurement. For each job there is a job sheet providing details on performance objectives, equipment, operations, materials, references, procedure, techniques, and time required. -
Formation of Intermetallic Phases in Al-10Si-0.3Fe Based Alloys
Formation of Intermetallic Phases in Al-10Si-0.3Fe based Alloys vorgelegt von Master of Engineering Jiamin Yu von der Fakultät III - Prozesswissenschaften der Technischen Universität Berlin zur Erlangung des akademischen Grades Doktor der Ingenieurwissenschaften -Dr.-Ing.- genehmigte Dissertation angefertigt am Helmholtz-Zentrum Berlin für Materialien und Energie Institut für Angewandte Materialforschung Promotionsausschuss: Vorsitzender: Prof. Dr. -Ing. Walter Reimers Berichter: Prof. Dr. rer. nat. John Banhart Berichter: Prof. Dr. rer. nat. Dieter Herlach Tag der wissenschaftlichen Aussprache: 16 December 2016 Berlin 2016 献给我最挚爱的父亲母亲 To my beloved parents Abstract Abstract The emphasis of the work lies on finding out how impurities and the addition of Sr influence the formation of Fe-rich intermetallic phases and the formation of the eutectic Si phase in Al-Si casting alloys. A further objective of this study was the understanding of the influence of the cooling rate on the formation of intermetallic phases. For this purpose, four Al-10Si- 0.3Fe-based casting alloys (high-purity alloy with and without addition of 200 ppm Sr and corresponding commercial alloys) have been chosen for this study. The experimental work was focused on the three-dimensional analysis of Fe-rich intermetallic phases using tomographic methods on the micrometer scale such as serial slicing with a Focused Ion Beam and Scanning Electron Microscopy imaging as well as synchrotron X-ray tomography. The three-dimensional analyses were supported by two-dimensional studies using a combination of optical microscopy, scanning electron microscopy and transmission electron microscopy. Besides the well-known phases, i.e. the α intermetallic phase, the tetragonal δ phase and the β phase, a new γ phase was found. -
PRECISION ENGINEERING TOOLS WE HAVE WHAT IT TAKES to EXCEED & EXCEL the Plant
PRECISION ENGINEERING TOOLS WE HAVE WHAT IT TAKES TO EXCEED & EXCEL The plant. The people. The passion 500,000 sq ft manufacturing | integrated research & development | advanced cnc machining | quality assurance Groz has always exceeded the expectations of tool manufacturers and users the world over. Groz carefully makes each tool under stringent quality control processes that are achieved in a hi-tech manufacturing environment in a 500,000 square foot plant. If you demand quality, trust Groz. ADDITIONS 07 08 Straight Straight & Edge Knife Edges Squares Dear Valued Customer, It is my pleasure to present to you the new catalogue that covers our 13 17 range of Precision Engineering Multi-Use Magnetic Tools. Rule and Compass Gauge We have covered fair ground over the last few years and with our state-of-the art production facility, we can now do much more 22 31 than before. You will see many Electronic Adjustable technologically superior products Edge Finders Vee Block Set as well as modifications to some of the earlier designs, in the following pages. Further, I assure you of the same top performance to which you are accustomed to from Groz. 31 35 Ball Bearing Pot We appreciate your business and Vee Block & Magnets value your loyalty & trust. Clamp Sets Warm Regards, 37 38 Sine Bars Sine Plates ANIL BAMMI Managing Director 46 49 Tweezersezers Tap Wrenchesnches - Prefessionalnal 68 7777 Rotaryry RRapidap Headd AActionct Millingng DDrillri Pressressess VicesVices Machinehine VicesVi CA02 PRECISION ENGINEERING TOOLS 1 Measuring and Marking -
Manufacturing Processes 4-5
MANUFACTURING PROCESSES 4-5 Virasak Book: Manufacturing Processes 4-5 (Virasak) This text is disseminated via the Open Education Resource (OER) LibreTexts Project (https://LibreTexts.org) and like the hundreds of other texts available within this powerful platform, it freely available for reading, printing and "consuming." Most, but not all, pages in the library have licenses that may allow individuals to make changes, save, and print this book. Carefully consult the applicable license(s) before pursuing such effects. Instructors can adopt existing LibreTexts texts or Remix them to quickly build course-specific resources to meet the needs of their students. Unlike traditional textbooks, LibreTexts’ web based origins allow powerful integration of advanced features and new technologies to support learning. The LibreTexts mission is to unite students, faculty and scholars in a cooperative effort to develop an easy-to-use online platform for the construction, customization, and dissemination of OER content to reduce the burdens of unreasonable textbook costs to our students and society. The LibreTexts project is a multi-institutional collaborative venture to develop the next generation of open-access texts to improve postsecondary education at all levels of higher learning by developing an Open Access Resource environment. The project currently consists of 13 independently operating and interconnected libraries that are constantly being optimized by students, faculty, and outside experts to supplant conventional paper-based books. These free textbook alternatives are organized within a central environment that is both vertically (from advance to basic level) and horizontally (across different fields) integrated. The LibreTexts libraries are Powered by MindTouch® and are supported by the Department of Education Open Textbook Pilot Project, the UC Davis Office of the Provost, the UC Davis Library, the California State University Affordable Learning Solutions Program, and Merlot. -
Materials Sciences Programs Fiscal Year 1996
DOE/ER-0703 Dist. Category UC-404 June 1997 Materials Sciences Programs Fiscal Year 1996 U.S. Department of Energy Office of Energy Research Office of Basic Energy Sciences Division of Materials Sciences Germantown Building 19901 Germantown Road Germantown, MD 20874-1290 FOREWORD The Division of Materials Sciences is located within the Department of Energy (DOE) in the Office of Basic Energy Sciences which is under the Office of Energy Research. The Director of the Office of Energy Research is appointed by the President and confirmed by the Senate. The Director of the Office of Energy Research is responsible for oversight of, and providing advice to, the Secretary of Energy on the Department's research portfolio and on the management of all of the Laboratories that it owns, except for those that are designated as having a primary role in nuclear weaponry. The Division of Materials Sciences is responsible for basic research and research facilities in strategic materials science topics of critical importance to the mission of the Department and its Strategic Plan. Other programmatic divisions under the Office of Basic Energy Sciences are Chemical Sciences, Engineering and Geosciences, and Energy Biosciences; information for them is contained on page 157. Materials Science is an enabling technology. The performance parameters, economics, environmental acceptability and safety of all energy generation, conversion, transmission and conservation technologies are limited by the properties and behavior of materials. The Materials Sciences programs develop scientific understanding of the synergistic relationship amongst the synthesis, processing, structure, properties, behavior, performance and other characteristics of materials. Emphasis is placed on the development of the capability to discover technologically, economically, and environmentally desirable new materials and processes, and the instruments and national user facilities necessary for achieving such progress. -
Wiggler - a Center Finder for the Lathe MT2 Spring Center - a Wiggler and a Help for Tapping
Wiggler - a center finder for the lathe MT2 spring center - a wiggler and a help for tapping February 2010 This idea came out during a discussion on the 7x12minilathe group in June 2008, though it is not really a new idea. This tool was made in 2008 and the MT2 taper, as well as the drill chuck arbors I'm using, was made using a taper attachment that is yet to be finished. I have been awaiting for the taper attachment to be definitively finished to show the tools made on it, but things go slowly sometimes and doesn't make sense to wait anymore. Of course, after all this time there are light wear signs. The main idea I have for lathe tooling is to make small tools for a small lathe. A spring center can also be made with a straight shank and then hold it on the drill chuck, but that is one tool holding other tool and there goes the lathe bed length. So this one was made with a MT2 taper to fit the mini-lathe tailstock and for two different uses. To be used as a lathe wiggler (or center finder) and also for tapping. To use it as a center finder, a bar was center drilled on one end and a 60º center turned on the other end. For tapping, a tap holder was cen- ter drilled on the rear end. The MT2 center was drilled and reamed for the center shaft and bored larger in the front end for the collar to be pressed on. -
MW Article Index
MW Article Index Article Title Author Name Subject Issue Page A Rocking, Swinging Grinder Table Harold Mason Shop Machinery MW Vol. 01 No. 1 Feb-Mar 1988 4 Old Lathe Collet Adapters Philip Duclos Lathes MW Vol. 01 No. 1 Feb-Mar 1988 12 A Vernier Dividing Head Alberto Marx Shop Machinery MW Vol. 01 No. 1 Feb-Mar 1988 16 Surface Grinding On a Vertical Mill Aubrey Keet Mills MW Vol. 01 No. 1 Feb-Mar 1988 19 A Band Saw Speed Reducer Bob Nelson Shop Machinery MW Vol. 01 No. 1 Feb-Mar 1988 22 Curved Spoke Flywheel Philip Duclos Projects MW Vol. 01 No. 2 Apr-May 1988 4 A Double-ended Dial Indicator Adapter Guy Lautard Shop Machinery MW Vol. 01 No. 2 Apr-May 1988 12 Automatic Carriage Stop R. P. Lebaron Lathes MW Vol. 01 No. 2 Apr-May 1988 15 A Reverse for a Small Lathe E. T. Feller Lathes MW Vol. 01 No. 2 Apr-May 1988 16 Belt Sander Robert S. Hedin Shop Machinery MW Vol. 01 No. 2 Apr-May 1988 20 Basic Metal Finishes James B. Harrill General Machining Knowledge MW Vol. 01 No. 3 Jun-Jul 1988 3 Make Your Own Collet Chuck Pat Loop Lathes MW Vol. 01 No. 3 Jun-Jul 1988 4 Adjustable Try Squares Ted Wright Shop Accessories MW Vol. 01 No. 3 Jun-Jul 1988 8 Brass Hammer Bill Davidson Shop Accessories MW Vol. 01 No. 3 Jun-Jul 1988 12 Unorthodox Mill/Lathe Grinder Philip Duclos Shop Machinery MW Vol. 01 No. -
1/13 Particle and Liquid Motion in Semi-Solid Aluminium Alloys
Manuscipt Text Only Click here to view linked References Particle and liquid motion in semi-solid aluminium alloys: a quantitative in situ micro-radioscopy study S. Zabler1*, A. Ershov2, A. Rack3, F. Garcia-Moreno4, T. Baumbach2, J. Banhart4,5 1Universität Würzburg, Institute of Physics and Astronomy, Würzburg Germany, *corresponding author, [email protected], phone: [+49] (0)931-31 86261, fax: [+49] (0)931-31 81909. 2Karlsruher Institute of Technology, ANKA, Karlsruhe Germany, [email protected], [email protected]. 3European Synchrotron Radiation Facility, Grenoble France, [email protected]. 4Helmholtz Center Berlin – Functional Materials, Berlin Germany, [email protected]. 5Technische Universität Berlin, Berlin Germany, [email protected]. Abstract Semi-solid melt exhibits a very unpredictable rheology and filling dynamics, when it is injected into thin-walled components. Optimization of the process requires visual insight into the casting process during the injection. For this purpose we inject semi-solid Al-Ge alloy into two different thin channel geometries while recording high-resolution radiographs at fast frame rates (up to 1000 images/s). The comparison of a bottleneck channel, which had been previously used for slower experiments, with a right-angle turn geometry reveals a significant influence of the channel’s shape on the flow behavior of the particle-liquid mixture. While the bottleneck is quickly sealed with densified solid, turbulences in the right-angle turn apparently permit the solid particles and clusters to move conjointly with the liquid and thus achieve a more complete filling. Single particle trajectories and rapid break-up of solid skeletons in such a system are observed for the first time in situ.